3D print quotes
What’s the right 3D printer for prototyping? Comparing 3D printing processes
What 3D printing process is optimal for prototyping? This article explores the best 3D printers for the prototyping phase of product development, including design advice to get the most out of each manufacturing technology.
Since the invention of 3D printing in the 1980s, the technology has developed into a robust manufacturing solution for simple and more demanding prototyping as well as more complex, industrial applications.
Engineers, designers, startups and established businesses can use 3D printing to work through their prototype development cycle. From basic look-and-feel models to bespoke custom parts for R&D or later-stage product testing, custom tooling and even end-use parts or large assemblies, 3D printing offers a variety of solutions.
Today, Hubs offers a wide range of 3D printing technologies for prototyping, from simpler processes like FDM (fused deposition modeling) using filament-based materials, to more complex ones like MJF (HP's Multi-Jet Fusion), which uses powder-based materials that are optimal for inserts, threads and painted surfaces.
Let’s break down the 3D printing technologies available through the Hubs' manufacturing network .
How do you select the best 3D printing process for prototyping?
Depending on your product application, there are several factors to consider when identifying the best 3D printing technology and process for your prototyping needs. These include your intent for the prototype (visual, functional, testing, high-volume or end-use) and your priorities and budget for the specific stage of development.
It’s essential to determine early in the process whether functionality or cosmetic appearance is your first priority. This will help you select the right 3D printing process. As well, when more than one process can produce prototypes in similar materials, choosing becomes a cost versus properties comparison.
Here are a few more general rules of thumb we use at Hubs.
-
For quick, inexpensive components for fit or proof of concept, we recommend FDM .
-
For functional polymer parts, we prefer thermoplastics ( SLS or MJF ) over thermosets.
-
For visual appearance and aesthetics, thermosets ( SLA ) are the best option.
-
For highly accurate, low-volume functional prototypes in metal or plastic, also consider CNC machining .
What are the key manufacturing criteria for your prototype? Dimensional accuracy, build size & support structures
It’s important to have an overview of the fundamental mechanics of each 3D printing process to fully understand the key benefits and limitations that will sway which matches your application.
Let’s break down key criteria to cover when prototyping with 3D printing.
Dimensional Accuracy is connected to the level of detail each process can achieve and the build quality of each 3D printer. Processes that offer higher accuracy can usually create parts with finer features. Industrial-grade machines have higher accuracy and repeatability than desktop printers. Layer height (mostly relevant in FDM) impacts dimensional accuracy.
If you’re designing a prototyping part that will come into contact with other components, it’s critical that you define the necessary tolerances. As selecting a process with higher dimensional accuracy may increase your costs, you can also finish features with critical dimensions or small details after 3D printing (for example, by drilling holes or tapping threads ).
Build Size determines the maximum dimensions of a part that a 3D printer can produce. For components that exceed the typical build size, consider migrating to an alternative technology or splitting the part into multiple components that can be assembled later.
Support structures determine the level of design freedom and affect how much post-processing to expect. Processes that require no support, like SLS or industrial FDM using Ultem, have fewer limitations and can produce free-form structures with greater ease.
Dimensional accuracy | Typical build size | Support | |
---|---|---|---|
FDM | Prototyping: ± 0.5% (lower limit ± 0.5 mm) Industrial: ± 0.15% (lower limit ± 0.2 mm) | 200 x 200 x 200 mm for desktop printers. Up to 900 x 600 x 900 mm for industrial printers | Not always required (dissolvable available) |
__SLA __ | Prototyping: ± 0.5% (lower limit: ± 0.10 mm) Industrial: ± 0.15% (lower limit ± 0.05 mm) | 145 x 145 x 175 mm for desktop.![]() | Always required |
SLS/MJF | ± 0.3% (lower limit: ± 0.3 mm) | 300 x 300 x 300 mm (up to 750 x 550 x 550 mm) | Not required |
Another important aspect to consider when choosing a technology is the impact of layer height .
Due to the additive nature of 3D printing, layer height determines the smoothness of the as-printed surface and the minimum feature size a printer can produce (in the z-direction). Using a smaller layer height also makes the stair stepping effect less prominent and helps produce more accurate curved surfaces.
