3D printer can build a house in 20 hours
3D Printer Can Build You A House In 20 Hours: Welcome To The Future
Luke Hopewell
Published 10 years ago: August 9, 2012 at 3:00 pm -
We’ve seen 3D printers used for everything from iPhone cases to makeshift weapons, but if you think bigger, what can these new printers really be used for? Could you really make your own house with a 3D printer in less than 20 hours? Turns out you can, and the technology is now set to be used by NASA for a future Moon colony.
The man behind this ambitious housing project is Professor Behrock Khoshnevis, and he’s disgusted that in the 21st century, the world is still ridden with poverty-stricken slums characterised by make-shift corrugated iron shacks. He wanted to find a way to improve the basic concept of house construction so that it was accessible to everyone, because with better shelter comes a more civilised society.
To build a house right now, you’re looking at a slow, labour-intensive, dangerous process that’s almost always over-budget. Professor Khoshnevis said that housing construction is one of the only industries that still does things manually, unlike the motoring or technology industries for example that use automated production methods to complete routine construction tasks.
So how do you fix a slow, expensive housing concept that has been set in stone for the last few centuries so that everyone around the world can get access to it? That’s easy, Professor Khoshnevis says. You use 3D printing.
Khoshnevis is heavily involved in computer-aided design (CAD), robotics and rapid prototyping with the University of Southern California, and he’s using that experience to scale up 3D printing so that it can be used in housing construction.
“I name this process Contour Crafting, which is essentially a way of streamlining the process by benefiting from the experience we have gained in the domain of [automated and technology-assisted] manufacturing,” he told TEDxOjai attendees earlier this year.
Khoshnevis wants to build entire neighbourhoods with Contour Crafting, and he claims it can be done at a fraction of the cost in a smaller block of time.
As far as expenses go, the materials for the 3D printed house are projected to cost 25 per cent less than traditional houses and labour costs can be cut in half. In terms of timing from start to finish, Khoshnevis said that “we anticipate that an average house, like 2500 square foot house, can be built in about 20 hours from a custom design”.
Here’s how it works. A CAD design is sent to a large-scale 3D printer that is mounted to a block of land. The printer lays out the concrete-like foundation of the home through a nozzle that can move anywhere on the property. Like any 3D print-out, the house is made layer-by-layer and reinforced with various materials — like electrical, plumbing and communication infrastructure — as the build progresses.
The concrete used is a mixture of concrete and fibre polymers, meaning that it is more than three times stronger than traditional concrete used in today’s houses. The concrete that goes into your house right now can withstand roughly 3000 pounds per square inch of pressure, while the new printed concrete can withstand around 10,000 pounds per square inch.
The best thing about the construction process, Khoshnevis added, is that it can print out any house design you like. Curved walls? No problem. Water feature in your front yard? Can do. Custom tile design and a few feature walls? Simple, thanks to the addition of laser jet printer nozzles attached to the printing array.
As if that’s not impressive enough, Professor Khoshnevis’ concept is currently being supported by NASA so that the space agency can one day be used to build a colony on the Moon. You read it right, the Moon.
This is the future I want to live in. One where I can print out my own house in less than a day, for half the cost, using the same technology NASA is using on the moon. I want to go to there. [TEDxOjai via Reddit]
More From Gizmodo Australia
About the Author
Meet the Giant 3D Printer That can Build a House in Under 24 hours
