3D metal printing machine price
Iro3d lowers the cost of 3D metal printing with a $ 5,000 machine
Published on November 27, 2018 by Michelle J.
The US start-up iro3d has begun shipping its first low-cost 3D metal printers, machines now available starting at $ 5000. This is a relatively low price in the metal additive manufacturing market when compared to solutions developed by 3D Systems or EOS. Even newcomers like Desktop Metal and Markforged who want to lower the cost of the technology offer machines that are closer to 100 000 €. But what can we expect from this small iro3d metal 3D printer?
Earlier this year, the manufacturer iro3d presented its first version of its eponymous metal machine. A few months later, they had it tested by a few American dealers. The iro3d has now been delivered to a few companies in the United States. They are further intending to continue their momentum in Asia and Canada. It must also be said that its selling price is very attractive and the results displayed in terms of technical specificities are interesting.
iro3d; a 3D metal printer accessible to all
Like the new Pollen AM 3D metal printer, the iro3d is inspired by an indirect metal fabrication process called MIM for metal injection molding. It uses selective powder deposition technology and sand as support material. Instead of printing a finished metal part in 3D, the machine creates a sand crucible that contains the metal powder. After a sintering step, the crucible is removed to leave room for the desired metal part. Depending on the metal used, the temperature and the duration of the sintering vary. The manufacturer explains that for copper-iron, it takes 2 hours at 1184 ° C.
For now, iro3d is compatible with high carbon steel, copper alloys and nickel. However, the printing system would not yet be optimized to produce parts with aluminum, stainless steel, or titanium. Which are still widely used metals in the industry.
On the technical specifications side, the iro3d printer offers a print volume of 300 x 300 x 100 mm and a minimum layer thickness of 0. 3 mm. For the printing time, the manufacturer has established an average of 24 hours. A duration that will obviously depend on the size of the desired part. Iro3d also specifies that the machine avoids any shrinkage compared to other solutions that rely on plastic pellets loaded with metal. Note, however, that creating in a stainless steel crucible causes a 2% distortion of the workpiece due to the horizontal thermal expansion of the crucible. On the other hand, the manufacturer explains that with a ceramic crucible, this deformation was null.
We must count to pay $ 5,000 for this 3D metal printer excluding shipping costs. Add $ 5 for 500 grams of print media. You can find more information on the manufacturer’s website HERE.
What do you think of the iro3D metal solution? Let us know what you think in a comment below or on our Facebook and Twitter pages! Don’t forget to sign up for our free weekly Newsletter, with all the latest news in 3D printing delivered straight to your inbox!
Metal 3D Printer Cost: Is it expensive? Buyer's Guide
If you are considering investing in a metal 3D printer, you are likely curious about the cost. Are the machines expensive? Do they cost a lot to operate? This guide will answer all those questions and more! Keep reading to learn about the things you need to consider before buying a metal 3D printer and some of the best options on the market today.
Metal 3D printers are used for a wide variety of manufacturing needs. They are becoming faster and easier to use. These machines are powerful too since they can now use more metals than ever.
3D printing with metal has many applications for engineers, whether you are in the automotive, health, aerospace, or other industry. You can use them to build detailed parts, prototypes, and pieces that can take your business to the next level.
So, how much does a metal 3D printer cost?
Unfortunately, there is no easy answer to this question. The manufacturers of metal 3D printers don’t broadcast their prices online, so you can’t just google what the cost is. Part of the reason they do this is that they will tailor their quotes to fit the specific needs of their clients.
That means you won’t be able to just order them online. You will likely need to reach out to the manufacturer, schedule some meetings, and sign a formal contract.
Even though the cost of this technology has decreased over time, it is still expensive compared to other 3D printing options. You can expect to spend anywhere from $80,000 to $1,000,000 on a metal 3D printer!
The cost will vary based on the type of metal printer you choose, as well as its size and expected performance. You will also need to add in the cost of the materials and additional tools required to complete the metal 3D printing process.
Similarly, 3D printing metal is not something anyone can do – you will need someone with serious skill and experience to operate them. We will get into this additional expense in the next section.
Things to Consider Before 3D Printing MetalAs we mentioned, there is a lot more to getting a metal 3D printer than the cost of the machine. That is only just a fraction of the cost, representing only about 40% of the total expenses associated with 3D printing metal.
You may be wondering, what else do you have to consider?
The total cost of ownership also includes material expenses, post-processing requirements, and operation and maintenance. Let’s get into these in a bit more detail:
Material Costs
Before you can 3D print metal, you must first buy the materials needed to make the machine work! The type of metal and materials you need will vary based on the specific machine you purchase, but this will be a recurring expense.
Most metal printers use a powder that is heated to create the metal object, and a kilogram of this can cost you anywhere from $300 to $600.
If you are working with an SLM or DMLS 3D printer though, you can expect your materials to cost $2,000 to $4,000 per build. Note that this assumes that you can fit up to 12 parts on one single build plate.
The material costs you will incur will depend on what you plan to use the 3D printer for, but make sure you incorporate this into your calculations ahead of time!