Typical layer thickness | |
---|---|
FDM | 50 - 400 μm (most common: 200 μm) |
__ SLA/DLP__ | 25 - 100 μm (most common: 50 μm) |
__SLS __ | 80 - 120 μm (most common: 100 μm) |
3D printing for basic prototyping - manufacturing with FDM
If you’re looking to build a basic prototype on a budget - to visualize a part or design, check the look and feel, and have a rough idea of form, fit and function - FDM may be the best 3D printing option.
It’s important to remember that FDM uses filament-based thermoplastics. As such, parameters like infill and layer resolution will impact the accuracy and cost of your custom parts. The more infill you have, the more material you will need, raising the cost.
As an extrusion-based printing method, FDM comes with its own design limitations and requires support structures in many instances. FDM machines can only make one part at a time, so if you have higher volumes of parts, then SLS and MJF may be more suitable. These technologies are suitable for volume prototyping as they can print multiple parts at the same time.
An ABS part printed using FDM3D printing for complex prototyping - manufacturing with SLA, SLS & MJF
If you aim to build more complex, highly accurate prototypes to test form, fit and function (or want to test parts for durability and strength), you will get the most out of SLA, SLS and MJF. For more complex prototyping, SLA, SLS and MJF are more efficient and easier to scale, and in many cases, the most cost-effective option, especially for the part quality you get.
In terms of the materials these processes use, SLA uses liquid photopolymer resins and SLS and MJF use powder materials, so there’s nothing to remove after printing. SLA does use support structures, so if you’re printing intricate or detailed features, you’ll want to factor in removal time.
Post-processing time is important to consider, especially when prototyping at higher volumes. With SLA, time is required to cure liquid resin, and ensure parts dry properly (referring back to the extra time needed to remove supports)
In contrast, SLS and MJF powder materials require time to cool and need to be able to be cleaned easily. Intricate or detailed features could result in cracked, blocked or filled internal holes/channels that can’t be cleaned. Designs should allow for cleaning, powder removal and sufficient cooling to ensure highly accurate prototypes.
What materials do 3D printers use?
Depending on the 3D printing technology you are using, materials usually come in filament, powder or resin form. The two main 3D printing material groups are polymers (plastics) and metals, while other materials such as ceramics (one of the newest materials to be used in 3D printing) or composites (perfect for strong, lightweight parts) are also available.
Polymers can be broken down further into thermoplastics and thermosets. The main difference between these two designations is how they behave when heated. When you heat thermosets, the material gets stronger, but can’t be remolded or heated after the initial forming. In contrast, you can reheat, remold and cool thermoplastics as necessary without leading to any chemical changes.
Different technologies are built to print with certain materials more optimally than others, with the level of accuracy and material cost becoming mitigating factors.
What are thermoplastics and thermosets?
Thermoplastics are the most commonly used type of plastic. The main feature that differentiates them from thermosets is that they can go through numerous cycles of melting and solidifying. This means that you can reverse the process of heating and forming thermoplastics into the desired shape.
As no chemical bonding takes place when you heat and form thermoplastics, you can recycle or melt and reuse them. One way to think about thermoplastics is to liken them to butter. You can repeatedly melt and resolidify butter, and with each melting cycle, its properties only change slightly.
Thermoplastics have good mechanical properties and high impact, abrasion and chemical resistance. They can also be filled with carbon, glass or other additives to enhance their physical properties. Engineering thermoplastics, such as Nylon, PEI and ASA, are widely used to produce end-use parts for industrial applications.
Overall, thermoplastics are best suited for manufacturing functional prototypes and some end-use parts. It’s important to note that thermoplastic products are not suitable for load-bearing applications.
Typical 3D printing thermoplastics | |
---|---|
__ SLS__, MJF | Nylon, TPU |
FDM | PLA, ABS, PETG, Nylon, PEI (ULTEM), ASA, TPU |
Thermosets (also known as thermosetting polymers or plastics), in contrast to thermoplastics, remain in a solid state after a single round of curing. They are better suited for applications where aesthetics are important, as they can produce parts with smooth surfaces (similar to what injection molding produces) and fine details.
