Will 3d printing replace machining
How CNC Machining and 3D Printing Can Work Together in your Shop
Do you ask yourself if CNC machining or 3D printing is the better manufacturing process? The answer is simple: “It depends!”
Many workshops rely on CNC machining as the backbone of their production processes. However, with the rise of additive manufacturing, more and more companies think about including 3D printing into the workflow or even replacing their CNC machines. Let us give you an overview of what 3D printing can do for you, and how you can best combine both processes.
Overview of CNC machining or Subtractive Manufacturing
CNC machining uses a computerized tool machine to produce the desired object by removing the surplus material from a blank. It is still the most cost-effective process for manufacturing parts in medium to large numbers. As a tried and tested method, CNC machines are available in workshops all over the world, and extensive knowledge exists about the whole process chain. It is very versatile in terms of materials that can be machined, geometries that can be produced, and achievable surface qualities and tolerances. Therefore, in many cases, CNC machining is still the method of choice.
However, CNC machining is still a highly specialized process, especially if geometries are of higher complexity or challenging materials are involved. CNC machining also requires highly skilled designers and programmers, leading to high personnel costs. Often special clamping tools are required, which must be designed and manufactured as well. This increases part costs, even more so, if the parts are in small numbers. Also, since you are starting with a block of material when CNCing a part, material cost will always be higher, and the amount of waste will also be more.
Overview of 3D Printing or Additive Manufacturing
Although various methods of 3D printing have proven to be a viable manufacturing process, it still is not as common as conventional machining. But FFF (Fused Filament Fabrication) is becoming more and more popular in various industrial branches to produce small to medium batches of end-use parts or prototypes. Plastic is melted, then extruded through a nozzle, and the part is built up layer by layer. Apart from support structures, only the amount of material making up the final part is used, so almost no waste is produced. The object is printed directly on the flat surface of the print bed, so no clamping tools are required. Only a little specific knowledge is required to set up a BigRep printer and start a print. The printing process itself does not limit the part design in any way; almost any geometry can be printed. This helps in overcoming established ways of thinking in design and development. Riley Gillman, Technical Operations Manager at Nikola Motor Company said, "You can really challenge the engineering process and the manufacturing process!”
Due to the layer-based process, the surface quality is not comparable to milled parts and can require post-processing to a certain extent. And although more and more parts with very narrow tolerances can be printed, values as they are common for milled parts often cannot be matched. The choice of material is also limited; FFF only allows plastics to be used that can be melted.
How to Use Your Big 3D Printer Best?
Hand Jigs and Production Tools
This handheld tool that is used during the assembly of cars shows one typical application. The over 120 cm long part was initially planned to be milled out of a block of aluminum. However, overall costs, including machine, personnel, and material costs would have been around 10.000 € with an estimated time to completion of about two weeks. A Chinese manufacturer quoted 5.800 USD with a similar delivery time. Finally, it was decided to print the part in BigRep HI-TEMP CF on a BigRep PRO, which took 32 hours. The costs were about 790 USD, resulting in savings of 86%! A welcome side effect for the users handling the part was a reduction in weight of about 50%, compared to the aluminum version. All things considered, a very successful use case.
3D Printed End-Use Parts
Boyce Technologies uses 3D printing to produce end-use parts in their 5G kiosks that they make for Verizon. Due to the special shape of these air ducts, milling would have taken a long time and required extensive preparation time and post-processing. By 3D printing the parts instead, huge costs were saved in not only time and material costs, but also with the number of employees required to support preparation and post-processing. With large-format additive manufacturing, another benefit is that many parts can be printed at the same time, allowing for optimal use of the printer’s build volume.
How to Combine 3D Printing and CNC Machining?
The advantages additive manufacturing offers can be increased even more by combining it with other manufacturing processes. 3D printed objects can be reinforced by metal parts in places where higher loads occur; insert nuts made of brass can be inserted in plastic parts. Printed parts can also be machined in order to achieve dimensions with critical tolerances or required surface qualities, or even to mill threads. Jigs and fixtures as well as clamping and positioning tools made by 3D printing facilitate working with CNC machines. By intelligently combining 3D printing and CNC machining, users can benefit from the advantages of both processes.
A perfect example of how the 3D printer is also helpful when designing and manufacturing simple jigs, like positioning or assembly tools, as shown below. In this application, Gillman at Nikola was tasked to find a way to securely hold an aluminum part in place for CMM inspection. The aluminum part itself could not have been produced by 3D printing due to very specific geometrical requirements, so it had to be milled on a CNC machine. But making the fixture from aluminum would have required open space on a CNC machine and a lot of raw material. So, Gillman decided to produce it using his BigRep PRO. From idea to part, it only took a few hours, at material costs of under 20 USD!
In the last few years, Nikola Motor Company has experienced an increased shortage of materials as an ever-decreasing availability of external suppliers. Here a 3D printer offers flexibility and independence.
