Ted 3d printing kidney
How Close Are We to Creating Human Organs on a 3D Printer? – Texas Monthly
Sitting in his Rice University lab back in 2013, Jordan Miller was feeling stuck. The bioengineering assistant professor had spent months trying to do something no one had ever done before: create artificial lung tissue that functioned just like the real thing. And though he’d overcome some serious obstacles along the way, he’d reached one he couldn’t see his way past.
The process behind Miller’s experiment was, if not quite simple, at least easy enough to explain in general terms. His intent was to pour a water-based solution into a 3D printer of his own design and then flash a high-resolution image at the liquid from below. In theory, the light would, in a process known as photolithography, solidify the bottom of the liquid into a flat layer of gel, as if Medusa herself had shot her transforming gaze at it. Then the operation would repeat over and over, creating a series of stacked gelatinous layers that would form a biocompatible piece of tissue-like material.
There was a problem, though. To get the solution to solidify, Miller had to shine the printer’s blue light onto a yellow solution—no other color was as efficient at absorbing blue light. But Sudan 1, the standard yellow dye used in a photolithography 3D printer, doesn’t dissolve in water. What’s more, it’s toxic and carcinogenic—not exactly the kind of material people would want surgically implanted into their bodies. The only other dyes that Miller knew would work in the printer were toxic too. He was stymied.
Brainstorming with graduate student Bagrat Grigoryan, Miller asked a question that he probably didn’t need an advanced degree to pose: “What about food coloring?”
It was such a blindingly obvious suggestion that they were immediately skeptical of it. But they couldn’t think of any reason it wouldn’t work. After a quick visit to a nearby H-E-B, Grigoryan added some food coloring into the lab’s special mixture, turned on the printer, and the two men listened to the machine hum softly as it shone blue light on the yellow liquid and—zap! zap! zap!—created the first microlayer. Forty minutes later, when the printer signaled that it was finished, Grigoryan held up the piece of tissue-like material for his boss to inspect. “It was definitely a wow moment,” Miller says.
It was also the first in a series of victories. About a year later, using the same materials and a more complex version of the same process, a team of bioengineers led by Miller created an artificial version of an air sac, the part of a human lung that oxygenates blood and is essential to breathing, and therefore to life. The squishy, gelatinous, ten-millimeter-long air sac looked like a tiny, clear, bulbous purse, and when Miller and his team tested it, they saw that it could absorb oxygen.
It was an important step toward a major objective: creating artificial organs, which could save the lives of thousands of people a year. Achieving that feat remains far down the road, but this new process—enabled by simple grocery-store food coloring—has offered bioengineers a map for getting there.
The implications of Miller’s breakthrough could extend to virtually every organ in the human body. About 113,000 Americans are waiting for organ transplants from donors, and many of those transplants will require that recipients take powerful and dangerous drugs to stop their bodies’ immune systems from rejecting them—and sometimes they’re rejected even so. If the production of artificial tissue (and eventually full organs) can be perfected and scaled up, the dangers of long waits for transplants could all but come to an end.
It’s an exciting prospect that has attracted millions of dollars of government money, including from the U.S. military, and spawned private companies with names like Advanced BioMatrix, Cellink, and FluidForm. But organs on demand won’t be a reality anytime soon. And getting there will take humanity down some very strange, seemingly science-fictional paths.
