3D printer driver board
The 6 Best 3D Printer Controller Boards in 2022 – Clever Creations
Our site is reader-supported. When you buy via the affiliate links on this site, we will receive a commission at no cost to you. All opinions remain our own. Learn more
From using Arduinos with CNC shields to now having a full-fledged WiFi-equipped circuit, 3D printer controller boards have come a long way. They’re the brains of any 3D printing setup and are responsible for controlling, coordinating, and executing all of a printer’s functions.
If you’ve bought a fully assembled 3D printer that you are happy with, it’s doubtful that you ever had to think about the controller board. But if you’re someone who wants to upgrade his 3D printer or build a DIY printer from scratch, you probably understand how important it is to select the best 3D printer controller board for your needs.
To help you with getting the best control board for your 3D printer, we’ve compiled a list of the six best motherboard options that you can buy right now.
3D Printer Controller | Summary | Input | Processor | Price | Best Offer |
---|---|---|---|---|---|
Duet 2 WiFi | Best overall | 11-25V | 32-bit | $170 | MatterHackers |
Duet 3 6HC | Best high-end | 11-32V | 32-bit | $255 | MatterHackers |
BTT SKR Mini E3 V2.0 | Best on a budget | 12/24V | 32-bit | $65 | Amazon |
Creality 3D 4.2.7 | Best for Ender 3 | 24V | 32-bit | $50 | Creality3D |
BIGTREETECH Octopus | Most stepper drivers | 4.75-36V | 32-bit | $52 | Amazon |
BIGTREETECH TFT35 V3.0 | Best LCD add-on | 5V | 32-bit | $45 | Amazon |
Best 3D Printer Motherboards in 2022
Duet 2 WiFi
Best overall
Check Price
AmazonMatterHackersE3D
The Duet 2 Wi-Fi features a 32-bit ARM-based processor specifically designed for industrial automation projects. As-is, the Duet 2 Wi-Fi can support up to five unique stepper motors. This, however, can be extended to support up to five extra stepper motors and extruders with the Duex 5 expansion board.
All stepper drivers used on the Duet 2 Wi-Fi are TMC2660s, which have a high current rating of 2.4A and are able to run the stepper motors quietly in up to 1/256 micro-stepping. The board runs on the well-documented and feature-rich RepRap firmware.
The great thing about the Duet 2 Wi-Fi is its compatibility with different Duet expansion boards and accessories. You can connect a PanelDue board to get a full-color graphic touch screen, temperature sensing daughterboards, the Duex 5 for additional steppers, servos, fans, and heaters. It even has the option to use a smart effector for delta 3D printers for bed leveling.
The many features and ability to use it with practically any 3D printer make the Duet 2 Wifi the overall best 3D printer controller board that you can get right now. It definitely costs more than your typical board, but you get what you pay for.
Standout Features
- Wi-Fi connectivity
- External stepper driver support
- Quiet 1/256 microstepping
Technical Details | |
---|---|
Input voltage | 11V - 25V |
Stepper drivers | 5x TMC 2660 |
Microstepping | Up to 256 |
Microprocessor | ARM Cortex M4F, 32-bit |
Connections | 2.4GHz WiFi, USB serial port |
SD card slot | Yes |
What We Like
- Powerful
- Many I/O ports
- Built-in Wi-Fi
Could Be Better
- High price
Find Duet 2 WiFi at
AmazonMatterHackersE3D
Duet 3 6HC
Best high-end
Check Price
AmazonMatterHackersE3D
The Duet 3 6HC is the latest release from Duet 3D. The 6HC in the name stands for 6 High Current stepper motors. The board uses a faster 300 MHz 32-bit ARM processor, allowing for high-speed calculations. The Duet 3 features six Trinamic 5160 stepper motor drivers rated at a 6.3 A peak current.
Other than this, you get 10 PWM outputs for the heated beds, extruders, and fans. It has 9 I/O ports for end-stops, Z probes, filament sensors, and other peripherals. These allow you to decorate your 3D printer with many sensors, fans, and accessories and still have room left for more.
The CAN-FD buses will let you connect other Duet boards, smart tools, and custom add-ons, thus ensuring upgradability. There’s a dedicated high-speed SPI bus to a single board computer (SBC) to let you connect SBCs like Raspberry Pi’s.
The Duet 3 6HC is expensive and aimed at professionals that require a versatile high-end 3D printer controller. However, the RepRap community’s ample amount of documentation and support means that if you want one, you can easily configure it to work with any off-the-shelf 3D printer as well.
Aside from being more than powerful enough to drive nearly any 3D printer, the Duet 3 is an equally attractive option for a home CNC machine or laser engraver.
Standout Features
- High-speed ARM processor
- High current stepper drivers
- Numerous i/o options
Technical Details | |
---|---|
Input voltage | 11V to 32V |
Stepper drivers | 6x TMC2160 or TMC5160 |
Microstepping | Up to 256 |
Microprocessor | ARM Cortex M7, 32-bit |
Connections | Ethernet and USB Serial port |
SD card slot | Yes |
What We Like
- Wide stepper motor compatibility
- Suitable for high-end 3D printers
- Lots of expansion options
Could Be Better
- High price
- Requires technical expertise
Find Duet 3 6HC at
AmazonMatterHackersE3D
BIGTREETECH SKR Mini E3 V2.
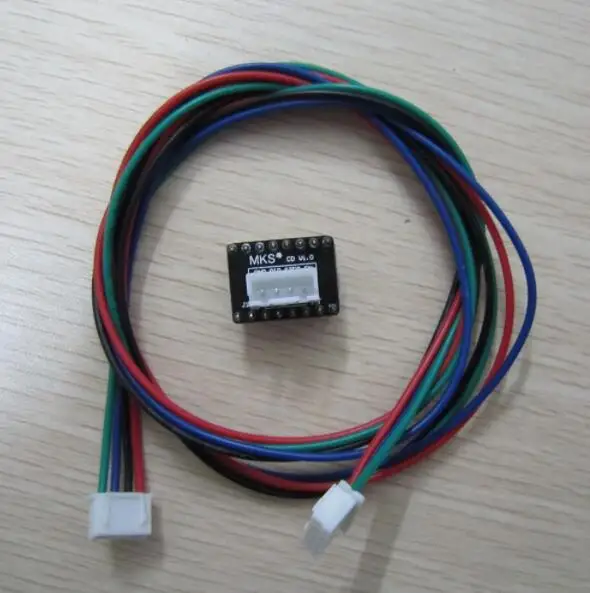
Best on a budget
Check Price
AmazonBigtreetechGeekbuying
The SKR Mini E3 V2.0 is the successor to the original E3, designed explicitly for the Ender 3 3D printers. With the SKR Mini E3 V2.0, Bigtreetech offers support for more Creality machines like the CR-10, CR-10S5, and Ender 3 3D printers.
The V2.0 is a 32-bit 3D printer controller board that features ultra-silent, TMC 2209 stepper motor drivers and can handle 2A RMS current. It also comes with two Z-axis ports, so that you can drive dual Z-axis stepper motors.
Aside from the excellent stepper drivers, the SKR Mini E3 V2.0 also comes with support for BLTouch and filament detection sensors. This gives you the option to install additional Ender 3 upgrades and Ender 5 upgrades that reduce the chance of failed 3D prints.
The Mini E3 V2.0 supports the open-source Marlin firmware. It offers a variety of additional features like the power resume function, automatic shutdown, and onboard sensorless homing functions.
If you’re on a budget and want to upgrade your Creality 3D printer, the SKR Mini E3 V2.0 is likely the best 3D printer controller for you.
Standout Features
- Parallel Z-axis interface
- BLTouch and filament detection ports
- Improved thermal performance
Technical Details | |
---|---|
Input voltage | 12/24V |
Stepper drivers | 4x TMC2209 |
Microstepping | 256 |
Microprocessor | ARM Cortex-M3, 32-bit |
Connections | Mini-USB-B type |
SD card slot | Yes |
What We Like
- Low price
- Easy to use
- Silent stepper drivers
Could Be Better
- Limited upgradability
Find BIGTREETECH SKR Mini E3 V2. 0 at
AmazonBigtreetechGeekbuying
Creality 3D 4.2.7
Best for Ender 3
Check Price
AmazonCreality3D
The Ender 3 is still one of the best budget Creality 3D printers. But it has aged in terms of its features and capabilities. The latest version of the 3D printer controller board from Creality – 4.2.7 aims to bring the Ender 3 to the current 3D printing trends.
The Creality 3D 4.2.7 controller board features a 32-bit ARM processor with increased flash storage that lets you run more firmware features faster, and with this supporting the latest Marlin 2.0 firmware. Creality calls this controller board the “silent mainboard” due to the TMC 2225 stepper motor drivers that keep your 3D printer’s motors silent.
This 4.2.7 now comes with a pre-installed bootloader, which means that you can update the firmware by merely inserting the SD card with the firmware BIN file. It also has ports for the BLTouch auto leveling sensor and filament sensors that remove the need for any previously needed extenders.
The Marlin 2.0 comes pre-installed with the board, and with a little bit of configuration, you can directly use it with your Ender 3. It is an excellent upgrade for the Ender 3 3D printers, considering that you get an officially supported board with the latest features.
