Rubber filament for 3d printers
Ultimate Materials Guide - 3D Printing Flexible Filament
Overview
Flexible filaments are made of Thermoplastic Elastomers (TPE) which are a blend of hard plastic and rubber. As the name suggests, this material is elastic in nature allowing the plastic to be stretched and flexed easily. There are several types of TPE, with Thermoplastic polyurethane (TPU) being the most commonly used among 3D printing filaments. In many cases, these terms are used interchangeably, along with popular brand names such as Ninjaflex. The degree of elasticity in the plastic depends on the type of TPE and the chemical formulation used by the manufacturer. For example, some filaments can be partially flexible like a car tire but others can be elastic and fully flexible like a rubber band. This guide will cover tips to help you with both of these variations of flexible filaments.
- Flexible and soft
- Excellent vibration dampening
- Long shelf life
- Good impact resistance
- Difficult to print
- Poor bridging characteristics
- Possibility of blobs and stringing
- May not work well on Bowden extruders
Hardware Requirements
Before 3D printing with flexible filaments, make sure your 3D printer meets the hardware requirements listed below to ensure the best print quality.
Bed
Temperature: 45-60 °C
Heated Bed Optional
Enclosure Not Required
Build Surface
PEI
Painter’s Tape
Extruder
Temperature: 225-245 °C
Direct Drive Extruder Recommended
Cooling
Part Cooling Fan Required
Best Practices
Flexible filaments come with many unique challenges that you want to be aware of. These tips will help you reduce the chances of common 3D printing issues such as clogging, kinking, and stringing.
Use Direct Drive Extruders
While some partially flexible filaments work fine with Bowden Extruders, most fully flexible filaments require a Direct Drive extruder for best results. The distance between the drive gear and the melt zone of the hot-end needs to be as short as possible to efficiently feed the filament into the nozzle. Additionally, the pathway through which the filament travels into the melt zone should have tight tolerances to prevent the filament from kinking or coiling inside. For these reasons, it is typically much easier to print flexible filaments with a Direct Drive extruder versus a Bowden extruder. If you are unsure about your 3D printer’s capabilities, you may want to check with the manufacturer to see if the extruder has been approved for use with flexible filaments.
Use Slow and Consistent Feed Rates
Flexible filaments typically print best using a slow and consistent feed rate. Because the material is elastic, it can be very difficult to control sudden changes in the print speed. Higher print speeds can cause the filament to compress and will most likely result in a jam. Slow and steady is the best approach. Simplify3D provides all of your feed rate settings on the Speeds tab of your process settings so that you can easily configure these values. Finding the optimal print speed for your material can take several attempts based on trial and error. We have seen that speeds of 1200 mm/min (20 mm/s) can be a good starting point for most materials.
Reduce Resistance from the Filament Spool
A few tweaks to your material spool can also make a big difference with flexible materials. Typically, your extruder will pull the filament into the nozzle, forcing the filament spool mounted on your printer to unwind a bit of plastic in the process. However, because flexible materials are elastic, this will stretch the filament out as it is being pulled in and can actually result in under-extrusion. Try mounting the spool above your printer so that the filament unwinds in a downward direction which can reduce the resistance. It can also be incredibly helpful to mount the spool’s hub on a bearing to allow the spool to spin as freely as possible.
Tune Your Retraction Settings
The elastic nature of flexible filament makes it sensitive to quick movements such as retractions. In order to successfully print the filament, you will need to optimize your retraction settings to reduce these movements. While you are first starting with this material, we would recommend disabling retraction completely. You can make this change in Simplify3D on the Extruders tab of your process settings. With retraction disabled, you can focus on finding the perfect speed and extrusion rates that allow you to reliably print your models. After you are more confident in these settings, you may wish to add a very small amount of retraction with a slower retraction speed to help with any potential oozing from the hot-end. Simplify3D also includes a unique option called Coasting, which will automatically help lower the pressure in the nozzle when you approach the end of a segment, which can significantly reduce blobs and stringing with these materials. If you want more information about other options that can help reduce hairs and stringing on your prints, we have an entire section on our Print Quality Guide dedicated to that issue: How to Reduce Stringing and Oozing.
Optimize Your Travel Movements
Retractions can be particularly troublesome for flexible materials, so it is typically best to minimize the number of retractions required for your print. Simplify3D has a great feature that was built specifically for this situation. Instead of moving in a straight line from point A to B, the software will actually choose a completely new path when moving between these points, with the goal of staying within the interior of your object so that there won’t be any oozing or stringing. With this unique feature enabled, you can greatly reduce the amount of retractions required for your print and significantly improve your print quality. To use this feature, click on the Advanced tab of your process settings, and enable the “Avoid crossing outline for travel movement” option.