Riley Gillman summarizes the reasons for using his 3D printer: “Very often, we produce large parts with very challenging time limits. The geometry of the parts plays a large role; some of the parts are simply too complex to manufacture them using conventional methods. And sometimes we simply don’t have the budget to use any other process than 3D printing!”
How Can You Profit from Additive Manufacturing?
3D printing is most commonly used when large parts are required on short notice or when multiple iterations of a single part are needed. 3D printing enables you to make changes to 3D models quickly and easily, and then manufacture them in-house, massively reducing lead times. Functional prototypes are available much faster and you have a better idea of what the final product will look like.
Is it Beneficial for You to Use 3D Printing?
It is important for companies to understand the costs behind a 3D printer and what the ROI will look like. Here is a simple example: If you are paying about 5.000 USD per part with a 3D printing service and you need 4 similar sized parts per month, you will be spending about 20.000 USD a month! When you start comparing this to what it costs to purchase a printer, it becomes apparent that buying a printer is a worthwhile investment.
Which Process is Best Suited for You?
After all these considerations, the answer “It depends!” is easier to understand. The first step should always be, deciding which technology is best for your part and its intended use. Both processes have their advantages and their own applications, so 3D printing will not fully replace CNC machining.
And if you aim to combine both processes so that they complement each other, buying a 3D printer will give you many benefits, including:
- increased flexibility and independence
- time and costs savings
- expanded manufacturing portfolio
- improved internal processes
If this sounds interesting to you, speak to one of our experts! We will show you which one of our 3D printers is best suited for you and your applications. Or send us a CAD file of a sample part, and we will calculate costs and printing time for you.
See How CNC and 3D Printing Work Together at Nikola Motor
Riley Gillman, Technical Operations Manager at Nikola Motor Corporation, shows:
- The Advantages and disadvantages of CNC and 3D Printing
- Integrating 3D printing into your machine shop
- Selecting the right manufacturing process for part
- Cost and time savings for real custom examples
- Understanding ROI
About the author:
Michael Eggerdinger
Product Marketing Manager
Michael is a toolmaker, a mechanical engineer, and a patent engineer. His years of working in manufacturing and as a project manager in various industries provide him with a profound knowledge of the main challenges in modern production processes. In 2017, he bought his first 3D printer to be used at home, and he has been hooked ever since!
Will 3D Printing Replace CNC Machining?
For example, Swedish Automotive Manufacturer, Koenigsegg 3D printed the turbocharger for the world’s first series produced megacar. The One:1 produces one Megawatt of power and is named after its astonishing ratio of hp-to-kg.
Meanwhile, in Aviation and Aerospace, Airbus made history when they began printing aeroplane parts in 2014. Each one of these industries is constantly chasing weight reduction, and Additive Layer Manufacturing (ALM) is the ideal solution in this area.
However, CNC processes still offer some advantages that are worth considering before looking into 3D printing. So, to help you make your decision, here are a few points worth considering:
Accuracy
CNC is well known for its dimensional accuracy.
While metal 3D printing, in particular, can be associated with thermal distortion, cracking and other defects. Thankfully, there are now software technologies to help 3D printing engineers simulate, predict and reverse potential defects in advance. These software improvements have the capability to entirely negate past inaccuracies.
Complexity
Pre-programmed CNC machining can turnaround complex projects speedily.
But, one of the main advantages of 3D printing is its ability to handle almost any complex geometry. This reduces the number of parts that are usually needed in an assembly when using CNC. So, for complex parts that are difficult to manufacture, 3D printing must be considered first.
An added bonus is that there are now software technologies that take advantage of this feature to help designers choose the minimum weight and optimum stiffness through topology analysis before printing.
3D printing technologies differ in terms of the tolerances they can handle. And CNC is generally considered superior. Although, when considering the minimum layer thickness achieved by some 3D printing technologies, this advantage becomes less noticeable.
Environmental Impact
Just how sustainable is 3D printing in comparison to CNC machining?
3D printing generates less waste as material is usually fed and any leftover material can be recycled. This makes it cleaner than CNC which usually involves cutting from a material and creating . However, 3D printing is limited to the build size. So, when it comes to the maximum size of parts 3D printing cannot compete well with CNC.
There is almost no limit to the type of material that can be used in 3D printing such as plastic and metal. There are 3D printing examples of food, chocolate, vitamins and even human tissues. Although CNC can be used for a wide range of materials there are still materials that CNC cannot do, such as certain superalloys.
User-Friendliness
Generally, 3D printing is easier to use as it is automated.
Once the engineer orientates the part, defines slicing & scan path and generates support, if needed. This can all be automated using software technology, so that the printer works unsupervised until it is finished.
CNC usually requires a skilled operator to set-up the speed, cutting path, take manual measurements as well as re-positioning. And the operator must supervise throughout the entire process.
It’s worth noting that both manufacturing processes may require post-processing and therefore this cannot be used for comparison.
