Small cap 3d printing stocks
5 3D Printing Stocks to Consider in 2022
An in-depth look at the leading 3D printing stocks in the U.S stock market this year. Here’s what you need to know.
By Nicholas Rossolillo – Updated Jul 11, 2022 at 2:42PM
Back in the early 2010s, stocks were booming for 3D printing -- also known as additive manufacturing, a computer-controlled process in which three-dimensional objects are made. But the boom was followed by a bust as many pure-play 3D printing companies didn't immediately deliver on lofty expectations.
Rumors of the manufacturing technology's demise are clearly premature. These days, 3D printing is a high-growth niche that is steadily reshaping the manufacturing and industrial sectors. Some estimates point to a doubling in annual revenue from additive manufacturing between 2022 and 2026. Even growth investor Cathie Wood has launched a fund focused on manufacturing tech, The 3D Printing ETF (NYSEMKT:PRNT), via her company ARK Invest.
Here's what you need to know about 3D printing and additive manufacturing stocks for 2022:
Image source: Getty Images.
Investing in 3D printing stocks
The manufacturing of products in all corners of the economy is being revolutionized by 3D printing, from healthcare equipment to metal fabrication to housing construction. It's invading so many sectors that tech giants such as Microsoft (NASDAQ:MSFT), Autodesk (NASDAQ:ADSK), and HP (NYSE:HPQ) have launched products aimed at 3D printing and additive manufacturing. Other engineering and software outfits such as Dassault Systemes (OTC:DASTY), ANSYS (NASDAQ:ANSS), and Trimble (NASDAQ:TRMB) have also gotten involved in 3D printing technology.
Here are five key players to consider for 2022 that are a more focused bet on 3D printing:
Company | Market Cap | Description |
---|---|---|
Desktop Metal (NYSE:DM) | $1.3 billion | Recent IPO that focuses on metal fabrication technology. |
Stratasys (NASDAQ:SSYS) | $1.5 billion | One of the original 3D printing pioneers, with a wide array of printers and supporting design software. |
Xometry (NASDAQ:XMTR) | $1.9 billion | A manufacturing marketplace, including access to on-demand 3D printing services. |
3D Systems (NYSE:DDD) | $1.9 billion | Another original 3D printing pioneer and the largest pure-play stock on 3D printing technology. |
PTC (NASDAQ:PTC) | $11.7 billion | A manufacturing technology provider with a suite of software and related services for industrial businesses. |
1.
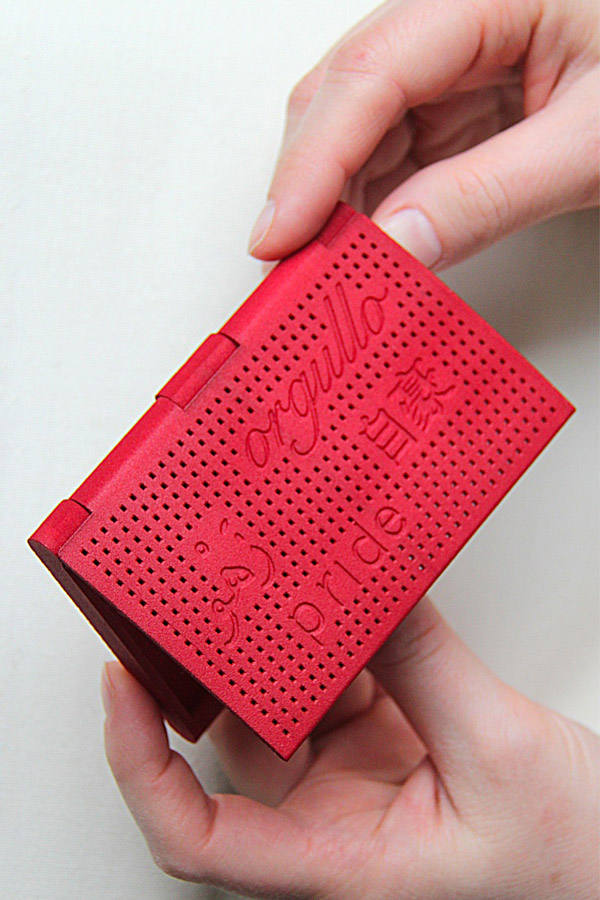
This company is a recent entry into the 3D printing space after going public via a SPAC at the end of 2020. The stock has been a terrible market underperformer since then, losing three-quarters of its value as of spring 2022. However, Desktop Metal could still be a promising investment for the long term.
As its name implies, Desktop Metal develops 3D printing hardware and accompanying design software for metal and carbon fiber parts. The company's smaller systems can handle prototyping and one-off parts, and larger printers are production grade-designed for manufacturing facilities. Desktop Metal serves companies operating in automotive, consumer goods, and heavy industrial equipment businesses.
Despite a tenuous start as a public company, Desktop Metal was actually increasing revenue at a torrid triple-digit pace in 2021. Gross profit margins are thin, and the company generated a steep net loss, but that should improve over time as the business scales its operation. Desktop Metal also has several hundred million dollars in cash and investments to fund its expansion. It used some of these funds to acquire additive manufacturing peer ExOne at the end of 2021.
2. Stratasys
Stratasys was part of the early 2010s 3D printing stock boom and bust, but its business has endured. Sales took a dip early in the COVID-19 pandemic but are rebounding as the Israel-based company picks up new manufacturing contracts.
Stratasys serves a diverse set of customers, including aerospace and automotive parts manufacturers, medical and dental companies, and makers of basic consumer products. In addition to a wide array of 3D printer models, Stratasys develops software to help users accelerate the time between design and final printing.
It isn't the highest-growth name on this list, but Stratasys is profitable (on a free cash flow basis) and has more than $500 million in cash and investments on its balance sheet, as well as no debt. Management thinks its payoff from years of research and development into additive manufacturing will accelerate in 2022.
3. Xometry
This is another newcomer to public markets. Xometry completed its initial public offering (IPO) over the summer of 2021, raising almost $350 million in cash in the process. As is often the case with new IPOs, the stock has underperformed since then. It has lost over half of its value from the time it started trading on public markets, but the business itself is rapidly growing.
Xometry is a marketplace for on-demand manufacturing of prototyping and mass production. It has a network of more than 5,000 suppliers that companies can call on to meet their fabrication needs. Among the suppliers on the Xometry platform are 3D printing companies, injection molding, and automated machining. The company reported having more than 28,000 active buyers utilizing its platform at the end of 2021.
