3D print spur gear
3D Printed Gears | igus®
- Home
- Custom Parts Services
- 3D printed gear
Upload CAD data and order
Create CAD file of your gears
Use the gear service life calculator
Additive manufacturing for low-wear gears, spur gears, bevel gears, sprockets and worm wheels
Our 3D-printed gears are made of low-friction, maintenance-free, self-lubricating plastic printing materials that have been engineered to last up to 50 times longer than standard 3D-printing materials inside moving applications. We extensively test our iglide® polymers inside our 41,000ft.2test laboratory to ensure every 3D-printed part offers exceptional wear resistance comparable to injection-molded components. All gear types can be customized to meet your requirements, including weight, tooth shape, and transmission ratio, and can be printed with a wall thickness of 0.5mm or more.
Benefits:
- Gears, spur gears, bevel gears, worm wheels, sprockets and more made of durable iglide® materials
- Shipped in 24 -72 hours
- Individual gears - no minimum order quantity
- Long service life thanks to optimized tooth shape in our gear configurator
- Low-wear and friction-optimized iglide® materials to choose from
- Service life and specifications comparable to iglide® injection-molded parts
Gears made of wear-resistant polymers
POM vs. iglide® I6: downtime at POM, iglide® I6 hardly any abrasive wear
Test parameters:
- Torque: 4.
9Nm
- Speed: 12 [rpm]
- Counter partner: hard anodized aluminum
- Duration: 2 months
1. POM: 321,000 cycles: High wear
2. POM: 621,000 cycles: downtime
3. iglide® I6: 1 million cycles: low wear
Test result: We tested a variety of 3D-printed and mechanically manufactured polymers in the worm gear test. No other polymer reached as long of a service life as our wear-resistant iglide® I6 material (in SLS 3D printing). Worm gears made of iglide® I6 are also used inside our robolink® robotic arm modular system.
Calculate service life of your gear
Our service life calculator allows you to optimize the size, number of teeth or teeth module of your gear to improve its durability.
Use the gear service life calculator
3D printing service
Use our online gear shop to print gears, spur gears, bevel gears, sprockets and worm gears made of our low-friction, self-lubricating, maintenance-free iglide® polymers. iglide® lasts 50 times longer inside moving applications than standard 3D-printing materials.
Visit our 3D printing lab
We continuously test the tribological properties of our iglide® materials inside our 41,000-square-foot test lab.
Filament and laser-sintering powder made of iglide® polymers
- Up to 50 times more abrasion resistant than standard material
- Wear-resistant components for prototypes and small batches
- Simple processing
- Ideal for tribological applications
- Self-lubricating and dirt resistant
Learn about our 3D printing materials
Discuss your project with a 3D Printing expert
Whether you're interested in turnkey, fully assembled solutions or looking to build your own customizable project, learn more about how igus® can assist you with a solution based on your specific application and requirements. Contact us via the form below or call us at (800) 521-2747 to discuss your project today!
Contact an Expert
3D Printed Gears: Guide & Best Free Downloads
3D printing your own working mechanisms is a big part of a lot of the more complex 3D printing projects you’ll come across. Naturally, many of these homemade mechanisms need 3D printed gears to work.
Whether it’s as cool fidget toys or part of a larger project, making reliable 3D printed gears is often the linchpin of a design.
Like different ways of tying knots have their own specific purpose, there are also a lot of different gear designs suited to what you’re building. 3D printing a simple cog-style gear will work for some mechanisms, while it won’t be viable for others.
Here we’re going to look at how to 3D print gears, what kinds you can print and why, and also some useful hints and tips to keep in mind when printing. By the time you’re done here, you’ll have all the know-how to print your own gears with confidence!
Common Uses for 3D Printed Gears
In this electrical age of ours, it can be hard to think about what gears are actually used for these days. Generally speaking, when we think of gears we often think of old factories, steampunk settings, and ancient Indiana Jones-style trap mechanisms.
