Xerox 3d metal printing
Metal 3D Printer Selection Begins with the End in Mind
By Pete Basiliere - Founder, Monadnock Insights The choice of 3D printing technology, whether using plastics, composites, or metals, begins with the end in mind. The items you want determines their material, which determines the best technology for printing the part. From there, choose the 3D printer provider that offers the technology and printer models that are appropriate for your application.
For example, let's say that you want to make aluminum load-bearing brackets that are components of a larger device. Your supply chain logistics staff dictate a quick turnaround, while a low total cost is required for adequate profit margins. On the surface, five 3D printing technologies offer the means for producing that bracket: binder jetting, directed energy deposition, powder bed fusion, sheet lamination, and liquid metal. However, the part requires a blend of availability, cost, material, and performance characteristics. That leaves two options: powder bed fusion and liquid metal.
Comparing the two technologies will determine which is most appropriate for use and, therefore, which vendor to consider. The initial evaluation should focus on three areas: quality, total cost of ownership, and staff skillset.
ElemX 3D Liquid Metal printed drive hub
Evaluate metal 3D printers based on their ability to replicate parts with the same quality as the original component. You, and your customers, have certain expectations regarding the fit, finish, and use of your parts, whether for one order or multiple orders placed over time.
Quality
Characteristic | Powder Bed Fusion | Liquid Metal |
Accuracy: Ability to precisely print as designed | Layer thickness: 0. Wall thickness: 1.0 - 10 mm Density: >99.0% Dimensional tolerance (without post-processing): <0.1 mm to 0.3 mm | Layer thickness: 0.24 mm minimum Wall thickness: 3 mm Density: >98.5% Dimensional tolerance (without post-processing): <0.5 mm to > 0.6 mm |
Strength: Performance of finished parts compared to internal and external standards | Comparable to cast parts; high strength aluminum cracks; may be brittle with low elongation; heat treatments improve strength | Material properties as good or better than input material |
Finish: Average roughness | Surface texture after printing: Ra values from 4.5 - 20 μm | The Surface roughness for our process after printing is 28 μm +-5μm |
ElemX 3D Liquid Metal printed docking socket
A new machine's total capital cost depends as much on whether similar systems are in place as it does on the purchase price. Expanding a current facility, especially one with space set aside for the 3D printer, is much less expensive than retrofitting a structure or constructing a new building. Similarly, a new machine's operating cost may involve unanticipated expenditures ranging from protective gear (gloves and glasses) to high-end personal protective equipment, with breathing apparatus to specially stored and carefully used gasses.
Total Cost of Operation
Characteristic | Powder Bed Fusion | Liquid Metal |
3D printer capital cost - Investment cost for printer and auxiliary equipment | $100,000 to greater than $1 million; average of $467,635[1]; additional cost for sintering furnace | Equivalent to mid-range PBF Cost includes printer, chiller, slicer software, build plate removal tool, and initial supplies kit |
Facility capital cost - Investment cost for facility build or retrofit and safety systems | May exceed the cost of the 3D printer based on structure costs and equipment for safe material handling of gasses and reactive Al alloy powders[2] $1 million + | Basic safety measures around heat and the argon gas used in the printhead area Utilizes basic shop infrastructure such as compressed air and 480v power source
|
Production speed - Process time for 125 mm (5 inch) cube | Varies with build size, scanning scheme, laser power and beam size, and the number of lasers; Process time for 125 mm (5 inch) cube: 0. | Varies with part; up to 0.5 pounds per hour max build rate |
Material cost - Purchase price for materials used to 3D print the part, including production and post-processing waste | Material cost includes powder used by the item, support materials, powder loss during cleaning, and build plate used in printing; Metal powders range up to $250/kilogram[4] | Commercial off-the-shelf A356 (Al4008) aluminum alloy; cost includes support materials but no powder removal or build plate; aluminum wire ranges up to $70/kg |
Post-processing cost - Expense for auxiliary activities | Process gas cost, support trimming, build plate must be cut away, sintering | Support trimming; build plate removal without cutting; no sintering |
Just as a new driver does not buy a new car before learning to drive, ensure that you have the in-house skills necessary to implement metal 3D printing. No doubt you have designers and operators who will jump at the chance to participate in an exciting new technology and product offering. However, the learning curve for Powder Bed Fusion is very steep compared to liquid metal 3D printing and must factor into your evaluation. Fortunately, various universities, trade organizations, and technology providers offer training courses for designers and operators.
