3D printed big chungus
Free STL file Big Chungus・3D printable design to download・Cults
Han Solo Bust
Free
Luke Skywalker v2
Free
Duck Headphone Hanger
Free
Daenerys
Free
Slave Leia
Free
Indiana Jones Bust
Free
Conan The Barbarian
Free
T-800 Full body
Free
Best 3D printer files of the Art category
The Sims Plumbob LED Hat, A Casual One Piece Costume, Wearable Plum Bob Sim Diamond with Headband Strap for Cosplay, Comiccon, Halloween
€7. 69
Articulated Moloch horridus, Thorny Devil, spiked lizard
€1.88
squid game pink soldier
€17.29
Annie Leonhart - Attack On Titan - Shingeki no Kyojin
€19.21
Chibi Dino. Self balancing.
€1.16
Low Poly Masks
€2.88
Boo!
Free
GOLGOTH 2 GORU GORU
€3
Best sellers of the category Art
Bearded Dragon Articulated Toy, Print-In-Place Body, Snap-Fit Head, Cute Flexi
€3.34
FLEXI PRINT-IN-PLACE STANDING YETI
€2.83
Flexi Print-in-Place Phoenix
€3. 79
Cute Flexi Print-in-Place Squirrel
€2.41
Cute Flexi Print-in-Place Fox
€2.40
Bat articulated toy, print-in-place body, snap-fit head, cute-flexi
€3.34
ZOU GHOST - GHOST WITH LEGS
€2.76
Leopard Gecko Articulated Toy, Print-In-Place Body, Snap-Fit Head, Cute Flexi
€3.34
Flexi Print-in-Place Skeleton Hand
€1.91
Stitch Love (Easy print no support)
€1.50
Cute Flexi Print-in-Place Sloth
€2.83
Baby Crystalwing Dragon, Cinderwing3D, Articulating Flexi Wiggle Pet, Print in Place, Fantasy
€3. 84
Cute Flexi Print-in-Place Skeleton
€2.83
Flexi Print-in-Place Astronaut
€2.83
Cute Flexi Print-in-Place Elf
€1.87
Biting dragon
€3
Would you like to support Cults?
You like Cults and you want to help us continue the adventure independently? Please note that we are a small team of 3 people, therefore it is very simple to support us to maintain the activity and create future developments. Here are 4 solutions accessible to all:
ADVERTISING: Disable your AdBlock banner blocker and click on our banner ads.
AFFILIATION: Make your purchases online by clicking on our affiliate links here Amazon.
DONATE: If you want, you can make a donation via PayPal.
WORD OF MOUTH: Invite your friends to come, discover the platform and the magnificent 3D files shared by the community!
▷ big chungus 3d models 【 STLFinder 】
Big chungus
myminifactory
A hollow Big Chungus
#Statue of Big Chungus
thingiverse
Big Chungus on Statue of Liberty
Big Chungus Base
thingiverse
I printed the Big Chungus by Toshi_TNE, and wanted to really make something to glorify the great Chungus. So I made this base for the bust to sit on.
Toshi_TNE's bust: https://www.thingiverse.com/thing:3315507 It's states on each side...
BIG CHUNGUS 3D model
cgtrader
This is my rendition of Big Chungus. Use this in your projects, and be imaginative as possible with your ideas! I mean, come on, how much closer can you get to the original? BUY NOW! Only $3!!! if there are ANY issues with this model please let me...
Big Chungus Hood Ornament
thingiverse
Added onto the big chungus thing so that it could be attached to a gopro mount and then attached wherever you want! I use mine as a hood ornament.
...
Orient it as you wish, I like to orient it so that he is "laying down on his side"
This is the...
Big Chungus Stamp Thing idk...
cults3d
its a plate with big chungus on it what more could you want...
Sus Big Chungus -Among Us
thingiverse
It is exactly what it looks like. ...The most suspicious Big Chungus
Big Chungus
cults3d
Zbrush doodle. Whiskers not included, I plan on making them out of a piece of wire. ...Happy holidays.
