3D printed wings
Eclipson EBW-160 - 3D printed flying wing
THE BLACKWING
EBW-160 R/C
If you just want a great flying wing, without the FPV equipment, the R/C (Radio Controlled) Version of your Eclipson EBW-160 will suit your needs.
This model is extremely easy to print, build, transport, and fly thanks to the inherent simplification of the flying wing configuration. Another distinctive characteristic of this design is its longitudinal stability which is equal to the stability achieved by a classic airplane design. This characteristic makes it very easy and safe to hand launch. 3D printing design freedom allowed us to design an aircraft that is both very aerodynamic and lightweight. For instance, the airframe structure weighs in at only 265 gr for an airplane with a wingspan of 1.6 meters. With a low wing loading (23g/dm2) more than one hour flight times are achievable!
(This version does not include all the necessary parts for FPV flight , optional vertical tail and big volume version)
Includes:
-STL files
-G-codes for PLA and LW-PLA
-Decals (2 Schemes)
For free:
-Model for Real Flight simulator
€18
Features:
-Stable design
-Replaceable keel with launch hook
-Efficient design (Max L/D = 18)
-Easy to assembly
SPECIFICATIONS
LW-PLA PLA
STRUCTURE WEIGHT 265gr 480gr
TAKE OFF WEIGHT 680gr 1100gr
STALL SPEED 23kmh 27kmh
MAX GLIDE RATIO 17 18
WING LOADING 23g/dm² 38g/dm²
WING SPAN 1,6 m
WING SURFACE 29 dm2
WING ASPECT RATIO 9
WING AIRFOIL -Root NACA1116
-Tip NACA0010
ASSEMBLY GUIDE AND REVIEW
DOWNLOAD DRAWING
SHOPPING LIST
ALL THE COMPONENTS THAT YOU HAVE TO BUY TO FLY THE AIRPLANE
3D PRINTER
MIN PRINTING VOLUME - 210x210x180 (X,Y,Z)
NOZZLE DIAMETER - 0,4 mm
Recommended
FILAMENT
QUANTITY - 265gr (LW-PLA) 480gr (PLA or PETG)
TYPE - LW-PLA , PLA or PETG
(Other materials can be used for category C parts)
ECLIPSON STANDARD POWER PACK
SERVOS NEEDED - x2
Recommended
BATTERY
VOLTAGE - 11,1V (3S) or 7,4V (2S)
CAPACITY - 5000 mAh to 6000 mAh
DISCHARGE - >10C (the lower the more efficient)
WEIGHT - 360gr to 420gr for PLA version
190gr to 230gr for LW-PLA version
(necessary to set the C.
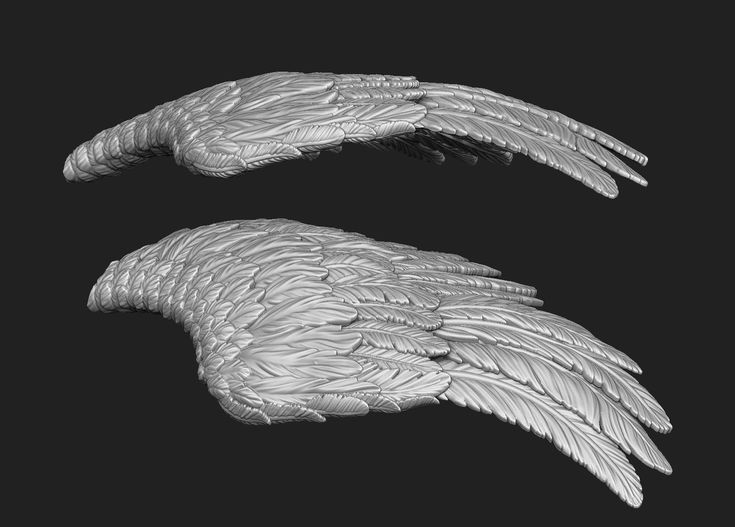
HEIGHT - <30mm
Proposed:
Configuration 1- Two batteries in parallel (PLA version)
Turnigy Graphene Professional 3000mAh (2Units)
+ XT60 Harness
Configuration 2- One battery (PLA version)
Turnigy 5000mAh 3S
Configuration 3- Two batteries in parallel (LW-PLA version)
ZIPPY Compact 2200mAh 2S(2Units) + XT60 Harness
RADIO CONTROL SYSTEM
MIN CHANNELS - 3CH
Recommended
OTHER PARTS
-PUSH RODS - D1,2mm (min length 60mm) 2units
-SERVO LEAD EXTENSION (min 400mm) 2 units
-BOLT- M3X14mm 4units
-TAPE
-SCREW - M2X8mm (aprox) 25units
-VELCRO
-PUSH RODS CONNECTORS (Not mandatory) 2units
-GLUE - cyanoacrylate + accelerator (not mandatory)
Recommended
rc version components
Wings best 3D printing models・Cults
3pc Fairy Wings Bath Bomb Mold
€6
1pc Fairy Wings Bath Bomb Mold
€6
MOTU Fright Fighter wings
€7. 99
Amazonian royal flycatcher
€26
Articulated bone Dragon
€5.62
Tiger Statue op 2 3D print model
€37.49
cute unicorn
€1.88
Cookie cutter Joel Pedro Pascal the last of us
€0.89
Cookie cutter Ellie's tattoo The last of us
€0.89
Cookie cutter fireflies the last of us tvshow
€0.89
Glass wing Kestrel Logo
Free
pre dart wing
€0.50
