3D laser scanner technology
What is 3D Scanning? | Laser Design
First of all, let’s be clear that 3D laser scanning is not magical. True, the technologies that make it possible are very advanced and quite amazing. But behind the mirrors—found in the laser probe (without any smoke)—there is a lot of know-how and experience that makes the laser scanning experience seem so easy to Laser Design customers.
Read on or watch our video on What is 3D Scanning?
What is 3D Scanning?
3D Laser Scanning is a non-contact, non-destructive technology that digitally captures the shape of physical objects using a line of laser light. 3D laser scanners create “point clouds” of data from the surface of an object. In other words, 3D laser scanning is a way to capture a physical object’s exact size and shape into the computer world as a digital 3-dimensional representation.
3D laser scanners measure fine details and capture free-form shapes to quickly generate highly accurate point clouds. 3D laser scanning is ideally suited to the measurement and inspection of contoured surfaces and complex geometries which require massive amounts of data for their accurate description and where doing this is impractical with the use of traditional measurement methods or a touch probe.
The 3D Scanning Process:
Data Acquisition via 3D Laser Scanning
3D Laser Scanning Process An object that is to be laser scanned is placed on the bed of the digitizer. Specialized software drives the laser probe above the surface of the object. The laser probe projects a line of laser light onto the surface while 2 sensor cameras continuously record the changing distance and shape of the laser line in three dimensions (XYZ) as it sweeps along the object.
Resulting Data
The shape of the object appears as millions of points called a “point cloud” on the computer monitor as the laser moves around capturing the entire surface shape of the object. The process is very fast, gathering up to 750,000 points per second and very precise (to ±. 0005″).
Modeling Choice Depends on Application
After the huge point cloud data files are created, they are registered and merged into one three-dimensional representation of the object and post-processed with various software packages suitable for a specific application.
Point Cloud Data for Inspection
If the data is to be used for inspection, the scanned object can be compared to the designer’s CAD nominal data. The result of this comparison process is delivered in the form of a “color map deviation report,” in PDF format, which pictorially describes the differences between the scan data and the CAD data.
CAD Model for Reverse Engineering
Laser scanning is the fastest, most accurate, and automated way to acquire 3D digital data for reverse engineering. Again, using specialized software, the point cloud data is used to create a 3D CAD model of the part’s geometry. The CAD model enables the precise reproduction of the scanned object, or the object can be modified in the CAD model to correct imperfections. Laser Design can provide a surface model or the more complex solid model, whichever results are needed for the application.
Have additional questions? Check out our Glossary, sign-up for our eNewsletter, watch the 3D Laser Scanning Video or ask a question of your own!
What Is 3D Laser Scanning Technology?
What Is 3D Laser Scanning Technology?
Duncan Parnell
For those in the industrial manufacturing sector and other relevant industries, 3D laser scanning services are quickly becoming standard in many facets of 3D laser scanning processes. From the design process to inspection and distribution of products, 3D scanning services are a must-have.
Before you learn how to use a 3D printer step by step, you should first understand how the 3D laser scanning process works, how it can benefit your company, its various applications and the trends in the industry today.
What Is 3D Laser Scanning?
3D laser scanning is a technology that employs lasers to measure an object's geometry to craft a digital 3D model. This technology is used throughout a number of industries and settings, as 3D laser scanning can capture three-dimensional data of objects, regardless of their surface features or size.
As the scanning is done with lasers, the objects do not need to be physically touched to take precise records of the existing dimensions of the object. From these scans, you'll be able to generate a model using 3D imaging software.
What Is 3D Imaging?
Essentially, 3D imaging is the ability to create an illusion of depth in a 2D image. A program manipulates the data in a 2D image to make it appear in a 3D format. Practically, 3D imaging is useful if you need to construct an object digitally, and it can also be helpful when you need to print out a 3D model.
The 3D models generated by laser scanning are constructed by capturing measurements from a variety of viewpoints with laser points or lines. The thousands of data points captured by the lasers and computer software are grouped into point clouds. These point clouds contain coordinates that all have x, y and z values, with x standing for easting, y for northing and z for elevation. The amount of detail and information contained in these point values allows users to build the most accurate models possible digitally.