Cost
The right process for the right production volume.
This is largely dependent on the volume of printing and related to the speed of delivery. Therefore, for low quantities (preferably in 100’s), 3D printing offer lower cost and it is faster. Other factors require further consideration such as CNC parts repair and replacements. But for large quantities, of 500 and more, other manufacturing should also be considered, such as casting.
Final Thoughts
The choice between 3D printing and CNC is highly dependent on the materials in use, the number of parts, speed of delivery required and geometrical complexity. The case for 3D Printing becoming the primary manufacturing process is largely dependent on the development of improved accuracy, increased build size and accelerated print time.
Steel 3D Printing - A Quick Guide / Sudo Null IT News
Any metal 3D printing technology can print with steel. This is the most popular material. But which steel grades and which technology is best for your application? Will printed steel parts really be as strong and durable as traditionally made parts?
Let's see how a 3D printed steel part is revolutionizing manufacturing and opening doors to new applications in aerospace, medical equipment, automotive, tool making, heavy industry, architecture and more. In addition, more affordable desktop printers are expanding the scope and scope of real steel 3D printed parts.
Strength of steel printed parts.
Cast steel part (left), 3D printed version (center). On the right, a fully 3D printed hinge requires no assembly. (Source: Desktop Metal)The most common question when it comes to a 3D printed metal model is "Will it be as strong as a forged or cast part?" ?". The short answer is yes... and no.
3D printed steel parts can be just as strong, and sometimes even stronger, than those made in the traditional way. It depends on many factors such as: end use, type of steel, choice of 3D printing method, post-processing and shape of the part. Also, the comparison depends on which of the strength characteristics you focus on: tensile strength, static load strength, fatigue strength, etc.
Parts printed from steel are used in the aerospace industry, for the military, and also, for example, for the manufacture of a footbridge, shown below. Therefore, the strength of printed products is beyond doubt, but let's take a closer look.
A 3D printed or laser powder sintered (LPBF) steel part has a finer grain structure than cast metal products. This provides better tensile strength characteristics, but in other respects the cast parts are currently still stronger. Most often, LPBF 3D printing is used to replace cast components, but in some cases, 3D printed components can replace forged parts.
One study showed that, under certain conditions, stainless steel parts made using LPBF 3D printers were three times stronger than parts made from the same steel using the traditional method.
In experiments comparing 3D printed steel parts to traditionally made steel parts, researchers create identical parts using two methods and compare their performance. However, head-to-head comparison of details is only part of the big picture.
The main advantage of printing with steel is not only its strength, but also the unique ability to create internal channels and lattice fillings in parts, which is impossible using traditional manufacturing methods. Metal 3D printing makes it possible to produce parts faster than traditional production, since this method does not require the use of special equipment and tools, it allows you to create assemblies as a whole, eliminating the need for subsequent assembly and welding. Designing a printed part usually means that less metal is needed to make it, and therefore less weight, for the same strength.
MX3D Wire Arc Additive Manufacturing (WAAM) printed steel architectural support (Source: MX3D) Steel 3D printing is also more stable and cost effective as it reduces waste. When using subtractive manufacturing methods, such as CNC machining, you make a part by cutting it out of a large one, with a lot of waste. With additive manufacturing, you only use the material you need to make the finished product.
Steel 3D printing is not intended to replace traditional methods in all areas, but it may be a better choice for a wide range of applications. Particularly when the required parts are unique and designed for specific applications, such as rocket engines, racing cars or the oil and gas industry. 3D printing is the fastest and most flexible technology for mass production and prototype production. For military and industrial applications, steel 3D printing is a faster and more efficient way to create individual parts for vehicles and machines. Stainless steel 3D printing is rapidly finding applications in medicine to create unique surgical instruments and implants.
If you know what characteristics your final product should have (tensile strength, compressive strength, hardness, density, etc.), then all these parameters can be incorporated into the product at the production stage.
Types of steel for 3D printing
Metal powder is the most used metal material for 3D printing (Source: GKN Additive) There are thousands of different grades of steels and alloys with different mechanical properties, used in traditional manufacturing but in 3D printing there are only a few dozen of them, and some of them are unique, created specifically for this technology. Among the steel options, the following can be distinguished:
-
Stainless steel (316L, 304L , 17-4PH, 15-5PH, 420, 254, Ph2, GP1, 630, 410).
-
Tool steel (D2, M2, h23, h21, MS1, 1.2709).
-
Low alloy steel (4140).
-
Structural alloyed (20MnCr5).
Recently, unique alloys have been developed specifically for 3D printing, designed to solve the problems that occur with classical production methods.
For example, 3D printer manufacturer Desktop Metal released a patented stainless steel in 2022 that the company says combines the tensile strength, ductility, and corrosion resistance of 13-8 PH stainless steel, combined with the hardness low alloy steel like 4140. The company says customers can go to market with this material and skip the galvanizing step to protect products from corrosion.
