Support material for 3d printing
Which 3D printing supports to use: PLA, PVA or Breakaway
David Roberson5 December 2017
Applications
With the launch of Ultimaker’s Breakaway support material, there are now even more options for supporting your 3D prints. But which one is right for your design? Let’s take a look at the different options and when to use each one.
When using an FFF 3D printer, support material enables you to print models that would otherwise not be possible due to, well, gravity. It ‘supports’ the material above it so you can print objects with features like overhangs or cavities.
A model with support material
And with support material removed
For more advanced users, support material can also give you more design freedom. With it you can orient your model exactly how you want for the best results, or create designs with moving parts built in that are free to move once you remove the support material.
Build material supports
The original way to support your 3D print. If you are printing with, for example, PLA, then 3D printing software like Ultimaker Cura can create support structures for your model that will print in the same material.
If you are using a single-extrusion 3D printer, this is the only way to print support structures. It’s also a good option if you don’t want to worry about material compatibility. Not all build materials are compatible with separate support materials.
The main drawback to using build material supports is that when you remove the supports manually, you will never be able to get a model that is 100% accurate compared with your original design. If you cut or sand your supports too much or leave any small bumps, your model will be a slightly different shape to your design.
This can be a problem if your 3D print needs to be very accurate, for example you are prototyping a part to test its fit or form.
Cutting and sanding away supports can also damage the surface of your 3D print and need post-processing techniques like polishing to achieve a good quality surface finish.
To remove build material supports, you will need a cutting implement (most people use a knife or pliers) and sandpaper to get rid of any final traces.
Dissolvable PVA
If your 3D printer can print more than one material, then it is also possible to combine your build material with a separate support material that is easier to remove.
PVA is a water-soluble support material. Because it dissolves away when submerged in water, it gives you almost complete design freedom. Large overhangs, cavities, intricate shapes are all possible, and there is no risk of scratching your print while removing the support. It leaves behind a very smooth surface.
One downside of PVA is that while it is effortless to remove, it does take several hours to dissolve so it can hold up your 3D printing workflow. PVA is also more expensive than other support material options and its quality can degrade if not stored properly.
Ultimaker PVA is optimized for use with PLA, Nylon, and CPE.
To remove PVA, all you need is a container of tap water big enough for your model. Read our complete guide to dissolving PVA.
Breakaway supports
The newest support material offered by Ultimaker, Breakaway has some similarities to the other types of support.
Watch the videoLike build material, it is removed manually. But like PVA, it is a separate material printed with dual extrusion.
The result is a balance between the advantages of the other support material options. You can remove Breakaway by hand so there’s no need to wait hours for anything to dissolve, but it also peels away cleanly from the rest of your print so you have an accurate model and don’t need to post-process it.
However, for the smoothest surface finish we still recommend PVA. And the Breakaway material in your print needs to be accessible for you to remove it, so you do not have complete design freedom.
Ultimaker Breakaway is optimized for use with ABS, Nylon, PLA, CPE, and CPE+.
To remove Breakaway supports, you will need a set of pliers. Read our complete guide to removing Breakaway.
Quick comparison: When to use...
Build material supports: When you don’t need a print that is 100% accurate compared to the dimensions of your 3D design. Or if you only have a single extrusion 3D printer
PVA: Ideal if you’re printing a complex shape or when you want a really smooth surface finish beneath your supports, but takes several hours to dissolve
Breakaway: If you’re short on time, Breakaway is quicker to remove than PVA and keeps the dimensional accuracy of your print, with a quality surface finish
Explore Ultimaker materials
Support 3D Printer Filament | MatterHackers
- Home
- Store
- 3D Printer Filament
- Support Filament
Dissolvable and breakaway support materials for dual extrusion 3D printing.
Support Filament Collections
All Support Filament 3D Printer Filament
Getting Started
Choosing the Right 3D Printing Support Material // Comparison Guide
Support Filament
Ionic Hi-Temp Hybrid Support Material
Print intricate 3D models in advanced materials with this reliable hybrid-support material.
PRO Series Breakaway Support Material
Provides fast, easy, and clean mechanical breakaway for 3D printed parts.
MH PVA Support Filament
MH PVA Support Filament is a dissolvable support material for dual extrusion parts.
PVA (Polyvinyl Alcohol)
Polyvinyl Alcohol, a water-soluble support material that dissolves away in a water bath to leave only your perfectly printed part.
Ultimaker Support Materials
Easy and quick to remove breakaway support
MH Build Series PVA Filament
An affordable, low cost PVA filament intended for producing supports when printing complex 3D prints
Guides & Articles
How To Succeed When 3D Printing With PLA Filament
Discover the best practices for 3D printing with PLA filament - from finding the right temperature, to which surfaces to 3D print on, this step-by-step guide will help you succeed with 3D printing PLA.
How To Succeed When Printing With ABS
ABS filament is a versatile material that's a great option for when you need your 3D-printed parts to be strong and heat-resistant. Learn how to print this material like a Pro in this in-depth guide.
How to Succeed when 3D Printing with PETG Filament
This in-depth guide provides everything you need to succeed when printing with PETG filament. Embrace the fantastic properties of durable and easy to print, PETG filament!