Generally, they have high stiffness but are more brittle than thermoplastics, so they are not suitable for functional applications. Specialty resins are available, that are designed for engineering applications (mimicking the properties of ABS and PP) or dental inserts and implants.
Common thermosets include phenolic, epoxy, silicon and polyurethane, which provide various benefits for production. Epoxies, for example, are tough, resistant to a wide range of chemicals and highly elastic.
Typical 3D printing thermosets (resins) | |
---|---|
__SLA __ | Standard resin, Tough resin (ABS-like), Durable resin (PP-like), Clear resin, Dental resin |
Ready to start prototyping with 3D printing?
Our online 3D printing services Get a free, instant quote
Ready to transform your CAD file into a custom part? Upload your designs for a free, instant quote.
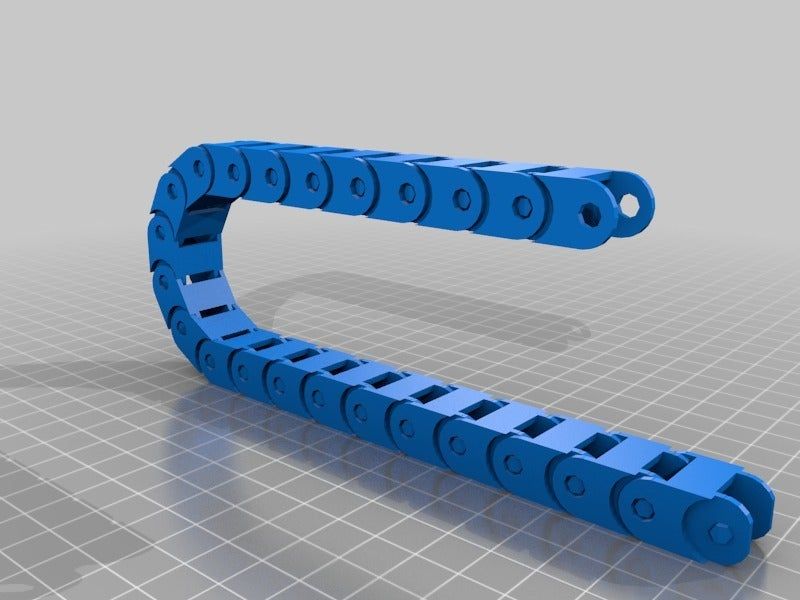
FDM 3D Printing Service | Instant Quotes, Online Ordering
Upload your CAD files, receive an instant FDM 3D printing quote and get your parts into production in less than 5 minutes.
Get instant quote See available materialsFast•Cost-effective•Lead times from 1 day
Our FDM 3D printing service
Our global network of certified FDM 3D printing manufacturing partners will allow you to rapidly verify your designs with low-cost prototypes. Simply upload your parts, get a quote, and go into production in less than 5 minutes.
FDM capabilities
Requirement | Desktop FDM | Industrial FDM |
---|---|---|
Maximum build size | 500 x 500 x 500 mm (19.68" x 19.68" x 19.68") | 406 x 355 x 406 mm* (15.![]() |
Standard lead time | 2 business days | 3 business days |
Dimensional accuracy | ± 0.5% with a lower limit on ± 0.5 mm (0.0196") | ± 0.25% with a lower limit: ± 0.25 mm (0.01") |
Layer height | 100-300 μm | 100-300 μm |
Infill | 20-100% | Ultra-light, Light, Solid |
The maximum build size for Carbon-filled Nylon (Onyx) is 320 mm x 132 mm x 154 mm
* Up to 914 x 609 x 914 mm via manual review
Our infill types are equivalent to Stratasys Infill types, as such:
Solid: This is equivalent to Stratasys' Solid build style
Light: This infill is equivalent to Stratasys Sparse Double Dense build style
Ultra-light: This infill is equivalent to Stratasys Sparse build style
FDM bracket with soluble support structures
Available materials for FDM
Below is a list of our standard materials for industrial and desktop FDM 3D printing. To instantly compare material prices, upload your parts to our online platform.
