Voxel8 3d printer price
Voxel8: 1st Electronics 3D Printer
0Shares
Just before the holidays, we covered news of a startup that had just received a round of venture capital from Braemer Energy Ventures to develop a very unique product. Details about the product were kept under wraps at that time, but, now, Voxel8 has officially unveiled their multi-material electronics printer, the Voxel8 Developer’s Kit.
News like this coming from another source might seem like pure pipe dream hype. Voxel8, however, is entirely serious and they’ve got the experience and connections to deliver on their electronics printer. The company is headed by none other than Dr. Jennifer Lewis, a Harvard professor with an enormous portfolio of 3D printing, materials, and electronics research. Her work caught the public’s attention when her previous lab at the University of Illinois at Champaign-Urbana 3D printed a microscopic lithium ion battery. At that time, many predicted that the battery foreshadowed a future of complex, multi-material parts with built-in electronics. Only a little over a year has passed and that future is already coming to fruition.
The Voxel8 Developer’s Kit is a low-cost 3D printer capable of 3D printing in two materials: PLA and conductive silver ink, with the PLA stored in the base of the printer and the ink located directly in the printhead itself. Sounds simple, but the Developer’s Kit opens up a huge range of possibilities. With it, the startup has already been able to construct some extremely impressive objects. For instance, at CES, the company will be displaying, alongside their amazing printer, a quadcopter produced almost entirely in one piece from their machine. The PLA and connective circuits of the quadcopter were 3D printed in one go, with the electronics, battery, and motors inserted throughout the printing process. The benefits of such a process are almost endless.
As Voxel8 Business Director, Daniel Oliver, explains, “Effectively, you could build a quadcopter with any geometry you want, stuff it with the components – on the motor- and the board-side – and, basically, have a fully functioning quadcopter without any wiring harnesses. ” He continues, “People will also be able to start creating circuits on their desks. So, if you wanted to test out a circuit design, you could print out a circuit board directly on your desk. You’d have to stuff the components in, as you were doing it, but we’ve shown that you can print out what is basically an Arduino board on our printer.”
Not only does this hint at the possibility of, one day, 3D printing complete electronic items in one process, but, more immediately, the design of electronic devices becomes free from the two-dimensional plane of a PCB board. Instead of allowing electronic parts to dictate design, Oliver explains that designs will now dictate the placement of electronic parts. As users model new objects, they can weave their electronics into the design itself, allowing circuits to traverse curves and climb walls. Engineers will no longer need to find a location to situate their circuit boards, but can place them wherever they see fit.
Talking to Daniel, I wondered what the software would look like for such prints, as I wasn’t sure that Slic3r would be quite up to the task. He told me that Voxel8 was already working with Autodesk to design the software for their product. The “Spark Powered” software, dubbed “Project Wire”, allows users to upload a CAD model and start filling it virtually with electronics and conductive ink.
Users drag and drop electric components – like LEDs, chips, and resistors – into their design and draw connections from one piece to the next within layers of their object. Then, when the machine begins fabricating the item, it pauses for you to place the electronics, and resumes printing. You can see all of this in the promo video below:
As amazing as all of this is, the Voxel8 Developer’s Kit is only the beginning. Spun out of Dr. Lewis’s lab, the company has all of the materials research in its arsenal to usher in a whole new era of 3D printing. Voxel8’s proprietary platform (licensed from Harvard and U of I) is designed to be upgradeable for every new feedstock the company releases in the future. Though Oliver couldn’t mention exactly which materials these would be, the imagination runs wild with the possibilities of Lewis’s research: lithium ion batteries, lightweight composites, stretchable sensors, solar panels, biosensors.
