Wambam 3d printer
Wham Bam Systems- 3D Printing Innovation
About Wham Bam
Wham Bam 3D Printing Innovations
Wham Bam Systems is dedicated to improving the 3D printing experience through innovation. Our first product line, the Wham Bam Flexible Build System, addresses the need for printers to have a more reliable build surface which is easy to install and makes printing and removing a breeze. We have since released the Slap Mat for resin printing cleanup and the HotBox enclosure for 3D printers.
Wham Bam was created when Peter Solomon, a long time inventor, award-winning designer, maker and 3D printing addict realized that many of his personal modifications to his printers would be very useful to all 3D printers.
Peter has been contributing to the community for years by posting his models to thingiverse, his how-to videos on youtube, and his advice to many forums. He became obsessed with resolving first layer adhesion as this is one of the issues that affects every 3d printer, and then needed to find a way to get prints off the bed easier. When he made his first prototype and shared on social media nearly everyone wanted one, and BOOM - Wham Bam was born!
Wham Bam will continue to make high quality, economic 3D printer products following the same mission: Making 3D printing Easy, Productive and Fun!
Our First Product - Flexible Build System
Print With Confidence
Remove Prints With Ease
Remove Prints With Ease
Print sticks to our PEX build surface and build plate is secured to printer with magnets
Learn More
Remove Prints With Ease
Remove Prints With Ease
Remove Prints With Ease
A flexible, removable build plate allows easy print removal without a chisel or spatula
Learn More
Print More Efficiently
Remove Prints With Ease
Print More Efficiently
Print edge to edge with no binder clips and quickly swap build plates
Learn More
Wham Bam Newsletter
Get exclusive deals, new product insights, plus some helpful tips and tricks . .. just let us know where to send it!
Sign Up
Flexible Build System
What Is The Wham Bam Flexible Build System?
Are you having a difficult time getting your 3D print to stick to your printer bed? Does your print peel up during a long print and destroy your work? Are you tired of temporary fixes such as glue sticks, hair spray, and painter’s tape? Once you get your print to stick, do you have to pry, chisel, cut the perimeter, or put your bed in the freezer, just to get your print off the surface without gouging the surface or cutting yourself?
We have created the specially formulated Wham Bam PEX Polymer Build Surface which surpasses PEI in temperature resistance, performance, and material ‘stickability”. It sticks so well you would have a heck of a time getting the print off the bed without our Wham Bam Flexi Build Plate. Simply remove the Wham Bam Flexi Build Plate from the Wham Bam Flexi Magnetic Base on your 3D printer when the print is finished and flex slightly to pop your print right off! See our demo video below.
Flexible Build System In Action
What the Reviewers are saying:
"Thank You Guys"
"It Just Pops Off"
"It Just Pops Off"
"I honestly stopped using my printer for a while because my prints stuck so well that I'd ruin them or break the glass trying to get them off. The Wham Bam System has got me heavily into 3D printing again. Thank you guys!" - Rob R.
"It Just Pops Off"
"It Just Pops Off"
"It Just Pops Off"
"I’m liking how the prints look. Super smooth on the bottom. And I love that it just pops off. No more spatula. My installation experience went pretty smooth" - Carlos P
See More Reviews
"Class Of Its Own"
"It Just Pops Off"
"Class Of Its Own"
"The fact that the magnets are able to withstand higher temperatures puts this system in a class of its own. Capable of using a wide range of materials that other companies cannot claim without damaging their magnetic sheet permanently." - James P
The fit to your machine is the buyer's responsibility
Please measure your bed (do not rely on build volume) before ordering noting that the spring steel Flexi Plate has two front tabs that stick out by 10mm on smaller kits and 15mm on larger kits. Wham Bam will not be responsible for mistaken sizes ordered. Click here for more sizing info
Sizes and Machine Fits
Shop Now
More sizes being developed now!
Click here to request a new size Flexible Build System.
Quality Materials
Our Wham Bam Flexi Build Plates are made from high quality spring steel that won't kink or warp when you flex them, they just return back to shape! The Spring Steel has been formulated with a Chromium Alloy creating a rust proof steel for long life.
Our magnets and films have all been formulated to resist over 150°C so you can heat your bed to high temps for specialty filaments and not worry about loss of performance.
We have developed the Wham Bam PEX Build Surface from a specially formulated polymer with a higher melt point than even PEI to attract most any filament without damaging the sheet. Prints easily pop off once cooled and flexed.
Wham Bam Newsletter
Get exclusive deals, new product insights, plus some helpful tips and tricks . .. just let us know where to send it!
Sign Up
American and Turkish engineers assembled a metal-to-metal desktop 3D printer
News
creation of a budget 3D printer capable of printing all-metal products. Let's talk about what they did.