Standout Features
- 32-bit processor
- Pre-installed bootloader
- Silent TMC 2225 stepper drivers
Technical Details | |
---|---|
Input voltage | 24V |
Stepper drivers | 4x TMC2225 |
Microstepping | Up to 256 |
Microprocessor | ARM Cortex-M3, 32-Bit |
Connections | Micro-USB port |
SD card slot | Yes |
What We Like
- Easy to install and use
- Official company support
- Affordable
Could Be Better
- No UART control
- Poor quality control
Find Creality 3D 4. 2.7 at
AmazonCreality3D
BIGTREETECH Octopus
Most stepper drivers
Check Price
AmazonBigtreetechGeekbuyingBanggood
The BIGTREETECH Octopus controller board natively supports eight stepper motors. You can choose your stepper motor drivers and the mode in which you want to run them, and this makes the board a beast in terms of sheer stepper motor support.
This 3D printer controller board supports up to four hot-end heaters. Then there are six PWM controllable fan interfaces, six end-stop switches, and two inputs for filament detection sensors. You even get a CAN bus interface if you decide to upgrade further and a USB-A port that can interface with a Raspberry Pi using emulated serial over USB.
Another expansive feature of the Octopus board is the support for a dual Z-axis drive. This can come in handy if you’re building a large cartesian or even a Core XY-type 3D printer. There are many other features too, and the sheer number of connectivity options make it one of the best 3d printer controllers if you’re planning to build something like a Voron 3D printer that needs many stepper motors.
Standout Features
- Supports up to 8 stepper motors
- Interfaces with Raspberry Pi
- Marlin and Klipper firmware support
Technical Details | |
---|---|
Input voltage | 4.75V - 36V |
Stepper drivers | 8 pluggable stepper driver support |
Microstepping | Up to 256 |
Microprocessor | ARM Cortex-M4, 32-bit |
Connections | USB type C port |
SD card slot | Yes |
What We Like
- Suitable for large 3D printers
- Lots of expansions ports
- USB-C interface for easy compatibility
Could Be Better
- Complex wiring
- Limited community support
Find BIGTREETECH Octopus at
AmazonBigtreetechGeekbuyingBanggood
BIGTREETECH TFT35 V3.
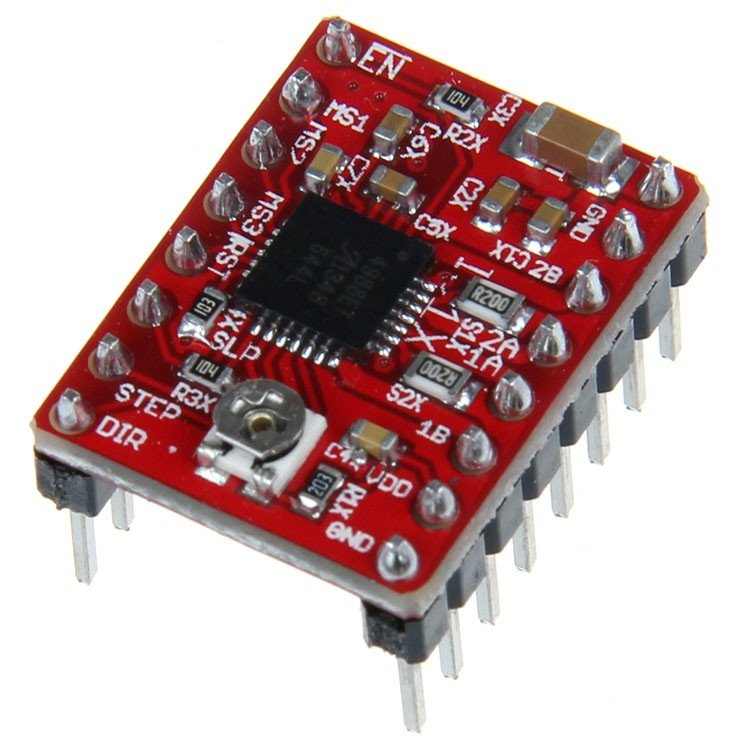
Best LCD add-on
Check Price
AmazonBigtreetechBanggood
The BIGTREETECH TFT35 V3.0 is an LCD touch screen upgrade designed for the Ender 3 and CR-10 3D printers. The V3.0 stands out because of its dual nature. You can use it as a regular LCD screen with the knob or use the touch screen to navigate the menu quickly.
It gives you the best of both worlds without the hassles of either. Additionally, you get a port for an external Wi-Fi module, a full-sized SD card slot, and a USB 2.0 port, giving you plenty of options in terms of connectivity.
However, the touch screen is not plug-n-play, and you need to tweak some firmware settings to get it working with your 3D printer. Teaching Tech on YouTube has a comprehensive guide covering everything you need to get the TFT35 working.
The BIGTREETECH TFT35 V3.0 is not meant as a completely new overhaul for your 3D printer but rather is aimed to improve the functionality of interfacing with it. The touch screen combined with the knob is suitable for many users. And considering the price, it is a worthwhile upgrade to make.
Standout Features
- Dual-mode use
- Pre-installed bootloader
- Wi-Fi module and filament detection ports
Technical Details | |
---|---|
Input voltage | 5V |
Microprocessor | ARM Cortex-M3 series 32-bit |
Connections | USB A port and external Wi-Fi module support |
SD card slot | Yes |
What We Like
- Easy to use
- Compatible with many 3D printers
- Lots of configuration options
Could Be Better
- Firmware can be buggy
- Technical expertise required
Find BIGTREETECH TFT35 V3.0 at
AmazonBigtreetechBanggood
Buyer’s Guide
Above we have listed some of the best 3D printer controller boards available. But what if you want to look for more boards? What exactly do you look for in a 3D printer motherboard, and how do you select one for yourself? Here are a few pointers that you need to keep in mind.
Firmware Compatibility
Firmware is the software on the 3D printer controller board that is responsible for all calculations and commands to the printer hardware. There are many different types available, for example, Repetier, Prusa, Klipper, and Smoothieware.
Recommended:
Creality Sonic Pad Review: A Klipper Solution That Needs More Work
Each one is designed for a slightly different purpose, and you need to keep in mind your goals with the machine. For example, if you want a high-speed 3D printer, Klipper is the best choice for you. Marlin and RepRap are the go-to options if you want well-documented and widely used firmware.
You need to consider the choice of your firmware beforehand to select the best suitable controller board for yourself. Make sure there’s enough documentation and support available with your combo so that if you run into any issues, you can quickly sort it out.
Processor
3D printers either have an 8-bit controller board or a 32-bit board. An 8-bit board is cheap to manufacture and provides all the basic functionalities you would expect from a 3D printer. However, it comes with low onboard memory, and the lower number of bits means that it can process fewer calculations at a time, thus significantly affecting its speed.
32-bit motherboards operate at a higher clock speed, have a slightly greater onboard memory, and execute calculations at a much higher rate. They’re compatible with more I/O ports and communication interfaces, and all of these translate to a more feature-rich 3D printer motherboard.
If you want a basic 3D printer with limited functionalities, 8-bit boards are an option. They’ll save a bit of money, and you won’t have to pay for things you won’t use. However, if you want your 3D printer to be future-proof, have advanced functions, and print faster, a controller board with a 32-bit processor is vastly superior.
In our list with the best 3D printer controller boards above, we have only added 32-bit controllers. We believe that an 8-bit board is not worth buying and a 32-bit board is always the better option.
Communication methods
The most basic method of communication on a 3D printer motherboard is a USB port. A USB serial port allows you to control your 3D printer via a USB connection with a computer.
Wi-Fi and Ethernet ports are other methods of communicating with your 3D printer. An ethernet port would allow you to control your 3D printer over a local wired network.
Wi-Fi connectivity would allow you to control your printer wirelessly. One benefit of Wi-Fi is that you don’t even have to be present in the same room as your 3D printer, and you can control it remotely from anywhere.
Low-end controller boards don’t come with Wi-Fi and Ethernet ports; some might have pins for attaching external Wi-Fi modules, though. A USB serial port is enough if you want a basic 3D printer. If you want wireless 3D printing or operate many 3D printers simultaneously, you should consider getting a Wi-Fi-equipped controller board.
Connectors
Aside from a USB port, there are many other connectors (or headers) on the controller board. These are used for a wide variety of purposes. Endstop connectors, hot end heaters, stepper motor connectors, bed leveling, and filament runout detection sensors are some of the few.
A well-specced-out controller board like the Duet 2 Wi-Fi or the Duet 3 6HC will have almost all of these connectors and then some more. Connectors allow you to interface various devices with your 3D printer, providing additional functionality.
The more connectors your controller board has, the more expensive it will be and take a lot of space. You need to know what features you want in your 3D printer and select the board with the particular connectors to get the maximum benefit.
Stepper Drivers
Stepper motor drivers affect the size of the stepper motors you can drive in your 3D printer and the sound levels you hear in the process. On most 3D printer controller boards, stepper drivers can’t easily be swapped out. Therefore, selecting the right kind of controller board with the right stepper driver is essential.
Basic stepper drivers like the A4988 are cheap, easily accessible, and provide a relatively good experience for basic 3D printers. They do drive stepper motors loud, are unreliable, and can only provide the steppers with limited current.
TMC drivers, on the other hand, are known for their silent operation and current-carrying capacities. The TMC 2xxx series are rated at 2A peak current, while the TMC 5160 typically offers 3A to 4.4A on 3D printer controller boards.
