Ucf 3d printing lab
Manufacturing Lab - UCF College of Engineering and Computer Science
Days/Hours: Tuesday, Wednesday, and Thursday, 8 a.m. – 5 p.m.
Upon entering the Manufacturing Lab, please sign in on the clipboard and speak with the lab manager, Clarence Bess, before using the lab equipment to further discuss and develop your project. Don’t forget to sign out when leaving.
The Manufacturing Lab is also home to Limbitless Solutions.
Services
- 3D Printer (located in office) Please send over designs in a STL file. See below for information on how to make a request to use the printer.
- 3 Manual Milling Machines with digital read outs.
- Hurco
- Tri Onics
- Sharp
- Small Computer Numerical Control Milling Machine (Can be programmed to cut to cut aluminum, steel, copper, brass, wood, plastic. Does not cut concrete.)
- Haas VF-2, Milling Machining Center (holds 20 different tools and changes cutters/drills)
- Fadal Machining Center (folds 20 different tools and changes cutters/drills)
- Haas ST-10 Lathe
- Time Master Manual Lathe with digital readout and 5-foot bed.
- MasterCam Lab
- Run a program here before we go to the machine to see how it works. Includes simulator.
- Small supply of stock including wood, aluminum, steel, acrylic and copper.
- WellSaw Horizontal band saw
- DoAll Horizontal band saw
- DeWault cut-off saw (for cutting materials that are heat treated)
- Vertical cut-off saw
- 12-inch Compound Miter Saw (usually for cutting wood)
- Small Lathe, Jet Lathe with a 3-foot bed
- Hardware (screws, nuts, bolts)
- Basic tools
General Rules and Procedures
- Food and drinks are not allowed in the Manufacturing Lab.
- Please sign in and speak with Clarence Bess, lab manager, before entering the lab and working.
- No loose-fitted clothing or jewelry is permitted in the lab.
- Close-toed shoes only.
- Cell phones are permitted in the workspace.
- Clean up after yourself.
- To request a work order and receive a quote for a project, visit machinelab.
cecs.ucf.edu and click on request a quote > e2-113-mlserver > orders > add new item. Please allow up to 72 hours for a response.
- Don’t forget to attach your design (preferably in Solidworks) for machining. If the job is to be made on the 3D Printer, save your design as STL Files and then attach.
- Capacity: If no machines running – 20 people. If machines are in use – five people per one instructor. Eye protection needed.
Cost
- Any work completed by the lab manager is $40 an hour. Please see the General Rules and Procedures section, above, for more information on requesting a quote.
- The first half hour of work is free, but you must be present to watch and learn from the lab manager.
- For 3D Printer, the cost is $7/cubic inch for print jobs.
Contact: Clarence Bess, lab manager
[email protected]
(407) 823-1604
Please contact Clarence Bess to schedule tours and events.
-
FOX 35 Nov, 16, 2022
UCF researchers could develop the cure for hydrogen leak that grounded Artemis 1Assoc. Prof. Jan Gou featured
-
Orlando Sentinel Oct. 8, 2022
What Florida learned from Hurricane IanProf. Thomas Wahl featured
-
Science Magazine Sept. 22, 2022
AI-based screening method could boost speed of new drug discoveryAsst. Prof. Ozlem Garibay featured
-
News 6 WKMG Aug. 7, 2022
In this Florida city, when drivers go the wrong way, most don’t crash. Here’s why.Prof. Haitham al-Deek featured
-
Phys.org July 14, 2022
High-tide floods surge as climate changes and sea level risesAssoc. Prof. Thomas Wahl featured
- Read More
View Calendar
Army lab, UCF optimize 3D printing process | Article
ABERDEEN PROVING GROUND, Md. - Army researchers collaborated with academic partners from the University of Central Florida to improve additive manufacturing. This partnership may help deliver extreme lightweight components to future Soldiers.
By optimizing the printing process for the additive manufacturing of a high-strength magnesium alloy and fabricating 24 micro-lattice structures, researchers characterized the compressive strength and failure modes, which will enable much lighter Army components.
“We used a magnesium alloy known as WE43, which has only been successfully 3D printed by a handful of researchers,” said Dr. Brandon McWilliams, the lead researcher for 3D printing metals at the U.S. Army Combat Capabilities Development Command, known as DEVCOM, Army Research Laboratory. “In this work, we optimized the process to achieve higher density than previously reported and used that to produce and characterize lattice structures made up of WE43.”