Desktop FDM materials
Group | Type |
---|---|
PLA | Prototyping PLA |
PETG | Prototyping PETG |
ASA | Prototyping ASA |
ABS | Prototyping ABS |
TPU | Prototyping TPU with shore hardness 85A - 95A |
Industrial FDM materials
Group | Type |
---|---|
Nylon | Markforged Onyx |
PEI | ULTEM 9085, ULTEM 1010 |
ASA | Stratasys ASA |
ABS | ABS M30, ABSplus |
The parts of a speaker prototype, printed with FDM.
Upload your parts to get a free, instant quote
Get instant quote
Our FDM manufacturing standards
We manufacture your parts according to strict manufacturing standards. A verification of these requirements is included in our inspection report that is shipped with every order.
- Desktop FDM: A dimensional accuracy of ± 0.5% with a lower limit of ± 0.5 mm (± 0.020").
- Industrial FDM: A dimensional accuracy of ± 0.25% with a lower limit: ± 0.25 mm (± 0.010").
- Consistent surface finish with no bumps or delamination. Marks left by retraction and layer changing are acceptable.
- All support material is removed such that the supported surface has a consistent finish.
- All parts are printed with 3 outline / perimeter shells or a wall thickness of 1.2 mm.
Selecting the optimal shell and infill parameters for FDM 3D Printing
The table below summarizes the recommended and technically feasible values for the most common features encountered in 3D printed parts.
Feature | Recommended size |
---|---|
Unsupported walls | 0.![]() |
Supported walls | 0.8 mm (0.0315'') |
Minimum feature size | 2.0 mm (0.00787'') |
Minimum hole diameter | 2.0 mm (0.00787'') |
Learn more about the process in our Knowledge Base article.
3D Printing rapid prototyping services
Get instant quote
Overview of 3D printer manufacturers
3D printing appeared in the late 1980s, but 2020 became a breakthrough year for the technology. The pandemic disrupted supply chains, and it was 3D printing that made it possible to quickly obtain the necessary items and spare parts, ranging from consumables for hospitals and clinics to parts for medical, industrial and other equipment.
The prospects and pace of development of the sector in recent years have significantly increased its investment attractiveness, however, there are certain risks that should not be discounted.
Vadim Kizimov
private investor
Author profile
Buy
Buy
Buy
Buy
Service in partnership with Investment mi. koff Quotes are updated every 15 minutes
Brief overview of technology
3D printing is the process of converting a model developed on a computer into a real three-dimensional object. Printing occurs due to the successive layering of thin layers of material. These are mainly thermoplastics of various types, but ceramic, biocompatible and other composite mixtures can also be used. That is why this technology is called additive.
3D printing technologies differ depending on the materials and equipment used, but the general scheme of the process is always the same:
- A virtual model of the object is created on the computer, and in order to make a model, you do not need to have 3D modeling skills. A special scanner photographs a real object from different angles, creating a digital copy of it.
- The program is slicing - splitting the model into many thin horizontal layers.
- The template is loaded onto the 3D printer, the device reads the diagram and prints it layer by layer in volumetric form.
Applications
Using a 3D printer, you can copy any object or create your own. The possibilities for additive printing are almost limitless. Now the technology has already found application in various industries:
- health care: the creation of orthopedic orthoses, dentistry, transplantology, the manufacture of prostheses;
- industrial production: parts of machine tools and equipment;
- space, aviation and automotive industry;
- robotics;
- construction: models of buildings or individual structural elements;
- food production: figured chocolate, jellies and other desserts;
- household items: from smartphone cases and collectible figurines to shoes and interior items;
- jewelry.
At the moment, additive technologies are most in demand in medicine — 3D printing makes it possible to create consumables, prostheses, orthoses, mouth guards, and even absolutely accurate models of human organs — and in industrial production when creating parts and equipment elements.
But the scope of 3D printing is constantly expanding, opening up new opportunities for both large companies and small start-ups.
Industry Prospects
At the moment, 3D printing does not yet allow you to get fast and large-scale results, but the technology has proven itself in areas that require precision and uniqueness.