Skillset
Characteristic | Powder Bed Fusion | Liquid Metal |
Designers - Engineers or CAD specialists who create the digital models to be 3D printed | Requires an understanding of PBF design guidelines, especially the need for external, accessible supports and ensuring powder removal from hollow areas | Requires an understanding of LM design guidelines, especially orientation of the part on its build plate |
Operators - Personnel who run the 3D printer and support staff | Must recognize PBF parameters and the influence of adjustments on the as-built part, including the interaction of the process heat source with the feedstock, and problems associated with inadequate preparation and setup of the build platform, handling and storage of feedstock, and application of the gases[5] | Must recognize LM parameters and the influence of adjustments to the printhead and feed rate on the built part, and handling of raw materials |
Beginning with the end in mind is key to successful 3D printing of aluminum and any other material. Assess your requirements and weigh the relative merits of the different technologies from a quality, total cost of ownership, and skillset perspective before you buy.
Pete Basiliere provides research-based insights on 3D printing and digital-printing hardware, software and materials, best practices, go-to-market strategies and technology trends. Before founding Monadnock Insights, Pete spent eleven years as Gartner’s Research Vice President – Additive Manufacturing. Pete’s full bio can be found here.
[1] Wohlers Report 2020;
[2] "Metal PBF - Is a Bomb Shelter Really Necessary;
[3] Wohlers Report 2020;
[4] Wohlers Report 2020;
[5] European Federation for Welding (EWF) Guideline for European/International Operator Powder Bed Fusion – Laser Beam;
On-Demand Manufacturing. Simpler. Safer. Stronger.
We're leading the way in additive manufacturing innovation using polymer and metal 3D printing technologies to introduce new equipment, materials and tools that enable production of complex parts fast.
Learn more
Related Articles
Awards – Pacesetter, Keypoint Intelligence BLI & More
Xerox products & services have received some of the industry’s top honors including Pacesetter, Keypoint Intelligence – Buyers Lab & other workplace awards.
Learn more
CareAR's real-time visual solution makes support easy
See how CareAR ups the AR ante with Smart Handz solution for remote technical support.
Learn more
What is Additive Manufacturing?
What exactly is 3D printing? It’s the process of printing by adding multiple layers upon each other, rather than printing a single layer of ink.
Learn more
Xerox Named a Sustainability Leader in the Print Industry by Quocirca
Quocirca, a leading source for independent research, thought leadership, and actionable insight for the print industry, has named Xerox a sustainability leader in its Sustainability Trends 2022 report.
Learn more
How Xerox Turned Printer Filters into Face Masks
When the call went out at Xerox to think about new ways to use materials on hand to help the coronavirus humanitarian effort, Mark Adiletta, long-time Xerox engineering manager, had a crazy thought: What if we use printer filters to make medical-grade fac
Learn more
Artificial intelligence for print shops
Look under your digital press’s hood and find out how AI helps you work smarter and grow your business.
Learn more
Explained: What’s going on at Xerox Elem Additive?
In 2019, Xerox made a big statement with its acquisition of Vader Systems, a New York-based start-up bringing to market a Liquid Metal additive manufacturing technology.
Liquid Metal was a development made by Scott and Zachary Vader, a father-son team, which uses wire feedstock to produce parts at ‘quick speed and low cost. ’ Xerox saw it as a technology that could provide solutions to product development and supply chain, while also acknowledging it could harness its expertise in jetting, system design and product design to deliver robust 3D printing equipment to market.
Over three and a half years, Xerox commercialised the technology, hired the likes of Tali Rosman to lead the Elem Additive business unit, and installed the resulting ElemX printer in defence organisations, research labs and service bureaus.