You need to consider the microstepping capabilities of the stepper motor drivers as well. Microstepping divides a full step into smaller steps. The smaller the step, the higher the resolution and the smoother the vibration. As a minimum, you want 1/16 step microstepping, but the best 3D printer controller options offer up to 1/256 step
Touch screen support
A touch screen enhances the functionality and ease of use of a 3D printer by making navigating the menu and dialing in the various features easier.
Not all controller boards have touch screen support built-in. While choosing a controller board, look at the connectivity options and the compatible touch screens. You need to make sure that the board’s firmware supports it, and there is at least a little bit of documentation on how to interface the controller with the touch screen.
FAQ
What is a 3D printer controller board?
A 3D printer controller board is a piece of hardware that controls all electronic components in a 3D printer. It is responsible for motion, temperature control, and reading all commands from GCode files.
Why upgrade your printer’s stock controller board?
As time passes, the current features in your 3D printer start to seem obsolete. A controller board upgrade will give you access to many advanced features, allow for added functionalities and enhance your overall 3D printing experience.
Is a 3D printer controller board the same as a 3D printer motherboard?
Yes, in the context of 3D printing, the terms ‘controller board’ and ‘motherboard’ are used interchangeably. They mean exactly the same thing.
Conclusion
The best 3D printer controller boards are the ones you’re able to afford and will work with your 3D printer. With so many options on the market, it can be tough to choose just one. The important thing is figuring out which one of these top-rated controllers would be right for you.
In our opinion, the Duet 2 Wi-Fi is the overall best 3D printer controller board that you can get right now. Despite its high price, the Duet 2 Wi-Fi ticks all the boxes in terms of features, connectivity, upgrades, and ports. It is designed to be a universal solution for all types of 3D printers and can serve as an effective replacement for practically any board.
Let us know what you think about it, and if you have anything else to add, feel free to comment below.
Scroll to Top
6 Best 3D Printer Controller Boards In 2022
- Last Updated: October 19, 2022
- Jackson O'Connell
The controller board on a 3D printer is arguably the most important part of a machine. Just like you can’t function without a brain, a 3D printer can’t function without this integral circuit board.
The controller board, sometimes known as a motherboard or mainboard, is responsible for processing and carrying out all of the commands sent to the machine. Without it, your 3D printer is just a bunch of motors, sensors, and probes, sitting on a metal frame, doing absolutely nothing.
The controller board varies from printer to printer (often based on brand), and some are better than others for reasons we’ll explain later. Luckily, you can usually replace the board on your printer to improve printing performance, usability, or other factors.
In the sections below, we’ll explain more about 3D printer motherboards and how they vary. We’ll then dive into our review of some of the best controller boards on the market that you can use on your machine.
Enjoy!
BTT SKR Pro V1.2
Check Latest Price
BTT SKR Mini E3 V2. 0
Check Latest Price
Duet 2 Wi-Fi V1.04
Check Latest Price
Table of Contents
- Best 3D Printer Controller Boards At A Glance
- What Is A 3D Printer Controller Board?
- Why Change Your 3D Printer’s Board?
- What To Consider When Buying a Controller Board?
- Processor
- Number of Ports
- Compatibility
- Stepper Drivers
- Quality
- Price
- Best 3D Printer Controller Boards
- 1. BTT SKR Mini E3 V2.0 (Best Overall)
- 2. Duet 2 Wi-Fi V1.04 (Best Premium Choice)
- 3. BTT SKR Pro V1.2 (Best Value)
- 4. Creality V4.2.7
- 5. MKS Robin E3D
- 6. Smoothieboard (V1)
- Conclusion
Best 3D Printer Controller Boards At A Glance
1. BTT SKR Mini E3 V2.0 (Best Overall)
2. Duet 2 Wi-Fi V1.04 (Premium Choice)
3. BTT SKR Pro V1.2 (Best Value)
4. Creality V4.2.7
5. MKS Robin E3D
6. Smoothieboard (V1)
What Is A 3D Printer Controller Board?
A 3D printer controller board is a type of microcontroller meant for a 3D printer. As a microcontroller, the board’s sole purpose is processing commands, known as G-code for 3D printers, and following them.
Every electronic component – motors, sensors, probes, etc. – is wired to the different ports on the board. When the processing chip on the motherboard reads a G-code command, it gives power to the specific motor ports to carry out the command. And, when data needs to be used, it takes it from the sensor ports, like an automatic bed leveling sensor if your printer has one.
The board is also where the firmware program is running. If you’re unfamiliar with the term, firmware helps bridge the digital and physical realms of 3D printing by giving the controller board a way to decode the G-code commands so it can carry them out. Firmware also contains certain features and capabilities like linear advance and meshes for automatic bed leveling.
3D printer controller boards also have something called stepper motor drivers. These components of the board are responsible for the rotation of the motors connected to the board. Stepper motor drivers directly impact the noise level produced by the motors as well as their accuracy and precision.
Some boards have integrated stepper motor drivers, which means they can’t be changed and are built into the board. However, other, more customizable boards, have stepper motor driver ports that allow you to use your own drivers.
But most of this explanation isn’t what you’ll be needing in your day-to-day 3D printing activities. The main thing you need to know about a controller board is that it has different ports to support different hardware, and each controller board is different.
Why Change Your 3D Printer’s Board?
Source: Youtube Design Prototype TestSo, why change your 3D printer’s controller board?
Well, as we said, each board is different, and some are better than others, offering enhanced features. This might mean more ports, a faster processor chip, or support for different firmware programs, which can all directly or indirectly improve the printing and usability of your machine.
Perhaps the most common reason to switchboards is to enable a certain upgrade that requires an extra port. This includes adding a second Z-axis stepper motor or an automatic bed leveling sensor.
Another reason is for a better processor chip to get better prints. For example, motherboards that have a 32-bit processor architecture are known to yield smoother prints compared to 8-bit boards.
Yet another example is to get a quieter printing experience by switching to a motherboard with newer stepper motor drivers than your old board. Check out our review of the best quiet 3D printers here.
What To Consider When Buying a Controller Board?
3D printer controlled boards are pretty complex, with many different features onboard. As such, there are quite a few considerations to keep in mind when looking for a controller board for your machine.
In this section, we’ve gone over what we considered when picking out the best controller boards for this list.
Processor
Our first consideration was the processor on the controller boards. In the early days of 3D printing, the typical motherboard had an 8-bit microprocessor, but, now a 32-bit processor is the new standard. All of our selections have a 32-bit architecture as we wanted to make sure they can all handle the latest firmware features, like linear advance.
Number of Ports
The second consideration is the number of ports, including both motor and sensor ports. All of the controller boards on this list feature the necessary four (X, Y, Z, E) motor ports, but some go above and beyond with extra stepper motor ports to allow for more upgrades.
As for the sensor ports, each of the included controller boards has a sensor port for an automatic bed leveling sensor, and many have ports for a filament runout sensor as well.
Compatibility
Our third consideration was the popularity and compatibility of the controller boards. While a board can be unpopular and a good option, typically, the more popular a 3D printer controller board is, the more firmware programs support the board. We made sure at least a few different firmware programs could run on each of the included controller boards.
Stepper Drivers
Fourth, the stepper motor drivers were another thing we kept in mind when looking at the controller boards. If the board had integrated drivers, we made sure they were at least decently quiet. And, if the board had open driver ports, we made sure they supported some of the more recent TMC drivers as these types of drivers are most popular.
Quality
Fifth, the manufacturer of the product also matters, and we didn’t forget about it. A quick search on AliExpress will bring up many 3D printer boards that seem good on paper, but, when they arrive, they perform poorly. We made sure each of the controller boards we’re calling the “best” come from the best and most reputable manufacturers around.
Lastly, we reviewed the price of each of the listed products to make sure they all were in reach for the average hobbyist. We can’t be comparing $2,000 boards to $50 boards cuz’ that wouldn’t make sense.
Best 3D Printer Controller Boards
Now that we’ve gone over what a 3D printer controller board is, it’s time to get into the options. We’ve scoured the market and handpicked the best boards for you, reviewing each in the sections below.
1. BTT SKR Mini E3 V2.0 (Best Overall)First up, the BTT SKR Mini E3 V2.0 is a very powerful 3D printer motherboard developed by the experts at BigTreeTech (BTT). Hence its name, the SKR Mini, has a pretty small footprint and can fit in consumer-grade printers like the Ender 3.
What’s most appealing about the board, however, isn’t its size but rather its 32-bit architecture.
Moreover, the board has a powerful processor chip that runs an astounding 72-MHz, which is much faster than almost any stock board on consumer 3D printers. This will allow you to run larger and more feature-heavy firmware programs like Marlin 2.0 for your machine.
If that doesn’t get you excited, the board also provides five stepper motor ports and even a port dedicated to an automatic bed leveling sensor. This will allow you to make upgrades to your printer, like dual Z-axis motors and auto bed leveling, without having to ask, “Can my motherboard handle this?”.
Additionally, the device features onboard TMC2209 stepper motor drivers. While the 2209s aren’t the latest drivers in the game, they will provide a decently-quiet printing experience, not counting for the noise from the fans.
On this note, the Mini E3 also has three fan ports, which certainly isn’t a lot but is standard for today’s boards. A few other features of this board is a micro-USB connector, a micro-SD card slot for printing storage, and support for a touchscreen LCD.
