Strongest 3d printing material
What is the strongest 3D printing material?
Timon Rijnaarts20 May 2022
Guide
It won’t be an overstatement to say that most of you reading this article have often wondered ‘which 3D printing material is the strongest?’ It is surely an intriguing question. One that everyone wants to know the answer to. Whether you are a hobbyist or an expert, most of your projects need materials that are strong and tough. With this article, we aim to compare the toughest 3D printing materials and provide you with an answer.
But this also begs the question of what strength means for 3D printing materials?
What does ‘strong’ mean when it comes to 3D printing?
Well, strength in 3D printing materials can be defined in a number of ways. Some of them include hardness, impact resistance, compressive strength, and so on. However, two of the most commonly understood types of strength that most people care about are tensile strength and flexural strength. That is how much a material can be stretched and bent respectively. In the following overview, we will list the MegaPascal (MPa) of pressure that each material can endure. The higher these numbers, the ‘stronger’ the material when subjected to those particular stresses. The numbers we use are based on the technical datasheets for Ultimaker materials. Materials from other brands may vary.
Best FFF/FDM materials for printing strong parts
For our comparison of the strongest 3D printing materials, we will be considering seven different materials. Namely, Polylactic Acid (PLA), Tough PLA, Acrylonitrile Butadiene Styrene (ABS), Polycarbonate (PC), glycol-modified polyethylene terephthalate (PET-G ), Nylon, and Polypropylene (PP). Which one is best for you depends on your needs, budget, and a number of other factors. Later in this article, we will discuss specific applications and which material may be best for them.
PLA filament
PLA, or polylactic acid, is a highly versatile and popular FDM 3D printing material. Its popularity stems from the fact that it is simple to print, easily available at low prices, and comes in a variety of colors. For that reason, it’s likely the first material most people will print with.
PLA is not usually chosen for its strength properties, due to the material being brittle. If you are printing on a budget, PLA can be appropriate in some cases but if your part needs to flex before breaking, you are usually better off using a different material.
PLA filament properties
Tensile Strength: 53-59 MPa
Flexural Strength: 97-101 MPa
Tough PLA filament
Tough PLA is a tougher version of regular PLA or Polylactic Acid. It combines the ease of printing that one can expect from PLA and takes away the main disadvantage of PLA: its brittleness. For this reason, it’s ideal for functional prototypes that need a bit of flex.
Tough PLA is not as brittle as regular PLA, it exhibits higher tensile strength than ABS, is easier to print than ABS, and is compatible with the water-soluble support material PVA.
Tough PLA filament properties
Tensile Strength: 45-48 MPa
Flexural Strength: 83-96 MPa
ABS filament
ABS, also known as acrylonitrile butadiene styrene, is a popular thermoplastic polymer. It is well-known for its impact, chemical, water, and heat resistance. It also has outstanding high and low-temperature performance, which makes it perfect for automotive components. ABS also has good electrical insulation properties, making it a good choice for the housing and casing of electrical parts.
Furthermore, ABS is comparatively cheaper than most materials and is relatively easy to post-process. As a result, it is an excellent material for mass production and is used in a wide range of common products. The fact that ABS is simple to post-process also means it can be bonded and painted.
ABS filament properties
Tensile Strength: 34-36 MPa
Flexural Strength: 60-61 MPa
Polycarbonate (PC) filament
Polycarbonate filament (PC) is a stiff thermoplastic polymer that is resistant to heat and chemicals. It is a high-strength material designed for use in harsh environments and technical applications. It has good heat deflection due to its high glass transition temperature and it is typically available in a version with improved impact resistance as well.
Polycarbonate filament has numerous applications in everyday life. Polycarbonate, unlike plexiglass, does not shatter. It bends and deforms similarly to hard rubber until it finally breaks. It also has excellent optical clarity.
Polycarbonate can be difficult to work with due to its high temperature resistance, meaning that warping can be an issue. Choosing the correct glue and avoiding sharp angles in your parts can help you print successfully with this material.
