3D printing jetting
What is Material Jetting 3D printing?
What is Material Jetting 3D printing and how does it work? In this comprehensive intro to this additive process, we explore the main principles of the technology and how to tell if it's the right way to manufacture your custom parts. After reading this article you will understand the fundamental mechanics of the Material Jetting process and how these relate to its benefits and limitations.
How does Material Jetting 3D printing work?
These are the main steps in the MJ 3D printing process:
I. First, the liquid resin is heated to 30 - 60oC to achieve optimal viscosity for printing.
II. Then the printhead travels over the build platform and hundreds of tiny droplets of photopolymer are jetted/deposited to the desired locations.
III. A UV light source that is attached to the printhead cures the deposited material, solidifying it and creating the first layer of the part.
IV. After the layer is complete, the build platform moves downwards one layer height and the process repeats until the whole part is complete.
Unlike most other 3D printing technologies, MJ deposits material in a line-wise fashion. Multiple inkjet printheads are attached to the same carrier side-by-side and deposit material on the whole print surface in a single pass. This allows different heads to dispense different material, so multi-material printing, full-color printing and dispensing of dissolvable support structures is straightforward and widely used.
Support structures are always required when printing parts with Material Jetting and need to be removed in the post-processing stage.
With Material Jetting, the liquid material is solidified through a process called photopolymerization. This is the same mechanism that is used in SLA. Similarly to SLA, MJ-printed parts have homogeneous mechanical and thermal properties, but unlike SLA they do not require additional post-curing to achieve their optimal properties, due to the very small layer height used.
What are the characteristics of Material Jetting 3D printing?
Printer Parameters
In Material Jetting, almost all process parameters are pre-set by the machine manufacturer. Even the layer height is linked to each specific material, due to the complex physics of droplet formation. The typical layer height used in Material Jetting is 16 - 32 microns.
Material Jetting is considered one of the most accurate 3D printing technologies. MJ systems have a dimensional accuracy of ± 0.1% with a typical lower limit of ± 0.1 mm (sometimes as low as ± 0.02 mm). Warping can occur, but it is not as common as in other technologies, such as FDM or SLS, because printing happens at near room temperature. For this reason very big parts can be printed with great accuracy. The typical build size is approximately 380 x 250 x 200 mm, while large industrial systems can be as big as 1000 x 800 x 500 mm.
Multi-material & full-color printing
A key advantage of Material Jetting is the ability to produce accurate multi-material and multi-color prints that represent end-use products.
Multi-material and multi-color printing in MJ can be employed in three different levels:
- At the build area level, different parts can be printed in different materials or colors simultaneously, speeding up the manufacturing process.
- At the part level, different sections of a part can be designated to be printed in different material or color (for example creating a stiff case with flexible buttons for prototyping with haptic feedback).
- At the material level, two or more printing resins can be mixed in different ratios before dispensing, creating a "digital material" with specific physical properties, such as hardness, stiffness or hue.
To designate a different material or color to particular areas of the part, the model must be exported as separate STL files. When blending colors or material properties to create a digital material, the design must be exported as an OBJ or VRML file, because these formats allow the designation of special properties (such as texture or full color) on a per face or per-vertex basis.
Support structures
Support structures are always required in Material Jetting. Supports are always printed in a secondary dissolvable material that can be removed after printing using pressurized water or by immersion in an ultrasonic bath.
Material jetted parts can have very smooth surfaces with little to no indication of support after removal.
Part orientation in MJ is more flexible compared to other 3D printing technologies, like FDM or SLA. It is still important though, as the extensive use of support material also increases the overall cost.
Matte vs. glossy
Material Jetting offers the option of printing parts in either a glossy or matte setting.
In the glossy setting, support material is added only when it is structurally required (i.e. for overhangs). Surfaces not in direct contact with support will have a glossy finish, while supported areas will be matte. In the matte setting, a thin layer of support material is added around all the whole part, regardless of orientation or structural requirements. This way all surfaces have a matte finish.
The glossy setting should be used when a smooth shiny surface is desired. The cost of printing glossy is lower, as less material is used. The drawbacks of using this setting are the non-uniform finish of the printed parts and the slight rounding of the sharp edges and corners on the top, glossy surfaces.
The matte setting should be used when accuracy and uniform surface finish are a requirement. The cost of the matte setting is slightly higher, as more material is used and additional post-processing time is required. Notably, parts printed in the matte setting also have a relatively lower surface hardness.
What are the benefits & limitations of Material Jetting 3D printing?