Deployments of the ElemX were being announced at regular intervals, Xerox was still promoting the technology on socials as little as four weeks ago, and then news started to leak that there had been a significant shift in the business operations of Xerox Elem Additive.
Xerox has since confirmed that Elem Additive is being scaled back. But why?
What’s going on at Xerox Elem Additive?Well, less than a few weeks ago.
When Elem Additive General Manager Tali Rosman appeared on the TCT Additive Insight Innovators on Innovators podcast in August, all seemed well with the company. The discussion centred around how 3D printing technologies, like Elem Additive’s Liquid Metal process, could have an impact in industries such as defence. Rosman and her co-participant Mike Pecota touched on the work Xerox had been doing with the US Navy, while Xerox had also announced several additional users in other sectors.
Then, in early October, a flurry of posts on LinkedIn seemed to point to a significant change at the company. Activity on LinkedIn from several Xerox Elem Additive employees suggested the company had made the decision to lay-off a significant number of staff, including the ‘majority of R&D.’ A Xerox spokesperson has since confirmed that, “On September 30 [2022], Xerox scaled back its Elem Additive 3D business and is now solely focused on supporting current installations.”
It comes just six months after Xerox stated in its annual financial report for the year 2021 that ‘we expect 3D to grow revenues rapidly in future years.’ As a publicly listed corporation, Xerox updates its shareholders regularly, with revenue and cash flow on a downward trend. As per its Q2 2022 financial results, revenue is down 2.6% year-over-year, while its operating cash flow is down 299m USD year-over-year to 85m USD, and its free cash flow is down 296m USD year-over-year to 98m USD. Since 2011, the company’s annual revenue has decreased by around 15 billion USD.
Xerox is not alone in making reductions to its workforce in the 3D printing space in recent months. Redundancies have been made at Nexa3D in recent weeks, Desktop Metal announced 12% of staff were to be laid off in June, and it has also been reported manufacturing service Fast Radius is to cut its workforce by up to 20%.
Among those to be let go by Xerox Elem Additive are Rosman, as well as Senior Product Managers, Mechanical Engineers, Senior Metallurgists, Quality Technicians and Supply Chain Analysts.
So, what does that mean for the Elem Additive division at Xerox?As Xerox’s spokesperson says, the focus is now on supporting current installations. These include ElemX machines deployed at the US Naval Postgraduate School, RIT, Siemens, Oak Ridge National Laboratory and Vertex Manufacturing. As per Rosman’s first appearance on the TCT Additive Insight podcast in February 2021, the wider Xerox Corporation is also an occasional user of Liquid Metal technology.
We are now in the process of looking and assessing all of these different businesses across the pipeline. Some of these will get through, and some of them will get rapidly shut down.
The departing R&D staff are also believed to have worked towards the development of IP around Liquid Metal technology, while Xerox had told shareholders in February that an ElemX2.0 was targeted for 'completion' in Q4 2022. This product was said to have the capacity to process Aluminium 6061, which would ‘increase the aperture of the industry verticals we’re going to get into at scale, which is the whole automotive and aeronautical industry.’
With the subsequent ‘scaling back’ of Elem Additive, and with Xerox not having a presence at IMTS or Formnext, it is now not known whether the company still intends to introduce this capability to existing users of Liquid Metal.
Xerox has had its toe in the additive manufacturing water for many years, contributing its printhead technology and capacity for materials and software development. In 2019, however, the company decided to submerge itself fully by acquiring the Vader Systems technology and pulling together various other assets and developments to form a ‘significant business.’
Speaking to TCT in June 2019, Kevin Lewis, Xerox’s Head of Business Strategy for 3D at the time, stressed that the ‘differentiation of the technology’ and that ‘Xerox’s expertise could be put towards helping that technology progress further,’ were among the key reasons for acquiring Vader Systems and its Liquid Metal technology. As noted by Vader Systems co-founder Scott Vader in the same interview, it was also important that the technology ‘supported true manufacturing.’ This element came up in Xerox’s 2019 Investors Day, when the acquisition was announced, as did the fact that Vader had already received ‘strong customer feedback from major manufacturers. ’
At the time, Xerox also stated the Liquid Metal technology would provide a new way for the company to deliver more value to customers.