A U.S. one-cent coin shown next to a scale-model of a lung-mimicking air sac with airways and blood vessels.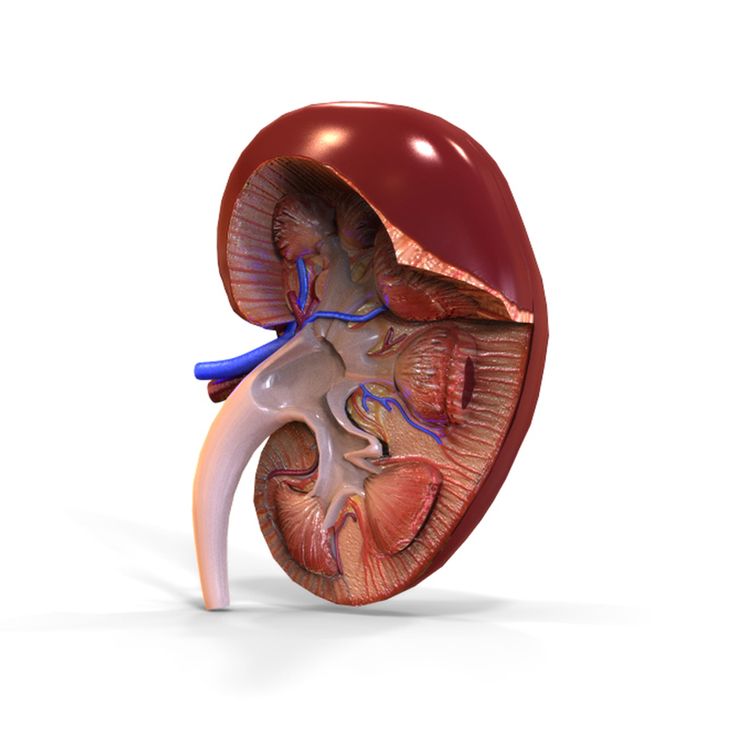
Though more than 100,000 U.S. patients are awaiting transplants, the actual need for organs is even more dire than that number suggests; nearly 730,000 Americans die each year of organ diseases. Some researchers have suggested that a flush supply of organs would prevent more than 30 percent of all deaths in the United States. Barring that, we make do with what we have: generous organ donors and the best immunosuppressant drugs money can buy.
Attempts to build artificial organs from manufactured tissue to meet this demand are nothing new; the idea has been a research focus for the past few decades. In the nineties, Harvard University bioengineers hand-stitched a scaffold—the hollow structural framework—of a bladder from biocompatible materials and successfully grew cells derived from a patient’s own cells on it. They started with the bladder because it’s a relatively simple organ—basically just a muscular sac for holding urine with valves for releasing it—not nearly as complicated in its function as the kidney or liver.
By 1999, the Harvard researchers were implanting young patients with lab-grown bladders that continue to perform well. (Though, two decades on, engineered bladders still haven’t been approved by the FDA for widespread use.) The potential use of printers in this process was pioneered in 2000 by Thomas Boland, a researcher then at Clemson University who filled the ink tanks of a standard desktop printer with bio-inks—cellular material suspended in a solution—and created cells. Soon other engineers were using 3D printers to build layer upon layer of tissue.
At a much-ballyhooed TED Talk in 2011, Anthony Atala of the Wake Forest Institute for Regenerative Medicine, who was part of the Harvard team that created the artificial bladder, garnered press attention when he revealed onstage what many at first mistook for a functional human kidney that his lab had printed. It was, in fact, just a detailed model. It lacked the complex vasculature—the intricate arrangement of blood vessels vital to living tissue—necessary for an organ as complex as the kidney.
For years, bioengineers working with bio-inks failed to replicate the complexities of the multivascular networks found in our organs. By pursuing a photolithographic approach, Rice succeeded where everyone else had come up short. “That’s a nice advance because it addresses one of the main challenges we have today in the field, to bring vasculature and blood supply and oxygen and nutrients to the tissues being printed,” Atala told Texas Monthly. His lab has since experimented with the same technique.
Rice bioengineers Bagrat Grigoryan, Jordan Miller, and Sazer at their laboratory.Jeff Fitlow/Rice UniversityTwo years ago, when Miller and Grigoryan realized they were on to something, they founded their own company, Volumetric, looking to commercialize the technology they created, which now powers a 3D Printer called Lumen X. (Rice owns the intellectual property they developed while working at the university, and Volumetric has exclusive license for its use.)
Miller was inspired to pursue a career in tissue engineering as an undergraduate at Massachusetts Institute of Technology in 2001, after attending a professor’s talk about the potential for using skin scaffolds to aid in the healing of burn victims. “It was preventing scar tissue from forming and was saving people’s lives. It was a fascinating technology,” he says. Soon after, he asked to join the professor’s lab. He went on to earn a bioengineering PhD from Rice, followed by postdoctoral work at the University of Pennsylvania. In 2013, he returned to Rice, where he’s among a handful of professors working on regenerative medicine.
At age 39, he possesses a boyish quality; he talks about the body with enthusiasm, reverence, and awe, as if he’s discussing an architectural marvel. “You have a beautiful airway,” he says excitedly, “ensheathed by a very complicated blood vessel structure.”
One topic that particularly animates him is the notion that he may not need to draw exclusively on human biology to create artificial organs for humans. “Do we need to make something that’s identical to the organs in the body, or is something that’s functionally equivalent going to be as effective?” he asks. “It’s interesting.”