Magnesium Elektron WE43 is a high strength casting alloy. It can be used in temperatures of up to 300°C (572°F), according to AZoM, an online publication for the materials science community. “This alloy has good mechanical properties coupled with excellent corrosion resistance.”
Advanced additive manufacturing has the potential to deliver critical parts at the point of need, reducing the need for lengthy logistic chains. Also, the U.S. Army’s modernization strategy calls for lightening the load to help support future Soldiers.
The research team published their findings in the peer-reviewed journal Materialia.
McWilliams said he believes joining advanced lightweight alloys with novel multi-scale structures through additive manufacturing will be a key aspect of modernizing Army weapon systems. There are many lightweight structural applications in the automotive, aerospace and biomedical industries.
“Current systems are too heavy, which increases burden to the Soldier, reduces fuel efficiency and degrades mission effectiveness,” he said. “It is my goal as an Army researcher to conduct research, which has the maximum chance of success of transition from basic and applied research stage to practical application in order to enable transformational overmatch.”
Partnering with academia and industry has been a priority with the laboratory since it introduced its Open Campus initiative.
“This was an exciting and rewarding collaboration that produced the technological accomplishment founded on fundamental understanding of materials and additive manufacturing,” said Prof. Yongho Sohn, lead researcher at University of Central Florida. “Technological vision with clear scientific objectives defined by Dr. McWilliams and his team was the key to our contribution.”
Army researchers will now evaluate the high strain rate and ballistic properties of these 3D-printed materials and look for demonstration applications, such as ultra-lightweight unmanned aircraft system and robotic vehicle components, he said.
Visit the laboratory's Media Center to discover more Army science and technology storiesDEVCOM Army Research Laboratory is an element of the U. S. Army Combat Capabilities Development Command. As the Army’s corporate research laboratory, ARL is operationalizing science to achieve transformational overmatch. Through collaboration across the command’s core technical competencies, DEVCOM leads in the discovery, development and delivery of the technology-based capabilities required to make Soldiers more successful at winning the nation’s wars and come home safely. DEVCOM is a major subordinate command of the Army Futures Command.
3D printing laboratory - All about plastics - education, technology, perspectives
Prototyping and modeling using 3D printers has recently become more and more widespread. This is due not only to the development and cheapening of equipment for creating three-dimensional models, the emergence of new polymeric materials for three-dimensional printing, but also the emergence of the need for such modeling for medical products, aircraft parts, instrumentation, automotive and aircraft manufacturing, as well as souvenirs. and other areas. The use of polymeric materials for structural purposes for prototyping made it possible to produce not only models, but also small batches of technical products. nine0003
According to the recent study “3D Printing Market (2013-2020)” published by Markets and Markets (“M&M”), between 2013 and 2020, the annual growth of the 3D printing market will be 23%, resulting in will grow to 8.4 billion US dollars by 2020 (http://www.orgprint.com/wiki/3d-pechat/obzor-tehnologij-3D-pechati).
3D printing is a technology for creating three-dimensional objects from a digital sample (CAD) by layer-by-layer application of additive materials. 3D printing methods include stereolithography (SLA), powder laser sintering (SLS), electron beam melting (EBM), layer-by-layer printing with molten polymer thread (FDM), formation of three-dimensional models from layer-by-layer sheet material (LOM) and others. nine0003
Initially, 3D printing was used exclusively for prototyping objects, but recently a radical step has been taken towards production. Automotive, aerospace, medical, and consumer products are among the industries that are actively embracing 3D printing. According to M&M, 3D printing in medicine and aerospace will grow exponentially in the near future. 3D printing has significant growth potential, it is indispensable where piece production of personalized products is needed. nine0003
This article touches upon some aspects of 3D printing, which is carried out by layer-by-layer printing with a melted polymer thread (rod).
Layer-by-layer printing with a molten polymer thread , also known as Fused Deposition Modeling or simply FDM, is used to obtain single products that are close in their functional characteristics to serial products, as well as for the manufacture of investment molds for casting metals.
