3D print hearing aid
3D printing technology for improved hearing
At the beginning of this millennium, Sonova was one of the first companies in the world to employ innovative 3D printing technology for production. Today, 3D printing has long been the standard at Sonova: All the shells for custom in-the-ear hearing aids as well as various custom earpieces for behind-the-ear and receiver-in-canal hearing aids are produced using 3D printers. This enables the shape of the shell to be tailored optimally to the wearer's individual ear canal and degree of hearing loss.
Mass-produced custom-made products
Sonova has been advancing the industrial use of 3D technology for many years. At the beginning of the millennium, Sonova was one of the very first companies to start digitally producing shells for custom in-the-ear hearing aids, followed by custom earpieces for behind-the-ear and receiver-in-canal hearing aids. At the time, this pioneering technology represented a breakthrough in the modernization and digitalization of hearing-aid manufacturing. Previously, production had been the sole preserve of modelers who finished each unique piece by hand in a time-consuming and costly process. Digital manufacturing of custom in-the-ear hearing aids started in 2001/2002. Engineers developed the necessary tools – scanner, software, and printer – and then these were adapted to Sonova's specific requirements. In the years following, the technology was continuously improved and refined, and increasingly also employed to model the earpieces for behind-the-ear hearing aids. Since 2001, RSM (Rapid Shell Modelling) software developed in collaboration with Sonova’s partner Materialise ensures that computer-aided modeling can be done even more easily and efficiently.
Layer by layer from nothing
First, silicone impressions of the ear canal (which are still taken by hand) are scanned into the computer using laser technology. Further processing is then carried out digitally on-screen. Once a hearing aid shell has been finished on the computer, the file with the three-dimensional structure is stored in a central database and transmitted to the 3D printers at the production site. The actual printing is a fascinating process to watch: Layer upon layer of light-curing acrylic resin appears to be built up from nothing to form the new hearing aid shell.
Harnessing this technology, Sonova is able to mass-produce hundreds of thousands of custom-made products every year. Despite the high quantities involved, each product differs in its shape and is tailored to suit the individual needs of each wearer. This is the most impressive demonstration of the huge potential of 3D printing.
Taking an ear impression at the hearing care professional’s office is the first step in manufacturing a custom-made hearing aid shell. Scanning the ear impression During the scanning process, a laser optically measures the impression. Using proprietary 3D modeling software, specialists turn the digital scan of the impression into a virtual shell, optimally fitting the ear canal of the customer and reflecting all the ordered options.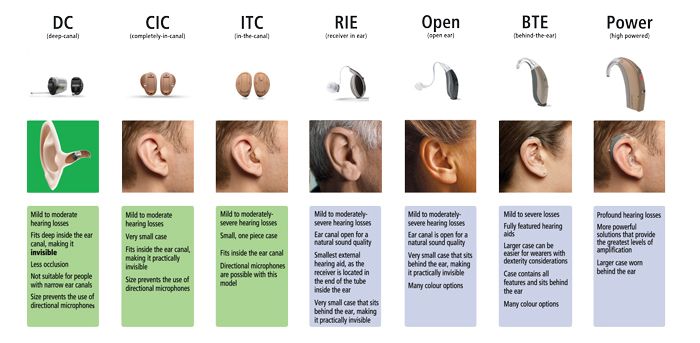
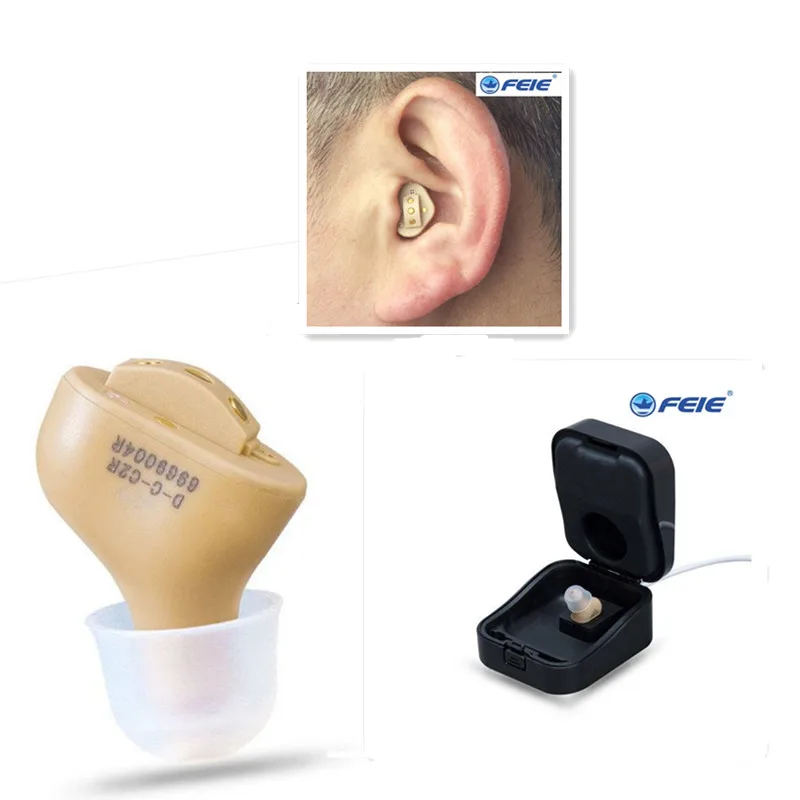
Quickly delivered to customers
The use of 3D printing technology means that the hearing aid shells produced by Sonova across the world meet the same high standards of quality. The entire digital production chain can be closely controlled, giving Sonova a competitive advantage. Once an order is placed, it takes just a few days for the finished product to be delivered, and the customer receives a hearing aid with optimal fit.
