3D printed super car
The Czinger 21C is a 1,233bhp 3D-printed hypercar
Geneva Motor Show 2020
Californian Koenigsegg rival has an 11,000rpm V8, a 1+1 layout… and costs $1.7m
Jack Rix
Published:
21 Feb 2020
Skip 13 photos in the image carousel and continue reading
Turn on Javascript to see all the available pictures.
We’ve seen the teasers, we’ve grappled with the name (silent C, pronounce it like the tower burger) now, at last, Czinger is ready to divulge all the good stuff on its 21C hypercar. And the big news is it’s 3D printed. Well, large sections of the chassis are, paving the way for a revolutionary new car manufacturing process that could change… everything.
Before we get into all that though, ready for the numbers? Please adopt the brace position. The engine is an in-house developed 2. 9-litre twin-turbo V8 producing 937bhp with an 11,000rpm red-line. It’ll be the world’s most power-dense production engine, connected to a seven-speed sequential gearbox.
Advertisement - Page continues below
On the front axle are two electric motors fed by a 2kWh lithium-titanate (faster to charge and discharge than normal lithium-ion) battery pack housed in the sills and kept topped up by a rear motor generator.
In the non-homologated, track orientated 2021 launch car they contribute a further 237bhp for four-wheel drive and a grand total of 1,174bhp. Which is a lot. The kerbweight is 1,165kg, which isn’t. “I love Bruce Lee. I’m not an Arnold Schwarzenegger guy. The future is about being lean and mean and efficient, it’s all about power to weight.” That’s Kevin Czinger, founder and CEO. More on him in a bit.
You might like
BMW iX1 review: prototype EV tested in the UK
Report 5
This is what happens when you take a Bentley Bentayga on track
Official: this is the production-ready Lamborghini Huracán Sterrato
The claimed performance figures are 0–62mph in 1. 9 seconds, a quarter mile in 8.3secs at 170mph and a top speed of 236mph, despite 790kg of downforce at 155mph. Wait until 2022 for the more slippery, and fully homologated, road-biased version and you get more hybrid assistance for a total of 1,233bhp, although it weighs a bit more at 1,250kg. Hardly a fatty, still - almost - that perfect one-to-one power-to-weight ratio. Top speed climbs in the low-downforce version to a tyre-troubling 268mph.
Were you to choose this moment to scoff loudly and dismiss Czinger as another prime piece of vapourware, I wouldn’t blame you. The gutter of supercar history is clogged with ambitious start-ups like this, but Czinger’s endgame isn’t just to sell 80 (25 track, 55 road) 21Cs for $1.7m a pop. Its mission is to change the way cars are designed and built through the freedom of 3D printing and a revolutionary manufacturing process designed to de-materialise and de-capitalise everything… 21C is merely a proof of concept.
Advertisement - Page continues below
“Here’s what it is, man. I want to build really bad-ass stuff, but if you’re a craftsman who is actually a technologist, you need to create the right tools. I want this car company Czinger to be five blocks ahead of anybody else on the planet in creating these tools and expressing them as the cutting edge of the mind.” Kevin Czinger again, not your average CEO.
2359
I’m walking around the 21C with Czinger in his LA factory and you can forget classic mid-engine proportions, the 21C is a shape-shifter. Long and low from the side, a single curve sweeping from nose to tail, but then narrow as you circle around. From the front, a windscreen that originates ahead of the front axle; from the rear, a wing, diffuser and mesh, mainly.
Distinctive looks were baked-in from the moment Czinger insisted on a 1+1 layout. “I love superbikes. Being in that centre driving position is optimal from a driving, handling and emotional standpoint,” he says. I slide my bum over the wide sill and drop into the driver’s seat. He’s not wrong, I’m not even moving and there’s an immediate sense of focus. In a McLaren F1 or Speedtail you’re flanked by your passengers, practically wearing them as shoulder pads, but here you’re on your own. Even with a passenger in the back, legs akimbo, you’ll soon forget they’re there.
Get all the latest news, reviews and exclusives, direct to your inbox.