The increased availability of equipment and the absence of the need for long training of personnel to work with 3D printers also played a role. Over the past six years, the number of global and specific industries that use 3D printing technology has increased, and this market is truly limitless:
- large companies or organizations may refuse to purchase the necessary consumables or parts, producing them on their own in the volumes they need;
- The role of additive printing in medicine has already been discussed above, and there are also broad development prospects here;
- 3D solutions lower the barrier to entry for new players.
Now, to launch your own production, there is no need to rent a room and purchase sophisticated equipment. For example, niches for creating custom car tuning parts, collectible figurines for computer game fans or unique gifts have just begun to open and have already begun to gain popularity.
At the end of 2021, the additive printing market was worth $15 billion, calculations were based on the cost of 3D printing and the production of printers and components. In the coming years, the expert agency Business Insights predicts an annual growth of the segment by more than 24%. At this pace, by the beginning of 2029, the size of the 3D printing market will grow at least five and a half times.
Technology deficiencies and risks of companies
Despite the prospects for the development of 3D technologies, 3D printing cannot yet be unequivocally called a profitable industry. There are a number of difficulties that do not allow you to fully rely on additive technologies.
Still high cost of equipment. Cheap 3D printers can print small objects. To create parts of large dimensions, it is necessary to purchase expensive equipment, which may turn out to be unprofitable.
Poor performance. This drawback should be considered in conjunction with the previous one: now the speed and cost of 3D printers do not allow them to be used in mass production, making a tangible profit.
Insufficient strength of manufactured parts. The layered structure is more brittle in the direction of the layers than the monolith and cannot withstand heavy loads.
Lack of stability. The use of additive technologies on an industrial scale requires equipment and materials that can provide higher production reliability. At the moment, 3D printing is most often used for prototyping, quality control, or for the production of single parts.
The need for post-processing , which increases the cost and time of production of each unit.
Unpredictability. Additive manufacturing is constantly evolving, new materials and printer models are emerging, and there is always a risk that equipment that has been heavily invested in will suddenly become obsolete.
3D printing companies on the St. Petersburg Stock Exchange
There are quite a few companies associated with 3D printing on the St. Petersburg Stock Exchange, and it is not their main activity. This industry is so young that at the moment it does not even have a benchmark significant index.
But the global trend of increasing demand for additive technologies in various areas of life can open up new prospects for industry pioneers.
Proto Labs (NYSE: PRLB). Capitalization - 2.56 billion Proto Labs was founded in 1999 in Minnesota, and by 2022 it already has more than ten branches in seven countries of the world. The company specializes in the creation of prototypes and finished parts for individual orders. In this niche, Proto Labs is one of the largest and fastest manufacturers: it takes only a few days to create a part of any complexity.
Since 2014, Proto Labs has been using additive technology for manufacturing parts. In total, the company operates in four areas:
- Injection molding, revenue growth +4% year-on-year.
- CNC machining, +41%.
- 3D printing, +17%.
- Sheet metal production, +24%.
While 3D printing still only accounted for 14.8% of the company's revenue as of the end of 2021, the technology's growth trends could bring more tangible profits in the future.
Source: Tinkoff Investments Source: Tinkoff Investments3D Systems Corp (NYSE: DDD). Capitalization - 1.88 billion. The company was founded in 1986, headquarters - in Rock Hill, South Carolina.
3D Systems manufactures and sells equipment, software and materials for additive manufacturing. Most often, the company's products are used in the aerospace, automotive, semiconductor and healthcare industries.
In 2021, 3D Systems announced two separate acquisitions. The company has agreed to acquire Titan Additive LLC, a developer and manufacturer of large-format industrial 3D printers, and Kumovis, a German provider of additive manufacturing solutions for personalized medical applications.
After the announcement of the results for the fourth quarter of 2021, the company's quotes increased by 15%. This positive reaction was driven by double-digit revenue growth of 13.1% yoy, excluding sales of part of the business. In addition, 3D Systems reduced its net loss by almost three times, and the revenue forecast for 2022 was increased by 10%.
