3D printing rubber gaskets
3D Print Rubber - 3D Printing Gaskets
Rubber and rubber-like materials are everywhere in modern industry. Soft materials like latex, silicone, and thermoplastic elastomer are useful in applications that demand flexibility and durability for industrial parts and consumer goods alike.
While rubber manufacturing has historically been the domain of casting and injection molding, modern advances in 3D printers and 3D printed materials have made additive manufacturing the ideal solution for producing small to medium quantities of rubber-like parts.
Our 3D printed rubber services can manufacture high-quality rubber-like parts in as few as two days―all you need is a 3D model! Start your project by getting a quote or keep reading to learn more.
Get a quote for your project using our quoting tools. Our engineers will review your project and get back to you 24 hours or less. 3D printed rubber parts ship in as few as two days!
3D Printed Rubber Applications, From Prototyping to Production
3D printed rubber parts can be used in place of molded rubber for just about any application. Like other methods of 3D printing, rubber prints accurately produce complex internal geometries like lattices and tubes at no extra cost, easily achieving designs that would be impossible with other types of manufacturing.
And because 3D printing doesn’t require any costly molds or tooling, 3D printed rubber parts can be manufactured in just a few days compared to multiple weeks of lead time for injection molding. This combination of high agility and no start-up costs allows rubber 3D printing to excel for both prototyping and small- to medium-sized production runs.
3D printed rubber is ideal for:
Prototypes
Gaskets
Seals
Hoses
Grips
Lids
Plugs
Connectors
Footwear
Tires
Medical Devices
Sporting Goods
Advantages of 3D Printed Rubber vs.
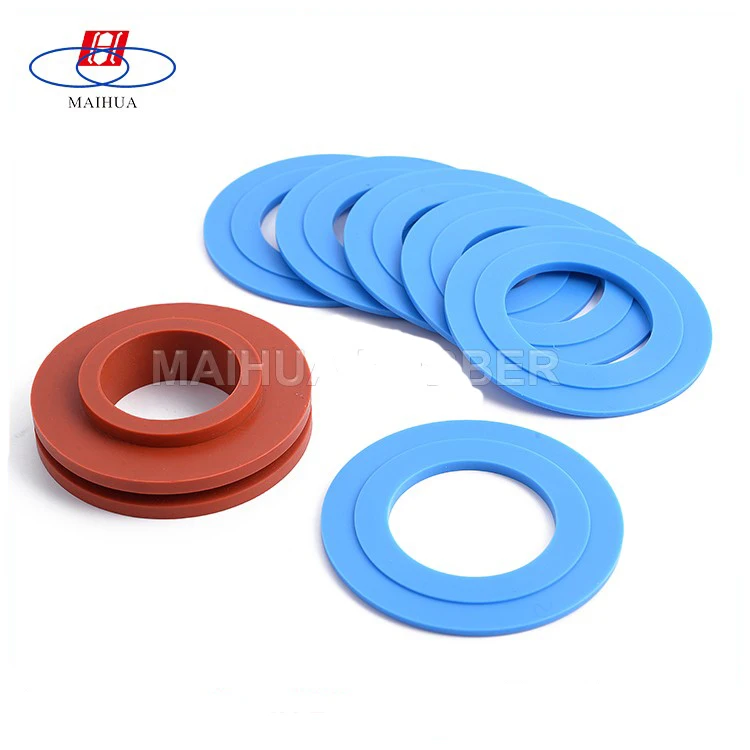
Traditionally, rubber manufacturing has required injection molding, casting, or sheet lamination. Rubber-like materials are far too soft to machine, and 3D printing was restricted to harder plastics for most of its development. Now, new developments in 3D printers and materials have opened up a wide range of new possibilities for 3D printed rubber products. So how does 3D printing compare to casting or injection molding for manufacturing rubber?
Short Lead Times and No Setup Costs
Injection molding requires machined metal molds that cost tens of thousands of dollars and take months to produce. Any design changes require new tools, making adjustments extremely expensive and time-consuming.