Your Email*
Country*
Please select your countryUnited KingdomAfghanistanAland IslandsAlbaniaAlgeriaAmerican SamoaAndorraAngolaAnguillaAntarcticaAntigua and BarbudaArgentinaArmeniaArubaAustraliaAustriaAzerbaijanBahamasBahrainBangladeshBarbadosBelarusBelgiumBelizeBeninBermudaBhutanBoliviaBosnia and HerzegovinaBotswanaBouvet IslandBrazilBritish Indian Ocean TerritoryBritish Virgin IslandsBruneiBulgariaBurkina FasoBurundiCambodiaCameroonCanadaCape VerdeCaribbean NetherlandsCayman IslandsCentral African RepublicChadChileChinaChristmas IslandCocos (Keeling) IslandsColombiaComorosCongo (Brazzaville)Congo (Kinshasa)Cook IslandsCosta RicaCroatiaCubaCuraçaoCyprusCzech RepublicDenmarkDjiboutiDominicaDominican RepublicEcuadorEgyptEl SalvadorEquatorial GuineaEritreaEstoniaEthiopiaFalkland IslandsFaroe IslandsFijiFinlandFranceFrench GuianaFrench PolynesiaFrench Southern TerritoriesGabonGambiaGeorgiaGermanyGhanaGibraltarGreeceGreenlandGrenadaGuadeloupeGuamGuatemalaGuernseyGuineaGuinea-BissauGuyanaHaitiHeard Island and McDonald IslandsHondurasHong Kong S. A.R., ChinaHungaryIcelandIndiaIndonesiaIranIraqIrelandIsle of ManIsraelItalyIvory CoastJamaicaJapanJerseyJordanKazakhstanKenyaKiribatiKuwaitKyrgyzstanLaosLatviaLebanonLesothoLiberiaLibyaLiechtensteinLithuaniaLuxembourgMacao S.A.R., ChinaMacedoniaMadagascarMalawiMalaysiaMaldivesMaliMaltaMarshall IslandsMartiniqueMauritaniaMauritiusMayotteMexicoMicronesiaMoldovaMonacoMongoliaMontenegroMontserratMoroccoMozambiqueMyanmarNamibiaNauruNepalNetherlandsNetherlands AntillesNew CaledoniaNew ZealandNicaraguaNigerNigeriaNiueNorfolk IslandNorthern Mariana IslandsNorth KoreaNorwayOmanPakistanPalauPalestinian TerritoryPanamaPapua New GuineaParaguayPeruPhilippinesPitcairnPolandPortugalPuerto RicoQatarReunionRomaniaRussiaRwandaSaint BarthélemySaint HelenaSaint Kitts and NevisSaint LuciaSaint Martin (French part)Saint Pierre and MiquelonSaint Vincent and the GrenadinesSamoaSan MarinoSao Tome and PrincipeSaudi ArabiaSenegalSerbiaSeychellesSierra LeoneSingaporeSint MaartenSlovakiaSloveniaSolomon IslandsSomaliaSouth AfricaSouth Georgia and the South Sandwich IslandsSouth KoreaSouth SudanSpainSri LankaSudanSurinameSvalbard and Jan MayenSwazilandSwedenSwitzerlandSyriaTaiwanTajikistanTanzaniaThailandTimor-LesteTogoTokelauTongaTrinidad and TobagoTunisiaTurkeyTurkmenistanTurks and Caicos IslandsTuvaluU.
S. Virgin IslandsUgandaUkraineUnited Arab EmiratesUnited StatesUnited States Minor Outlying IslandsUruguayUzbekistanVanuatuVaticanVenezuelaVietnamWallis and FutunaWestern SaharaYemenZambiaZimbabwe
By clicking subscribe, you agree to receive news, promotions and offers by email from Top Gear and BBC Studios. Your information will be used in accordance with our privacy policy.
The problem with a 1+1, mid-engined car is there’s quite a lot of human to fit in before you get to the oily bits. Hence the driver’s seat pushed right to the pointy end of the car, and an engine slung out over the rear axle. I question Czinger on the sanity of this configuration: “Yes, it’s a challenge, but what the heck is life for?”