Top 4 Applications of 3D Laser Scanning
There's a reason 3D laser scanning is used throughout the industrial manufacturing industry. It's useful in a variety of applications that can provide a significant amount of value to a company. Below, you'll find some of the most important ways companies use 3D laser scanning:
1. 3D Modeling, Design and Printing
Once you've made a 3D laser scan, you'll have several different ways you can use the data. For example, one of the most common applications of a 3D laser scan is to turn it into a digital model. Often, these digital models are converted into 3D CAD formats, using 3D software such as Artec Studio. In the program, you can view and interact with the model, which is perfect for companies that want to make adjustments to an existing product.
Many times, companies use 3D data gained from scanning products or facilities to help themselves design similar products or facilities. Additionally, one of the most impressive new applications of 3D laser scanning is 3D printing. With 3D printing, objects or models of buildings can be scanned and printed out in a variety of sizes.
2. Reverse Engineering
If you have an object with dimensions you don't know, you can use 3D laser scanning to get the most accurate measurements. The data from the scan can then produce a 3D model of the object or space in multiple formats. This sort of reverse engineering functionality means that companies can figure out how to reconstruct an object even without its design documents.
3. Planning
One of the most beneficial applications of 3D laser scanning across several industries is the ability to plan future actions and prototypes better. Say you have a facility and are looking to add a new machine or area to it. You can scan the current facility to find where new parts of the facility or machines can fit in with the current structure. The same principles can be applied to products that need to be compatible with other products from the company.
4. Marketing and Educational Applications
For companies that work with clients and are engaged in design work, 3D laser scans can help marketing teams bring their product to clients virtually. In the educational sphere, 3D laser models can be used as an instructional tool to show people how to construct or produce different items properly. For example, architecture students may find it valuable for an instructor to show them how a building maintains its structural integrity through the data that a scan provides.
Though 3D scanning still sometimes seems like magic, it’s made possible through highly advanced technology that has been continually improving for years. A 3D laser scanner is a non-contact, non-destructive digital technology that captures the shape of a physical object by using a line of laser light. It creates a point cloud, or a set of data points in a coordinate system, that represents the exact size and shape of a three-dimensional object.
3D scanners measure an object’s finest details, capturing free-form shapes and generating accurate point clouds for objects with complex geometries and contoured surfaces. This allows you to quickly capture precise data and deliver it quickly.
How It Works: The 3D Laser Scanning Process
3D laser scanning has gone through a revolution over the years that has provided enhanced precision, faster scanning and better results. Controlled steering of laser beams, in addition to distance measurements, makes the process possible. An internal rotary encoder in the machine controls the motion of scanning by adjusting several scanning mirrors to guide the laser beams. The process happens in several steps:
- Quality control.
When it comes to ensuring that products are being properly produced, 3D laser scanning is quickly becoming a must. It has proven its value by being able to provide users with a quick update on a product's construction. For example, a company can take the data gained from a scan to catch any errors that have been made and correct them before a product is unveiled to the public.
- Rapid prototyping. A top benefit to 3D laser scanning is the ability to reduce how many prototype cycles are needed. With 3D scan data, you'll reduce the prototypes created, as you'll have the ability to get the measurements right before going to production. Before it's produced, the object will be constructed with the correct physical measurements, giving it the right scale and proper functionality.
- Optimizes engineering and manufacturing. The data gathered by a 3D scan can be applied to the engineering portions of the project. For example, the 3D scan data will help you perform CAE, FEA and CFD engineering analysis on your created or modified products.
- Accurate documentation. In a variety of industries, 3D laser scanning provides companies with the ability to precisely document products that they offer. With a 3D laser scan, companies can quickly have precise measurements for all of the products that they offer.
- Meet deadlines. Though it might not be obvious, 3D scanning services can help companies keep tabs on the progress of their work. If you're a construction company, regular laser scanning will give you a detailed breakdown of how much has been accomplished on a worksite, which will then ensure that deadlines are met. The same principle applies to the manufacturing of objects, as laser scanning can keep tabs on the progress of whatever is being produced.
1.
