3D printer filament mixer
Array – Mosaic Manufacturing
Why Array
Large build volume and automated print monitoring means low downtime and high throughput.
Print up to 8 materials in a single part with industrial materials , including PEEK, PEKK and Ultem
With one operator able to run the equivalent of 250 3D printers, 3D printing large production volumes is finally possible.
Increase your throughput by 10x
Increase your capacity by ten times. Array's robotic system swaps out materials and print beds to ensure your printers are running even when you're not around.
Reduce Downtime with Element HT
Reduce any unplanned downtime from hours to minutes by leveraging ElementHT's modular design for quick serviceability of key components.
Spend your time where it counts
Rely on Array's bed removal and material changing systems so your team spends less time working with printers and more time on other activities.
Unlock ultimate flexibility with Palette X
Print with up to 8 materials in a single part to unlock an entirely new range of prints. Mosaic's Palette X technology brings a new dimension to your parts.
Automate your workflows with Canvas
Access smart queueing, analytics and an equipment dashboard to understand and control all your printing workflows with Canvas Enterprise.
Reduce your cost per part by
up to 95%With Array's high throughput and low-cost base, see your cost per part drop by over 10 times. Input your best estimates in our total cost per part calculator and one of our representatives will get in touch to give you a sense of how Array will impact your bottom line.
TOTAL COST PER PART CALCULATOR
Step 1/4
1. Select Materials
Choose up to 5
ABS ASA CF Nylon CF PETG ESD Nylon 6 PC PEEK PEI 9085 PEKK PETG PLA TPU
Please select an option to continue
2.
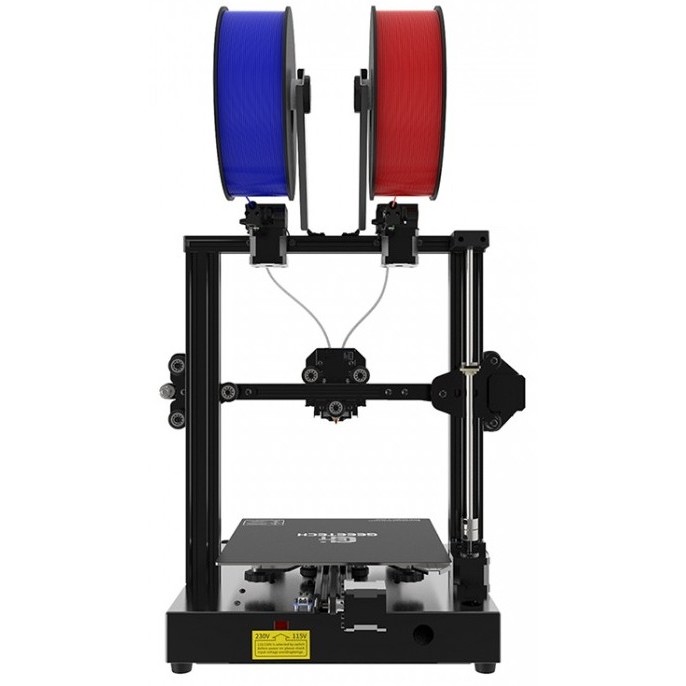
(For this year)
0-50 51-100 101-200 201-500 501-1000 1001-2000 2001-4000 4001+
Please select an option to continue
3. Indicate # of prints/month
(Next year)
0-50 51-100 101-200 201-500 501-1000 1001-2000 2001-4000 4001+
Please select an option to continue
4.
