3D aluminium printer
Large Format 3D Printer for Aluminum and Inconel Parts
We’re pretty proud of our newest 3D printer. And who wouldn’t be? According to its maker, GE Additive, the Concept Laser X Line 2000R is “the largest metal laser melting machine” on the planet. It’s equipped with a pair of 1000-watt fiber lasers, a 31.5 in. x 15.7 in. x 19.7 in. (800mm x 400mm x 500mm) build volume, and it’s very well-suited for all manner of end-use aerospace, automotive, and industrial components.
Oh, and did we mention we have two?
Large Format, Production Printing
What’s more important to you is what types of parts these massive printers can produce, what kinds of metals they can print, and what you need to know about designing large-format 3D-printed parts.
Let’s start with the first question, which is easy to answer. Anyone who follows GE Additive knows that its team is all about lowering manufacturing costs, improving product performance, and decreasing time to market. So are we. Simply put, the X Line 2000R has a bunch of cool features that make it easier to operate and maintain, thus increasing our ability to crank out otherwise impossible parts—big, complex, highly accurate metal parts made directly from a 3D model.
Meet the Materials: Aluminum vs. Inconel
So what are the metals? We've dedicated the newest machine to AlSi10Mg, an aluminum alloy defined under ASTM standard F3318. Though considered by some to be a casting alloy, it has also proven to be top of the list for anyone searching for a strong yet lightweight 3D printing metal that also excellent thermal conductivity. It contains roughly 10% silicon by weight, so is a bit more abrasive to machine than 6061-T6 aluminum, but offers comparable tensile strength (around 50 ksi). Depending on the heat treatment used, it’s also a bit harder—approximately 72 on the Rockwell B scale, compared to 60 or so for 6061—leading to a slightly lower elongation at break (between 5% to 8%, based on the shear direction).
Tensile Strength* | Elongation at Break | Hardness* | |
Inconel 718 | 139-208 ksi | 1818-40% | 27-46 HRC |
Aluminum (AlSi10Mg) | 45-50 ksi | 8% | 46-59 HRB |
*Varies by resolution and heat treatment
These properties help make AlSi10Mg the de facto standard within the additive manufacturing (AM) world for a range of aluminum components. It's an ideal choice for thin-walled heat exchangers, ductwork, and radiators, as well as brackets, levers, and other mechanical or structural components. Further, GE Additive has developed build parameters that deliver a good balance between print speed, part density, and surface quality.
Then, there’s Inconel 718—the workhorse of the aerospace and energy industries. This nickel-based superalloy is intended for high-stress, high-temperature, or highly corrosive environments (sometimes all three at once). ASTM standard F3055 defines “INCO 718” 3D-printed parts as having physical properties on par with their forged or cast counterparts. This means ultimate tensile strength of 139-208 ksi, elongation at break up to 40%, and a melting point of at least 2300° F (1260° C), making it extremely suitable for gas turbine components, rocket engines, and other mechanically or thermally demanding environments.
Decision Time
So which one should you use? Unfortunately, the decision is not simply about weight. Because 3D printing can create very complex lattice-like and honeycomb structures, designers can produce lightweight parts compared to those made subtractively, even when using relatively dense, heavy metals like Inconel 718. On the flip side, modern design tools and printing processes tend to make all 3D-printed structures much stronger than they otherwise would be, putting aluminum in the running for applications that were once unthinkable.
Much of the decision comes down to cost. The aluminum powder used in all 3D printers is less expensive than any superalloy, Inconel included. And due to its lower melting point, the particles are a bit easier to fuse than Inconel, decreasing processing time somewhat. Lower temperatures also mean fewer concerns over thermal growth and curling, an important consideration on any laser-based 3D printer. However, given that raw material expense represents a smaller portion of the total 3D-printed part cost compared to machined or cast components, designers should focus instead on the specific material properties needed for their application
Benefit Comparison: Inconel 718 vs. Aluminum
In summary, Inconel 718 should be used in extreme temperature environments (hot or cold), where corrosion and chemical attack are likely, or where this highly capable alloy's superior strength and hardness are necessary. AlSi10Mg aluminum, on the other hand, is the first choice where weight is the primary consideration (assuming that the finished part will meet all physical demands) or where piece-price is a key driver. As always, determining the cost delta is a simple matter of uploading the CAD model to our quoting system, selecting the different materials, and comparing the quotes for each.