Related information
A Closer Look at Sonova's 3D Printed Titanium Hearing Aids
How Personalization Has Changed the Hearing Aid Industry
Over the counter usually sets the expectation of one size fits all. However, that is not the case when it comes to hearing aids, which today are 99% personalized to uniquely fit the wearer. This example of mass customization was made through a partnership between Phonak, now part of Sonova, and Materialise. The duo created a solution with a better fit to wearers by digitizing a labor-intensive process by using custom software and 3D printing. At the end, the comfort provided to the wearer and the seamless process has changed the hearing aid industry for the better.
Making the Shift to Digital
Perhaps you don’t need a hearing aid now but, like millions before you, some day you might. When that day comes, you will be happy that Phonak officially started their collaboration with Materialise and its team of software developers in 2000 to create a solution that would forever change how hearing aids are designed and produced.
Prior to the collaboration, producing a hearing aid was a labor-intensive process that could only be performed by a shrinking pool of highly-skilled artisans. The process was not only time-consuming, but it often required quite a lot of manual retouching of the hearing aid before a comfortable fit could be achieved for the end-user.
The shift involved going from this labor-intensive, manual process to one that is mostly digitized. The two sides brought their specialties to the table - Phonak with audiology requirements and Materialise with 3D printing and software development — and embarked on a process of co-creation. Through a series of brainstorming sessions, the companies developed an end-to-end solution that ultimately provides a better product to customers.
At the end, the new digitized and automated process was put in place, saving time, effort, and resulting in a more comfortable, acoustically optimized hearing aid that can now fit so deep in the ear that it is nearly invisible to the outside world.
How the process works:
- An audiologist takes an impression of the patient’s ear canal
- The impression is scanned and the digital file is uploaded to the hearing-aid manufacturer
- A digital model is created in as little as 6 minutes using RSM and then optimized for the patient
- Using Magics technology, the shells are prepared for building, with several shells being printed in a single build (and of course, the orientation of the shells on the platform has also been optimized for a more efficient build)
- The shells are manually finished and the electronics are easily inserted since the shell has been optimized to hold them.
- The patient receives a high-quality hearing aid that fits great and sounds fantastic.
Thanks to this process, hearing aids can be made faster and more accurately than ever before. An added bonus for any patient unfortunate enough to lose, step on, or damage their hearing aid in some way, is that their digital file can be used to create a replacement without having to start the process all over again from the beginning.
It is no wonder that around 99% of the world’s hearing aids are now made using this method.