Although it isn't profitable yet, Xometry's unique approach to the 3D printing and additive manufacturing industry is growing fast. Like other names on this list, it has a sizable war chest of cash and short-term investments that it can spend on research and marketing as it tries to attract more suppliers and buyers to its marketplace.
4. 3D Systems
3D Systems was another early player in the 3D printing industry, and while it suffered through the boom-and-bust period of the early 2010s, its business has held steady for much of the past decade. After a brief dip during the early days of the pandemic, 3D Systems is back in growth mode.
The company develops printers and design software for all sorts of materials and industries (medical device makers, dental labs, semiconductor designers, aerospace, and automotive manufacturers). It claims leadership among independent 3D printing companies (as measured by sales). As the 3D printing industry expands in the coming years, 3D Systems thinks it will be able to attract lots of new business with its extensive experience and global reach.
As an established tech outfit in the manufacturing sector, 3D Systems offers investors the prospect of more stable growth, along with profitability. It also has a large net cash position from which it can consolidate its lead in 3D printers and software technology.
5. PTC
By far the largest company on this list, PTC is a longtime technology partner of manufacturing and industrial enterprises. Fast approaching $2 billion in annualized sales and highly profitable, PTC has all the tools needed to digitally transform industrial businesses.
Besides 3D printing computer-aided design software (ANSYS is a peer and software partner that also operates in this space), PTC specializes in augmented reality, industrial IoT (Internet of Things), and product life-cycle management software. Most of its revenue is subscription-based (including its Creo software that enables 3D printing), making for a stable and steadily growing business model that generates ample cash flow. PTC puts spare cash to work developing new products for its partners and makes bolt-on acquisitions of other software companies that enhance its overall portfolio.
As a larger company, PTC won't be the fastest-growing stock in the additive manufacturing and 3D printing space. However, the company has established itself as a leader in industrial technology and should be a primary beneficiary as the production of manufactured goods gets more efficient.
The future of 3D printing
Manufacturing technology is making inroads throughout the global economy by reducing the cost of production and localizing and speeding up the time it takes to deliver customer orders. This is far from mere hype. Nevertheless, as is the case with all technology investments, progress won't go straight up. Expect twists and turns in these stocks as they develop new methods to design and make products.
If you decide to invest, do so in a measured way. Maintain a diversified portfolio, be wary of stocks benefiting from investor over-optimism, and always leave spare cash to invest more when there are inevitable dips. Given enough time -- years and decades -- investing in 3D printing could eventually provide a big payoff.
Related communication stocks topics
Investing in 5G Stocks
As the 5G technology rollout continues, these companies look like winners.
Investing in Top Telecommunications Stocks
Our world is increasingly interconnected, and these companies make it happen.
Investing in Communication Stocks
Communications has a broad definition. These companies are the leaders in the space.
Investing in Top Consumer Discretionary Stocks
When people have a little extra cash, they indulge in offerings from these companies.
Nicholas Rossolillo has positions in Autodesk and PTC. The Motley Fool has positions in and recommends Autodesk, HP, and Microsoft. The Motley Fool recommends 3D Systems, ANSYS, Dassault Systemes, PTC, and Trimble Inc. The Motley Fool has a disclosure policy.
Motley Fool Investing Philosophy
- #1 Buy 25+ Companies
- #2 Hold Stocks for 5+ Years
- #3 Add New Savings Regularly
- #4 Hold Through Market Volatility
- #5 Let Winners Run
- #6 Target Long-Term Returns
Why do we invest this way? Learn More
Related Articles
3 Dividend-Paying Tech Stocks to Buy in November
3 Robinhood Stocks to Buy Right Now
Better Buy: Microsoft vs. Alphabet
2 Growth Stocks to Buy and Hold Forever
PTC (PTC) Q4 2022 Earnings Call Transcript
Why Is Everyone Talking About Microsoft?
3 Things About Microsoft That Smart Investors Know
Premium Investing Services
Invest better with The Motley Fool. Get stock recommendations, portfolio guidance, and more from The Motley Fool's premium services.
View Premium Services
Top 3D Printing Stocks for Q4 2022
Table of Contents
Table of Contents
-
Best Value 3D Printing Stocks
-
Fastest Growing 3D Printing Stocks
-
3D Printing Stocks With the Best Performance
SSYS is top for value and performance and NNDM is top for growth
By
Noah Bolton
Full Bio
Noah has about a year of freelance writing experience. He's worked on his investing website dealing with topics such as the stock market and financial advice for beginners.
Learn about our editorial policies
Updated October 06, 2022
The 3D printing industry is made up of companies that provide products and services capable of manufacturing a range of products. 3D printing, also known as additive manufacturing, creates physical objects from digital designs. The printing process works by laying down thin layers of material in the form of liquid or powdered plastic, metal, or cement, and then fusing the layers together. Though still too slow for mass production, it is a revolutionary technology that has the potential to disrupt the manufacturing logistics and inventory management industries. The 3D printing industry is comprised of only a handful of companies, including players such as Proto Labs Inc., Faro Technologies Inc., and Desktop Metal Inc.
The industry is so young that it has no meaningful benchmark index. But the performance of these stocks can be compared to the broader market as represented by the Russell 1000 Index. These stocks have not performed well. Stratasys Ltd. (SSYS), the best performing 3D printing stock, has dramatically underperformed the Russell 1000, which has provided a total return of -12.5% over the past 12 months. This market performance number and all statistics in the tables below are as of Sept. 20, 2022.
Here are the top three 3D printing stocks with the best value, fastest sales growth, and the best performance.
These are the 3D printing stocks with the lowest 12-month trailing price-to-sales (P/S) ratio. For companies in early stages of development or industries suffering from major shocks, this metric can be substituted as a rough measure of a business's value. A business with higher sales could eventually produce more profit when it achieves (or returns to) profitability. The price-to-sales ratio shows how much you're paying for the stock for each dollar of sales generated.