Cost | Tolerance to Extreme Temp. | Lightweighting | Corrosion Resistance | |
Inconel 718 | X | X | ||
Aluminum (AlSi10Mg) | X | X |
Better 3D Printing Builds for Large Parts
Some might wonder if large-format 3D-printed metal parts come with a different design playbook. Not really. Design for Additive Manufacturing (DfAM) guidelines tell us that the thick, bulky parts with which traditional manufacturers are familiar should be optimized for 3D printing. Eliminate heavy cross-sections and excess material in favor of the honeycombs and lattice structures mentioned earlier. Avoid unsupported horizontal planes wherever possible—if not, additional post-processing will be needed to remove build supports, driving up costs.
And as with all additive manufacturing, look for opportunities for part consolidation. This last bit of advice is especially true on large-format parts, where what was once a multi-piece assembly containing perhaps hundreds of individual components and fasteners can be printed as a single part. The potential cost and lead-time savings are enormous, as is the advantage of shortening the supply chain. If you have any questions or need a hand with your part design, you know where to find us.
3d Print Aluminum | Metal 3D printing
Aluminum’s material characteristics make it ideal for many applications in many industries, for example aerospace and automotive.
EOS’ aluminum family of powders encompasses the AlSi10Mg, AlF357 and Al2139 AM alloys which are typical aluminum-silicon casting alloys. These powders are designed and tested for use on EOS’ metal 3D printers.
All EOS aluminum powders are shipped with an inspection certificate (according to EN 10204, Type 3.1) showing the results of the extensive QA testing not only of the powder itself, but also of test parts built on a dedicated system with a dedicated process.
EOS also offers a wide range of validated processes for each of the above materials. These offer the optimal combination of parameters (e.g. laser power, layer thickness, etc.) in order to ensure that the properties of the 3D printed part are consistently achieved.
Parts printed using EOS Aluminum AlSi10Mg offer good strength, hardness and dynamic properties as well as good thermal properties and low weight.
Typical Part Properties | |
Chemical composition in compliance with | AlSi10Mg |
Ultimate Tensile Strength | 460 MPa |
Yield Strength | 245 MPa |
Elongation @ Break | 5 % |
EOS Aluminium AlSi10Mg Material Data Sheet
914,6 KB
Download
Source: Conflux | EOS
Conflux Heatexchanger built in aluminum
Parts printed using EOS Aluminum AlF357 offer a combination of low weight, corrosion resistance and high dynamic load bearing capacity.
Typical Part Properties | |
Chemical composition in compliance with | AlSi7Mg0.6, SAE AMS 4289 |
Ultimate Tensile Strength | 330 MPa |
Yield Strength | 260 MPa |
Elongation @ Break | 11 % |
EOS Aluminium AlF357 Material Data Sheet for EOS M 290 and EOS M 400
770,4 KB
Download
EOS Coral Heatsink in Aluminum
EOS Aluminium Al2139 AM is a 2000-series high strength alloy specifically designed for AM. It demonstrates outstanding performance in elevated temperatures up to 200 °C. The fast and simple heat
treatment procedure enables an affordable part production.
Typical Part Properties (T4 heat treated state) | |
Chemical composition | modified from Aluminium Association Teal Sheet for Al2139 |
Ultimate Tensile Strength | 520 MPa |
Yield Strength | 460 MPa |
Elongation @ Break | 4 % |
EOS Aluminium Al2139 AM Material Data Sheet for EOS M 290
318,8 KB
Download
Source: AM Metals | EOS
Wheel Carrier with integrated cooled engine housing
High-precision aluminum 3D printing at Sprint 3D!
aluminum 3D printing is a relatively new technology in the production of high strength metal products. Using aluminum alloys, you can create almost any product - from home decor and souvenirs to parts of industrial equipment or even aircraft.
SPRINT3D is already using 3D printing technology with aluminum for its customers. We use the latest equipment - Renishaw AM400 (SLM) aluminum 3D printer that allows you to grow products of almost any complexity based on metal powders.
We invite you to learn more about aluminum 3D printing, features and benefits.
Why 3D printing with aluminum is a new step in production
First and foremost are the materials used. Not just powdered aluminum is used. The material itself is quite malleable. But when nanoparticles are mixed with raw materials, crystallization occurs, which greatly increases the strength of finished products and prevents the formation of cracks during their hardening. nine0005
For the first time, the technology has been successfully applied in the aerospace industry.