- 5 stepper motor ports, automatic bed leveling sensor port
- 32-bit architecture and 72-MHz processor chip
- Support for touchscreen LCD and large firmware packages
- Micro-USB and micro-SD card connectivity options
- TMC2209 stepper motor drivers built-in
- Only three fan ports
- The stepper motor drivers are somewhat old
Check Latest Price
2.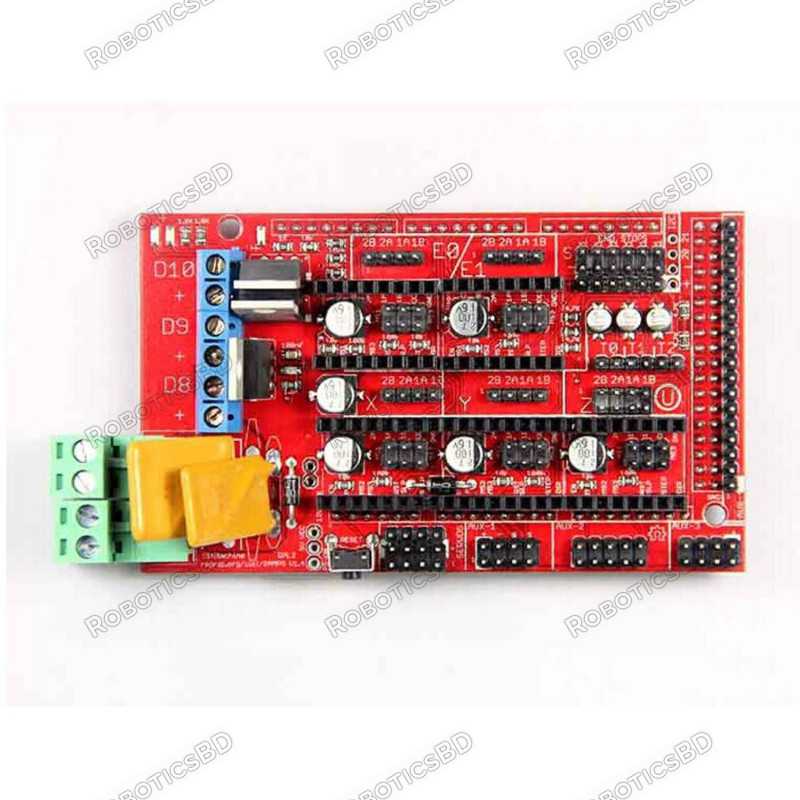
Duet3D is on the pricier side of the consumer 3D printing market but they still make the cut.
Their Duet 2 Wi-Fi V1.04 board is a great option, especially for DIY 3D printers where the hardware isn’t made by just one manufacturer. That’s because the board is completely open-source, so you can use basically any motors, sensors, or other electronic attachments and, with some configuration, get them to work with the board.
As indicated by the name of this product, the Duet 2 Wi-Fi has an onboard Wi-Fi module that allows you to control your printer remotely. This means you can use Duet3D’s default online interface to start/stop prints, send G-code commands, set temperatures, and more.
It’s like an OctoPrint server built into the board!
And, when it comes to ports, the Duet 2 has got you covered with five motor ports to allow for an extra Z-axis motor. There are also plenty of other ports to allow for a Duet3D-developed PanelDue touchscreen LCD, two hot ends, a heated bed, and five endstops. And don’t forget about your automatic bed leveling sensor (e.g. BLTouch) or filament runout sensor because those can also both fit on this board.
And, in the unlikely scenario that you are still a few ports short, you can purchase Duet3D’s expansion board, which connects to the Duet 2 Wi-Fi and provides a few more motor and sensor ports.
As for the processor, it just makes sense that Duet3D used a powerful 32-bit chip on this monster of a board.
The drivers on the board are also exceptional and Duet3D opted for TMC2660 stepper drivers, which are some of the latest in the game. On top of keeping your printer quieter than quiet, these high-quality drivers allow for 256 microstepping. This feature ensures a super high level of accuracy and precision in stepper motor movements, improving the quality of prints.
Besides the close to $200 price tag, another major downside of this board is its massive size, which comes with offering the number of ports it does. The Duet 2 Wi-Fi isn’t a board that will fit into your Ender 3, Anycubic Mega, or really any other consumer-grade 3D printer. You’ll have to make a custom fitting (many 3D printable options online) to fit the board on your printer.
- Built-in WiFi support and an online control interface
- Many motor ports for more upgrades
- Many sensor and attachment ports to support ABL and runout sensors
- TMC2660 stepper drivers and 256 microstepping
- 32-bit processing
- Optional expansion port board
- Very large; hard to fit on a regular 3D printer
- Very expensive
- Duet3D makes it difficult to run certain firmware programs (e.
g. Marlin)
- Only a few LCDs are supported by the board
Check Latest Price
3. BTT SKR Pro V1.2 (Best Value)Another board from BigTreeTech is the BTT SKR Pro V1.2. The board is called “Pro” because it has more features and better features than most of BTT’s other boards. Unlike the Duet 2 Wi-Fi, though, this board is a normal size and can fit in most printers like the Ender 3.
But don’t be misled by the pretty regular size of the board as the SKR Pro V1.2 is far from normal. Boasting seven motor ports, the Pro V1.2 is a great option for dual-extrusion printers, where you need two extruder motors and two X-axis stepper motors. Alternatively, you can use the extra motor ports to have dual Z-axis motors to improve the quality of your prints.
Surprisingly, despite having seven motor ports, the Pro V1. 2 only has six driver ports for the stepper motors. That’s because one of the drivers is meant to run both of the motors in the Z-axis motor ports.
On this note about the drivers, the Pro V1.2 has open stepper motor driver ports, meaning you can fit whatever compatible stepper drivers you want. While this means the price of the board (which isn’t too much) isn’t the full price because you have to buy drivers, this allows you to choose what drivers you want based on how quiet and accurate you need your stepper motors to be.
Overall, the SKR Pro V1.2 is the board to get if customization is your middle name. Moreover, the board supports a lot of different drivers, firmware programs, and LCDs. The many ports on the board allow for basically whatever upgrade you want.
- Open-ended stepper drivers
- Wide support for firmware programs, LCDs, stepper drivers
- Seven motor ports
- 32-bit processor
- Wi-Fi module
- Small footprint
- Somewhat expensive
- Cable management can be difficult
- You have to buy the drivers separately
Check Latest Price
4.
Creality is one of the largest names in the consumer 3D printing industry, with tens of the most popular printers on the market under its belt. Creality also makes a fair amount of optional upgrades for their printers, like the Creality V4.2.7 board.
The V4.2.7 was originally developed as a “silent” board for Creality’s Ender 3 V2, but it can be used on whatever printer you want as long as the parts are compatible.
As an Ender 3 enthusiast myself, I can honestly tell you that this board has improved my printing experience a lot.
First off, the 32-bit processor and decently-large EEPROM (storage space) on the V4.2.7 allow you to run feature-heavy firmware programs like Marlin 2.0. The board also has a built-in bootloader that allows you to flash new firmware programs through the micro-SD card slot.
But, in my opinion, the most beneficial part of the V4.2.7, is its integrated TMC2225 drivers.
The drivers quiet your printer so much to where you can really only hear the light humming of the fans. While these drivers can only reach 32 microstepping, which isn’t as accurate as some of the later TMC drivers, it’s still good enough to make parts very accurate.
It’s also worth mentioning that the board is pretty small and can fit in many consumer-grade printers like all Creality printers as well as some non-Creality machines too. Sadly, the board only has four motor ports, so you can’t run two extruders or two Z-axis motors.
However, this 32-bit 3D printer board has specific ports for an automatic bed leveling sensor and a filament runout sensor, making installing those upgrades super easy.
- TMC2225 drivers for very quiet printing
- Small size; fits in most Creality printers
- Firmware flashing is possible through the micro-SD card slot
- Not too expensive
- 32-bit processor
- Ports for an ABL sensor and a filament runout sensor
- Microstepping capabilities aren’t super good
- Only four motor ports
Get Discount (Official Store)
Check Latest Price
5.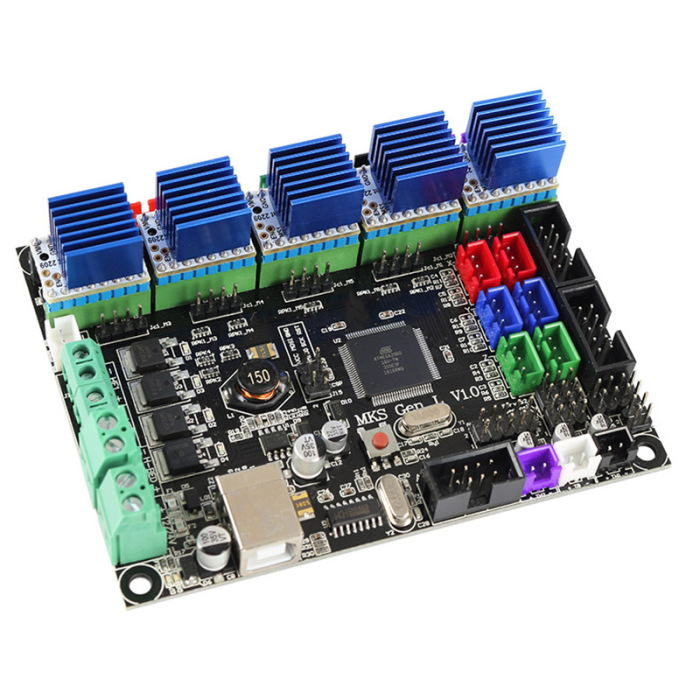
Our last board comes from the experts at Makerbase, who make the MKS line of motherboards for 3D printers. The MKS Robin E3D isn’t the most popular board from Makerbase, but I think it’s very underrated and deserves a lot more credit for what it offers.