But the real fun begins when you see a bare chassis. Any sections, especially high-load areas, that can be 3D printed, are. Everything from the suspension wishbones to front crash structure, windscreen surround to dashboard is ctrl+P in aluminium and titanium alloys. Wherever possible, printed nodes are joined by cost-saving, off-the-shelf materials – like carbon-fibre tubes and standard-sized aluminium extrusions to create a super-stiff and beautiful structure. You see, the software that designs the printed components only puts material where it needs to be, creating mesmerising, organic shapes that flow like tendons and muscle.
So there are gains in rigidity, cost benefits in less raw materials and it’s easily recyclable. At the end of a 3D-printed component’s life you melt it, shoot nitrogen through it and it returns to a powder, ready to be printed again. Then there’s the multipurpose perks – stuff like the exhaust muffler, designed by Czinger’s software to act not only as a silencer but as an integral part of the rear crash structure. You’ll also notice a 3D-printed rectangular exhaust tip – created so it can spit X-shaped flames on the overrun.
Skip 10 photos in the image carousel and continue reading
Turn on Javascript to see all the available pictures.
Cool, but not the full picture. Because it’s Czinger’s DAPS (divergent adaptive production system) that rips up the traditional car building business model. By splitting a factory into any number of 15m x 15m fully automated ‘cells’, each capable of assembling 10,000 chassis a year – that’s one every 20 minutes – and costing just $2.5m upfront for the robots and other hardware. “We’ve turned Henry Ford on his head,” says Czinger.
You’ll still need a climate-controlled 3D-printing lab churning out components on site and some extra space for final assembly by humans, but it reduces start-up costs for a new company exponentially. And because there’s no tooling, flexibility is through the roof. If one model isn’t selling well and another is, you simply switch that cell to produce the more popular version and meet demand. You needn’t sink hundreds of millions into a gigafactory based on vague predictions, you start small and scale up.
But still, we’re scratching the surface. Czinger’s ultimate vision is an “infinite expression of unique creativity”. Translated into English that means powerful software into which you put your needs, a computer then performs all the engineering calculations and outputs the components you need. Just press print, assemble, and the car is yours. “We’re only at a sub-systems level now,” he tells us, “but full vehicle integration isn’t far off.” Imagine an online vehicle configurator that doesn’t just let you choose your trim and paint, you could lay out the exact shape, size and capabilities you need, pay less for it, and tread more lightly on the environment.
“This isn’t a Lego block kit. This is a kit that says ‘before you touch the first Lego block you’ve customised every single block you’re going to use,’” Czinger explains. “After that you want to build something else? Just push it aside and customise every Lego block again, and they’re all interdependent and interrelated. That’s what digital manufacturing is in the end. We’re not going to be a supplier, we’re going to be a licenser of those tools.”
The 21C has four wheels and an engine, enough power to reverse the earth’s rotation, belongs on a teenager’s bedroom wall and we hope to drive it in anger very soon, but it’s not a car. Not really. It’s a company with a big idea making noise in the most engaging way possible. Top Gear doesn’t do marketing tools, but if it did, they’d look like this.
Geneva Motor Show 2020Supercars
Top Gear TV
Does the Czinger 21C Supercar Herald the 3D-Printed Future of Car Making?
- The Czinger 21C supercar is fast and a little revolutionary, but the manufacturing process that went into it could change the world.
- Czinger uses additive manufacturing, or what we call 3D printing, to make parts that are then glued together by robots.
- The Czinger manufacturing method is being exported around the world.
At first glance, it was just another supercar being hyped by its millionaire maker as the fastest thing since Warp Factor 6. Granted, the Czinger 21C was fast—the tandem-seated carbon-fiber-over-aluminum-spaceframe hybrid superbeast had lapped Laguna Seca in 1:25.446 seconds. There was no disputing that, it said so right there in the press release:
“Czinger, the trailblazing company that uses revolutionary design and manufacturing technologies to build state-of-the-art, homologated high-performance vehicles, has set a new lap record at WeatherTech Laguna Seca Raceway, smashing the old record by an astonishing two seconds!”