Dan tells me that the device is geared towards engineers and advanced Makers. Though ordinary consumers may not be producing electronics with it, they could be in the near future as the technology is refined and as consumer culture transitions more completely towards prosumerism. The Developer’s Kit is meant to drive a growing desire for functional, multi-material 3D printing. Once people begin designing for the Voxel8 platform, the company will be able to push their technology even further – perhaps, to an industrial scale. In the long term, one can imagine industrial printers capable of printing objects with embedded electronics en masse (Project Ara, anyone?). Leveraging Lewis’s bioprinting research, it’s also possible to see a medical-grade version of their machine used in laboratory settings to 3D print multiple types of cellular materials into a single, biological object. I really believe that there is nothing that she and her team aren’t capable of.
And Autodesk CTO, Jeff Kowalski, seems to agree, saying, “We’re excited to work with companies like Voxel8 because they are really pushing the boundaries of where 3D printing is capable. They’re pushing that front edge, so we can actually start to develop new functionalities using 3D printers – create things that have never been created before – and by incorporating conductive inks directly in the 3D printing process we can start to create things that have functions after they’re created.”
A time in the shape of the Voxel8 logo, 3D printed by the Developer’s Kit.Autodesk isn’t the only impressive partner that Voxel8 has on board. The startup is being advised by John Kawola, the CEO of Harvest Automation Inc. and former CEO of Z Corp – later the VP and GM of Personal and Professional 3D Printers Business Unit at 3D Systems Corp. Voxel8’s Hardware Lead, Michael Bell, has launched two companies around computer software and battery technology, tech that was later transferred to Google and Tesla Motors. Bell holds two patents in battery safety research at Tesla and has two more pending in the field of 3D printing electronics, through his research at Harvard. Alongside Bell and Lewis, the company’s Materials Lead and Software Lead are already members of Lewis’s prestigious lab. And Dan Oliver is a former systems engineer from Honeywell Aerospace turned Harvard MBA grad.
Now, there are a number of Makers and researchers who have explored the 3D printing of electronic devices. For instance, about two years ago, a group of researchers at the University of Warwick developed a conductive 3D printing material called CarboMorph. And some companies have released conductive filament or printheads for 3D printing electronics, such as RabbitProto, which manufacturers a conductive paste 3D printhead. Voxel8, however, is the first company – that I’m aware of – to release a 3D printer specifically devoted to manufacturing multi-material electronic components.
There ink may be more conductive than other similar materials on the market, but Voxel8’s roster and experience is more than enough to convince me that they represent the future of the industry to come. To kick that industry off, you can pre-order the Developer’s Kit for $8,999, which includes the printer, software, materials, support, and training. Pre-ordering also puts you first in line for the printer and gives you premium access to the company’s new materials as they become available.
As you can tell, I’m excited about this thing, but, more than the machine itself, I’m excited to see what people do with it. 3DPI has already covered countless examples of projects that could benefit from 3D printable circuitry: Adafruit’s wearable fitness tracker, the DynePod wearable computer, Disney Research’s printed teddy bear arm, so many quadcopters, bionic prosthetics, just to name a few (too many). In the coming year(s), we can expect to see a whole new slew of Instructables, Adafruit guides, and prototypes for the future of electronics. And, after that? Who knows!
Michael Molitch-Hou
Michael Molitch-Hou previously served as Editor-in-Chief of 3D Printing Industry, he is now the Editor of Engineering . com's 3D printing section. He has covered additive manufacturing technology day in and day out since 2012 and has hundreds of article to his credit. He is the founder of The Reality Institute.
3ders.org - $8,999 Voxel8 Developer's Kit 3D printer now shipping
Jun 1, 2016 | By Benedict
Voxel8, the 3D printing enterprise spearheaded by Harvard professor Jennifer A. Lewis, has started shipping its Developer’s Kit 3D printer, with Google ATAP set to be one of the first recipients. The modular 3D printer is, for a limited time only, still available at the pre-order price of $8,999.
When Voxel8 first announced its Developer’s Kit 3D printer back in 2015, the 3D printing community got pretty excited: here was a desktop FFF 3D printer which could print embedded electronics at room temperature, housed in an ultra-stylish shell, available for under $10K. And on top of all that, the machine had been developed by Prof. Jennifer A. Lewis, a Harvard engineer and one of the most important women in 3D printing.