Material Jetting 3D printing comes with a lot of advantages, though there are several drawbacks to keep in mind. Let's break these down beow.
Material jetting can produce smooth parts with surfaces comparable to injection molding and very high dimensional accuracy.
Parts created with Material Jetting have homogeneous mechanical and thermal properties.
The multi-material capabilities of MJ enables the creation of accurate visual and haptic prototypes.
Material jetted parts are mainly suitable for non-functional prototypes, as they have poor mechanical properties (low elongation at break).
MJ materials are photosensitive and their mechanical properties degrade over time.
The high cost of the technology may make Material Jetting financially not viable for some applications.
Detailed [](/knowledge-base/how-design-parts-material-jetting-3d-printing/)design guidelines of each of the aspects discussed here are explored in other Knowledge Base articles. The main characteristics of Material Jetting are summarized in this table.
Material Jetting | |
---|---|
Materials | Acrylic photopolymers (thermoset) |
Dimensional accuracy | ± 0.1% (lower limit of ± 0.05 mm) |
Typical build size | 380 x 250 x 200 mm (up to 1000 x 800 x 500 mm) |
Common layer thickness | 16 - 32 microns |
Support structures | Always required (printed using dissolvable material) |
Ready to transform your CAD file into a custom part? Upload your designs for a free, instant quote.
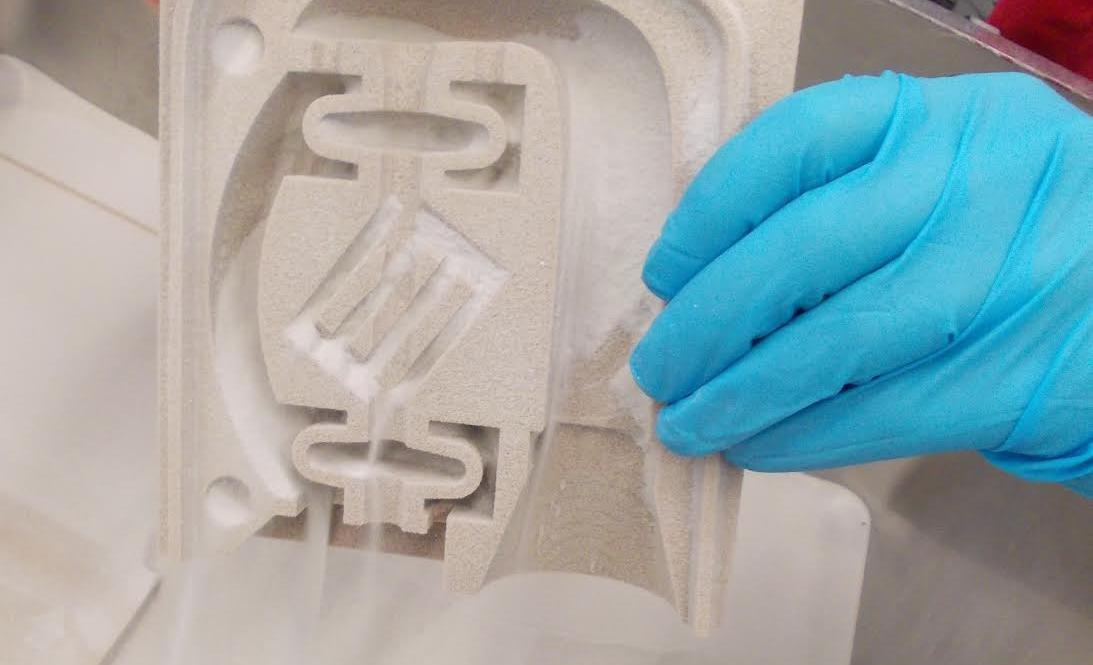
What are the Material Jetting 3D Printers on the Market?
Published on April 29, 2021 by Amelia H.
Material Jetting is one of the seven families of additive manufacturing processes. As the name suggests, it consists of depositing material on a printing tray, layer by layer, much like a 2D printer that drops ink on paper. Here, the print head actually projects many fairly large drops of ink, usually composed of photopolymers which are then hardened by UV light. But the process can also use metal, ceramics and even wax, dividing material jetting into three subgroups: Material Jetting, better known as the patented technology PolyJet; NanoParticle Jetting (NPJ) and Drop on Demand (DOD). Regardless of the process used, the user usually obtains high-precision, highly detailed parts with the possibility of printing in colour and with several materials. To help you make your choice, we have selected a few 3D printers per technology, classified by sub-group.
