Thermally conductive plastic 3d printing
Thermally Conductive Polymer Materials for 3D Printing
Over the last few weeks we have been taking a look at various polymers with added engineering functionality.
So far we have looked at those with altered electrical properties such as electrically conductive materials and ESD-safe materials. These materials had various levels of surface-resistivity allowing charge to flow through the material at different rates.
Analogous to electrically conductive materials in the thermodynamic domain are thermally conductive materials. These are materials that allow the conduction of heat through their body.
What’s the point of that? To transport heat from one place to another. A heat sink is a great example of this principle.
Heat sink printed with TCPoly Ice9 filament. Image credit: TCPolyExtruded Materials
Starting with the extruded materials, there are a few options available. One company in particular stands out, as they claim to have a material that is 50 times more thermally conductive than standard filaments.
TCPoly has what they claim to be the most thermally conductive filament on the planet.
The material is named Ice9 (because it’s useful for cooling stuff) and is a thermoplastic filament with 8 W/m-K of thermal conductivity off-the-shelf.
However, if you actually print something with it, that can increase up to 15 W/m-K. Why does it change?
Because thermal conductivity = K = (QL)/(AΔT)
Where,
- – K is the thermal conductivity in W/m.K
- – Q is the amount of heat transferred through the material in Joules/second or Watts
- – L is the distance between the two isothermal planes
- – A is the area of the surface in square meters
- – ΔT is the difference in temperature in Kelvin
As you can see there are a couple of variables in there related to the geometry of the part (L & A), and altering them directly affects the value of K.
To give you an illustration of how thermally conductive their materials are, they are as thermally conductive as stainless steel but at half the density of aluminium. Cool!
Further searches in this area may lead you to a company named Tiamet3D, who have a filament named Ultra Diamond PLA that is, according to their own website, a PLA-based filament laced with industrial nanodiamonds.
Their product blurb claims that Ultra Diamond PLA has “high thermal transfer: 3x-5x more than standard PLA”.
PLA has a thermal conductivity of about 0.13 W/(m*K). Normal ABS 0.25. Steel has between 10 and 50 W/(m*K), depending on the alloy and other factors.
Sintered Materials
Like the electrically modified materials from the last articles, AM powders do not suffer from the issue of settling / floating due to different densities as the individual powder particles tend to be coated, allowing uniform distribution of the powders in the powder chamber.
Interestingly, due to the geometric and dimensional effects of a part on the thermal conductivity, items printed with powders in SLS-type systems can have their thermal conductivity modified simply by altering the packing density of the powder before it is sintered.
A solid part will conduct heat better than a foam made from the same substance.
To expand on that concept, this research team has demonstrated that the biggest influence on thermal conductivity of Polyamide 12 powder is the inter-particle bonding. Higher density packing means better contact between particles and better bonding.
This other research team has been building on previous research of coating Polyamide 12 with CNT (carbon nanotubes) and confirmed that the addition of CNTs does marginally increase thermal conductivity.
Photopolymers
As with the other functional materials we looked at in the previous articles, if you’re looking for a thermally conducting resin, you may be in for a little wait yet.
The same limitations stopping the electrically conducting resins are at play where it comes to thermally conducting resins. That is, the additives have a tendency to settle, meaning that any photopolymer being used with physically added particles (as opposed to chemically bonded particles) is going to need mixing right up to and possibly during the SLA / DLP printing process.
That isn’t to say that there aren’t any thermally conductive resins on the horizon. They are still currently in the research phase for the time being.
This paper discusses the addition of Halloysite nanoclay nanofillers to the resin, to increase the thermal conductivity of plastic molds used for injection molding. Thermal management of molds is critical in drawing the heat away from the molten plastic in order to reduce differential warping.
There are other teams working with the addition of copper particles, but again, the same issue will likely prevent this research from becoming mainstream for the immediate future.
Final Thoughts
As you can see, generally speaking, plastics are not great for conducting heat, although there are some outliers showing that plastic prints comparable to some alloys are possible.
For the most part, plastics fall far below what a piece of metal would offer in terms of heat transfer.
As with the previous materials we examined in the last weeks, it seems that the widest range of thermal conductive materials is available to those with filament deposition 3D printers, which is not surprising given the proliferation of filament printers out there.
And naturally, due to the nature of filament extrusion, whose feedstock retains its shape and additive distribution until it is extruded, it is easier to print these materials with repeatability and maintain a consistent quality. That said, there is a long way to go before filaments can match metals in terms of thermal conductivity.