Best Value 3D Printing Stocks | |||
---|---|---|---|
Price ($) | Market Cap ($B) | 12-Month Trailing P/S Ratio | |
Stratasys Ltd.![]() | 15.49 | 1.0 | 1.6 |
3D Systems Corp. (DDD) | 9.00 | 1.2 | 2.0 |
Proto Labs Inc. (PRLB) | 37.49 | 1.0 | 2.1 |
Source: YCharts
- Stratasys Ltd.: Stratasys offers 3D printing solutions, such as 3D printers, polymer materials, a software ecosystem, and related parts. It serves a variety of industries, including aerospace, automotive, consumer products, and healthcare. On Sept. 13, Stratasys completed the merger of its MakerBot subsidiary with Ultimaker, which offers platforms used to make 3-D printers. Ultimaker is backed by NPM Capital. The merged company will keep the Ultimaker name and focus on providing solutions, hardware, software and materials to the industry. NPM Capital will have majority ownership of the new company at 53.5%, and Stratasys will own 46.5%.
- 3D Systems Corp.: 3D Systems provides 3D printing solutions.
The company offers a range of hardware, software, and materials designed for additive manufacturing. Its products and services are used in a variety of industries and sectors, including aerospace, automotive, semiconductor, healthcare, and more.
- Proto Labs Inc.: Proto Labs is an e-commerce-based company that provides digital manufacturing services. It offers 3D printing, injection molding, CNC machining, and sheet metal fabrication. On Aug. 5, Proto Labs announced financial results for Q2 2022, the three-month period ending on June 30, 2022. Net income fell more than 80% to $2.6 million from the prior-year quarter while revenue rose 3.1%.
These are the 3D printing stocks with the highest YOY sales growth for the most recent quarter. Rising sales can help investors identify companies that are able to grow revenue organically or through other means and find growing companies that have not yet reached profitability. In addition, accounting factors that may not reflect the overall strength of the business can significantly influence earnings per share. However, sales growth can also be potentially misleading about the strength of a business, because growing sales on money-losing businesses can be harmful if the company has no plan to reach profitability.
Fastest Growing 3D Printing Stocks | |||
---|---|---|---|
Price ($) | Market Cap ($B) | Revenue Growth (%) | |
Nano Dimension Ltd. (NNDM) | 2.45 | 0.6 | 1,270 |
Desktop Metal Inc. (DM) | 3.07 | 1.0 | 203.9 |
Stratasys Ltd. (SSYS) | 15.49 | 1.0 | 13.3 |
Source: YCharts
- Nano Dimension Ltd.: Nano Dimension is an Israel-based 3D printing company focused on developing equipment and software for 3D-printed electronics. It develops printers for multilayer printed circuit boards and nanotechnology-based inks.
The company serves a range of industries, including consumer electronics, healthcare, aerospace, and automotive. On Sept. 1, Nano Dimension released Q2 2022 results. The company's net loss widened sharply to $40.0 million from a loss of $13.6 million in the same quarter a year earlier even as revenue soared more than 13-fold. The larger second-quarter loss was fueled partly by $10.9 million in non-cash adjustments for depreciation and amortization expenses, and share-based payments.
- Desktop Metal Inc.: Desktop Metal manufactures 3D printers and related equipment used to build complex parts from metal. It also offers 3D printing software. The company serves a range of industries, including automotive, consumer products, education, and heavy industry. On Aug. 08, the company reported Q2 2022 results. Desktop Metals' net loss increase nearly seven-fold to $297.3 million compared to the same quarter a year earlier even as revenue tripled.
- Stratasys Ltd.
: See above for company description.
These are the 3D printing stocks that had the smallest declines in total return over the past 12 months out of the companies we looked at.
3D Printing Stocks With the Best Performance | |||
---|---|---|---|
Price ($) | Market Cap ($B) | 12-Month Trailing Total Return (%) | |
Stratasys Ltd. (SSYS) | 15.49 | 1.0 | -34.5 |
Proto Labs Inc. (PRLB) | 37.49 | 1.0 | -50.6 |
Materialise NV (MTLS) | 10.95 | 0.6 | -53.9 |
Russell 1000 | N/A | N/A | -12.5 |
Source: YCharts
- Stratasys Ltd.: See above for company description.
- Proto Labs Inc.: See above for company description.
- Materialise NV: Materialise is a Belgium-based provider of additive manufacturing software and 3D printing services. It serves a range of industries, including healthcare, aerospace, and automotive. On Sept. 7, Materialise completed its acquisition of Identity3D, which makes products that encrypt, distribute, and track digital parts as they move through supply-chains. The value of the deal was not specified in the announcement.
The comments, opinions, and analyses expressed herein are for informational purposes only and should not be considered individual investment advice or recommendations to invest in any security or to adopt any investment strategy. Though we believe the information provided herein is reliable, we do not warrant its accuracy or completeness. The views and strategies described in our content may not be suitable for all investors. Because market and economic conditions are subject to rapid change, all comments, opinions, and analyses contained within our content are rendered as of the date of the posting and may change without notice. The material is not intended as a complete analysis of every material fact regarding any country, region, market, industry, investment, or strategy.
Article Sources
Investopedia requires writers to use primary sources to support their work. These include white papers, government data, original reporting, and interviews with industry experts. We also reference original research from other reputable publishers where appropriate. You can learn more about the standards we follow in producing accurate, unbiased content in our editorial policy.
YCharts. "Financial Data."
Stratasys Ltd. "Stratasys Completes Merger of MakerBot with Ultimaker."
Proto Labs Inc. "Proto Labs Q2 2022 Earnings Release."
Nano Dimension Ltd. "Earnings Press Release for Q2 2022."
Desktop Metals Inc. " Desktop Metals Second Quarter 2022 Earnings."
Materialise NV. "Materialise Acquires Indenity3D."
Problems, defects, 3D printing errors and solutions
Often during the operation of a 3D printer, problems may arise due to which defects appear on the finished model. Or instead of a neat product, plastic noodles suddenly appear on the table.
In fact, the causes of defects can be conditionally divided into 2 types - these are physical and software.
Physical ones are those that arise due to problems with the mechanics or any other causes that can be eliminated physically. These include problems with printer mechanisms (belt tension, backlash), clogged or deformed nozzle, incorrect table geometry, etc.
Software - these are defects that occur due to incorrect slicer settings or, less often, errors in the printer firmware. For example, incorrectly selected print speed, retract settings, incorrectly selected temperature for plastic, etc.
Very rarely, the problem may lie in the wrong or “flying” printer firmware (although usually the printer simply will not start then), overheating of some boards during printing, etc. These are rather special cases, so we will not consider them.
Model peels off or does not stick to the build plate
This is the most common 3D printing problem. Every 3D printer has had a case when the first layer treacherously rolls, clinging to the extruder, or the most offensive - when it tears off a partially printed model from the table. The first layer must stick tightly otherwise nothing will be printed.