Note the exclamation mark! True, the 21C had a proprietary 2.88-liter twin-turbo V8 located right behind its two tandem seats, aided and abetted by an 800-volt electric drive system with one motor for each front wheel making a total of 1233 bhp. So it could do it.
Having seen so many such releases, however, we were skeptical. For instance, the release said, “lap record.”
“We don’t record lap records outside of sanctioned race laps,” said the WeatherTech Raceway track spokesman we called.
This content is imported from YouTube. You may be able to find the same content in another format, or you may be able to find more information, at their web site.
The lap record at WeatherTech Raceway Laguna Seca is held by Helio Castroneves, who turned a 1:07.722 in a Penske Indy car during the CART race in 2000. That’s quicker than 1:25.446, isn’t it? Well, this record is for production cars, see, and the Czinger beat the Randy Pobst-driven McLaren Senna by two seconds. The difference is that McLaren actually manufactured 500 Sennas and sold them to customers. Czinger hasn’t made any 21Cs that you can buy and won’t before 2023 or so. We could nitpick semantics like “lap record” and “production” all day.
But it would be a mistake to dismiss the Czinger 21C supercar just because of some over-anxious publicity stunt.
The biggest news about the Czinger is not how fast it’ll go, but how it and its maker will change the way cars are manufactured. For the last 118 years, since Henry Ford built the first assembly line in Highland Park, Michigan, cars rolled down a line and had parts added to them by human workers. Those parts were cast, stamped, extruded, sintered, or machined. Then all the parts were bolted, riveted, welded, or even glued together. Once you did enough of that, you had a car.
Kevin Czinger, for whom the lap-record supercar is named, has a different idea, making him potentially the Henry Ford of the new millennium.
Instead of all that extruding, stamping, bolting, and riveting, Czinger has developed a system based around additive manufacturing, or additive-layer manufacturing, which is the industrial production name for 3D printing. AM is a computer-controlled process that creates three-dimensional objects by depositing materials in layers in whatever shape they’ve been computer-programmed to become. In the case of car making, the material is usually some kind of aluminum alloy, but there are many, many materials that can be used.
Czinger didn’t invent additive manufacturing, 3D printing, or robots, of course, but he has a new way of bringing them all together.
"Most of the system is newly invented with ~500 patent filings," Czinger said. "It is a new system architecture, in-house purpose-built software and hardware for the three subsystems, and there is a new vehicle architecture.”
Wait, who’s Czinger? Kevin Czinger is something of a manufacturing revolutionary. He has a manufacturing facility in Torrance, California, unlike any you may have seen. In one huge room are a number of large, industrial AM machines printing parts, or adding layers until they’ve printed a part. In another room is a circle of robots centered around whatever it is they’re manufacturing. As the parts are printed and then delivered to the robots, the robots grab them in their computer-controlled hands and glue them together. Glue enough of them together and you have a car.
“That’s taking almost 50% of the mass out of a combined subsystem.”
Czinger is putting together not only the manufacturing process and facility I saw in Torrance, but has plans to set up similar, custom-built facilities all over the world. In most applications, you get a much more efficient part in terms of increased strength and decreased weight. In the conference room where we were talking there were a number of automotive assemblies, all looking a little like the creature in the Alien movies. I said that I like the look of a brake assembly, for instance.
“That’s taking almost 50% of the mass out of a combined subsystem,” Czinger said.
On the end of the conference table was an entire rear assembly of a car. Czinger walked over and picked the whole thing up. By designing everything through CAD, then downloading the design to the AM printer, the part can be made much lighter, with less material, and in a truly optimized shape.
“This is digital manufacturing, as it will be in the future,” Czinger said. “Today, we’re printing at a rate that if you took the very fastest machine on the planet, we’re printing 15x faster than that.”
He worked with the makers of AM machines to get the speed and accuracy he wanted. He sees what he’s doing as a revolution akin to the move from typewriters to computers—specifically, the first IBM Selectric typewriters that had two lines of memory.