But as you can see, there is research ongoing into other printing methods for thermally conductive materials, so expect new materials to hit the market in future.
Research Shows Promising for Thermally Conductive Filaments
You may recall a while back that we did a series of articles on various thermally conductive and electrically conductive polymers suitable for 3D printing.
In this article, we will revisit the concept of thermally conductive plastic filaments, because a team of researchers has released a paper referencing the very materials that we referred to previously.
The researchers from the South-Eastern Finland University of Applied Sciences (XAMK), and the University of Southern Denmark have published their findings around the use of thermally conductive plastics in combination with topology optimization for the production of passive heatsinks.
Specifically the research focused on the use of the ICE9 Rigid Nylon thermally conductive nylon filament from TCPoly, for the design of passive heat sinks using topology optimization for anisotropic heat transfer.
ICE9 Rigid Nylon is one of the filaments we looked at in our previous article on thermally conductive plastics.
Recall how we said that both electrical and thermal conductivity can be altered by the addition of carbon to plastic bulk materials.
The specimens in the research were printed in various orientations and topologies and thermal conductivity measurements were performed to assess the effectivity of the printing process parameters.
The research showed that their experiments showed a 10%–20% reduction in thermal resistance compared to a reference straight fin design.
The image below shows a schematic of the aforementioned straight fin design used in the experiments. Reference samples were made from both printed filament and from extruded aluminum.
The heatsinks were produced with a Minifactory Ultra 3D printer. The printer was selected due to its ability to print high temperature filaments with (dual) nozzle temperatures of up to 470°C.
Due to the anisotropic differences between orientations (especially regarding air gaps and layer bonding imperfections), it was noted that there was better thermal conductivity in one orientation (in-layer orientation) compared to the cross layer orientation.
This table shows the results of the thermal conductivity experiments for both in-layer and cross-layer orientations of the ICE9 samples compared to the reference designs.
Various optimizations were carried out before the final prints to eliminate air gaps and other defects.
In practice, according to the paper, the reduction in air gaps was achieved by adjusting material fed (flow), the width of the print lines (line width) and the settings for filling and infill overlap. By adjusting these settings, it was possible to achieve the optimal prints with the smallest air gaps.
The paper concludes that topology optimization can indeed achieve improved performance of passive heat sinks produced using thermally conductive filaments such as the ICE9 Rigid Nylon material.
The best designs that the researchers had tested demonstrated a 10% and 20% lower thermal resistance when compared to the reference straight-fin heat sink in the vertical and horizontal installation directions, respectively.
In terms of the gains from topology optimization, the optimized heat sinks achieved a 5 to 10% improvement in the thermal resistance for the vertical installation direction and a 15 to 20% improvement for the horizontal direction.
This was due to the performance of the straight fin reference design, which has superior performance in that orientation thanks to the layout of the fins which are aligned in the direction of gravity.
It was also noted that control of the thermal environment was necessary to ensure best results, as effects such as warping could affect the isotropy of the thermal conductivity.
In short, the research demonstrates the utility of both topology optimization and thermally conductive filament, but notes that the effectivity of the parts could be improved by tweaking the parameters further to fit thermal performance requirements.
You can read the open access paper, titled “Material extrusion additive manufacturing and experimental testing of topology-optimized passive heat sinks using a thermally-conductive plastic filament” over at this link.
Metal-filled plastics
Reviews
Each manufacturer (well, or at least large manufacturers) has composite plastics, for example, filled with graphite fibers, or metal powder. The same Bestfilament has long been releasing PLA mixed with powdered bronze, even in a 1:1 ratio. Many did not like him visually, since the fraction was very large.
