Scan model for 3d printing
How to Use 3D Scanning and 3D Printing for Reverse Engineering
Reverse engineering is a powerful way to create digital designs from a physical part, and can be a valuable tool in your prototyping toolkit alongside technologies like 3D scanning and 3D printing.
3D scanners measure complex objects very quickly, and can speed up your design workflow tremendously when real-life references are involved. With the ability to capture and modify physical shapes, you can design 3D printed parts that fit perfectly on existing products of all kinds. 3D printed jigs allow you to repeatedly locate a drill or saw, or assemble parts precisely with adhesive. Create close-fitting, reusable masks for sandblasting, painting, or etching.
In this post, we’ll walk through the step-by-step reverse engineering process for an aftermarket digital gauge and explain how to scan a part for 3D printing, with tips along the way for using the right reverse engineering tools, from CAD software to to 3D scanners and 3D printers.
For a full breakdown of 3D scanning workflows and technologies, download our white paper.
Download the White Paper
Looking for a 3D scanner for your 3D printer? Read our detailed guide on choosing the best 3D scanner to use with your 3D printer.
One of the biggest challenges people encounter when converting physical objects to digital is a major incompatibility between two different types of 3D models: meshes and solids.
A 3D scanner outputs a mesh, rather than a constructive “solid” model. Meshes need to be reverse engineered to be made editable.
Meshes are the main output of all 3D scanners, and the format commonly understood by 3D printers (STLs). A mesh represents the surface of a shape with a large number of triangles, connected edge to edge. Mesh models don’t contain any information about the object, besides the position of the triangles that define the shape.
On the other hand, engineers are trained to work with solid models. Solid models hold information about how an object is designed, and this information is explicitly encoded into the model as features in a ‘stack’ of logical steps. In solid CAD, it’s possible to change the dimensions for a single feature, and the rest of the model will update to accommodate the change.
Since meshes lack information about the construction of the object, the ways you can alter a mesh model are limited—CAD software like Solidworks and Onshape can’t directly modify meshes. If you need to make major modifications to the underlying design of a scanned part, the mesh needs to be converted to a solid CAD drawing: this process is reverse engineering.
Reverse engineering is important when you want to create new parts that reference or incorporate older designs, where the original CAD design isn’t accessible.
For example, you can create replacement parts that match the original design of damaged existing pieces, or use reverse engineering processes to integrate complex surfaces from existing objects into 3D printable jigs, which are useful when modifying mass manufactured and handcrafted products.
To demonstrate the basic steps in a reverse engineering workflow, let's take a look at the process for creating an assembly jig for an aftermarket digital gauge that fits onto the air vent of a Volkswagen Golf.
Spray coat the object with a temporary matte powder to improve scan accuracy. Even slightly glossy surfaces tend to degrade scan quality, while reflective and transparent surfaces cannot be scanned at all without a matte coating.
Use a temporary matte powder to improve the scan accuracy of your object.
Use a high accuracy 3D scanner to capture the important sections of the part. Tabletop structure light or laser scanners are the right tools for the job, with accuracy of ±100 or better.
Learn more about how to choose the right 3D scanner for your application in our 3D scanning white paper:
Note: You may need to orient and re-scan your object several times if the object has deep recesses.
Some scanners produce extremely large mesh files, which will make later steps grind to a halt.
Scanner software repairs small gaps and simplifies the scan, making the data more manageable in CAD. Try to reduce the model as much as possible without destroying important details.
Tip: If you need more control, Meshmixer is a great choice for refining scanned meshes.
Import the mesh into CAD software equipped with reverse engineering tools. Geomagic for Solidworks is a powerful choice for resurfacing complex, organic shapes.
If you are reverse engineering a part with simpler flat surfaces, Xtract3D is a less expensive, lightweight alternative.
In this step, move and rotate the scan mesh into alignment with any existing design components.
Tip: Make drawing easier by rotating and aligning your scan to face the orthographic view directions.
There are three paths to extract the shape of the scan in order to create a solid model that is editable with CAD tools: semi-automatic surfacing, automatic surfacing, and manual redrawing.