In contrast, 3D printing requires no tooling or other setup costs and can begin production immediately. This leads to parts that can be manufactured in as little as one day and much greater affordability at low quantities, making 3D printing Moreover, design changes are easy and can be executed at no additional cost.
The Best Choice for Rubber Prototypes
When it comes to product development, 3D printed rubber is a godsend. Even under the most ideal conditions, traditional technologies take weeks of lead time and tens of thousands of dollars for each new design.
Because 3D printing doesn’t require any tooling or setup, 3D printed parts can quickly be designed and redesigned at no additional cost. This agility has made 3D printing an indispensable part of prototyping and product development.
A Question of Quantity
As a result of these differences in lead times and setup costs, 3D printing is much more economical for small- to medium-volume production, while casting and injection molding provide greater value for productions of 1000 parts or more.
Although metal molds are expensive, molded parts become very cheap to produce once the tooling is made. When those initial costs are spread out over thousands of parts, individual part costs plummet, making injection molding the least expensive technology around for high-volume manufacturing.
3D printing, on the other hand, generally stops providing additional per part savings once part quantities exceed the capacity of a single machine. As a result, 3D printing has a much flatter cost curve that makes it a great option for small to medium quantities but significantly less economical for large production runs.
Unlimited Design Possibilities
Rubber 3D printing can easily achieve complicated designs that would simply not be possible with other manufacturing technologies. From interior cavities and lattices to variable wall thicknesses, organic shapes and built-in hoses—all of which are difficult or impossible to create with injection molding—3D printed rubber parts unlock endless new design options. You can even combine multi-part assemblies into single pieces, saving costs and improving functionality.
Plus, 3D printed parts can be highly customized, down to single parts at a time, without additional costs. This is especially useful for industries like medicine or athletics that have a high demand for products customized to each individual user. Needless to say, this would be extraordinarily expensive with casting or injection molding.
To learn more about the unique design capabilities of 3D printing, check out our Design for Additive Manufacturing (DfAM) Guide.
Is It Really Rubber?
3D Printed Rubber Materials
The answer to whether 3D printed rubber is really rubber depends who you ask. There are a lot of materials that are referred to as rubber: thermoplastic polyurethane, thermoplastic elastomer, silicone, and, of course, natural rubber!
Natural rubber, also known as latex, cannot be liquefied and re-solidified in the manner required by 3D printers. However, thermoplastic elastomers can achieve similar levels of flexibility and softness to rubber and have the thermal properties necessary for 3D printing.
The most effective rubber-like materials for 3D printing are thermoplastic polyurethane (TPU) and thermoplastic elastomer (TPE). It’s important to note, however, that both TPU and TPE refer to multiple materials. In fact, TPU is really a type of TPE―distinguished by its use of polyurethane and increased hardness.
Thermoplastic Polyurethane (TPU)
Thermoplastic polyurethane (TPU) is valued by engineers for its flexibility and strength. Not only does TPU’s hardness (Shore 85A to 95A) make it easier to print than TPE, but it also provides higher abrasion, chemical and thermal resistance. Moreover, its resistance to oil and grease makes it a great fit for hoses, gaskets and seals. While not as soft as natural rubber, printed TPU can achieve thinner walls than molded parts to create a similar level of flexibility.
TPU can be 3D printed with Multi Jet Fusion or selective laser sintering and is widely used in transportation, medicine, home goods, consumer electronics, and more.
Thermoplastic Elastomer (TPE)
Thermoplastic elastomer (TPE) is softer than TPU―Shore 40A to 70A—and offers moderate abrasion, chemical and thermal resistance. TPE parts can be trickier to print than TPU due to the material’s softness, but it offers a smoother finish.
Nylon TPE is available for selective laser sintering and is used in many of the same industries as TPU. However, because softer TPE materials are not yet available for Multi Jet Fusion, TPE parts are more expensive and slower to produce.