BIG CHUNGUS
thingiverse
Customized version of https://www.thingiverse.com/thing:3045130 Created with Customizer! ...https://www.thingiverse.com/apps/customizer/run?thing_id=3045130
Big Chungus
thingiverse
Zbrush doodle. Whiskers not included, I plan on making them out of a piece of wire. Happy holidays. UPDATE: Added version without a base as requested. This will be the last thing I'll upload. Some people don't seem to understand what non...
big chungus
sketchfab
I asked my followers what animal should i draw.
Big Chungus bobble-head
prusaprinters
It is based on MrNICE's chungus model. ...The spring and base are generic.</p>
Big Chungus Low-poly 3D model
cgtrader
Bugs Bunny is Big Chungus. ...
BIG CHUNGUs prusa topper
thingiverse
sus
big chungus projector
thingiverse
Customized version of https://www. thingiverse.com/thing:2094215 Created with Customizer! ...https://www.thingiverse.com/apps/customizer/run?thing_id=2094215
Ender 3 Pro Knob The Rock Big Chungus
thingiverse
The Rock & Big Chungus Ender 3 Pro Knob. ... Supports are optional, I printed mime without any support.
BIG CHUNGUS Bike Stem topper
thingiverse
Wanted to keep the steerer tube on my bike original length; should fit on any standard 1 1/8th threadless fork. ... That'll hold 'em alright.
Big Chungus but with an appropriate number of polygons
thingiverse
I found the other model had a few too many polygons so I reduced it (by 92%)
Big Chungus but with an appropriate number of polygons and support for teeth
thingiverse
Found this but saw that the teeth failed added some supports just in his mouth.
... Will print latter and update results.
Big Chungus but with an appropriate number of polygons and support for teeth
prusaprinters
<p>Found this but saw that the teeth failed added some supports just in his mouth.</p> <p>Will print later and update results.</p> <p>Edit: Had to change XY compensation to 0.1 (Prusa Slicer) as the supports wouldn't appear in the slicer.</p>...
Chungus Trump Big Trumpus
thingiverse
Print in orange for greatest effect
dwayne the rock chungus
thingiverse
i was bored so i made a rock big chungus
Dwayne The Rock Chungus
thingiverse
I have a Rock and i have a Big Chungus Now i created a Dwayne The Rock Chungus
Buddha Chungus
thingiverse
This is a combination of "Pop Buddha" by tamraz and "Big Chungus but with an appropriate number of polygons" by jrddupont.
The Meme is old but it checks out. ...
King Chungus
thingiverse
Glorious Timelapse video: https://youtu.be/z1NPgZli6P8 Models used: Big Chungus: https://www.thingiverse.com/thing:3315507/files Fortnite hand cannon: https://www.thingiverse.com/thing:2821249/files Bowsette super crown:...
THE ALMIGHTY CHUNGUS
thingiverse
... He even has a giant poster of Big Chungus on his closet door. I've currently printed three Chungi. (This number will go up, so check in to see how many times I've printed it! ... Edit this design: https://www.tinkercad.com/things/8sLVg5hs0ly
buddha chungus
cults3d
Behold the buddha chungus in all his big glory
buddha chungus
thingiverse
Behold the buddha chungus in all his big glory
The Carrot
grabcad
Its for big chungus
haha
myminifactory
Big chungus meme 2019
17 real buildings printed on a 3D printer - The Future on vc.
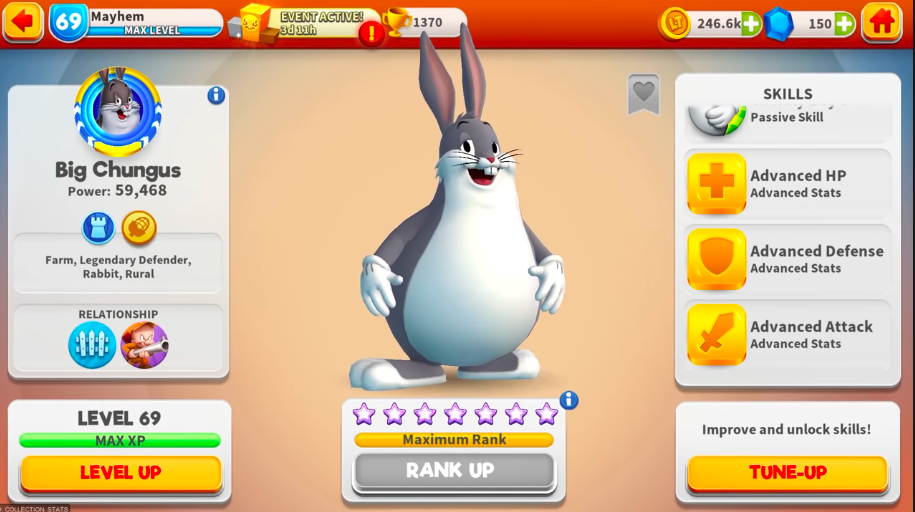
3D printing technologies are developing extremely fast and are used in various areas of human life.