Semi-automatic surfacing
Complex curved surfaces are difficult to manually draw, so you may choose to use semi-automatic surfacing. This function generates surfaces that fit to detected regions of the scan. By varying the sensitivity of the surface detection function, different surfaces will be found.
Tip: Geomagic for Solidworks detects surfaces on the scan to fit 3D curves. Use a “brush” to manually add or subtract areas on the scan from each region.
You may need to repeat this process several times with different sensitivity settings to detect all your surfaces. These surfaces can then be trimmed and knit together to create an editable solid.
Use semi-automatic surfacing to re-create curved shapes when you want maximum editability later on, and when sharp edge accuracy is important.
The re-surfaced result, after trimming.
Automatic surfacing generates a solid model from any watertight scan. You can use standard CAD tools to subtract and add to this auto-surfaced body, but it will be more difficult to move basic features around on the body itself.
You may not need control over edge placement. For example, if you are scanning a part of the human body to create custom ergonomically-shaped products, or want to create a jig to precisely or repeatably modify a handmade object. In these cases, automatic surfacing is a great way to save modeling time.
Note: Compare the results of a automatic surfacing to semi-automatic surfacing: some accuracy is lost, especially around sharp edges.
For simple features such as bosses, holes, and pockets, it’s usually fastest and most accurate to redraw the features using the scan model as a reference. Reverse engineering software allows you to create sketch planes aligned with flat surfaces on the scan and to extract cross sections from the scan mesh, which helps you match the shape of the original object.
Once the scan has been converted to a solid, it can be subtracted from another solid body to create a jig that securely holds the original part.
The design of the new gauge component also references the dimensions of the scan, using curves extracted with semi-automatic surfacing.
Printing the jig on a Formlabs stereolithography (SLA) 3D printer gives you a high degree of accuracy comparable to the output of engineering-grade 3D scanners. Use Formlabs Rigid 4000 Resin for its strength and precision.
Once these steps are complete, the 3D printed jig is ready to use to assemble the new gauge onto the OEM air vent.
The final 3D printed assembly jig, printed in Rigid 4000 Resin.
How to Choose the Best 3D Scanner to Use With Your 3D Printer
3D scanning has an important place at the beginning and end of 3D fabrication workflows. Engineers, product designers, and researchers use 3D scanners as a faster and more efficient way to start constructing digital models, whether by incorporating existing designs via reverse engineering, digitizing hand-sculpted clay designs, or referencing the exact shape of the human body.
After fabrication, 3D scanning can support quality control and help to verify the accuracy of a 3D printed part, or, after the part has been used, a scanner can reveal how it’s performed—a scan of a deformed part can show you where to reinforce the design in the next revision.
With such a wide range of product options from handheld 3D scanners to desktop 3D scanners, it can be difficult to choose the best 3D scanning system that’s right for your application and budget. In this post, we explore the most important factors to consider when purchasing a 3D scanner and showcase some of the key applications that are empowered by combining 3D scanning and 3D printing.
White Paper
3D scanning and 3D printing workflows can be applied to replication and restoration, reverse engineering, metrology, and more. Download our white paper to explore these applications and learn how to get started.
Download the White Paper
There are multiple scanning technologies currently on the market, all offering their own advantages and weaknesses.
Laser triangulation uses light projected onto the object to take up to millions of measurements (dots) per second. The light reflected from the dots back into the scanner’s sensor to help it capture the geometry of the object. These types of scanners are often the most accurate, and are great for highly detailed parts that have opaque surfaces.
Laser triangulation scanners do have limitations. For example, this technology is not used in most portable scanners because the laser dots need to project from a stable source, and the source has to be kept a close distance from the scanned object. Laser triangulation scanners don’t always work on transparent or shiny surfaces either. Typically, they require reflective markers to be applied onto the object, which need to be removed after use and can be an obstacle depending on the object being scanned.
Finally, the laser dots can be harmful to human eyes, so it is important to use extra safety precautions when scanning body parts with a laser triangulation system, or to check with your scanner manufacturer to make sure the device is eye-safe.