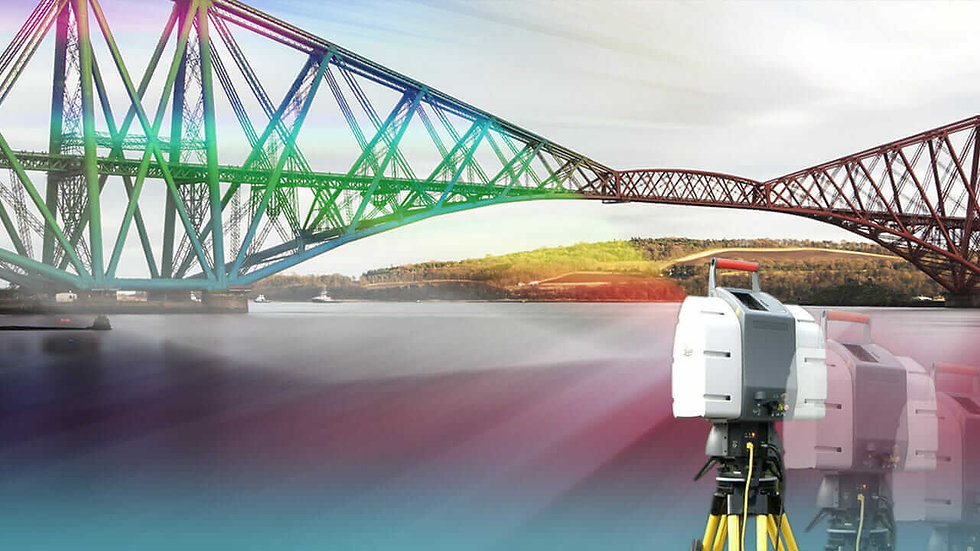
The first step to the 3D laser scanning process is to pick out an object or facility that you'd like scanned. Once you select your object, you'll need to scan it. For smaller objects, you'll place them on the bed of a digitizer to begin the scanning process. For larger objects, such as buildings, you'll need to use other types of portable 3D laser scanners that can be brought out to the site.
What Are The Different Types of 3D Scanning?
To scan an object properly, you'll need to know the two main types of 3D scanning on the market today: time-of-flight and triangulation.
- Triangulation
Triangulation uses trigonometry to get the most accurate dimensions of the object. This method involves the use of a scanner and a camera, with the camera sitting at the top vertice of a triangle and the laser scanner sitting beneath the camera at the second vertice. The object is located at the third vertice, waiting to be scanned.
Once the scanner, camera and object are in place, the scanner scans the object. As the distance and the angle between the laser and the camera are known, the scanner can calculate the distance to the object and then begin taking the measurements of the entire object.
The scanner takes its measurements by emitting a laser line. This line lets it scan and measure the object's cross-section all at once. The laser moves up the object's surface until it captures all of its dimensions. The data gained is then fed into a computer where you can then put it to use in a variety of applications. Typically, companies use this type of scanning for short-range applications, with the objects usually being smaller.
- Time-of-Flight
In contrast to triangulation, time-of-flight scanning can occur at a great distance and is often used for larger scanning jobs, such as a building or vehicle. In practice, these scanners can be considered laser range finders, as they determine the distance to the object or surface they are scanning to help them take measurements. The way they make these measurements is through a LiDAR system.
How does LiDAR work? In short, LiDAR gathers accurate data by emitting laser light and then measuring how long it takes for the light to hit the surface and bounce back to the sensors. As the speed of light is a constant that's known, the amount of time that it takes to get to the surface and bounce back tells the 3D scanner the distance between them.
Once the distance is determined, the laser will begin scanning, measuring distance one point at a time. The scanner will automatically move the laser to each point of the surface in its field of vision, with the process being extremely fast. The majority of time-of-flight scanners can measure thousands of data points per second. Due to their medium to long-range scanning capabilities, this method is often used in environmental or surveying scanning.
2. The Data
The resulting data from this process is the point cloud. Millions of points appear on a computer monitor during the laser’s movement, which captures the entire surface shape of any scanned object. The process gathers up to a million points per second with cutting-edge models like the TX8 laser scanners and others. Scanners maintain a precision within .0005 inches of the exact value.