Post-Processing
Printing the metal part or prototype is only the beginning of the 3D printing process. You will need to complete post-processing steps afterward, which include cleaning the object, coating its surface, and removing support structures.
How you manage this depends on the type of machine you purchase. If you opt for a metal binder machine, you must heat the objects in an oven for sintering. Power bed fusion involves building support structures to anchor the part to the build plate, so you must remove them once it’s complete.
Here are some standard cost estimates for post-processing techniques:
- Stress Relief: $500 to $600 per build
- Heat Treatment: $500 to $2,000 per build
- Support Removal: $100 to $200 per part
- Surface Treatment: $200 to $500 per part
- CNC Machining: $500 to $2,000 per part
Like our material cost estimates, these ranges assume you can fit between six and twelve parts on your build plate.
Operation & Maintenance
Finally, you must consider the cost of operating and maintaining the metal 3D printer. Simply put, these machines are not plug-and-play. They require extensive setup and skill to operate, so you will need to hire someone to manage the machine.
That means if you plan on running the printer full-time, you’ve got to hire a full-time operator. As you can see, the expense of operating a metal 3D printer can add up quickly!
Metal 3D Printing ServicesThere are various types of metal 3D printing services, and the cost will vary considerably depending on the technology you choose. If you need to connect with reliable and competitive metal 3D printing services, you can easily do so using Jiga’s marketplace.
The most common options are metal powder bed fusion, direct energy deposition, metal filament extrusion, and binder jetting. Let’s dive into how each of these processes works and what materials they use to build 3D metal objects!
Metal Powder Bed Fusion 3D Printing
Metal powder bed fusion is the most popular choice for metal 3D printing.
SLS stands for selective laser sintering. This process relies on a high-powered laser to sinter metal powder into a solid structure.
First, the machine will dispense a thin layer of metal powder on the build platform. The machine will heat the powder to just below the melting point, so the laser can easily trace the model into a solid part.
The particles fuse layer by layer, and eventually, you are left with your completed prototype! Any leftover powder supports the structure as it is built and can be reused for future projects. Once the structure is finished, it will cool down within the machine to prevent warping and optimize its mechanical properties.
Of course, post-processing is required. You must clean the excess powder off the part and separate the part. If necessary, you can use media tumbling or blasting to process the piece even further.
Other names for this process include direct metal laser sintering (DMLS) or selective laser melting (SLM). Regardless of what you choose to call it, this powder bed fusion technique uses lasers to selectively bond the metal particles – one layer at a time.
The average cost of an SLS or SLM printer is $550,000, but the price can climb up to $2,000,000 depending on the features you choose to include!
Directed Energy Deposition (DED)
Another type of metal 3D printing process is directed energy deposition or DED.
This method can be compared to filament extrusion since the metal powders are pushed through a special nozzle. You can also use metal in wire form, as that can also be easily pushed through the nozzle.
However, unlike SLS that sinters the material on the print bed, DED uses a laser to solidify the material as it is deposited. The robotic arm that lays the material down on the print bed also holds a laser that melts it simultaneously.
Not only does this speed up the 3D printing process, but it also reduces any material waste that you might experience with SLS machines.
The entire process also occurs in a sealed chamber because it must be filled with inert gas to prevent unwanted oxidation and to maximize control of the materials.
DED machines are perfect for repairing parts or building large 3D metal objects. Similarly, the high printing speed makes it ideal for manufacturing parts at production volumes. The drawback, though, is that you sacrifice surface quality and finish.
Most DED machines cost upwards of $500,000, so it is not necessarily a cheap option!
Metal Filament Extrusion
You can also choose a metal 3D printer that uses filament extrusion. The metal material, or filament, is heated up and processed through the nozzle.
Unlike the dangerous metal powder used in the previous options, this filament is made of metal particles mixed with a binding agent. That means it can be handled easily and safely but requires additional post-processing steps.
For example, it must go through de-binding and sintering to reach the final form.
These machines usually cost about $140,000, and this estimate includes the tools needed for post-processing. Like with all options, though, the cost can creep much higher if you select a larger, more sophisticated machine.
Material Jetting and Binder Jetting
The last type of metal 3D printers we want to mention use a material or binder jetting process.
Think of these machines like an inkjet printer – they spray the metal onto the build surface, and as soon as it hardens, another layer of metal “ink” is added onto it. Binder jetting works the same way, except that a liquid binder is also applied to the metal materials. It works layer by layer, so the process is completed over time.
Similarly, the prototype you construct will be very fragile until you complete the post-processing requirements. The sintering and infiltration steps will take it from its green state and turn it into a strengthened metal part.
Due to the unique technology used in this process, you can use more materials than just metal. It’s a great option if you are interested in working with sand or ceramics!
Expect to spend about $400,000 – or more – for a metal binder jetting system.
Cost of Metal 3D PrintersNow that you understand how 3D metal printing works and the different methods you can choose from, let’s review some of the best solutions on the market. This section will cover the specs for each machine as well as their average cost.
Markforged Metal X
If you are looking for an affordable metal 3D printing machine, consider the Metal X by Markforged. This option has a build volume of 300 x 200 x 180 mm and costs just under $100,000.