“IBM said they’re going to digitalize the typewriter,” Czinger said, picking an analogy a writer/reporter could grasp. “I’m 62, so I remember when they had the IBM Selectric, and they’re like, ‘We’re digitalizing! We’re adding two lines of memory!’ Right? No, you have to architect desktop computing and desktop publishing if you want to have an actual digital system. We have 150 engineers and scientists here under one roof, like an old-school, Cold War skunk works, like the original Kelly Johnson skunk works. We architected an entire system for design, print, assembly, with what that really means, which is that all of the constraints are computer generated, including how you manufacture and how you assemble equipment that prints at the right rate and quality with the right materials. And then (we have) an automated assembly system that’s completely fixtureless, the assembly system can go from doing a full-scale large drone to a battery electric SUV with zero switchover time. None of the hardware ever changes.”
I got to see the system, but much of it is proprietary, so I can’t discuss a lot of details. But he had me sold. Sure looked like the future to me.
“We had a first principle idea which was to remove all of the hard tooling from the (manufacturing) process so that we could have a hardware base that adapted to any design,” said Kevin Czinger’s son Lukas Czinger, a Yale graduate in electrical engineering. “We can do that rear frame, do a customer rear frame, do a full chassis, just by changing the software, no hardware changes.”
About a year ago, in October 2020, the Czingers birthed a beta version of this new process. And it seems to do what it was designed to do.
“You could take that entire complex form and just 3D-print that as one solid metal piece.
”
“For our OEMs, we were able to show a print rate 50% faster than they needed for value production and an assembly rate about 35% faster than they need for full-volume production,” Kevin said. “We have a dozen programs for multi component structures,” said Kevin. “Our first production programs are going to be in vehicles on the road in early 2022. And these are with brands that are within groups that are in the top five global automotive groups by annual volume.”
So, just to review, it’s: computer-designed parts, 3D printers making those parts, which are assembled by robots, in a much smaller space than typical assembly lines.
So no more River Rouge. The Czingers say that carmakers could replace assembly lines that had been a mile long with assembly stations like the one I saw, greatly reducing the lead time, cost, and complexity of car making. And you can switch the car model that you’re building with every new assembly. No more downtime during model-year changeover. And all those spare parts carmakers have to keep in warehouses for 10 years? They will be replaced by instant 3D printing of whatever spare part you need.
So is this really a brave new world that has such robots in it?
“3D printing offers the chance to pretty dramatically reduce how much effort you have to put into assembly,” said Peter Zelinski, editor-in-chief of additivemanufacturing.media. “So something like a car’s chassis or even just a component like the assembly around the wheel, the wheel carrier, you think about all of the little parts from many different places that are riveted together or welded together or held with fasteners, and you could take that entire complex form and just 3D-print that as one solid metal piece.”
While carmakers have used additive manufacturing or just plain old 3D printing for years, it’s never been optimized on such a large scale.
“Additive Manufacturing has been used in the auto industry for some time, but the last few years we have really seen accelerated growth in the technology,” said Ali Shabbir, GM engineering group manager for additive design and manufacturing, via email. “General Motors sees value in three key areas. Prototype parts allow for rapid, iterative development of components and greatly reduces tooling costs while increasing agility in providing functional pre-production parts. Manufacturing tools can be printed to be lighter and more ergonomically designed for assembly operators, all while significantly reducing lead times. Localized printing is also promising technique, as additive manufacturing engineers in Warren, Michigan, could design a part and then send the designs to be printed at assembly plants around the world. Production parts are the latest application of additive manufacturing we have implemented. Based on volume, cost, and build complexity, a business case for each production part needs to be made.”
Toyota doesn't use AM very much.
"Very little for in-line production," Toyota said in response to a question about AM's presence in production. "Most of 3DP applications are proto parts, proto tools, proof of concepts, occasionally spare part manufacturing. The largest utilization of 3DP is for prototyping and pre-production purpose."