Point cloud data files are huge. After their generation, they are registered and merged into a 3D representation of the object. Then, they’re post-processed with various software packages depending on the specific application.
3. Data Uses
Once the data has been collected and the image has been fully rendered in whatever scanning software you're using, you'll be able to select the kind of model you'd like to create through your software's 3D imaging capabilities. Sometimes you may only want a digital model, but you can also print out the model if you'd like to see a more tangible visual representation of the product.
If you're using the data you gained for inspection purposes, you can compare the designer's CAD nominal data to the object you scanned. From that comparison, you can receive a deviation report that utilizes a color map. This report will show the difference between any CAD data and scan data.
Additionally, the data can be used for reverse engineering with a CAD model. The laser scan of an object will deliver plenty of information that you can then use to reverse engineer an object. In the software, the point cloud data from an object can be plugged in to build a 3D CAD model of the object's geometry.
After the CAD model has been generated, it's easy to then to quickly reproduce an exact copy of a scanned object. Reverse engineering also allows companies to correct any imperfections in previous models. By reverse-engineering them, they can find the flaws and then keep what works while adjusting the parts that have issues in the CAD model.
Benefits of Using 3D Laser Scanning
3D laser mapping and scanning carry with them several benefits that industrial manufacturers and other businesses would be wise to utilize. To give you an idea of how 3D laser scanning can assist your company, consider the following benefits:
Technology Trends Influencing 3D Laser Scanning Capabilities
Currently, there's a debate going on in the 3D laser scanning industry about the merits of using photogrammetry or 3D laser scanning to craft 3D interactive models. Generally, it's better to use photogrammetry if you need to cover a large amount of space quickly, but for those who want a higher level of accuracy, laser scanners should be your top choice.
One main technological trend that has made 3D laser scanning faster has been the advent of drones that can quickly gather data in hard-to-reach areas. This new piece of technology closes some of the gap between photogrammetry and 3D laser scanning in terms of speed. Companies are also starting to use UAVs to eliminate LiDAR collection processes, which can cut some costs associated with LiDAR.
As reverse engineering and part inspection continue to become a major fixture of industrial manufacturing, the accuracy that 3D laser scanning provides makes it the clear choice over previous photogrammetry methods. Other new trends include more mobile LiDAR scanners, greater automation and faster processes, the growth of multimodal scans and greater AR/VR integration.
Contact Duncan-Parnell With Any Questions About 3D Scanning or Imaging
3D scanning services are vital to modern industrial manufacturing processes. 3D laser scanning technology has many applications and benefits that can affect virtually every stage of the design and manufacturing processes of products. For those interested in adding 3D scanners, 3D software or 3D scanning services, consider browsing our vast selection of 3D scanning products.
If you're just looking for more information, we have you covered as well. For those who want to know more about the 3D printing process, consider reading our blog about how to use 3D printer software and the various printing methods. Additionally, if you have other questions, feel free to contact us today!
About author
Back to Blog
90,000 technologies, methods and principles of 3D scanners04/16/2021
Content
-
- What is 3D scan and why it is used by
- How 3D scanner
- 3D scan technologies
- Methods 3D
- Contact 3D scanners
- Non-contact 3D scanners
- Types of 3D scanners according to the principle of use
- Advantages and disadvantages of 3D scanners
- Things to consider when choosing a 3D scanner
- Applications
Currently, few people are not familiar with such a concept as 3D printing. Many companies are using modern 3D printers with might and main, recreating layouts of various shapes and sizes with their help. There are also those that recreate whole objects - not only small ones (for example, phone cases, souvenirs, sneakers), but also large ones (houses, engine parts, etc.). But all this would not be possible without 3D scanners. It is they who allow you to accurately copy almost anything - from huge buildings and structures to humans, animals, small objects and much more. nine0003
What is 3D scanning and what is it used for
Three-dimensional scanning is a technology that appeared in the 60s of the 20th century. It was created in order to transfer the physical parameters of the object into a digital format in the form of a three-dimensional model. The need for this naturally arose when people around the world increasingly began to use computers both in everyday life and in production.