First off, the board has six motor ports to allow for both dual Z-axis motor and single-headed dual extrusion. Alternatively, you could build an independent dual-extrusion printer with the same number of motor ports.
However, this isn’t the only good part about the Robin E3D, and I think the open-ended stepper motor driver ports are another one of its main benefits. While the market seems to dislike the open-ended driver boards, they allow you to basically control the price of the machine because drivers make up a large part of the cost for most boards.
The E3D supports many different drivers, and you can put some TMC2209s on the board to achieve low noise and also have the option to run linear advance if you’re using Marlin firmware.
On a note about firmware, you should be able to change your board’s firmware through the micro-SD card slot, and most firmware programs are compatible (e.g. Marlin).
The board also supports many sensors, like ABL and filament runout ones. You can also connect a touchscreen LCD to the board and use Makerbase’s default TFT interface to control your printer through the screen.
The board is just a bit bigger than the default boards found on most consumer printers like the Anycubic Mega and Ender 3, so upgrading will require a fitted mount. However, it won’t be too hard as there are some 3D printable models online that work.
- Open-ended stepper drivers
- Small footprint
- Supports many sensors and attachments, like ABL, filament runout, and TFT screens
- Supports many different firmware programs
- Six ports for stepper motors
- Requires modifications to fit in most printers
- You have to buy your own stepper drivers
Check Latest Price
6.
While not as popular as the mass-manufacturing companies like BTT, MKS, and Creality, Smoothieware sure knows how to make a good motherboard. Smoothieware’s v1 Smoothieboard is the company’s flagship product and it launched on Kickstarter a few years ago, passing its target goal by about $100,000.
Perhaps the main reason this board is so revered is that it’s basically the only one ever made by an organization that develops 3D printer firmware. As such, the Smoothieboard v1 is optimized to run Smoothieware, which is the name of the firmware program that Smoothieware makes.
Yeah, it’s very confusing to talk about!
While the board is usually unavailable due to its lack of popularity, it doesn’t really need to be super popular when it has a native firmware program that it’s optimized for. But still, the board has a decent amount of other features too, like its 32-bit ARM processor which handles the rather-large Smoothieware firmware package.
The board comes in a few variations, like the 3X, 4X, and 5X, which have 3, 4, and 5 motor ports, respectively. While this isn’t too many motors, the 4X and 5X versions should be great for your printer and you might be able to use the 3X for a different type of CNC-style machine.
- Optimized to run Smoothieware
- 6 endstop ports and 6 other ports for fans, heaters, and more
- Ethernet port for internet connection
- Powerful 32-bit ARM processor
- Unavailable on many sites
- Relatively expensive
- Doesn’t have too many motor ports
- Pretty old integrated stepper motor drivers (Allegro A5984, 32 microstepping)
- Doesn’t run other firmware programs
Check Latest Price
Conclusion
Just like you wouldn’t want to have an outdated brain, you don’t want to use an outdated motherboard on your 3D printer. And, while you can’t easily replace your brain, upgrading your controller board isn’t too difficult.
There are many different controller boards on the market today, and each has different stepper drivers, processors, motor ports, sensor ports, attachment ports, and firmware support. As such, the best 3D printer controller board for you depends on what features you plan on using or upgrades you plan on making.
If you just want to make the switch from an 8-bit to a 32-bit microcontroller board, but don’t plan on making too many upgrades, I would suggest going with the Creality V4.2.7. This board has a great 32-bit chip, can handle the latest firmware programs, and has a few extra sensor ports, but is nothing fancy.
Now, if you want to go all out and make as many upgrades as possible, the Duet 2 Wi-Fi is more up your alley. The many ports on the board, combined with the optional expansion board and onboard Wi-Fi module, make it a great option for those looking to explore the upgrade capabilities of their machine.
Driver for 3D printer
For the correct operation of any 3D printer, you need a special device that will be responsible for controlling the stepper motor. Incorrect installation or malfunction will result in printing problems or damage to the printer itself.
What is a 3D printer driver?
The 3D printer driver is a device whose main function is to control the kinetic movement of the printer's stepper motors. The driver sends commands to the microcontroller that describe the movement of the shaft - the number of steps and direction, at the output receiving a sequence of signals specified in a certain way for the motor winding. The driver in this process is responsible for converting one signal to another.
Manufacturers offer many models of 3D printing drivers that vary greatly in quality. Top models are able to maintain high output currents while maintaining an acceptable operating temperature, and are able to control the motor so that it does not make excessive noise, does not overheat, and the print head moves smoothly, without jerks and accelerations.
Drivers are used everywhere where stepper motors are used: in all CNC machines, actuators, 3D printers, laser engravers, etc.
Modern 3D printers use kinematics and a control method, which consists in the sequential transmission of the coordinates specified for the movement of the hotend. Methods is the generally accepted standard for controlling all devices equipped with a CNC unit. Data transfer is carried out in a specially developed programming language called G-code.
Control boards and drivers are responsible for the physical movement according to the given code.
Boards, in turn, are divided into two types based on their capacity:
- 8-bit.
- 32-bit.
The first 3D printers were designed using the self-replicating mechanism used to quickly reproduce REPRAP prototypes and were based on one of the most common boards used in robotics, the Arduino. To develop the firmware of devices in these cases, a special environment was used - the Arduino IDE. In the future, in order to expand its capabilities, the RAMPS expansion board was additionally developed, which allows you to effectively control the rotation of stepper motors and take into account the zero position using limit switches.
Additionally, drivers were developed to control stepper motors that could be combined with these boards (Pololu drivers).
To date, the installation of such a driver is required for each stepper motor of a printing device controlled by the Arduino + RAMPS bundle. RAMPS is able to work effectively when connected to up to five stepper motors.
Other All-in-one boards are equipped with special pads for Pololu drivers, which are widely used among users.
Many drivers have been developed that are compatible with the boards used in modern 3D printers. The most popular include:
- Driver A4988. The manufacturer produces the device in green and red colors, the maximum divider step is 1/16.
- There are purple and blue devices on the market.
The main drawback of the model is the lack of a well-thought-out hold mode, which causes the device to get very hot. Such a chip is recommended to be installed only in conjunction with a powerful heatsink that can compensate for excessive heating. The maximum divider step is 1/32.
- The original driver is made in Germany and the USA, but it is easy to buy a similar one made in China on the market. Copies differ from the original only in the accompanying piping - resistors, capacitors, etc., therefore, when using non-original devices, it may be difficult to select the voltage to power stepper motors. The device is characterized by quiet operation, background noise and engine sounds are minimized by manufacturers. The driver is equipped with its own chip, which is able to interpolate a 1/16 divisor to 1/256 without creating additional load on the processor.
- Made in China by Makerbase. A distinctive feature of the driver is the wide possibility of adjusting the microstep divider - from full to 1/128.
There is no internal share in this driver model. The device is intended for installation on 32-bit boards only.
- Manufactured by Panucatt Devices. The driver is able to support microstepping from full to 1/32 and has well-thought-out protection against excessive voltage and high temperatures. Two model options are available: in the standard version, the voltage adjustment pin pad is shorted, so voltage adjustment can be made by the user in a manual setting format using a screwdriver and a multimeter. In the version with digital adjustment, debugging is performed at the software level and can only be supported by its own controllers - Azteeg X3, X3 PRO and X5 mini V3.
- This model is also manufactured by Panucatt Devices. The driver is equipped with a sensor that protects it from overheating and high voltage and also comes in two versions - standard and digital. The device is based on the THB6128 chip. Designed for installation on eight-bit boards.
- A new version of the driver from Trinamic and Watterott.
A special board via the UART interface is responsible for dividing the microstep. The built-in board allows you to connect the driver to a computer using a USB cable and configure it using your own software.
Installing and configuring the driver for the 3D printer
For the correct operation of the 3D printer, before starting it for the first time, it is necessary to install and configure the drivers.
IMPORTANT! Before debugging, it is recommended to temporarily disable the anti-virus programs installed on the computer. This will help to avoid false triggering on files downloaded from external devices or the Internet.
The installation process takes place in several stages:
- Start the installation by downloading the driver file and running it. To do this, you will need to log in with an administrator account and run a file called "exe file". Next, following the instructions of the installer, complete the process and connect the 3D printer to your computer using a USB cable.
The program will automatically find the device and assign it a COM port.
- Next, you need to download and install a program called Repetier Host. Once the download is complete, launch the program file and wait for the download to complete. After the installation is completed, along with the program, all the necessary accompanying programs will be launched, including slicer programs. During installation, it is recommended to uncheck the box next to the item about installing the Server utility, since it will not be required for further work and will take up device resources unreasonably.
- The next step is setting up the settings for the personal computer. During this, a corrected interface in Russian will also be configured, the necessary scripts and an active link to the help section. At this point, the Magnum 3D and Magnum 3D Vase slicing profiles will be rewritten, so any changes made by the user should be renamed before starting the process. Otherwise, they will not be saved after reinstalling the program.