Actually, it’s kind of freaky. While the blueprints for organs will likely be inspired in large measure by human organs, they could also incorporate elements from other species. Human lungs are efficient, Miller points out, but they’re not as efficient as, say, bird lungs. And bird lungs aren’t as efficient as bat lungs.
Miller isn’t suggesting that he’d give someone oversized replicas of bat lungs—only that he might borrow design elements from them. And it gets weirder still. Ideas for organ innovations could come from outside the animal kingdom as well. Some of the designs used in Miller’s air sac, for example, were derived from the vein patterns present in leaves. “We recognize that a lot of the structure in humans resembles the structure in trees: branching, tapering, bifurcation,” he explains. “Because our bodies share design patterns that we see in plants, we can use plant-derived algorithms to design architecture for human tissue.”
In fact, Miller says that he’s been looking beyond flora and fauna for inspiration. Much as a prosthetic leg’s running blade functions more like a spring than a foot, some elements of his artificial air sac were derived from the structure of waterfalls. “You have the tiny tributaries draining into the bigger vessels,” he says, “and there are ways to mimic those phenomena in the lab and in the computational side to get things that will resemble some other vascular architecture and hierarchies that we see in the body.”
For now, though, the Rice lab is focused on optimizing the design of its air sac (Miller’s team’s tiny model was still ten times life-size) as well as other organ subunits, such as the lobule of the liver and the kidney’s glomerulus. These subunits must be perfected before anyone can build a fully functioning artificial organ. They also might first be deployed as implants that could work as short-term “patches” to keep patients’ organs working as they wait for compatible transplants. Atala’s team has already done this in trials at Wake Forest with bits of printed skin, cartilage, and muscle, as well as the vaginal and urethral organs.
It’s important to keep in mind that bioengineers have largely been focused on an artificial organ’s scaffolding—they still have a lot to learn about how to grow the human cells that would fill out the scaffolding to create a complete organ. Still, Miller believes we could see entire artificial organs within the decade. (Though decades more of clinical trials will likely take place before they are approved for widespread use.) The timing depends, of course, on funding and how well human bodies take to these artificial structures. There’s no guarantee that artificial organs won’t be rejected much as transplanted organs sometimes are, though there’s hope they will have a higher success rate since they could be created from a patient’s own cells.
The prospect of such technology transforming countless lives has motivated Miller since age sixteen, when, already deeply interested in biology, he was asked to check the organ-donor box on a driver’s license application. It was the first time he remembers reckoning with the knowledge that there are many sick people waiting for others to die just to have a shot at extending their own lives. “That was quite transformative for my young mind at the time,” he recalls. “It really said to me, ‘This is something worth working on.’ ”
This article originally appeared in the March 2020 issue of Texas Monthly with the headline “The New Kidney in Town.” Subscribe today.
3D-Printed Kidneys Take Small Steps Toward Organ Replacements
When you purchase through links on our site, we may earn an affiliate commission. Here’s how it works.
Kidneys represent the human organ in highest demand among the more than 120,000 U.S. patients currently waiting for organ donations. (Image credit: <a href="http://www.shutterstock.com/gallery-540784p1.html">Lightspring</a> | <a href="http://www.shutterstock.com">Shutterstock</a>)A model of a 3D-printed kidney drew wild applause when a surgeon first held it up at a TED conference in 2011. But the dream of creating replacement human kidneys using 3D-printed technology still remains years away, even as the technology has enabled the rise of "bioprinting" aimed at building organs suitable for transplantation.
Kidneys represent the human organ in highest demand among the more than 120,000 U.S. patients currently waiting for organ donations. Researchers hope that new generations of 3D printers can use living human cells to build replacement organs layer by layer — especially organs such as livers, hearts and kidneys.
"These are by far the most complex, because you have a lot more cells per centimeter than any other organ, and because you have so many cells that are functionally complex," said Tony Atala, director of the Wake Forest Institute for Regenerative Medicine in Winston-Salem, N.C.