The build volume is rather large considering the price, and while $100,000 is by no means cheap, it will cost you less than the other options on this list!
Note that this cost only includes the 3D printing part of the machine. You will need to purchase a de-binding fluid wash statement and sintering furnace separately. This will likely bring your total cost of ownership closer to $165,000.
It uses atomic diffusion additive manufacturing to construct metal prototypes and aims to provide a more cost-effective solution for the average consumer. The Metal X operates like an FDM printer since it uses an extruder to make metal parts from powder mixed in a plastic matrix.
When you choose this model, you can work with various steels, titanium, copper, and Inconel filaments.
3D Systems DMP FLEX 100
The 3D Systems DMP Flex 100 is a powder bed fusion machine built for industrial use. This manufacturer is very popular for metal 3D printing and is based out of the US. For users needing to build small or complex metal parts, this is the perfect solution.
The DMP Flex 100 is fast and precise, so you can quickly build the same part repeatedly. When you purchase this system, you also get access to an all-inclusive software solution that gives you everything you need to be successful with metal additive manufacturing.
It has a print bed of 100 x 100 x 90 mm and costs about $250,000.
Desktop Metal Studio
The next metal 3D printer on our list is the Desktop Metal Studio. This is an office-friendly option and an ideal prototyping solution.
The printer itself costs about $60,000. You will need to purchase the de-binder and furnace separately, and you can expect to pay $15,000 and $85,000 for these, respectively. That puts you at a total average value of $160,000.
Even though it is a smaller model, it has a sizeable build volume of 300 x 200 x 200 mm. It uses bound metal deposition technology to extrude unique metal rods. The de-binder will dissolve the object after it is printed, so you are left with a porous piece that must be put into the furnace.
Once in the furnace, the prototype is heated and sintered to meet the desired density and strength.
Arcam Spectra H
Another great option is the Arcam Spectra H. GE additive owns this Swedish manufacturer, and they develop 3D printers specifically for the aerospace industry.
Although the price is not on their website, we estimate that it retails somewhere between $100,000 and $250,000. It relies on electron beam melting technology, or EBM, to create lightweight and precise metal pieces.
It offers one of the larges build chambers on the market, with a height of 430 mm and a diameter of 250 mm. After the machine prints your prototype, you must move it into a powder recovery system.
Here, a magnetic separator and compressed air clean the part. The cost of this additional machine is unknown but will likely require a significant investment.
Trumpf TruPrint 1000
The Trumpf TruPrint 1000 LMF is a selective laser melting (SLM) metal 3D printer. It costs over $250,000, and the price will vary depending on the options you select.
This tool is an industrial machine with a large build plate of 100 x 100 x 100 mm. Since it uses metal powder as feed material, you will need to factor those costs in as well.
Even though it has a considerable build volume, the machine itself is compact. You can use it for making small prototypes and parts, and you can control it remotely through a tablet application.
EOS M 100
The EOS M 100 is an entry-level model that goes for about $350,000. This number does not include post-processing add-ons, but this machine can produce high-quality and cost-effective prints.
The EOS M 100 is powered by DMLS or direct metal laser sintering. If you need to run small batches for medical accessories or other tools, this machine will be a great fit.
It has a smaller build chamber of 95 x 100 mm, which works so well for small production runs.
Is It Worth it to Buy a 3D Metal Printer?So, is it worth it to buy a 3D metal printer?
That depends on what your goals are. The best thing to do is research your options and survey your peers to see what is working for them.
Printing metal 3D parts can help you bring complex designs to life and supports on-demand production. In other words, it improves your flexibility and control on the production line! Similarly, metal 3D printing produces less waste than CNC milling processes, which increases its cost-effectiveness over time.
The obvious drawback of 3D metal printers is the high cost of entry. It may take you a significant amount of time to get a positive return on investment, so make sure to calculate your throughput to determining that value.
The printing process is not perfect either and almost always requires post-processing steps. Whether it is sintering or de-binding, you will always have to add some finishing touches to achieve the desired product.
Only you can determine if it is worth buying a metal 3D printer. Consider the pros and cons we posed as well as the unique situation your business is in!
Types of metals are aluminum, stainless steel, brass, copper, bronze, and titanium. There are different
Read
The right manufacturing supplier needs to be reputable, stable, reliable, and genuinely capable of supplying
Read
How metal 3D printers work.