But gears do still play an important part in a lot of machines and tools even now. Most mechanical locks still use gears and tumblers to work, as do analog watches, pulley mechanisms, and tools like woodworking and car repair equipment.
Even fun things like homemade fidget toys use 3D printed gears as a primary staple. The mechanical concepts of speed and torque are applied to gears to make toys like Beyblades too, which you can also 3D print.
You can even use 3D printed gears to repair or enhance other machines like this geared extruder and this gluing gear print for general maintenance. Any of these designs are worth saving if you plan on working with mechanical prints for a while yet, but they also work well as one-off projects to further your 3D printing journey.
These kinds of gears are much cheaper than visiting repair stores or getting custom-made designs from professionals. As 3D prints vs. traditional metal gears, they won’t last as long, but they’re a good option if you’re on a budget or just prefer to fix or make things yourself.
3D Printing Gears: Ideal Filaments
Different 3D printing filaments are better suited to different projects. Gears are designed to be in near-constant motion, so the filament you use should be durable to ensure longevity and reliability.
The nature of 3D printing means you’ll never really have anything as strong and tough as something factory-made and metal, but that doesn’t mean there aren’t a few things to keep in mind to ensure you get the best results.
Naturally, you’ll want to use the strongest filament available to you to 3D print your gears.
These include filaments like:
- Nylon
- Polycarbonate
- PETG
But, if none of those are available you can actually 3D print gears using PLA if that’s all you have available.
PLA may not be the first choice when it comes to strength, but with careful measurements and post-processing, you’d be surprised at how well it holds up over time.
If you’ve got the means, though, then I recommend using PLA+ if you can. PLA+ is an enhanced version of PLA in terms of durability and longevity. While more expensive, and a little trickier to find, PLA+ has been proven to make surprisingly reliable 3D printed gear mechanisms before.
Cool 3D Printed Gears
Now that you know what to do, it’s time to get printing gears! While you’ve probably got some ideas in your head already, there are still plenty of cool 3D printed gear designs and projects out there to sink your teeth into.
Here we’re going to look at a few of the best 3D printing projects that use gears practically in their designs.
Spider-Man Web Shooter
Maybe not the first thing that came to mind when thinking about 3D printed gears, but definitely the first one I wanted to talk about.
This working Spider-Man web shooter uses small 3D printed gears originally designed for watch repair to shoot webs just like everyone’s favorite web-head!
Walking Cat
Gears are an important part of many moving mechanisms, and this walking cat makes for a great project both in general and also for testing out your skills with 3D printing gears.
As well as being a fun toy and a great way to get used to the more complex designs 3D printing is capable of, the walking cat also uses plenty of different gears at different sizes and angles.
This makes it both a great project to sink your teeth into, as well as an excellent learning resource to see how different gears interact with each other in one mechanism.
Planetary Gearbox
Another great learning resource, as well as a fun print, is this planetary gearbox. It works like a numbered padlock, but with the inner workings visible to you.
This not only looks cool, but also makes for a good introduction to the basics of gear functionality as well as a learning tool for children or beginners in mechanical engineering.
Lotus Automata
One of the coolest (and prettiest) 3D printed gear mechanisms I’ve come across is the lotus automata, a hand-cranked display piece that opens up like a real lotus flower.
While you’ll need plenty of different prints with different colors, the outcome is a great centerpiece that works well with different kinds of gears to make a fun and beautiful print that’s well worth the time and effort.
Types of Gears
There are a lot of kinds of gears, each with their own ideal purposes. Knowing which one is best for you is important for making sure your mechanism works at peak performance.
While it’s unlikely you’ll be 3D printing generators or high-end water pumps, we’re going to briefly go over what kinds of gears best fit which uses so you’ll have a better idea going forward.
Spur Gears
Spur gears are what most of us picture when we think of gears, and are the most common type of gear to 3D print.
Spur gears are simple toothed cogs that move with each other for mechanisms like pulleys and clocks, and are very useful in a variety of sizes to keep machines ticking along nicely.
Helical Gears
Helical gears are best described as curved spur gears. They are capable of withstanding more torque than their simple counterparts, and are commonly used for more load-bearing machines like generators and high-strength pumps.