ExOne offers two special blends of steel and bronze that the company says allows 3D printed steel parts to achieve increased corrosion resistance while being easy to machine and polish.
While most of the metal powders used in 3D printing are similar to those used for other manufacturing methods, their numbers are on the rise as more companies adopt the technology. Some metal powder manufacturers, such as GKN, also make custom powders for specific 3D printing applications.
How to print with steel
The strength, properties and applications of 3D printed steel products largely depend on which 3D printing technology you use. Some methods produce stronger parts, other methods provide better hardness or abrasion resistance, and some technologies are simply very fast.
Below are the main metal 3D printing methods, their properties and some of the most common application examples.
Fused Deposition Printing (FDM)
BCN3D's Epsilon printer extrudes metal filament from stainless steel (Source: BCN3D) as more printer manufacturers certify metallic filaments for use on their printers, such as Ultimaker, BCN3D, Makerbot, Raise3D. Raise3D has recently released a complete metal printing suite - Metalfuse (3D printer, debinding oven and sintering oven).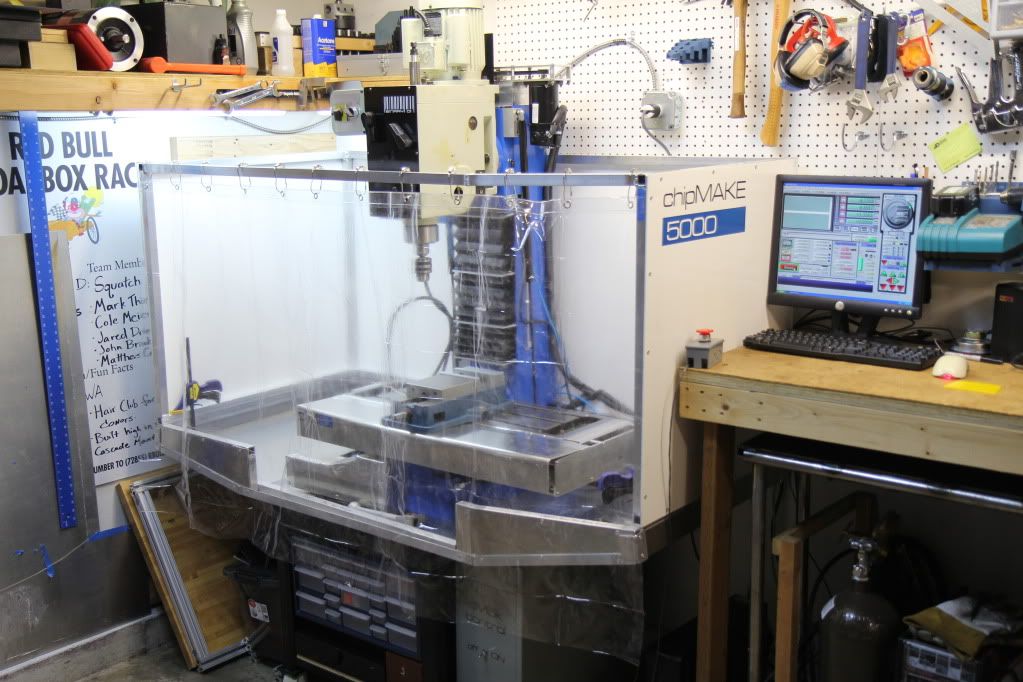
FDM media was once limited to thermoplastics. Companies like BASF Forward AM and The Virtual Foundry now offer metal filaments that can be used on almost any FDM printer as long as it has a hardened steel nozzle for abrasive media.
These materials are approximately 80% metal and 20% plastic. After printing, the post-processing process removes the plastic, resulting in 100% metal parts.
Due to the removal of the bonding plastic, FDM metal parts shrink during post-processing. The amount of shrinkage is constant and can be taken into account in CAD systems, which allows to obtain relatively accurate finished parts.
Forward AM's 316L Stainless Steel Ultrafuse filament produces finished parts with material properties that the company claims are comparable to injection molded metal parts.
(Source: BCN3D) While 3D printing with metallic materials may not be suitable for demanding applications such as aerospace, the economics of producing simple metal components without critical loads on an affordable FDM printer can outweigh the impossibility of applying them in some areas.
Metal prototype parts and finished parts that will not be subjected to extreme stress are ideal uses for this technology.
Bound Metal Deposition (BMD)
Desktop Metal's Studio System 3D printer used bonded metal bars that were extruded layer by layer to form a metal part (Source: Desktop Metal)Similar to FDM, Metal mesh deposition method (BMD) or bonded powder extrusion (BPE) is a 3D printing process based on extrusion. This method uses bonded metal rods or bonded powdered metal filaments, which consist of a much higher percentage of metal powder than the filaments used in FDM. As with FDM, post-treatment to remove the binder and heat treatment in a final sintering oven are required.