Toyota doesn't see it as a major contributor to mass-production yet, either.
"Not with the current technology – 3DP cycle times are very long – unless we batch production of 3DP parts or use it for low option manufacturing."
“For our prototyping and prove-out we use it a lot,” said Andre Hudson, head of product design at INDI EV. “But in the production, there’s just so many challenges, it’s a whole different thing—the materials, the thicknesses of materials, the process—to make it durable enough to actually be to put in a product that you’re going to sell to somebody to use. I still think we’re quite a ways off.”
Limitations of AM include the size of AM machines right now, which limit the size of parts that can be made. You can’t AM and entire automotive space frame, for instance.
Kevin Czinger agrees that massive adoption of a system like his in the global auto market is still in the future.
“3D printing today is not even a baby step,” he said. “It’s not even born. We had to design the materials and the machines to actually do it at an industrial level.”
I asked Zelinski if he thinks we’re in the middle of a revolution in manufacturing.
“I think we are, actually. We are in the middle of the beginning of it,” Zelinski said. “But the revolution won’t be a change in the types of parts we see today and how they’re made. It’s an utter rethinking of A) part designs and B) manufacturing enterprises. So the part designs change because, as you saw how he lifted up that component (the big rear subframe). There’s all kinds of design freedoms now to use way less material, far fewer fasteners, to have lattice structures on the inside instead of a solid form, to make things lighter and to utterly rethink how manufactured parts are designed and what they look like.”
So expect to see lighter cars made from less material at what could be a lower cost. But maybe not this week.
Do you think we’ll see 3D-printed cars in any real volume in the near future? Or will it remain a niche manufacturing process? Share your thoughts in the comments below.
Mark Vaughn Mark Vaughn grew up in a Ford family and spent many hours holding a trouble light over a straight-six miraculously fed by a single-barrel carburetor while his father cursed Ford, all its products and everyone who ever worked there.
3D-printed supercar unveiled
3D-printed Blade supercar with bodyshell and creator Kevin Zinger / Divergent Microfactories
Divergent Microfactories (DM) unveiled a prototype of a powerful, lightweight vehicle for production in small volumes in low-cost industries around the world. The California startup idea echoes another industry novelty - a 3D printed car from the American company Local Motors, which highlights the potential of new manufacturing technologies for small flexible industries that challenge the economy of large car factories, writes the Financial Times. nine0003
DM's Blade is built on a chassis that is 90% lighter than traditional car designs. A double car with a tandem seating and guillotine doors weighs 635 kg, with a 700 hp engine. with. it can accelerate to 60 mph (96.6 km/h) in about 2 seconds. The company is going to build a plant over the next 1.5 years to develop a technique for manufacturing a car, and then sell the technology to make it to entrepreneurs who can raise $10 million to create their own factories to make a car, says Kevin Zinger, founder and CEO of the company. nine0003
DM, as Local Motors, is betting on 3D printing to avoid the high cost of stamping equipment for car chassis manufacturing. Also known as layering, the technique involves layering a material, in this case aluminum, to form a part.
The Blade is based on a three-dimensional framework of hollow aluminum nodes - 3D printed structural connectors that are held together by carbon rods. The design forms a light and elastic body, which is quickly assembled in any room without the use of special tools. Companies that have licensed the technology can source most other components from local suppliers and build their vehicles using the modular design, Zinger says. nine0003
These parts are assembled into the body shell of the Blade /Divergent Microfactories
At the beginning of the year, Local Motors unveiled a prototype of its own car, completely 3D printed, including the chassis and outer shell. The car is also designed to be assembled at local facilities using components from various suppliers. The cost of creating a local production could be $10-20 million, says Justin Fishkin, director of strategy at Local Motors. The Knoxville, Tennessee plant being built to produce the "printed car" is designed to break even at 2,400 cars a year, he says. nine0003
Mini-factories using 3D printing among other production methods have begun to attract the attention of entrepreneurs due to the rapid reduction in equipment costs. Their big advantage is their low capital intensity, says PA Consulting manufacturing expert Tim Lawrence. "Setting up production lines, assembly lines, special tooling requires huge amounts of investment. 3D printing is an add-on technology, you don't have to squeeze on tools, so you don't need much capital equipment," he says. nine0003
Layering is widely used in the aerospace industry and on some Formula 1 car manufacturers. But the technology is too slow to catch on in the mainstream auto industry, where its use has so far been limited to pre-production stages. Automakers are using 3D printing to sample plastic components like interior door handles, speaker grilles and air vents, as well as various metal parts. Some cars with low production volumes are equipped with components obtained by 3D printing, for example, the Swedish hypercar Koenigsegg uses this method to make engine turbines. nine0003
But the use of technology in mass production is seen as a distant prospect. For factories producing several hundred thousand cars a year, conventional methods of car production are faster and more cost-effective.