Artist depiction of Contour Crafting's printer.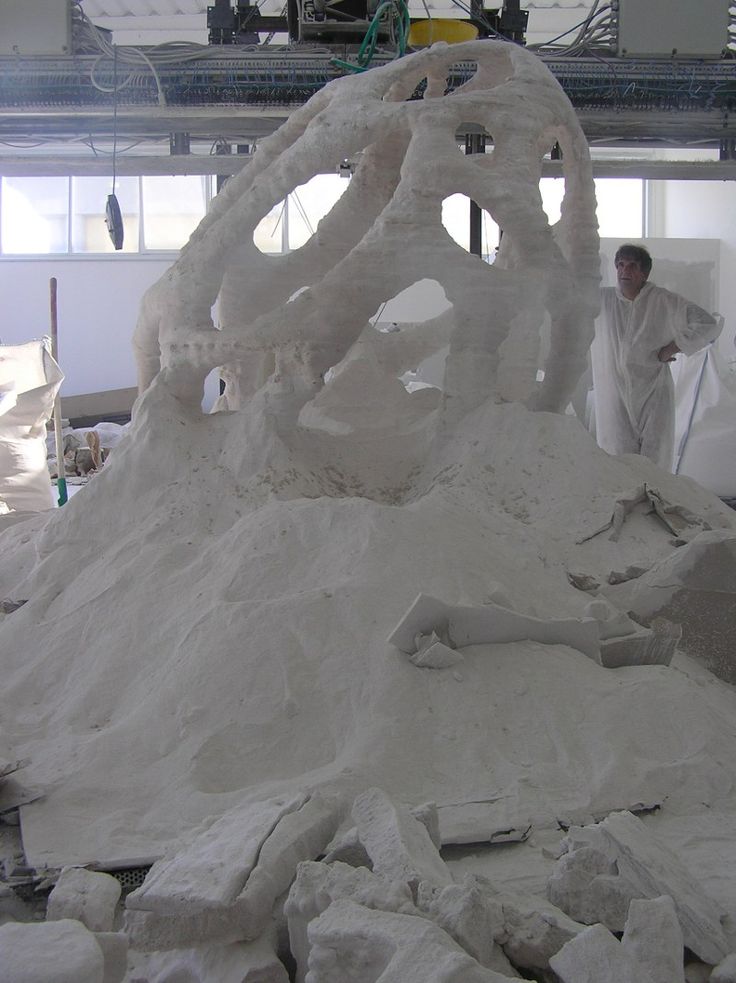
A company from Southern California called Contour Crafting, a project that started at the University of Southern California, say that they can print a 2500 square foot house in merely 20 hours - that's less than a day!
This feat is achieved by utilizing a revolutionary large size 3D printer that uses concrete as the printing medium. Behrokh Khoshnevis, the professor at USC that created the technology, said the technology is incredibly versatile and allows for unprecedented flexibility in architecture, compared to traditional standards; however, it is still a university project that has not been commercialized, though Khoshnevis has high hopes.
How to Print a Home in a Day
At first, when you hear of this project, you may think it is extremely ambitious, an entire house in less than a single day is revolutionary. Here's how it's managed: The process starts with a team dropping the printing machine off at the designated site. They then assemble the required frame unit for the printer and then attach the printer to the frame.
The concrete reservoir is then pumped full of concrete from a standard concrete pumping truck and the printer can begin its job. As seen in the video below, the device can literally print a wall in virtually any shape, layer by layer, out of concrete.
Each time, it prints an outer section to the wall and then fills in the hollow wall with a support filling. Since the method used to lay the concrete is continuous, Contour Crafting is able to program the printer to build walls that are curved and would otherwise be fairly difficult to construct by pouring concrete the traditional way.
This allows for the home owner to build a unique house to them in virtually any shape one can imagine. Even with adding curved walls, the construction time of the house is barely affected, keeping construction time minimal. To further decrease finishing costs the printer can install all the conduits for electrical, plumbing and air conditioning as it is building the house. The end result would be a complete structure that would require minimal finishing construction to make the interior more personalized and enjoyable.
What it Means for Humanity
Photo of the housing problem in India. Photo Credit: PressTV.Compared to most other industries, construction is fairly far behind in automation. This not only slows the process of building structures, it also leaves plenty of workers in fairly dangerous working conditions.
Automating the construction process would greatly reduce risks to construction workers; however, it would also greatly decrease the need for construction workers, as the majority of the job is now being done by the printer. For many this is obviously a conflict of interest, as it poses a threat to their career.
However, automating the construction process would also allow the first world nations of the world to subsidize low income housing for their own citizens, and also allow us to correct housing issues all over the world.
An automated process would allow nations to build emergency housing for victims of natural disasters or conflicts. Because the technology is highly adaptable, the printer can use onsite materials. This will cut the cost of production by eliminating the need to transport heavy materials to the building site. In the event of an emergency, the lack of a need for laborers to build shelters means that relief workers can spend more time rebuilding local infrastructure or helping those who require medical attention.
The Controversy
Example of a Lunar base created by 3D printing. Photo Credit: Contour Crafting.Currently 3D printers are being used for a multitude of different applications, from printing pizza's to human ears, NASA even sent a 3D printer to the ISS. These tasks are possible because several different models of printers are able to use various printing mediums, ranging from foods to concrete and even carbon fiber.
Another promising feature both NASA and Contour Crafting are researching is building habitats on our own moon and possibly even other planets and their moons as well.