- After the installation is completed and the settings are set, you should run the Repetier-Host program and select the COM port to which the printer was connected. This step is mandatory because the installer automatically assigns COM3 to the device, which can interfere with further debugging.
- Next, following the instructions of the program, you need to update the downloaded scripts and restart the computer.
- During the reboot, you will need to press the F8 button and select the "Disable Driver Enforcement Signing" option.
- After downloading, you will need to do the following: open the Start menu, open the Settings tab, go to the Update and Security section and select Recovery. Then, going to the tab "Special boot options", you must select the item "Restart now".
- When the process is completed (the reboot should go through in normal mode), you should open the "Diagnostics" tab, go to the "Advanced Options" section, select the "Boot Options" item and restart the computer again.
When the device reboots, a menu will appear on the screen with a choice of parameters that will be used by the system in the future.
IMPORTANT! In order to install an unsigned driver, you must disable automatic digital signature verification by selecting the appropriate item in the menu and pressing the F7 button.
There is an alternative method for installing the driver for 3D printers. It is used if the system to which you plan to connect is 64-bit. In this case, the instructions above will not work.
In this case, when connecting the CNC device to the computer for the first time, for an unrecognized USB Serial device, you must select the driver yourself by opening the Modems section and selecting Compaq, and then Ricochet Wireless USB Modem devices.
Errors and how to avoid them
During the driver installation process, some errors may occur that prevent the process from completing.
The most common reasons for their occurrence include:
- Technical malfunction of the device.
Even if the driver is detected by the system when connected to a computer, if it malfunctions, the installation will not be able to proceed correctly.
- Faulty installation program. The installer may have been corrupted during download or may have been infected with malicious code. The cause of errors may also be the absence of one or more files in the archive.
- The driver version does not match the installed device. Most often, such a problem is encountered by those users who install a driver downloaded from third-party sites, and not the one that came with the device when purchased. The error may be caused by the fact that the driver version does not match the specific device or operating system version installed on the computer.
- An attempt to install a new driver over the previously installed one will also cause an error. To fix the error, uninstall the old version of the program, and then start the installation again with a new file.
- The user is trying to install unlicensed software.
If the downloaded driver does not have a special certificate that allows the operating system to recognize it, then the computer, when trying to install it, will give a corresponding error when the file is first launched.
Correct operation of a 3D printer is impossible without installing drivers - devices responsible for the movements of stepper motors. Their market for 3D printing is huge, so each user can choose the device that suits him.
- March 14, 2021
- 1993
Get expert advice
3D printing for the newest. From A to Z. Steppers, drivers and some magnetic field.
In continuation of the previous post for novice users of 3D printers.
This time I will talk about control boards, common drivers for stepper motors and a little theory about their work. Unfortunately, the post has a limit - 65535 characters, and I no longer fit into them to describe the common control boards in more detail, so they will be in the next post, just like the analysis of firmware, positive aspects and disadvantages.
Existing 3D printers have grown out of large machines, from which they borrowed kinematics and a control method, which consists in sequentially transmitting coordinates to move the hot end. This peculiar method is the generally accepted standard for the control of CNC (Computer Numerical Control) machine tools. This programming language is called G-code. The language is peculiar, and there is no need to learn it, the translation of the model from a graphical view into machine code for moving the hot end along the axes and feeding plastic is carried out in slicer programs. I will describe them a little later, but for now I want to return to the physical part of the printers and consider what can be used to correctly turn stepper motors and get a finished model.
1. Control boards and how they operate.
For a simplified understanding of the board, it is worth dividing it into 2 categories according to their capacity. There are 8-bit and 32-bit. The first 3D printers based on REPRAP ( Replicating Rapid Prototyper - a self-replicating mechanism for rapid prototyping) were based on a common robotics board aimed at non-professional users - Arduino. To create the firmware, we use our own free development environment - the Arduino IDE.
Arduino and Arduino-compatible boards are designed to be expandable as needed by adding new components to the device. As the most powerful, the Arduino Mega 2560 board with an 8-bit processor was taken.
To expand its capabilities, that is, control the heating of a hot table (Heat bed), hot end (Hot end), control the rotation of stepper motors, take into account the zero position using limit switches and other things, an expansion board RAMPS (RepRap Arduino Mega Pololu Shield) was developed .
Also, drivers compatible with this board (Pololu drivers) were developed to control stepper motors.
Which are inserted into the slots on the board. That is, for each stepper motor connected to the Arduino + RAMPS bundle, a driver is needed. RAMPS supports up to 5 stepper motors.
To control a stepper motor, it is necessary to adjust the motor supply voltage with a trimmer resistor. The setting is made with a multimeter in the DC voltage measurement mode. One probe touches the ground (the extreme contact on the driver labeled GND or the negative wire from the power supply), while the other touches the tuning resistor.
Next, you need to calculate the required voltage using the formula, based on the current for which the motor is designed.
Vref - voltage measurement pin for setting the current according to the formula.
Current Limit - stepper motor current.
Vref formula for A4988 varies from value of current sense resistors. These are the two black rectangles on the driver board. Usually signed R050 or R100.
Vref = Current Limit * 8 * (RS)
RS = 0.100
Vref = Current Limit * 8 * 0.100 = Current Limit / 1.25
RS = 0.050
Vref = Current Limit * 8 * 0.050 = Current Limit / 2.5
For example for 17HS4401 : : 6 \u003d 1.7 / 2.5 \u003d 0.68V
And by rotating the resistor we achieve this figure on the multimeter display. An important addition, in order to adjust the voltage, you must turn off the printer, and turn it on to measure.
Formulas for other types of drivers can be found in this article.
Other All-in-one boards (all on one board, without such layered designs) have similar pads under the already common Pololu drivers.
Also, to select the operating mode of the stepper motor, jumpers are made between the pads for installing stepper motors, by closing which we select one or another operating mode.
There are only 5 operating modes for the stepper motor with A4988 drivers: full step, 1/2 step, 1/4 step, 1/8 step and 1/16.
Jumpers total 3: MS0, MS1, MS2. Low - no jumper, high - installed.
It turns out that when there is not a single jumper, the motor rotates without dividing the step into microsteps, and when all 3 are installed - by 1/16.
The splitting of a step into microsteps is done for the sole purpose of increasing the accuracy of movement. That is, using a 1/4 step split, we will not be able to stop in the middle between 2 and 3 microsteps. At 1/16 this is possible.
There are many drivers available that are compatible with boards used in 3D printers. Small list:
1 ) A4988.
Available in green or red.
Maximum divisor 1/16.
2 ) DRV8825.
Available in both purple and blue. Due to the lack of a normal hold mode (in a static position, but with the rotor fixed, this mode usually consumes less energy than rotation) gets very hot. Therefore, it is recommended to install a good heatsink on the chip.
Maximum divisor 1/32.
3 ) TMC2100.
There is both the original, available in stores in Germany and the US, and many Chinese copies.
The chip is the same, made in Germany, but the binding (resistors, capacitors ...) each Chinese sculpts in his own way, so it becomes difficult to select the voltage to power the stepper motor. This driver is positioned as quiet, in which the noise and squeak of engines is minimized.
Noise comparison between A4988 and TMC2100.
But as expected, something must be sacrificed in return. It gets very hot, and when overheated, skipping steps begin and movements along the axes may be incorrect.
For the first time, the cube became a snot caterpillar for me.
As a result, you need good cooling (some Chinese neglect metallization to remove heat, since the chip is located 'on the belly') and very precise voltage regulation. There are also small tricks - it seems to have fine-tuned it, it prints small details for a month without congresses, and you put the detail for a day or two, and somewhere at the end of the print you will get a 0.5 mm microcongress.
The driver has its own chip that interpolates the 1/16 divider to 1/256 with no load on the processor, and ensures very quiet operation.
4 ) LV8729
The most common driver is made by the Chinese company Makerbase (MKS).
Drivers feature a wide range of microstep divider adjustments. From full to 1/128. There is no internal divider, like the TMS2100.
Use with 1/64 and 1/128 with 8-bit electronics (based on AtMega 2560) is not recommended, as it requires a lot of CPU resources. Designed for installation in 32-bit boards.
5 ) SD5984.
Panucatt Devices drivers. Sold only there, the Chinese do not make such. They also support step splitting from full to 1/32. There is protection against high current and overheating. As you noticed in the photo, there are 2 'extra' pins - the drivers support voltage regulation from the outside, that is, in the firmware of the board. Which makes it very convenient to control and adjust the voltage.
Available in 2 versions:
1) Standard version. The platform for voltage adjustment pins is shorted, and voltage adjustment is possible as in all other drivers - by hand, in the sense of a screwdriver and a multimeter. Supported by all boards.
2) Digital adjustment. Pins are available and adjustment is done programmatically. Supported only by native controllers: Azteeg X3, X3 PRO and X5 mini V3.
6 ) SD6128
Drivers also manufactured by Panucatt Devices.
Unlike the SD6128, they have a step split up to 1/256. Also, there is protection against overheating and high current. Similarly, it is present in 2 versions: with manual voltage adjustment, and with support for software adjustment. Software adjustment is only available for Azteeg X3, X3 PRO and X5 mini V3 boards.
The driver is based on the THB6128 chip. The driver works in both 3.3V (32-bit boards) and 5V (8-bit boards). The divider is installed in the same way, with jumpers, in accordance with the table from the pdf description.