Structured light scanners (also known as white light scanners or blue light scanners) generally use a projector with two cameras at angles on either side. A pattern of light is projected and laid over the component being scanned, the cameras capture the ways in which the object deforms the light pattern, and then multiple images are integrated into a single 3D snapshot.
Structured light scanners are available in both stationary and portable format—the technology is the most commonly used process for handheld 3D scanners. Structured light scanners are far more common in medical applications, since it is safe to use on both humans and animals and excels when an object is not perfectly still. Traditional white light scanners have been slower to scan than laser triangulation scanners.
Structured light scanning is the most commonly used technology in handheld 3D scanners.
Depth-sensing cameras project a field of dots in infrared (IR) to sample a 3D scene. Depth-sensing cameras are simple to use and are the least expensive scanning option, but their accuracy and resolution are low, and fine details are sometimes lost. Large objects may be captured with depth-sensing cameras, but accuracy declines with increased distance from the subject and at steeper angles to the camera.
Photogrammetry means the act of deriving precise measurements from photographs. It involves taking a set of overlapping photos of an object, building, person, or environment, and converting them into a 3D model using a number of computer algorithms. This is the most commonly used method when creating a 3D scan with a smartphone, since modern phone cameras are capable of capturing and combining a large numbers of photos. Photogrammetry should be considered the least expensive and least accurate method for creating 3D prints, and is not suitable for serious business applications.
LiDAR (light detection and ranging) sensors can be found on some higher-end smartphones and tablets, such as the latest versions of the iPhone Pro and the iPad Pro. This has made the iPhone and iPad viable scanners for those with only occasional scanning needs, offering performance a step above devices that only have access to photogrammetry. Applications that generate 3D mesh files via your smartphone’s or tablet's camera should be seen as the floor for entry-level scanning; users should expect additional work in their CAD software to remove gaps in meshes and improve the 3D model for applications like sending it to a 3D printer. Smartphones use fewer light points when scanning objects, resulting in less detail than a true, stand-alone scanner. iPhones are good substitutes for scanners if you have significant CAD design ability or need to transfer basic models into a digital space.
WEBINAR
Watch this webinar with Peel 3D to explore how to integrate 3D scanners into your 3D printing workflow to elevate your product development process.
Watch the Webinar Now
Scan accuracy varies considerably between scanner technologies, and higher accuracy generally comes at a higher cost. The required tolerances of your final part can be a helpful guide for determining your accuracy requirements for a 3D scanner.
High Price, Highest Accuracy ($15,000 and more) | More Affordable, High Accuracy ($12,000 and under) | Low price, Low Accuracy |
---|---|---|
Zeiss T-Scan Hawk Scantech Simscan EviXscan Optima+ M Creaform HandyScan 307 Silver Series | peel 3d peel 1, peel 2 & peel 2-S FARO Freestyle 2 Polyga Compact S1 | iPhone Pro and iPad Pro Structure Sensor Matter and Form 3D Scanner V2 Revopoint POP |
With accuracy in the range of 0.1 mm or better, laser and structured light scanners are a good fit for professional applications and alongside high-resolution 3D printers. Formlabs stereolithography (SLA) 3D printers (such as the Form 3+) produce parts at a similar accuracy, and with a similar printable area, to the scan volume of many desktop 3D scanners.
Besides the accuracy between measured points and their actual location, scanners also vary in terms of resolution, which is the distance between captured points at a given scan distance. This means that details on the scanned object that are smaller than the scanner’s resolution won’t be captured. For example, a highly accurate 3D scanner with a lower resolution might detect the general shape of jewelry on a statue, but not clearly show individual details on a ring or necklace. Depending on your project requirements, this may or may not be a dealbreaker.
An easy way to remember these metrics is: accuracy is the measurement error between the part and digital value. Resolution refers to the density of measurements.