And why has Xerox decided to scale back its additive activity?A Xerox spokesperson said: “As outlined at our Investor Day event earlier this year, the innovation studio model we have established enables us to quickly determine which businesses we continue moving forward with and which we scale down. This was a difficult, but necessary, decision.”
Xerox presentations at its Investor Day in February threw up many interesting titbits. Naresh K. Shanker, the Senior VP, CTO & Head of Palo Alto Research Center (PARC) at Xerox, spoke with much enthusiasm for additive manufacturing, suggesting the technology could enable distributed and localised manufacturing, as well as production on-demand. He also spoke in detail on the deployment of a Liquid Metal machine on a US Navy aircraft carrier, as well as software developments pertaining to its digital manufacturing endeavours and the aforementioned Aluminium 6061 capability.
“This is really an exciting business,” he said. “We’ve got it off the ground and we’ve got a tremendous amount of launches coming up in the second half of this year. Our goal right now is to double and triple the number of machines this year that we are going to be launching.”
But he also mentioned the ‘venture studio’ established within PARC. This concept, “helps us very quickly accelerate even more businesses across the pipeline. And what we use is a customer-led innovation process. The focus is to test and validate problem, solution, fit and product market fit early in the life cycle, so we can put the capital structures early on.”
He went on: “And this also helps us determine very rapidly what businesses we will move along the pipeline and just as quickly, what businesses we will shut down […] We've talked about Elem and Eloque that we launched, including Novity, and we are now in the process of looking and assessing all of these different businesses across the pipeline. Some of these will get through, and some of them will get rapidly shut down. And what's important is to make sure that we are very efficient around the use of capital in terms of how we progress these entities.”
Somewhere between its 2022 Investor Day and September 30, Xerox has made the decision to significantly scale back the 'exciting business' that was Elem Additive. At this stage, there is no indication that Xerox will make the technology available to new users through other avenues, but Shanker did say back in February: “The second key business benefit that we’ve derived from [the venture studio concept] is that we now have vehicles to actually take these businesses to market in the form of spin-outs, joint ventures and even licensing opportunities with regards to the technology.”
What have former Xerox Elem Additive employees had to say?Those that have sought to update their employment status on LinkedIn have, in the main, expressed their disappointment at the decision and/or their pride at having successfully commercialised the Liquid Metal technology.
Bender Kutub, a Senior Product Manager at Xerox Elem Additive, noted, “it has been an amazing journey with the Elem Additive team, we accomplished a lot in [a] short period of time thanks to a great group of highly skilled and motivated individuals.”
Kevin Scofield, Director of Product Management at Xerox Elem Additive, said: “Xerox has made the unfortunate decision to cease all new development and sales of the Elem Additive product suite. While disappointing, it does not lessen the pride I have in bringing two new software apps (Navigator, Builder) from concept to launch in less that (sic) 18 months.”
Michael Lloyd, 3D Printing Quality Technician at Xerox Elem Additive, offered: “I was with many talented people [at Xerox] and I highly recommend, (sic) that any company pick them up.”
A Xerox spokesperson told TCT: “We are working to minimise the impact to the affected individuals and will provide transition assistance for those impacted.”
Want to discuss? Join the conversation on the Additive Manufacturing Global Community Discord.
Get your FREE print subscription to TCT Magazine.
Metal 3D printing
Metal 3D printing can be considered one of the most enticing and technologically challenging areas of additive manufacturing. Attempts to print with metals have been made since the early days of 3D printing technologies, but in most cases they ran into technological incompatibilities. In this section, we will look at technologies that have been tested for printing both composite materials containing metals and pure metals and alloys.
