3D printed castle video
Using 3D printed sand, these structures become stronger than concrete
Tech
Innovations
Rest assured, this 3D printed sand castle will withstand fire, wind, and water.
Watch next
A wildflower restoration project creates the UK's biggest grassland yet 1:16
An electric version of the classic '60s Mini Moke is driving into the U.S. 1:16
How a couple replanted an entire forest in Brazil 1:41
Trapped air pollution is the secret ingredient of these sustainable tiles 1:17
Scientists at Oak Ridge National Lab in Tennessee have discovered a way to 3D print exceptionally strong sand structures. Using a specially developed binder, the team at ORNL printed a tiny sand bridge that can hold up to 300 times its own weight.
Video Producer
(opens in a new tab) (opens in a new tab)
Teodosia is a video producer at Mashable UK, focussing on stories about climate resilience, sustainability and social good.
The projects hopes that better infrastructure will benefit the local community.
By Teodosia Dobriyanova
Tradition and innovation come together to bring sustainability to the forefront of locally sourced construction.
By Teodosia Dobriyanova
That's how they built the Great Wall of China.
By Emmett Smith
One laser farm robot a day keeps the weeds away.
By Teodosia Dobriyanova
We've lost a lot, but there is so much out there we can still save.
By Teodosia Dobriyanova
Opposites attract.
By Meera Navlakha
"I asked him."
By Sam Haysom
Which Nick toon would you take to space?
By Emmett Smith
“My brother was badly hurt before he fell, I think he discovered something he was afraid of.”
By Yasmeen Hamadeh
VirginOrbit is currently figuring out what went wrong.
By Teodosia Dobriyanova
I want one and, after watching this video, you'll want one, too.
By Matt Binder
"Oh, it's a true story. I work for the dog."
By Yasmeen Hamadeh
Will this glow-up finally end the door debate?
By Yasmeen Hamadeh
If anyone would know, it's this guy.
By Mark Stetson and Christianna Silva
Beau is afraid... and so am I.
By Belen Edwards
By signing up to the Mashable newsletter you agree to receive electronic communications from Mashable that may sometimes include advertisements or sponsored content.
3D Printed Medieval Castle Walls B: Proof of Concept Video
Jon Off CNCKing.com News,
Just finished-up my 3D Printed Medieval Castle Walls B: Proof of Concept Video which you can watch below – the actual model will be officially launched in a few days… the 3D animation is still rendering and because I’ve used transparent glass for some of it, taking longer than normal but it’s worth it… looks awesome!
This project was a lot of fun to design and print – I’m very happy with the results and as explained in the video – the Cubify software that made it possible even with my flaw which I didn’t see until after I 3D printed it and was in the final stages of getting the 3D animations ready.
You’ll notice some fuzzies in the top, not sure why this happens around the end of the 3D printing process – maybe the great travel distance causes some filament to harden but it’s very easily removed – it has the same consistency as spider’s webs.
If you look on the turret on the left, you’ll see the blue peaking through the doorway, that’s because I have the walkway going all the way through each turret – a major feature of this project I absolutely wanted to see if I could achieve using extrusion 3D printing WITHOUT SUPPORTS. You also see the depth I’ve added to the walls and inlays in the turrets themselves… there was a lot of testing involved and big assumptions made and the results speak for themselves – AWESOME!
As mentioned in the video, this is “B” of my three-step design process, the first was rather simple, I wanted to see how the archways performed and wall construction with small caps.
This print proved all my assumptions were accurate which gave me the confidence to add a whole new level of quality and detail to the print. It is quite a major design leap between the two and I’m hoping to have an equally as large one with the third and final one.
As mentioned earlier, it takes a while and a lot of failure to get to this point, like any new machine, you have to learn how to create optimal designs for it, what can and cannot be done and with each and every design choice, know the ramifications of them in the real world when making them in the virtual one. Although I really wished this was NOT THE CASE, there is no way to skip this learning curve and you can’t cram this stuff in a weekend either (though my book will help you a lot). You got to play as hard and often as you can!
Interestingly, these two prints are essentially the same dimensions with the turrets making it slightly taller – I’ll do a wrap-up of the design evolution of this project once I got a working third version but so far – Cube has performed admirably and predictably. Of course, I’ll make all these prints available so you too can print the STL on your own 3D printer on CNCKing.com.