Pro-Tips
- Optimize the feed rate by printing at lower layer heights in the 0.1mm – 0.2mm range. The lower layer height requires less plastic, so it allows your extruder to use a lower feed-rate, relieving the burden on the filament.
- Try to avoid using rafts with flexible materials, as the base layers of the raft have higher extrusion rates which may create issues.
- If you are designing a flexible part that needs to fit on top of another object, try using a negative tolerance between the parts so that the flexible part will need to stretch to fit over the other object snugly.
Get Started with Flexible Filaments
Now that you’re ready to start printing with flexible materials, we have a few tips to help you get started. View some typical applications below, try out a few of our sample projects, or choose a popular filament brand to purchase for your next project.
Common Applications
- Vibration dampening
- Grip Sleeves
- Phone cases
Sample Projects
- RC Car Tire
- Phone case
- Bike Handle
Popular Brands
- NinjaTek Ninjaflex, Armadillo, Cheetah
- Polymaker PolyFlex
- eSun TPE
- Sainsmart Flexible TPU
3D Print Rubber - 3D Printing Gaskets
Rubber and rubber-like materials are everywhere in modern industry. Soft materials like latex, silicone, and thermoplastic elastomer are useful in applications that demand flexibility and durability for industrial parts and consumer goods alike.
While rubber manufacturing has historically been the domain of casting and injection molding, modern advances in 3D printers and 3D printed materials have made additive manufacturing the ideal solution for producing small to medium quantities of rubber-like parts.
Our 3D printed rubber services can manufacture high-quality rubber-like parts in as few as two days―all you need is a 3D model! Start your project by getting a quote or keep reading to learn more.
Get a quote for your project using our quoting tools. Our engineers will review your project and get back to you 24 hours or less. 3D printed rubber parts ship in as few as two days!
3D Printed Rubber Applications, From Prototyping to Production
3D printed rubber parts can be used in place of molded rubber for just about any application. Like other methods of 3D printing, rubber prints accurately produce complex internal geometries like lattices and tubes at no extra cost, easily achieving designs that would be impossible with other types of manufacturing.
And because 3D printing doesn’t require any costly molds or tooling, 3D printed rubber parts can be manufactured in just a few days compared to multiple weeks of lead time for injection molding. This combination of high agility and no start-up costs allows rubber 3D printing to excel for both prototyping and small- to medium-sized production runs.
3D printed rubber is ideal for:
Prototypes
Gaskets
Seals
Hoses
Grips
Lids
Plugs
Connectors
Footwear
Tires
Medical Devices
Sporting Goods
Advantages of 3D Printed Rubber vs.
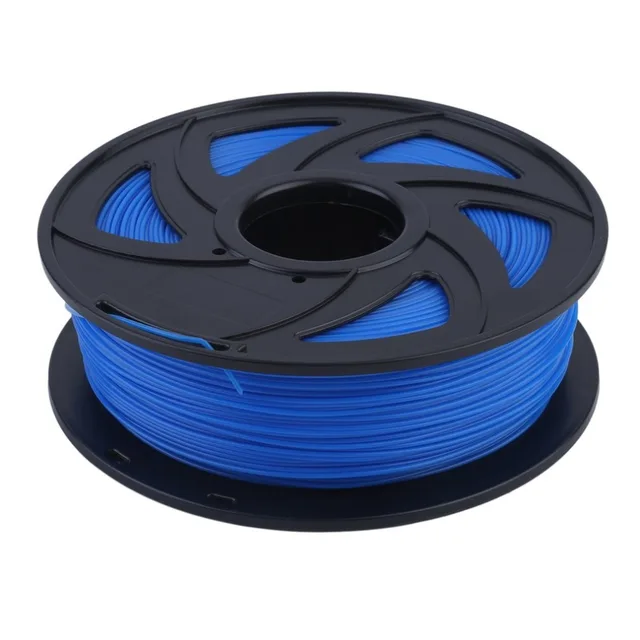
Traditionally, rubber manufacturing has required injection molding, casting, or sheet lamination. Rubber-like materials are far too soft to machine, and 3D printing was restricted to harder plastics for most of its development. Now, new developments in 3D printers and materials have opened up a wide range of new possibilities for 3D printed rubber products. So how does 3D printing compare to casting or injection molding for manufacturing rubber?
Short Lead Times and No Setup Costs
Injection molding requires machined metal molds that cost tens of thousands of dollars and take months to produce. Any design changes require new tools, making adjustments extremely expensive and time-consuming.