- 1 3D inkjet printing (3DP)
- 2 Lamination Printing (LOM)
- 3 Layered deposition (FDM/FFF)
- 4 Selective laser sintering (SLS) and direct metal sintering (DMLS)
- 5 Selective laser (SLM) and electron beam melting (EBM)
- 6 Direct laser additive construction (CLAD)
- 7 Free electron beam melting (EBFȝ)
3D inkjet printing (3DP)
How 3D inkjet printers (3DP) work
Inkjet 3D printing is not only one of the oldest additive manufacturing techniques, but also one of the most successful in terms of using metals as consumables . However, it is necessary to immediately clarify that this technology allows you to create only composite models due to the technological features of the process. In fact, this method allows you to create three-dimensional models from any materials that can be processed into powder. The binding of the powder is carried out using polymers. Thus, finished models cannot be called fully "metal".
At the same time, there is the possibility of converting composite models into all-metal ones due to heat treatment in order to melt or burn out the binder material and sinter metal particles. The models obtained in this way do not have high strength due to porosity. An increase in strength is possible due to the impregnation of the resulting all-metal model. For example, it is possible to impregnate a steel model with bronze to obtain a stronger structure.
Models obtained in this way, even with metal impregnation, are not used as mechanical components due to their relatively low strength, but are actively used in the jewelry and souvenir industry.
Lamination printing (LOM)
How 3D printers using lamination technology (LOM) work
models.
Metallic foil can also be used as a consumable.
The resulting models are not all metal, as their integrity is based on the adhesive used to bond the consumable sheets.
The advantage of this technology is the relative cheapness of production and the high visual similarity of the resulting models with all-metal products. Typically, this method is used for layout.
FDM/FFF
Model made with BronzeFill before and after polishing
The most popular 3D printing method has also made use of metals as consumables. Unfortunately, attempts to print with pure metals and alloys have so far not led to significant success. The use of refractory metals runs into quite predictable problems with the choice of materials for the construction of extruders, which, by definition, must withstand even higher temperatures.
Printing with fusible alloys (for example, tin) is possible, but does not give enough high-quality output for practical use.
Thus, in recent years, the attention of consumables developers has switched to composite materials, similar to inkjet printing. A typical example is BronzeFill, a composite material consisting of thermoplastic (details not disclosed, but apparently PLA plastic is used) and bronze powder. The resulting models have a high visual similarity with natural bronze and can even be polished to a high gloss. Unfortunately, the physical and chemical properties of finished products are limited by the parameters of the thermoplastic binder, which does not allow classifying such models as all-metal.
Nevertheless, such materials can be used not only in the creation of models, souvenirs and art objects, but also in industry. Thus, the experiments of enthusiasts have shown the possibility of creating conductors and shielding materials using thermoplastics with a metal filler. The development of this direction can make it possible to print electronic circuit boards.
Selective laser sintering (SLS) and direct metal sintering (DMLS)
The most common method for creating all-metal 3D models involves the use of laser machines for sintering metal powder particles. This technology is referred to as Selective Laser Sintering or SLS. It should be noted that SLS is used not only for working with metals, but also with thermoplastics in powder form. In addition, metallic materials are often coated with more fusible materials to reduce the required power of laser emitters. In such cases, finished metal models require additional sintering in furnaces and impregnation to increase strength.
A variation of the SLS technology is Direct Metal Laser Sintering (DMLS), which, as the name implies, is focused on working with pure metal powders. These plants are often equipped with sealed working chambers filled with an inert gas for working with metals subject to oxidation, such as titanium. In addition, DMLS printers necessarily apply consumable heating to a point just below the melting point, which saves on the power of laser systems and speeds up the printing process.
SLS, DLMS and SLM systems
The laser sintering process begins with the application of a thin layer of heated powder to the work platform. The thickness of the applied layers corresponds to the thickness of one layer of the digital model. Then the particles are sintered between themselves and with the previous layer. Changing the trajectory of the laser beam is carried out using an electromechanical system of mirrors.