Atala helped pioneer the idea of building artificial scaffolds in the shapes of organs and seeding them with living cells in the lab. That allowed his team to create and implant tissue-engineered bladders into seven young volunteers in 1999. Now he has set his sights on the more challenging task of building more complex organs such as kidneys with the help of 3D printing — the process he demonstrated with the 3D-printed model in the shape of a kidney in front of the TED crowd in 2011. [7 Cool Uses of 3D Printing in Medicine]
But the hype surrounding the futuristic idea of bioprinting can prove misleading. News headlines mistakenly reported that Atala had held up a real living kidney on the TED stage in 2011. This year, breathless news reports also overhyped the work of a Chinese team at Hangzhou Dianzi University of Electronic Science and Technology that had 3D-printed a mass of living cells in the shape of a miniature kidney.
"They printed the shape of it, but they're not printing at the level of individual cells yet," said Stuart Williams, executive and scientific director of the Cardiovascular Innovation Institute in Louisville, Ky. "That's one of the limitations of 3D printing."
Even the finest next-gen 3D printers won't be able to print human tissue at small enough scales to match the real-life complexities of human organs, Williams explained. Similar problems have prevented 3D printing from building the tiny networks of blood vessels required to keep full-scale organs healthy.
The kidney represents a special challenge for 3D printing, because of its detailed, tiny structures that allow the organ to filter out waste chemicals from blood and turn the waste into urine. Bioprinting researchers hope to take advantage of the self-organizing tendencies of stem cells extracted from patients to fill in the missing details and knit together full-size organs.
"It's going to be hard to get a full-size kidney with 3D printing alone, without nurturing biological activity and encouraging [the organ] to grow into its final form," said Keith Murphy, CEO of Organovo, a San Diego-based startup.
A 3D-printed kidney, like other 3D-printed replacement organs, likely won't become a reality within the next 10 or 15 years, researchers say. But they plan to use the simplified, miniature versions of 3D-printed organs created so far as guinea pigs for pharmaceutical drug testing — an idea that could help scientists to discover drugs suitable for humans more efficiently and ethically than animal testing.
You can follow Jeremy Hsu on Twitter @jeremyhsu. Follow us @livescience, Facebook & Google+. Original article on LiveScience.
Jeremy has written for publications such as Popular Science, Scientific American Mind and Reader's Digest Asia. He obtained his masters degree in science journalism from New York University, and completed his undergraduate education in the history and sociology of science at the University of Pennsylvania.
Harvard scientists one step closer to progress
3D printing of a kidney
Talk about the possibilities of 3D bioprinting does not subside at all, flaring up with renewed vigor as this unique technology develops. Not only scientists and researchers argue about the practical implementation of bioprinting, but ordinary people are not alien to the dream of successfully creating living human tissues and organs. In the meantime, we are busy dreaming, the greatest minds of mankind are hard at work on the manufacture of the functioning elements of our body using a 3D printer. For example, 3D printing of a kidney, which has occupied the minds of researchers from all over the world for a long time, is now much more real. So, scientists from Harvard University have advanced in the creation of a real human kidney, having made a tubular structure on a 3D bioprinter that mimics the function of this organ. nine0005
Their development can have a serious impact not only on the development of bioprinting in general, but also on the study of the effect of drugs on the human body. In addition, laboratory-grown kidneys will help scientists artificially model the state of diseases in order to find the best methods for their treatment.
A group of researchers has been working in the field of 3D bioprinting for several years and during this time has achieved significant success. It is they who should be credited with the development of several methods for printing with living cells, as well as a method for making blood vessels. At present, their ideas are widely used in this environment for printing "live" structures of human tissues of various kinds. The method allows scaling these constructs, creating denser tissues with high viability. nine0005
3D printing of a kidney on a 3D printer
Now scientists have taken up a new project based on the above technology. Its essence lies in the use of 3D printing to create a functional renal architecture containing living epithelial cells lining the surface of the renal tubules. Thus, 3D printing of a kidney is more real than ever. The task itself is very difficult, because for a qualitative imitation of the structure of the kidneys, careful observance of many factors is required, in particular, the qualitative functioning of nephrons, one of the most important elements of this organ. nine0007 Nephrons perform filtration and secretion of substances, being a vital structural unit of the kidneys. That is why a qualitative imitation of their tubules can serve as the key to the successful creation of artificial organs. However, a 3D printed artificial kidney will no longer be just a science fiction fantasy.