How to Succeed with 3D Printing Metal on a Desktop 3D Printer
The time is here to explore easy and affordable metal 3D printing. 3D printing with real metal on a desktop 3D printer is now possible using Ultrafuse Metal 3D printing filament from BASF Forward AM.
How To Succeed When 3D Printing With Nylon
Learn how to 3D print Nylon like a pro. Nylon is a stronger and more durable alternative to PLA or ABS and easy to 3D print with using these Tips and Tricks.
How To Succeed When Printing With Flexible Filament
Let’s take a look at what makes flexible filaments easier to print and how you can add flexible filament to your 3D printing material toolbox.
How to Succeed with NylonX
NylonX has quickly become one of our favorite filaments for strong, durable, and ready-to-use parts. Here's an in-depth look at Nylon X, and some printing tips to get the most out of this great new material.
How to Succeed When 3D Printing with MH Build Resin
Make SLA resin 3D printing easier with this helpful detailed article on how to successfully fine-tune photopolymer resin to your 3D printer.
How To Succeed: 3D Printing with Nylon and Nylon Composites
Nylon and nylon composites perform exceptionally well in a variety of uses, it just takes a gentler touch to print it successfully.
How To Succeed When 3D Printing With ASA Filament
Follow this step-by-step guide to learn how to print with ASA, the perfect material for any outdoor projects.
What is support material in 3D printing
Support material is an auxiliary material used in 3D printing to build complex objects and increase the quality and stability of construction. Without the use of support, 3D printing of models with cavities, overhanging structures, complex detailing, thin walls or floors, and other complex elements is impossible.
Support serves as a kind of temporary foundation for the printed product. Layered construction assumes that each next layer of the product relies on the previous one. In the case when the design of the product does not provide support under the first layer in one place or another, support comes into play. nine0003
Support serves as a kind of temporary foundation for the printed product. Layered construction assumes that each next layer of the product relies on the previous one. In the case when the design of the product does not provide support under the first layer in one place or another, support comes into play.
Complex geometry detail before and after removal of support.
Complex geometry detail before and after removal of support.
Benefits of using support material
- Ability to print more complex objects (than without support).
- High accuracy and stability in the construction of complex and small elements (does not allow them to "disperse", deform under the weight of the following layers).
- Significant reduction in CAD file constraints (slopes, wall thicknesses, corners, cavities, etc.).
Benefits of using support material
- Ability to print more complex objects (than without support). nine0016
- High accuracy and stability in the construction of complex and small elements (does not allow them to "disperse", deform under the weight of the following layers).
- Significant reduction in CAD file constraints (slopes, wall thicknesses, corners, cavities, etc.
).
How to determine where support is needed?
The software provided with all professional 3D printers does this automatically. You just need to upload a file in STL format, and the program will independently calculate where the use of auxiliary material is necessary for high-quality construction. It is worth noting that most software also allows the user to edit the number and location of auxiliary structures. nine0003
How to determine where support is needed?
The software provided with all professional 3D printers does this automatically. You just need to upload a file in STL format, and the program will independently calculate where the use of auxiliary material is necessary for high-quality construction. It is worth noting that most software also allows the user to edit the number and location of auxiliary structures.
Model placed in virtual print chamber
Model in the virtual print chamber with automatically calculated support
Model placed in the virtual print chamber
Model in the virtual print chamber with automatically calculated support
In addition, the program calculates the amount of support material required before printing.
In addition, the program calculates the amount of auxiliary material required before printing.
Types of support materials
Mechanically removed
Excess material is broken off, sawn off, scraped off. The simplest type, usually used in cheap desktop printers that work with plastic. In this case, the support is the same material from which the model itself is built. But, in order to facilitate its subsequent removal and reduce the consumption of model material, the support is built more “sparsely” compared to the object itself. It has a much lower density and strength, only sufficient to temporarily support the weight of the object being grown. nine0003
Types of support materials
Mechanically removed
Excess material is broken off, sawn off, scraped off. The simplest type, usually used in cheap desktop printers that work with plastic. In this case, the support is the same material from which the model itself is built. But, in order to facilitate its subsequent removal and reduce the consumption of model material, the support is built more “sparsely” compared to the object itself. It has a much lower density and strength, only sufficient to temporarily support the weight of the object being grown. nine0003
Manual support removal process video
Manual support removal process video
Soluble
Auxiliary material dissolves in a special liquid. This method of removing support, for example, is used in Stratasys' uPrint SE professional plastic 3D printers. Advantages: withstands significant loads and temperatures, dissolves without damage to the base material.
Soluble
Auxiliary material is soluble in a special liquid. This method of removing support, for example, is used in Stratasys' uPrint SE professional plastic 3D printers. Advantages: withstands significant loads and temperatures, dissolves without damage to the base material. nine0003
In the photos you can see the whole process of calculating, building and removing the soluble support material. 3D printer - uPrint SE Plus. Dissolution time - 1.5 hours.
Lost wax
Melts and flows out at low heat (well below the deformation temperature of the main product). Usually has a wax base. Advantages: delicacy, accuracy of application. Used in photopolymer and wax 3D printers of the ProJet series by 3D Systems.
In the photos you can see the whole process of calculating, building and removing the soluble support material. 3D printer - uPrint SE Plus. Dissolution time - 1.5 hours.