When a layer is drawn, the excess material is not removed, but serves as a support for subsequent layers, which allows you to create models of complex shapes, including hinged elements, without the need to build additional support structures. This approach, coupled with high accuracy and resolution, makes it possible to obtain parts that require almost no machining, as well as solid parts of a level of geometric complexity that is unattainable by traditional production methods, including casting.
Laser sintering allows you to work with a wide range of metals, including steel, titanium, nickel alloys, precious materials, etc. The only drawback of the technology can be considered the porosity of the resulting models, which limits the mechanical properties and does not allow achieving strength at the level of cast counterparts.
Selective Laser (SLM) and Electron Beam Melting (EBM)
Despite the high quality of the patterns produced by laser sintering, their practical application is limited by the relatively low strength due to porosity. Such products can be used for rapid prototyping, prototyping, jewelry production and many other tasks, but are of little use for the production of parts that can withstand high loads. One solution to this problem has been the conversion of direct metal laser sintering (DMLS) technology to laser melting additive manufacturing (SLM) technology. In fact, the only fundamental difference between these methods is the degree of heat treatment of the metal powder: SLM technology is based on complete melting to obtain homogeneous models that are practically indistinguishable in physical and mechanical properties from cast counterparts.
An example of a titanium implant made using electron beam melting (EBM) technology
A parallel method that has achieved excellent results is electron beam melting (EBM). At the moment, there is only one manufacturer that creates EBM printers - the Swedish company Arcam.
EBM achieves accuracy and resolution comparable to laser melting, but with some advantages. Thus, the use of electron guns makes it possible to get rid of the delicate electromechanical mirror systems used in laser systems. In addition, the manipulation of electron beams using electromagnetic fields is possible at speeds that are incomparably higher compared to electromechanical systems, which, coupled with an increase in power, makes it possible to achieve increased productivity without significantly complicating the design. Otherwise, the design of SLM and EBM printers is similar to laser metal sintering machines.
Ability to work with a wide range of metals and alloys allows you to create small batches of specialized metal parts that are almost as good as samples obtained using traditional production methods. There is no need to create additional tools and infrastructure, such as molds and furnaces. Accordingly, significant savings are possible in prototyping or small-scale production.
Laser and electron beam melting machines have been successfully used to produce items such as orthopedic titanium prostheses, gas turbine blades and jet engine injectors, among others.
Direct Laser Additive Building (CLAD)
How CLAD plants work
Not so much a 3D printing technology as a "3D repair" technology. The technology is used exclusively at the industrial level due to the complexity and relatively narrow specialization.
CLAD is based on the deposition of metal powder on damaged parts with immediate welding by laser. The positioning of the "print head" is carried out along five axes: in addition to moving in three planes, the head has the ability to change the angle of inclination and rotate around the vertical axis, which allows you to work at any angle.
Such devices are often used to repair large items, including manufacturing defects. For example, the installations of the French company BeAM are used to repair aircraft engines and other complex mechanisms.
Complete CLAD units use a sealed inert atmosphere working chamber for titanium and other oxidizable metals and alloys.
Free electron beam melting (EBFȝ)
How EBF printers work
Technology developed by NASA for use in zero gravity. Since the absence of gravity makes working with metal powders almost impossible, EBFȝ technology involves the use of metal threads.
The build process is similar to Fused Deposition 3D printing (FDM), but using an electron beam gun to fuse the consumable.
This technology will allow the creation of metal spare parts in orbit, which will significantly reduce the cost of delivering parts and provide the ability to quickly respond to emergency situations.
Go to the main page of the Encyclopedia of 3D Printing
How metal 3D printers work. Overview of SLM and DMLS technologies. additive manufacturing. 3D metal printing.
Metal 3D printing. Additive technologies.
SLM or DMLS: what's the difference?
Hello everyone, Friends! 3DTool is with you!
BLT metal 3D printer catalog
Selective laser melting ( SLM ) and direct metal laser sintering ( DMLS ) are two additive manufacturing processes that belong to the family of 3D printing , using the powder layering method. The two technologies have much in common: they both use a laser to selectively melt (or melt) metal powder particles, bonding them together and creating a pattern layer by layer. In addition, the materials used in both processes are metals in granular form.