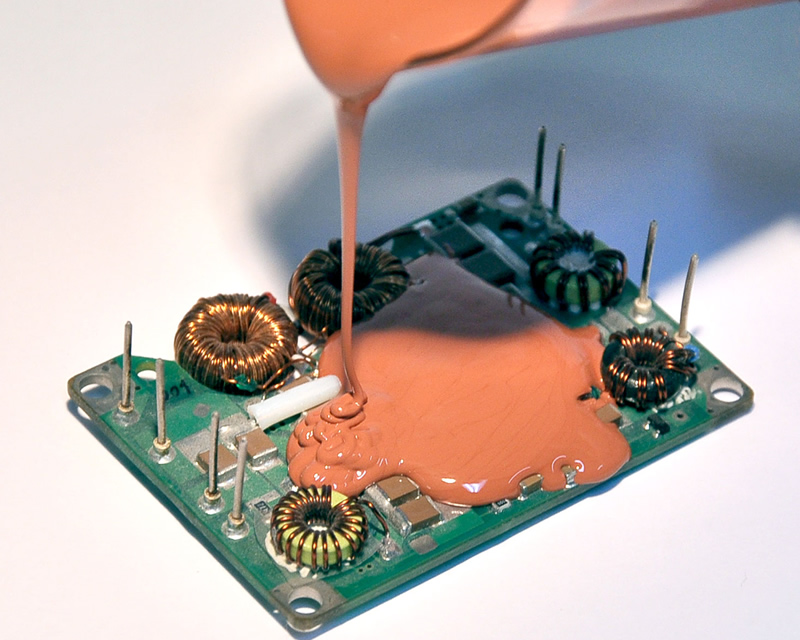
I want to show aluminum filled composites. I have a new plastic from ABSmaker - Pet-g with aluminum powder (it is very similar in color to titanium, and the preliminary name is Titanium) and PLA from Esun with aluminum powder - eAllfill (thanks to Terem for a kilogram sampler).
Since Titanium is not yet mass-produced, the appearance of the package is standard and simple - a cardboard box with a coil inside. Simple, cheap and no nails.
Esun has its own branded window boxes. nine0003
A reel sealed in a disposable bag with the same label on it. The plastic in the rod is dull, uniformly gray, as such there is no shine of the particles. Apparently they are very small.
I don't know the ratio of plastic to powder. But there is a magic piece of paper with
the characteristics of plastics and recommendations for printing them.
It is very useful when the manufacturer does not disdain certifications and talks about the properties of the material.
ABSmakera still has a test batch, maybe because of the powder the diameter is walking, or I have jambs in the printer, that's not the point. Nozzle 0.5mm, printing temperature 240 degrees. nine0003
The Lego helicopter printed a child, it shines perfectly, from some angles of the layers it is generally imperceptible because of the shine. The screw was also made of Titanium-a, but it broke when it fell. Not in layers at all.
Kink glossy.
Also, a printed BQ mask.
The thing in print is very complex, because the support area is small, it just walks like hell when printing.
Stripes above the eye and on the forehead - the same swaying of the mask from printing, because small bends and snot make the mask fold back. nine0003
These larger places no longer seem as flawed as in the backlight.
Although, of course, there is a light tryndets.
The metallic sheen is very beautiful.
Slightly unshaven on the face gives PET-G a head.
You can see the diameter of the festivities or the dangling of the mask, in the end I was already afraid that it would simply be torn off, but the glue from Picaso held very well. Why Picaso and not The3D? It's simple, it's cheaper, but it holds the same. By the way, I sprinkle Byaki on the rug - it holds very well even on a cold one. nine0003
Also printed a hunter.
How does eSun eAllFill print? No way. Tried nozzle 0.3 and 0.5 mm. After the first couple of layers clogs the nozzle. And so - rough to the touch, a kind of gray and matte.
Subscribe to author
Subscribe
Don't want
31
High Temperature 3D Printing - Massively / Habr
There is an impressive variety of thermoplastics that can be printed on consumer-grade desktop 3D printers. But, despite this, most often users turn to polylactide (PLA) threads. This is not only the cheapest of materials, but also the easiest to work with. Its extrusion can already be carried out at a temperature of 180 °C, and good results can be obtained even without preheating the table. The disadvantage of PLA-printed objects is that they are relatively brittle and do not tolerate high temperatures well. For prototyping or printing low-stress components, PLA is great. However, many users quickly go beyond its capabilities. nine0003
Polyethylene terephthalate (PETG) is usually the next step. It is not much harder to work with compared to PLA, while it is more reliable and can withstand higher temperatures. In general, it is better suited for creating mechanically loaded parts. But if you need to make even stronger and more heat resistant parts, you can switch to acrylonitrile butadiene styrene (ABS), polycarbonate (PC) or nylon. And this is where the problems begin. These materials are extruded at temperatures over 250°C and closed chambers are recommended for best results. These printers are at the top of the budget range that hobbyists are willing to work with. nine0069
Industrial 3D printers like this one, the Apium P220, start at around $30,000. (PAEK, PEEK, PEKK). Components made from these plastics are suitable for aerospace applications as they can replace metal while remaining much lighter.
Such plastics need to be extruded at temperatures of around 400°C, and a sealed chamber is required for operation, the temperature in which constantly exceeds 100°C. The cheapest printers of this kind cost tens of thousands of dollars, and some models even cost six figures. nine0003
Naturally, not so long ago, the same could be said about all 3D printers. Once used only by well-equipped research labs, these machines now sit on the workbenches of hackers and hobbyists the world over. It is difficult to predict whether the same price-cutting race will start for high-temperature 3D printers, but the first steps to democratize the technology have already been made.