bird model 3D
€1.25
Eagle
€6.25
snow goose 3D print model
€14
White-eye Bird 3D print model
€18. 74
BUTTERFLY WINGS Cutter with Stamp / Cookie Cutter
€1.90
Goat Statue 3D print model
€18.74
Transformers G1 Apeface Wings
€2.49
phoenix
€25
Chick 3D print model
€2.99
Hen Cock Chick 3D print model
€3.99
ailles STL
€1.25
phoenix
€25
Butterfly or Mask ? Wall Art Decor
Free
Angel Bull Terrier
€5
Caddy guitar wing token
€1.50 -15% €1. 28
Mechanical Pegasus
€10
angel
€10 -50% €5
Butterfly heart basket** COMMERCIAL VERSION**
€8.11
Butterfly heart basket
€4.45
VALENTINE'S DAY 💖- COOKIE CUTTERS : HEART WITH WINGS💖.
€0.65
Wing 01
€1.99 -30% €1.39
69 Feather Set
€5 -30% €3.50
Harry Potter, Golden Snitch pendant
€2. 50
colibri humming bird
€30
Loop blade propeller
Free
Parrot 3D print model
€3.99
Chinese Hwamei aka Melodious Laughingthrush 3D print model
€3.99
Parrot 3D print model
€3.99
Parrot Tree 3D print model
€3.99
Parrot Tree 3D print model
€3.99
Egyptian goddess form Anatomy Siting Sculpture 2
€17
Female form Anatomy Siting Sculpture 1
€16
ROBLOX avatar boy angel wings and hoodie
€2.03
Bat Love
€3. 28
Bat Love
€7.38
Pigeon
€3.28 -20% €2.62
3d printer helps to improve the design of a racing motorcycle
Implementation stories
Automotive industry
Rapid prototyping
Author: Viktor Naumov
Author: Viktor Naumov
3D printing and motorcycle racing: when every detail matters | Drilling templates | Footboard attachment | Air intake | results
The idea of using 3D printing is based on its technological features (such as the possibility of customization and reproducibility of the object), which allow the development of innovative solutions for the creation of racing motorcycles. Motorcycle racing is a highly competitive field where even the smallest detail can affect the result and lead you to victory.
Andrea Pirazzini, founder and director of Help3D, a 3D service provider, has a passion for racing and competes in the Velocità CNV Motoasi Italian Championship for 100 octane pit bikes. In Andrea's opinion (and we fully agree with him), the advantage of additive technologies is the ability to create unique shapes from technical materials is exactly what you need to work on prototypes and models of racing motorcycles.
Another big advantage of 3D printing, according to Andrea, is the variety of materials that can be used. The world of additive manufacturing is constantly evolving and there is a need to develop technical materials with advanced performance characteristics to create better and more efficient parts. That is why 3D printing can be applied to any manufacturing process, streamlining and streamlining prototyping.
Andrea has already used a Sharebot 3D printer to print plastic prototypes for racing bikes and has worked with the Quarto di Litro team at the University of Pavia on parts for the concept bike.
All parts were made on Sharebot Q and Sharebot 42 3D printers (modified version - Sharebot 43). For example, a multi-component fork assembly that was printed on the Sharebot 42 in just 20 hours using PLA plastic, or spacers and links made from thermoplastic polyurethane (TPU). The choice of these elastic materials is due to the high load that they must withstand. The printed part was tested and no problems were found as a result.