Over 10 Million Satisfied Customers and Counting
Sonova was one of the earliest companies to show how 3D printing could be used as a means of mass production – and an effective one. It is incredible to realize that since 2000, this partnership has managed to transform an industry, has helped more than 10 million people, and has expanded the possibilities for better acoustics, increased personalization, and higher quality of life for individuals suffering from hearing loss. Furthermore, through this long-term partnership Materialise has lived up to its mission of innovative product development resulting in a better and healthier world.
Rapid production of temporary hearing aid inlays
Application
SE. Frank Talarico, an audiologist who practices at the Canadian Hearing Beyond clinic and is constantly working on new methods to help fight hearing loss more effectively and make treatment more convenient and affordable, shared his experience. nine0003
Photo: Hearing Beyond
Temporary liners
Traditionally, custom earmolds are made from impressions of the ears: an impression is taken in the clinic, then sent to the lab for the manufacture of the earmold, and the finished earmold is sent back to the clinic for fitting. The whole process takes one to two weeks. Modern hearing aids greatly simplify the process by using hand-held scanners to eliminate the need for impressions, but it still takes about a week to make an inlay. If the results of the fitting reveal the need for modifications, the whole process has to be started again. Meanwhile, patients can only wait patiently and somehow manage without vital devices. nine0003
As an audiologist, Frank believes hearing loss even for a day is unacceptable. In some cases – where the hearing loss is not severe – conventional BTEs can be used temporarily, but in severe cases they may not be powerful enough or they may be uncomfortable and then personalization is indispensable. This problem has a solution - temporary liners, produced quickly, within one business day.
In addition to the primary task, temporary earbuds can be used just to adjust the power of hearing aids. Finally, such a solution could come in handy in poorly equipped clinics in poor parts of the world, using donated BTEs without the necessary resources to produce custom molds in a traditional way. nine0003
Shining 3D EinScan-SE 3D Scanner
The problem of fast production is solved with the help of 3D printers. 3D printing is an inexpensive and flexible manufacturing solution that is available almost everywhere. Before 3D printing an inlay, you need to have an individual 3D model on hand, and 3D scanning technologies already help here.
How to do it
The first step is to take an impression. The role of the patient in our example is played by a special mannequin named Karl, more precisely CARL (Clinical Assistant for Research and Learning). After taking the impression, the excess material is cut off. nine0003
Carl in the process of making an impression (left), original impression (center) and final impression (right). Photo: Hearing Beyond
The next step is to digitize the impression using the inexpensive EinScan-SE desktop 3D scanner. As Frank confirms, this device has the necessary accuracy and resolution for working with small objects, especially when detail is important. After 3D scanning, only minor editing was required to remove minor defects and draw the internal channel. Final editing done in Blender. nine0003
3D scanning and impression editing. Photo: Hearing Beyond
The last production step is to 3D print the inlay on the FDM 3D printer. Since the part needs to be soft for comfortable wear, Frank used Recreus Filaflex elastic filament with a hardness of 70 Shore A. The material feels similar to Formaseal silicone sealant.
3D printed insert. Photo: Hearing Beyond
After 3D printing, only the assembly of the device, fitting and hearing test remain.
Finished inlay next to the impression and hearing aid fitting at Karl. Photo: Hearing Beyond
In this case, the performance test was performed with a Bernafon Leox 7 Ultra Power hearing aid, and Carl was programmed for a conditional hearing loss of 80 dB, which is a very severe case. The device was able to adjust to the required sensitivity in accordance with the DSL v5 formula for adults, that is, successfully complete the task. nine0003
It usually takes about two hours to produce two inlays using the 3D printing method described above, although in practice it all depends on the size of the parts and the material used.