Direct 3D printing with metals (without intermediate steps such as growing polymer-metal blanks, and then etching and sintering) can be divided into two areas, referred to in Russian GOST as “synthesis on a substrate” (in the English terminology Powder Bed Fusion or PBF ) and "direct energy and material supply" (Directed Energy Deposition or DED). Synthesis on a substrate involves sintering or fusing metal-powder compositions in containers using laser emitters or electron beam guns. In the direct supply of energy and material, various energy sources can also be used, for example, the same lasers or electron beams, and the materials can be either powders deposited into the sintering or fusion zone or metal wire.
A project by scientists from California State University and Osman Ghazi University of Eskisehir is a variant of the second track called Wire Arc Additive Manufacturing or WAAM. Here, the material is wire, and the products are grown by arc welding, specifically in this case, with a non-consumable electrode in a protective inert atmosphere. WAAM is already being used in industry, for example in the repair and even additive manufacturing of ship parts: in 2017, the Dutch production center RAMLAB produced the first type-certified 3D printed ship propeller ( in the illustrations above and below ).
The resolution of WAAM 3D printers is, to put it mildly, small and requires a lot of post-processing, but they are easily scaled up and do not require fuss with relatively expensive, and often dangerous powders, and at the same time outperform traditional methods in terms of producing geometrically complex products with minimum waste. But you can scale both up and down, and the heroes of our story decided to create such a device not on the basis of an expensive industrial-grade multi-axis robotic arm, but by redesigning a budget desktop FDM 3D printer with the intention of keeping within one thousand dollars.
As a basis, the guys took an open-source "drygost" called Bukobot by the Californian company Deezmaker. The team assembled the device themselves by printing plastic parts on a Stratasys uPrint SE Plus 3D printer, and the power source for the head is an Everlast-branded welding machine. The movable electrode is mounted on one carriage with a mechanism that feeds a metal wire into the melt zone.
Inconel 718 Single Layer Metallography
Experiments were carried out with two types of consumables — AISI 1030 high-carbon steel wire and Inconel 718 heat-resistant nickel-chromium alloy with a diameter of 0.8 mm using tungsten electrodes with a diameter of 2.37 mm and blowing with an inert gas — argon. A series of experiments included experiments on 3D printing at different speeds with the appropriate adjustment of the material feed rate and current strength. For steel, these parameters varied within 2.5-3.5 mm/s with a feed rate of 14-18 mm/s at 45-55A, and with Inconel they tried to print at speeds of 4. 88-5.03 mm/s with a feed rate wire 7.69-10.49 mm/s at 40-50A.
Appearance and section of a 30 layer Inconel 718 specimen
Predictably, the team faced a host of challenges, including mechanical failures, errors in machine code, overheating and even burnout of electrical connections, and electronic and stepper motor failures caused by welder interference.
When working out the parameters, the results varied greatly: when working with the same steel, even at a current of 50A, 3D printing at high speeds produced a series of drops instead of solid lines, so the combination of a paving speed of 3 mm / s with material feed at a speed of 18 mm / s at a current of 55A ( option No. 8 in the illustration above ). With these settings, we managed to get a wall of twenty-five layers in the illustration below.
In general, the experiment was recognized as successful, as the very possibility of WAAM 3D printing with metals on budget, self-assembled equipment with a total cost of around one thousand dollars was proved without significant defects, such as interlayer oxidation or cracking. The team's full report can be found at this link.
Do you have interesting news? Share your developments with us, and we will tell the whole world about them! We are waiting for your ideas at [email protected].
budgetary metal printing WAAM
Follow author
Follow
Don't want
13
選擇語言Bahasa Indonesia (Bahasa Indonesia)Bahasa Malaysia (Malay)Čeština (Czech)Dansk (Danish)Deutsch (German)English (English)Español (Spanish)繁體中文 (Chinese (Traditional))Français (French)한국어 (Korean) Italiano (Italian) 简体中文 (Chinese (Simplified)) ไทย (Thai)Turkçe (Turkish)العربية (Arabic)
Wedج المحاولة مورة خرى للصص اليا# أو الال لـship imesز المς لömpد مuzz المlfuty 9
Omlouváme se, nemůžeme najít stránku, kterou hledate.
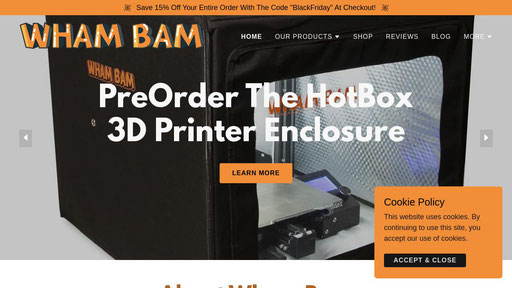
Vi kan desværre ikke finde den side, du leder efter. Gå tilbage til den forrige side, eller besøg Hjælp for at få flere oplysninger
Gå til dit feed
Die gewünschte Seite konnte leider nicht gefunden werden. Versuchen Sie, zur vorherigen Seite zurückzukehren, or besuchen Sie unseren Hilfebereich, um mehr zu erfahren.