Polycarbonate filament properties
Tensile Strength: 43-65 MPa
Flexural Strength: 89-114 MPa
PETG filament
PETG, or Polyethylene Terephthalate Glycol, is a thermoplastic polyester that has been chemically modified with the addition of Glycol to limit crystallization and improve toughness. The inclusion of glycol improves PET’s , durability and formability for production. It has a strong impact and abrasion resistance and can sustain higher temperatures compared to PLA.
Because of its excellent properties and relatively low price, PETG is commonly used in 3D printing. It is a good engineering-grade material that can be used in place of ABS. It also has less of a tendency to warp, which means it's easier to print accurate parts.
PETG filament properties
Tensile Strength: 38-44 MPa
Flexural Strength: 75-79MPa
Nylon filament
Nylon for 3D printing is commonly found in several forms: PA6 and PA6/66, which are stiffer versions of Nylon, and PA 12, which is a flexible type of Nylon. Nylon has helpful qualities that make it an appealing material for 3D printing. Nylon is both strong and durable, as well as flexible. This characteristic is beneficial when printing pieces with thin walls. Furthermore, nylon has a high melting point with a very low coefficient of friction, allowing it to be used in the printing of functional interlocking items such as gears.
One major disadvantage of nylon as a 3D printing material is that it is highly hygroscopic, which means that it absorbs moisture. This can make it difficult to achieve the expected performance when printing.
Nylon filament properties
Tensile Strength: 63-65 MPa
Flexural Strength: 63-83 MPa
Polypropylene (PP) filament
Polypropylene (PP) is a widely used plastic that may be found in almost any household. It is the material of choice for storage and packaging applications as well as many traditional forms of manufacturing like injection molding. The popularity of PP is due to its high chemical resistance, heat resistance, impact resistance, and flexibility.
Its qualities make it perfect for applications such as food packaging, outdoor exposure, chemical storage tanks, and even medical applications like prosthetics, among others.
Polypropylene Filament Properties
Tensile Strength: 10-12 MPa
Flexural Strength: 13-15 MPa
Best settings for printing strong parts
Wouldn't it be great to be able to print stronger parts even without changing the material you’re using? Luckily, it is possible. The key is to optimize your settings. To get the most out of your printer and material, you must customize the settings you use for not only each material, but also each part.
Below are some of the best settings to modify to strengthen your part:
Infill type and density: Infill type and density are important contributing factors toward the strength of a printed part. The greater the infill density, the greater the strength. However, a high infill density is not usually advised as it uses up a lot of material and takes more time to print. To increase the strength of a part without increasing the density, you can also change the infill pattern depending on the part functionality. For example, in compression strength tests, triangle/grid infill shows higher compression strength versus cubic and gyroid infill patterns
For most visual prints, you can use an infill of around 20 percent, but for stronger parts, try going over 50 percent. An alternative is to use modifier meshes to selectively generate higher infill density in the areas where the stresses will be the highest.
Part Orientation: Part orientation may not be on your checklist of steps to ensure a stronger print, but it is crucial. Tensile strength is weaker along the Z-axis in 3D printing (typically 40-70% of the strength when compared to the XY-axis), especially in tall and thin printed parts. As a result, you must carefully orient the part to match the required axis of strength. While doing this, you will also have to take into consideration the support structure and a balance will have to be found based on what matters most in that particular part.
Shell Thickness: The outer surface thickness of the part is referred to as its shell thickness. Generally speaking, the thicker the shell, the stronger the part. Based on this, you can decide the shell thickness you need for your part. A shell thickness which is double the layer thickness is usually a good place to start.
Post-processing for stronger parts
The work is not finished once a part is printed. It’s possible to increase the strength of your printed part with a little extra work.
Annealing: Semicrystalline materials like Nylon, PET, PEEK and some forms of PLA can be annealed. This is thermal treatment where the material is fully transformed in its crystalline state, giving you a stiffer and stronger part.