Zinger, co-founder of electric vehicle maker Coda Automotive, which went bankrupt in 2013, says the experience spurred him to look for new and more flexible forms of production after the high cost of tooling for Coda machines meant they couldn't respond to rapidly changing circumstances. Layering also creates more variety and customization for consumers without increasing manufacturing costs for the manufacturer, which can significantly change the aftermarket. nine0003
Media news2
Is advertising distracting? With a subscription you won't see it on the siteWorld's first 3D printed supercar
700 horsepower under the hood, weighs only 650 kilograms, and accelerates to 100 km/h in just 2.2 seconds. Introducing the Blade, the world's first 3D printed supercar.
10 PHOTO
1. 3-D printing is increasingly used in our lives - from everyday objects and medical implants to real bridges. Now to this list will be added another car, which will also be faster than most supercars.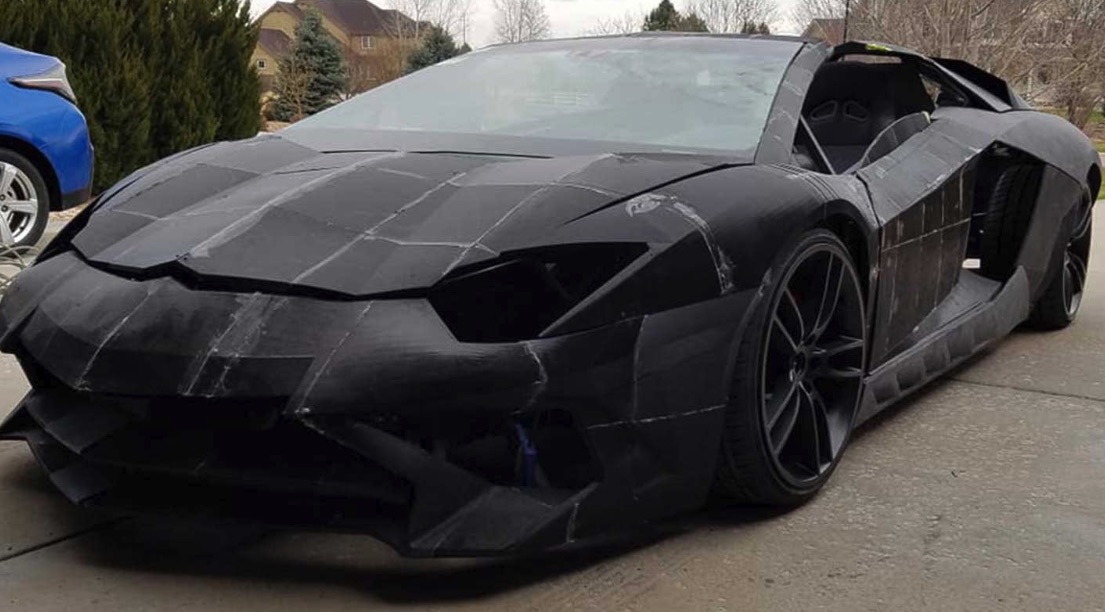
3. According to the company's representatives on the official website, the new 3D printing technology will significantly reduce the costs associated with the production of cars (materials, energy, etc.), as well as reduce environmental pollution. (Photo: Mel Lindstrom/divergentmicrofactories.com). nine0002 4. The Blade supercar is more environmentally friendly, safer and lighter than conventional cars. (Photo: Mel Lindstrom/divergentmicrofactories.com).