The differences between SLM and DMLS come down to the basics of the particle bonding process: SLM uses metal powders with a single melting point and completely melts the particles, while in DMLS the powder consists of materials with variable melting points.
Specifically:
SLM produces single metal parts while DMLS produces metal alloy parts.
Both SLM and DMLS technologies are used in industry to create final engineering products. In this article, we will use the term "metal 3D printing" to summarize the 2 technologies. We will also describe the main mechanisms of the manufacturing process that are necessary for engineers to understand the advantages and disadvantages of these technologies.
There are other manufacturing processes for producing dense metal parts, such as electron beam melting (EBM) and ultrasonic additive manufacturing (UAM). Their availability and distribution is rather limited, so they will not be presented in this article.
How metal 3D printing SLM or DMLS works.
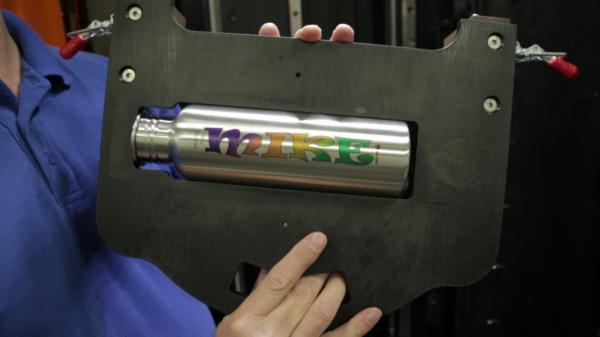
How does metal 3D printing work? The basic manufacturing process for SLM and DMLS is very similar.
1. The printing chamber is first filled with an inert gas (such as argon) to minimize the oxidation of the metal powder. It then heats up to the optimum operating temperature.
2. A layer of powder is spread over the platform, a powerful laser makes passes along a predetermined path in the program, fusing the metal particles together and creating the next layer.
3. When the sintering process is completed, the platform moves down 1 layer. Next, another thin layer of metal powder is applied. The process is repeated until the entire model is printed.
When the printing process is completed, the metal powder already has strong bonds in the structure. Unlike the SLS process, parts are attached to the platform via support structures. The support in metal 3D printing is created from the same material as the base part. This condition is necessary to reduce deformations that may occur due to high processing temperatures.
When the 3D printer's chamber cools down to room temperature, excess powder is removed manually, such as with a brush. The parts are then typically heat treated while they are still attached to the platform. This is done to relieve any residual stresses. They can then be further processed. The removal of the part from the platform occurs by means of sawing.
The scheme of the 3D printer for metal.
In SLM and DMLS, almost all process parameters are set by the manufacturer. The layer height used in metal 3D printing varies from 20 to 50 microns and depends on the properties of the metal powder (fluidity, particle size distribution, shape, etc.).
The basic size of the print area on metal 3D printers is 200 x 150 x 150 mm, but there are also larger sizes of the working area. Printing accuracy is from 50 - 100 microns. As of 2020, metal 3D printers start at $150,000. For example, our company offers 3D metal printers from BLT.
metal 3D printers can be used for small batch production, but the 3D printing capabilities of such systems are more like those of mass production on FDM or SLA machines.
The metal powder in SLM and DMLS is recyclable: typically less than 5% is consumed. After each impression, the unused powder is collected and sieved, and then topped up with fresh material to the level required for the next production.
Waste in metal printing, are supports (support structures, without which it will not be possible to achieve a successful result). With too much support on the manufactured parts, the cost of the entire production will increase accordingly.
Adhesion between coats.
3D metal printing on BLT 3D printers
SLM and DMLS metal parts have almost isotropic mechanical and thermal properties. They are hard and have very little internal porosity (less than 0.2% in 3D printed condition and virtually non-existent after processing).
Metal printed parts have higher strength and hardness and are often more flexible than traditionally made parts. However, such metal becomes “tired” faster.
3D model support structure and part orientation on the work platform.
Support structures are always required when printing with metal, due to the very high processing temperatures. They are usually built using a lattice pattern.