Applications for strong printed parts
Strong printed parts have a wide range of applications spread across industries and functions. The following are examples of applications where strength is critical along with which materials you may want to consider using:
Functional prototypes: Functional prototypes are meant to test and demonstrate the final functionality of the product being developed. Functional prototypes are rigorously tested so that accurate data can be gathered on the behavior of the part during real-world performance. This means that the characteristics of the prototype and the final product must match so that the data generated during the testing phase can be trusted. Because functional prototypes are prone to wear and tear, they must be robust. For this application, tough PLA and PET-G filaments are commonly used. Although, any material can be appropriate as long as it shares the properties of the material which will eventually be used for mass production.
End-Use Components: When printing end-use parts, improved strength characteristics greatly increase the number of end-use applications that 3D printing can be used for. Polypropylene is commonly used for parts such as prosthetics, polycarbonate is used for eyewear and electronic casings, and polypropylene, PET-G, or PEEK are often used for applications requiring chemical contact.
Manufacturing Aids: These are the tools and devices that assist in the manufacturing of parts. These are also used during the assembly stage to speed up the assembly of parts. Stronger prints are recommended for this application because they can experience a lot of wear and tear with repeated use. Nylon and PET-G are often appropriate materials to use here.
We hope this information will help you make a better decision on material selection. Visit the Ultimaker marketplace to find the material that’s right for your application.
Go to Ultimaker Marketplace
Choosing between PC, nylon, TPU, and others
Good 3D printing materials tend to offer a mix of desirable characteristics. These characteristics can include printability, durability, chemical resistance, temperature resistance, and flexibility, to name just a few. Chief among these desirable properties, however, is strength: nobody wants their 3D printed parts to break, and material strength is one of the best ways to ensure this doesn’t happen.
Take a look at the filament market and it’s easy to see that the strongest 3D printer filaments out there command a higher price than their weaker counterparts. This is partly due to the cost of the stronger raw materials, and partly due to the increased use of 3D printing as a tool for end-use manufacturing, with real functional parts requiring greater strength than prototypes. Demand for high-strength materials is growing, and many manufacturers have been happy to provide solutions.
This article looks at some of the strongest 3D printer filaments available for users of FDM 3D printers. It is by no means an exhaustive guide to high-strength materials, but it takes a look at some of the most popular high-strength filaments in the consumer sphere, while also touching on some professional-grade materials reserved for advanced users.
Strong 3D printing filament is in high demand, but “strength” can actually mean a few different things in this context. When comparing filaments, you’ll see terms like tensile strength, impact strength, tear strength, and flexural strength — all of which can be measured using standardized strength tests — in addition to more general terms like durability and toughness.
These different terms are needed because materials can be strong or weak in different ways. For example, try to imagine the relative strength of a glass bottle and a piece of chewing gum. If you were to hurl the two objects at a wall, the glass would obviously break and the chewing gum would survive almost unscathed. But you could much more easily pull the chewing gum apart with your hands than you could the glass bottle.
All of the various strength-related attributes are important when it comes to choosing and buying 3D printer filament. However, two types of strength are generally prioritized over any other. These are tensile strength and impact strength.
Tensile strength
Used to indicate the ultimate strength of a material or part, tensile strength can be defined as the ability to resist breakage when under tension, i.e. when being pulled or stretched.
Tensile strength is the most widely used indicator of strength for 3D printed parts, because it indicates a material’s suitability for load-bearing or mechanical applications. It is expressed in megapascals (MPa) or, in the United States, in pounds per square inch (psi), and values are determined by performing a tensile test: literally pulling a piece of the material apart and using a tensometer to record the exact degree of tension at which the material breaks. It is a key metric for almost any functional printed part.
At the low-cost consumer level, the strongest 3D printer filaments in terms of tensile strength include polycarbonate (PC), polyethylene terephthalate glycol-modified (PETG), and polylactic acid (PLA). Weak materials include thermoplastic polyurethane (TPU) and acrylonitrile butadiene styrene (ABS).
Materials with good tensile strength are harder to break when pulled
Impact strength
Another key indicator of strength is impact strength. Synonymous with toughness, impact strength is the ability of a material or part to absorb shock and sudden impact without breaking. It is an important material property for items like safety equipment and children’s toys.