42,981 views
Recently, much attention has been paid to the printing of buildings, and printed houses are increasingly appearing in recent years in different countries of the world - in the USA, Saudi Arabia, Mexico, France, Russia, the United Arab Emirates and others. I have prepared a list of existing 3D printed buildings for 2020.
What is a 3D printer for construction.
Today's 3D construction printers differ in designs and wall construction methods. The most common printers are portal construction, two- and four-support construction, based on a manipulator arm or a circular design. The equipment allows you to create small architectural forms and elements of structures for their subsequent assembly on site, or allow you to print the entire building on the construction site. The height and dimensions of the printed building depend on the specifications of the printer being used.
How the printing process works.
The extruder extrudes a fast-hardening concrete mixture with various additives. Each subsequent layer is applied on top of the previous one, due to which a vertical structure is formed. The concrete layers below are thus compacted, thereby increasing their ability to withstand the next layers, and hence the entire weight of the structure. To strengthen the structure, it is reinforced, which can be both vertical and horizontal. The laying of the horizontal armored belt is carried out between the layers, the vertical reinforcement is installed after the composition has hardened, and then it is poured with concrete.
Advantages of 3D printing over other construction methods.
3D printer fabrication opens up great opportunities for construction and related industries. Practical application has revealed the following advantages of additive manufacturing:
- It removes the limits from the imagination of designers and architects who design buildings, as it provides opportunities that are not available with the construction methods we are used to.
- High speed of construction of buildings and structures.
- Complete process automation.
- Low power equipment.
- Significant savings compared to conventional construction methods by reducing labor and energy costs and accelerating construction time.
- The formation of waste building materials is completely eliminated.
- Minimization of human intervention in the construction process not only allows building in places inaccessible to people, but also eliminates the human factor in ordinary territories and reduces the likelihood of error.
1. June 2014. China. China's Shanghai WinSun Decoration Design Engineering Co has unveiled 3D printed houses at an industrial park in China's Jiangsu province. A total of ten houses were created, each of which cost a little more than three thousand pounds sterling. Over the next ten months, the technology improved and the company produced several different types of buildings for the exhibition, the tallest of which has five floors.
2. August 2014. USA. Andrey Rudenko's company Totalkustom printed the lock. The printing took a total of 2 months. The machine's printing speed was 50 cm in 8 hours. The main part of the castle, measuring 3m x 5m and 3.5m high, was printed as a single unit, and the towers were then printed separately.
3. July 2015. China. Chinese company Zhuoda assembled a two-story house in record time. The modular home, made up of six 3D printed modules, was assembled on site in less than 3 hours. Of course actually about 90% of the work was carried out in the company's workshops, and on the site they were only assembled into a single building.
4. September 2015. Philippines. Andrey Rudenko's Totalkustom company built apartments on the territory of a hotel in the Philippines, 10. 5 mx 12.5 m in size and 3 meters high. The building was built using local materials - sand and volcanic ash.
5. May 2016. UAE. Chinese company Shanghai WinSun Decoration Design Engineering Co printed prefabricated structures for the subsequent assembly of an office building in Dubai. The area of a one-story building is about 250 square meters. m.
6. March 2017. Russia. Apis Cor introduced the first 37 sq. m.. The printed house has an interesting shape, but as the participants themselves say: this is just to show the flexibility of printing technology, the shape of the buildings can also be the usual square. Compared to other construction 3D printers, this printer is very compact (4×1.6×1.5 m), weighs 2 tons, and can be easily transported to the construction site.