Accuracy can mean slightly different things depending on the manufacturer and 3D scanning technology. For example, the accuracy of handheld scanners depends on the distance to the subject and the quality of scan reconstruction, while desktop scanners have consistent accuracy within the constrained scan volume. If you are considering buying a 3D scanner for precise measurement, make sure to compare like to like.
In general, structured light scanning provides the best resolution and accuracy when compared to laser scanning. For some artistic use-cases for 3D scanning you may need a lot of detail, while overall accuracy is less important—especially if you don’t require your part to fit precisely with other parts in an assembly. In these cases, photogrammetry is an excellent low-cost option to explore.
Both depth-sensing cameras and photogrammetry are a good solution for scanning large objects in order to create 3D printed scale models and also offer enough accuracy for capturing the shape of the human body.
Several entry-level laser scanners are available using technology similar to higher-end systems. These scanners are a great way to start replicating small objects at 1:1 scale. As one would expect, the accuracy of entry-level laser 3D scanners is lower than a high-end scanner, but they can easily provide enough detail to replicate small decorative objects and figures where accuracy is not critical.
If you only have occasional 3D scanning needs, digitization services can scan your object, as well as perform CAD translation and accuracy inspection.
The area that a 3D scanner can capture varies significantly between scanners. Find a scanner that fits your size and resolution requirements without too much overhead, as cost typically increases with scan volume.
Handheld scanners can be manually moved around the object and have fewer size constraints than desktop models. Most inexpensive handheld scanners can capture objects from the size of a basketball to an entire room. High-end handheld scanners have an even wider range, and fill the niche for all objects that require precise measurements, but cannot fit in a desktop scanner. Handheld scanners are also able to capture objects nearly instantaneously, which makes them well-suited for taking human measurements (where the subject is not perfectly still) for ergonomics and medical applications.
If the area of the model can’t be seen by the scanner, it will cause a gap in the model. You can automatically repair small missing sections with most scan software programs to create a 3D printable model. However, repaired holes are rarely accurate to the original object. For parts that demand close to perfect accuracy, auto-repair of gaps or holes will not be sufficient. Read our MeshMixer tutorial for advanced tips to edit and repair 3D files for 3D printing.
Many scanners use turntables to increase what the scanner can see. The sophistication of a scanner’s turntable affects how easily and completely the object is captured: some scanners have the ability to move the object around multiple axes, imaging the object from more angles. This feature is important when reverse engineering plastic parts with deep recesses and ribs, which are impossible to capture from a single angle.
Scanners may rotate the object to capture occluded areas. Red regions are occluded and will be missing in the scan. Areas with deep relief are difficult for a single axis turntable to fully capture due to occlusion.
Cost concerns are straightforward; how much you are willing to spend on a scanner will reflect your business’s budget and how often the scanner is going to be used. Higher cost scanners will be able to capture small objects and create highly-detailed meshes that don’t require significant touch-ups in CAD software. Handheld scanners are also often on the higher end of the price range, due to their portable nature. The low-cost scanning market offers a wide range of options, but you have to know what to look for.
Use this flowchart to determine what scanner you need based on accuracy, scan volume, and budget.
Download the high-resolution version of this infographic here.
A 3D scanner expands the capabilities of a 3D printer, allowing you to replicate the shape of almost any object. Together, the two technologies create a powerful, digital workflow that can simplify and sophisticate processes in a range of industries.
The output from a 3D scanner is a mesh of triangles representing the surface of an object at a real-world scale. In some cases, the scan can be used directly to replicate objects without any CAD work. A hybrid workflow can also be powerful, where solid CAD models are combined with scanned 3D models. For example, customized ergonomics capture a physical imprint of a part of the human body, and integrate them with a mechanical design.
3D scanners are also valuable tools for measuring the accuracy of manufactured objects. Many factors affect 3D print accuracy, and metrology-grade 3D scanners provide a clear picture of how a material performs for demanding applications.
A variety of powerful workflows are enabled by combining a 3D printer and a 3D scanner:
- Reverse engineering to create replacement parts, products with custom ergonomics, and more.
- Replication and restoration of parts, especially in art and jewelry.
- Consumer audio for creating custom earpieces.