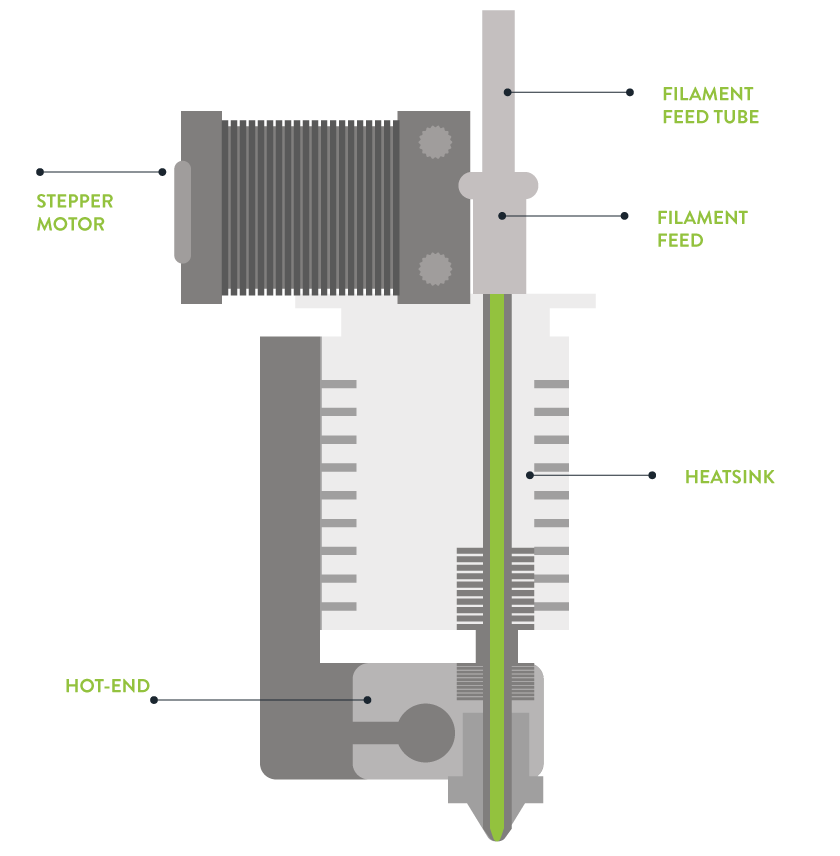
(Hours)
0-2 3-6 7-10 11-14 15-17 18-20 21+
Please select an option to continue
MATERIAL & SUPPORT
Worry-free inventory and top tier support
MANAGING MATERIAL
Smart Material Handling
With Mosaic's re-usable Material Pods, you will be notified if your material is running low and can order high quality, accessibly priced Mosaic materials directly through our materials store.
SUPPORT
Industry Leading Support
We are passionate about our customer's success. Access Mosaic's top tier support, warranty and optional Service Plans to ensure your Array is running for years to come.
Spec Sheet
Download the official spec sheet for Array
Case Studies
Explore real world applications.
3D Printing Service Bureau
Objex Unlimited: Increasing throughput to better serve customer needs
Learn how Objex Unlimited is accessing Array in order to increase their throughput, decrease cost per part, and provide a frictionless experience for their customers.
Learn moreCase Studies
Explore real world applications.
Manufacturing with Array
Athletic Knit: Digitizing and modernizing production in the athletic apparel industry
Working alongside the Mosaic Solutions team, Athletic Knit is working to implement Array into their manufacturing process to access scaled production of customized parts.
Inquire about Array
High throughput. Low Cost. Minimal downtime.
Array
Contact for pricing
Element HT – Mosaic Manufacturing
Element HT
With a hot-end temp. of up to 500°C, and a heated chamber, Element HT allows you to print high strength parts for the most demanding applications.
With an all metal gantry, and a precision motion system, Element HT was developed with manufacturing level reliability in its DNA.
Element’s 14 x 14 x 14 build volume to print with up to 8 materials in a single part including rigid, flexible, and soluble support material in your prints.
Print with industrial materials
Print high strength materials with Element HT's 500°C hot-end and 80°C heated chamber. Experience an industrial-grade printer without the industrial overhead.
8 Material, High‑temp Printing
Element HT gives you the flexibility to print with multiple materials while also allowing you to print strong, functional prints with industrial-grade materials such as:
- PEEK
- Ultem 9085
- Matrix
- Polycarbonate
Automated Filament Changing
Choose your material in Canvas, let your Element HT handle the rest. Element HT will autoload your filament to let you focus on more important things.
Heated Build Chamber
Element HT's heated build chamber gives you the ability to print with the strongest materials on the market to ensure your parts can handle any application.
Industrial Print Head
Print the highest strength materials with the lowest downtime. Designed for serviceability, Element HT's print head is able to reach 500°C to print the widest range of materials on the market.
Precision printing tolerances
Access Element HT's 14" x 14" x 14" build volume to create larger parts, or multiple small parts in a single print. Print with 20 micron layer heights and closed loop feedback system to ensure a precise output.
Spec Sheet
Download the official spec sheet for Element HT
Element HT
3D Printing Evolved.
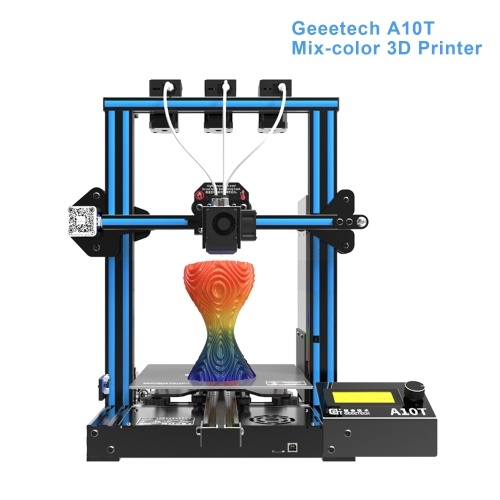
UPTIME
Maximize your printer's uptime
Designed for maximum uptime in a production environment, Element HT's modular design means you will spend less time fixing and more time printing.