Impact strength is defined as the amount of energy — generally expressed in kilojoules per square meter (kJ/m2) — that the material is able to absorb without breaking. Brittle materials have a low level of impact strength and can break more easily when subjected to sudden impact. However, materials can have a high impact strength and a low tensile strength, and vice versa.
Unfortunately, due to the many different ways of testing for impact strength, it can be difficult to compare the exact toughnesses of two different filaments side by side. Two different filament manufacturers might use different testing methods and even different units of measurement.
At the consumer level, the strongest 3D printer filaments in terms of impact resistance include ABS filament, PETG filament, PC filament, and flexible filaments like TPU. One very weak material in terms of impact strength is PLA, which can easily shatter if it is dropped or struck.
Other strength metrics
Beyond tensile strength and impact strength, some notable terms you might find on a material’s data sheet include:
Flexural strength: Refers to how well a material can resist breakage when it is bent or under load; expressed in megapascals (MPa)
Tear strength: Refers to how well a material can resist the growth of cuts when it is under load; expressed in kilonewtons per meter (kN/m)
Elongation at break: Relates to tensile strength and refers to how much a material stretches before it breaks when under tension; expressed as a percentage
Recommended reading: 5 options to get strong parts with 3D printing
Approx tensile strength: 70 MPa
One of the strongest FDM 3D printing materials — in terms of both tensile[1] and impact strength — is polycarbonate (PC). In fact, polycarbonate filament would likely be one of the most popular printing materials were it not so difficult to print.
Advantages of polycarbonate, besides its excellent tensile and impact strength, include its temperature resistance and its suitability for printing transparent parts. An obstacle to the printing of PC is its very high melting point and the very high temperatures required to print it. Extruder temperatures of at least 260 °C are required, with some formulations needing more than 300 °C, which is beyond the capabilities of consumer-level desktop 3D printers. A bed temperature of around 100 °C is recommended.
Some brands of PC contain additives that reduce the material’s melting point, but these additives can also compromise the material’s strength and heat resistance, making them less suitable for end-use parts such as automotive components.
PC 3D printing is usually limited to non-budget systems that can print at high temperatures and extract the best strength properties from the material. However, even these systems can struggle to control the material’s proneness to warping.
Popular PC filaments include Raise3D Premium PC, Polymaker PolyMax, and 3DXTech 3DXMax PC.
Approx tensile strength: 50–80 MPa
Another strong filament in both the tensile and impact departments is nylon (PA). Although not as robust as PC, nylon filament is marginally easier to print, requiring an extruder temperature of around 250 °C and a heated bed set to around 80 °C.
Nylon is perhaps more often associated with selective laser sintering (SLS), where it is used in powder form to make industrial parts and prototypes. However, nylon FDM 3D printer filament is widely available and typically comes at a lower price point than PC. Compared to PC, it is slightly more flexible, which may be desirable for certain functional parts. Other advantages of nylon filament include its excellent durability, surface smoothness, and layer adhesion.
Although most desktop printers can process nylon filament, the high-strength material has drawbacks. For example, it is highly hygroscopic and prone to absorbing moisture, which can cause a variety of printing issues, such as the formation of bubbles in the nozzle. Like PC, nylon is also susceptible to warping as it cools down.
Popular nylon filaments include MatterHackers Pro Series Nylon, Ultimaker Nylon, and ColorFabb PA.
Approx tensile strength: 20–50 MPa
Though not usually thought of as high-strength materials due to their very low tensile strength, flexible filaments like thermoplastic polyurethane (TPU) actually offer a very high level of impact strength, making them suitable for shock-absorbing printed objects and functional parts like protective enclosures. Naturally, TPU has a very high elongation at break compared to more rigid materials, and the material also has good abrasion resistance and chemical resistance. Its tensile strength, however, is very low, making it unsuitable for mechanical parts.
Most desktop 3D printers can print TPU and other varieties of thermoplastic elastomer (TPE), with a hot end temperature of around 230 °C required. However, note the best 3D printers for printing flexible filaments have direct-drive extruders, as Bowden extruders can suffer filament tangles.
Popular TPU filaments include NinjaTek Cheetah TPU, Polymaker PolyFlex, and Fillamentum Flexfill.