Lost wax
Melts and flows out at low heat (well below the deformation temperature of the main product). Usually has a wax base. Advantages: delicacy, accuracy of application. Used in photopolymer and wax 3D printers of the ProJet series by 3D Systems.
Lost-wax master wax and after removal
Lost wax master model and after removal
Washable
Special gel-like material that can be washed out of the master model with warm water. Advantages: simple removal process, high construction accuracy, does not damage the model material when removed. Used in photopolymer 3D printers of the Objet series from Stratasys.
Washable
Special gel-like material that can be washed out of the base model with warm water. Advantages: simple removal process, high construction accuracy, does not damage the model material when removed. Used in photopolymer 3D printers of the Objet series from Stratasys. nine0003
Model before printing
Model in build chamber with support material
Finished model after removing support material
Model before printing
Model in build chamber with support material
Finished model after removing support material
9005 Powder support We should also mention powder 3D printing technologies (CJP, SLS, SLM). Here, the same material acts as auxiliary and main. However, that part of the powder that was "auxiliary", after cleaning, can be reused as the main material.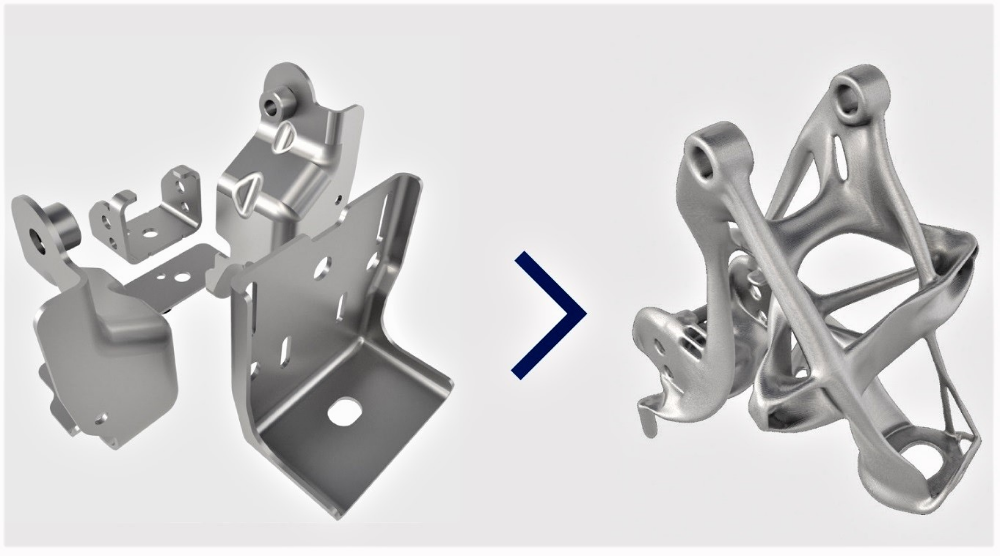
Powder support
We should also mention powder 3D printing technologies (CJP, SLS, SLM). Here, the same material acts as auxiliary and main. However, that part of the powder that was "auxiliary", after cleaning, can be reused as the main material. Due to this, such technologies are practically waste-free.
Get advice on choosing a 3D printer
Call +7 495 646-15-33
Write to WhatsAppLeave a request for a call
Come to our demo hall
Learn moreI confirm the accuracy of the information I entered and agree to the processing of my personal data in accordance with the privacy policy and user agreement.
Main plastics for FDM 3D printing
Contents
- Introduction
- Conditional division into “amateur” and “professional” plastics nine0016
- Basic materials
- ABS
- PLA
- PETG
- HIPS
- SBS (Watson)
- TPU (FLEX )
- NYLON
- AS
- PP
- PC
- POM
- PMMA
- PEEK
- Ceramo
- PVA
- WAX
- Clearing
- Composite materials nine0016
- Conclusions
- FAQ
Introduction
At the current level of technological development and the chemical industry in the world, an insane amount of plastics has been developed and sold, which continues to increase every day. However, most of this diversity is due to slight modifications to the basic compositions, as well as the intrigues of marketers from manufacturing companies who come up with different names for the same products, just to sound good. In this article, we will try to briefly describe different types of plastics, which fundamentally differ from each other in composition and, as a result, properties and characteristics. We describe their strengths and weaknesses, and the preferred areas of application arising from them. nine0003
Important note. Plastics of even the same type can differ quite a lot from each other depending on the manufacturer, additives, quality, color, batch, and even on the period and storage conditions. This is especially true for materials such as PLA, they are contraindicated in high and low humidity, high and low temperatures, direct exposure to sunlight (UV in particular), but after a year or two, even under ideal conditions, they become brittle like dry spaghetti and unsuitable for work. Therefore, the information in this article (and other sources) is valid only for average plastics and applies to their original, new state. For the same reason, we will not delve into the variety of technical characteristics, we will only touch on the main ones, since the spread is too large and any figure will be approximate. Information about the more or less exact parameters of each specific plastic on a specific coil should be taken from the manufacturer's specifications. nine0003
Note. This article deals only with plastics for FDM printing, liquid polymers and materials for other technologies - a topic for separate articles.