The Developer’s Kit 3D printer was shown to an enthusiastic crowd at CES 2015, who witnessed the 3D printer making electronic devices by “co-printing” thermoplastics and highly conductive silver ink—a process which allows the printer to embed conductors, wires, and batteries directly into its 3D printed components. Voxel8 then began taking preorders for the 3D printer, prompting swathes of individuals and companies—including Google Advanced Technology and Projects (ATAP)—to enthusiastically sign up for the Voxel8 experience.
Many industry experts have earmarked embedded electronics as important future application of 3D printing, with Israel-based 3D printing company Nano Dimension seemingly leading the way in the emerging field of 3D printed circuit boards. The Voxel8 Developer’s Kit 3D printer, however, offers users something pretty unusual: an affordable, highly usable FFF 3D printer equipped with an auto-leveling build plate, automatic printhead calibration, and the ability to print functional materials.
To make the creation of 3D printed electronic components as simple as possible, Voxel8 teamed up with Autodesk to create a simple yet powerful software package for the Developer’s Kit 3D printer. The Project Wire software tool, which can be run in Google Chrome or Firefox, allows users to simply import existing CAD models, then add electronic components and wires in 3D. Wires can be drawn either through or on top of 3D models, while the software ensures that traces are accurately aligned between layers for optimal conductivity.
Everything about the Voxel8 3D printer has been optimized for creating usable electronic devices. Although some simple components can be created in a single print, the Developer’s Kit printer is also designed to enable easy stop/start printing, enabling external parts to be incorporated into a printed component mid-way through a print. A highly repeatable, kinematic coupling allows users to remove the build plate, insert extra components, then resume printing.
In contrast with its high-tech product, Voxel8 has managed to maintain an almost homely feel to its entire 3D printing enterprise. All Developer’s Kit 3D printers have been assembled at Voxel8’s Somerville, Massachusetts production facility, where each 3D printer will be packed and sent directly to customers. The video below gives a sneak peek into the company’s manufacturing line, where the 3D printer is turned from its constituent parts—many of which were sourced and assembled locally—into its glorious whole.
As the 3D printers begin their shipping journey to customers, many users will soon be reaping the rewards afforded by the versatile machine. A handful of customers, however, have already had a chance to put the printer to use. RightHand Labs, a company which specializes in making robotic grippers, has been using the Developer’s Kit to create a testing system for its robotic fingers, so that the company knows whether each finger is functioning correctly.
Since the manufacturer who produces RightHand Lab’s robotic fingers sends each digit back with loose wires, the startup needed a reliable means of attaching them to a test circuit to make sure they’re working correctly. By using the Voxel8 3D printer, RightHand Labs was able to quickly make an electronics circuit which can electronically and mechanically connect the series of wires to a microcontroller board. An embedded LED then lights up if the test has been successful. “Voxel8’s printing technology has enabled us to rapidly build reliable electro-mechanical test fixtures for our research products,” the company commented.
Customers who pre-ordered the Voxel8 Developer’s Kit 3D printer will receive an email update shortly with an estimated ship date. The machine is, for a limited time still available from $8,999, with Standard, Professional, and Enterprise editions available depending on support requirements.
Voxel8 Developer’s Kit 3D printer technical specs:
- Technology: FFF
- Build volume: 150 x 150 x 100 mm
- Layer resolution: 200 microns
- Filament: 1.