As of now, it possible to make more then you probably think with 3D printers, from guitars to guns and even Aston Martin cars, and this has already led to a considerable amount of controversy.
The range of controversy includes the legality of 3D printed items such as guns, and for obvious reasons, many countries are looking to amend laws regarding 3D printed weapons. This still leaves the issue of Intellectual Property. Currently, 3D printing does not fall anywhere under intellectual property laws. This mean small business owners could see their products rampantly copied, which could seriously affect their business.
Even as industrial 3D printing becomes more practical and the material cost lowers in price, large scale manufacturers will also start to see their products copied more frequently. Currently, the only real protection businesses have is copyright laws. If a person is blatantly copying your product to sell in mass quantities there is legal grounds to sue over copyright infringement; however, the cost to pursue someone who has copied a small amount of items would outweigh any monetary recovery.
Share This Article
Huge US-developed 3D printers can build a 232-square-meter house in 20 hours
Archive
, without a reliable roof over their heads, almost 1 billion people worldwide. It is this fact that is one of the main reasons leading to epidemics or rampant crime. To solve the problem, Hoshevis and his Contour Crafting project propose the use of 3D printers that can build an entire building. nine0003
According to the portal 3dtoday.ru, huge 3D printers, developed by the Hoshevis team, will be able to build a house with an area of 232 square meters in 20 hours, including laying utilities, fine finishing and painting. It may sound fantastic, although the video shown by the creator of the project shows how the device's print head lays down cement layer by layer, creating the finished wall. To reduce weight and save material, the walls will be made hollow inside, but this will not affect their strength, which will be even higher than that of walls erected by the traditional method. nine0003
3D printed houses will not necessarily be in the shape of "boxes". Devices quite effectively cope with printing and more complex forms.
The "construction" project is not the only one the Contour Crafting team is working on. So, the company, in partnership with NASA, is working on the creation of printers that can be used to create "lunar bases". Speaking of the "printing buildings" project, Hoshevis sees it as a goal to more effectively create entire neighborhoods of affordable housing in the world's poorest regions. Given the fact that it will be possible to make changes to the model and layout of houses, the resulting areas will not look like a cluster of "faceless boxes". nine0003
Calculations show that building houses using the new technology will save 20-25% of total costs and 25-30% of materials. The greatest savings will be achieved in the use and payment of labor - this resource will be required by 45-55% less. The new technology will also be more environmentally friendly: the process will require less energy, and therefore less CO2 will be emitted into the atmosphere.
But won't the spread of mechanical "builders" lead to an increase in unemployment, when thousands and millions of people previously employed in this area will be left without work? Hoshevis does not think so, citing the situation of the early 20th century as an example, when 3D printing in such assumptions was replaced by the spread of agricultural machines. Today, less than 1.5% of Americans are engaged in farming, and this did not lead to the collapse of either the industry or the economy as a whole. At the same time, according to Hoshevis, Countour Crafting, having made old vacancies less in demand, will simultaneously open a number of new and more promising ones. "Progress and the use of new technologies always increase economic efficiency and lead to greater savings," he said. nine0003
Article prepared for 3DToday. ru
Subscribe to the author
Subscribe
Don't want to
From dosshouses to palaces: ten buildings printed on a 3D printer
Houses made of garbage for the price of an iPhone and palaces printed in a few days. We tell how 3D printing has transformed the construction industry and what modern printers are capable of
Refuge from the elements in Amsterdam - 8 sq. m
In 2015, the Dutch bureau Dus Architects built a tiny house of 8 square meters. m. It is located in the industrial area of Amsterdam, and anyone can rent it. Despite the small area, the shelter has a veranda and a sofa that converts into a double bed. The bathroom, also created on a 3D printer, is taken outside. The shelter was built from bioplastic based on linseed oil. To make a stable house without heavy frames, the engineers designed the walls in the form of a honeycomb. nine0003
Photo: DUS Architects
Urban Retreat is part of a temporary functional housing project. The Dutch authorities hope that 3D printing will help provide housing for victims of natural disasters in the future.
Garbage and Clay Houses - 30 and 60 sqm m, the cost of which was only about $ 1,000. The building received the symbolic name Gaia - in honor of Gaia, the ancient Greek goddess of the Earth, since only natural materials were used in the construction. nine0003
Engineers believe the cost-effective technology can be used to build temporary shelters for victims of natural disasters or refugees. The house became part of the Shambhala Village project, the first settlement in the world where all buildings will be printed.