Recommended reading: TPU print settings explained
In professional and industrial settings, many FDM users are now turning to high-performance materials like PAEK (PEEK and PEKK) and PEI (ULTEM) for the production of end-use parts, especially in demanding industries like automotive and aerospace. When filament strength is the highest priority, these engineering-grade materials are far better than ordinary products like PLA filament.
High-performance plastics offer a very high level of tensile strength. PEEK filament, for example, can have a tensile strength as high as 100 MPa, notably higher than PC filament and significantly higher than ABS filament. Materials in the PAEK family also have very good impact strength; PEI is slightly less tough, but is typically much more affordable than PAEK filament.
The obvious drawback of high-performance polymers is that they cannot be printed on beginner-level printers or even mid-level desktop machines. They demand much higher temperatures (nozzle, bed, and enclosure) than regular materials, are more expensive, and sometimes require annealing to maximize their mechanical performance.[2]
Popular high-performance filaments include 3DXTECH ThermaX PEEK and Markforged ULTEM 9085.
The strength and stiffness of thermoplastics can be increased by mixing them with reinforcing additives, creating what is called a composite filament. Common additives include chopped carbon fiber and fiberglass.
Composites are popular in FDM 3D printing because they enable users to incorporate strong materials like carbon fiber without adjusting the printing process. Because there is a greater amount of thermoplastic than additive in the composite, the material can still be melted and extruded like an ordinary filament.
Reinforced composites can have a high level of tensile strength. For instance, MatterHackers NylonX (a composite of nylon and carbon fiber) has a tensile strength of 100 MPa.
Note, however, that FDM carbon fiber filaments have limits on their strength, because the chopped fibers mixed into the material are randomly oriented. Advanced composite printing technologies, such as those developed by Markforged and Desktop Metal, are able to print continuous fibers, resulting in much stronger parts.[3]
Choosing the strongest 3D printer filament for your needs comes down to two key factors: the type of strength required and the level of strength required (that is feasible with the printing hardware available).
If the parts need to withstand constant loads and stresses, then materials with a high tensile strength should be prioritized. These include PLA and PETG at the cheaper end, materials like PC in the middle, and composites or high-performance polymers — offering the very highest levels of tensile strength — at the premium end.
If the parts need to withstand sudden impact, then materials with a high impact strength or toughness should be prioritized. Such materials include ABS and TPU at the consumer end and high-performance polymers at the premium end.
In general, materials like nylon and polycarbonate are favored by many FDM users because they offer a good balance between affordability, tensile strength, and impact strength.
[1] Tanikella NG, Wittbrodt B, Pearce JM. Tensile strength of commercial polymer materials for fused filament fabrication 3D printing. Additive Manufacturing. 2017 May 1;15:40-7.
[2] Yi N, Davies R, Chaplin A, McCutchion P, Ghita O. Slow and fast crystallising poly aryl ether ketones (PAEKs) in 3D printing: Crystallisation kinetics, morphology, and mechanical properties. Additive Manufacturing. 2021 Mar 1;39:101843.
[3] Yang C, Tian X, Liu T, Cao Y, Li D. 3D printing for continuous fiber reinforced thermoplastic composites: mechanism and performance. Rapid Prototyping Journal. 2017 Jan 16.
What is the most durable material for 3D printing?
3DPrintStory     3D printing process     What is the most durable material for 3D printing?
While the 3D printing process seems like a great alternative to traditional manufacturing methods, the parts produced can be fragile and unusable. As a rule, this is the result of using standard materials that are not designed for strength and durability. But there is a solution: use durable materials! Durable 3D printing materials can greatly enhance your options, as you can print parts and assemblies for small projects without fear of breakage.
In this article, we'll take a look at the three most durable types of 3D printing materials. However, before that, we will take a closer look at what strength means in terms of filament materials.
What is strength and how do we evaluate it?
The strength of a material can be measured and evaluated in different ways. In this article, we will mainly use tensile strength (stress before something breaks). We will list the tensile strength of each 3D printing material in pounds or pounds per square inch (PSI).