- Dental and medical applications, and how 3D scanning is enabling patient-specific workflows.
- Metrology to validate and measure the accuracy of manufactured objects.
Webinar
Watch this webinar for a detailed look at how to start using 3D scanning to improve part design and production when paired with reverse engineering CAD and 3D printing.
Watch the Webinar Now
3D scanners and 3D printers are essential parts of digital workflows across industries. Download our white paper or watch our webinar to get a detailed look into how to start using 3D scanning to improve part design and production and learn how to pair 3D printing and 3D scanning to empower a variety of workflows in engineering, product design, and more.
Learn more about the 3D printer side of the equation: get to know stereolithography (SLA) and selective laser sintering (SLS) 3D printing technologies and see Formlabs advanced 3D printing materials for yourself with a free sample 3D printed part.
Explore Formlabs 3D PrintersRequest a Free Sample Part
Top Ten 3D Scanners from $100 to $100,000 / Sudo Null IT News There are several ways for you: you can of course create your 3D model from scratch in a 3D modeling program or find a suitable one on the Internet, but you can also scan an existing object! The purpose of this review is to help you understand the variety of 3D scanners available and offer the best in every price segment from a photogrammetric smartphone app to professional 3D scanners.
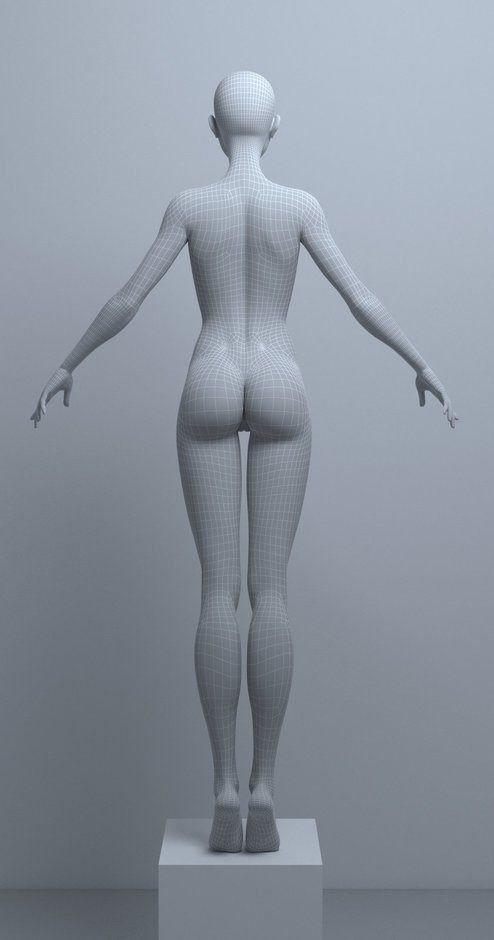
Scanners are listed in ascending price order so you can choose the one that suits your budget and use the resulting 3D models for both 3D printing and animation.
If you are not satisfied with the proposed solutions, there is an extended overview at this link.
3D scanner in hand:
1. Best smartphone app: Autodesk 123D Catch (free)
Autodesk 123D Catch is a free photogrammetric application. It allows you to create a 3D model from photographs of an object taken from different angles. You can use it to scan objects, people, and even the landscape. For some applications, if you don't need perfect accuracy, you don't need special equipment. This application actually provides quite good detail and is easy to use. However, it will take you at least 30 minutes for the app to process your photos as the processing takes place on the server and it takes time to send them.
2. Best DIY 3D Scanner: Kinect ($99.99)
The Xbox Kinect is designed to expand your gaming experience. It is not designed for 3D scanning, but you can easily find manuals and third party software (like ReconstructMe) to turn it into a 3D scanner. If your arms are growing out of your shoulders, this is an interesting and inexpensive solution for 3D scanning.
Price: $99.99
Resolution: 0.051mm
)
This scanner can be attached to your tablet or phone (generally designed for iPad, but can be adapted to other devices). Lightweight and easy to use, with a very good resolution. Suitable for large items (can scan a full-length person) and outdoor scanning. You will be able to use it with software running on Occipital's SDK. This will increase the resolution and give you access to special features like room scanning. It probably won't be something you'll use for 3D printing, but it's interesting for game development, for example.