7. October 2017. Russia. In Yaroslavl, the company Spetsavia presented the first residential building in Europe and the CIS, built using construction 3D printing technology. Construction of the house began in 2015. The box of the building was printed by a portal printer piece by piece and then assembled on the foundation in one month in December 2015. In the summer of 2017, the roof was completed and the bulk of the interior finishing work was carried out.
8. March 2018. France. Yhnova presented a five-room one-story house with an area of 95 square meters. For its construction, the engineers used a large manipulator, at the end of which an extruder for polyurethane foam is fixed. While working, he applied the foam in accordance with the 3D model of the building loaded into it. After applying the foam, the builders periodically filled the erected part with concrete, and also inserted the frames of doors and windows.
9. March 2018. USA. American Company Icon built a prototype home in Texas to prove the technology's performance. The area of the building was 32 sq.m., printing was performed by a portal type 3D printer moving along rails installed on the site.
10. July 2018. Spain. Be More 3D printed a 24 m2 concrete building. For the construction, a two-support 3D printer was used, the width of which is 7 meters and the height is 5 meters.
11. September 2018. Denmark. 3D Printhuset printed a 50 square meter office in Nordhavn. The 3D printer used for printing is of the portal type and has a size of 8 x 8 x 6 meters. Print speed 2.5 meters / min. Each layer is 50-70 mm. The print material is concrete made largely from recycled tiles and sand.
12. October 2018. Italy. Company Crane Wasp using a three-bearing construction 3D printer erected a building in ten days. The house uses passive solar heating technology and natural ventilation. The composition for printing was created on the basis of waste from rice cultivation (it was 25% local soil (clay and sand), 40% straw, another 25% - from rice husks and 10% - from hydraulic lime).
November 13, 2018. Italy. Arup in collaboration with the architectural bureau CLS Architetti erected a building in 1 week with an area of 100 sq.m. The building was printed in segments with subsequent assembly at the construction site.
November 14, 2018. Saudi Arabia. The Dutch company CyBe Construction has completed the construction of a building with an area of 80 sq.m. It took about a week to 3D print the necessary elements, and a little more than a day to assemble. The walls are made up of 27 printed blocks, and the parapets needed another 21 blocks to make.
15. August 2019. USA. S-Squared 3D Printers (SQ3D) showed a prototype residential building that can be built from floor to roof in just twelve hours. The house has an area of 46 m2. During the printing process, a 3D printer of a two-support design was used.
16. October 2019. UAE. Apis Cor has announced the completion of the world's largest 3D printed building. Located in Dubai, the 650 sq. meters has a building height of 95 meters and entered the Guinness Book of Records as the largest building printed directly on the construction site.
17. December 2019. Mexico. American company Icon erected two residential buildings for the non-profit organization New Story, in southeastern Mexico. The imprinted buildings have a flat roof, curved walls and an area of 46.5 square meters
As can be seen from the impressive list of completed projects, progress in the field of construction 3D printing clearly does not stand still, new techniques are constantly being introduced, various materials are being created, including from recycled raw materials, and high-tech equipment is being developed. In a short period of time, the technology has attracted the interest of a large number of enterprises that are engaged in the development of equipment, special building mixtures, libraries of structural solutions for designing buildings for 3D printing, as well as the preparation of a legislative, regulatory and regulatory framework.
I am sure that in the future the entire construction process will be able to become fully automated, without human intervention, not only when printing foundations and walls, but also when printing ceilings and roofs, automatically install utilities, doors and windows. Also, perhaps in the future we will not be limited to printing houses of 2-3 floors, but will be able to move on to multi-storey construction. All this is no longer something impossible and has ceased to sound like fantastic dreams of a high-tech future. It is only necessary to give time for the natural evolution of 3D construction technology.
How Relativity Space 3D Prints Rockets
Relativity Space Co-Founder, CEO Tim Ellis / Relativity Space / AFP
Relativity Space is printing a metal space rocket on a 3D printer it invented specifically for this purpose. Almost all: 95% is printed, and the remaining 5% falls on electronics, seals and some other elements. 3D printing has many advantages. She's cheaper. She's faster. It is made on the spot, no need to wait until the parts are brought from another factory. It is stronger: fewer places for fastening parts. “The Shuttle had 2.5 million parts,” says Relativity Space co-founder Tim Ellis. “According to our estimates, SpaceX and Blue Origin have reduced this number to 100,000 per rocket. We have a thousand - less than in your car.