Conditional division into amateur and professional plastics
The word “conditional” in the title is not accidental, there is no clear division of plastic types according to such a criterion as “professionalism”. All of them can be used both at home and at work, but working with some of them places very high demands on the printer, which in most cases are not available to home “favorites”. For example, not all budget printers will be able to provide a nozzle temperature above 250 ℃, and not every nozzle will endure such treatment. A thermal camera is also not a cheap pleasure, especially an active one, capable of maintaining a predetermined temperature in the print working area. And the price of professional / engineering plastics, as a rule, is several times higher than usual ones, which makes them completely uninteresting for home use. However, it is interesting and useful to get acquainted with them, you need to know what FDM technology is capable of, brought to perfection, so we included professional materials in this review too. nine0003
Plastic materials
ABS , the full, hard-to-pronounce name is acrylonitrile butadiene styrene. One of the oldest representatives of thermoplastics for FDM printing, has both an army of old-school fans and modernist deniers, holivars between which have not subsided for more than a year. We will not join any of the parties, everyone decides for himself what to love and what to hate, as well as change his mind in the course of time, experiments, experienced admiration and disappointment. nine0003
ABS is a fully synthetic material, which means it has the following advantages:
strength and impact resistance,
chemical resistance,
long service life,
high temperature resistance,
possibility of light post-processing, both mechanical (drilling, grinding, cutting, etc.) and chemical (dissolved in acetone),
Individual parts made of ABS are bonded immediately and permanently with acetone, nine0003
low price.
Due to its merits, ABS is excellent for printing functional, mechanically stressed products. Parts can work for a long time at temperatures from -40 to +80 degrees Celsius, in damp conditions and even in water, as well as in the environment of some aggressive chemical vapors and liquids. With the help of an “acetone bath”, the surfaces of ABS products are given a pleasant glossy appearance, which makes it possible to successfully use it for artistic and decorative purposes, which, incidentally, is facilitated by the widest color gamut of all plastics on the market. In addition, ABS is one of the most inexpensive materials, which undoubtedly contributes to maintaining its popularity. nine0003
ABS is not without flaws, and there are many. The first follows from its chemical origin: when heated, an unpleasantly smelling gas is released, which is far from beneficial to the health of others. This property already imposes a desire to equip the workplace with exhaust ventilation, which is not so easy for living conditions. Some adherents of the ABS sect say with blue lips that there is nothing wrong with that, but not everyone believes them, looking into their honest, but sunken and yellowed eyes.
In addition, ABS is a rather capricious material, large shrinkage breaks and warps products during the printing process at the slightest uneven cooling. Any draft will cause delamination of the part, separation from the table and most likely lead to marriage. And this imposes another expensive wish on the workplace: a closed box, preferably with heating of the internal volume. This is especially true when printing volumetric products and when manufacturing parts with exact dimensions. Scale correction should be done in advance in the model or in the slicer. nine0003
For good adhesion to the table, it will need to be heated to at least 90 ℃, and preferably 100-110 ℃, which makes another strict requirement for the printer.
ABS does not tolerate sunlight and exposure to other sources of UV radiation, but this disadvantage can be partially solved by coloring the product, since it is painted well.
Based on the above, ABS can be recommended for:
- printing of functional, mechanically loaded products, nine0016
- printing housings,
- decorative printing,
- manufacture of vessels, tubes and containers,
- printing plastic parts.
PLA is the full name of polylactide. Also the "old man" in the world of FDM printing, but in contrast to the poisonous ABS, it is almost a natural product. It is based on lactic acid extracted from corn, sugar cane, potatoes and other agricultural products. It does not pose any danger of poisoning during printing, on the contrary, it smells pleasantly like fried potatoes, but it tends to degrade during storage, in other words, biodegrade. This fact must be taken into account. After some time, usually a couple of years (there are a number of studies on this topic with opposite conclusions), the product may begin to actively lose its strength and appearance, which already excludes a number of possible applications. It has a lot of improving modifications from various manufacturers of varying degrees of success nine0003
Pros:
material is very easy to print, and therefore especially recommended for beginners,
there is no shrinkage during cooling, the material sticks perfectly to the table even without heating, it is not afraid of drafts, which means that any simple printer will work,
does not require corrections to the dimensions of the part,
strong and hard, practically no springiness, perfectly holds the load in compression, tension and fracture much more than ABS, nine0003
non-toxic,
is available in a wide range of colors including metallic, wood, glow in the dark, iridescent and other complex colors,
is well processed mechanically, well painted, and therefore suitable for the manufacture of decorative products.
Cons::
- the above degradability over time, especially outdoors. with a difference in temperature and humidity, although the situation can be slightly improved by applying a protective coating to the product, nine0016
- very low softening temperature - about 50 ℃, the product will “float” in direct sunlight and even in the shade on a hot summer day,
- brittleness at temperatures below -10℃,
- can occasionally get stuck in hotends when printing, although this does not happen always and infrequently.