Gap between table and nozzle 9 too large0023
This is the most common reason. You just need to set the correct gap between the table and the nozzle.
Modern printers often use an auto-calibration (auto-leveling) table system or an auxiliary table leveling program. To calibrate such printers, use the instructions. If there is no manual, it can be downloaded from the manufacturer's website.
If you have a simple printer without auto-calibration, a self-assembly or KIT, use a probe or a piece of paper folded in half to calibrate. The probe should be slightly pressed against the table by the nozzle. Before calibration, the table and extruder must be heated. Align the table surface over each adjustment screw (there may be 3 or 4) in turn, and only then check the center point.
If you're having trouble getting your table surface perfectly level, try raft printing. Raft is a thick substrate in several layers that is printed under the model. It will help smooth out the slight curvature of the table.
A small cheat sheet to determine the correct gap on the first layer
Plastic with poor adhesion
Some types of plastic, due to various reasons, such as large shrinkage, do not adhere well to the surface of the printing platform. In this case, try using stickers or special 3D adhesives to improve adhesion between the table and the first layer of plastic.
In the early days of 3D printing, there were experiments with different homemade 3D adhesive recipes. ABS diluted in acetone, BF glue, sugar syrup and even beer. Some experiments have been successful. Until now, some enthusiasts use some types of hairspray or glue sticks as 3D glue. But still they are inferior in their properties to industrial 3D adhesives.
Some types of high temperature plastics with a high percentage of shrinkage (ABS, Nylon, etc.) may peel off the table during printing. This is due to uneven cooling and “compression” of the model (the lower layers have already cooled down, but the upper ones have not yet). For such plastics, it is imperative to use a 3D printer with a heated table and a closed case.
Plastic temperature too low
The hotter the plastic is when it exits the nozzle, the better it will adhere to the print bed. It is better to print the first 5-10 layers at a higher temperature (+ 5-10 degrees) and turn off the blower fan.
Wrong first layer settings (speed and thickness)
A thicker layer sticks easier, so the standard first layer is 0.3mm thick. With an increase in print speed, the heating block may simply not have time to heat the plastic to the desired temperature and it will stick to the table worse. Before printing, check the speed and thickness settings of the first layer in the slicer.
A lot depends on how the 3D printer prints the first layer. Try to control the printing of the first layer and only then leave the printer to work alone.
Plastic does not choke from nozzle
The printer has already begun to print, but the print table remains empty. Or part of the model did not print.
Clogged nozzle
In 3D printing, a nozzle is a consumable. The nozzles are clogged or worn out (frequency depends on the type of plastic). The simplest thing is to replace the nozzle. But if there was no spare at hand, you can try to clean the old one. To do this, there is a whole set of thin needles. Or you can heat a clogged nozzle above the melting point of the plastic and “burn out” the blockage. But later it is still better to replace the nozzle.
Low temperature nozzle
You need to increase the temperature of the extruder in the settings of the slicer or check the health of the thermistor and heating block. Sometimes the thermistor may not read the temperature correctly due to a malfunction or incorrect 3D printer firmware settings.
If the problem arose after replacing the thermistor - contact the manufacturer or read articles about PID tuning.
Empty extruder
As the extruder heats up, plastic begins to ooze out of the nozzle. Because of this, the extruder may start printing half empty. Because of this, part of the first layer is not printed. You can push the plastic manually by simply pushing the bar into the nozzle. Or solve this problem programmatically - in the slicer, add a contour print around the model (one line).
Some manufacturers and 3D enthusiasts add a line print on the edge of the table at the beginning of each GCode. This is done so that there is plastic in the nozzle by the time the model is printed.
Feed mechanism does not push through plastic
The plastic pushes the feed mechanism to the extruder - a motor with a special pulley put on the shaft. If for some reason the plastic is not pushed through (nozzle clogged, extruder temperature low, etc.), then the pulley “gnaws” through the bar. You need to push the plastic bar with your hands or cut off the damaged piece.
Elephant foot
The first layers of the model are wider and protrude beyond the boundaries of the model. This is due to the fact that the upper layers put pressure on the first ones that have not yet cooled down and flatten them.
High table temperature
Due to the too high temperature of the table, the lower layers remain soft for a long time. Try lowering the table temperature. It is better to reduce gradually (in increments of 5 degrees). You can try to turn on the blower when printing the first layers.
Small gap between nozzle and platen
If, when printing the first layer, the nozzle is too close to the table, then excess plastic will be forced out. After a few coats, this will not be as noticeable, but can lead to the effect of an “elephant's foot”.
Plastic re-extrusion
When too much material is squeezed out of the nozzle, the walls of the model are not smooth, but bumpy, with sagging.
The solution is software - in the settings of the slicer, you need to set the material feed rate (fluidity) to a lower value. The average value is 95-98%.
It is worth checking the diameter of the rod. If its size is greater than 1.75, then the plastic will be squeezed out more than necessary.
Plastic underextrusion
The plastic is squeezed out too little, because of this, gaps may appear between the layer. The finished model will be fragile and fragile.
Wrong thread diameter
Check the filament diameter in the slicer settings. Sometimes, instead of the popular 1.75, the default is 2.85.
Incorrect feed rate settings
Check the fluidity settings in the slicer. The average should be 95-98%.
Clogged nozzle
Something could get into the nozzle and partially block the exit of the plastic. Visually, the plastic will choke from the nozzle, but in a smaller amount than necessary for printing.
Hairiness or cobwebs on finished model
Thin threads of plastic protrude from the outer wall of the model (most often on one side). The defect appears due to the flow of plastic from the nozzle during idle movement.
Insufficient retract
A retract is a slight pull of a plastic filament from an extruder. Due to the retract when the extruder is idle (from layer to layer or from model to model), heated plastic does not drip from the nozzle. For some flowable plastics (eg PETG) the speed and amount of retraction must be increased.
"Hairiness" can be easily removed by grinding or cutting off the threads with a sharp scalpel.
High temperature extruder
The higher the extruder temperature, the more liquid the plastic becomes. It is important to find a balance so that the plastic is not too liquid and sticks well in layers.
In the selection of the optimal extruder temperature, a test model - a tower - helps a lot. It clearly shows how plastic behaves when printed at different temperatures.
.