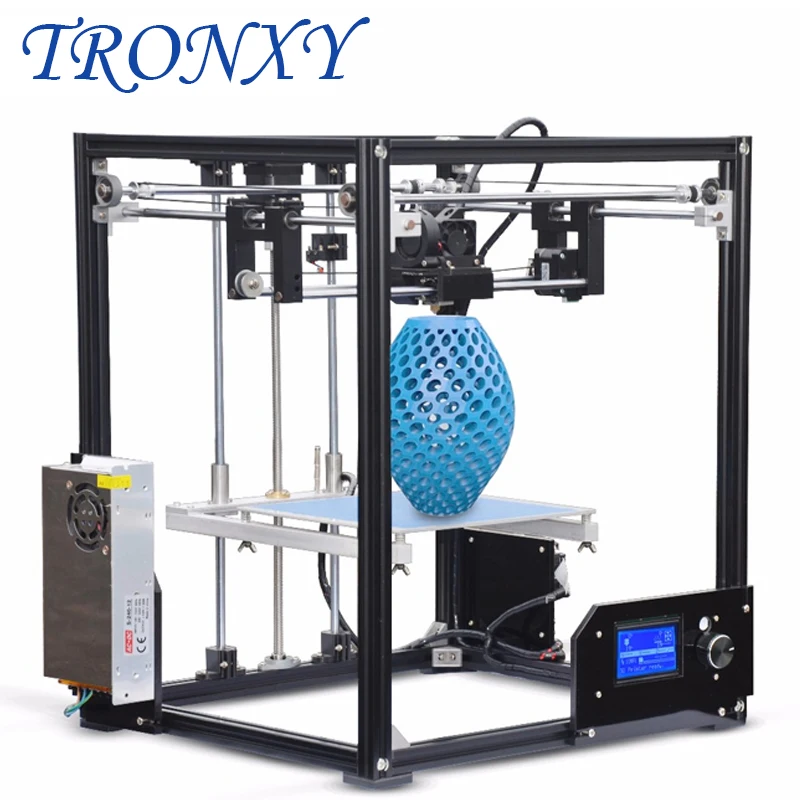
- Allows small-scale production of metal products. The main advantage is high geometric accuracy, which was previously unavailable. nine0043
- Suitable for low volume production and prototype printing. For example, to check the ergonomics of the product and carry out the necessary checks.
- This is the best choice for tool making. Complexity, dimensions, geometry - everything is individual.
We use the most suitable production material, aluminum alloy AlSi10Mg-0403. It contains aluminum alloyed with silicon (no more than 10%), magnesium, and other components in small quantities. Thanks to silicon, the alloy becomes much stronger than pure aluminum. In addition, an oxide layer is formed on the surface of the printed products, which has increased corrosion resistance. It can even be enhanced using chemical anodizing technology. nine0005
4 key benefits of
3D printing with aluminumThere are many more benefits, but we will focus on the main ones:
- Increased flexibility in design and production. For example, the technology allows the creation of complex internal channels, mesh structures and bionic elements. Previously, this required the serious work of specialists and the introduction of expensive technologies into production.
- Short design and production times. nine0003 3D printing with aluminum is much easier and faster than creating similar products using other methods. First of all, due to the maximum automation of the process.
- Reduced finished product weight. Similar blanks made using other technologies weigh more. This puts some restrictions in terms of operation and their implementation in various units, tools and mechanisms.
- Reduced financial costs in production.
With the same budget and volume of material, it is possible to produce a numerically large batch of products and, in general, reduce costs by at least a few percent. nine0043
Existing mathematical models that have been used for 3D printing on other equipment can be quickly and inexpensively optimized for 3D printing with aluminum on new equipment. At all stages of production, product control is ensured. For this we use computed tomography. This allows you to eliminate even the slightest defects.
Our
AM400 AM400 aluminum 3D printer is a versatile printer that can work not only with the mentioned AlSi10Mg-0403, but also other metal powders. But we use it mainly in conjunction with aluminum powder materials. One of the key advantages of this printer is the ability to quickly change the printing system between different types of metal. This reduces production time and allows different materials to be processed on the same machine. nine0005
Main parameters of the model:
- Working area: 25 cm × 25 cm x 30 cm.
- The level of argon use is at least 60% lower than in analogues.
The printer is already widely used in the aerospace industry. The reason is the ability to reduce the weight of the product, while maintaining all its parameters and strength indicators. The AM400 allows you to create particularly complex parts. For example, with complex internal cooling circuits. Previously, this was not possible due to the use of outdated metal casting methods. They did not allow creating models of high complexity. nine0005
The AM400 aluminum 3D printer is ideal for small batch production. But if necessary, it can also be used for mass production.