For installation in 8-bit boards, it is not recommended to use dividers higher than 1/64 due to possible processor overload.
7 ) SD8825.
Panucatt Devices' own version, similar to the usual DRV8825, with the only difference that there are 2 pins for voltage control on the driver. Adjustment is available only on boards of our own production: Azteeg X3, X3 PRO and X5 mini V3.
Divider 1/32.
8 ) TMC2130.
I have already described my experience of using and buying. I repeat, if there is a desire to get confused using SPI on the board, and try to adjust the voltage - please. The widespread firmware for 8-bit Marlin boards has already added a library for this driver and auto-regulation of its voltage (the current is added until an overheating error appears, then it decreases step by step, in 50mA steps), but so far there are sensible mentions of installing and I did not see the Pololu driver setup. The only implementation that deserves attention is the implementation of Joseph Pryusha, on the new MK3. In his new EINSY RAMBO board, the driver data is already soldered into the board, and the firmware supports voltage regulation. One of the advantages of this driver is the control of the moment on the motor rotor, that is, at the moment the stopper carriage touches, the moment on the rotor shaft increases sharply, and the board understands that the carriage has reached its maximum and there is no point in trying to move it further. Therefore, there are no limit switches.
The board, similarly to the TMC2100, has an internal divisor from 1/16 to 1/256. Switching between dividers is done by software, via the SPI interface.
Quite a lot of Chinese clones have appeared, in which the SPI interface is soldered, and the operation is completely similar to the TMC2100. According to a representative of Watterott, there is no difference between the TMC2100 and TMC2130 with soldered SPI.
9 ) TMC2208
New drivers from Trinamic and Watterott. The microstep division configuration is carried out via the UART interface, with such a board.
The board provides the connection of the driver through this interface via a cable to the computer's USB. Next, with the help of its own utility, the parameters are configured.
After configuring the firmware, the board can be disconnected from the driver.
Chinese clones of this board have already appeared.
I got myself one. I can draw the only conclusion - Chinese clones are much more capricious and more difficult to adjust the voltage than the originals. There were BigtreeTech TMC2100 and Makerbase TMC2100 and these blkbox TMC2208, and of course the original TMC2100. Set up the Chinese, what would be straight
, I couldn't miss a single step in long enough printing. For that, the original in 5 minutes and everything is ok.
The chip has the same divisor from 1/16 to 1/256 as all other TMC2100,2130.
10 ) RAPS128
It is difficult to say who repeated whom if all stereotypes are removed. German drivers based on THB6128 (like the Panucatt Divices SD6128, according to Wiki REPRAP.org and the manufacturer's website. Judging by the description on the website of the store where they are sold, the Germans do not hesitate to install LV8729V, like the Chinese MKS LV8729.
The driver has a divisor from full step to 1/128. For 8-bit boards, it is not recommended to set the divisor above 1/32.
Very noticeable, not 1, but 2 potentiometers stand out.
The left one is for setting the voltage, and the right one is responsible for adjusting the current slope. The manufacturer recommends keeping the position of this potentiometer somewhere in the middle, from 1.1 to 3V. In the datasheet for any driver there are tabular values \u200b\u200bfor setting the current decay.
A small digression.
I will present a small squeeze of this article , to understand the principles of operation of stepper motors and the difficulties of controlling them.
Stepper motor. How does it work and why does it need a current drop?
A stepper motor is an electromechanical device that converts electrical impulses into discrete mechanical movements.
However, stepper motors have many useful features, and most importantly - they are cheap.
Why is a stepper motor good?
- the angle of rotation of the rotor is determined by the number of pulses that are applied to the motor;
- motor provides full torque in hold mode;
- precise positioning and repeatability. Good stepper motors have an accuracy of 3-5% of the step size. This error does not accumulate from step to step;
- quick start/stop/reverse capability;
- brushless reliability, stepper motor life is actually determined by bearing life;
- one-to-one dependence of the position on the input pulses provides positioning without feedback;
- the possibility of obtaining very low rotational speeds for a load attached directly to the motor shaft without an intermediate gearbox;
- quite a wide range of speeds can be covered, the speed is proportional to the frequency of the input pulses;
But not all is well. ..
- Stepper motors have a resonance phenomenon;
- possible loss of position due to lack of feedback;
- power consumption does not decrease even without load;
- difficult to work at high speeds;
- low power density;
- relatively complex control scheme;
There are three main types of stepper motors:
- variable reluctance motors
- permanent magnet motors
- hybrid motors
You can even feel the type of motor by touch: when the shaft of a de-energized permanent magnet motor (or a hybrid one) rotates, a variable resistance to rotation is felt, the motor rotates as if by clicking. At the same time, the shaft of a de-energized variable reluctance motor rotates freely. Hybrid motors are a further development of permanent magnet motors and do not differ from them in the way they are controlled. You can also determine the type of motor by the configuration of the windings. Variable reluctance motors usually have three (rarely four) windings with one common terminal. Permanent magnet motors most often have two independent windings. These windings may have taps from the middle. Sometimes permanent magnet motors have 4 separate windings.
In a stepper motor, the torque is generated by the magnetic fluxes of the stator and rotor, which are appropriately oriented relative to each other. The stator is made of high permeability material and has multiple poles. A pole can be defined as a certain area of a magnetized body where the magnetic field is concentrated. The poles have both a stator and a rotor. To reduce eddy current losses, the magnetic circuits are assembled from separate plates, similar to the core of a transformer. The torque is proportional to the magnitude of the magnetic field, which is proportional to the current in the winding and the number of turns. Thus, the torque depends on the parameters of the windings. If at least one winding of the stepper motor is energized, the rotor assumes a certain position. It will be in this position until the external applied moment exceeds a certain value, called the holding moment. After that, the rotor will turn and will try to take one of the following equilibrium positions.
We are interested in the hybrid motors most commonly used in 3D printers.
Hybrid motors combine the best features of variable reluctance and permanent magnet motors. The rotor of a hybrid engine has teeth arranged in an axial direction.
The rotor is divided into two parts with a permanent magnet in between. Thus, the teeth of the upper half of the rotor are the north poles, and the teeth of the lower half are the south poles. In addition, the upper and lower halves of the rotor are rotated relative to each other by half the pitch angle of the teeth. The number of pairs of rotor poles is equal to the number of teeth on one of its halves. The toothed pole pieces of the rotor, like the stator, are assembled from separate plates to reduce eddy current losses. The hybrid motor stator is also toothed, providing a large number of equivalent poles, as opposed to the main poles where the windings are located. Usually 4 main poles are used for 3.6 deg. motors and 8 main poles for 1.8- and 0.9deg. engines. The teeth of the rotor provide less resistance to the magnetic circuit at certain positions of the rotor, which improves static and dynamic torque. This is ensured by the appropriate arrangement of the teeth, when part of the rotor teeth is strictly opposite the stator teeth, and part is between them.
The rotor of a conventional 3D printer motor has 100 poles (50 pairs), the motor has 2 phases, so the total number of poles is 200, and the pitch, respectively, is 1.8 deg.
As you can see in the picture, the air gaps at the upper and lower pole pieces of the rotor are different. This is achieved by turning the pole pieces by half the pitch of the teeth. Therefore, there is another magnetic circuit that contains minimal air gaps and, as a result, has a minimal magnetic resistance. Another part of the flow closes along this circuit (shown in the figure by a dashed white line), which creates the moment. Part of the chain lies in a plane perpendicular to the figure, therefore it is not shown. In the same plane, the magnetic flux of the stator coil is created. In a hybrid engine, this flow is partially closed by the rotor pole pieces, and the permanent magnet “sees” it weakly. Therefore, unlike DC motors, the hybrid motor magnet cannot be demagnetized at any winding current.
The gap between the teeth of the rotor and the stator is very small - typically 0.1 mm. This requires high precision during assembly, so the stepper motor should not be disassembled for the sake of satisfying curiosity, otherwise its service life may end there.
To prevent the magnetic flux from closing through the shaft, which passes inside the magnet, it is made of non-magnetic steel grades. They are usually very brittle, so a shaft, especially a small diameter, should be handled with care.
To obtain large torques, both the field created by the stator and the field of the permanent magnet must be increased. This requires a larger rotor diameter, which worsens the ratio of torque to moment of inertia. Therefore, powerful stepper motors are sometimes structurally made from several sections in the form of a whatnot. Torque and moment of inertia increase in proportion to the number of sections, and their ratio does not deteriorate.
Hybrid engines are divided into 2 types. Depending on the configuration of the windings, the motors are divided into bipolar and unipolar. A bipolar motor (in the figure below under the letter a) has one winding in each phase, which must be reversed by the driver in order to change the direction of the magnetic field. In total, the bipolar motor has two windings and, accordingly, four outputs.
The unipolar motor (b) also has one winding in each phase, but a tap is made from the middle of the winding. This makes it possible to change the direction of the magnetic field created by the winding by simply switching the halves of the winding. The middle terminals of the windings can be combined inside the motor, so such a motor can have 5 or 6 terminals. Sometimes unipolar motors have separate 4 windings, for this reason they are mistakenly called 4-phase motors. Each winding has separate leads, so there are 8 (c) leads in total. With an appropriate connection of the windings, such a motor can be used as a unipolar or bipolar. A unipolar motor with two windings and taps can also be used in bipolar mode if the taps are left unconnected. In any case, the winding current should be chosen so as not to exceed the maximum power dissipation.