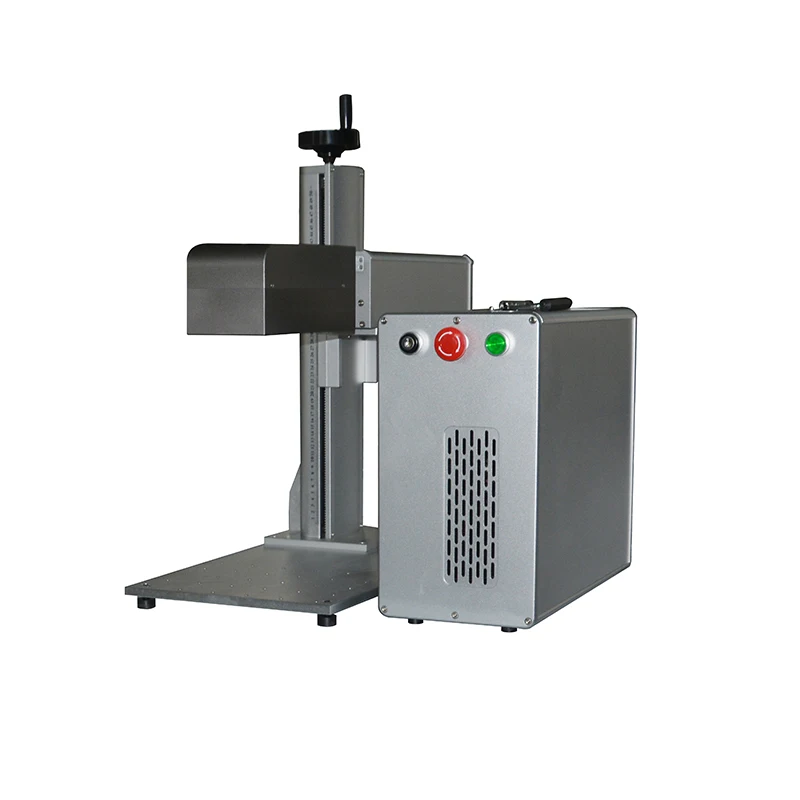
Metal 3D printing. Additive technologies.
SLM or DMLS: what's the difference?
Hello everyone, Friends! 3DTool is with you!
BLT metal 3D printer catalog
Selective laser melting ( SLM ) and direct metal laser sintering ( DMLS ) are two additive manufacturing processes that belong to the family of 3D printing using the powder layer method. The two technologies have much in common: they both use a laser to selectively melt (or melt) metal powder particles, bonding them together and creating a pattern layer by layer. In addition, the materials used in both processes are metals in granular form.
The differences between SLM and DMLS come down to the basics of the particle bonding process: SLM uses metal powders with a single melting point and completely melts the particles, while in DMLS the powder consists of materials with variable melting points.
Specifically:
SLM produces single metal parts while DMLS produces metal alloy parts.
Both SLM and DMLS technologies are used in industry to create final engineering products. In this article, we will use the term "metal 3D printing" to summarize the 2 technologies. We will also describe the main mechanisms of the manufacturing process that are necessary for engineers to understand the advantages and disadvantages of these technologies.
There are other manufacturing processes for producing dense metal parts, such as electron beam melting (EBM) and ultrasonic additive manufacturing (UAM). Their availability and distribution is rather limited, so they will not be presented in this article.
How 3D printing with SLM or DMLS metal works.
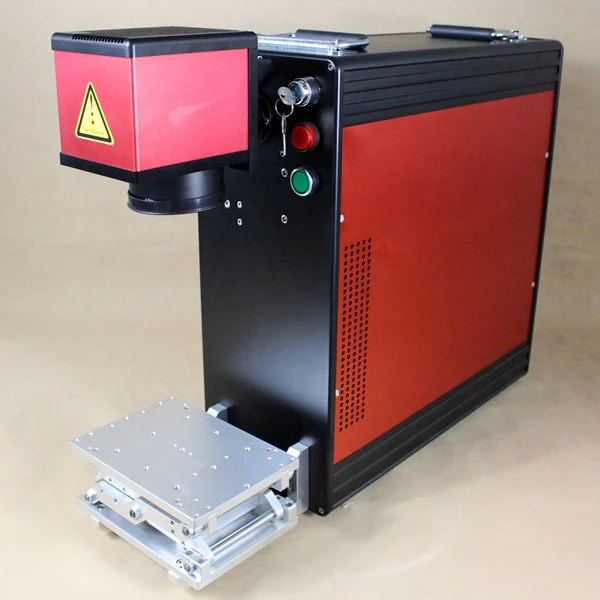
How does metal 3D printing work? The basic manufacturing process for SLM and DMLS is very similar.
1. The printing chamber is first filled with an inert gas (such as argon) to minimize the oxidation of the metal powder. It then heats up to the optimum operating temperature.
2. A layer of powder is spread over the platform, a powerful laser makes passes along a predetermined path in the program, fusing the metal particles together and creating the next layer.
3. When the sintering process is completed, the platform moves down 1 layer. Next, another thin layer of metal powder is applied. The process is repeated until the entire model is printed.
When the printing process is completed, the metal powder already has strong bonds in the structure. Unlike the SLS process, parts are attached to the platform via support structures. The support in metal 3D printing is created from the same material as the base part. This condition is necessary to reduce deformations that may occur due to high processing temperatures.
When the 3D printer's chamber cools down to room temperature, excess powder is removed manually, such as with a brush. The parts are then typically heat treated while they are still attached to the platform. This is done to relieve any residual stresses. They can then be further processed. The removal of the part from the platform occurs by means of sawing.
Scheme of operation of a 3D printer for metal.
In SLM and DMLS, almost all process parameters are set by the manufacturer. The layer height used in metal 3D printing varies from 20 to 50 microns and depends on the properties of the metal powder (fluidity, particle size distribution, shape, etc. ).