PLA is therefore recommended for:
- printing of large items, incl. prototypes and forms,
- print products with precise geometric dimensions, nine0016
- decorative prints, incl. for painting,
- print cases,
- printing of mechanically loaded parts (taking into account the operating time, temperature, etc.),
PETG - polyethylene terephthalate flavored with glycol. A very promising newcomer to 3D printing materials. It successfully combines most of the advantages of PLA and ABS, while devoid of most of the disadvantages of them. Today it can be called a favorite in the general-purpose plastics market for both beginners and experienced printers. nine0003
Pros:
- is simple and not capricious in printing,
- does not emit harmful substances and does not smell when heated,
- does not shrink, which means it does not warp, does not come off and is not afraid of drafts and keeps the exact dimensions of the part without the need correction,
- table temperature from room to 80 ℃, which means it can be printed on almost any printer,
- excellent sinterability, almost never delaminate,
- strength comparable to ABS, while PETG is more flexible, stretchable and resilient,
- is not afraid of water and a number of chemicals, incl. acids, alkalis and solvents,
- UV resistant,
- extremely durable,
- softening point from 80℃,
- non-toxic,
- beautiful glossy surface, gears and other contact parts of medium duty machines,
- high impact resistance,
- wide range of colors, including transparent,
- low price.
Cons:
- requires careful adjustment of print parameters and some getting used to it after ABS and PLA,
- a little “snot” due to high fluidity,
- low adhesion of the surface, which means it is poorly painted, poorly glued (but it washes well ),
- viscous, poorly processed mechanically and even worse chemically, solvents such as DCE and DCM do not smooth the surface, but soften the part, which only leads to loss of shape. nine0016
Thus, PETG can be recommended to any user for the manufacture of almost any product, from artistic to mechanically loaded. The lack of toxicity allows it to be used for dishes, food containers, molds and children's toys.
HIPS is a high strength polystyrene. It was originally meant as an auxiliary plastic for ABS, used as a support. It dissolves quickly and without residue in limonene without affecting the base material. However, it can be used independently, for example, for the manufacture of decorative unloaded products, “high strength” is present here only in the name. nine0003
Pros:
- low density, light weight,
- softness, very easy to machine,
- matt surface that looks good, visually hides unevenness and layers, can be easily painted if necessary,
- high softening temperature (similar to ABS),
- less shrinkage than ABS, making printing a little easier, especially on large parts,
- non-toxic, odorless, food-safe,
- durable,
- not afraid of moisture,
- good color range, but not as rich as ABS and PLA.
Cons:
- requires a high table temperature, from 90 ℃,
- is afraid of drafts and uneven cooling, although not as much as ABS, but care should be taken,
- fragility and low strength, not recommended for use for loaded parts,
- is UV resistant, but can be overcoated. nine0016
HIPS has a rather narrow range of applications, it is decorative products without load (printed and put on a shelf) and support for printing with ABS plastic.
SBS aka Watson, real name styrene butadiene styrene. The same age as PETG in the world of plastics, that is, it appeared on the market relatively recently. Similar to PETG in many ways: easy to print, non-toxic, shrinkage is present, but insignificant and does not affect quality. Does not tolerate ultraviolet light, avoid sunlight or apply a protective coating. Distinctive features: especially transparent and flexible. SBS produces the best lampshades, shades and other transparent elements for lighting products. Solvent-treated surfaces finally get rid of irregularities, acquire smoothness and even greater transparency, imitating glass. nine0003
Pros:
- easy to print,
- low shrinkage for easy printing and dimensional accuracy,
- impact and tear resistance,
- non-toxic, food and liquid compatible,
- waterproof,
- frost resistance,
- excellent transparency,
- beautiful color range, especially for transparent rods,
- easy mechanical and chemical processing,
- flexibility and resilience, even thin-walled products are very strong.
Cons:
- high flexibility, not suitable for machine parts,
- relatively weak adhesion of layers forces to reduce print speed and/or increase nozzle temperature.
- is degraded by UV light.
Excellent for safety glass-look decorative items. Due to its transparency, it is ideal for printing plafonds of lamps and fixtures. nine0003
TPU is a thermopolyurethane, also known as FLEX by some manufacturers, a soft rubber-like plastic. It is used for the manufacture of flexible products: wheels, dampers, gaskets, belts, coasters, toys and even shoes. Extremely tear and impact resistant, heat-resistant, softening point is about 110℃. It cannot boast of ease in printing, it sticks poorly to the table even at a temperature of 80-90 ℃, the layers do not fuse very readily, which limits the printing speed. It is hygroscopic, it is highly recommended to dry the rod before printing, otherwise voids and “pimples” are provided. Doesn't handle retracts well, especially in bowdens, the long flexible bar is very intertwined. nine0003
Pros:
- soft and flexible, hardness varies by version and manufacturer,
- impact resistant,
- tear resistant,
- abrasion resistant,
- waterproof,
- oil resistant,
- indifferent to gasoline, can be used for containers, lids and gaskets,
- heat resistant, works at high temperatures.
Cons:
- difficult to print, requires fiddling with settings and may need to modify the printer, such as the bar feed mechanism,
- low print speed,
- poor adhesion to the table,
- a small selection of colors, most often: white, gray, black.
- Indispensable for the manufacture of flexible "rubber" parts and decorative elements.