There are only a few 3D printers using this method such as Desktop Metal, Markforged and more recently 3DGence, but more companies are entering this market, so stay tuned. These printers are valued as a convenient solution for office 3D metal printing, they are more expensive than most FDM printers, but cheaper than the powder-based metal 3D printing technologies described below.
These printers use their own proprietary filament. Desktop Metal and Markforged offer four types of steel.
Ideal niches for this technology are metal prototype parts, where it is necessary to test the functionality of a part before mass production using traditional methods. Popular applications are molds, punching dies, nozzles, impellers, fasteners and heat exchangers.
For example, Shukla Medical uses Markforged's Metal X printer to print steel prototypes of its orthopedic implant removal instruments.
Laser powder sintering.
Laser powder sintering technology uses one or more lasers to melt powdered metal into a desired shape layer by layer (Source: GE Additive) metal printing. This technology is used by 80% of all metal 3D printers on the market.This method uses powerful lasers to selectively sinter metal powder layer by layer.
LPBF 3D printers are available in a wide range of sizes, prices and laser powers. These and other characteristics affect the properties of the finished part, print speed and other parameters of the finished products.
Steel and steel alloys are the most popular material for LPBF equipment and, unlike FDM and BMD, metal powders are commercially available as they are most commonly used in traditional production methods.
LPBF is a technology that maximizes the quality of a 3D printed part. Applications include aerospace components such as monolithic thrust chambers, rocket engine components and heat exchangers, molds, tools and other applications, as well as high wear parts and surgical instruments.
Binder Jetting
Binder 3D printing technology uses metal powder and a binder to form metal parts (Sorrce: ExOne) binder, and not with a laser. During post-processing, the binder is removed.Binder application stands out for its high printing speed compared to other 3D printing methods or traditional manufacturing, and metal parts made with this technology have material properties equivalent to those made by metal injection molding.
The number of manufacturers producing metal-bonded inkjet 3D printers is much smaller than that of LPBF machines. Leading manufacturers include ExOne, Desktop Metal, Digital Metal, GE Additive and HP.
Binder blasting is ideal for medium to high volume production of metal tools and spare parts.
In fact, HP claims that its Metal Jet 3D printer was designed specifically for mass production of 316L stainless steel products. HP has partnered with Parmatech to produce metal parts for the medical industry. Pennsylvania-based ExOne uses this technology to manufacture hard metal cutting tools and tool steels.
Electron Beam Melting (EBM)
(Source: GE Additive)Electron Beam Melting (EBM) is another powder cladding technology. It works in a similar way to selective laser melting (SLM), but instead of using a laser as the energy source, it uses a much more powerful beam of charged particles.
The recoater moves the powder onto the printing plate and an electron beam selectively melts each layer of powder. After each layer is printed, the plate is lowered and another one is applied on top of the previous layer.
EBM can be much faster than SLM, but SLM produces smoother and more accurate pieces. The electron beam is wider than the laser beam, so EBM cannot produce the same precise parts as SLM. Another difference is that the manufacturing process takes place in a vacuum chamber, which reduces the amount of impurities in the material that can lead to defects. That is why EBM is often chosen for printing components for the aerospace, automotive, defense, petrochemical and medical implant industries.
Titanium is the most popular metal for most EBM applications, however steel can be used.
Cold Spray
(Source: Impact Innovations)Cold spray 3D printing is done by injecting metal powders through a jet nozzle into a supersonic stream of pressurized gases such as air, nitrogen or helium. The process is called "cold" because the metal particles do not melt, but hit the metal substrate and adhere to its surface during the so-called plastic deformation.
Cold spray printed products are not prone to porosity, thermal cracking and other defects associated with melt-based technologies. This method has several advantages over other production methods. The technology is used in the military and aerospace industries around the world. For example, the US Army uses cold spray to repair the mounts of a worn Bradley 25mm steel turret gun.
In the automotive industry, cold spray steel is used for crash repairs because the high strength steel substrates in cars can be susceptible to thermal repair methods such as welding.
Direct Energy Deposition (DED) and Wire Arc Additive Manufacturing (WAAM)
WAAM Steel Parts from MX3D (Source: MX3D) Direct Energy Deposition (DED) uses welding powder or wire that enters through a nozzle and is fed into the power source to melt the metal. A melt region is created and applied to the substrate. DED is a new process, reminiscent of an old building technology known as "cladding", in which a coating is applied to a substrate, often for thermal insulation or weather resistance. DED is useful for fabricating large objects as a whole, as well as complex geometries that require extensive machining. DED can get such parts much closer to finished than traditional CNC machining.
Because DED uses a coating process, it can be used to add complex geometries to existing steel parts, thus combining complexity with cost reduction. For example, the French company AddUp advertises a rocket nozzle that uses a preformed large 304 stainless steel hopper cone printed with an isogrid structure, usually made from a larger piece by traditional methods.