3D printing of a kidney: features
So, let's briefly describe the 3D bioprinting process used by Harvard scientists. First, a silicone layer is applied as a base layer, on which a sinuous line of “temporary ink” will then be applied. The structure cools slightly, after which the ink is removed, leaving instead a hollow tube suitable for the introduction of living cells. Immediately after implantation, the cells begin to adhere to the walls of the 3D printed tube, forming a new epithelium. As such a structure matures (which can take up to two months), it begins to perform the same important functions as the nephron tubules, so well that it becomes potentially suitable for more serious applications. nine0005
3D printer budding
According to the developers, this architecture is extremely robust and functions flawlessly, which represents a significant step forward in 3D bioprinting. The structure can be used for a variety of medical purposes, from researching the effects of drugs to finding options for diagnosing and treating diseases. 3D printing of a kidney using this technique will not go unnoticed and will receive a lot of different applications.
And scientists are confident in the success of the directly innovative method of 3D printing of living tissues. They claim that their approach allows the creation of flexible, scalable structures that can be used in bioprinting of organs other than the kidneys. Undoubtedly, their achievement is extremely serious and will open many doors to the world of medicine. nine0005
Back to home page
3D printer: what is it and how does it work? | GeekBrains
https://gbcdn.mrgcdn.ru/uploads/post/1999/og_image/501bb6c82a53bb3bc2a0fee73b0c9e9e.png
In 2011, a printer filled with a human kidney TED printed directly during a TED conference. Two years ago, Adidas announced a new sneaker that can be 3D printed in 20 minutes. And recently, Elon Musk's SpaceX successfully tested the spacecraft's engines, which were also printed on a 3D printer. nine0005
In today's world, 3D printing is not an amazing technology of the future, but a well-studied reality. It is used in architecture, construction, medicine, design, production of clothing and footwear and other areas. At the request of "3D printer", search engines give out hundreds of drawings and prototypes of varying complexity - from a soap dish and a table lamp to a car engine and even a residential building.
Anyone can buy a printer and print a case for a smartphone, but not everyone goes beyond 3D printing from a drawing. In this article, we will tell you when 3D printing appeared, how the technology can be applied and what its prospects are. nine0005
How the 3D printer came to be
Let's not bore you too much with the dates and briefly retell the history of 3D printing.
A precursor to 3D printing. In the early 1980s, Dr. Hideo Kodama developed a rapid prototyping system using photopolymer, an acrylic-based liquid substance. The printing technology was similar to the modern one: the printer printed the object according to the model, layer by layer.
First 3D printing. The production of physical objects using digital data was demonstrated by Charles Hull. At 19In 84, when computers were not much different from calculators, and ten years before the release of Windows-95, he invented stereolithography, the forerunner of 3D printing. The technology worked like this: under the influence of an ultraviolet laser, the material solidified and turned into a plastic product. The form was printed on digital objects, and this became a boom among developers - now it was possible to create prototypes at a lower cost.
The first 3D printer. Source: habr
The first manufacturer of 3D printers. Two years later, Charles Hull patented the technology and opened the 3D Systems printer company. It released the first machine for industrial 3D printing and is still leading the market. True, then the printer was called differently - an apparatus for stereolithography. nine0005
The popularity of 3D printing and new technologies. In the late 80s, 3D Systems launched mass production of stereolithographic printers. But by that time, other printing technologies had also appeared: laser sintering and deposition modeling. In the first case, the powder was processed by the laser, not the liquid. And the majority of modern 3D printers work according to the fusing method. The term "3D printing" came into use, the first home printers appeared.
A revolution in 3D printing. At the beginning of the 2000s, the market split into two directions: expensive complex systems and those that are available to everyone for printing at home. The technology began to be used in specific areas: for the first time, a bladder was printed on a 3D printer, which was successfully implanted. nine0005
Kidney Test Print. Source: BBC
In 2005, the first high-quality color 3D printer appeared, creating kits for itself and "colleagues".
How a 3D printer works
Basically, 3D printers consist of the same parts and are similar in design to conventional printers. The main difference is obvious: a 3D printer prints in three planes, and in addition to width and height, depth appears.
Here are the parts of the 3D printer, not counting the body:
- extruder, or print head - heats up the surface, measures the exact amount of material using a gripping system and squeezes out semi-liquid plastic, which is fed in the form of threads;
- desktop (it is also called a working platform or printing surface) - on it the printer forms parts and grows products;
- linear and stepper motors - set the parts in motion, are responsible for the accuracy and speed of printing;
- clamps - sensors that determine the print coordinates and limit moving parts. They are needed so that the printer does not go beyond the desktop, and make printing more accurate; nine0078
- frame - connects all elements of the printer.