Selective Laser Melting Technology and Features
The AM400 supports the SLM laser melting technique. This is one of the newest destinations used in the most demanding segments:
- engineering sector;
- space/aerospace;
- production of spare parts and structural products.
3D printing with aluminum paired with SLM technology allows you to create functional metal products with increased construction accuracy. For example, you can implement complex systems of channels within the product for cooling.
Key features of the SLM:
- The vacuum technology used saves 60 to 80% argon. nine0043
- Preparation of equipment for production - no more than 15 minutes.
- Focal spot - 70 microns. This gives an improved quality of model building in this class.
- The powders used are practically not in contact with the atmosphere.
- For R&D powders, the built-in small chamber can be used.
- Renishaw branded encoders guarantee increased durability.
And this is only a small part of all the benefits. nine0005
Our offer
SPRINT3D prints metal parts, engine components, components of complex metal structures. We also carry out 3D printing with aluminum for the medical industry.
Contact our manager to discuss production possibilities, terms and main parameters of future products. We will provide convenient conditions, a comfortable price and standardized quality of 3D printing of all products. If necessary, we will offer alternative production options. nine0005
You can get advice, discuss the order and find out the price of production on the website through a special form or by phone number 8 (495) 740-51-70.
You may be interested in
Our company offers 3D aluminum printing using Selective Laser Melting technology. SLM technology allows you to create structural parts that are close in parameters to casting. Complex shapes are possible with internal structures that cannot be replicated by casting or milling. nine0005
We have a Concept Laser M2 Cusing machine for printing with AlSi10Mg powder alloy. This is a 3D printer for layer-by-layer printing with powder metals and alloys in a nitrogen or argon environment.
During the printing process, a thin layer of aluminum powder is applied to the platform, where it is fused by a laser along the outlines of the future part. The platform then lowers slightly and the process repeats. As a result, we get a strong anisotropic part, as close as possible in terms of characteristics to casting. nine0005
Aluminum printing examples
Aluminum 3D printing prices
Technology | Equipment | Region | Layer, µm | Accuracy, mm | Materials | nine0228 Price (r/cm3)|
---|---|---|---|---|---|---|
SLM | Concept Laser M2 | 250x250x280 | 20-80 | +-0.![]() | 12X18H10T (stainless steel) 03Х17Н12М2 AlSi10Mg (aluminum) | 500r/cm3 500r/cm3 400r/cm3 |
Manual post-processing | nine0268 Cleaning of support material, surface grinding and polishing, painting work1500 rub/man-hour | |||||
3D modeling | Create 3D models from drawings or templates | 2500 rub/man-hour |
SLM and DMLS aluminum printing technologies are used in completely different areas: from the creation of new parts for the aerospace industry, to the printing of broken parts for cars and other equipment. Unlike traditional manufacturing methods such as milling and casting, the selective layer-by-layer fusion process has much fewer restrictions on shapes, negative angles, cavities, and so on. nine0005
Why is powder metal printing so good? First of all - small-scale. Casters and millers may simply not take on one medium or small aluminum part - preparatory procedures are very expensive. The production of molds for casting, as well as the preparation and debugging of the CNC program, require time and money. And one detail will be easily printed for you.
For 3D printing with aluminum, we use AlSi10Mg powder alloy - its composition is aluminum, about 10 percent silicon and magnesium. Lightweight and strong, this alloy is great for rapid prototyping and new parts. nine0005
SLM printing with Al powder is widely used in the aerospace industry. Lightweight and durable parts with the ability to create internal cavities and cooling channels are indispensable for modern aircraft manufacturing. Also, this technology began to be used to create custom cooling radiators in electronics.
How is aluminum printed on a 3D printer? First, a thin first layer of powder is applied, with a thickness of 25-100 microns. Then the laser beam goes around the desired areas, fusing the powder to the metal. Then a layer of powder is applied again and the process is repeated. Of course, a lot of experience of the staff is necessary, the specialist must correctly locate the part and support in the specialized software. 3D printing parameters may also differ for different alloys and different powders with different grain sizes. And finally, post-processing in the form of tumbling or grinding may be required. nine0005
Why order from us? Our company has its own production, with its own 3D printers, including those for metal. This allows us to quickly fulfill your orders and keep prices low. Our employees have extensive experience in the field of additive technologies, which allows us to perform prototyping work as efficiently as possible.
Advantages of 3D printing with aluminum
The main advantages of powder printing with aluminum alloys.
nine0191 Speed
Printing an aluminum (silumin) part is much faster than making it with traditional metal casting and CNC milling.