Worm Gears
Worm gears employ a changing parallel design. Unlike standard gears, they can be manipulated to lock in place. This comes in handy for self-locking mechanisms like doors and hard packaging.
Worm gears effectively work against each other, and require a lot more care and maintenance as this causes a lot more wear over time.
Bevel Gears
Bevel gears are cone-shaped gears that work perpendicular to each other. The curved teeth and size difference between two touching gears mean they can handle a lot more speed than most other gear types with ease.
Bevel gears come in a lot of different types on their own, which we’re not going to go over here. The most common uses for these are in fast-moving machines and tools like vehicles and power drills.
While bevel gears can be 3D printed for fun and practical uses, their most common uses aren’t ideal for 3D printing as the heat generated by the speed is too much for most filaments to handle.
Rack and Pinion Gears
Rack and pinion gears involve one gear moving with a straight, toothed line. Designed to move back and forth seamlessly, they work best as guides for steering mechanisms on tools and vehicles as well as weighing scales and seesaws, which need to move in two directions with ease.
How to 3D Print Gears: Helpful Tips
As you’ve probably already guessed, 3D printing gears requires more preparation and precision than the average print. To make sure you get working gears, you’re going to need to think and plan ahead, especially if you’re printing your gears from scratch.
Here are some helpful steps and tips to make sure you get reliable results.
Plan Before You Print
Careful planning is an important step in any 3D print, but it’s even more important when you’re printing working mechanisms with moving parts.
While a millimeter or two in any given direction won’t make much of a difference in most 3D printing projects like statuettes and ornaments, with gears it can mean the difference between a functioning mechanism and a weird paperweight.
Always double-check your measurements before you get printing. You can do this with particular precision if you have particularly good STL editing software that can test your mechanisms before they’ve even been printed.
Test and Prototype
There’s nothing worse than having a great design only to find out all too late that it doesn’t quite work. The waste of both materials and time is always frustrating, which is why testing and prototyping is a great way to avoid this annoyance.
Scaling your design down before printing is one way of prototyping. The print will use less material overall and take less time to print. What you’ll have will be a miniature version of your gears so you can see for yourself if they fit well together and work as they should.
Just be sure to scale the model down exactly without tweaking anything else, otherwise you’ll get inaccurate measurements that will ultimately be useless as prototypes.
It’s not just the gears you’ll want to test, though, so be sure to also scale down the shaft on which the hears will be turning. The distance between the gears is just as important as the teeth fitting together, so be sure to test every inch of your mechanisms before beginning what will hopefully be the final print.
Make Notes and Save the Files
Once you’ve got a working file, be sure to save it as is so you can return to it at any time. This will help for not only duplicate prints, but also later repairs and sharing with your friends.
As mentioned above, 3D printed gears won’t last as long as traditional metal ones, regardless of what filament you use. So keeping the file safe and easy to find will be handy when you need to replace worn parts.
FAQs
Are 3D printed gears any good?
Generally speaking, 3D printed gears won’t be as durable as store-bought metal gears. This isn’t to say they’re not good, however, and with enough careful planning, 3D printed gears will be perfectly workable.
Is PLA strong enough for gears?
Despite being one of the weaker filaments, PLA can be used to make 3D printed gears. While other filaments like nylon and PETG are preferable, PLA will still do the job. If you must use PLA, we recommend looking into PLA+ for any 3D printed gears and moving parts.
How do you 3D print gears?
3D printing gears is as simple as any other project, the main thing to keep in mind is the precision of both the gear teeth and the shaft. With enough planning and prototyping, you can make working gears with just about any FDM filament.
How do you attach 3D printed gears to a shaft?
If you’re working with a pre-existing design, your gears and shaft should already fit together easily. However, if you’re designing your gears from scratch, you’ll need to make sure the shaft and the gear opening match in size.
Gears can be attached to shafts using screws or adhesives. For 3D printed gears, adhesives work better as they will be easier to remove for future repairs.