Rubber Printing Services
Multi Jet Fusion (MJF)
Multi Jet Fusion 3D printing is the fastest, most affordable, and most effective option for most 3D printing projects. It is also the newest printing technology to allow rubber printing, with TPU01 options available in black or gray.
MJF prints combine industrial strength, accurate fine details and a high-quality finish to create parts that are equally suited to industrial parts and commercial products. With lead times as little as one day, MJF is the premier printing option for prototypes and small- to medium-sized production runs.
Selective Laser Sintering (SLS)
Selective laser sintering prints nylon TPE parts with excellent mechanical strength but is more expensive and slower than MJF. SLS parts have a medium-quality finish and larger surfaces can warp.
This technology scales relatively well at medium volumes and is generally cheaper than FDM at those quantities. SLS can achieve slightly larger part sizes than MJF.
Start Rubber 3D Printing Today
If you need rubber manufacturing for your business, RapidMade can help you take your projects from 3D models to high-quality 3D printed rubber parts in as few as two days. When you work with RapidMade, you get a team of 3D printed experts dedicated to helping you succeed.
Learn more about our 3D Printing Services and get started today by requesting a quote. We’ll review your project and get back to you within one day!
3D Printing Gaskets; Here’s what filament to use! – 3D Solved
One of the reasons I like 3D printing so much, is because of how useful it can actually be to fix things in your own home, such as your bathroom or kitchen sink.
However, not all filament types have the same properties, which begs the question; Which filament is the best one to print gaskets that actually work and last for years?
in short; The best filament to print gaskets with is TPU, not just because of its flexible properties but also because it can withstand 110°C as well as very low temperatures without deforming or getting damaged, and it’s even resistant to abrasions, chemicals and oils, making it the ideal plastic to print objects that go through a lot of wear and tear, such as gaskets.
In this article, I will go over why TPU is the best filament for the subject at hand, the potential problems you could run into when printing with TPU, which brands to get, and even how to print with TPU successfully.
So, without any further ado, let’s get started!
Table Of Contents
- Properties of TPU that make great 3D printing gaskets
- Can TPU withstand high temperatures?
- Potential problems when printing with TPU
- Recommended Filaments for Printing gaskets
- How to print with TPU
- Conclusion
- Check out our recommended products section
Properties of TPU that make great 3D printing gaskets
Gaskets printed out of TPU.Thermoplastic Polyurethane (TPU) is a flexible type of thermoplastic that is also highly resistant to abrasion, as well as wear and tear. In the manufacturing process, it’s used for a number of different types of items for both consumer and industrial use. When the right blend is used to make TPU, it can offer a smooth and soft texture, but still maintain the durability to be used in a variety of applications.
3D printing with TPU is ideal for those looking to get soft, flexible and functional prints without sacrificing durability and resistance to abrasions, chemicals, and oils.
TPU can also work without problems at temperatures of up to 110°C, and all of these features make it the ideal type of filament to print gaskets with. Additionally, the fact that TPU is also resistant to extremely low temperatures means that parts printed with TPU will not become brittle and difficult to work with.
TPE filament is a good substitute for TPU, but it tends to deform at lower temperatures and retain less of its flexibility. TPE is also a little more difficult to print than TPU.
Gaskets, O-rings, and seals require high abrasion resistance, long-lasting durability, and resistance to oils and other chemicals. TPU’s High abrasion and chemical resistance accompanied by excellent flexibility, tear strength, and elongation ensure that your gaskets and seals are printed with the same if not higher quality than the commercial ones you buy at any hardware store.
The interlayer adhesion of TPU is excellent, which means that there’s very little curling, warping or delamination during the printing process, and the final product will generally come out great.
The flexibility of TPU depends a lot on how the 3D printing software is configured; Designs with a lower infill percentage are more flexible as opposed to those with a higher infill, and this allows you to create objects that are slightly more elastic or rigid.
All of this being said, it takes a lot of power for a 3D printer to process TPU filaments since the temperature at which it prints at is 250°C, and most affordable 3D printers aren’t capable of printing TPU straight out of the box and some modifications might be needed.