The basic size of the print area on metal 3D printers is 200 x 150 x 150 mm, but there are also larger sizes of the working area. Printing accuracy is from 50 - 100 microns. As of 2020, metal 3D printers start at $150,000. For example, our company offers 3D metal printers from BLT.
metal 3D printers can be used for small batch production, but the 3D printing capabilities of such systems are more like those of mass production on FDM or SLA machines.
The metal powder in SLM and DMLS is recyclable: typically less than 5% is consumed. After each impression, the unused powder is collected and sieved, and then topped up with fresh material to the level required for the next production.
Waste in metal printing, are supports (support structures, without which it will not be possible to achieve a successful result). With too much support on the manufactured parts, the cost of the entire production will increase accordingly.
Adhesion between coats.
3D metal printing on BLT 3D printers
SLM and DMLS metal parts have almost isotropic mechanical and thermal properties. They are hard and have very little internal porosity (less than 0.2% in 3D printed condition and virtually non-existent after processing).
Metal printed parts have higher strength and hardness and are often more flexible than traditionally made parts. However, such metal becomes “tired” faster.
3D model support structure and part orientation on the work platform.
Support structures are always required when printing with metal, due to the very high processing temperatures. They are usually built using a lattice pattern.
Supports in metal 3D printing perform 3 functions:
• They form the basis for creating the first layer of the part.
• They secure the part to the platform and prevent it from deforming.
• They act as a heat sink, removing heat from the model.
Parts are often oriented at an angle. However, this will increase the amount of support required, the printing time, and ultimately the overall cost.
Deformation can also be minimized with laser sintering templates. This strategy prevents the accumulation of residual stresses in any particular direction and adds a characteristic surface texture to the part.
Since the cost of metal printing is very high, software simulations are often used to predict how a part will behave during processing. These topology optimization algorithms are otherwise used not only to increase mechanical performance and create lightweight parts, but also to minimize the need for supports and the likelihood of part distortion.
Hollow sections and lightweight structures.
An example of printing on a BLT 3D printer
Unlike polymer powder melt processes such as SLS, large hollow sections are not typically used in metal printing as the support would be very difficult to remove, if at all possible.
For internal channels larger than Ø 8 mm, it is recommended to use diamond or teardrop cross-sections instead of round ones, as they do not require support. More detailed recommendations on the design of SLM and DMLS can be found in other articles on this topic.
As an alternative to hollow sections, parts can be made with sheath and cores, which in turn are machined using different laser power and pass speeds, resulting in different material properties. The use of sheath and cores is very useful when making parts with a large solid section, as it greatly reduces printing time and reduces the chance of warping.
The use of a lattice structure is a common strategy in metal 3D printing to reduce part weight. Topology optimization algorithms can also help design organic lightweight shapes.
Consumables for 3D metal printing.
SLM and DMLS technologies can produce parts from a wide range of metals and metal alloys, including aluminum, stainless steel, titanium, cobalt, chromium and inconel. These materials meet the needs of most industrial applications, from aerospace to medical applications. Precious metals such as gold, platinum, palladium and silver can also be processed, but their use is of a minor nature and is mainly limited to jewelry making.
The cost of metal powder is very high. For example, a kilogram of 316 stainless steel powder costs approximately $350-$450. For this reason, minimizing part volume and the need for supports is key to maintaining optimal manufacturing cost.
The main advantage of metal 3D printing is its compatibility with high-strength materials such as nickel or cobalt-chromium superalloys, which are very difficult to machine with traditional methods. Significant cost and time savings can be achieved by using metal 3D printing to create a near-clean shape part. Subsequently, such a part can be processed to a very high surface quality.
Metal post-processing.
Various post methods. treatments are used to improve the mechanical properties, accuracy and appearance of metal printed products.
Mandatory post-processing steps include the removal of loose powder and support structures, while heat treatment (heat annealing) is typically used to relieve residual stresses and improve the mechanical properties of the part.
CNC machining can be used for critical features (such as holes or threads). Sandblasting, plating, polishing, and micro-machining can improve the surface quality and fatigue strength of a metal printed part.
Advantages and disadvantages of metal 3D printing.
Pros:
1. Metal 3D printing can be used to make complex custom parts, with geometries that traditional manufacturing methods cannot provide.
2. Metal 3D printed parts can be optimized to increase their performance with minimal weight.
3. Metal 3D printed parts have excellent physical properties, metal 3D printers can print a wide range of metals and alloys. Includes difficult-to-machine materials and metal superalloys.
Cons:
1. Manufacturing costs associated with metal 3D printing are high. The cost of consumables is from $ 500 per 1 kg.
2. The size of the working area in metal 3D printers is limited.
Conclusions.
• Metal 3D printing is most suitable for complex, one-piece parts that are difficult or very expensive to manufacture using traditional methods, such as CNC.
• Reducing the need for building supports, will significantly reduce the cost of printing with metal.
• 3D printed metal parts have excellent mechanical properties and can be made from a wide range of engineering materials, including superalloys.
And that's all we have! We hope the article was useful to you.