5. With 3D printed aluminum parts connected with special carbon fiber tubes, the Blade's chassis will be 90% lighter than traditional cars. At the same time, the Blade will be stronger, more durable and, most likely, accident-free, which in turn will help reduce the cost of CASCO insurance.
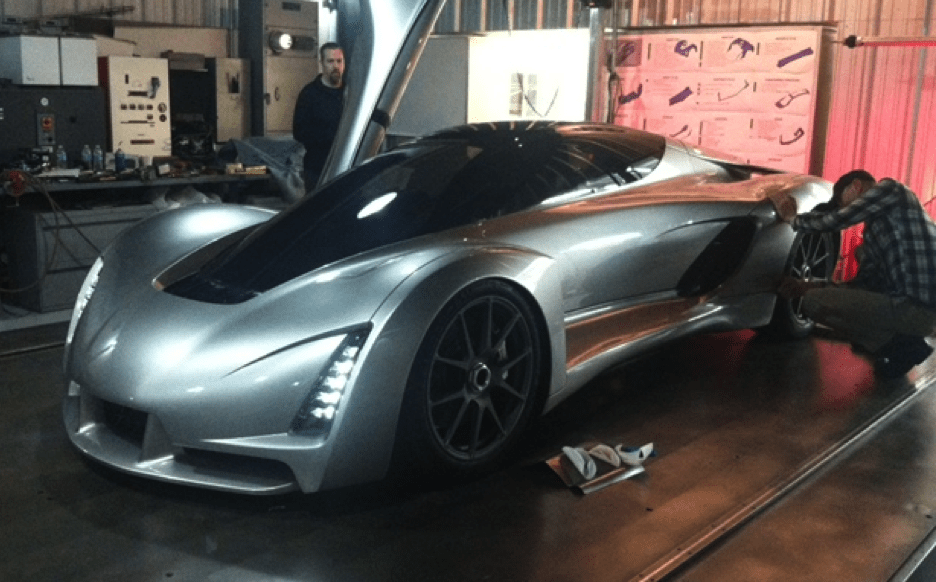
7. Under the hood of the Blade is a 700 horsepower engine, thanks to which it can accelerate to 100 km/h in 2.2 seconds. For comparison, the Porsche 911 Turbo accelerates to hundreds in 2.9 seconds, and the Lamborghini Aventador in 2.7 seconds. (Photo: Mel Lindstrom/divergentmicrofactories.com).
8. The Blade supercar is not only super modern and fast, but also environmentally friendly. Divergent Microfactories claims it has very low emissions, accounting for only 1/3 of the pollution emitted by electric vehicles.
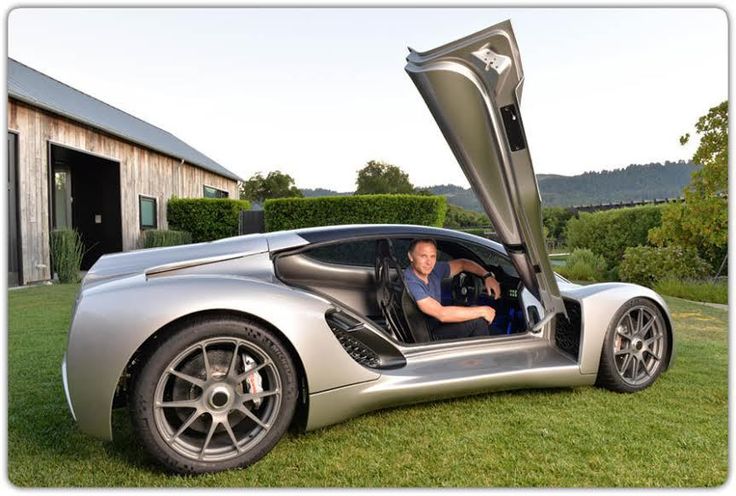