90,000 workers made on a 3D printer of polymers with improved friction propertiesExtremely long-term worker service life with improved sliding properties
Test parameters:
- Moment 4.
9NM
- Speed: 12obs
- Material Material Material Mater : hard anodized aluminum
- Duration: two months
Rating
► POM (turned): Complete failure after 621,000 cycles
► iglidur I6 (laser sintering): Low wear after 1 million cycles
3D printed gears based on high quality iglidur polymers
► Predictable service life
► All geometries available: special shapes and wear pieces
► Improved tooth base geometry for longer service life
► Self-lubricating properties: running without lubrication thanks to solid lubricants
Up to 5 times longer service life than conventional polymer gears
Tried and tested: gears made from iglidur material show a significant increase in service life compared to gears made from traditional polymers made by machining or injection molding .
Which material is best for which type of transmission?
- iglidur I3 is characterized by increased strength and is especially suitable for spur gears, as well as helical bevel gears, the material can be used for all other types of wear-resistant transmission mechanisms.
nine0010
- iglidur I6 has improved sliding properties and is therefore ideal for worm gears or other gears where food grade requirements are required.
- iglidur I8-ESD suitable for making gears that need to be antistatic, e.g. for ATEX zones
Our customers equipment with 3D printed gears
Polymer gear for engine tuning
The Formula Student Team from Weingarten near Ravensburg was also looking for specially designed polymer gears for racing cars. Gears were used as chain tensioners as part of the chain drive, so they had to be especially strong. Unfortunately, the production of gears of non-standard sizes takes a lot of time, the classic production process on a metal-cutting machine is a time-consuming undertaking. nine0027 igus® 3D printing service made it possible to deliver and test polymer gears in less than 72 hours. The material used was iglidur® I6, which has the special wear properties of - it retained its full functionality after 1 million cycles in the test lab, making it ideal for use in race car construction. In this case, the special components produced by additive manufacturing not only managed to be delivered to the customer in the shortest possible time, but they also turned out to be more durable and economical. nine0007
3D printed race car gears
Layered Polymer Gears for Silent E-Bikes
Strong, wear-resistant, no lubrication required: polymer properties outperform metal
Light weight and quiet operation are especially important for e-bike construction.
" The standard metal gear makes a lot of noise during operation. We removed it and gave it to igus® for 3D printing using iglidur I3 material. Everything was simple and fast. We used the 3D printing service, downloaded the appropriate "
3D printed chain sprocket for electric bikes
3D Printed Resin Gears for Prototyping
iglidur® I6 gear train for electric vehicle charging system
Easelink, a Graz-based company, has developed "Matrix Charging", a charging system that automatically connects to the underside of an electric vehicle to charge it while parked. To develop an economical and high-quality system, the designers chose prototype gears made from iglidur® polymers using additive manufacturing technology. The igus® 3D printing service ensured fast delivery, testing and development of simple elements until the perfect result. iglidur® I6, a particularly wear-resistant and lubrication-free laser sintered powder material, is ideal for the construction of gears, shafts and other heavily loaded components that typically require regular lubrication and maintenance as well as frequent replacements. nine0007
Rapid gear prototyping with laser sintering technology
Previous NextWear test for 3D printed products
iglidur polymers are more wear resistant than PLA, ABS and other materials and manufacturing processes
nine0004 Comparison of 3D printing resinsWhy 3D printing at igus?
More information about
- Our materials
- additive manufacturing
- Services and support
3D printing information
3D printing news
Industrial 3D printing innovations. New products and services for additive manufacturing based on wear-resistant polymers. nine0007
Overview of our innovations
FAQ: Q&A
iglidur 3D printed worm gears
What is iglidur I6 and why is it a great material for worm gear design?