Photo: WASP
Another WASP project is the futuristic Tecla house created in 2021 with Mario Cucinella Architects. Residential building with an area of 60 sq. m printed in 200 hours.
Photo: dezeen
The company's printer can use both concrete and a biodegradable mixture of clay, straw, rice husks and hydraulic lime as "ink". Construction takes place in two stages: first, the concrete frame of the wall is printed, and then the printer fills its inner layer with clay. The main advantage of the technology that WASP uses is the absence of construction debris. nine0003
Printed house in the suburbs - 37 sq. m
An unusual house in Stupino near Moscow is one of the first projects of Apis Cor, a Boston startup with Russian roots. The construction of the building was completed in the winter of 2017. House of 37 sq. m was built in 20 hours, and its cost was ₽590 thousand. The material sets only at temperatures above 5°C, so the construction site was covered with a tent. At the same time, the finished building can withstand temperatures down to minus 35°C. For construction, an industrial printer weighing 2.5 tons was used, which allows you to design up to 100 square meters. m of housing per day. nine0003
Unlike most competitors, Apis Cor prints its buildings on site rather than assembling them from prefabricated blocks. The house in Stupino became an advertisement for startup technology: Apis Cor founder Nikita Chen-yun-tai intended to sell printers, not houses. The idea of the Russian startup was successful - even Time wrote about an innovative house in the Moscow region.
Homes for the homeless - 38 and 45 sq. m
Icon is an American robotics startup focused on 3D printing of large-scale objects. For example, together with NASA, they designed a prototype rocket landing pad, and are now planning a project for a printed lunar space station, Olympus. But the company is also engaged in more mundane buildings. nine0003
Together with design firm Logan Architecture, Icon printed six houses for the poor in 2020. Each area is 38 sq. m. For construction, a Vulcan II 3D printer and special concrete were used. All buildings have an equipped kitchen, living room, bedroom and bathroom. The 3D quarter was built on the territory of an already existing community for the former homeless, where more than two hundred people now live.
Photo: Shane Reiner-Roth / The Architect's Newspaper
In Mexico, Icon is partnering with New Story, a foundation that raises donations to build safe, affordable housing for the poor. In 2019th project organizers said they plan to print 50 houses, each of which will have two bedrooms, a bathroom, a kitchen and a living room. The area of Mexican houses is 45 square meters. m.
Photo: Icon
Because 3D-printed houses are built many times faster and cheaper than usual, they can be a lifesaver for the homeless.
Lotus House - 60 sq.m. m. It was designed by students of the University of Washington as part of the Solar Decathlon China 2018 competition. The task of the participants was to create an environmentally friendly building that would run on alternative energy sources. The student team went further and decided that even the construction process itself should be waste-free and carbon-neutral. nine0003
The building itself is only partly 3D printed. On it, engineers made molds for casting concrete walls. The advantage of this approach is that the printed designs can be used at least a hundred times. In conventional construction, wooden molds are used, which wear out after only two castings.
The building itself was made in the shape of a lotus - the designers said that they wanted to emphasize the beauty and delicacy of Chinese culture in the design.
Photo: Liam Otten / Archinect
Germany's first two-story printed house - 80 sqm m
A two-story villa printed in North Rhine-Westphalia is an example of the use of 3D printing in the construction of luxury housing with custom design. The living area of the building was 80 sq. The 3D villa is a joint project of MENSE-KORTE ingenieure+architekten and developer PERI GmbH.
Photo: Mense-Korte
The villa was built using a unique BOD2 3D printer that can print pipes. This feature gives designers a free hand: complex engineering solutions on BOD2 can be completed faster and cheaper than with standard construction. ArchDaily writes that an innovative printer used in the construction of a German villa can print 1 sq. m wall in just five minutes. nine0003
Curve Appeal Ecosystem Home - 240 sqm m
Another example of conceptual 3D printing is the Curve Appeal 240 sq. The building belongs to WATG Urban Architecture Studio. The printing of the building was completed in 2020.
Construction lasted three years. The building project was created back in 2016, and then won first place in The Freeform Home Design Challenge. Designers received $8,000 from the organizers to implement the concept.
Photo: WATG
Curve Appeal is made from 28 printed panels. The unusual design maintains the microclimate of the house: according to the designers, the temperature inside the building does not depend on the weather outside.
The world's largest printed building in Dubai - 641 sq. m
The world's largest 3D printed building is located in the UAE. Building with an area of 641 sq.