Supports in metal 3D printing perform 3 functions:
• They form the basis for creating the first layer of the part.
• They secure the part to the platform and prevent it from deforming.
• They act as a heat sink, removing heat from the model.
Parts are often oriented at an angle. However, this will increase the amount of support required, the printing time, and ultimately the overall cost.
Deformation can also be minimized with laser sintering templates. This strategy prevents the accumulation of residual stresses in any particular direction and adds a characteristic surface texture to the part.
Since the cost of metal printing is very high, software simulations are often used to predict how a part will behave during processing. These topology optimization algorithms are otherwise used not only to increase mechanical performance and create lightweight parts, but also to minimize the need for supports and the likelihood of part distortion.
Hollow sections and lightweight structures.
An example of printing on a BLT 3D printer
Unlike polymer powder melt processes such as SLS, large hollow sections are not typically used in metal printing as the support would be very difficult to remove, if at all possible.
For internal channels larger than Ø 8 mm, it is recommended to use diamond or teardrop cross-sections instead of round ones, as they do not require support. More detailed recommendations on the design of SLM and DMLS can be found in other articles on this topic.
As an alternative to hollow sections, parts can be made with sheath and cores, which in turn are machined using different laser power and pass speeds, resulting in different material properties. The use of sheath and cores is very useful when making parts with a large solid section, as it greatly reduces printing time and reduces the chance of warping.
The use of a lattice structure is a common strategy in metal 3D printing to reduce part weight. Topology optimization algorithms can also help design organic lightweight shapes.
Consumables for 3D metal printing.
SLM and DMLS technologies can produce parts from a wide range of metals and metal alloys, including aluminum, stainless steel, titanium, cobalt, chromium and inconel. These materials meet the needs of most industrial applications, from aerospace to medical applications. Precious metals such as gold, platinum, palladium and silver can also be processed, but their use is of a minor nature and is mainly limited to jewelry making.
The cost of metal powder is very high. For example, a kilogram of 316 stainless steel powder costs approximately $350-$450. For this reason, minimizing part volume and the need for supports is key to maintaining optimal manufacturing cost.
The main advantage of metal 3D printing is its compatibility with high-strength materials such as nickel or cobalt-chromium superalloys, which are very difficult to machine with traditional methods. Significant cost and time savings can be achieved by using metal 3D printing to create a near-clean shape part. Subsequently, such a part can be processed to a very high surface quality.
Metal post-processing.
Various post methods. treatments are used to improve the mechanical properties, accuracy and appearance of metal printed products.
Mandatory post-processing steps include the removal of loose powder and support structures, while heat treatment (heat annealing) is typically used to relieve residual stresses and improve the mechanical properties of the part.
CNC machining can be used for critical features (such as holes or threads). Sandblasting, plating, polishing, and micro-machining can improve the surface quality and fatigue strength of a metal printed part.
Advantages and disadvantages of metal 3D printing.
Pros:
1. Metal 3D printing can be used to make complex custom parts, with geometries that traditional manufacturing methods cannot provide.
2. Metal 3D printed parts can be optimized to increase their performance with minimal weight.
3. Metal 3D printed parts have excellent physical properties, metal 3D printers can print a wide range of metals and alloys. Includes difficult-to-machine materials and metal superalloys.
Cons:
1. Manufacturing costs associated with metal 3D printing are high. The cost of consumables is from $ 500 per 1 kg.
2. The size of the working area in metal 3D printers is limited.
Conclusions.
• Metal 3D printing is most suitable for complex, one-piece parts that are difficult or very expensive to manufacture using traditional methods, such as CNC.
• Reducing the need for building supports, will significantly reduce the cost of printing with metal.
• 3D printed metal parts have excellent mechanical properties and can be made from a wide range of engineering materials, including superalloys.
And that's all we have! We hope the article was useful to you.
Catalog of 3D printers for metal BLT
You can purchase metal 3d printers, as well as any other 3d printers and CNC machines, by contacting us:
• By email: Sales@3dtool.