Despite the obvious number of pounds the material can support, there is still a margin of error depending on how the part was printed. We've compiled research from a variety of sources to make sure these three materials are the strongest.
You must also understand that the material itself is not the only factor that affects the strength of the finished product. The design itself, post-processing and the 3D printing process also affect the strength of the part.
Polycarbonate
Polycarbonate (PC) is considered by many manufacturers and reviewers to be the strongest 3D printing filament available. In particular, it is possible to achieve high strength of polycarbonate products by 3D printing with an all-metal hot end and a 3D printer in a case that is isolated from the influence of the external environment.
Some Numbers
Airwolf 3D has come to the conclusion after many filament tests that polycarbonate is the best choice of durable filaments for desktop 3D printers. They were able to hang up to 685 pounds on a polycarbonate printed hook and found that this material had a tensile strength of 9800 psi. In contrast, the same part printed in PLA could only support 285 pounds.
Using a similar test, MatterHackers studied the tear strength of this type of thread, as well as a number of other materials. They were able to hang an average of 409 pounds on the polycarbonate hook, while the PLA parts had a significantly lighter average weight of just 154 pounds.
Finally, renowned 3D printing YouTuber Thomas Sunladerer reviewed several polycarbonate materials and gave very positive feedback on the strength of the material.
3D printing with polycarbonate
It is worth noting that the quality of 3D printing with polycarbonate is not very good. Compared to other materials, protrusions and small details may not turn out as well as using the same PLA.
According to Rigid.Ink, polycarbonate is mostly sold in clear. This 3D printing material has excellent heat resistance as well as impact resistance. But note that you will have to print at high temperatures. As mentioned above, it is better to use an enclosed 3D printer and a solid metal hotend.
Pros of polycarbonate : extra strong, excellent thermal and impact resistance.
Cons of polycarbonate : does not cope well with protrusions and small details of a 3D model, requires a body and an all-metal hot end, a limited number of colors.
Nylon
Next on our list of durable 3D printing materials is nylon. This material is considered by many to be the most reliable for desktop 3D printers. Nylon is inferior in strength to polycarbonate, but still clearly stronger than other competitors such as PLA and ABS.
Some numbers
A hook printed with nylon (910) thread had a breaking strength of 7,000 psi, while the same ABS hook only had a strength of 4,700 psi, according to Airwolf 3D. Airwolf 3D also noted that the nylon filament-printed clip holds 485 pounds.
MatterHackers posted similar results and noticed that a hook printed with their NylonX material can hold an average of 364 pounds before it breaks. Rigid.Ink also reviewed some nylon threads and gave them a four out of five rating for strength and a five for durability. For comparison: the strength and durability of PLA is three conventional units.
Nylon 3D printing
Nylon is slightly easier to print than polycarbonate, but it's still not PLA. Nylon filament is quite hygroscopic, so it must be kept dry and requires a high printing temperature of 220-270°C. This material is prone to slight warpage, but is also resistant to impact, fatigue, and high temperature.
Nylon pros: impact resistance, fatigue resistance, heat resistance, easier to print than polycarbonate.
Nylon 9 cons0042 : hygroscopic, warping, very high hot end temperature required.
Composites
Finally, composite threads, although not essentially a single material, can be extremely strong. Composites are threads with certain additives that affect the properties of the material, including to increase strength. The names of these threads usually have the words "pro", "reinforced" (reinforced) or "infused" (infused), since they are usually a mixture of different materials.
For this reason, it is impossible to assess where the composite fibers are compared to the two previous materials. Some composites, such as Carbonyte, can compete with nylon threads for strength, while some composites are less durable.
It all depends on what the composite thread consists of. Durable is usually a high strength material such as nylon impregnated with another high strength material such as carbon fiber or glass.
Speaking of carbon fiber, this is also a very strong filament that is sometimes used for 3D printed bicycles. However, some composite fibers are stronger than many pure carbon fibers, so they are not in the top three, but deserve special mention as composite fibers.
Some numbers
We will use carbon fiber nylon and glass fiber nylon threads as examples. MatterHackers has determined that hooks printed on these materials can hold an average of 349and 268 pounds respectively.