Source: Tinkoff Investments Source: Tinkoff Investments Align Technology (NYSE: ALGN). Capitalization - 32.4 billion American company Align Technology is a manufacturer of medical equipment for dentistry and orthodontics. The patented Invisalign bite treatment system is based on the use of transparent removable orthodontic caps, which are printed on a 3D printer individually for each client.
The company is headquartered in Silicon Valley and has a rapidly growing branch network covering Russia, Mexico, Costa Rica, the Netherlands, Australia and Japan.
Digital orthodontics is rapidly evolving, and Align Technology is not going to give up just yet. The percentage structure of revenue for 2021 is distributed as follows: 80% - sales of Invisalign products, 20% - sales of intraoral scanners and other dental equipment.
Source: Tinkoff Investments Source: Tinkoff InvestmentsHP Inc. (NYSE: HPQ). Capitalization - 39.7 billion. The company does not specialize in the production of 3D printers, but is still one of the leaders in the additive printing market.
In 2014, HP developed Multi Jet Fusion 3D powder printing technology to lower the price and speed of industrial 3D printers, and two years later, the first HP Multi Jet Fusion models went on sale.
In 2017, Hewlett Packard introduced the world's first 3D lab for testing various types of additive printing raw materials. And in 2018, it announced Metal Jet technology for 3D printing of industrial quality metal products.
HP Metal Jet Printer delivers 50 times the performance and significantly lower cost of finished parts than other technologies.
On April 7, 2022, investors were shocked by the news that Warren Buffett had bought $4.2 billion worth of shares in the company. Immediately after the announcement of the deal, HP shares grew by 14.75%.
Compare companies by multiples, growth rates, and R&D spending.
Source: Tinkoff Investments Source: Tinkoff InvestmentsCompany multiples
Capitalization, billion dollars | P/E | Forecast P/E | P/S | Debt to equity | |
---|---|---|---|---|---|
PRLB | 2.56 | 38.00 | 28.00 | 2.81 | 0.01 |
ALGN | 32.40 | 41.00 | 32.00 | 8.18 | 0.04 |
DDD | 1.![]() | 5.30 | 5.00 | 2.88 | 0.60 |
HPQ | 39.70 | 6.80 | 8.70 | 0.69 | −3.58 |
Capitalization, billion dollars
PRLB
2.56
ALGN
32.4
DDD 9008
0002 HPQ
39,7,000
Algn
32
HPQ
8.7
PRLB
2.81
Algn
8,18
DDD
2.88
HPQ
0.69
DEBT TO equity
PRLB
0.01
Algn
0.04
DDD
0.6
HPQ
−3.58
Power growth rate, million dollars
8888 | 2019 | 2020 | 2021 |
---|---|---|---|
PRLB | 458 (+2.69%) | 434 (−5.24%) | 488 (+12.44%) |
ALGN | 2406 (+22%) | 2471 (+3%) | 3952 (+60%) |
DDD | 636 (−8%) | 557 (−12%) | 615 (+10.![]() |
HPQ | 58,760 (+1.3%) | 56,630 (−3.62%) | 63,000 (+11.25%) |
2019
458 (+2.69%)
2020
434 (−5.24%)
200003
488 (+12.44%)
2019
2406 (+2222 %)
2020
2471 (+3%)
2021
3952 (+60%)
2019
636 (−8%)
2020
557 (−12%)
2021
615 (+10.4%)
2019
58 760 (+1.3%)
2020
56 630 (−3.62%)
2021
63 000 (+11.25%)
Help growth, million dollars
2019 | 2020 | 2021 | |
---|---|---|---|
PRLB | 63 | 50 | 35 |
ALGN | 442 | 1775 | 772 |
DDD | −69 | −149 | 322 |
HPQ | 3152 | 2884 | 6503 |
2019
63
2020
50
2021
35
2019
442
2020
1775
2021
772
2019
−69
2020
−149
2021
322
2019
3152
2020
2884
2021
6503
R&D costs, as a percentage of revenue
2019 | 2020 | 2021 | |
---|---|---|---|
PRLB | 7.![]() | 8.5% | 9.0% |
ALGN | 6.5% | 7.1% | 6.3% |
DDD | 13.1% | 13.3% | 11.2% |
HPQ | 2.6% | 2.6% | 3.0% |
2019
7.2
2020
8.5
2019
6.5
20200003
7.1
2021
6.3
2019
13.1
2020
13.3
2021
11,2,2
2019
9000
2020 9,0003
2.6
Summarizing the data, several conclusions can be drawn:
- All companies are profitable, with the exception of DDD, which received a one-time profit in 2021 through the sale of non-core assets.