The main polymer materials used in FDM technology in Russia are ABS plastic, PLA (polylactide), to a lesser extent polyamide (PA-12 or PA-11), TPU, PET-G and a number of other polymers. Almost all polymeric materials are imported. nine0003
High impact polystyrene (HIPS) is used as support polymers. This material is used for printing ABS plastic, PMMA, PET-G. Polyvinyl alcohol PVA (PVOH, PVA or PVAL) is also used as a support polymer, however, due to the water solubility of this polymer, it is more difficult to obtain a thread from it, modification of the standard technology is required.
At the Interplastica-2018 exhibition, work was announced on the synthesis of special grades of structural polymer materials for 3D printers at the Kabardino-Balkarian State University (PSU, PFS, etc.). In the report of KNRTU (Kazan), the topic of using PP filament for 3D printing was mentioned, which is not surprising, since in the Republic of Tatarstan a wide range of PP grades is produced by Nizhnekamskneftekhim PJSC. The problem with polyolefins in printing is associated with poor adhesion to the 3D printer substrate and high shrinkage when cooled. nine0003
FDM printing technology is as follows: a polymer thread is fed into a heated head with a controlled temperature, in the head it is heated to a melt state and the resulting thermoplastic modeling material is fed with high precision in thin layers onto the working surface of a 3D printer. The layers are applied on top of each other, joined together and cooled, gradually forming the finished product.
The diameter of the nozzle through which a thread with a diameter of 3 or more often 1.75 mm is fed is 0.3-0.4 mm in the first case, and 0.1-0.3 mm in the second case. Therefore, the requirements for a polymer thread should be quite stringent in terms of sizing (thickness variation), stability of rheological properties (melt flow), melt purity (presence of impurities or contaminants). nine0003
1 shows the scheme of printing polymer thread FDM
1. Flow chart of 3D printing by FDM polymer filament printing.
The production of thread (rod) for FDM technology is carried out on extrusion plants for extruding rod, including a dryer, an extruder, usually a single-strand extrusion head, a calibrator (if necessary), a cooling bath, a gauge for the thickness (diameter) of the thread, 2 (rarely 4 -x positional) bar winder on the coil. There is a lot of information on the Internet about homemade filament extruders, as a rule, of low productivity and low quality filament. However, the production of thread must be carried out on specialized extrusion lines. nine0003
A diagram of such a line is shown in fig. 2.
Fig. 2. Extrusion plant for the production of polymer thread
I would like to note that for the wide development of FDM technology in our country, it is necessary to clearly define the characteristics of polymer materials that determine the possibility of their use in 3D printing technology with a polymer thread, as well as to synthesize or modify industrial polymers in order to obtaining material with the required characteristics. In particular, both thermophysical properties (for example, the thermal diffusivity coefficient, which determines the cooling rate of the material), and rheological properties (fluidity at different temperatures), as well as temperature parameters of the weldability of layers depending on the properties of the feedstock, etc., should be taken into account. nine0003
3D printing in chemistry - Ananikov Laboratory AnanikovLab.
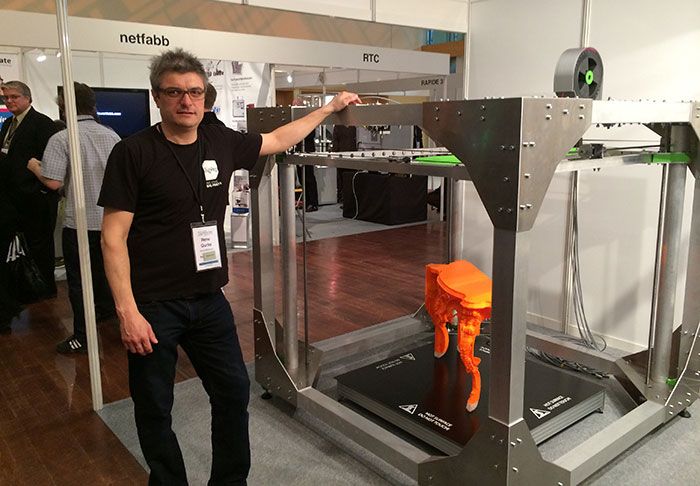
The cheapest, simplest, and most common 3D printing method is Fused Deposition Modeling (FDM). In the vast majority of cases, this method uses the direction of the polymer: the polymer in the form of a thread with a diameter of about 2 mm, wound on a spool, is fed into a small extruder, where it melts and is extruded (pressed) through the nozzle already in the form of a thin thread, from which the layers of the future part are formed. . The nozzle opening diameter and layer thickness together determine the resolution of an FDM printer. The design of such a 3D printer is relatively simple, so these devices are produced by many companies and their cost is low compared to 3D printers designed for printing by other additive methods. A significant advantage of FDM technology is the low cost of consumables, which are various polymers: acrylonitrile butadiene styrene (ABS), biodegradable polylactide (PLA), polyethylene terephthalate (PET), polypropylene (PP), nylon, polycarbonate, etc. nine0003
The process of 3D printing of chemical equipment elements from chemically resistant plastic using an FDM 3D printer.