iglidur I6 is a laser sintered material specially developed for the production of worm gears. In addition to the common advantages of all iglidur polymers, such as wear resistance and no need for lubrication, iglidur I6 has special sliding properties that increase the functionality of the worm gear. The idea of developing such a material came from the design engineers who created our robolink robotic arm. In tests, worm gears made from iglidur I6 have repeatedly proven to be more wear resistant than other 3D printed polymer worm gears. Polymer worm gears are suitable for industrial applications only if they are made from high quality polymer. Early tests with PLA and ABS materials failed because the high coefficient of friction caused components to wear relatively quickly. It is for this reason that designers began to develop new polymers with the required properties. Special versions are available for high temperature or food processing applications. Wear resistance tests of these materials confirm that they are characterized by a high degree of wear resistance. The characteristics of the iglidur I6 material can be found here.
nine0007
Advantages of worm gears made by 3D printer
The most important advantages are wear resistance properties, impact strength, internal resilience to reduce surface pressure, exceptional impact strength, automatic lubrication properties, corrosion resistance, quiet operation, no need for maintenance, as well as good properties for emergency operation. The most important criterion for the use of a polymer. Special materials have excellent wear resistance and hardness; high precision, detailed surface treatment; and extremely long service life, which also characterizes the work of worm gears made from them. nine0007
Advantages of polymer worm gears over metal counterparts
In principle, polymer gears are designed to run without additional lubrication, so worm gears made from iglidur on the printer run without lubrication. The user benefits greatly as downtime and maintenance costs are greatly reduced when high quality polymer worm gears are used. The 3D printer manufacturing method provides design engineers with a more flexible approach than turning and milling metal or polymers. Worm gear geometry can be perfected first and compromises deferred until later. The improved geometry means it takes more time to design polymer worm gears than milled gears. Surface pressure and wear properties are significantly reduced due to large contact areas. nine0007
Which equipment is best suited for metal gears?
Usually a worm wheel is used at the outlet of the gearbox. Traditionally, it is made of a copper-tin alloy. This material has excellent properties in dry conditions when interacting with steel components. This is an important argument in favor of the use of metal worm gears in conditions where a large amount of heat is generated or high torque is transmitted. Worm gears made of metal are also often part of the cooling and lubrication circuits. In many cases, the worm is made from hardened steel and is used in conjunction with a worm gear made from a softer metal such as brass or bronze. However, self-lubricating polymers for the manufacture of worm wheels are increasingly being used. nine0007
Requirements for the design of the worm wheel or worm gear
The design of the worm gear and worm gear requires a very precise unification of the geometry of the tooth profile. This is necessary to transmit the specified torques, as well as to ensure wear resistance and abrasion resistance of the tooth profile. Simple and cost-effective technologies for the production of piece products and small batches of products are important if the found design solution is to be transferred to a computer and 3D printing systems, which makes them commercially attractive. nine0007
Worm gear material combination
Hard anodized aluminum gear worms are especially suitable for heavy duty applications. However, the corresponding gear worms, which are 3D printed by igus in iglidur I3, are strong enough for normal loads, as the material is highly resistant. Another significant advantage is also the absence of restrictions on the design of forms, since even complex and rare forms of the worm mechanism, such as globoid screws, can be made on a 3D printer, and quickly and inexpensively. nine0021
What is a worm gear?
The worm gear is the counterpart to the worm in the worm gear. Since the sliding properties are especially important for worm gears, they are usually made of bronze. 3D printing worm gears from high-quality polymers costs many times less and, importantly, is faster, and at the same time has comparable characteristics.
What is a worm gear?
Worm gears are used where reliable, precise and quiet gearbox operation is required. Quiet and durable operation is of particular importance. Worm gears can be used to realize axial movement between the drive and the power take-off. On a small area, a significant force is transformed. Therefore, the main applications for worm gears are conveyor systems, robotics, profile processing, separators, extruders, mining machines and rowing machines. Worm gears are used in presses and rolling mills, theater and stage equipment, actuators for construction machinery and lifting equipment. nine0007
How does a worm gear work?