Rigid.Ink gave the fiberglass nylon filament four out of five ratings for strength and five for durability. They also gave the carbon fiber nylon a five out of five rating for both strength and durability. In comparison, PLA and ABS were in the top three for strength.
3D printing with composites
Composites vary in the way they are 3D printed, but they are generally relatively similar to their base material. Durable composite fibers are usually made from nylon, so you'll have to print at fairly high temperatures. These threads are also quite expensive.
Advantages of composites : This is a combination of several materials to achieve the best possible properties, durable.
Cons of composites: Expensive, requires high 3D printing temperatures.
3D printing material comparison
3D printing material comparison
3dunitprint2022-02-07T14:43:04+03:00
3dunitprint Knowledge base 0 comments
ABS - PLASTIC
Acrylonitrile butadiene styrene (ABS) is one of the most popular plastics. It is an easily accessible, durable and lightweight material. ABS plastic comes in a wide range of colors. Its strength and ease of processing have led it to become the most popular of the engineering polymers.
Manufacturing techniques: FDM
- Rugged
- Flexible
- Easy to process
- Resistant to everyday chemicals
- Temperature resistant
- High print shrinkage
- Smell of “plastic” when printed
- Not suitable for food contact
Strength
90%
Cost
20%
Moisture resistance
70%
Resistance to ultraviolet
9000%Chemical resistance
40%
PLA - PLASTIC
The raw material for the production of PLA plastic is corn starch (but you can also find varieties of sugar cane and tapioca), which makes it biodegradable. This is a simple material for 3D printing, when heated, it releases a pleasant sweet aroma. For this reason, many people prefer its ABS.
Manufacturing techniques: FDM
- Eco-friendly, biodegradable
- Food contact
- Hard, durable
- Low shrinkage
- High surface quality
- Low softening point 50°C
- Narrow temperature range (-20 to +40°C)
- Short-lived
- Fragile
Durability
75%
Cost
20%
Moisture resistance
20%
UV resistance
25%
Chemical resistance
45%
PETG, PET, PETT - PLASTIC water. This material is the second alternative to ABS, it does not emit caustic fumes when melted, while remaining strong and flexible.
Manufacturing techniques: FDM
- Odorless printing
- UV resistance
- Wide operating temperature range.
- Good slip and impact resistance
- Non-toxic, can be printed on articles intended to come into contact with food.
- Lower strength and softening point than ABS.
- High printing temperature quickly destroys the PTFE insert in the hot end
- Scratches more than ABS.
- Absorbs moisture from the air
Strength
90%
Cost
30%
Moisture resistance
75%
Ultraviolet 60% 80%
Chemical resistance
9000 (polycarbonate) is a high strength material designed for harsh environments and engineering applications. It has extremely high thermal deflection and impact resistance. Polycarbonate also has a high glass transition temperature of -150° Celsius. This means that it will maintain its structural integrity up to this temperature, parts made with this material show significantly improved mechanical strength compared to ABS and PLA.Manufacturing techniques: FDM
- Impact resistance
- High temperature resistant
- Naturally transparent
- Flexibility
- Durability
- Tendency to warp
- Very high print temperature required
- High tendency to shrink during printing
- Absorbs moisture from the air, which can cause print defects
Strength
90%
Cost
45%
Moisture resistance
55%
Ultraviolet
9000,000,000,000,0002 Chemical resistance 9000%HIPS - Plastic
HIPS (wake polystyrene) is a dissolvable support material commonly used with ABS. When used as a support material, it can be dissolved in d-Limonene leaving the print free of any defects caused by the removal of supports. HIPS has many of the same printing properties as ABS, making it a logical partner for dual extrusion. This material is more stable and slightly lighter than ABS, making it an excellent choice for parts that wear quickly or are used to print lighter products.