One of the most interesting prototypes is a 1:1 printed pit bike body (23 hours of work). Thanks to 3D printing, Andrea Pirazzini was able to reproduce every technical and aerodynamic detail with the highest precision and resolution. He also created the air intake and spigot from high-strength polybutylene terephthalate (PBT).
iQB Technologies experts recommend article: Plastic works wonders: how a 3D printer imitates human organs
3D printing and motorcycle racing: when every detail counts
MotoGp is the world championship in road racing, the main competition in its class. At an event of this caliber, every detail counts, and the bike's continuous optimization helps the rider lap a few precious tenths of a second faster.
We used to think that only a better motor is enough for more speed, but in fact, everything is not so simple. Over the last few years at MotoGp, motorcycles have been getting aerodynamic fenders on the front of the fairing: at first they were thought to be just a beautiful accessory, but over the years fenders have become the basis of motorcycle aerodynamics, especially because they increase downforce, and therefore traction on asphalt, and also reduce the resistance to movement during acceleration.
Drilling templates
In preparation for the next racing season, the famous Italian racing motorcycle manufacturer Aprilia, using Sharebot 3D printers and Help3D technical support, has developed drilling templates for the motorcycle front fairing. The template 3D models were created directly from the fairing CAD models and then printed using the Sharebot QXXL and Sharebot 42 printers.
These templates made it possible to create holes with exceptional precision, which is not possible with classical manual template creation methods. It should be noted that the shape of the wings (made of carbon fiber) is adapted to the fairing, so it is important that the holes in the body provide a snug fit at an ideal angle.
Footrest attachment
It's no secret that a rider on a motorcycle should sit "like a glove." It's not just about a comfortable posture, but also about optimizing the rider's aerodynamics on the bike.
The kickstand plays a vital role in the rider's riding position: it is more rearward and higher than in a road bike. If it is the wrong size, then the rider may feel discomfort, and in this position he will be uncomfortable.
Sharebot 3D printers allowed the Aprilia Racing team to create a series of PLA footpeg mounts to see which model would work best for the team's riders. After analyzing different solutions and selecting the ideal model for each rider, the parts were made on a CNC milling machine.
With this solution, Aprilia has been able to reduce the design time and, above all, the production costs for each footpeg, while at the same time creating the optimal model for each rider.
Air intake
Engine performance also depends very much on how and how efficiently it "breathes". Sizing an air intake for a MotoGp requires careful study of the flow and turbulence created within the design. The air intake uses lightweight and ultra-strong carbon fiber. The downside is that a mold is required to make the part: thin sheets of carbon fiber pre-impregnated with epoxy are placed in a mold and then placed in an autoclave to complete the catalysis process and eliminate air bubbles.
In preparation for the season, the Aprilia Racing team created a series of PLA gearbox prototypes on the Sharebot QXXL 3D printer. By simulating various adapters and reducers, the sports division technicians were able to test different volumes on the test rig, starting with just the air intake.
This approach made it possible to determine the optimal air intake geometry without the need to first create a mold and exfoliate the carbon fiber, thereby saving time and money. The printed reducer can be tested on the bench, simply replacing one model with another, without removing the air intake each time. After determining the optimal geometry, one final mold was made to create the air intake.
Results
Let's summarize the 3D printing projects using Sharebot FDM printers, which allowed us to optimize the design and aerodynamics of motorcycles for the MotoGp World Championship.
-
Drilling templates for front fairing: 3D template models are created directly from fairing CAD models, then 3D printed. This solution made it possible to make holes with exceptional accuracy, which is unattainable using traditional methods.
-
Motorcycle Footrest Mounts: A series of parts are printed in PLA plastic to choose the most suitable for each of the team's riders, then the final products are produced by a CNC milling machine.
-
Air intake: A series of prototype gearboxes were made from PLA to test and determine the optimal air intake geometry. 3D printing made it possible to do without tooling, and one final mold was made based on the results of testing.
Material provided by Sharebot
Article published on 11/13/2020, updated on 06/11/2021
Sharebot 3D printers open up new possibilities
Author: Nikita Kudryashov
Today we will talk about three interesting 3D printing projects implemented using the advanced professional equipment of the Italian company Sharebot. With 3D printers from this manufacturer, you will have an innovative approach to production, a variety of tasks to be solved, and the ability to create complex large-sized models in the shortest possible time.