Price: $ 379
Resolution up to: 0. 5 mm
accuracy to: 4 mm
4. The best of cheap manual 3D scanners: Cubife ($ 399)
3D 3D-scanners can be quite affordable and easy to use if you choose from inexpensive portable models. Cubify fits these criteria very well and has a relatively good resolution. But still, its capabilities are not enough for texture scanning and it is better to use it for subsequent 3D printing of one-color models.
Price: $ 399
Resolution: 0.9 mm
Resolution at a distance of 0.5 m: 1 mm
3D scanner on the table:
5. Best and cheapest table 3D 3D 3D 3D 3D 3D 3D- Scanner: Matter and Form ($519)
If you're looking to take your quality to the next level, you can purchase a desktop 3D scanner. This model is compact, easy to use, and delivers good resolution, especially considering the price (not your go-to option if you're looking for perfection, but great for educational and demo purposes). The scanning process takes place with the help of a laser and a rotating platform. The scan takes about five minutes and simultaneously reads the texture of the object.
Price: $ 519
Resolution: 0.43 mm
accuracy: ± 0.25 mm
6. The best device "two in one": XYZPRINTING DA VINCI 1.0 ($ 600)
is inexpensive combines a 3D scanner and a 3D printer. The quality of the models is not too high, but the price is very low for such a combined device. This makes the XYZprinting Da Vinci the easiest solution for beginners who want to get into the world of 3D scanning-printing.
Professional 3D scanners:
7. Best value for money portable 3D scanner: Fuel3D Scanify ($1490)
Very easy to use, intuitive, and feels good in the hand, this scanner delivers good accuracy and texture quality. The only limitation is that the size of the scanned area is limited, which is great for small objects, but for scanning a full-length person, for example, it will not work.
Price: $ 1490
Resolution: 0.35 mm
accuracy: to 0.3 mm
8. Best price The scanner uses a different scanning technology than others. Instead of a dual laser scanning system, it uses a structured light source and cameras for fast scanning with very fine detail down to 0.06mm! The scanner comes with DAVID Pro Edition 3 software that works with OBJ, STL and PLY 3D file formats that can be exported to other programs for further editing.
Price: $ 3995
Resolution: 0.06 mm
accuracy: 0.5% of the size of the object
9. The best table professional 3D-scanner: SolutionIX REXAN 4 ($ 79 900)
The 3D scanner and its price provides much better scanning quality. Solutionix Rexcan is equipped with two cameras for greater accuracy. It uses optical phase shift triangulation technology and two high-resolution CCD cameras to provide high-precision data.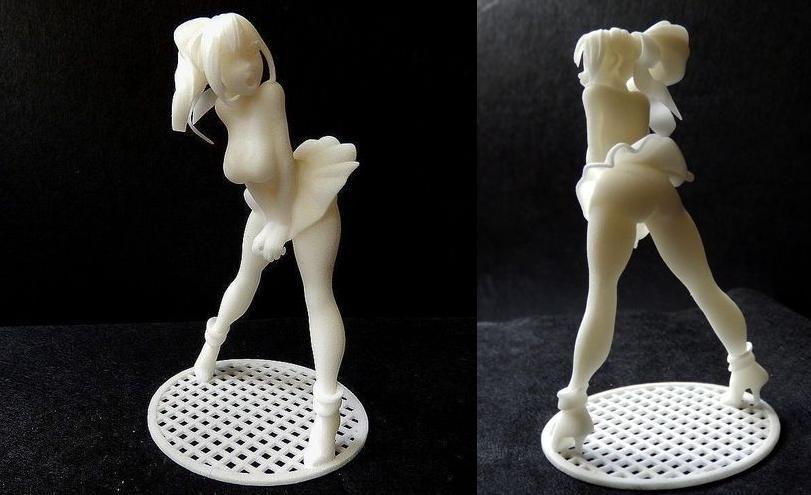
Price: $ 79 900
accuracy: from 0.03 to 0.71 mm
10. Best professional manual 3D scanner: Metrascan 750 ($ 50,000 - $ 100,000)
Creaform Metrascan 750 is a complete professional, production solution for accurate 3D scanning. It is light, accurate, fast, and scans objects of any surface quality, with any texture with excellent accuracy.