So which one is better?
When comparing bipolar and unipolar motors, the former has a higher power density. For the same size, bipolar motors provide more torque.
The torque generated by the stepper motor is proportional to the magnitude of the magnetic field generated by the stator windings. The most important is the limitation on motor heating due to ohmic losses in the windings. Just this fact demonstrates one of the advantages of bipolar motors. In a unipolar motor, only half of the windings are used at any given time. The other half simply takes up space in the core window, which forces the windings to be made with smaller diameter wire. At the same time, all windings are always working in a bipolar motor, i.e. their use is optimal. In such a motor, the cross section of the individual windings is twice as large, and the ohmic resistance is, accordingly, half as much. This makes it possible to increase the current by the root of two times with the same losses, which gives a gain in torque of about 40%. If increased torque is not required, a unipolar motor allows you to reduce the size or simply work with less loss. In practice, however, unipolar motors are often used, since they require much simpler winding control circuits.
How to control a stepper motor?
There are several ways to control a stepper motor. I will not paint everything, since they refer to full-step or half-step modes of operation. We are interested in the microstep mode. With this control method, the current in the phases must be changed in small steps, thus ensuring the splitting of a half step into even smaller microsteps (An important resource is the processor frequency, i.e. with what frequency it can send a STEP signal to move the driver). When two phases are switched on at the same time, but their currents are not equal, then the equilibrium position of the rotor will not lie in the middle of the step, but in a different place, determined by the ratio of the phase currents. By changing the ratio, it is possible to provide a certain number of microsteps within one step. To implement the microstep mode, more complex drivers are required that allow you to set the current in the windings with the required ratio. The half-stepping mode is a special case of the microstepping mode, but it does not require the formation of a stepped coil supply current, therefore it is often implemented.
Microstepping is achieved by making the stator field turn more smoothly than full or half stepping. The result is less vibration and virtually silent operation down to zero frequency. A smaller pitch angle can provide more precise positioning. There are many different microstepping modes, with step sizes ranging from 1/3 of a full step to 1/512. The stepper motor is a synchronous motor. This means that the equilibrium position of the stationary rotor coincides with the direction of the stator magnetic field. When the stator field rotates, the rotor also rotates, trying to take a new equilibrium position.
In order to obtain the desired direction of the magnetic field, it is necessary to choose not only the correct direction of the currents in the coils, but also the correct ratio of these currents.
The displacement of the balance point of the rotor indicates that the rotor can be fixed in any arbitrary position. To do this, you just need to correctly set the ratio of currents in the phases. It is this fact that is used in the implementation of the microstep mode.
Microstepping results in a smoother rotor at low frequencies. To achieve high speeds in the microstep mode, a high repetition rate of microsteps is required, which cannot always be provided by the control microcontroller. It is because of this that the transition from 8-bit electronics to 32-bit occurs, since delta printers use the movement of 3 motors at once to move along one axis.
With each step, the rotor does not immediately stop in the new equilibrium position, but performs damped oscillations around the equilibrium position. The settling time depends on the characteristics of the load and the driver circuit. Generally, fluctuations are undesirable. You can get rid of this phenomenon using microstepping mode. Below are shown the movements of the rotor when operating in full stepping and microstepping modes.
It can be seen that spikes and fluctuations are observed in the full-step mode, while they are absent in the microstep mode. However, even in this mode, the rotor position graph differs from a straight line. This error is explained by the geometry error of the motor parts and can be reduced by performing calibration and subsequent compensation by adjusting the phase currents.
When the rotor rotates, the motor has dead zones that limit positioning accuracy.
The figure shows the dependence of torque on the angle of rotation of the rotor.
The presence of dead zones is very important for microstepping. If, for example, there are dead zones with a value of d, then a microstep of less than d will not move the rotor at all.
When the motor is running under load, there is always some shift between the angular position of the rotor and the orientation of the stator magnetic field. Especially unfavorable is the situation when the motor starts to decelerate and the load torque is reversed. It should be noted that lag or lead refers only to the position, not to the speed. In any case, as long as the motor is not out of sync, this lag or lead cannot exceed two full steps. This is a very pleasant fact.
Each time the stepper motor takes a step, the rotor rotates S radians. In this case, the minimum moment occurs when the rotor is between adjacent equilibrium positions.
This torque is called the operating torque, it means what is the largest torque that the motor can overcome when rotating at low speed. If the motor is stepping with two energized windings, then the operating torque is equal to the holding torque for one energized winding.
The drive parameters depend on the characteristics of the load. In addition to friction, a real load has inertia. Inertia prevents speed change and requires high acceleration and deceleration torques from the motor, limiting maximum acceleration. On the other hand, increasing the load inertia increases the speed stability.
When designing stepper motor drivers, it must be taken into account that the motor windings are inductive. This inductance determines the rise and fall time of the current. Therefore, if a square wave voltage is applied to the winding, the current waveform will not be square wave. At low speeds (a), the rise and fall times of the current do not have much effect on the torque, but at high speeds the torque drops. This is due to the fact that at high speeds, the current in the motor windings does not have time to reach the nominal value (b).
In order for the torque to drop as little as possible, it is necessary to ensure a high rate of current rise in the motor windings, which is achieved by using special power circuits.
The behavior of the torque with an increase in the switching frequency of the phases is approximately the following: starting from a certain cutoff frequency, the torque monotonically decreases. Typically, two torque versus speed curves are given for a stepper motor.
The inner curve (start curve) shows at what maximum friction torque for a given speed the stepper motor can start. This curve intersects the velocity axis at a point called the maximum start frequency or throttle response frequency. It defines the maximum speed at which an unloaded motor can start.
The outer curve (acceleration curve) indicates at what maximum friction torque for a given speed the stepper motor is able to maintain rotation without skipping steps. This curve intersects the velocity axis at the point of maximum acceleration frequency. It shows the maximum speed for a given motor without load. The region that lies between the curves is called the acceleration region.
In order to operate at high speed from the acceleration area, it is necessary to start at low speed from the start area and then accelerate. When stopping, you need to act in the reverse order: first perform braking, and only after entering the start area, you can stop the supply of control pulses. Otherwise there will be a loss of synchronism and the position of the rotor will be lost.
It should be noted that the continuous operation of the stepper motor at high speed is not always possible due to the heating of the rotor.
When accelerating or decelerating, it is important to correctly select the rate of change of speed and maximum acceleration. The acceleration should be the smaller, the higher the inertia of the load. The criterion for the correct choice of the acceleration mode is the acceleration to the desired speed for a specific load in the minimum time. Most often, acceleration and deceleration with constant acceleration are used.
The implementation of the law, according to which the motor will be accelerated or decelerated, is usually performed by the program control microcontroller, since it is the microcontroller that is usually the source of the clock frequency for the stepper motor driver. To generate a clock frequency, it is convenient to use a hardware timer, which is included in the same Arduino processor - Atmega2560. When the motor rotates at a constant speed, it is enough to load the timer with a constant value of the step repetition period (step duration). If the engine is accelerating or decelerating, this period changes with each new step. When accelerating or decelerating at constant acceleration, the frequency of repetition of steps should change linearly, respectively, the value of the period that must be loaded into the timer should change according to the hyperbolic law.
Resonance
Stepper motors have an unwanted effect called resonance. The effect manifests itself in the form of a sudden drop in torque at certain speeds. This can result in skipped steps and loss of synchronization. The effect is manifested if the step frequency coincides with the natural resonant frequency of the motor rotor.
When the motor takes a step, the rotor does not immediately settle into a new position, but makes damped oscillations. The fact is that the system rotor - magnetic field - stator works like a spring pendulum, the oscillation frequency of which depends on the moment of inertia of the rotor (plus the load) and the magnitude of the magnetic field.
The resonant frequency is determined by the moment of inertia of the motor rotor itself and the moment of inertia of the load on the motor shaft. Therefore, the rotor resonant frequency of an unloaded motor, which is given among the parameters, is of little practical value, since any load connected to the motor will change this frequency.
When non-micro stepping is used, the main cause of oscillation is the intermittent rotation of the rotor. When a step is taken, some energy is imparted to the rotor by impetus. This impulse excites vibrations. The energy that is imparted to the rotor in half step mode is about 30% of the energy of a full step. Therefore, in the half-step mode, the oscillation amplitude is much smaller. In microstepping mode with 1/32 of the main step, only about 0.1% of the energy of a full step is reported at each microstep. Therefore, in the microstep mode, the resonance phenomenon is almost imperceptible.
Current reversal methods
Stepper motor operation requires reversal of the magnetic field direction independently for each phase. Changing the direction of the magnetic field can be done in different ways. In unipolar motors, the windings are center tapped or there are two separate windings for each phase. The direction of the magnetic field is changed by switching half windings or whole windings. In this case, only two simple switches A and B are required for each phase.
In bipolar motors, the direction is changed by reversing the polarity of the winding leads. Polarity reversal requires a full H-bridge (figure below). Key management should be carried out by a logic circuit that implements the desired operation algorithm. It is assumed that the power supply of the circuits has a nominal voltage for the motor windings.
After the inductor is disconnected from the power supply, the current cannot stop immediately. There is an EMF (electromotive force) of self-induction, which has the direction opposite to the power source.
To adjust the torque, you need to adjust the current in the windings. In any case, the current must be limited so as not to exceed the power dissipation on the ohmic resistance of the windings.