Aircraft 3D Project: Large Aircraft Rapid Prototyping
Aircraft 3D is a large aircraft model created by Sharebot's R&D department using the Sharebot Q XXL professional 3D printer, a turnkey solution for industrial plants based on FDM technology.
Q XXL, the next model after Sharebot Q, combines the main functions of the Q-series (automatic print platform calibration system, Sharebox3D interface and remote control) with the largest build chamber (700 x 400 x 300 mm) and special nozzle 0, 8 mm. All this makes it possible to produce durable prototypes for the automotive and mechanical engineering industries, for example, models of bumpers and other automotive components. QXXL is an advanced, truly innovative work tool for optimizing production in accordance with Industry 4.0 standards.
Parts of the aircraft model printed on a Sharebot large format FDM printer
Printed with PLA-S universal filament. PLA is a commonly used biodegradable 3D printing material made up of a thermoplastic polymer derived from corn. PLA is resistant to impact and durable material, it eliminates the effect of distortion during printing, is not subject to retraction and deformation. The material is available in a wide range of colors, does not emit any odor, and can be extruded at lower temperatures than other materials, so there is no need to heat the print platform.
The model of the aircraft was supposed to be created in eleven printing sessions: eight for the body, two for the wings and one for the tail. During simulation, Sharebot set dimensions and geometry to simplify the printing process by adapting the parts to a larger 3D printer: the first version of the model was created for the XXL Plus printer, after which the designer Daniele Fumagalli adapted the model for the Q XXL build chamber.
Parts printed with a 0.8mm nozzle, with a layer thickness of 0.6mm. These Sharebot Q XXL settings have optimized the workflow for making a larger model by speeding up printing without sacrificing quality and resolution. The whole process took 206 hours (one week), also thanks to the remote control system and thread sensor. With a traditional 0.4mm nozzle, it would have taken another week, or a total of 500 hours, according to Sharebot.
One of the advantages of additive manufacturing is the ability to post-process the model after the printing process. The assembly of the printed model of the aircraft was done with ordinary glue, after which the body, tail and wings were treated with putty to polish the surface and remove small bumps. The plane was then covered with acrylic paints (in Sharebot's signature black and white color scheme).
Prototypes of automotive parts and components. And not only...
Matteo Limonta, project manager, designer and founder of the MADesign community, shared his experience with Sharebot 3D printers, which he uses in the automotive industry and other areas. A young specialist prints prototypes of parts that will later be created from metal or iron.
“With 3D printing, I have solved two major problems. The first is the filling of interior spaces, since it is often difficult to produce parts with thin surfaces without flaws and with geometry that exactly matches the real parts, explains Limonta. “Secondly, I improved the post-finishing process: a 1.2 m product can be divided into 6 elements that are easy to print and then assemble. I printed these parts on a Sharebot XXL, a professional 3D printer capable of making very large models. Gluing these parts together is not an easy task, but the end result is extremely pleasing.”
Rapid prototyping with 3D printing is increasingly used by car and automotive component manufacturers
Automotive is not Matteo's only area of interest. He recently took part in a social project organized by the municipality of Milan: “I was asked to create a card for the blind in Braille,” says Limonta, “four cards 30 × 25, which are ideal for printing on Sharebot XXL.”
The designer has also worked on other additive manufacturing projects. For example, he designed equipment for a weaving mill, which is no longer available on the market, and it was printed from Nylon Carbon. It is a specialized technical plastic based on carbon fiber and nylon, ideal for printing professional and functional prototypes. “Now this device works in conjunction with metal equipment and functions just fine,” he said.
Matteo, who occasionally works at his father's auto parts factory, says 3D printing has helped build customer relationships: you can better explain the real features of the future product.
Innovative biomedical material - a step into the future
Finding and developing new solutions and applications for 3D printing is one of the main tasks of Sharebot. The company is confident in the need to invest in research, as it allows us to improve 3D printers and use innovative and more efficient materials.
Sharebot's R&D department has tested a new material for the SnowWhite 3D printer, a biomedical powder based on polyvinyl acetate (PVA). This material could open up new applications for 3D printers that implement selective laser sintering (SLS) technology.
Sharebot SnowWhite SLS Printer Build Chamber
In the direct laser sintering process, a laser sinters layers of thermoplastic powder in a heated chamber.