Schematic of a 3D printer. Source: Lostprinters
All of this is computer controlled.
How products are created
The additive 3D printing process is responsible for creating a three-dimensional product - this is when layers of material are superimposed on each other during the manufacture of an object, from bottom to top, until a copy of the form in the drawing is obtained. This is how plastics are printed. And photopolymer printing works on stereolithography (SLA) technology: under the influence of a laser emitter, photopolymers harden. In addition to plastic and photopolymer resins, modern 3D printers work with metal clay and metal powder. nine0005
Printing consists of continuous cycles that repeat one after another - one layer of material is applied to the next, and the print head moves until the finished object is on the working surface. The printer itself removes print waste from the desktop.
How a 3D drawing works
The printer prints a product according to a 3D drawing: it is created on a computer in a special program, then saved in STL format. This file is output to the cutting program for the printer - it helps to set the model of the physical properties of the product, such as density. Next, the program converts the model into instructions for the extruder and uploads it to the printer, which starts printing the product. nine0005
3D drawing is easy to make at home - read the instructions on habr.
How to program a 3D printer
Brief instructions for setting up the printer:
- Select a 3D model. You can draw the product yourself in a special CAD editor or find a ready-made drawing - the Internet is full of models of varying complexity.
- Prepare 3D model for printing. This is done by the slicing method (slice - part). For example, in order to print a toy, its model must be “split” into layers using slicer programs and transferred to the printer.
Simply put, the slicer shows the printer how to print the object: which contour to move the print head, at what speed, what thickness of the layers to make. nine0078
- Transfer model to printer. From the slicer, the 3D drawing is saved to a file called G-code. The computer downloads the file to the printer and starts 3D printing.
- Monitor printing.
Whether printed products can be used
Depends on the quality of the media, printer and end product. Often home printers do not accurately convey the shape and color of an object. Plastic products need additional processing: sometimes they are printed with burrs and defects, and almost always with a ribbed surface. nine0005
Product after and before processing. Source: 3D-Today
There are several ways to finish the surface - not all are suitable for home use:
- mechanical processing - hand sanding, deburring;
- chemical - immersion in acetone, sandblasting, applying a special solution with a brush.
What can be printed with a 3D printer
The Internet is full of collections with instructions for printing 3D products. 3D-Today publishes photos of the work of printer owners, from small parts to sculptures. Three years ago, Habré posted a list of "50 cool things to print on a 3D printer." Make3D wrote about larger projects like printing cars, weapons, solar panels, and prosthetics. nine0005
There are a number of promising areas where 3D printing is already being applied.
Making models according to your own sketches. Konstantin Ivanov, the creator of the 3DPrintus service, in an interview with Afisha said that 3D printing will lead to the flourishing of customizable things: anyone can assemble and print the desired product online. For example, make a model of a robot and order its printing on an industrial printer, create and print your own design of wedding rings or shoes. Examples of such projects are Thinker Thing and Jweel. nine0005
Rapid prototyping. The most popular area in which 3D printing is used. Test models of prostheses, prototypes of medical corsets, bas-reliefs, Olympic equipment are made on 3D printers.
Prototypes of children's prostheses, 3D printing. Source: 3D-Pulse
Complex geometry. The 3D printer can easily handle the production of models of any shape. A few examples:
- an Australian university explored the possibilities of a 3D printer and printed a stool in the shape of a fingerprint; nine0005
- A Danish chef has won a haute cuisine competition by 3D-printing complex-shaped miniature dishes of seafood and beetroot puree;
One of the chef's winning dishes. Source: 3D-Pulse
- A German institute has developed a system for accelerated 3D printing - in 18 minutes, the printer produces a complex geometric product 30 cm high. It usually takes printers an hour to print pocket figures.
3D printing technology
Briefly about the main methods of 3D printing.
Stereolithography (SLA). In a stereolithographic printer, a laser irradiates photopolymers and forms each layer according to a 3D drawing. After irradiation, the material hardens. The strength of the product depends on the type of polymer - thermoplastic, resins, rubber.
Stereolithography does not support color printing. Other drawbacks include slow operation, huge size of stereolithographic setups, and you can't combine multiple materials in one run. nine0005
This technology is one of the most expensive, but guarantees printing accuracy. The printer applies layers with a thickness of 15 microns - this is several times thinner than a human hair. Therefore, with the help of stereolithography, dental prostheses and jewelry are made.