Temperature test
Top "perforated" or uneven
The top of the model is bumpy or with holes. The problem may arise if the top of the model is flat. For example, like a cube.
Insufficient airflow
When printing the top plane (cover), the plastic does not have time to cool down and remains too liquid. Because of this, the threads are torn and holes are formed. Increase the fan speed on the last layers.
Few top layers
The top of the print may be too thin and deform as a result. Check slicer settings. The number of upper layers is not recommended to be set less than 6.
Low percentage of filling
If the infill percentage is too low, then the top layer will simply have nothing to rely on. Increase the fill percentage in the slicer settings.
Model deformation
Some parts of the model seem to have melted in some places or on one side. The problem most often occurs when printing with PLA plastic. The defect appears due to the fact that the plastic does not have time to cool and deforms.
Insufficient airflow model
Turn the fans on to maximum. If their power is not enough (in some printers, the fan is located only on one side), you can put a regular desktop fan and direct it to the 3D printer table.
Small model
Small models are difficult to blow well. Try to print small items alongside larger ones, or place several identical models in different corners of the table. So the plastic will have more time to cool.
Layer offset
Layers shift along the x or y axis during printing.
Print head jam
Turn off the printer and try to move the extruder along the x and y axes with your hands. The extruder must move freely. If there are jams, check the mechanics of the printer. Bearing wear or the curvature of the shafts may be to blame.
Electronics overheating
Sometimes electronics problems can be to blame for misaligned layers. The most common cause is overheating of the drivers or too low current exposed to them.
Table top is loose
This is most often seen in 3D printers with glass. During printing, the nozzle may hit the model and move the glass slightly. Before printing, check if the glass or other printing surface is well fixed on the heating table.
Skip layers
Small holes are visible on the print, or the shell of the model is not continuous.
Teflon tube deformed
There are 2 types of thermal barriers - all-metal and with a Teflon tube. If overheated, the Teflon tube may deform. Plastic will pass through it, but in a smaller amount.
Low extruder temperature or high print speed
If the extruder is not heated enough, then the plastic will not be liquid enough and simply will not have time to be forced through the nozzle. The higher the print speed, the higher the extruder temperature should be.
Sometimes the outer walls print well, but the infill is “torn”. In this case, slow down the infill print speed in the slicer.
Model bundle
Cracks form on the surface of the printout during or after printing. Cracks can be large or very small. Most often, this problem occurs with plastics with a high percentage of shrinkage - ABS or Nylon.
Sudden temperature difference (if model delaminates during printing)
With a sharp temperature difference (for example, a draft), part of the model cools down faster. This leads to uneven shrinkage and incorrect distribution of internal stress. For plastics with low shrinkage, this is not critical. But if the shrinkage percentage is more than a few percent, the model may burst in layers.
For printing with such plastics, it is recommended to use a printer with a closed housing. If this is not possible, try to avoid drafts and sudden temperature changes in the room where the 3D printer prints as much as possible.
Print temperature
Due to too low printing temperatures, the layers may not “stick” well to each other. Raise the print temperature in the slicer settings.
Hardening (if the model cracks after printing)
Sometimes cracks appear on the model a few days after printing. This is due to uneven distribution of internal stress after cooling. You can try to “harden” the finished product.
For hardening, the model is placed, for example, in an oven, and heated to the softening temperature of the plastic. After that, the heating is turned off and the oven is left to cool slowly with the model inside. Due to this, the stress inside the print is distributed more evenly. But accuracy is very important in this method - if you make a little mistake with the temperature, the finished product can “float”.
Ringing
In places where the extruder changed direction, ripples are visible. Most often it looks like a shadow around the “sharp” protruding elements of the model.
Mechanical problems
Sometimes the problem occurs due to extruder play. Check if the extruder mount to the rails is loose. Be sure to check the tension of all belts.
High print speed or high accelerations
Moving the extruder too fast can cause vibrations that cause ripples on the wall of the model. The lighter the weight of the extruder, the less noticeable the ripples will be. To get rid of ringing, simply reduce the print speed in the slicer settings.
Slits for thin-walled models (not solid shell)
The thin wall of the model is not solid, but consists of two thin walls with a narrow gap between them. This problem is often faced by fans of printing "cutting" for baking.
Left model with wall defect, right without
Wall thickness and nozzle diameter mismatch
If the wall thickness is 1 mm, and the nozzle diameter is 0.4, it turns out that for a solid wall, 2 nozzle passes are few, and 3 are already many. The result will depend on the slicer algorithm, but most often you will get 2 walls with a thin slot in the middle (the slicer cannot change the wall thickness). The solution to the problem may be a slight refinement of the 3D model or the use of a different slicer.
Algorithms for calculating 3D models are constantly being improved and refined, and now this problem is less common.
When modeling, take into account not only the thickness of the nozzle, but also the percentage of “overlapping” of lines on each other. If you have a nozzle with a diameter of 0.4 - make the wall in your model not 0.
8, but 0.7 - 0.75.
Wrong model geometry
When instead of a circle you get an oval, and instead of a square you get a semblance of a rhombus.
The main reason is malfunctions in the mechanics of the printer. Be sure to check:
Belts
Check belt tension in x and y. Belts stretch over time and may need to be tightened or replaced. Each 3D printer has its own way of tightening the belt. If the belts are slightly stretched, you can tighten them with the help of a "spring".
Loose pulleys, etc.
Check if all bolts and nuts are tight. Are there backlashes. Pay special attention to tightening the pulleys located on the motors along the x and y axes.
Sagging of some parts of the model
Some parts are not printed, broken, or instead of a neat surface, a swollen plastic snot is obtained.
No support for overhangs
A 3D printer cannot print in the air, so if there are overhanging elements in the model, you need to set supports - supports. The slicer can set the necessary support itself, you need to check the appropriate box in the settings.
When printing with soluble support, you can set the gap between the model and support - 0. This will make the surface smoother. If the support material and the model are the same, you need to add a small gap. Otherwise, it will be difficult to separate the support from the model.
Split model
Sometimes the supports can take more plastic than the model. In this case, to save material and time, it will be more convenient to cut the model. If you have more than one 3D printer, then the model will print several times faster.
When cutting the model, you can leave grooves or mortgages so that the pieces of the model are connected without displacement.
Totals
In this article, we talked about the most popular 3D printing defects and how to solve them. Don't be intimidated by such a long list. Some problems are rare and you are unlikely to encounter them.