NYLON , in Russian nylon, synthetic plastic from the polyamide family. Very durable material on all sides with a very slippery surface and maximum abrasion resistance. Due to this property, it is widely used for the manufacture of mechanical parts operating under high loads and with rubbing surfaces, such as gears, screws, plain bearings, hinges, and so on. At the same time, rubbing surfaces do not need lubrication, which means they do not collect dust and other abrasive, they work even longer than metal ones. Durable, withstands temperatures up to 120 ℃, it would seem an ideal plastic, but no, the pluses are crossed out by a very difficult print. The high degree of shrinkage warps the part when it cools, and the exceptional slip minimizes adhesion to the worktable. As a result, printing something more than a few millimeters in height on consumer printers is very difficult, almost impossible. The edges of the product are bent higher and higher with each layer, come off the table, then the whole workpiece comes off ... Tricks to improve adhesion do not help much: substrate, varnish, glue, thermal adhesive tape, and so on. As if this is not enough - nylon is also extremely hygroscopic, it absorbs moisture from the air quickly and a lot, which makes it cloudy and, when you try to print it in this form, bursts out of the nozzle with explosions of steam with pieces of plastic.
It is necessary to dry thoroughly and for a long time before each printing, and print as quickly as possible so that it does not have time to moisten again. In terms of complexity, it can probably be attributed to professional plastics, for printers with improved characteristics. nine0003
Pros:
- perhaps the most durable plastic available,
- resilient,
- low slip surface, abrasion resistant,
- heat resistant,
- chemical resistant,
Cons:
- very difficult to print, requires printers with an active thermal chamber, heating of the nozzle to 260 ℃ and the bed to 120 ℃, which puts 99% of household printers out of the game,
- high shrinkage, size correction is required,
- need to dry thoroughly before each use,
- elastic, must be taken into account when designing parts,
- high price,
- only two colors: white (translucent) and black.
At the amateur level, you can afford to print several small flat gears or hinges, with a thickness of 5-6 mm, and even then it will not work right away. But unlike rubbing pairs made of other materials, nylon ones will last almost forever and in almost any conditions. Sometimes the pain is worth it. nine0003
ASA is acrylonitrile styrene acrylate, a more expensive analogue of ABS that is UV and weather resistant. Rigid, resistant to oils, acids, gasoline, diesel fuel and similar liquids. Does not yellow over time. Used for outdoor parts such as cars, outdoor furniture and decor. In terms of printing complexity and in everything else, it is approximately equivalent to ABS with all its pluses and minuses. It has the same shrinkage, so the models need to be sized. With excellent mechanical properties and chemical resistance, it remains a household plastic that can be printed on almost any printer, without forgetting, however, about the specifics. nine0003
Pros:
- strong, hard, durable,
- UV resistant,
- operating temperature -40℃ to 90℃,
- can be easily machined and smoothed with an acetone bath,
- stains well.
Cons:
- capricious in printing, warps from uneven cooling, afraid of drafts,
- does not stick well to the table, even heated to 110℃, nine0016
- during printing emits harmful gases, which, moreover, smell unpleasant, it is advisable to use a hood.
- small assortment,
- is at least twice as expensive as ABS.
It makes sense to use for outdoor products such as automotive parts, outdoor lighting, decorative products, gardening tools, window and balcony elements, wearable accessories and so on. It will last for a long time in any conditions without losing its valuable properties. nine0003
PP - polypropylene. Strong, wear-resistant, not afraid of water and most chemicals, durable. Due to this, it is often and happily used in industry, but difficult for 3D printing. Problems are poor adhesion to the table and a high degree of shrinkage, which tends to bend inward and tear off the surface when printing. He often succeeds. Requires high table and extruder temperatures. It can be attributed to professional plastics, which are better not to use at home without special need. nine0003
Pros:
- high strength,
- low slip, low friction wear,
- chemical resistance,
- non-toxic.
Cons:
- complex printing,
- high requirements for printers (temperature, heat chamber),
- large shrinkage,
- does not tolerate frost, it is better not to use at negative temperatures.
Suitable for functional parts working indoors (apartment, office, workshop) or outdoors in a warm climate. However, it can be quite successfully replaced by more flexible materials with similar characteristics. nine0003
PC - polycarbonate. Controversial plastic. On the one hand, it has high strength, especially impact, does not lose its properties in a wide temperature range from -140 to +150 ℃, which makes it unique in some senses, on the other hand, it does not tolerate ultraviolet and humidity, which nullifies its chic capabilities for outdoor applications. Printing is not easy, it requires temperatures up to 310 ℃ from the nozzle, and up to 120 ℃ from the table, which not every “household” printer can handle. Afraid of drafts, shrinks when cooled, warps and breaks away from glass at the first opportunity. A closed chamber is recommended, preferably an active one. It makes sense to use in cases where extremely high temperature and impact resistance is required. It is well processed mechanically - sharpened, drilled, skinned. Easy to paint, which can partially correct the UV problem..
Pros:
- high strength, especially impact,
- huge operating temperature range,
- low slip coefficient, low friction wear,
- easy mechanical post-processing,
- chemical resistance, 901
Cons:
- complex printing,
- high requirements for printers (temperature, thermal chamber),
- high shrinkage,
- hygroscopicity,
- is degraded by UV light.