Material Jetting
Stratasys – J750 Digital Anatomy
Stratasys is the leading player in 3D material jet printing, having merged in 2012 with Objet Ltd. the company that patented the process. Its process has been called PolyJet and makes it possible to create multi-material, multi-color and even transparent parts. Stratasys today offers a wide range of PolyJet 3D printers but we will focus on the J750 Digital Anatomy, mainly designed for the medical sector. It offers a volume of 490 x 390 x 200 mm but above all can recreate very precisely the behavior of human tissues on anatomical models, allowing health professionals to have a real feeling and to train better.
Mimaki 3DUJ-553 Printer
In 2017, the Japanese manufacturer Mimaki, which has historically specialized in 2D printing, unveiled the 3DUJ-553 industrial 3D printer. With a print volume of 508 x 508 x 305 mm, the 3D printer is based on a UV LED process. In this process a light hardens the different layers applied successively. The machine deposits ink droplets coloured, white or black, on the printing tray until the final piece is obtained. A considerable advantage for professionals, especially since the 3DUJ-553 would offer 10 million colors to its users. In addition, it is also possible to add transparency with translucent ink. Thanks to its simulation software, it is possible to have a very precise overview of the shape and colors of the part before printing. Also, the printer has a surveillance camera, allowing users to follow the printing process remotely. Finally, the machine uses a support structure that can be dissolved in water. This makes it possible to obtain accurate and neat models, without damaging them.
NanoParticle Jetting
XJet Carmel 1400MThe XJET Carmel line of AM systems relies on the company’s patented inkjet technology, NanoParticle Jetting (NPJ). NanoParticle Jetting is a material jetting technology that builds parts by jetting a liquid containing nanoparticles of either metal or ceramic material in suspension. XJET offers both metal and ceramic systems. Its metal NPJ systems come in two sizes. The smaller possesses a build plate of 700cm2, XJet Carmel 700M. While the larger, at 1’400cm2, called XJET Carmel 1400M, is equipped with one of the largest build trays the industry has to offer. XJET Carmel 1400M, delivers impressive quality, accuracy, and reliability, as well as high levels of productivity. Both sizes are compatible with software including Autodesk and Netfabb. The XJET Carmel 1400M is also compatible with a mobile app.
Like its metal systems, XJET’s Ceramic AM systems also come in two sizes, one with a build plate of 700cm2, called XJet Carmel 700C, the other with a build plate 1’400cm2, called XJet Carmel 1400C. Again, both sizes are compatible with software including Autodesk and Netfabb, and only the larger printer is compatible with the mobile app. Like XJET Carmel 1400M, XJet Carmel 1400C possesses a maximum build height of 200mm. Thanks to its NanoParticle Jetting Technology, XJet’s Ceramic systems deliver parts of the utmost quality, with impressive levels of detail, finish and accuracy. Which, as with XJet’s Metal systems, is accompanied by uncompromised throughput and build time.
Drop On Demand
Solidscape – S390
Belonging to the Prodways group, Solidscape has developed a range of 3D DOD printers dedicated to the jewellery sector, including the S390. Thanks to its two printing heads, the machine allows to deposit wax and a soluble support material in order to design very precise moulds, whether for injection, for lost wax moulding, etc. It offers a printing volume of 52 x 152 x 101 mm and a wide choice of compatible materials. The S390 automatically generates print media to protect the most fragile parts of the model. These dissolve completely, leaving durable wax models ready to be molded.
DragonFly LDM®
The DragonFly LDM® Lights-Out Digital Manufacturing system is unique in that it is the industry’s only comprehensive additive manufacturing platform for around-the-clock 3D printing of electronic circuitry. Equipped with Nano Dimension’s state-of-the art, LDM technology. This allows for unattended operation as the printer maintains itself, with typically just one weekly maintenance operation needed thanks to improvements like a new advanced printer head, software management algorithms and automatic self-cleaning of the print heads every few hours. Approximately the size of two refrigerators, DragonFly is extremely large with machine dimensions of 1400mm x 800 mm x 1800mm (~4’7” x 2’7.5” x 5’11”) and a build volume of 160mm x 160mm x 3mm (6.5” x 6.5” x 0.125”). It is a precise inkjet deposition printer with dedicated nano-inks, equipped with two printheads: one for nano-Silver conducive ink and the other for dielectric polymer ink. The DragonFly is able to concurrently print using simultaneous multi-material additive manufacturing. Minimum trace layer thickness is at 17 microns, the minimum Dielectric layer thickness is 35 microns and technical accuracy is .01mm or 1 micron, with Nano Dimension claiming that the system is setting new precision standards for 3D printed electronics. The DragonFly LDM® can be used in a variety of industries including aerospace, defense, automotive, medical and electronics, among others.