There is a list of problems that arise due to the design features of a 3D printer, so try to choose a printer that suits your needs. To do this, you need to understand what products and what material you need.
Problems associated with printing algorithms are quickly eliminated by software developers.
Do not be afraid of possible difficulties and each print will be successful.
13 notes about 3D printing, after 3 years of owning a 3D printer / Habr
This article will be, first of all, of interest both to those who have directly encountered 3D printing, that is, who owns a 3D printer, but also to those who are just about to join the ranks of 3D printers and are thinking about buying their own printer.
In the framework of this article, I would like to present my observations as a direct owner of a 3D printer for more than 3 years.
Despite the fact that 3D printers have been known for a long time and, in my memory, have become widely used, judging by the information on various resources, starting around 2010 (I may be wrong, these are my subjective observations), for a long time I ignored this area, it’s hard to say why…
Probably, he considered it some kind of “childish pampering”, another hype topic for which there is simply not enough time…
The break happened when one of the wheels on my travel suitcase wore out. You know, a big plastic suitcase, with four spinning wheels on the bottom. Unfortunately, it is a “rather disposable thing”, due to the lack of bearings on the wheels, which is why the wear of the friction point of the axle and wheel allows the suitcase to last no more than one or two seasons.
And it’s like “lightning flashed in the middle of the day: 3D printer!” It is with his help that I can fix this problem! Looking ahead, I’ll say that I didn’t succeed in fixing the suitcase in this way, so I had to use a different approach . ..
As a result, I "upped" him - by installing wheels from unnecessary roller skates. Thanks to this “up”, the suitcase has become a real all-terrain vehicle and, even being very loaded, it rides easily - pushed forward even with “one finger”. And even in the snow, 5-6 cm thick. A tank, not a suitcase turned out! By the way - I took spinning wheeled "units" in Leroy. Then he took off and threw out his native plastic wheels, inserting them from roller skates:
But this thought itself became a kind of trigger that allowed me to finally join the world of printers and buy my first 3D printer.
Like many, before buying it, I studied various forums and sites for a long time, delving into all the subtleties. And for some reason, I immediately liked the type of printer called the delta printer. Probably because during operation it looks like some kind of "alien device".
If at your leisure you like to sit “looking into the carpet”, then with the advent of such a printer you will have a much more interesting activity, even, one might say, hypnotizing :-))
And this, in fact, is my delta (if anyone interesting), which went, let's say, "ultimate up": all the electronics were placed upstairs, on a self-made welded frame, covered with polyethylene and a magnetic door was made. The coil with a bar is installed at the top, on the frame. The axis on which the coil is put on is machined on a lathe from aluminum and a bearing from the VAZ timing is inserted into it. As a result, the coil - "rotates even from the passage of a fly nearby":
Well, yes, I won’t argue for a long time, let’s start reviewing the main facts that I have accumulated as a result of owning this car ... The facts are purely subjective and may differ from your vision. In any case, I will be glad to comments, clarifications, etc.
▍ NOTE 1. Delta is good, but...
Here I should give a number of my observations regarding the delta printer:
- It contains a completely finished frame of the future box, which makes it easy to form a heat chamber. I understand that many printers are made in the form factor of a “certain box” (but this point cannot be ignored), which greatly facilitates the process of wrapping this box with heat-insulating material.
In my case, as such a material, I used a plastic film.
- Already thanks to its design, delta allows you to work at much higher speeds than XY printers. By the way, it is on the delta principle that many modern high-speed industrial robots are built to sort various parts directly on the conveyor belt:
However, this plus does not allow to fully realize the occurrence of parasitic vibrations, even despite their suppressors:
Thus, accurate printing is possible, only at speeds (at least that was the case for me), no more than 60 mm per second. A complex procedure for aligning the movement of the head parallel to the table, which is why, for many, the so-called "lens" appears. People struggle with it with varying degrees of success, but I have not encountered this on my printer and for me, therefore, the “lens” has never been a problem. At the same point, it is worth noting the calibration of the table, which was initially absent on the first deltas, and I had to use an external third-party solution from one American do-it-yourselfer called EZBED. This solution was a hardware-software complex that allows you to quickly and easily calibrate the printing table, that is, to let the printer understand its geometry. Modern printers do not have this issue as they come with a built-in calibration solution. It is worth noting that I solved this problem by attaching a limit switch to the print head, and using the Marlin-1.1.9 firmware.
▍ NOTE 2. “Size is not the main thing...” :-)
When I got the printer, I was impressed by the possibility of huge printouts, a la the handguards of some futuristic rifles, huge body parts, etc.
However, if you try to analyze the results of your many years of practice, it turns out that in most cases, rather small objects were printed that easily fit in the palm of your hand, a maximum of two palms. Despite such a seemingly small size, the printing of these details took a significant amount of time. Of course, this very much depends on which nozzle you print with. But, despite this, it is difficult to disagree with the fact that most of the printed parts will be quite utilitarian and small in size.
Therefore, to be honest, the need for a printer that allows you to print "Venus de Milo in life size" is not obvious.
Of course, you can object to me that “I’m going to buy a printer, I’ll get used to it a bit and I’ll get started!!!”
Here you need to take into account one simple point: there are no universal things. And in order to understand how much 3D printing in general and your printer, in particular, you will need to solve your problems, and how much it will be able to solve such problems, you just need to first try the 3D printing method personally and then a lot will become clear to you .
Therefore, for a beginner, I recommend taking a small printer that allows you to print extremely small items that fit in the palm of two. With such a device, you will definitely never lose, as it will always be needed. In addition, with its help you will be able to get used to the printing process and, if necessary, purchase a larger device, already clearly understanding its capabilities and ability to solve your set of tasks.
▍ NOTE 3. "What type of printer to get."
Based on the foregoing, I do not recommend taking a delta printer and this can be said right away.
Not because it is bad, in fact, it prints quite accurately, its main problem (in my opinion) is the inability to print rectangular flat, fairly large case components, as well as the inability to fully realize high-speed work, since the quality drops critically. Here it turns out to be a rather offensive situation - the printer can work quickly, but this cannot be done, since the quality will be “nothing”.
And then what kind to take? Depending on the budget and capabilities, I recommend taking any cube printer, for example, the same Core XY (the head moves, and the table goes down as the model “grows”, from top to bottom):
Image source: thingiverse.com
Such a printer allows you to easily print fairly large flat parts of cases, has good speed and accuracy. In addition, the presence of a rigid box-shaped frame allows it to be easily covered with polyethylene to create a sealed heat chamber. In addition, the very fact that the table does not move while working reduces the number of problems with model peeling.