MANAGEMENT
Customize, Store and Slice
Access a modern and simplified software built for multi-material 3D printing. Canvas allows you to easily create, slice, and manage your print projects on the cloud.
MATERIALS
Print with quality materials
Unlock the highest repeatability, automation and simplest experience with Mosaic's Filament, or use your favorite material brand.
Print Monitoring
Automated print monitoring
Maximize printer uptime with a system that closes the loop on the printing process. Element HT detects print anomalies and reports them to you.
Support
Industry Leading Support
We are passionate about our customer's success. With Element HT, you'll have experts on hand available to guide you and ensure you have an incredible printing experience.
Explore Element and Element HT
Element
Rockmass Technologies: Rapid prototyping and production with Element
Learn how mining technology company Rockmass Technologies is harnessing Element in order to increase the flexibility of how they use additive manufacturing technology in their prototyping and production workflows.
ReadExplore Element and Element HT
Element
Introducing Element and Element HT
Read our product overview blog to learn more about how Element is designed to give you the most flexibility with your designs, and allows you to get the most value out of 3D printing in your organization.
ReadCompare Element
Reliable, Flexible & Intuitive
Element HT
$9,999. 00 USD
Filament mixer - 3D printers
extruder color filament-production
I have seen questions (for example, what prevents us from mixing colors of 3d filaments in the extruder?) and some solutions for mixing filament colors / materials at the time of printing for multi-color printing, but my question is different: is there (available) commercially available devices, or a DIY/homebrew solution, for 2 or more 1.75mm filaments, mixing them in proportion, and pressing back 1.75mm filament for printer use?
Basically, it just needs the N extruder drives to feed at the correct proportional speed, one of the multi-inlet heaters, the 1.75mm extrusion nozzle, and the other drive pull the extruded filament at the correct speed to keep the diameter stable. But I'm curious if anyone has tried to tweak this. Another approach might be to take a tip made for 3mm filament, drill a hole in the nozzle to 1.75mm, and put 3 pieces of 1. 75mm filament into it at the same time (the size seems to match pretty closely).
My interest in this is that I mostly print small things, and even one kilogram of thread takes several months, so it's not practical to buy and store a bunch of different colors. I would also like to experiment with mixing flex PLA and plain PLA to get a material with much less plasticizer so that it is not flexible, just less brittle.
Grinding into pellets and measuring ratios is too much work to be worth it. The key part of the question is to do this directly from thread to thread.
@r .. Github Stop Helping Ice, #3
Discussion
2 Answer
▲ 0
We do our own incandescent thread
Theoretically can be done using any equipment for the production of threads , taking two threads, grinding them into granules and feeding them into the machine in the right mixture for the right color. However, industrial plants such as Filabot are heavy, large and expensive.
Luckily, there are installations for creating filaments for hobbyists. They vary in price and quality, but can give good results if you fiddle a little with them. Among the kits I've seen in the works is the Filastruder, but there are also DIY items that cost less than $200.
Pelletizing
If you are good at mechanics, you can design a feed mechanism that pushes the threads of parts at a known feed rate into the thread pellet cutter in the right quantities towards each other, creating a uniform mixture along the length of the thread.
Mixed Waste
As an alternative to homemade mix pellets in the fiber bin, crushed waste prints/support structures can be used. After grinding the material into coarse pieces with a blender, to obtain evenly small pieces of 1-2 mm in size, the material must be small enough to be fed through the hopper without problems. the blender will also take care of proper mixing and can use raw threads to mix with used .
Hot End Mixing
To mix the filaments in the heater, you will need a specialized heater with two leads into the melt zone and two extruders that push the filaments out at the same feed rate. Modification of the feed system will be extensive and will require special firmware.
Splicing threads
Another possibility would be a machine that would splice the thread in a certain way. One machine that could do this seems to be Mosaic's Palette 2, but it's worth it (April 2019year) about 600 US dollars. Another possibility would be to use a multi-material upgrade for the Prusa i3 Mk3.
However, this would result in an inhomogeneous mixture of filaments, the transition zones would change from high concentrations of material A to high concentrations of material B whenever materials are swapped. Even with very short lengths of spliced material, the mix will be inconsistent. With the help of colored threads, this can create a rainbow pattern.
, @ Trish
▲ 2
Okay, just found out that someone has demonstrated a trivial machine that does exactly what I asked for: any FDM printer.
It sounds crazy, but it works! This technique will allow you to create one-off images and color match your 3D prints.
It works by changing the filament (and color) of your filament while printing, and this results in a multi-colored filament that can be printed again to keep the color uniform.
3D Printing Filament! -Print your own multicolor filament!, with demo video.
I'm in the process of trying this and it looks promising! Filament:
measures 1.65-1.75mm in diameter and is gently fed and extruded.