The first samples of 3D scanners were quite simple and did not have wide functionality. Gradually, they became more complex and improved, making it possible to achieve an ever clearer image of the object. This has become especially relevant with the advent of lasers. nine0003
3D scanners allow you to transfer object data into digital format
3D scanning has opened up new opportunities in various areas of human activity - from the automotive industry and the military industry to design, medicine and cinema.
How a 3D scanner works
A 3D scanner is a device that examines an object by digitizing it using sensors and using the information received to create a three-dimensional model. In fact, a 3D scanner creates a digital copy of a physical object of any configuration and complexity. In this, it fundamentally differs from its predecessors - conventional scanners that can only read information from documents and photos. nine0003
The scanning process itself can take place in different ways - depending on the type of 3D device and the technology used, as well as on what object you want to process with it - moving or static.
3D Scanning Technologies
There are 2 main types of 3D scanners - laser and optical. Their fundamental difference lies in how and with the help of what the “removal” of data takes place. Let's take a closer look at both.
Laser 3D scanning, as the name implies, uses a laser and can be carried out both at short and long distances from the object. nine0003
Laser Scanner
For the most part, 3D laser scanners work on the principle of triangulation, when the camera finds a beam on the surface of an object and measures the distance to it, after which a cloud of points is created, each of which has its own coordinates in space, and a 3D model is built. Their "advantages" are affordable price and ease of use combined with high scanning accuracy. Of the "minuses" - there are restrictions on the remoteness and size of the object. nine0003
Another type of laser scanner works by measuring the response time of a beam from the surface of an object - the so-called laser range finder. They are widely used where it is necessary to create 3D models of various buildings and structures. It is not advisable to use them at short distances, since in such cases the response time is very short and the accuracy of the data is reduced. Otherwise, this type of scanner is characterized by high scanning speed and the ability to read all the details. nine0003
The disadvantage of laser scanners is the impossibility of their use on moving objects. Then optical 3D scanners come to the rescue, which shoot with one or more cameras from different angles an object illuminated by a special projector. Based on the received image, a three-dimensional image is built.
Optical scanner
A "contraindication" for the use of this technology are reflective and translucent surfaces - shiny, mirror or transparent. But when scanning a person, they are simply irreplaceable. nine0003
3D scanning methods
Any object can be digitized both by contact and non-contact methods. In the first case, active interaction with the subject is necessary, in the second, accordingly, no. Both of these methods have their advantages and disadvantages.
Contact 3D scanners
They have a mechanical probe with a special sensor that measures parameters and transmits the collected information to the device. To do this, the object under study is placed on a special surface and fixed (if necessary). Such tight physical contact makes it possible to determine and then build a 3D image as accurately as possible, however, there is a small risk of damage to the prototype. nine0003
Non-contact 3D scanners
This category includes all devices capable of scanning at a distance. This is especially true for objects located in hard-to-reach places.
Non-contact 3D scanner
A stream of radiation (it can be ultrasound, light, X-rays or a laser) is directed to the object and reflected from it, it is recognized by the 3D scanner. They are similar in principle to a video camera and may require the use of additional devices for better lighting. nine0003
Non-contact 3D scanners come in 2 types:
-
Active - work with the help of a laser beam or structured light directed at an object, which, when reflected, give information about the location of the object in the form of coordinates.
-
Passive - use time-of-flight rangefinders that read the time and distance that the laser beam travels to the object, and so - for each point in space, which ultimately allows you to accurately recreate its three-dimensional image. nine0003
Desktop 3D scanners are very popular and widespread, since they are mostly simple and safe to use, do not require any special technical skills and are quite cheap. The EinScan-SE 3D scanner is one such example. It can be used both at home and in the office. It has access to the API of many popular 3D printers, which makes it possible to immediately print the created three-dimensional model.
Add to compare
Product added to compare Go
Manufacturer | Thor3D |
Add to compare
Product added to compare Go
Manufacturer | Shining 3D |
Add to compare
Product added to compare Go nine0003
Manufacturer | Shining 3D |
Add to compare
Product added to compare Go
Manufacturer | Range Vision |
Types of 3D scanners according to the principle of use
There is also a variety of species here. Let's highlight the main ones:
- nine0002 Manual: The are handy and simple models that are easy to use as they are quite compact and do not require special skills. True, their technical capabilities may be somewhat limited.