A worm gear is a special type of gear in the shape of a worm. The tooth moves around the gear shaft in a similar way to the movement of a screw. The mating gear is the worm gear. The worm can be represented as a spur gear with a diagonal thread. The peculiarity is that it has only one tooth. Although there are worm screws with two or more teeth. This design allows you to get a relatively high gear ratio. A popular feature of the worm gear is self-locking. The worm screw can drive the worm gear. And if it is the other way around, then self-locking will prevent this. Moving large loads can also be a problem, as sudden stop of the gearbox is not recommended for such equipment. nine0007
Printing gears on a 3D printer
3D printing
and devices.
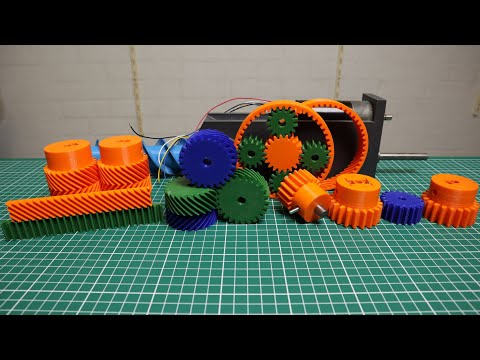
By design, the gears are divided into the following categories:
- spur gears
- helical gears
- Chevrony wheels
- gears with an internal clutch of
- Rifle gears
- sector gears
- gear with circular teeth
- conical gears
9000 Half of these gears are made from various types of plastic and are suitable for printing on a 3D printer.Printing a gear on a 3D printer is divided into 3 main steps:
1. Simulation.
2. Print.
3. Post-processing.
Gear modeling.
Not an easy stage and perhaps the most difficult one.
Don't be surprised if after redoing the model 5 times you don't get the result. There are a lot of nuances here. First you need to measure the dimensions of the gear very accurately, even a small deviation of 0.1 mm can play a role. In multi-tier gears, take into account the location of the teeth of different tiers relative to each other. If possible, simplify the design and make it stronger, namely: in industrial production, multiple recesses are often made to save money. In most cases, they are not needed and only complicate printing and post-processing. nine0007
When printing multi-tiered gears, if possible, the gear should be divided into parts and printed separately, and then docked and glued,
otherwise, the plastic may delaminate at the junctions of the tiers.
Seal
The cog's seal is a durability test.
Let's start with the choice of media. There are a lot of offers of dense plastic on the market. It is necessary to choose a plastic with a low abrasion coefficient. We use Relax and Nylon, in practice these materials have proved to be positive. They also have disadvantages, but more on that below. nine0007
Do not forget about the shrinkage of the material, as a rule, the percentage of shrinkage is indicated by plastic manufacturers. For greater accuracy, you can measure this value yourself. Print a cube with the exact dimensions of 20x20mm and after printing measure it with a caliper, just do not use cheap Chinese plastic electronic calipers, they give a large error, it is better to take a metal caliper with an error of 0.01 mm. Based on the dimensions of the printed product, you can calculate the percentage shrinkage of the material and add it to the product when printing. nine0007
The table needs to be exactly aligned, a small deviation can give an error in the dimensions of the gear print, critical for its operation.
For material adhesion, it is best to use ABS dissolved in acetone. Just make it liquid and apply a thin layer on the glass. A thick layer can warp the gear and the result will be poor. At the same time, the detachment of a part is also an unpleasant situation, especially if it was left unattended and this is the result of the work.
A slight delamination is also possible, which will also ruin the part. nine0007
No separation from the table was observed when using the ABS solution.
Also very important are the gear print settings, namely cooling and distance between supports.
This photo shows the difference between the two printed gears: on the left side the cooling is on, on the right it is off.
Each 3D printer has its own cooling settings, adjustable by experience.
The distance between supports should be made as small as possible, this is important when printing an overhanging main gear. So that it doesn't work out like this. nine0007
Here are some photos from our printers:
And even with all the preliminary calculations, before deducing the ideal G-code, you have to experiment.
Post-processing
Well, everything is clear here: we cut, we grind. For greater strength, we immerse the gear in dichloroethane for 5-10 seconds, it gives greater strength to the gear, penetrating into small cracks, gluing them, but this is not necessary, it all depends on the design of the gear.