Engineering difficulties
Simply put, a machine that supports these so-called. "engineering plastics", you need to be a hybrid of a 3D printer and a stove. This, of course, is the main problem. The printer itself - of the type and quality we are accustomed to seeing on our desks - will not survive in such conditions. In order for a consumer printer to produce PEI and PEEK plastic parts, it needs to be seriously redesigned. This is exactly what NASA did with the LulzBot TAZ 4 in 2016. nine0003
LulzBot TAZ 4 redesigned to support high temperature printing
The first step was to design an insulated housing to fit the TAZ 4 and install a set of 35W infrared lamps for heating. Under such conditions, the printer's electronics would naturally overheat - so it had to be taken outside.
Stepper motors would also overheat. But instead of taking them out, the team at the Langley Research Center decided to build cooling shrouds on each of the motors through which the compressed air must circulate. nine0003
Like many desktop 3D printers, the TAZ 4 uses several printed components. Since they are ABS, they would quickly break down in a chamber designed to support PEEK. They were printed from PC, but even this material was not resistant enough for permanent use. In classic RepRap tradition, the team printed the last, third set of components on their most modified printer, in PEI plastic, commercially named Ultem.
Surprisingly, the team had no trouble changing the printer's nozzle to one that could extrude plastic at 400°C. The popular E3D-v6 extruder costs less than $100 and has been shown to be able to maintain this temperature. True, the team had to replace the thermistor with a better one, as well as edit the Marlin firmware so that it allowed it to reach high temperatures. For conventional printers, too high a temperature should cause an emergency shutdown. nine0003
Printing results from Ultem 1010 plastic on a redesigned LulzBot TAZ 4.
In the end, the NASA report indicated that the LulzBot TAZ 4 redesign was a complete success. They noted that an attempt to print PEI with infrared lamps turned off ended in failure - delamination and distortion of the model, which was to be expected. They did not specify the cost of the conversion, but given that at that time the TAZ 4 cost $2200, the entire project could cost 10 times cheaper than similar commercial proposals. nine0003
Starting from zero
A NASA experiment has shown that an existing desktop 3D printer can be converted to print with high-temperature engineering plastics, and quite inexpensively. But hardly anyone believes that this approach is the ideal solution. There are too many repetitive operations involved here, and NASA engineers had to abandon some of the decisions made by the LulzBot developers. Still, the experiment provided a valuable baseline for other projects built from scratch. nine0003
In September 2020, a team from Michigan Technological University demonstrated the Cerberus, an open-source, high-temperature 3D printer capable of creating items from PEI and PEKK, that costs as little as $1,000 to build. Without trying to adapt existing designs, the team started development from scratch, aiming for high temperature printing. All electronics are housed separately from the sealed chamber, which uses a kilowatt heating element to quickly raise the temperature in the chamber to operating temperature. nine0003
All stepper motors are also outside the chamber. Because of this, the kinematics become more complex than in desktop 3D printers, but Cerberus no longer requires a special motor cooling system.
Building a Cerberus is quite affordable for the aspiring hobbyist. It has a simplified circuit, ready-made control electronics based on the Arduino Mega 2560 and RAMPS 1.4, and the same E3D-v6 extruder as the TAZ 4. In addition, the team posted clear and detailed instructions for assembling the printer - this is not in the NASA report. meet. nine0003
Expanding possibilities
Whether it's NASA's redesign of the TAZ 4, or the new Cerberus-type circuits, it's clear that the technical capabilities of PEI and PEEK printing in the home workshop are already available for those who really need them. So far, it's not as easy as buying a $200 3D printer on Amazon, but if there is demand, cheaper machines based on the same principles will appear on the market. The situation is not much different from the current wave of affordable laser cutters hitting the markets in the past few years. nine0003
Fans from all over the world print PPE
Is there a demand for such machines? A year ago, the answer might have been different from today. But in the fight against the coronavirus pandemic, there is a new demand for the rapid production of personal protective equipment (PPE) that no one could have foreseen.
print PPE that can be sterilized at high temperatures. The team believes that masks printed from PEKK can be reused rather than thrown away. nine0003
Components that can be printed and re-sterilized will obviously have other potential medical applications. A portable, low-cost machine capable of producing such components has the potential to save lives in places on the planet where supplies and equipment cannot be quickly accessed.