-
Portable: are mainly used for field work, they are convenient to take with you.
-
Desktop: have extended functionality and are used to create high-quality 3D models. Most often used in offices. nine0003
-
Stationary: are used, as a rule, in production, various enterprises, as they can scan a large number of objects of the same type at once. Mounted on special turntables.
Handheld 3D Scanner Calibry
Such a choice of products allows you to select the right model for a specific task. In some cases, scanners independently measure objects, in others - with the help of a person who sequentially moves the device until all the necessary information is collected. nine0003
Such options for hand-held 3D scanners as Calibry are in high demand among buyers. Despite the apparent simplicity of execution, it has a high resolution and scanning accuracy, due to which it is able to digitize objects with a length of 0.2 to 10 meters. Objects that have a non-standard surface - dark or shiny, with a large number of corners and small details will not become a problem either. Among other things, its undoubted advantage is its low weight, only 900 grams. nine0003
Advantages and disadvantages of 3D scanners
Surely, many of the potential buyers are wondering: do you really need a 3D scanner to invest a lot of money in it? What can this acquisition give and will such an investment be justified?
3D scanning has become an integral part of any modern manufacturing process
In order to understand how much you need this equipment, we will list its advantages and disadvantages. nine0003
Benefits:
-
They make it possible to scan objects located at a remote distance and in places inaccessible to the presence.
-
They have the ability to "read" not only colors and images, but also to convey the texture of the surface.
-
Significantly speed up the process of "taking" data from any object, even a very complex one with a large number of planes. nine0003
-
A variety of models allows you to choose the most convenient version of the scanner, including manual or portable, which can be easily taken with you.
Weaknesses:
-
Some scanners are unable to recognize transparent or black and white objects. In this case, their preliminary preparation (treatment with a special composition) is required. nine0003
-
I do not always display complex objects correctly, with a large number of inserts and partitions.
-
To obtain a high-quality result, they require skills and abilities to work with certain computer programs for creating 3D models.
-
If the rules of operation are constantly violated, it may become necessary for expensive repairs to the equipment.
nine0003
If you need high-precision and high-quality three-dimensional copies of objects, then you cannot do without a 3D scanner. It makes it possible to work in almost any conditions - indoors and outdoors, and with any objects by type and size. It is not surprising that now these devices are in great demand, which gives rise to the annual release of a large number of models, from which you can always choose the one that suits you in terms of quality and price.
What to consider when choosing a 3D scanner
The computer equipment market offers a huge amount of all kinds of equipment, including devices for three-dimensional scanning. Navigating that variety is sometimes not at all easy: some buyers are only concerned about the cost, others are interested in the number of options (sometimes completely useless), but the most far-sighted look at the ratio of the first and second.
Choosing the right 3D scanner is a big deal
It is not always easy to take into account all the technical points that can significantly affect what result will be ultimately achieved. We will tell you what you should pay attention to if you are thinking about buying a 3D scanner.
Focus on the following parameters:
-
How high is the accuracy of the 3D scanner. This is one of the most important features. It needs to be targeted first. nine0003
-
Resolution also plays an important role. It follows from the first, since the accuracy of measurements and the quality of copying depend on the resolution.
-
In what range the device operates, how close / far it can be from the scanned object.
-
The scanning field is the parameters of that object, thing that it is able to process in 1 session. nine0003
-
Does the scanner capture various atypical types of surfaces with complex terrain - channels, partitions, holes, etc.).
-
Portability, mobility of the device - how easy it can be moved if desired, taken with you, its size.
-
The time it takes to prepare for work, as well as the duration of the digitization process itself. nine0003
-
The range of possibilities in terms of copying: are there any restrictions on shapes, textures, material, as well as operating conditions - temperature, light, etc.
Of course, the better the quality of the 3D scanner, the more expensive it is. However, you should focus primarily on the tasks that you face, and only then take into account everything else.
Applications
Three-dimensional scanners are in demand in many areas of human life. They are irreplaceable both in the industry, and for household needs. The range of their application is so wide that it is possible to list for a very long time. It's easier to say where they are not needed.