Can TPU withstand high temperatures?
Given that TPU has a glass transition temperature of up to 60°C only, it begs the question: Is it possible to 3D print gaskets using this filament that will withstand high temperatures?
I did some testing and found that gaskets printed from TPU filament are more than capable of resisting continuous high temperatures of up to 110°C without any problems whatsoever.
It might sound weird at first but the reason behind this is simple: Above the glass transition temperature, 3D printed objects become soft and lose their rigidness, and this is not a problem for parts printed with TPU since they are already soft and flexible even below the glass transition temperature of TPU. It is to be noted here that, while TPU’s glass transition temperature is only 60°C, the melting temperature is 225°C.
So, in short: TPU can withstand temperatures of up to 110°C, or even higher given the right conditions, even despite its glass transition temperature being only 60°C. The reason for this is that since it’s already a flexible material, increasing its temperature won’t make it deform, as it happens with PLA for example.
Potential problems when printing with TPU
When printing with flexible filaments, you’ll want to make sure that the ventilation in your print area is good, as these materials sometimes expel a small amount of toxic fumes during printing, and ventilation can protect users from breathing in those fumes.
All flexible filaments, including TPU, are hygroscopic and tend to absorb moisture from the air and will swell up if they’re not dried before use (of course, the best solution is to store the filaments properly).
When the material is still wet, it can be extruded, but it won’t print well at all you will probably have to clean the extruder afterward. Therefore, using a filament that is completely dry is of the utmost importance.
If you try to extrude a material before it is completely dry, it will pop and sizzle. The sizzling you hear is caused by the water that was absorbed into the filament and that instantly turns to steam as it hits the nozzle, this usually leaves voids in your print or causes excessive stringing.
When this happens, the quality of the printed part isn’t only visually worse, the molecular structure is also compromised, so it’s not nearly as strong as it would be if it was printed using a dry TPU filament. For this reason, make sure to dry your flexible filaments before printing gaskets if you want them to work properly and last a long time.
Recommended Filaments for Printing gaskets
It’s important to purchase a high-quality TPU filament, especially if you’re thinking of using the printed parts for something that needs to withstand high temperatures and loads of wear and tear, like gaskets. There are many companies that sell low-quality TPU, and this causes problems when they are 3D printed.
I’d recommend these two TPU filament brands, and make sure to check out their technical specs before buying and strictly follow their printing guidelines.
NinjaFlex (TPU)
Ninjatek is the premium brand for 3D printing filaments and their flexible filament NinjaFlex is a reliable choice for 3D printing professional-quality seals, gaskets, and plugs.
The NinjaFlex filament has a texture that is much friendlier to extruders than other materials. Their unique technology will reduce the chance of breaking, or jamming your extruder and will print strong parts from direct-drive extruders.
While it may be more expensive than some other brands, if you need to print an object that has to be reliable, I think this is your best bet.
Matterhackers Pro TPU
MatterHackers PRO Series TPU is a great choice for 3D printing gaskets as well, since the parts printed from their TPU have springiness and fatigue resistance.
PRO Series TPU is a versatile material that can be used for a variety of applications, and just like NinjaFlex, I’d recommend it over most other brands.
How to print with TPU
Phone Case made out of TPU.One of the many unique challenges of using flexible filaments like TPU is that they can be tricky to use under certain conditions, and there are several problems that you’ll want to avoid while 3D printing TPU, such as filament clogging, kinking, and stringing. To avoid them, make sure you follow these instructions!
Note: Although not needed, you should print using a heated bed at roughly 65°C for best results and set the printing temperature between 225°C and 250°C.
Use Direct Drive Extruders
Fully flexible filaments are normally used with direct drive extruders because the filament is too flexible for a Bowden extruder. The closer the drive gear to the melting zone, the faster and more efficiently the filament will melt and feed into the nozzle.