Zu Ihrem Feed
Uh oh, we can't seem to find the page you're looking for. Try going back to the previous page or see our Help Center for more information
Go to your feed
Vaya, parece que no podemos encontrar la pagina que buscas. Intenta volver a la página anterior o visita nuestro Centro de ayuda para más información.
Ir a tu feed
Nous ne trouvons pas la page que vous recherchez.
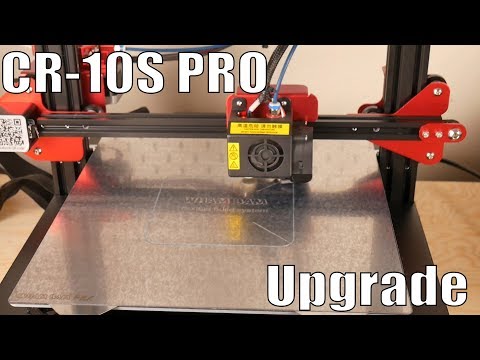
Maaf, sepertinya kami tidak dapat menemukan halaman yang Anda cari. Coba kembali ke halaman sebelumnya atau lihat Pusat Bantuan kami untuk informasi lebih lanjut
Buka feed Anda
Non abbiamo trovato la pagina che stai cercando. Prova a tornare alla pagina precedente o visita il nostro Centro assistenza per saperne di più.
Vai al tuo feed
申し訳 あり ませ ん お 探し の ページ 見つかり ませ ん。 前 の に 戻る か 、 ヘルプセンター 詳細 を ご 確認 ください
원하시는 페이지를 찾을 수 이전 페이지로 돌아가거나 고객센터에서 자세히 알아보세요.
홈으로 가기
Harap maaf, kami tidak dapat menemui laman yang ingin anda cari. Cuba kembali ke laman sebelumnya atau lihat Pusat Bantuan kami untuk maklumat lanjut
Pergi ke suapan
De pagina waar u naar op zoek bent, kan niet worden gevonden.
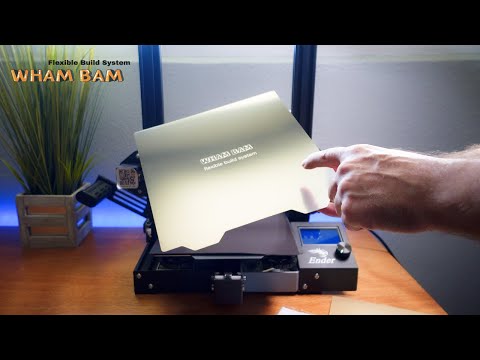
Vi finner ikke siden du leter etter. Gå tilbake til forrige side eller besøk vår brukerstøtte for mer informasjon
Gåtil din feed
Nie możemy znaleźć strony, której szukasz. Spróbuj wrócić do poprzedniej strony lub nasze Centrum pomocy, aby uzyskać więcej informacji
Przejdź do swojego kanalu
A página que você está procurando não foi encontrada. Volte para a página anterior ou visite nossa Central de Ajuda para mais informações
Voltar para seu feed
Ne pare rău, nu găsim pagina pe care o căutatţi. Reveniţi la pagina anterioară sau consultaţi Centrul nostru de asistenţă pentru mai multe informaţii
Accesati fluxul dvs.
The page you are looking for cannot be found.
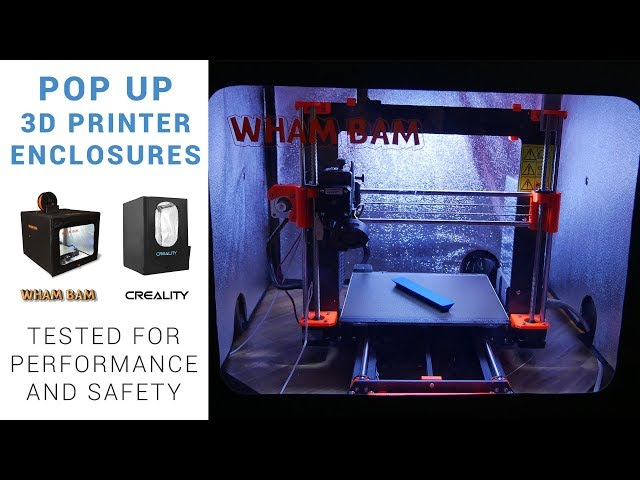