The most common areas of use are, of course, medicine, industry, architecture, construction, film industry and design.
For example, in dentistry, these devices allow you to create ultra-precise three-dimensional models of dentures. One type of such a scanner is Shining 3D's AutoScan DS-EX PRO, which does a great job with a variety of tasks while being quite affordable and reliable. nine0003
Medical 3D Scanner
In engineering, such technologies are also indispensable. Digital building prototypes are now much easier and faster to obtain than in the past, when it required multiple manual measurements and then entered into a database. Any physical object can now be recreated in three-dimensional form, moreover, in the shortest possible time and with a minimum error.
In cinemas, we can see with our own eyes "revived" fantastic characters, which were created using motion capture technology, which made them as realistic and impressive as possible. This would not have been possible without 3D scanners.
A few decades ago, it was even difficult to imagine all the things that we use all the time today. And in many ways this has become achievable thanks to three-dimensional digitization. This approach provides huge advantages in work (especially for technical specialists - engineers, designers, designers), however, in order to use them to the maximum, it is also necessary to understand computer programs for 3D scanning. nine0003
We will talk more about this topic in one of our next articles. And if you want to know more about it, stay tuned.
#Useful
Expert in the field of additive and subtractive technologies, 3D equipment and CNC machines with over 10 years of experience.
Share
all materials
How does a 3d scanner work? Device, principle and technologies of 3D scanning
3D Scanner is a stationary or small handheld device for scanning objects with complex spatial geometry. Simple scanners process images in a plane, while 3d scans physical volumetric objects, displaying information as a polygonal model or a cloud of points. Three-dimensional scanning devices are used in medicine (dentistry, plastic surgery, making prostheses, organ models, etc. ), for creating computer games, in the film industry, design, architecture, engineering, for designing industrial parts, cars, for reconstructing objects in archeology. Scanners analyze and digitally recreate a three-dimensional model of an object, its shape and color with a high degree of detail, working in different conditions (with insufficient visibility, in the dark, with vibration), with any materials, provide the desired format of output information for software for work with her on the computer. nine0003
How does a 3D scanner work?
The principle of operation of the 3d scanner is the ability of the device to determine the distance to an object, convert the received data into a digital image (three-dimensional model), transfer it to a computer. The scanner determines the coordinates of points in space on the surface of the processed object, analyzes them, and forms a detailed digital model. Cameras, lasers, rangefinders, devices for illumination are involved in its work.
3D scanning technologies
- Contact (contacts with the object).
- Non-contact (without object contact). These are the most promising and new technologies that allow you to create models of objects simply by directing a laser beam, light, waves at them. The scanner is applied at a distance and is able to create a copy of a hard-to-reach object without physical contact with it.
Non-contact 3d scanners
The two most common scanning technologies are optical (passive and radiation) and active laser. nine0003
Active emission principle
Scanner emits structured, intermittent light, laser triangulation. A laser beam, a beam of light generated in a special way (diodes, lamp flashes), and waves are directed to the object under study. Based on the analysis of their reflection and position, a three-dimensional copy of the object is formed.
Passive radiation principle
Do not emit anything, analyze the light or infrared (thermal) radiation of an object. Work like a human eye; nine0003
Photometric non-contact passive 3d scanning technology
Scanners from this group are represented on the market by the XYZprinting model. These are quite compact simple models that have only basic 3D scanning functions.
Pluses: reasonable price and compactness.
Device
Passive 3d scanner device (on the example of the specified model): housing, one compact camera, USB cable for connecting to a computer and transferring the image of the scanned object to it. Scanner without stand, manual, made in the form of a stapler. nine0003
How it works
A light-sensitive camera captures light from an object, processes it, and forms a three-dimensional model, exporting it to a computer. The user can have two modes of operation: scanning a person or objects. To get started, you need to install the software on your computer, connect the device to it via a USB cable, select the operating mode, press the button on the scanner and, slowly swiping it in front of the object, scan. nine0003
How the technology works
The device uses passive scanning photometric technology without any radiation and projection onto the object. The work is carried out with a slightly improved simple optical camera that captures visible light. The disadvantage is that if the lighting is insufficient, the object needs to be additionally illuminated.