Price: $79900
Resolution: 0.050 mm
Accuracy: Up to 0.03 mm
We hope this was a useful read and you found a 3D scanning solution suitable for your needs and your budget! If you want to learn more about photogrammetry, you can read this article.
Good luck with your 3D scanning!
3D scanning of objects - accuracy and quality of 3D models
3D scanning of objects
One of the components of 3D technologies is the 3D scanning technique, which allows you to quickly and easily obtain a digital model of the desired product. In short, 3D object scanning is the process of transforming the physical form of a real object into a digital form. This preserves the texture and even the color of the original sample. Thus, a 3D model of the required product can be obtained without any extra effort. 3D scanning of objects helps to prepare the necessary model for 3D printing and in some cases can play a decisive role in building a digital product.
The key device in the process of 3D scanning is a 3D scanner - a device that reads the physical parameters of objects and creates a 3D model based on them.
3D scanning of objects can be useful in the design of any complex elements, 3D modeling of which manually is extremely laborious. In particular, 3D scanning is useful for modeling various fixtures, components, main and spare parts. Often it is used in the absence of drawings and other documentation for the product, as well as when it is necessary to convert figured surfaces into a digital form, including art forms and casts.
3D scanning process
The 3D scanning process generally resembles a human three-dimensional vision system. The process of obtaining data with a 3D scanner resembles the formation of a three-dimensional image seen in the human brain. To do this, the 3D scanner compares two images that are offset from each other. The required accuracy of building a 3D model is achieved through the use of additional technological methods, for example, a periodic flash or laser illumination.
As for scanning accuracy, it depends both on the specific device and on the characteristics of the original product. It is possible to carry out 3D scanning of objects from 1 cm (with all the details), the maximum dimensions are not limited. To achieve the best detail, upon completion of the 3D scanning process, the 3D model is subjected to additional refinement by a specialist. Thus, thanks to 3D scanning of objects, digital models are almost flawless. Error for 3D scanning of objects with a surface area of 100 cm 2 is 1 mm and can be eliminated with subsequent refinement. 3D scanning of large objects can be implemented by batch processing of object photos from all sides.
Other questions and answers about 3D printers and 3D printing:
- Basics What is 3D printing?
- Basics What is a 3D model?
3D scanning methods
For a better understanding of the technology, it would not hurt to list the existing 3D scanning methods. There are two of them: contact and non-contact. The first one requires direct contact of the 3D scanner with the object. The non-contact method divides peripherals into two types:
- Active 3D scanners that emit a beam of directed waves onto an object and record their reflection. Possible types of radiation include x-rays, ultrasound, and light;
- Passive 3D scanners that capture ambient radiation reflected from an object, most often light.
All 3D scanning methods have their advantages and disadvantages, which affect the cost of 3D scanners, the speed and accuracy of scanning, as well as the range of objects available for scanning. When buying your own 3D scanner, it is recommended to study this issue in more detail, but it is better to get high-quality advice from professionals. The 3DDevice team is ready to help you with this and recommend the best 3D scanner model.
3D scanning and 3D printing
3D scanning and 3D printing complement each other, since the scanned 3D models are most often used for subsequent reproduction on a 3D printer. At the moment, 3D scanning is used for a variety of purposes and industries. Using a 3D scanner, 3D models of real people are created, which can then be reproduced through full-color 3D plaster printing. A more promising use of 3D scanning is in medicine, where it is used to create ultra-precise surgical models and implants. You can read more about our contribution to this branch of medicine here. Also interesting is the direction of using technology in the production of individual footwear and clothing.
In general, the possibilities of using 3D scanning of objects are quite enough.