75 mm
- Conductive trace width: 250 microns
- Supported files: STL
- Connectivity: WiFi, ethernet
- Materias: PLA, conductive silver ink
- Resistivity: 5.00 × 10-7 Ω-m
- Cure time: 5 minutes
- Display: 5” color touch screen
Posted in 3D Printer
Maybe you also like:
- EnvisionTEC reveals SLCOM 1 for 3D printing woven fiber composite parts
- 101Hero, world's cheapest 3D printer on Kickstarter for $49
- Josef Prusa unveils $699 Original Prusa i3 MK2 3D printer
- HP begins selling Jet Fusion 3D printer, 'ten times faster, half the cost' of current systems
- High speed, high accuracy Integrator DLP 3D printer by CRAFT3D hits Kickstarter
- Prodways unveils ProMaker P1000, first industrial laser sintering 3D printer at under €100K
- Ricoh’s first branded high-end 3D printer AM S5500P now available in Europe
- Delta force: SeeMeCNC ERIS Delta 3D printer available for $549
- Leapfrog shares sneak preview of forthcoming dual-headed Bolt 3D printer
- Sleek XOCO 3D chocolate printer lets you see your chocolate as it prints
- Custom-made pasta: Italian cuisine giant Barilla unveils 3D pasta printer
Wes wrote at 12/22/2017 5:39:00 PM:
Can you blend various grades of PPSU?
Kittamet Pradiarcheep wrote at 10/20/2017 11:29:32 AM:
To whom it may concern
My name is Kittamet Pradidarcheep. I am a graduate student at Shibaura Institute of Technology. I am writing this to you on behalf of Maeda Laboratory,Department of Mechanical Engineering. Since we are looking for this 3D printer to be installed in laboratory. So I would like to ask you for details about this machine because we have to use this machine to conduct the student research. I would appreciate and thank you in advance. We are looking to hearing from you.
Yours sincerely,
Kittamet Pradidarcheep
Email: [email protected]
dclunie wrote at 6/2/2016 2:01:03 PM:
8k? pass. you can do the same with a rep rap or other multi head extruders for about 1/4 the price or less.
Voxel8 demonstrates a 3D printer for printing electronic circuit boards
3D printing
Just before the New Year holidays, it became known that the start-up company Voxel8 received investments from the well-known venture capital firm Braemer Energy Ventures to develop a product described only as "unique".
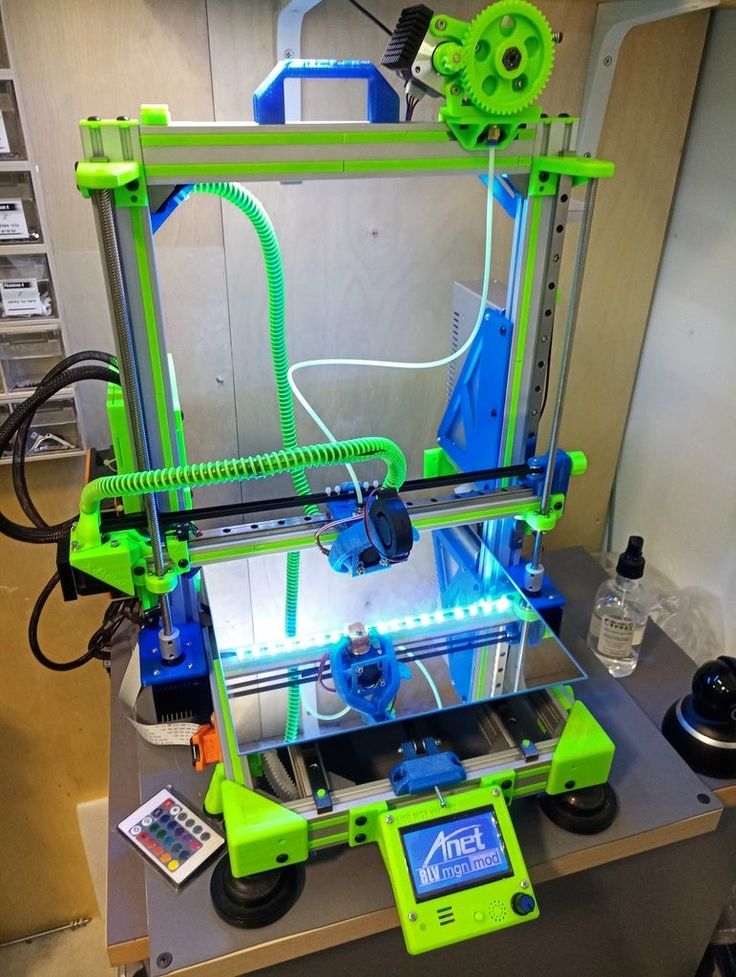
This kind of news sounds like science fiction, but in this case the developers are quite serious, especially considering the team's previous accomplishments. The company is led by Professor Jennifer Lewis of Harvard University and has a portfolio of research on 3D printing technologies, consumables and electronics. She had previously attracted the attention of the general public when a laboratory at the University of Illinois, under her leadership, printed a microscopic lithium-ion battery. At the time, it seemed that the small battery would herald the future of complex printed designs in various materials and with embedded electronic components. A little over a year later, the future knocked on the door of CES 2015.0003
The prototype machine is capable of printing with two materials - PLA plastic and silver-based conductive ink. The PLA is stored in the base of the machine and the ink container is built directly into the print head. It sounds simple enough, but the main thing is the result. The developers have already shown some impressive models printed with the new machine. One of them was a quadcopter, almost entirely printed with Voxel8, and in the form of a single, integral structure. The PLA body and wiring were printed in one piece, and the controller, battery, and motors were prefabricated in stages during the printing process.