Catalog of 3D printers for metal BLT
You can purchase metal 3d printers, as well as any other 3d printers and CNC machines, by contacting us:
• By email: Sales@3dtool. ru
• By phone: 8(800)775-86-69
• Or on our website: http://3dtool.ru
Also, don't forget to subscribe to our YouTube channel:
Subscribe to our groups in social networks:
In contact with
Steel 3D Printing - Quick Guide
Any metal 3D printing technology can print with steel. This is the most popular material. But which steel grades and which technology is best for your application? Will printed steel parts really be as strong and durable as traditionally made parts?
Let's see how a 3D printed steel part revolutionizes manufacturing and opens the door to new applications in aerospace, medical equipment, automotive, tool making, heavy industry, architecture and more. In addition, more affordable desktop printers are expanding the scope and scope of real steel 3D printed parts.
Strength of steel printed parts.
Cast steel part (left), 3D printed version (center).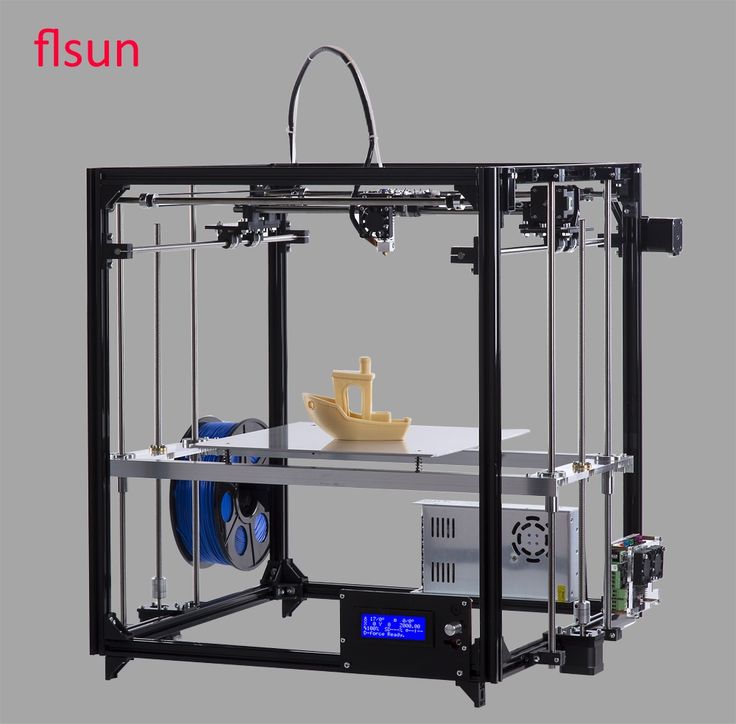
The most common question when it comes to a 3D printed metal model is "Will it be as strong as a forged or cast part?" ?". The short answer is yes... and no.
3D printed steel parts can be just as strong, and sometimes even stronger, than those made in the traditional way. It depends on many factors such as: end use, type of steel, choice of 3D printing method, post-processing and shape of the part. Also, the comparison depends on which of the strength characteristics you focus on: tensile strength, static load strength, fatigue strength, etc.
Parts printed from steel are used in the aerospace industry, for the military, as well as, for example, for the manufacture of a footbridge, shown below. Therefore, the strength of printed products is beyond doubt, but let's take a closer look.
Queen Maxima of the Netherlands officially opens a 3D printed metal bridge. Photo by Adriaande Groot (Source: MX3D) A 3D printed or laser powder sintered (LPBF) steel part has a finer grain structure than cast metal products. This provides better tensile strength characteristics, but in other respects the cast parts are currently still stronger. Most often, LPBF 3D printing is used to replace cast components, but in some cases, 3D printed components can replace forged parts.
One study showed that, under certain conditions, stainless steel parts made using LPBF 3D printers were three times stronger than parts made from the same steel using the traditional method.
In experiments comparing 3D printed steel parts to traditionally made steel parts, researchers create identical parts using two methods and compare their performance. However, head-to-head comparison of details is only part of the big picture.
The main advantage of printing with steel is not only its strength, but also the unique ability to create internal channels and lattice fillings in parts, which is impossible with traditional manufacturing methods. Metal 3D printing makes it possible to produce parts faster than traditional production, since this method does not require the use of special equipment and tools, it allows you to create assemblies as a whole, eliminating the need for subsequent assembly and welding. Designing a printed part usually means that less metal is needed to make it, and therefore less weight, for the same strength.
Steel 3D printing is also more stable and cost effective as it reduces waste. When using subtractive manufacturing methods, such as CNC machining, you make a part by cutting it out of a large one, with a lot of waste. With additive manufacturing, you only use the material you need to make the finished product.
Steel 3D printing is not intended to replace traditional methods in all areas, but it may be a better choice for a wide range of applications. Particularly when the required parts are unique and designed for specific applications, such as rocket engines, racing cars or the oil and gas industry. 3D printing is the fastest and most flexible technology for mass production and prototype production. For military and industrial applications, steel 3D printing is a faster and more efficient way to create individual parts for vehicles and machines. Stainless steel 3D printing is rapidly finding applications in medicine to create unique surgical instruments and implants.