Many space companies use 3D printing, but only for individual components. Skeptics insist that no one knows how the printed rocket will behave during takeoff and in space. So far, the startup's first rocket, Terran 1, has successfully passed all ground tests. The first copy for a real flight is collected slowly and carefully checked. Now it is ready for 85%. A test flight is scheduled for the end of this year. But investors believe in the idea. Last November, Relativity Space completed a series funding round and raised $500 million. After that, according to research company Pitchbook, with a business valuation of $2. 3 billion, Relativity Space became the second most valuable venture capital-funded space company in the world. In 1st place, of course, SpaceX (however, Pitchbook does not include Blue Origin in the rating, which is fully funded by Jeff Bezos).
Relativity Space has since raised another round, raising $650 million, based on a company-wide valuation of $4.2 billion. reusable. After all, competitors do not sleep. Relativity Space is just one of more than a dozen rocket companies created in the last 10 years.
Launch from Mojave
Ellis was born in 1990 in Texas. He is the eldest of three children of an architect father and a dentist mother. As a child, Ellis was fond of Lego and persuaded his parents to buy about 200 sets. He immediately threw away the instructions from them and collected the spaceships he invented himself. Until now, the thumb of his right hand, when at rest, arched back more than his left - Ellis assured the Los Angeles Times that this was the result of long hours when he assembled and disassembled the parts of the designer.
As Ellis got older, he began making amateur films with his friends, mostly action movies, where the characters were often confronted by zombies. He entered the University of Southern California to become a screenwriter. But already in his first year, he became interested in the profession of an aerospace engineer and joined the Rocket Propulsion Lab at the university, which was engaged in the development of rockets.
The University of Southern California is known for its space program. Its alumni include Apollo 11 commander Neil Armstrong, astronaut and former head of NASA Charles Bolden, and Dana Rohrabaker, chairman of the House Space and Aeronautics Subcommittee. There are several laboratories where students create real rockets and satellites. “I was amazed,” Ellis recalled in an interview with the university website about the first time he went to test the rocket engine he designed and built with his comrades in the Mojave Desert. – I always advise students: take part in practical classes. So you will understand why you need to study this or that differential equation, scheme or line of code.
They wanted to be the first student group to launch a rocket into space. But, having carried out dozens of successful launches, they did not even achieve a suborbital flight - this was done by their successors in 2019, having developed more powerful engines.
Why leave Bezos and Musk
At Rocket Propulsion Lab, Ellis met and became friends with classmate Jordan Noon. Then their paths diverged for a while. Noon went to SpaceX, where he worked, among other things, on the Dragon 2 spacecraft. His emergency rescue system uses a 3D printed SuperDraco engine.
Ellis interned for three summers at Bezos' Blue Origin, and after graduation he was accepted full-time. He convinced Bezos to create a metal 3D printing division (by then many competitors, including Boeing, were doing it). He also created it from scratch. The traditional way of producing parts is turning on a lathe, stamping or casting with a mold. In 3D printing, robotic arms deposit layer upon layer of molten metal. A printed rocket has fewer parts, and therefore, places to connect them using welding, rivets, etc., and therefore fewer vulnerabilities. Skeptics object that if defects are found, the entire part has to be discarded and its manufacture must be started anew. But Ellis says that Relativity Space has developed a way to restart the printing process from the right place. “3D printed rockets are the future of rocketry and space exploration,” he told Inc. magazine.
Ellis and Noon often called each other and talked about rockets, although they worked for different space companies. They put together a rough cost structure to understand why rockets are so expensive. “80 to 90% goes to wages,” Noon told Bloomberg. 3D printing can dramatically reduce these costs.
Ellis once mentioned that he was going to start a startup to 3D print entire rockets. He later admitted to Inc. that he tried to get Bezos to print more parts for the rocket, but his suggestions were never fully implemented. Then he decided to take up rocket science himself. Noon liked the idea. Both left in December 2015 to create startup Relativity Space.