A technology related to DED is wire-arc additive manufacturing (WAAM). Instead of powder, WAAM uses a metal wire that is melted by an electric arc. The process is controlled by robotic arms. WAAM is also capable of producing large-sized metal parts, as demonstrated by the Dutch company MX3D and its nine thousand-pound 41-foot stainless steel bridge in Amsterdam, as well as an oil and gas equipment repair part, proving that parts can be made in the field.
Micro 3D printing
Micro parts printed from steel (Source: 3D MicroPrint) Micro scale additive manufacturing, or micro 3D printing, can produce products with a resolution of a few microns (or less). There are three micro 3D printing methods to produce metal parts.
LMM (lithography-based metal fabrication) is a light-based technology that creates tiny parts from raw materials, including stainless steel, for applications such as surgical instruments and micro-mechanical parts.
Electrochemical deposition is the latest micrometal 3D printing process developed by the Swiss company Exaddon. In this process, the printing nozzle applies liquid with metal ions, creating details at the atomic level.
A third micrometal 3D printing method is microselective laser sintering, in which a layer of metal nanoparticle ink is applied to a substrate, then dried to produce a uniform layer of nanoparticles.
German researchers have successfully tested micro SLS printing of hollow microneedles using 316L stainless steel.
Metal parts from 3D Systems, Desktop Metal, MX3D and Materalise.Steel 3D printing - a quick guide
92 views
Metal 3D printing using pure steel and alloys produces durable functional parts for mechanical and industrial products.
Any metal 3D printing technology can print with steel. This is the most popular material. But which steel grades and which technology is best for your application? Will printed steel parts really be as strong and durable as traditionally made parts?
Let's see how a 3D printed steel part revolutionizes manufacturing and opens the door to new applications in aerospace, medical equipment, automotive, tool making, heavy industry, architecture and more. In addition, more affordable desktop printers are expanding the scope and scope of real steel 3D printed parts.
Strength of steel printed parts.
Cast steel part (left), 3D printed version (center). On the right, a 3D-printed whole hinge requires no assembly (Source: Desktop Metal)
The most common question when it comes to a 3D printed metal model is "Will it be as strong as a forged or cast part?". The short answer is yes... and no.
3D printed steel parts can be just as strong, and sometimes even stronger, than those made in the traditional way. It depends on many factors such as: end use, type of steel, choice of 3D printing method, post-processing and shape of the part. Also, the comparison depends on which of the strength characteristics you focus on: tensile strength, static load strength, fatigue strength, etc.
Parts printed from steel are used in the aerospace industry, for the military, as well as, for example, for the manufacture of a footbridge, shown below. Therefore, the strength of printed products is beyond doubt, but let's take a closer look.
Queen Maxima of the Netherlands officially opens a 3D printed metal bridge. Photo by Adriaande Groot (Source: MX3D)
3D printed or laser powder sintered (LPBF) steel part has a finer grain structure than cast metal products. This provides better tensile strength characteristics, but in other respects the cast parts are currently still stronger. Most often, LPBF 3D printing is used to replace cast components, but in some cases, 3D printed components can replace forged parts.
One study showed that, under certain conditions, stainless steel parts made using LPBF 3D printers were three times stronger than parts made from the same steel using the traditional method.
In an experiment comparing 3D printed steel parts to traditionally made steel parts, researchers create identical parts using two methods and compare their performance. However, head-to-head comparison of details is only part of the big picture.
The main advantage of printing with steel is not only its strength, but also the unique ability to create internal channels and lattice fillings in parts, which is impossible using traditional manufacturing methods. Metal 3D printing makes it possible to produce parts faster than traditional production, since this method does not require the use of special equipment and tools, it allows you to create assemblies as a whole, eliminating the need for subsequent assembly and welding. Designing a printed part usually means that less metal is needed to make it, and therefore less weight, for the same strength.
Architectural support printed in steel using Wire Arc Additive Manufacturing (WAAM) by MX3D (Source: MX3D)
Steel 3D printing is also more stable and cost effective as it reduces waste. When using subtractive manufacturing methods, such as CNC machining, you make a part by cutting it out of a large one, with a lot of waste. With additive manufacturing, you only use the material you need to make the finished product.
Steel 3D printing is not intended to replace traditional methods in all areas, but it may be a better choice for a wide range of applications. Particularly when the required parts are unique and designed for specific applications, such as rocket engines, racing cars or the oil and gas industry. 3D printing is the fastest and most flexible technology for mass production and prototype production. For military and industrial applications, steel 3D printing is a faster and more efficient way to create individual parts for vehicles and machines. Stainless steel 3D printing is rapidly finding applications in medicine to create unique surgical instruments and implants.
If you know what characteristics your final product should have (tensile strength, compressive strength, hardness, density, etc.), then all these parameters can be incorporated into the product at the production stage.