However, the advantages of this printer will not be fully revealed if it has a direct extruder. On the one hand, it will allow printing with rubber-like materials, on the other -
large inertia and head weight. And these are parasitic vibrations, wear of the fur. parts, etc. (like everything in life, “we treat one thing and cripple another” :-))
At the initial stages, this may not be necessary, but in the future it may be necessary to print, for example, tires for your homemade car. And with this, the Bowden extruder has obvious problems. Although, in fairness, printing with such a rubber-like material is far from a daily need. However, whoever seeks will always find: over time, I found a way to “upgrade” my printer with a Bowden extruder to print with flexible materials. "Crutches" of course. But even so.
By the way, there are printers of a cheaper type, the so-called "drygostol", printing by moving the table and head:
They are inexpensive, moderately accurate, but they require a sufficiently high-quality gluing of the printed model to the table, because the table moves, and the model can come off when the table is jerked sharply. When printing large models, this can be a problem.
▍ NOTE 4. What to print with?
It's only a matter of taste and purpose. That is, if your printout will only stand on a shelf and should differ in some kind of aesthetic appearance, these are some requirements, if the printout is an engineering part that will be operated under conditions of increased mechanical load, these are different requirements. That is, in the first case, you can use any PLA, SBS plastics, and others with similar properties.
For engineering parts, for example, I only use ABS. It combines high hardness, strength and low price. Although I understand that now this last statement will cause a storm of comments in the style of “no! - there is even stronger, even better, the same PETG, etc. ":-)
I just wanted to say here that thanks to the low price and the practical experiments that I conducted with ABS plastic, I realized that it is completely meets all my requirements.
However, the fact that ABS plastic releases carcinogenic substances when heated is quite annoying and forces you to take measures to prevent poisoning. For this, my printer prints completely closed and on an open balcony. After printing, the printer chamber opens, and it remains open in this form until it is completely ventilated and cools down.
▍ NOTE 5. "ABS is difficult to type on, it separates, peels off the table, and in general..."
With a properly configured printer (in my case, at a print temperature of 205 degrees, a thermal chamber and a desktop temperature of 100 degrees), the use of auxiliary techniques, for example, among which, one can name the so-called ABS juice (which is ABS- plastic dissolved in acetone), you can create wear-resistant and durable things, without any hypothetical problems.
For example, my printer has been printing for many hours at temperatures well below freezing. And this happened more than once, not twice, not three! And the print quality was excellent:
12 hour ABS printing at -4 C
▍ NOTE 6. Acetone for post-processing and ABS juicing
At one time, I wrote a fairly detailed article on this topic and I will try to give the main excerpts from it. The essence of the issue here is as follows: due to the fact that different GOSTs are used for the production of acetone, acetone differs in quality. Despite the fact that it would seem that “acetone is also acetone in Africa,” nevertheless, one type of acetone can differ significantly from each other. For example, ordinary acetone, which can be bought at any hardware store, such as "1000 little things", "store near the house" and the like, is very low quality acetone, smells disgusting (although someone like it, maybe someone likes its pleasant building aroma and "aftertaste" :-))).
In contrast, there is a much higher quality acetone, which, however, is not found at all in any household stores, even large chain stores, such as Auchan or Leroy Merlin.
This type of acetone is found exclusively in shops that sell varnishes and paints for automotive work, i.e. these are highly specialized shops for car workshops:
Acetone, which can be purchased there, is of excellent quality, smells almost like alcohol, quickly disappears,
:-) - this is a joke, of course, don't even try it.
However, its main advantage, compared to household type acetone, is that it perfectly dissolves ABS plastic and does not allow it to precipitate. For me personally, it was a very surprising observation when the same ABS plastic was perfectly dissolved with acetone from an auto shop, and completely precipitated when I tried to use household acetone (I just ran out of good acetone, and I had to use "what is ").
Therefore, if you want your result to be always excellent, then here is the right acetone. It should be labeled "for professional use":
▍ NOTE 7. What about ABS juice?
"ABS juice" is what printers call a mixture of acetone and pieces of ABS plastic dissolved in it. This mixture is smeared on the surface of the desktop before printing and allowed to dry. Thanks to this spread, the model easily sticks to the desktop and does not peel off during the printing process. After printing is completed and the platen has cooled down, the model can be easily separated.
All that needs to be said here is that, after trying different approaches over time, I settled on using flexible metal spatulas, also called "Japanese-style spatulas":
According to the results of many tests, this method of spreading turned out to be one of the most convenient options, such spatulas can be cleaned very quickly and easily after work. In other words, highly recommended!
▍ NOTE 8. "Yes, nothing sensible can be done on it, I indulged a little and decided to sell it - you can't use it for anything good anyway"
I absolutely disagree with the statement above, which is periodically heard from newcomers to 3D printing. You can even say more: at the moment I can’t even imagine how I used to live without a 3D printer! Since it is he who makes it possible for any do-it-yourselfer to significantly expand their capabilities and make piece products, almost of factory quality! Of course, for this, the appropriate hands must be applied to the 3D printer, but that’s another question… and take on things that I would never have thought to take on before!
For example, among my homemade products, the following can be listed:
- Heated sole for boots, which is a hose integrated into the insole (and filled with household silicone from a household store), through which water flows, heated with a catalytic type hand warmer.
Water is pumped using a small peristaltic pump. The engine with a metal gearbox, which is used in the creation of this pump, allows you to develop a force of 3 kg, which is even redundant for this homemade product. The engine is powered by Peltier elements mounted next to the catalytic heater. The project is currently in progress.
- Centrifugal water pump mounted on the shaft of an internal combustion engine that drives a high pressure wearable air compressor with a pressure of 500 bar. The pump pumps coolant through the casing of the high pressure pump, or rather its second stage. Despite the fact that the pump is 3D printed and runs at over 6000 rpm, nothing “fell apart, fell apart, didn’t break.” As you can see in the photo, the pump is installed instead of the “starter”, that is, the armstarter. The compressor scheme as a whole is as follows: 2 engines. Connected by clutch. One is heavy duty. The second is modified and turned into a high pressure compressor:
Yes, before assembling this, I also did not believe that this was possible. Moreover, even when I collected it, I did not believe my eyes :-))). However, it is a fact…
- I printed a number of Rank-Hilsch test tubes, the essence of which I have described in detail in this article.