In contrast, 3D printing requires no tooling or other setup costs and can begin production immediately. This leads to parts that can be manufactured in as little as one day and much greater affordability at low quantities, making 3D printing Moreover, design changes are easy and can be executed at no additional cost.
The Best Choice for Rubber Prototypes
When it comes to product development, 3D printed rubber is a godsend. Even under the most ideal conditions, traditional technologies take weeks of lead time and tens of thousands of dollars for each new design.
Because 3D printing doesn’t require any tooling or setup, 3D printed parts can quickly be designed and redesigned at no additional cost. This agility has made 3D printing an indispensable part of prototyping and product development.
A Question of Quantity
As a result of these differences in lead times and setup costs, 3D printing is much more economical for small- to medium-volume production, while casting and injection molding provide greater value for productions of 1000 parts or more.
Although metal molds are expensive, molded parts become very cheap to produce once the tooling is made. When those initial costs are spread out over thousands of parts, individual part costs plummet, making injection molding the least expensive technology around for high-volume manufacturing.
3D printing, on the other hand, generally stops providing additional per part savings once part quantities exceed the capacity of a single machine. As a result, 3D printing has a much flatter cost curve that makes it a great option for small to medium quantities but significantly less economical for large production runs.
Unlimited Design Possibilities
Rubber 3D printing can easily achieve complicated designs that would simply not be possible with other manufacturing technologies. From interior cavities and lattices to variable wall thicknesses, organic shapes and built-in hoses—all of which are difficult or impossible to create with injection molding—3D printed rubber parts unlock endless new design options. You can even combine multi-part assemblies into single pieces, saving costs and improving functionality.
Plus, 3D printed parts can be highly customized, down to single parts at a time, without additional costs. This is especially useful for industries like medicine or athletics that have a high demand for products customized to each individual user. Needless to say, this would be extraordinarily expensive with casting or injection molding.
To learn more about the unique design capabilities of 3D printing, check out our Design for Additive Manufacturing (DfAM) Guide.
Is It Really Rubber?
3D Printed Rubber Materials
The answer to whether 3D printed rubber is really rubber depends who you ask. There are a lot of materials that are referred to as rubber: thermoplastic polyurethane, thermoplastic elastomer, silicone, and, of course, natural rubber!
Natural rubber, also known as latex, cannot be liquefied and re-solidified in the manner required by 3D printers. However, thermoplastic elastomers can achieve similar levels of flexibility and softness to rubber and have the thermal properties necessary for 3D printing.
The most effective rubber-like materials for 3D printing are thermoplastic polyurethane (TPU) and thermoplastic elastomer (TPE). It’s important to note, however, that both TPU and TPE refer to multiple materials. In fact, TPU is really a type of TPE―distinguished by its use of polyurethane and increased hardness.
Thermoplastic Polyurethane (TPU)
Thermoplastic polyurethane (TPU) is valued by engineers for its flexibility and strength. It’s in mass production consumer products ranging from automobiles to tennis shoes. Not only does TPU’s hardness (Shore 85A to 95A) make it easy to manufacture, but it also provides higher abrasion, chemical and thermal resistance. Moreover, its resistance to oil and grease makes it a great fit for hoses, gaskets and seals. While not as soft as natural rubber, printed TPU can achieve thinner walls than molded parts (0.5mm or 0.020″) to create a similar level of flexibility.
TPU can be 3D printed with Multi Jet Fusion and is widely used in transportation, medicine, home goods, footwear and apparel, heavy industrial, consumer electronics, and more.
Rubber Printing Services
Multi Jet Fusion (MJF)
Multi Jet Fusion 3D printing is the fastest, most affordable, and most effective option for most 3D printing projects. It is also the newest printing technology to allow rubber printing, with TPU01 options available in black or gray.
MJF prints combine industrial strength, accurate fine details and a high-quality finish to create parts that are equally suited to industrial parts and commercial products. With lead times as little as one day, MJF is the premier printing option for prototypes and small- to medium-sized production runs.
Start Rubber 3D Printing Today
If you need rubber manufacturing for your business, RapidMade can help you take your projects from 3D models to high-quality 3D printed rubber parts in as few as two days. When you work with RapidMade, you get a team of 3D printed experts dedicated to helping you succeed.
Learn more about our 3D Printing Services and get started today by requesting a quote. We’ll review your project and get back to you within one day!