If you know what characteristics your final product should have (tensile strength, compressive strength, hardness, density, etc.), then all these parameters can be incorporated into the product at the production stage.
Kinds of steel for 3D printing
Metal powder is the most used metal material for 3D printing (Source: GKN Additive)There are thousands of kinds of different steel grades and alloys with different mechanical properties, used in traditional manufacturing but in 3D printing there are only a few dozen of them, and some of them are unique, created specifically for this technology. Among the steel options, the following can be distinguished:
-
Stainless steel (316L, 304L , 17-4PH, 15-5PH, 420, 254, Ph2, GP1, 630, 410).
-
Tool steel (D2, M2, h23, h21, MS1, 1.2709).
-
Low alloy steel (4140).
-
Structural alloyed (20MnCr5).
Recently, unique alloys have been developed specifically for 3D printing, designed to solve the problems that occur with classical production methods.
For example, 3D printer manufacturer Desktop Metal released a patented stainless steel in 2022 that the company says combines the tensile strength, ductility, and corrosion resistance of 13-8 PH stainless steel, combined with the hardness low alloy steel like 4140. The company says customers can go to market with this material and skip the galvanizing step to protect products from corrosion.
ExOne offers two special blends of steel and bronze that the company says allows 3D printed steel parts to have enhanced corrosion resistance while being easy to machine and polish.
While most of the metal powders used in 3D printing are similar to those used for other manufacturing methods, their numbers are on the rise as more companies adopt the technology. Some metal powder manufacturers, such as GKN, also make custom powders for specific 3D printing applications.
How to print with steel
The strength, properties, and applications of 3D printed steel products largely depend on which 3D printing technology you use. Some methods produce stronger parts, other methods provide better hardness or abrasion resistance, and some technologies are simply very fast.
Below are the main metal 3D printing methods, their properties and some of the most common application examples.
Fused Deposition Printing (FDM)
BCN3D's Epsilon printer extrudes metal filament from stainless steel (Source: BCN3D) as more printer manufacturers certify metallic filaments for use on their printers, such as Ultimaker, BCN3D, Makerbot, Raise3D. Raise3D has recently released a complete metal printing suite - Metalfuse (3D printer, debinding oven and sintering oven). This method is still much more popular for printing plastics, but with new plastic filaments filled with stainless steel powder, strong metal parts can be produced.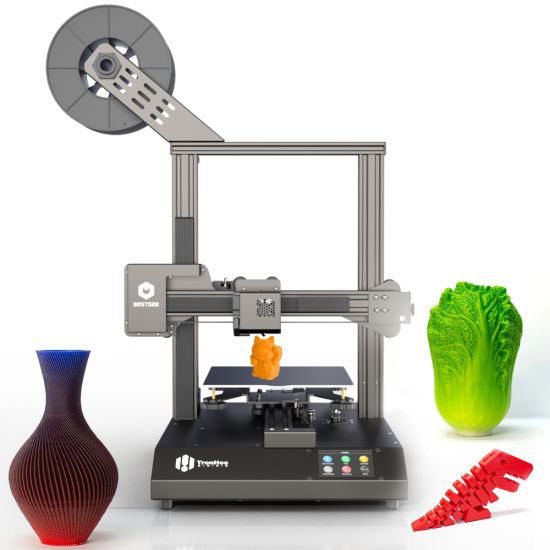
FDM media was once limited to thermoplastics. Companies like BASF Forward AM and The Virtual Foundry now offer metal filaments that can be used on almost any FDM printer as long as it has a hardened steel nozzle for abrasive media.
These materials are approximately 80% metal and 20% plastic. After printing, the post-processing process removes the plastic, resulting in 100% metal parts.
Due to the removal of the bonding plastic, FDM metal parts shrink during post-processing. The amount of shrinkage is constant and can be taken into account in CAD systems, which allows to obtain relatively accurate finished parts.
Forward AM's 316L Stainless Steel Ultrafuse filament produces finished parts with material properties that the company claims are comparable to injection molded metal parts.
(Source: BCN3D) While 3D printing with metallic materials may not be suitable for high strength applications such as aerospace, the economics of producing simple metal components without critical loads on an affordable FDM printer can outweigh the impossibility of applying them in some areas.
Metal prototype parts and finished parts that will not be subjected to extreme stress are ideal uses for this technology.
Bound Metal Deposition (BMD)
Desktop Metal's Studio System 3D printer used bonded metal bars that were extruded layer by layer to form a metal part. Metal mesh deposition method (BMD) or bonded powder extrusion (BPE) is a 3D printing process based on extrusion. This method uses bonded metal rods or bonded powdered metal filaments, which consist of a much higher percentage of metal powder than the filaments used in FDM. As with FDM, post-treatment to remove the binder and heat treatment in a final sintering oven are required. There are only a few 3D printers using this method such as Desktop Metal, Markforged and more recently 3DGence, but more companies are entering this market, so stay tuned. These printers are valued as a convenient solution for office 3D metal printing, they are more expensive than most FDM printers, but cheaper than the powder-based metal 3D printing technologies described below.
These printers use their own proprietary filament. Desktop Metal and Markforged offer four types of steel.