Manufacturing techniques: FDM
- Low cost
- Impact resistant
- Waterproof
- Light
- Soluble with d-limonene
- Heated deck required
- Closed chamber recommended
- High Print Temperature
- Ventilation required
Strength
80%
Cost
10%
Moisture resistance
80%
Ultraviolet resistance
70%
Chemical resistance
25%
FLEXIBLE - plastic
9000 FLEXIBLE (FLOOK FIRS) (TPE), which are a mixture of hard plastic and rubber.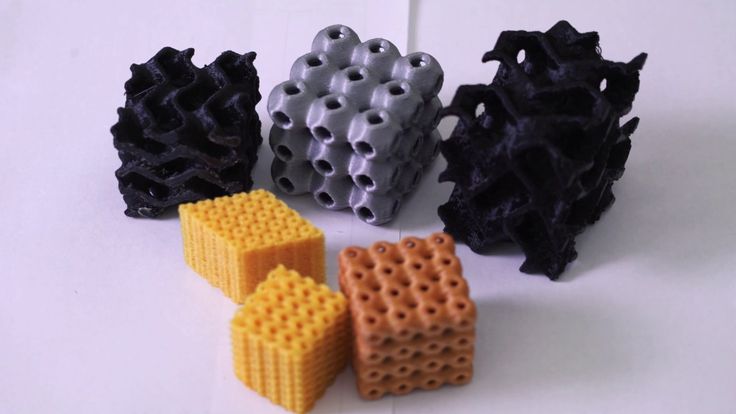
Manufacturing techniques: FDM
- Flexible and soft
- Excellent vibration damping
- Long shelf life
- Impact properties
- Hard to print
- Difficulty removing supports
- Not suitable for all 3D printers
Strength
80%
Cost
60%
Moisture resistance
80%
Persistence to ultraviolet
70%
Chemical resistance
70%
Photopolymers
Photopolymers are liquid resins, they usually consist of epoxy resin or a combination . When exposed to UV radiation, these monomers quickly form molecular bonds with each other and turn into a solid polymer. The main modern technologies where photopolymers are used are SLA/DLP and PolyJet. Resin 3D printing is also an additive process, just like FDM printing. This means that the process is based on a layer-by-layer building process, where one layer forms molecular bonds with the next layer. This process is repeated until the entire model is recreated.
Crafting Technologies: SLA/DLP , Polyjet
- High Detail
- Smooth surface
- Faster printing process
- Finished product uniform in all axes
- High material cost
- More labor-intensive removal of supports
- More limited choice of materials
Strength
80%
Cost
75%
Moisture resistance
80%
Dustyness to ultraviolet
9000Chemical resistance
9000 is one of the most popular 3D printing materials used by professional 3D printing companies.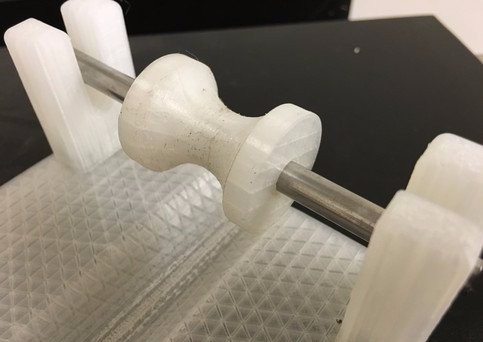
Given its flexibility and strength, nylon is an indispensable material for a wide range of applications from engineering to art. Nylon (polyamide) parts have a rough surface that can be polished to a smooth finish. Nylon is stronger than all other types of plastics, making it an ideal material for 3D printing products that require good tensile strength and mechanical strength.
Manufacturing techniques: SLS
- High detail
- High strength
- Finished part flat surface
- Supports not required
- Fast printing process
- High material cost
- Rough surface (can be removed with post-processing)
- Limited materials
- Available in one color (white)
Strength
90%
Cost
90%
Moisture resistance
65%
Dustyness to ultraviolet
80%
Chemical resistance
80%
metals (powder)
Metal powder (steel, aluminum, aluminum, aluminum, aluminum, aluminum, aluminum, aluminum, aluminum, aluminum, aluminum, aluminum, aluminum, aluminum, aluminum, aluminum, aluminum, aluminum, aluminum, aluminum, aluminum, aluminum, aluminum, aluminum, aluminum nickel, titanium) are metals that are ground to particles and are pre-base materials for most 3D printing processes producing metal parts.