“I never saw him give up, give up, or fail to solve a problem, even a really difficult one,” Ellis told the Los Angeles Times of Noon. “I knew our startup was going to have a lot of problems, and he was the right person to make it all work.” And Noon noted: “I am strong in technical and practical aspects, and Ellis is strong in creative thinking and non-standard solutions.”
For 1 kg of satellite
Relativity Space received its first money from venture investor Mark Cuban. Ellis and Noon made about 20 attempts to guess Cuban's email address, as Cuban preferred texting to other forms of communication. Some of the letters were returned with a note that such an address does not exist, some got to other people. But one of the addresses turned out to be correct, and Cuban read the letter with the headline "Space Is Sexy: 3D Printing of an Entire Rocket. " Ellis and Noon asked for $100,000. Cuban, after five minutes of texting them, agreed to invest $500,000 (although they had to wait two months to check if they were fraudsters). “They are smart, resourceful, driven and always learning,” Cuban wrote in an email to The Times. “These are exactly the traits I look for in innovators.”
First, the startup needed to create a huge 3D printer - there were no models on the market suitable for their purposes. A lot of effort was put into this. But now the latest generation printer is able to print a part up to 32 feet (almost 10 m) high, while the height of the Terran 1 rocket is 115 feet (35 m). Ellis and Noon say that even if the rocket venture fails, they can always cash in on the sale of industrial 3D printers.
Terran 1 /Relativity Space
Created with Cuban's money, the first printer could print parts half the size of the last generation. But the working rocket engine printed on it made an impression on investors. First, they invested almost $10 million in the startup, then another $35 million, and in October 2019d. - another $ 140 million. Ellis and Noon planned to stop there. They did not want to dilute their share, and the funds raised should have been enough for the time before the first commercial launch, if they worked without haste. But in November 2020, another $500 million round of funding was raised. As Ellis explained to CNBC, “the development and scaling of the project needs to be accelerated.” That summer, the startup moved to a new 11,000-square-meter headquarters in Long Beach, California. m, where there will be a site for the production of rockets (the most important thing is that their new printer climbed there in height). Over the past year and a half, the company has more than doubled the number of employees. She now has 400+ people and plans to hire 200 more this year.
Ellis told Inc. that they already have $1 billion in launch contracts from government and commercial entities. Terran 1 can carry up to 1250 kg of payload. This is smaller than SpaceX's Falcon 9, but larger than Rocket Lab's Electron. Relativity Space is targeting a mid-sized satellite niche, much like a car, Ellis said. Its competitors are the Russian Soyuz-2-1V and the European Vega. Or the same Electron, if Terran 1 displays several small satellites at once.
The launch cost of Terran 1 is $12 million, i.e. slightly less than $10,000 per 1 kg. Last year, Roscosmos CEO Dmitry Rogozin announced a more than 30% reduction in the price of launch services for a number of satellites to the level of SpaceX: to $15,000-17,000 per 1 kg instead of $20,000-30,000.
Target - Mars
The competitive advantage of Relativity Space is not only in cost, but also in the fact that it can print a rocket to customer requirements, changing both the diameter of the rocket and the shape of the fairing for the satellite - of course, within the limits allowed by aerodynamics, Forbes explained. And she can do it quickly. Once the technology has been proven in practice, Relativity Space is going to print the rocket in 30 days and take another 30 days for pre-launch tests, Ellis told Scientific American. According to him, even SpaceX takes 12 to 18 months to build a conventional rocket. But Musk claims that his reusable rocket is ready for a new flight 51 days after the previous launch.
So in June, Relativity Space raised another $650 million from investors to accelerate the development of its own reusable Terran R rocket (of course, also almost completely printed on a printer). Its first launch is scheduled for 2024. It will be larger than the first one - 216 feet (66 m) high and designed for 20 tons of payload.
For Ellis and Noon, the main thing is that this project is another step towards interplanetary flights. Musk is looking for a way to get colonists to Mars, and Ellis and Noon are hoping to help them settle on the Red Planet. "If you believe - and I believe - that Elon [Musk] and NASA will send people to Mars, then <...> they will need a whole bunch of things," Ellis told CNBC. “Our printers are reducing the amount of infrastructure that would need to be transported from Earth to Mars in order to establish a colony there,” explained Noon Inc.