Demonstration of the elasticity of a 3D printed Filaflex 70A liner. Photo: Hearing Beyond
Benefits of 3D printed inlays
The traditional technique for making liners involves the use of two-component silicone mixtures, where insertion of the tube to form a channel can be quite difficult and requires considerable skill. Exact adjustment is possible only after manufacturing and only mechanically. nine0003
When using a 3D scanner, the shape of the impression is saved as a digital model, enabling high-precision editing. Internal channels can be added directly in the software, and if the 3D printed liner doesn't fit, you can easily make changes to the 3D model and quickly print a new iteration. In addition, if the specialist has a 3D model on hand, a new inlay can be made without the need for the physical presence of the patient, making the process more convenient for everyone. nine0003
Another important advantage is open source. The software, equipment and materials used are available to anyone without the need to purchase special mixtures, which at the same time makes the process faster, more affordable and more convenient. This plays a particularly important role in low-income regions. Personally, Frank is working with an organization called Glia, which is developing low-cost homemade medical instruments and devices for countries that do not have the necessary resources to provide doctors with all the necessary equipment. nine0003
More information about EinScan-SE 3D scanner and other offers under the Shining 3D brand can be found on the official website of our company.
3D scanner EinScan-SE Hearing Beyond
Subscribe to the author
Subscribe
Don't want
2
Future technologies - today / Aurica
The introduction of new technologies into production is a prerequisite for successful business development. Otoplasty using 3D printing is used by the most advanced companies, including Aurika Group of Companies.
The topic of 3D printing at manufacturing enterprises is widely discussed in specialized publications, at conferences and forums. A significant advantage of using this technology is complete confidence in the high quality of the final product, since often otoplasty ordered from third-party laboratories does not meet the required level. nine0003
The technology has great potential and is under active development. Currently, 3D printing is becoming available not only to large industrial holdings, but also to small companies. With the help of printing, otoplasty is performed at the lowest cost, more accurately and quickly. 3D printing allows you to create your own brand, to conduct accelerated production processes.
However, 3D printing in-house does not make sense for every manufacturer. Here it is important to have trained specialists, reach a certain number of orders, evaluate and change all internal and external processes. It is optimal if the enterprise that is thinking about otoplasty using 3D printing has previously practiced modeling and had the appropriate equipment. nine0003
In order for a company to start digital manufacturing, it must be taken into account that this production requires certain investments in the purchase of a scanner, software, a 3D printer, as well as the necessary materials. The biggest cost is the acquisition of a 3D printer, while the scanner is, in fact, optional equipment, since the image can be transferred from anywhere in the world via email within a few minutes. When choosing a printer, it is important to understand that a lot depends on the material: not every printer is suitable for a certain material, and vice versa. nine0003
Aurika Group strives to be a pioneer in the industry in many ways, to become better every day than yesterday. This inspires the company to innovate. A 3D printer offers great benefits. The custom earmoulds that Aurika Group ordered from third-party companies were not suitable in terms of shape and acoustic properties. I had to finish the workpieces myself. It was this that largely contributed to the decision to start an independent printing process. The printer allows you to make several options to determine the most suitable one. The end result will always be the best. nine0003
Customized earmoulds are produced using 3D technology, an indispensable step in the process of modern hearing aids. Up to 60% of success depends on the correctly selected type and well-made individual earmold. Without an individual mold, even the most modern high-tech hearing aid, properly fitted and adjusted, cannot effectively solve the problem of a person with a hearing impairment.
Individual ear molds are made to order in the 3D laboratory of the Aurika Group of Companies based on casts of the client's ear canals. It is important that the earmold fits as closely as possible to the ear, following the contours of the ear canal. nine0003
Made by a qualified specialist on the basis of high-quality material, an individual earmould provides optimal acoustic transmission, comfortable and secure fixation in the auricle, without pressure and rubbing, no "feedback" effect (whistling) during the operation of the hearing aid, reducing the effect of occlusion (stuffing of the ear ).
The material and shape of the custom earmould must be selected in consultation with the hearing care professional. The choice depends on the degree of hearing loss, the anatomical features of the client's ear and the model of the hearing aid. nine0003
The Otoplastik laboratory uses two types of material, silicone and acrylic, to manufacture custom earmoulds, each of which has its own advantages. An additional option is the application of antibacterial varnish, which is a key point in printing. It is at this stage that biocompatibility comes to the fore, since the liner is in direct contact with human skin.
STAGES OF THE PRODUCTION OF INSERT
- The specialist examines the client in order to identify contraindications: inflammation, discharge, cerumen, consequences of operations. nine0135
- An otoblock (special tampon) is placed in the ear to protect the eardrum.
- The ear canal is filled with impression material, the impression hardens and is removed from the ear.
Learn more