POM - polyacetal. This is a truly professional plastic, nylon at maximum speeds. It outperforms its little brother in every way, including printing difficulty. It requires more temperature for both the nozzle and the table, moreover, those that household printers can very rarely provide: up to 250 and 130 ℃, respectively. Heat shrink is higher than nylon and ABS combined. An active thermal camera is already required, even for printing the smallest details. Hygroscopic, thorough drying before printing is essential. Suffering is justified by the highest strength, low coefficient of friction, high softening point, as much as 135 ℃. nine0003
Pros:
- very strong,
- low coefficient of friction, high wear resistance, excellent for making mechanical gears,
- frost resistant, can work at temperatures down to -50 ℃.
Cons:
- very tricky to print, requires drying, active thermal chamber, high temperature of the extruder and table,
- professional printers are required for printing.
Direction of use is the same as nylon, but it makes sense if the strength and other properties of nylon are not enough. nine0003
PMMA - polymethyl methacrylate, popularly called plexiglass. Another professional plastic with interesting properties, but difficult to print. It is transparent, resistant to UV, atmosphere, water and many chemicals. It is well processed mechanically, easily and firmly sticks together with itself and with other materials.
Pros:
- transparent, durable outdoors,
- non-toxic,
- is easy to process. nine0016
Cons:
- high temperature printing, up to 255℃,
- cures too quickly, requiring high print speed and precision,
- Shrinkage on cooling is not very large, but there is. Can be a problem given the high setting speed.
It is used in the same place as ordinary plexiglass: lamp shades, light boards, plates, housings, pipes and fittings of complex configuration. Can be used in contact with food and in medicine. nine0003
PEEK - polyetheretherketone. Professional hard plastic. The high melting point is both its plus and minus: on the one hand, parts made from it can operate at temperatures up to 150 ℃, which is inaccessible to most plastics, on the other hand, the extruder needs to be heated up to 410 ℃, and you can’t look for such household printers. Even a different nozzle is required, the standard bronze one is not good.
Pros:
- very strong, performs well under heavy mechanical loads,
- chemically resistant,
- durable,
- non-toxic,
- very high softening point,
- resistant to abrasion, can work in kinematic pairs.
Cons:
- high printing temperature,
- active thermal camera required,
- expensive.
It is used in especially critical parts and devices that experience high mechanical loads and high heating temperatures. Printing requires industrial equipment. Due to its high strength, chemical resistance and lack of toxicity, it is used in medicine, in particular for the manufacture of prostheses and frameworks in dentistry. nine0003
Ceramo - plastic imitating ceramics. Similar to ceramics in everything, in feel, in weight, just as hard, but brittle. It is well processed mechanically, you can go through the sandpaper to hide the traces of printing, and then it is almost indistinguishable from real ceramics. Non-toxic, withstands boiling water, Ceramo cups and teapots can be used for their intended purpose. With caution, you can print on household printers, since the print temperature is quite democratic, about 220 ℃. The main thing is not to go too far, that is, a bar, when printing, because it is also almost porcelain in terms of fragility. nine0003
Pros:
- almost identical to real ceramics,
- beautiful and pleasant to the touch,
- good layer sinterability,
- heat resistant,
- non-toxic,
- printable on household printers, with some restrictions,
- only white,
- is easy to machine.
Cons:
- is very fragile, however, this is a plus for imitation of ceramics, nine0016
- is not suitable for printers that bend the bar a lot when printing,
- requires careful handling at all stages, from storage to use of the finished product,
- is quite expensive.
It is used, as the name suggests, for the manufacture of "ceramic" products: cups, teapots, candlesticks, figurines, lamps and other decor. Not intended for mechanical parts under physical stress.
WAX One of the few materials used for the manufacture of intermediate products. Details printed with wax are poured with gypsum, after which it hardens, it is heated and melted out of the mold obtained in this way. In the future, the form can be filled with any material to obtain the final part, including metal. Before pouring, the printed model can be subjected to simple post-processing, for example, removing traces of printing, for which it is enough to gently heat the surface of the product with a hot air gun. Printing with wax is easy and enjoyable, and any 3D printer will do. nine0003
Plus:
- Easy printing, low temperature of the extruder and table,
- Good sintering of layers,
- High accuracy,
- Uniqueness,
BESSIONS:
- Small shrink , requires care when handling,
- is afraid of high temperatures.
Used in mold making for prosthetics, jewelry, prototyping and so on. nine0003
PVA is a polyvinyl alcohol, water soluble material. It is used exclusively as a support when printing complex objects with other plastics, such as ABS or PETG, it is enough to immerse the printed product in warm water for a few minutes and a finished clean model will remain without traces of supports. Allows you to print composite products from several objects in the assembly. You will need a printer with two extruders, which is now no wonder and not uncommon even in the domestic segment. nine0003
Pros:
- water-soluble,
- non-toxic,
- good adhesion to the table at any temperature, which allows it to be used in tandem with any plastic,
- no smell when printing.
Cons:
- requires a printer with two extruders,
- cannot be heated above 210℃,
- is hygroscopic, care must be taken when storing and dry before use,
- is expensive.
Application due to properties: as a support for complex models. As an independent material, it does not make sense, since it decomposes quite quickly even from atmospheric moisture. Due to the high price, it should be used in case of emergency, when otherwise it is very difficult to print the part or it is very difficult to get rid of the supports without the danger of damaging the product.