Techno Print 3D Company
This is our first review of the most popular and inexpensive 3D printers for 2020. The list will include the best-selling devices in two price ranges (up to 30 tr and up to 60 tr). Printers working with both plastic filament (FDM) and photopolymers (LCD/DLP) will be presented. This list will always be up to date, as it is periodically updated and supplemented. Read more→
The Chinese company Dazz3D announces the launch of the project on KickStarter and accepts pre-orders for Dazz3D Basic and Dazz3D Pro 3D printers. These revolutionary new devices are aimed at both the professional and amateur markets. Read more→
We all know that precise calibration of the 3D printer desktop is the foundation and the key to successful printing on any FDM printer. In this article we will talk about the main and most popular ways to level the "bed". So, as mentioned above, 3D printing without desktop calibration is impossible. We face this process Read more→
It's hard to go through a day today without hearing about 3D printing technology, which is bursting into our lives at an incredible speed. More and more people around the world are becoming addicted to 3D printing technology as it becomes more accessible and cheaper every day. Now almost anyone can afford to buy a 3D printer, and with the help of Read more→
The FormLabs Form 2 and Ultimaker 3 are perhaps the most popular 3D printers today, capable of high quality printing with incredible surface detail. Moreover, these two devices use completely different technologies, and therefore, there are a lot of differences between them. Many will say that it is wrong to compare them or Read more→
XYZprinting, best known for its daVinci line of desktop 3D printers, is bringing five new devices to the professional and industrial environment. One will use laser sintering technology, the second full color inkjet printing and three DLP machines. First of all, the novelties will be of interest to dentists and jewelers. Read more→
Cleaning the nozzle of a 3D printer is a fairly common process that any user of such a device has to deal with. This is not at all a complicated procedure that anyone can handle. You can complete this task in 15 minutes, using only handy tools and accessories. Read more→
Acetone steam polishing of ABS plastic is a process for smoothing the surface of 3D printed models. The result of this treatment makes your printed products look as if they were made by a professional mold casting method. If you want to understand how this is done correctly, then read this article. Aceto Read more→
Black ELASTAN D100 flexible material for 3D printing, rubber thread for 3D printer.
Options are available:
Ø1.75mm weight: 0.125kg
Ø1.75mm weight: 0.5kg
Ø1.75mm weight: 0.75kg
Ø1.75mm weight: 2.5 kg
- Description description description description description
- Features
- Print Modes
- Features
Benefits:
- high strength and elasticity;
- high wear resistance;
- high resistance to impact loads and hydroabrasive wear;
- excellent resistance to oils, fats and many solvents;
- the product can be subjected to repeated deformations without whitening and delamination of the model;
- good weather resistance;
- product operating temperature: -40 +120°С.
Print modes:
Options | Meaning |
---|---|
Extruder temperature | 230-260°C |
Platform temperature | 90-110°C |
Airflow model | need |
Print speed | 30-80 mm/s |
Printer type | closed |
For successful 3D printing with our ELASTAN monofilament, it is necessary to take into account the characteristics of the ELASTAN material and the properties of the specific ELASTAN monofilament. Therefore, we recommend:
- monofilament spools be stored in vacuum containers to prevent them from absorbing moisture from the air;
- the use of a closed 3D printer contributes to the slow cooling of the model, which prevents the deformation shrinkage of the material during printing.
Specifications:
Options | Meaning |
---|---|
Thread diameter, mm | 1.75/3.00 +/-0.05 |
Ovality, mm | +/-0.02 |
Linear mass, m/kg (length 1kg 1.75mm) | 325-340 |
Bending resistance times | - |
Print Technology | FDM |
Mechanical data:
Options | Meaning | ||
---|---|---|---|
D70 | D100 | D160 | |
Density, g/cm 3 | 1.15 | 1.18 | |
Operating temperature, °С | -40 - +120 | -40 - +100 | -40 - +80 |
Tensile strength, MPa | 57 | 68 | 55 |
Elongation at break, % | 370 | 436 | 680 |
Bending strength, MPa | 78 | 46 | 46 |
Water absorption, % 24h/23ºC, % | 1 | 1.![]() | 1.5 |
Elastan is a highly elastic material that is well suited for 3D printing of elastic products. Products from this material can be used in many aggressive environments. Elastan has a wide operating temperature range of -40 +120 °C, tolerates alternating loads well. Elastan hardness can vary over a wide range - from 40 (Shore A) to 95 (Shore D). Elastan is a structural plastic that is ideal for 3D printing machine parts and mechanisms subjected to dynamic loads. Products printed on a 3D printer from Elastan can be used in almost all areas of industry, for example, they can be decorative or protective coatings, parts of low-power machines (shafts, rollers), insulators, original elastic packaging and containers. The high wear resistance of this material allows it to be used for printing shoes or soles.
Tags: Elastan, Elastane, 1.