Won’t be much longer… and if you are wondering where the idea for this came about? Look no further than my original CNC laser cut design – his platform is too small for such a large object but you can see some heavy influences throughout this model and the A and B versions of my 3D printed Medieval Castle Walls project.
Previous: City of Swan: Wood isn’t Recyclable!
Next: 3D Printing a Weaved Basket: Proof of Concept
About The Author
Free 3D file MODERN DOOR LOCK・3D printing plan for download・Cults
DOOR LOCK
Free
ASIAN DOOR LOCK
Free
antique door lock
Free
Shirt buttons
Free
Tool carrier (electronics/tools)
Free of charge
Modern clothes hanger
Free
ASIAN DOOR LOCK
Free
JST XH 8 PIN only HERE
Free
Microphone stand
Free
DOOR LOCK
Free
BRICK
Free
The best files for 3D printers in the Tools category
Wall mounted spool holder
Free
Desk Organizer
Free
Side Load Bottle Cage - Slanted
0,71 €
Thanos Infinity bottle opener.
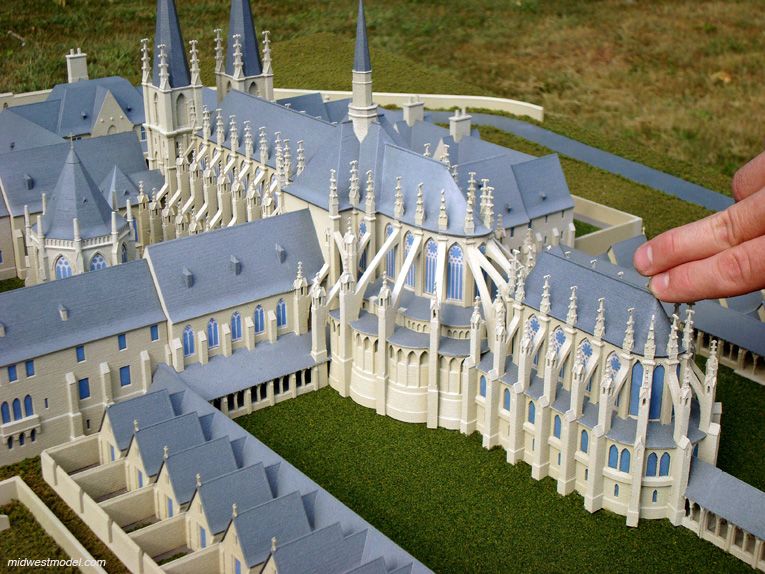
1.25 €
Ultimate-er Stringing Test
Free
DIY 3D Printed Dremel CNC
Free
nine0003 Airtight Filament ContainerFree
Zortrax Filament Tube Holder
Free
Bestsellers in the Tools category
well designed: Hemera fan duct
2.50 €
PRECISION CALIPER 3D PRINT DIY
3.12 €
Quick Print Paint Bottle Rack (6 sizes)
2.83 €
Case for Chill Buddy lighter
0,94 €
telephone ring holder
0,90 €
Generativ Design Y-Filamentsplitter Bambulab AMS-Extern RS-CONCEPTS
2,50 €
nine0003 PRECISE DIAL INDICATOR 3D PRINT DIY 1. 91 €
Bit holder Spartan 4 mm Hex
1,80 €
ENDER 3 S1, S1 PRO, SPRITE, V3 AIR DUCT FAN 5015, ACCELEROMETER, LED strip
€2.69 -20% 2.15 €
1.58 €
Ender 3 S1 Dual 40mm Fan Hot End Duct
1.42 €
Shrek Pooping Toothpaste Topper
2.85 €
SUPERBOX
1.50 €
Quick print stackable parts containers / storage boxes
2. 83 €
Paint stand with scissors
5.25 €
ARTEMIS -> Shop for Alligator 2 || 6.5" arrows || Repeating crossbow
6.25 €
Do you want to support Cults? nine0049
Do you like Cults and want to help us continue our journey on our own ? Please note that we are a small team of 3 people, so supporting us in maintaining activities and creating future developments is very easy. Here are 4 solutions available to everyone:
-
AD: Disable AdBlock banner blocker and click on our banner ads.
-
affiliation: Shop online by following our affiliate links here Amazon.
-
DONATIONS: If you want, you can donate via PayPal here.
-
* INVITE FRIENDS: * Invite your friends, discover the platform and great 3D files shared by the community!