Voxel8 Business Development Director Daniel Oliver says: “From a practical point of view, you could build a quadcopter of any shape, insert control blocks and motors, and get a fully functional aircraft without the need for wiring. Now people will be able to print boards directly on the desktop. Yes, electromechanical and complex electronic components will have to be installed separately for now, but at least a board like Arduino can be printed now.
The biggest benefit is the move away from the use of two-dimensional, "sheet" boards. As Oliver explained, where previously the design was dictated by the location of the parts, now the location of the parts will be dictated by the design. As the digital model is created, users will be able to "embed" components into different parts, using new technology to route connections along curves and along walls. There is no need to customize the design for electronic components anymore: you can print the board anywhere and however you like.
Voxel8 is currently working with Autodesk to develop suitable slicing and print control software. A project called "Project Wire" allows you to upload a CAD model and fill it with electronics and conductive ink at will. To do this, you need to place the components (LEDs, chips, resistors, etc.) in the desired places and "draw" the required wiring. When it comes to production, the device will automatically pause printing to allow the user to put the components back in place. Process shown in promo video:
Recall that the device shown is just a prototype. According to Oliver, the developers intend to expand the capabilities of the device, including the range of available materials. The topic of wire printing has long been of interest to the printer community, and some researchers are already building conductive filaments and specialized extruders for use in FDM printing: CarboMorph, RabbitProto, among others. But Voxel8 will be the first project to build a dedicated 3D printed circuit board, and the ink used is much more conductive than composite filaments made from plastic and conductive materials.
Judging by the cost, the first version of the printer will not be affordable for a simple printer. The $8,999 price tag is more suitable for professional engineers and designers. For its part, the company promises that pre-order users will be first in line to receive new materials as they are developed. The Voxel8 developers are already seriously considering bringing their technology to the industry. But this kind of ability would be quite useful to enthusiasts - for example, to print their own modules for phones of the Ara project.
Follow author
Follow
Don't want
7
More interesting articles
brtv
Loading
10/16/2022
339
5
Subscribe to the author
Subscribe
Don't want
Hello my friend! Today I decided to assemble a simple pneumohydraulic generator or Generator...
Read more
Leoluch
Loading
09/07/2015
352074
343
Subscribe to the author
Subscribe
Don't want
Good afternoon, dear visitors of the portal.
Today I decided not to leave in art...
Read more
302
Follow author
Follow
Don't want
Hello dear community!
If the experiment was successful, then something is wrong here...
Read more
News in the development of 3D printing technology|Kubikus.by 3D-studio in Minsk
100% printed compact jet engine
It's one thing to 3D print something very high-tech (like a rocket engine), but it's quite another to 3D print something with fuel and press the start button. But that's exactly what GE Aviation did recently when they tested a simple, compact a jet engine made entirely of 3D printed parts.
The engine was created by GE Aviation's Additive Development Center as part of a side project. The main goal of the project was to test technologies of layer-by-layer additive build-up, when one or another part is created by applying a metal powder, the layers of which are connected using a laser.