Industrial stereolithography machines can print huge products, several meters long. Therefore, they are successfully used in the production of aircraft, ships, defense industry, medicine and mechanical engineering. nine0005
Selective laser sintering (SLS). The most common method for sintering powder materials. Other technologies are direct laser sintering and selective laser melting.
The method was invented by Carl Descartes in the late eighties: his printer printed by layer-by-layer drawing (sintering). A powerful laser heats up small particles of material and moves along the contours of the 3D drawing until the product is finished. The technology is used to manufacture not whole products, but parts. After sintering, the parts are placed in an oven where the material burns out. SLS uses plastics, ceramics, metals, polymers, fiberglass in powder form. nine0005
The athlete is wearing New Balance shoes, which were made using laser sintering. Source: 3D-Today
SLS technology is used for prototypes and complex geometric parts. For printing at home, SLS is not suitable due to the huge size of the printer.
FDM or Fused Deposition Modeling. This 3D printing method was invented by American Scott Crump. FDM works like this: the material is fed into the extruder in the form of a thread, where it heats up and is fed to the worktable in microdroplets. The extruder moves along the working surface in accordance with the 3D model, the material cools down and solidifies into the product. nine0005
Advantages - high product flexibility and temperature resistance. For such printing, different types of thermoplastics are used. FDM is the most inexpensive among 3D printing technologies, which is why printers are popular for home use: for making toys, souvenirs, and jewelry. But mostly fusing modeling is used in prototyping and industrial production - printers quickly print small batches of products. Refractory plastic items are made for the space industry. nine0005
3D inkjet printing. One of the first methods of three-dimensional printing - in 1993, it was invented by American students when they improved a conventional paper printer, and soon the technology was acquired by the same company 3D Systems.
Inkjet printing works like this: a binder is applied to a thin layer of material along the contours of the drawing. The print head applies the material along the boundaries of the model, and the particles of each new layer stick together. This cycle is repeated until the product is ready. This is one of the types of powder printing: earlier inkjet 3D printers printed on plaster, now they use plastics, sand mixtures and metal powders. To make the product stronger, after printing it can be impregnated with wax or fired. nine0005
Items printed using this technology are usually durable, but not very durable. Therefore, with the help of inkjet printing, souvenirs, jewelry or prototypes are made. This printer can be used at home.
These candies were made on a ChefJet confectionery inkjet 3D printer that uses water, sugar, chocolate and food coloring instead of plastic. Source: 3Dcream.ru
Inkjet technology is also used in bioprinting, where living cells are layered on top of each other and thus organic tissues are built. nine0005
Where 3D printing is used
Mainly in professional fields.
Construction. 3D printers print walls from a special cement mixture and even houses with several floors. For example, back in 2014 Andrey Rudenko printed a 3 × 5 meter castle on a construction printer. Such 3D printers can build a two-story house in 20 hours.
Medicine. We have already mentioned the printing of organs, and 3D printers are also actively used in prosthetics and dentistry. Impressive examples - with the help of 3D printing, doctors managed to separate Siamese twins, and a cat without four legs was given prostheses that were printed on a printer. nine0005
For more information about 3D printing in medicine, see the 3D-Pulse article.
Space. 3D printing is used to make equipment for rockets and space stations. Another technology is used in space bioprinting and even in the work of lunar rovers. For example, the Russian company 3D Bioprinting Solutions will send live bacteria and cells into space, which will be grown on a 3D printer. Amazon founder Jeff Bezos unveiled a prototype lunar module with a printed engine, and space startup Relativity Space is building a rocket 3D printing factory. nine0005
Aviation. 3D parts are printed not only for spacecraft, but also for aircraft. Engineers at the US Air Force Lab can 3D print aircraft components, such as a fuselage skin element, in about five hours.
Architecture and industrial design. 3D printers print models of houses, neighborhoods and villages, including infrastructure: roads, trees, shops, lighting, transport. As a material, an inexpensive gypsum composite is usually used.
One of the unusual solutions is the design of concrete barricades by American designer Joe Ducet. After the terrorist attacks with trucks that crashed into a crowd of people, he proposed a model of durable and functional barriers in the form of a designer, which can be printed on a 3D printer.
UrbaStyle, a company that prints concrete molds on 3D construction printers, helped make the prototype.