Steel grades for 3D printing
Metal powder is the most used metal material for 3D printing (Source: GKN Additive)
There are thousands of different grades of steels and alloys with different mechanical properties used in traditional production, but in 3D printing there are only a few dozen, and some of them are unique, created specifically for this technology. Among the steel options, the following can be distinguished:
- Stainless steel (316L, 304L , 17-4PH, 15-5PH, 420, 254, Ph2, GP1, 630, 410)
- Tool steel (D2, M2, h23, h21, MS1, 1.
2709)
- Low alloy steel (4140)
- Structural alloyed (20MnCr5)
Recently, unique alloys specially developed for 3D printing have been introduced to solve the problems that occur with classical production methods.
For example, 3D printer manufacturer Desktop Metal released a patented stainless steel in 2022 that the company says combines the tensile strength, ductility, and corrosion resistance of 13-8 PH stainless steel, combined with the hardness low alloy steel like 4140. The company says customers can go to market with this material and skip the galvanizing step to protect products from corrosion.
ExOne offers two special blends of steel and bronze that the company says allows 3D printed steel parts to achieve increased corrosion resistance while being easy to machine and polish.
While most of the metal powders used in 3D printing are similar to those used for other manufacturing methods, their numbers are on the rise as more companies adopt the technology. Some metal powder manufacturers, such as GKN, also make custom powders for specific 3D printing applications.
HOW TO PRINT STEEL
The strength, properties, and applications of 3D printed steel products largely depend on which 3D printing technology you use. Some methods produce stronger parts, other methods provide better hardness or abrasion resistance, and some technologies are simply very fast.
Below are the main metal 3D printing methods, their properties and some of the most common application examples.
Fused Deposition Printing (FDM)
BCN3D's Epsilon printer extrudes stainless steel metal filament (Source: BCN3D)
Fused Deposition Forming (FDM) is a new technology for metal 3D printing, but it is developing rapidly as more printer manufacturers certify metal filaments for use on their printers, such as Ultimaker, BCN3D, Makerbot, Raise3D. Raise3D has recently released a complete metal printing suite - Metalfuse (3D printer, debinding oven and sintering oven). This method is still much more popular for printing plastics, but with new plastic filaments filled with stainless steel powder, strong metal parts can be produced.
FDM media was once limited to thermoplastics. Companies like BASF Forward AM and The Virtual Foundry now offer metal filaments that can be used on almost any FDM printer as long as it has a hardened steel nozzle for abrasive media.
These materials are approximately 80% metal and 20% plastic. After printing, the post-processing process removes the plastic, resulting in 100% metal parts.
Due to the removal of the bonding plastic, FDM metal parts shrink during post-processing. The amount of shrinkage is constant and can be taken into account in CAD systems, which allows to obtain relatively accurate finished parts.
Forward AM's 316L Stainless Steel Ultrafuse filament produces finished parts with material properties that the company claims are comparable to injection molded metal parts.
(Source: BCN3D)
While 3D printing with metallic materials may not be suitable for applications with tough strength requirements (such as aerospace), the economics of producing simple metal components without critical loads on an affordable FDM printer may outweigh the impossibility of using them in some spheres.
Metal prototype parts and finished parts that will not be subjected to extreme stress are ideal uses for this technology.
Bound Metal Deposition (BMD)
Desktop Metal's Studio System 3D printer used wired metal rods that were extruded layer by layer to form a metal part (Source: Desktop Metal)
Similar to FDM, Metal Mesh Method (BMD) or Bonded Powder Extrusion (BPE) is an extrusion-based 3D printing process. This method uses bonded metal rods or bonded powdered metal filaments, which consist of a much higher percentage of metal powder than the filaments used in FDM. As with FDM, post-treatment to remove the binder and heat treatment in a final sintering oven are required.
There are only a few 3D printers using this method such as Desktop Metal, Markforged and more recently 3DGence, but more companies are entering this market, so stay tuned. These printers are valued as a convenient solution for office 3D metal printing, they are more expensive than most FDM printers, but cheaper than the powder-based metal 3D printing technologies described below.
These printers use their own proprietary filament. Desktop Metal and Markforged offer four types of steel.
Ideal niches for this technology are metal prototype parts, where it is necessary to test the functionality of a part before mass production using traditional methods. Popular applications are molds, punching dies, nozzles, impellers, fasteners and heat exchangers.
For example, Shukla Medical uses Markforged's Metal X printer to print steel prototypes of its orthopedic implant removal instruments.
Laser powder sintering.
Powder laser sintering technology uses one or more lasers to melt powdered metal layer by layer into a desired shape (Source: GE Additive)
Laser powder sintering (LPBF), also known as selective laser sintering (SLM), is the most common form of metal 3D printing. This technology is used by 80% of all metal 3D printers on the market.
This method uses powerful lasers to selectively sinter metal powder layer by layer.
LPBF 3D printers come in a wide range of sizes, prices and laser powers. These and other characteristics affect the properties of the finished part, print speed and other parameters of the finished products.