Other Material Jetting Technologies
XYZPrinting da Vinci Color
The combination of FFF and inkjet technology makes the da Vinci Color from the Chinese manufacturer XYZprinting a unique 3D printer. The inkjet technology uses CMYK cartridges, which allows millions of colour combinations to be printed by absorbing individual ink droplets. This means that the parts can be printed with the da Vinci Color in any color, which is why it is very suitable, for example, for the implementation of creative projects. The machine is compatible with various (special) PLA and PETG filaments and also prints the XYZ carbon fiber material with a special extruder. The maximum pressure range is 200 x 200 x 150 mm and a plane resolution of 100 – 400 micrometers can be achieved. The printing speed is 30 to 60 mm per second. The da Vinci Color also has an integrated touch screen and removable printing plate and can be wirelessly connected to the home network.
ProJet CJP 860Pro from 3D Systems: (Colour Jet)
On a comprehensive list of 3D printers, we have of course not forgotten 3D printer manufacturing giant 3D Systems. That’s why the next machine is the ProJet CJP 860Pro color printer, which can create a realistic color experience thanks to its five print heads. What makes this 3D printer special is its ColorJet Printing (CJP) technology, which allows for parts that are up to 7 times cheaper than other technologies and, can eliminate waste through efficient use of materials. It also eliminates the need for supports, which significantly reduces post-processing time. The ProJet CJP 860Pro can also impress with its 5 to 10 times faster printing speed, saving additional time, allowing large format models to be built in just a few hours. As you can see, the press is an all-rounder: while it saves time and money, it delivers incredible color choice, a large build space capacity of 508 x 381 x 229 mm, and a sustainable factor.
What do you think about these material jetting 3D printers? Let us know in a comment below or on our Facebook, Twitter and LinkedIn pages! Sign up for our free weekly Newsletter here, the latest 3D printing news straight to your inbox!
3D Inkjet Printing (3DP) – 3dprofy
Turch October 21st, 2014
3DP stands for Three-Dimensional Printing , and translates as three-dimensional printing. This technology is one of the varieties of systems for the additive construction of a product according to its CAD model and differs from numerous similar schemes in that the process is carried out according to the principle of a conventional printer - through print head nozzles. Thus, 3D inkjet printing is a natural continuation of the development of conventional 2D printing technologies. To date, it has achieved fairly good results, such as color printing.
Products printed on the Z Corp's Spectrum Z510 color 3D printer
The history of the emergence and development of 3DP
For the first time, the idea of \u200b\u200brealizing equipment using this printing scheme was proposed by two students at the Massachusetts Institute of Technology Tim Anderson and Jim Bredt in 1993. It is thanks to them that the term 3D printing has spread around the world. And this is quite fair, because the first model of the device was a modification of a conventional 2D printer. Instead of ink, he used a special adhesive composition, which applied layer by layer to the surface of the bonded substance, the boundaries of the future three-dimensional product.
In 1995, Tim and Jim formed the Z Corporation, which brought this technology to market, improving it to such an extent that in 2012 3D systems Corporation wished to acquire it along with the company. Under her brand, former Z Corporation models are now sold worldwide.
One of the directions of the ExOne company (USA) is the production of 3D printers that use the same technology. This firm was founded in 2005 as a subsidiary of the Extrude Hone Corporation. Using the patents obtained by Anderson and Bedt, they launched a line of printers that even print metal products today.
3D inkjet printing technology
Today there are more than thirty 3D printing technologies, which in one way or another duplicate each other, although each has its own characteristics. The American Society for Testing and Materials (ASTM International) has divided 3D inkjet printing technologies into two categories:
- Material jetting - material jetting.
- Binder jetting Binder jetting.
In the first case, the building material itself is fed directly through the nozzles, which hardens after application. In the second, an adhesive is sprayed onto a thin layer of gypsum, polymer or metal powder. 3DP technology in its original form represented exactly the second method.
If we consider it in more detail, then printing occurs in the following way:0003
- To begin with, a CAD model is loaded into a computer connected via an Ethernet cable to the printer, which is “cut” into layers, about 0.1 mm thick.
- Next, a thin layer of powdered material (gypsum, polymers, sand, metal) is applied with a roller on a special platform.