Ideal niches for this technology are metal prototype parts, where it is necessary to test the functionality of a part before mass production using traditional methods. Popular applications are molds, punching dies, nozzles, impellers, fasteners and heat exchangers.
For example, Shukla Medical uses Markforged's Metal X printer to print steel prototypes of its orthopedic implant removal tools.
Laser powder sintering.
Laser powder sintering technology uses one or more lasers to melt powdered metal into a desired shape layer by layer (Source: GE Additive) metal printing. This technology is used by 80% of all metal 3D printers on the market.This method uses powerful lasers to selectively sinter metal powder layer by layer.
LPBF 3D printers come in a wide range of sizes, prices and laser powers. These and other characteristics affect the properties of the finished part, print speed and other parameters of the finished products.
Steel and steel alloys are the most popular material for LPBF equipment and, unlike FDM and BMD, metal powders are commercially available as they are most commonly used in traditional production methods.
LPBF is a technology that maximizes the quality of a 3D printed part. Applications include aerospace components such as monolithic thrust chambers, rocket engine components and heat exchangers, molds, tools and other applications, as well as high wear parts and surgical instruments.
Binder Jetting
Binder 3D printing technology uses metal powder and a binder to form metal parts (Sorrce: ExOne) binder, and not with a laser. During post-processing, the binder is removed.Binder application stands out for its high printing speed compared to other 3D printing methods or traditional manufacturing, and metal parts made with this technology have material properties equivalent to those made by metal injection molding.
The number of manufacturers producing metal-bonded inkjet 3D printers is much smaller than that of LPBF machines. Leading manufacturers include ExOne, Desktop Metal, Digital Metal, GE Additive and HP.
Binder blasting is ideal for medium to high volume production of metal tools and spare parts.
In fact, HP claims that its Metal Jet 3D printer was designed specifically for mass production of 316L stainless steel products. HP has partnered with Parmatech to produce metal parts for the medical industry. Pennsylvania-based ExOne uses this technology to manufacture hard metal cutting tools and tool steels.
Electron Beam Melting (EBM)
(Source: GE Additive)Electron Beam Melting (EBM) is another powder cladding technology. It works in a similar way to selective laser melting (SLM), but instead of using a laser as the energy source, it uses a much more powerful beam of charged particles.
The recoater moves the powder onto the printing plate and an electron beam selectively melts each layer of powder. After each layer is printed, the plate is lowered and another one is applied on top of the previous layer.
EBM can be much faster than SLM, but SLM produces smoother and more accurate pieces. The electron beam is wider than the laser beam, so EBM cannot produce the same precise parts as SLM. Another difference is that the manufacturing process takes place in a vacuum chamber, which reduces the amount of impurities in the material that can lead to defects. That is why EBM is often chosen for printing components for the aerospace, automotive, defense, petrochemical and medical implant industries.
Titanium is the most popular metal for most EBM applications, however steel can be used.
Cold Spray
(Source: Impact Innovations)Cold spray 3D printing is done by injecting metal powders through a jet nozzle into a supersonic stream of pressurized gases such as air, nitrogen, or helium. The process is called "cold" because the metal particles do not melt, but hit the metal substrate and adhere to its surface during the so-called plastic deformation.
Cold spray printed products are not prone to porosity, thermal cracking and other defects associated with melt-based technologies. This method has several advantages over other production methods. The technology is used in the military and aerospace industries around the world. For example, the US Army uses cold spray to repair the mounts of a worn Bradley 25mm steel turret gun.
In the automotive industry, cold spray steel is used for crash repairs because the high strength steel substrates in cars can be susceptible to thermal repair methods such as welding.
Direct Energy Deposition (DED) and Wire Arc Additive Manufacturing (WAAM)
WAAM Steel Parts from MX3D (Source: MX3D) Direct Energy Deposition (DED) uses welding powder or wire that enters through a nozzle and is fed into the power source to melt the metal. A melt region is created and applied to the substrate. DED is a new process, reminiscent of an old building technology known as "cladding", in which a coating is applied to a substrate, often for thermal insulation or weather resistance. DED is useful for fabricating large objects as a whole, as well as complex geometries that require extensive machining. DED can get such parts much closer to finished than traditional CNC machining.
Because DED uses a coating process, it can be used to add complex geometries to existing steel parts, thus combining complexity with cost reduction. For example, the French company AddUp advertises a rocket nozzle that uses a preformed large 304 stainless steel hopper cone printed with an isogrid structure, usually made from a larger piece by traditional methods.
A technology related to DED is wire-arc additive manufacturing (WAAM). Instead of powder, WAAM uses a metal wire that is melted by an electric arc. The process is controlled by robotic arms. WAAM is also capable of producing large-sized metal parts, as demonstrated by the Dutch company MX3D and its nine thousand-pound 41-foot stainless steel bridge in Amsterdam, as well as an oil and gas equipment repair part, proving that parts can be made in the field.
Micro 3D printing
Micro parts printed from steel (Source: 3D MicroPrint) Micro scale additive manufacturing, or micro 3D printing, can produce products with a resolution of a few microns (or less).