The filament also needs to travel through a channel with tight tolerances that prevent it from kinking or coiling. Because of these reasons, a Bowden extruder is typically less practical than a Direct Drive extruder. If you aren’t sure if your printer is ready for flexible filament, make sure to check with the manufacturer.
Note: As I mentioned earlier, most low-end printers can’t print flexible filament.
Use Slow and Consistent Feed Rates
For best results when printing flexible filament, a slow and consistent feed rate is recommended since it’s hard to control a sudden change in the extrusion speed when using an elastic filament.
The faster you try to print an object, the more likely it is that the filament will compress against the extruder and cause a jam. The best approach is to print at slow and constant speeds. You can save yourself time and money by testing various printing speeds and choosing an optimal one based on your findings.
More likely than not, speeds of 20 mm/s can be a good starting point for most materials.
Reduce Resistance from the Filament Spool
If you’re printing with flexible materials, you’ll need to change the way you load your spool: When your extruder pulls filament into the nozzle, the filament spool will unwind a bit of plastic. However, flexible filaments, like TPU, and materials that are high in elasticity will get stretched due to this pulling force and this will result in under-extrusion.
To solve this, mount your filament directly over the top of your printer, it will allow the filament to unwind in a more natural motion in a downward direction and eliminate friction. If the spool hub is mounted on a bearing, it allows the spool to turn far more freely, which can also help the filament unwind easily.
Tune Your Retraction Settings
Flexible filaments are sensitive to quick movements such as retractions. You need to reduce the retraction movements for successful printing by optimizing your retraction settings.
For those who are just getting started with TPU, I recommend that you disable retraction completely so you can focus on optimizing the speed and extrusion rates to print your models reliably.
After you have had more practice with these settings, if you add only a little retraction, you’ll reduce oozing.
Optimize Your Travel Movements
If you’re using flexible materials, you should use as few retractions as possible, because they can cause significant problems for your prints. Check the settings of your slicer to adjust this.
Conclusion
Most flexible filaments should work for printing gaskets, but TPU, especially the ones made by the brands I mentioned earlier, will do better overall.
Printing with it might be a bit tougher than printing will good old PLA, but it’s not as hard to print as some other materials, so give it a try!
I hope this information was useful!
Have a great day!
We created a recommended products section that will allow you to remove the guesswork and reduce the time spent researching what printer, filament, or upgrades to get, since we know that this can be a very daunting task and which generally leads to a lot of confusion.
We have selected just a handful of 3D printers that we consider to be good for beginners as well as intermediates, and even experts, making the decision easier, and the filaments, as well as the upgrades listed, were all tested by us and carefully selected, so you know that whichever one you choose will work as intended.
Free STL file T7 Rubber Gasket・3D Printing Template to Download・Cults
Anticluster Shake Tenere 700 A simple model.
3 €
Anti-cluster cocktail Tenere 700
3 €
Tenere 700 Hinged cap Mod
Free
Best 3D Printer Files in the Miscellaneous Category nine0017
Minimalist Wallet
Free
Astro Jetson
Free
M1911 em Impressão 3D dispara elasticos Rubber Band Gun 3D
3,53 €
IKEA Fan
Free
Duff Beer Carrier
Free
Pikachu Key Chain
Free
Misc - Spagetti Scale
Free
Vanzzla Jump Pads for Electric Unicycles (EUC)
18. 40 €
Bestsellers in Miscellaneous category
hinged shenron
3 €
PINOCCHIO MOBILE GUILLERMO DEL TORO PINOCCHIO
2,93 €
Chop Fernet World Cup
9.98 €
Addams Thing
1.99 €
Haslab Ghostbusters Proton Pack Ion Arm Box
5.69 €
nine0003 Grabis - caricature of the Czech prime minister €5.41 -50% 2.71 €
Item
8 €
Gengar - pokemon with flexible articulation (seal in place, without supports)
2,50 €
Key holder for middle finger
1 €
Articulated Gyarados
1. 99 €
5 gnomes (without support)
2.49 €
Elongated four-barrel laser cannon armored sponson
7,86 €
Brackets for shock absorbers and trx4m escalators
1.84 €
nine0003 Chainsaw man - Denji €17.48 -50% 8.74 €
Starbucks Studded Tumbler Inspired Keychain with Removable Screw Top Pill Box Square STL File for 3D Printing
2,53 €
4th planet Fighting pre-Olympic god
12 €
Do you want to support Cults?