Scanning is performed using the so-called silhouette method. It reproduces the contours of an object based on a sequence of frames captured by a video camera swept around the object against a well-contrasted background. nine0003
Stereoscopic non-contact passive 3d scanning system
Models with non-contact passive scanning technology
This type of device is represented by 3D Systems Sense, 4D Dynamics Gotcha models.
Device and principle of operation of a 3d scanner based on a non-contact passive scanning system
Devices are equipped with two cameras and an infrared sensor. The 3D Systems Sense scanner is made in the form of a stapler, it is a compact handheld device, it can be used with a tripod, in Gotcha (with a tripod and a handle), it is included. The principle of operation is passive optical. In both cases, power and data transfer is carried out via a USB cable. The devices have standard modes: scanning a person and an object. nine0003
Scan technology
The camera uses this technology to detect infrared (thermal) radiation and normal light reflected from an object. The systems are stereoscopic, that is, they use two cameras. The device compares frames, based on small comparisons of differences between them, determines the distance at each point of the image and recreates the object in digital form.
3d scanners with laser active scanning
This group of devices is represented by the following scanner models: 3D Systems iSense, DAVID Starter-Kit ver.2, MakerBot Digitizer. nine0003
Device
Devices have two lasers and a camera. It should be noted that the laser safety of gadgets corresponds to level I, which is completely safe for the eyes. The iSense scanner is designed to work only with the iOS operating system and with Apple iPad above 4 generations. It is made in a compact case, which is installed on a mobile gadget and connected to it with a USB cable, the battery lasts for 4 hours of its operation. It attaches like a webcam, scans and immediately displays the image on the iPad. nine0003
Models
DAVID Starter-Kit ver.2 3D scanner device: webcams and laser sensors with automatic adjustment function. The device comes with a tripod and tripod.
Maker Bot Digitizer is slightly different in design from the previous model. The body of the scanner is made as a pedestal, one part of which is a rotating platform, the other is equipped with two lasers on the sides and a camera in the middle. They scan an object located on the site.
How technology works
Let's describe how a 3D scanner works. Laser scanning is based on the triangulation method. This is an active scan tool. It uses laser beams by projecting it onto an object. The laser processes the surface of the object, its points are fixed on its different parts. The camera captures the laser dots on it, the angle of displacement of the laser beam and transmits the data to a computer with the appropriate software, which forms the object in digital form.
The scanning technology is called “triangulation”, because the triangle of the device's functional elements is involved in the work: the laser point on the object, its emitter, and the camera. In most cases, the dot is formed by a laser streak or spot passing over the surface of the object. nine0003
Structured light 3d scanning technology
Models that use structured or intermittent light technology in their work: DAVID SLS-2, RangeVision Smart, RangeVision Standard Plus, RangeVision Advanced, RangeVision Premium. A separate group includes manual Artec Spider, Artec Eva, Artec Eva Lite.
Device
The main functional elements of these devices are cameras and a light source that structures it in a special way and directs it to the scanned object. In the DAVID SLS-2 model, a video projector serves as a light source. These are mounted on a tripod with a tripod, which are included. This allows you to set up and calibrate instruments, install them in different positions and securely fix them, reducing vibration. Light sources in devices are halogen lamps, diodes, video projector. nine0003
Artec Spider, Artec Eva, Artec Eva Lite are made in a compact body with an iron-like handle. The handle has control buttons and outputs for interface and power cords. At the bottom there is also a hole for standard photo tripods and legs for fixing the device on the surface. 3d scanner device has the following. From the bottom it is equipped with a 3D camera (there are three of them in Artec Spider) with increased resolution, from the top of the device - a flash (projector) of structured illumination, a central color texture camera in the middle, along with light sources in the form of 6 or 12 diode bulbs. All light sources have white radiation. The device comes with a standard mini-USB interface cable and a power cable. Additionally, you can buy a rechargeable battery. nine0003
How the technology works
Such devices are also called structure-light 3D scanners. The scanning technology is similar to laser triangulation (light, emitter, camera). The important thing is that they can work without markers - the object does not need to be glued with a lot of markers and marks.