Cleaning - cleaning material for 3D printer heads. For the manufacture of products is not used. It is used by perfectionists when changing plastic, especially from one type to another, in order to ensure that the remnants of the previous one are removed from the nozzle. It works like this: the head is heated to the printing temperature of the removed plastic, a cleaning filament is manually fed in a few centimeters until it exits the nozzle in an even jet, then the hot end turns off, cools down a bit and the cleaning plastic is removed with the remnants of the previous solidified material. In real life, it is used extremely rarely, usually when changing, the old plastic is simply pushed out with a new one until it is completely replaced. To clean the nozzle from dust and other foreign substances, you can use any ordinary plastic using the same technology: heat it, cool it a little, remove it along with the garbage. Examine the result, it is possible to repeat several times. nine0003
Composite materials
Unlike the above monocomponent plastics, composite materials are a mechanical mixture of the base plastic and additives to impart additional properties to the material. Typically, two goals are pursued: changing the appearance for decorative plastics and improving physical or chemical properties, strength, hardness, resistance to ultraviolet, liquids, and so on. Most often, PLA and ABS plastics act as the basis, as the most common and easy to manufacture, print and operate. Composite materials are available in a great variety, here are just a few examples. nine0003
Metal-filled PLA
The filler is usually copper, brass, bronze, less often steel and iron. The proportion of metal in the filament ranges from 5 to 40%; the more, the closer the appearance of the product to the corresponding metal, but the lower its strength. In general, decorative composites cannot boast of high strength, their task is only to imitate metal and look beautiful. Functional parts designed for load are not recommended to be printed from this type of plastic. But grinding and polishing after printing is recommended, then the product will acquire the most chic look, up to indistinguishable from a real casting. Plastic with copper iron filler becomes covered with a patina over time, and iron with a rust coating, which makes them even more authentic. nine0003
Print parameters are similar to normal PLA, but may differ slightly, you should be guided by the manufacturer's recommendations. It should be borne in mind that metal particles contribute to the rapid wear of the nozzle, especially steel and iron. You will have to get used to the fact that the nozzle is a consumable item, and vigilantly ensure that its wear does not have time to affect the print quality. As an option, use steel and titanium nozzles, they are more tenacious, but they transfer heat worse, you will have to slightly adjust the heating temperature and print speed. nine0003
Wood-filled PLA
Mixture of 70% plastic and 30% wood fibre. The appearance of the filament varies depending on the type of wood: beech, birch, cedar, pine, and so on, and the shade of the printed product also depends on the temperature of the extruder, the higher, the darker. Finished models are very similar to real wooden ones, they smell the same, they feel the same in the hand, they are processed in the same way. Both the rod and the products have an exclusively decorative purpose, because they are very fragile, and care must be taken when handling them. nine0003
Carbon-filled PLA and ABS
Carbon fibers are added to plastics to increase the strength of the material. In addition, carbon significantly reduces shrinkage during plastic cooling, which greatly facilitates ABS printing and reduces the number of rejects. The finished product is stronger, lighter and dimensionally more accurate than that made from pure material. The print settings are the same as the base material. The disadvantages include increased abrasiveness (which forces you to monitor the condition of the nozzles and periodically change them to new ones) and a high price. nine0003
PC/ABS
A blend of PC and ABS that combines the stiffness, strength, especially impact and heat resistance of polycarbonate with the relatively easy and familiar handling of ABS. The big advantage is the ability to print in most consumer printers, which is almost impossible to achieve with a pure PC. Reduces heat shrinkage of ABS, which is also a big plus for accuracy and ease of printing. Composite is several times more expensive than ABS, but sometimes it is justified. The print options are similar to conventional ABS. nine0003
Pins
Novice “printers” often get lost in the variety of materials, want to try as quickly as possible and as many options as possible, spend a lot of time and effort on it, often making wrong conclusions and even experiencing anger and disappointment if something is not right. it turns out. In this article, we briefly described the pros, cons of each type of plastic and the possible difficulties that arise with one or another material. We hope that our work will help with the choice of the most suitable filament for a particular task, the printer and the qualifications of the master, will allow you to quickly get used to it and enjoy printing. Experienced users, on the other hand, will learn about unusual and professional plastics and decide whether they are worth paying attention to and whether they are ready to deal with them. nine0003
FAQ
What is the best plastic to start with in the world of 3D printing?
The simplest and easiest to work with is, of course, PLA. No wonder most often the coil with this plastic is attached to the new printer. There are settings for it in any slicer, any, even the simplest and most inexpensive printer, can withstand the parameters. It is very difficult to spoil a part from PLA even the first time, which, as you know, is lumpy.
What plastic do you recommend for everyday use? nine0134
There are as many opinions on this as there are typical everyday plastics, and it's up to you, but we recommend taking a closer look at PETG, it is optimal for both a beginner and an experienced user. Durable, not smelly, not capricious in printing, durable, resistant to many destructive factors. However, it is not suitable for all tasks, read above about the shortcomings and limitations.
Is it worth spending time, effort and money printing with professional plastics?
If the properties of ordinary household plastics are critically small for your tasks, then of course yes. For example, if you are manufacturing quadcopters, the bodies and protective bumpers of which must be as strong and light as possible, then you will need a carbon fiber composite.