Do you like Cults and want to help us continue our journey on our own ? Please note that we are a small team of 3 people, so supporting us in maintaining activities and creating future developments is very easy. Here are 4 solutions available to everyone:
-
AD: Disable your AdBlock banner blocker and click on our banner ads. nine0006
-
AFFILIATION: Shop online with our affiliate links here Amazon.
-
DONATIONS: If you want, you can donate via PayPal here.
-
* INVITE FRIENDS: * Invite your friends, discover the platform and great 3D files shared by the community!
Best flexible 3D printing materials: FLEX, TPU, eLastik and more
There are many applications that require parts printed from flexible, elastic, and soft materials.
Flexible materials can have a wide variety of properties: elasticity, durability, strength, fire resistance, chemical resistance (oil, gasoline, alkali), biocompatibility, which also makes them ideal for industrial applications. Today, flexible filaments approved for long-term skin contact are becoming increasingly common, making them ideal for prosthetics and wearable electronics. There are also flexible plastics made from 100% recycled material. nine0006
There are many manufacturers of flexible filaments for 3D printing on the market today. In this article, we will look at material options for high-quality printing of flexible wide-profile parts: from auto parts to smartphone cases.
Esun eTPU-95A
Esun eTPU-95A is the most widely used flexible 3D printing filament and is highly resistant to various types of loading. The high coefficient of elasticity provides a stable shape and long-term resistance of products to physical deformations. The material is resistant to industrial oils and chemicals, and also has moisture resistance, so that the resulting products can constantly come into contact with water. Esun eTPU-95A is perfect for printing sanitary napkins and seals, industrial dampers, and orthopedic insoles. Shore hardness is 95A, so thick-walled parts resemble hard rubber.
Esun eLastic
Esun eLastic is another common flexible material from Esun that is much softer than Esun eTPU-95A. Esun eLastic belongs to the category of TPE filaments, and its hardness is only 85A Shore. Given its high wear resistance, resistance to mechanical damage and low temperatures, this material is also suitable for use in industry, printing dampers and gaskets, especially in cases where the softness of thick-walled parts is important. Products made from Esun eLastic have a pleasant tactile properties, which is great for printing covers for portable electronics, shoes, medical devices, vehicle steering pads. Esun eLastic is considered a difficult material to print due to the high elongation of the rod, so a direct feed extruder must be used for printing. nine0006
Raise3D TPU-95A Premium
Raise3D TPU-95A Premium is a flexible filament from professional FDM printer manufacturer Raise3D. This material is designed specifically for industrial use and has the appropriate quality certificates. Raise3D TPU-95A Premium has a 95A Shore hardness, ideal for printing seals, bushings, gaskets, tubes, protective covers, shoes and insoles, etc.
BFlex Bestfilament
BFlex Bestfilament is an analogue of TPU-95A from a domestic manufacturer, so a printer with an extruder of the Bowden system can easily handle printing with this material. Claimed hardness is 40 Shore D, which is equivalent to 95A on the more common hardness scale for flexible materials.
BFlex Bestfilament is designed for industrial applications, as it is highly resistant to physical stress and mechanical damage, as well as to chemically aggressive media: oils, gasoline, alcohol and solvents. However, this filament is not resistant to UV rays, so it is not recommended to print parts that are intended to be exposed to sunlight for a long time. nine0006
TPU Soft Bestfilament
TPU Soft Bestfilament is much softer than BFlex Bestfilament and is closer in properties to Esun eLastic, so a direct extruder is recommended for printing with this material. Despite being noticeably soft, the material has excellent compressive strength, abrasion strength, and greater tensile strength than the harder BFlex Bestfilament.