Steel and steel alloys are the most popular material for LPBF equipment and, unlike FDM and BMD, metal powders are commercially available as they are most commonly used in traditional production methods.
LPBF is a technology that maximizes the quality of a 3D printed part. Applications include aerospace components such as monolithic thrust chambers, rocket engine components and heat exchangers, molds, tools and other applications, as well as high wear parts and surgical instruments.
Binder Jetting
Binder 3D printing technology uses metal powder and a binder to form metal parts (Source: ExOne)
Inkjet bonding is another powder printing method in which layers of metal powders are bonded using a liquid binder rather than a laser. During post-processing, the binder is removed.
Binder application stands out for its high printing speed compared to other 3D printing methods or traditional manufacturing, and metal parts made with this technology have material properties equivalent to those made by metal injection molding.
The number of manufacturers producing metal-bonded inkjet 3D printers is much smaller than that of LPBF machines. Leading manufacturers include ExOne, Desktop Metal, Digital Metal, GE Additive and HP.
Binder blasting is ideal for medium to high volume production of metal tools and spare parts.
In fact, HP claims that its Metal Jet 3D printer was designed specifically for mass production of 316L stainless steel products. HP has partnered with Parmatech to produce metal parts for the medical industry. Pennsylvania-based ExOne uses this technology to manufacture hard metal cutting tools and tool steels.
Electron Beam Melting (EBM)
(Source: GE Additive)
Electron beam melting (EBM) is another technology for powder cladding material. It works in a similar way to selective laser melting (SLM), but instead of using a laser as the energy source, it uses a much more powerful beam of charged particles.
The recoater moves the powder onto the printing plate and an electron beam selectively melts each layer of powder. After each layer is printed, the plate is lowered and another one is applied on top of the previous layer.
EBM can be much faster than SLM, but SLM produces smoother and more accurate pieces. The electron beam is wider than the laser beam, so EBM cannot produce the same precise parts as SLM. Another difference is that the manufacturing process takes place in a vacuum chamber, which reduces the amount of impurities in the material that can lead to defects. That is why EBM is often chosen for printing components for the aerospace, automotive, defense, petrochemical and medical implant industries.
Titanium is the most popular metal for most EBM applications, however steel can be used.
Cold Spray
(Source: Impact Innovations)
Cold spray 3D printing technology is carried out by injecting metal powders through a jet nozzle into a supersonic stream of pressurized gases such as air, nitrogen or helium. The process is called "cold" because the metal particles do not melt, but hit the metal substrate and adhere to its surface during the so-called plastic deformation.
Cold spray printed products are not prone to porosity, thermal cracking and other defects associated with melt-based technologies. This method has several advantages over other production methods. The technology is used in the military and aerospace industries around the world. For example, the US Army uses cold spray to repair the mounts of a worn Bradley 25mm steel turret gun.
In the automotive industry, cold spray steel is used for crash repairs because the high strength steel substrates in cars can be susceptible to thermal repair methods such as welding.
Direct Energy Deposition (DED) and Wire Arc Additive Manufacturing (WAAM)
WAAM steel parts from MX3D (Source: MX3D)
Direct energy deposition (DED) uses welding powder or wire that enters through a nozzle and is fed into a power source to melt the metal. A melt region is created and applied to the substrate. DED is a new process, reminiscent of an old building technology known as "cladding", in which a coating is applied to a substrate, often for thermal insulation or weather resistance. DED is useful for fabricating large objects as a whole, as well as complex geometries that require extensive machining. DED can get such parts much closer to finished than traditional CNC machining.
Because DED uses a coating process, it can be used to add complex geometries to existing steel parts, thus combining complexity with cost reduction. For example, the French company AddUp advertises a rocket nozzle that uses a preformed large 304 stainless steel hopper cone printed with an isogrid structure, usually made from a larger piece by traditional methods.
A technology related to DED is wire-arc additive manufacturing (WAAM). Instead of powder, WAAM uses a metal wire that is melted by an electric arc. The process is controlled by robotic arms. WAAM is also capable of producing large-sized metal parts, as demonstrated by the Dutch company MX3D and its nine thousand-pound 41-foot stainless steel bridge in Amsterdam, as well as an oil and gas equipment repair part, proving that parts can be made in the field.
Micro 3D printing
Micro parts printed from steel (Source: 3D MicroPrint)
Micro-scale additive manufacturing, or micro 3D printing, can produce products with a resolution of a few microns (or less). There are three micro 3D printing methods to produce metal parts.
LMM (lithography-based metal fabrication) is a light-based technology that creates tiny parts from raw materials, including stainless steel, for applications such as surgical instruments and micro-mechanical parts.
Electrochemical deposition is the latest micrometal 3D printing process developed by the Swiss company Exaddon. In this process, the printing nozzle applies liquid with metal ions, creating details at the atomic level.