The first test print:
turned out a little not too expressive, but decent, with an even mixture of colors. The mixed filaments were white flexible PLA and blue regular PLA, and the plasticizer seems to have mixed as expected too, but the print still seems brittle due to insufficient stretch. I suspect that with some tweaking of the filament flow, very good results could be obtained.
Upon further inspection, the brittleness/lack of stretch appears to be somewhat localized, so this is most likely due to the discrepancy between filament diameter/density. This is actually consistent with what I saw in the output of the filament slicer: there were +/- 45 degree areas in the helix (+ or - depending on the layer) where the gaps in the walls seemed to differ, and the additional gap filling material was printed or not printed. It could be a slicer bug, but it's most likely a bug in the model and I'd probably be better off recreating it myself in OpenSCAD...0003
, @ R.. GitHub STOP HELPING ICE
The cheapest, simplest, and most common 3D printing method is Fused Deposition Modeling (FDM). In the vast majority of cases, this method uses the direction of the polymer: the polymer in the form of a thread with a diameter of about 2 mm, wound on a spool, is fed into a small extruder, where it melts and is extruded (pressed) through the nozzle already in the form of a thin thread, from which the layers of the future part are formed.

The process of 3D printing of chemical equipment elements from chemically resistant plastic using an FDM 3D printer.
The polymer filament deposition method has an average spatial resolution (usually 0.1 - 0.2 mm) and makes it possible to manufacture parts of various shapes and levels of complexity (Fig. 1). The enormous possibilities of 3D printing make it a very promising technology in education and science. Piece-by-piece production of unique laboratory equipment, visual aids (Fig. 2), mock-ups, models (including working mechanisms with moving parts) - all this is feasible even with the widely available FDM printing method.
Fig. 1. Helical bonded channel made from two different resins in one 3D print run with two extruders running in sync. Finished products and a 3D model are shown.
Fig. 2. Ball-and-stick model of a molecule made by FDM printing from PLA plastic. To obtain a higher quality, the model was made in parts with subsequent assembly.
The high chemical resistance of some polymers (such as polypropylene, nylon, polyethylene terephthalate) in combination with the FDM printing method is well suited for the manufacture of small chemical laboratory equipment and chemical-technological laboratory installations. However, the real potential of 3D printing is not realized in the manufacture of standard laboratory equipment that can be bought, but in the creation of special products, such as chemical reactors, mixers and other elements of chemical installations, developed in-house for unique experiments.
The layering technology is mature enough to reproduce even the fine details of small chemical equipment. For example, Figure 3 shows a photograph of a mixer with three inlets and one outlet. The diameter of the internal channels of this mixer is only 2 mm. The conical notches on the inlet pipes are clearly visible, and the height of these notches is 0.5 mm. To increase the mixing efficiency, a miniature helical fin is made inside the central outlet channel. Of course, this is not yet the same thing as shoeing a flea, but everything is moving towards this. The manufacturing time of the mixer was 30 minutes. Try to make such a micro-mixer in half an hour using conventional methods!
Fig. 3. Mixer-tee in the working chamber of a 3D printer, made of polyethylene terephthalate using the FDM method.
Fig. 4. Chemical microreactor with a complex labyrinth channel inside, made of PET by FDM printing. The individual parts of the reactor and the assembly are shown.
The ability to manufacture products with a complex internal structure, as already noted, is one of the main advantages of 3D printing. This possibility is well illustrated in Figure 4, which shows a complete chemical reactor the size of a matchbox. Like the "adult" chemical reactor, this "baby" has a shell, a lid connected by bolts to the shell, and a gasket to seal the working space. It is enough to look under the lid to see the complexity of the inner world of this worker of science: a labyrinth channel is organized inside the reactor, forcing the reaction mixture entering the shell through the side pipe to move along a complex trajectory, so that the reaction time is optimal to obtain the desired products. There are small baffles at the bottom of the labyrinth channel to keep the finely dispersed catalyst from being washed out quickly. The reaction products leave the reactor through the lower branch pipe.
Microreactors can consist of any number of elements, each of which is individually manufactured using 3D printing (Fig. 5). Individual elements (Fig. 6) are eventually combined into workable chemical plants (Fig. 7).
Fig. 5. Microreactor, consisting of a shell, a lid, a catalytic cartridge and a replaceable nozzle. The individual parts of the reactor, the reactor assembly and a three-dimensional model of the assembly are shown.
Fig. 6. Mixer and zigzag microreactor made of PET.
Fig. 7. Laboratory chemical plant assembled from a microreactor and mixer, created by FDM printing methods.
3D printing can significantly speed up experimental chemical research, because it makes it possible to manufacture even complex multi-component chemical equipment right in the laboratory without significant material costs. This applies to both fundamental chemical research and chemical engineering projects. For chemical technology, 3D printing provides a truly unique opportunity to produce a series of reactors or other equipment with different design parameters in a short time to find the optimal solution.