- Printed mass of parts, more than 100 pieces, to create 10 web-controlled robots. There was also a detailed article about this here.
Well, and a bunch of all sorts of useful and not very crafts. As you can see from my crafts above, I have a special passion for creating some useful things, a utilitarian direction. That is, so that the printout is useful, and does not belong to the type “yyy breathe, Mikola, what am I doing here” :-), and then put it on the shelf and that's it. Although, engineers are also not alien to beauties, and this will be my next fact below.
▍ NOTE 9 Proper placement of the model when printing is half the battle
It would seem an obvious fact, but many underestimate it. Here I mean the following: by experience, I accidentally discovered that when printing various statues (in which I, completely unexpectedly for myself, discovered another passion of mine), it is advisable to place the statues at an angle to the printing table.
This allows the layers in the printout to run at an angle of approximately 45-50 degrees to the model. The result of this is that the printed model is almost completely invisible layers and the model looks like it has been post-processed, but at the same time retains a deep matte color, which, to my personal taste, is more like a marble than a glossy result of processing in an acetone bath :
An additional advantage of this method is that the layers going at an angle of 45-50 ° to the model give it additional strength. This is especially true for printing statues, which contain many thin elements that are easily chipped when the statue is accidentally dropped from a table or shelf (learned from bitter experience, this happened to me many times, and ruined some fairly decent prints).
That is, layers running across the model, if the model has a large extension in height, does not allow it to maintain sufficient strength. For better understanding, I tried to illustrate this point in the figures below:
▍ NOTE 10. Bleeding must be taken into account when printing, especially if the model is composed of separate parts and must be assembled by joining these parts to each other, entering into each other, etc.
I tried to illustrate this point in the figures below. The implication here is that if you're printing a composite model, you need to correct for the amount of bleed on the plastic (I'm not sure what it's called, but at least I tried to convey what I mean). If this is not taken into account, then the model will not fit.
For example, in my case this correction is 0.2 mm per diameter - if I want the model to fit more tightly; if I need a free joint, without excessive density, then 0.3 mm per diameter:
That is, suppose that the blue part has a size of 10x10mm. So it must be modeled in a CAD program as 9.8x9.8 mm (if we want it to sit tight) or 9.7x9.7 mm (to sit freely). Well, or expand the hole in the green part, and leave the blue one as it is.
This is often a problem when you download a prefabricated model from the Internet - but it is not going to, even if you crack! But because no amendments have been made…
For your particular case, the amendments may be different.
▍ NOTE 11. What if...
In fact, this note complements note number 8. Using a 3D printer allows you to create metal parts using a printed 3D model. For this, the casting method is used according to the lost wax or burnt model. In our case, we will deal mainly with metal casting on a burnt model.
Briefly, it looks like this: printing a 3D model (using PLA plastic) → pouring it with plaster → burning the PLA plastic, simultaneously with burning the mold, in a conventional stove oven → pouring the resulting shape with molten metal (melted in a conventional microwave) .
Image source: 3dtopo.com
I told about a simple method of melting metals in a home microwave oven here.
There was even a good article about casting on Habré.
▍ NOTE 12. Durability?
Despite the fact that ABS plastic is called exposed to ultraviolet radiation and, accordingly, burns out, losing its strength in the sun, in my practice, even printouts that are constantly exposed to the sun have not lost their strength and color at all, continuing to be successfully used and Currently.
It should also be added here that printouts are constantly exposed not only to the rays of the sun, but also work continuously in damp conditions!
As such printouts, I can give an example of winglets for technical cranes, which I printed out, but, unfortunately, did not photograph this process; as well as fasteners on shoes that I use “both in the snow, and in the heat and in the pouring rain, and in general are always with me”:
▍ NOTE 13.
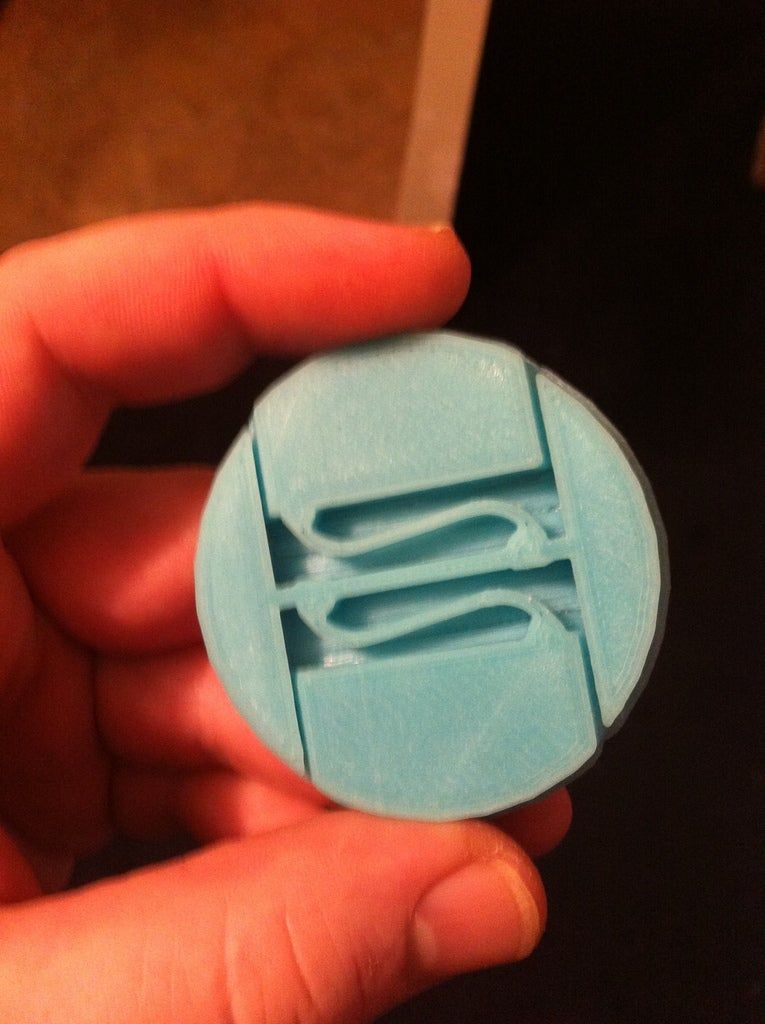