The polymer filament deposition method has an average spatial resolution (usually 0.1 - 0.2 mm) and makes it possible to manufacture parts of various shapes and levels of complexity (Fig. 1). The enormous possibilities of 3D printing make it a very promising technology in education and science. Piece-by-piece production of unique laboratory equipment, visual aids (Fig. 2), mock-ups, models (including working mechanisms with moving parts) - all this is feasible even with the widely available FDM printing method. nine0003
Fig. 1. Attached spiral channel made from two different resins in a single 3D print run with two extruders running in sync. Finished products and a 3D model are shown.
Fig. 2. Ball-and-stick model of a molecule made by FDM printing from PLA plastic. To obtain a higher quality, the model was made in parts with subsequent assembly.
The high chemical resistance of some polymers (such as polypropylene, nylon, polyethylene terephthalate) in combination with the FDM printing method is well suited for the manufacture of small chemical laboratory equipment and chemical-technological laboratory installations. However, the real potential of 3D printing is not realized in the manufacture of standard laboratory equipment that can be bought, but in the creation of special products, such as chemical reactors, mixers and other elements of chemical installations, developed in-house for unique experiments. nine0003
The layering technology is mature enough to reproduce even the fine details of small chemical equipment. For example, Figure 3 shows a photograph of a mixer with three inlets and one outlet. The diameter of the internal channels of this mixer is only 2 mm. The conical notches on the inlet pipes are clearly visible, and the height of these notches is 0.5 mm. To increase the mixing efficiency, a miniature helical fin is made inside the central outlet channel. Of course, this is not yet the same thing as shoeing a flea, but everything is moving towards this. The manufacturing time of the mixer was 30 minutes. Try to make such a micro-mixer in half an hour using conventional methods! nine0003
Fig. 3. Mixer-tee in the working chamber of a 3D printer, made of polyethylene terephthalate using the FDM method.
Fig. 4. Chemical microreactor with a complex labyrinth channel inside, made of PET by FDM printing. The individual parts of the reactor and the assembly are shown.
The ability to manufacture products with a complex internal structure, as already noted, is one of the main advantages of 3D printing. This possibility is well illustrated in Figure 4, which shows a complete chemical reactor the size of a matchbox. Like the "adult" chemical reactor, this "baby" has a shell, a lid connected by bolts to the shell, and a gasket to seal the working space. It is enough to look under the lid to see the complexity of the inner world of this worker of science: a labyrinth channel is organized inside the reactor, forcing the reaction mixture entering the shell through the side pipe to move along a complex trajectory, so that the reaction time is optimal to obtain the desired products. There are small baffles at the bottom of the labyrinth channel to keep the finely dispersed catalyst from being washed out quickly. The reaction products leave the reactor through the lower branch pipe. nine0003
Microreactors can consist of any number of elements, each of which is individually manufactured using 3D printing (Fig. 5). Individual elements (Fig. 6) are eventually combined into workable chemical plants (Fig. 7).
Fig. 5. Microreactor, consisting of a shell, a lid, a catalytic cartridge and a replaceable nozzle. The individual parts of the reactor, the reactor assembly and a three-dimensional model of the assembly are shown.
nine0003
Fig. 6. Mixer and zigzag microreactor made of PET.
Fig. 7. Laboratory chemical plant assembled from a microreactor and mixer, created by FDM printing methods.
3D printing can significantly speed up experimental chemical research, because it makes it possible to manufacture even complex multi-component chemical equipment right in the laboratory without significant material costs.