GE Aviation notes that the simplicity of the design of this engine was chosen for a reason. This is because at the present time the construction of commercial engines is such a complex process that it is almost akin to technological art.
3D printed engine based on a real compact engine, which is used in radio controlled models. The resulting sample makes 33,000 revolutions per minute.
"Additive printing really does have a number of advantages over traditional methods," says GE Aviation spokesman Matt Benvey.
“First, it's faster. You do not need to use many different and complex tools - everything is done on one machine from the 3D model that is on your computer. Secondly, with the help of this technology, it is possible to obtain geometries that could not be obtained by creating a part in the usual ways. ”
The world's most advanced 3D printed prosthetic hand has been created great attention. And today we are going to talk about the most advanced development in this direction.
True, the entry into the available market of this project is still seen only in the future, however, this rule is true, perhaps, for everything that is new, what is produced by man. After all, as long as a project seems viable, there is always room for improvement.
What we are going to talk about today is not just another 3D printed mechanical prosthetic hand. Largely they are really impressive, but they have limited features (which, in turn, are a key factor in determining their price).
Open Bionics has 3D printed an amazing prosthetic arm, which is currently being tested by Daniel Melville in a pilot program. launched in turn within the latest international exhibition of electronics Consumer Electronics Show 2015, held in January of this year. Melville was allowed to use the prosthesis for five days and perform various tasks with it, testing its capabilities. One of the features of the new prosthesis is the ability to greet with a handshake, "high five" and carefully take small objects. By the way, to his own joy and the joy of his loved ones, Daniel almost immediately got used to the prosthesis and constantly walked and shook hands with everyone he met.
The new prosthesis is so cool that its creator, 24-year-old Joel Gibbard (the same age as Daniel himself), won the Best Product Innovation at the exhibition, where the judges unanimously called the prosthesis "the world's most high-tech prosthetic arm".
Before creating the prosthesis, Daniel's right hand was scanned first. This process took only 20 minutes. Scanning was necessary in order to create the most suitable 3D-framework, prosthesis installation sites. The required frame was 3D printed in 40 minutes. The complete creation of the prosthesis took only 40 hours instead of several weeks, which are usually required to create conventional prostheses. After printing, various robotic parts were installed on the prosthesis and connected electromagnetic sensors of the prosthesis with the muscle and nerve endings of Daniel's arm.
While Daniel enjoys having a second functional arm (before that, he had to wear a regular cosmetic prosthesis, which is not even a quarter of what a new prosthesis can), Joel Gibbart is already looking for ways to improve his invention by making the prosthesis stronger, lighter and getting rid of the external wires that are present on the first prototype.
“The new prosthetic hand I designed weighs half the size of the current prototype. This will make it much more convenient to use,” says Joel.
“I'm not going to stop until I've done something really perfect in that regard. The new prosthesis will definitely be lighter, cheaper and more creative. And he will really be able to offer his owner full freedom of action.
The world's first 3D printer for printing electronic devices goes on sale
The Voxel8 team at Harvard has created a 3D printer that prints fully functioning electromechanical devices. The device uses special software software that allows you to create objects with working diagrams and space for embedded electronic components. The Voxel8 printer is the first of its kind and marks a major advance in 3D printing.
The Voxel8 engineering team showcased their achievements at CES-2015 in Las Vegas. The capabilities of a 3D printer with two print heads were shown on the example of a whole fleet of functioning quadrocopters.
The principle of operation of the new device does not differ from most other 3D printers, with the exception of some points. Its extruder uses conductive ink, allowing it to print working circuits and embed the missing electronic components in the craft. The conductive silver paste was specially developed in the laboratory of Harvard University.
Printer software developed in partnership with Autodesk, the world's largest software vendor for architects, engineers, designers. This partnership brought Voxel8's grand vision to life.
Perhaps the most interesting thing about this printer is that when it prints, it leaves room for electronic components. Once you put the right components on the board, it will connect them with a conductive pattern.