- ALGN and PRLB have the lowest leverage.
- All companies are growing.
- DDD has the highest R&D spending and the lowest revenue growth rate. Investors should pay attention to this.
What's the bottom line
Modern 3D printers can significantly reduce time and costs when solving geometry control and reverse engineering problems in the automotive, aviation, mechanical engineering, shipbuilding, jewelry and medicine industries.
However, in any industry, especially in a start-up one, it is necessary to carefully select companies for investment, since you can always get on a promising, at first glance, start-up, whose management, carried away by development costs, will not be able to turn a profit.
3D printing: an overview of technology, equipment manufacturers and how to invest in the industry
3D printing is one of the modern additive manufacturing technologies. Things and details are literally created layer by layer, while according to the classical scheme they need to be melted or cut using molds.
How does 3D printing work?
Additive technologies include printing and casting (burning, model melting). They use various complex plastics, ceramics, metals, gypsum and biomaterials.
Different technologies are used depending on materials, workpiece dimensions and precision. Familiar to all 3D printing is called "layer-by-layer deposition" and uses a filament - a special plastic. This is a cheap and fast technology, which is mainly used for creating models and prototypes.
More expensive and sophisticated technologies can create precise and durable parts or finished products from plastics. For this, photopolymers and other plastics are used.
To print from metals, powder alloys are used - standard and unique. With their help, you can create miniature and complex objects. And with the help of plaster, multi-colored models are printed, mainly for decorative purposes.
In general, 3D printing is very promising, it can be used to create almost any part - from auto parts to human organs. In the midst of a pandemic, for example, protective equipment for doctors and parts of ventilators for patients were often produced in this way.
The main segments of the 3D printing market are automotive, aerospace, consumer goods and electronics, and medical. According to Statista, the automotive and manufacturing sectors were the most profitable. But so far, for the most part, 3D printing companies do not work as pipelines, but provide services: the creation of parts, the implementation of technologies, maintenance and support. And the market share for the production of equipment for 3D printing is not yet highly developed, according to Acumen Research.
Benefits of 3D printing
This production reduces supply chains, reduces costs, production time and waste. Also, production becomes more flexible and can respond to surges in demand, supply disruptions and shortages of workers. The global supply chain crisis of 2020 has exposed the shortcomings of traditional manufacturing, which could accelerate the adoption of 3D printing technologies.
Businesses can also hold less inventory: if needed, they will “print” more for themselves if there is no delivery. This reduces the area of warehouses. You can even place printers closer to customers to reduce delivery times and costs. At the same time, companies are less dependent on suppliers.
Finally, you can create exactly as many parts as you need, even just one. But a classic production line often involves a minimum volume for work. Therefore, "printers" are often used for prototypes and R&D: it is easier and cheaper to experiment.
What are the prospects for the development of 3D printing technology?
ARK Invest believes that the development of additive technologies is helped by crises: 2000, 2008, 2020, because there are problems in supplies, especially international ones. Companies are thinking about dependence and want to have their own production. The issue arose especially acutely in the midst of a trade war between the United States and China, and the pandemic aggravated the situation.
ARK predicts that the 3D printing market will grow from $16 billion in 2020 to $1.1 trillion in 2030. And according to Statista, the global market will triple from 2020 to 2026.
Which stocks of 3D companies can I buy?
Several shares of companies directly involved in the 3D printing market are available to unqualified investors.
3D systems (DDD)
It is one of the largest companies with 28.4% market share according to Industry Data Analytics. 3D Systems develops software, equipment and materials, prints to order.