Aircraft 3D printing: An engineer's story Boeing
Each Boeing 787 passenger aircraft has about 30 3D printed parts. Combined, Boeing Commercial Airplanes (jet airliners and business jets) contain 25,000 printed parts. And military aircraft F-15 and F / A-18 - about 40,000. Most of the components are components of air ducts, but there are engine parts and parts of the interior of the cabins. nine0006
Boeing spokesman Bernardo Malfitano spoke at the EAA AirVenture Oshkosh Aviation Enthusiast Forum and talked about how 3D printing is being used in the aircraft industry today.
Mechanic, test engineer, aircraft builder and pilot
Bernardo Malfitano has been with Boeing since 2007. In his career, he was engaged in the repair and maintenance of the air fleet, analyzed the wear and tear of aircraft. Now he is involved in the development of new aircraft. nine0006
According to the expert, all popular 3D printing methods are now used in the aerospace industry: laser stereolithography (SLA), deposition method (FDM), selective laser sintering (SLS) and direct metal deposition (DMD). Unlike traditional techniques, in which the cost of a part depends on the circulation (the higher it is, the lower the price for each spare part), 3D printed products cost the same: it doesn’t matter if you ordered 10 or 1000 pieces. Therefore, it is advantageous to use this technology for small circulations. nine0006
Where are printed parts on airplanes?
Air ducts are the part of the aircraft where 3D printed parts are most widely used today. In modern aircraft, circulating air maintains a comfortable temperature for a person and a safe pressure. 3D printed air duct connections are used in the Boeing 787, F/A-18 and F-35 fighter jets, and Bell 429 helicopters.
There are also 3D printed parts in the systems that propel the aircraft. As a rule, these are metal products made by laser sintering or metal deposition. So, in the Boeing 777, the compressor is connected to the temperature sensor using a 3D-printed adapter. And in the F-15K Slam Eagle military aircraft, casings for turbines were made using volumetric printing. This reduced the cost of the part from $34,000 to $2,550 and halved its production time. nine0006
Interior details . Shelves, brackets and various fixtures in passenger aircraft cabins are often printed in plastic. For example, the popular Boeing A350 has over 500 of these parts on board.
Small parts. End caps, parts of seats and instrument cases - all this can also be made using the 3D printing method. In the Boeing A300 passenger ship, brackets and seat belt buckles for crew seats are produced in this way. nine0006
Advantages of 3D printing for aircraft construction
Additive technologies attract aircraft designers not only because they are economical. They make it possible to optimize the shape at the model stage and significantly reduce the weight of the product. So, by replacing the cast metal bracket with a plastic one printed on a 3D printer, the designers managed to reduce its weight from 918 grams to 326. Of course, there is more than one bracket on the plane, so the total gain in weight is several kilograms. For passenger aircraft, lightening the design means reducing fuel consumption, which reduces not only the costs of the airline, but also environmental damage. nine0006
Parts with mesh and honeycomb structure are lighter than monolithic ones, but at the same time they do not lose strength. Each new sample introduced in the aircraft industry undergoes multi-stage tests, especially if it is a functional part.
Is it possible to print the entire aircraft?
If additive technologies are so good for 3D printing, is it possible to print an entire airplane? Bernardo Malfitano is sure that now it is impossible.
Today, 3D printing is successfully used to make drone bodies and working models of aircraft. At the Berlin Air Show in 2016, visitors saw the Airbus Thor, a remote-controlled aircraft about 2 meters long. All of its parts were 3D printed. nine0006
But to create the hulls of large aircraft - passenger liners, cargo planes, fighter jets - modern 3D printing technologies are not reliable enough.
Malfitano explained that the US has statutory manufacturing standards. The aircraft industry is governed by 14 CFR Part 25 (“Airworthiness Standards: Transport Category Aircraft”). It says that the structure of the materials must be strong, and the details must be reliable, which must be confirmed by certain tests. Meanwhile, testing parts created by 3D printing often reveals defects and inhomogeneities. nine0006
The second factor is the price. Aircraft manufacturing is mass production, so it is now more profitable to use traditional techniques at most nodes.
Bernardo Malfitano's entire presentation can be viewed here.
Learn more about the possibilities of today's 3D printers at the 3D Print Expo. You will see flagship models from well-known companies and a gallery of amazing art objects created using 3D technologies.