- The print head sprays the binder (glue, water, special mixture) along the coordinates of the boundaries of the first layer received from the computer.
- After that, the platform with the model is lowered by the thickness of the layer down, and the chamber with the building material is lowered by the same distance.
- Next, the roller unrolls the next layer and the process repeats.
- After the end of 3D printing, the product is removed from the powder layer and thoroughly cleaned of its residues.
When making models from metal powder, a firing process in a special furnace is added. Let's take a closer look at this process.
The figure above shows 4 stages of his stage:
- First, according to the above scheme, the so-called "green model" is formed from the matrix powder and binder (1,2).
- Next, the article is placed in an oven filled with a protective gas, usually nitrogen.
- When the temperature rises to 1000-1100 degrees, the binder is removed, and the free space around the powder particles is impregnated with bronze (or other metal) previously placed next to the "green" model. This process is called infiltration.
Materials used for 3DP printing and their cost
Gypsum has traditionally been used in 3D printing, and water played the role of a binder in this case. However, technology has stepped forward and, as is clear from the previous section, metals (bronze, copper), sand and polymer mixtures are now also used. Dyes are mixed into the binder, which makes it possible to carry out color printing on such a 3D printer.
The cost of the simplest powders is on average 600-700 euros for a 10 kg bucket (8200 cm3), the price of the binder is about 660 euros for 3.8 liters.
Characteristics of finished products and their application
Models made of gypsum and polymers are not too strong to be used in the production cycle as a mold, however, they are quite suitable for rapid visualization of prototypes of various parts and products . It can also be used in various architectural and design works or in the manufacture of souvenirs.
Products using metals have better properties, however, their strength is still at an average level: tensile strength 610 MPa, hardness HRC = 10-20.
Such characteristics are quite suitable for the manufacture of plastic injection molds, which can withstand from 200 to 500 thousand production cycles. They are also used to make parts that work under friction conditions - shafts, bushings, gears, etc.
Disadvantages
- Gypsum-based products are quite fragile and can only be used in a narrow field of activity.
As a mold, it can only be used once, after which it is destroyed.
- When working with gypsum powders, a lot of dust is generated, so a good extraction is necessary.
Advantages
- High speed of building parts - about 6 mm in height per hour, with a working area of 780 x 400 mm it will be 1780 cm3, which is an order of magnitude superior to laser rapid prototyping technologies.
- Relatively low cost of consumables.
ExOne offers the following 3D printer models:
M-Flex printer model from ExOne.
Results
Printers using inkjet 3D printing technology is one of the possible solutions to implement the problem of rapid prototyping. It should be noted that despite some shortcomings, it still found a place in the market today and continues to develop actively along with many of its competitors.
Color Inkjet (CJP)
- 1 CJP Technology
- 2 Process
- 3 Materials
- 4 Application
- 5 Other additive manufacturing technologies
CJP Technology
Color Inkjet Printing (CJP) is a type of 3D inkjet printing (3DP) proprietary technology from 3D Systems.
Process
3D Systems ProJet 660 Professional CJP Printer
As with 3D inkjet printing (3DP), CJP technology involves the application of thin layers of powdered consumables, followed by the selective application of a binder polymer. A distinctive feature of the technology is the use of multi-colored connecting elements, which allows you to create complex color 3D models.
Unused materials are not removed from the working chamber during the process, but serve as a support for subsequent layers, which allows you to create objects of high geometric complexity. However, at the end of the print cycle, the residual powder can be collected and reused.
Materials
Colored tires created with a 3D Systems ProJet 660 CJP printer
Plastics with various mechanical properties that mimic rubber, impact-resistant thermoplastics and other materials are used as consumables.
For example, 3D Systems CJP printers use VisiJet PXL media impregnated with ColorBond (to strengthen color models), StrengthMax (high strength impregnation for functional models), or Salt Water Cure (environmentally friendly impregnation to increase the strength of surface layers).
Application
Color inkjet (CJP) dolls used in the ParaNorman cartoon
Color inkjet printing (CJP) technology is mainly used for prototyping products of complex geometric shapes and colors, as well as for the production of small batches finished products.
The method is used in medicine, industrial design, education, architectural design and even puppet animation.
Due to the relatively high cost of CJP printers, this technology is not yet widely used in the home and is used mainly in professional environments. At the same time, CJP technology is much more affordable than using high-precision rapid prototyping methods such as selective laser sintering (SLS) and more versatile in terms of creating color models than laser stereolithography (SLA).