Pc power supply 3d printer
ATX supplies are super useful for 3D printers! – Tom's 3D printing guides and reviews
Why have we stopped using ATX computer power supplies? I explain what the pros and cons are of going with an simple “industrial” power supply vs. a full ATX supply, including being able to shut it down through the firmware yet still getting a solid 5V supply for a Raspberry Pi!Ok, let’s talk about some basics today. A little while back I did a video on how you can combine 12, 24, 5V components in the same setup and on that video, a bunch of you asked in the comments why ATX computer power supplies aren’t really used anymore in 3D printer builds. So let’s try and find out what had these falling out of favor and check out some of the things you can do with an ATX supply that would be really tricky with these simpler ones.
Form factors
There are a few pros and cons to each one, and it’s not like one is always clearly better than the other. So let’s start with the obvious differences, first, ATX supplies have a standardized shape that is kind of bulky in every direction, while the industrial supplies are slimmer, but also longer.
That makes it a bit easier to tuck them for example under the print bed, but the ATX form factor can work really well on some printer builds, too. Just typically, this type of form factor can be used more flexibly. There are also other PC power supply form factors that are made to plug into the same type of motherboard and components, for example the SFX size or Mini-ITX, which is just a shrunken down version of ATX. Those are typically a bit more expensive, though.
Set of wiresNow, the other difference you can see right away is that the ATX supply has a set of wires it comes with.
Some of the better units are modular, so you can just plug in the wiring looms you actually need, but typically, all of these are all permanently attached to the supply. On more powerful supplies, the wiring itself can take up as much space as the unit itself because it’s got enough plugs for 20 hard drives, four graphics cards, two mainboard and 12 floppy drives. I always find it kind of heartbreaking to cut off the connectors from a perfectly good power supply, but the plugs on here really are only used in computer parts. Also, just one wire by itself can not handle the entire output power, so if you need more than 100 or 200W, you’ll have to splice together wires from different plugs, and that can get really messy.
More on that in a second, as there’s more to it, but one upside of having standard connectors is on the input side, where you’ve got the standard IEC receptacle, so at least on the mains, high voltage side, you have a really easy, clean and safe way to plug it in.
The industrial supplies just come with a bunch of screw clamps that you can tighten onto crimped connectors or bare wire, but not onto tinned wire, but that’s both for the AC mains input as well as the DC output, so you’ll have to hook up mains to it yourself, too. On the upside, each of these clamps on the output can basically carry the entire output current with a single wire as long as the wire itself can handle it.
Ok, to expand on why you need to splice together wires on the ATX supply. The industrial supplies and also some simpler ATX units have just what’s called a single “rail”, basically one single output for 12V. But more more commonly on ATX supplies, there are two, three or four 12V rails, which are basically several independent supplies. One rail might supply the plug for the mainboard and power the CPU, another rail might be for one set of PCIe connectors for the graphics card and then another rail for the other set of PCIe connectors.
Now, it’s not entirely perfect just tying these separate supplies, these separate rails together, but it’s going to work to supply more current if you’re for example powering a large 12V heated bed. But to make use of the full output power, you will need to know which connectors are connected to which rails and grab power from each one, or just tie them all together.
Group regulationAnd another thing that comes along with these supplies being built for computers is that they don’t just generate 12V, they also generate 5V, 3. 3V, -5V and -12V, those last two ones are often used for audio.
Now, on cheapers supplies, you’ll often find what’s called “group regulation”. In very simplified terms, these power supplies will regulate 12V, 5V and 3.3V together so that the voltages are just fixed ratios to one another, that simply saves cost because you only need one transformer that has multiple secondary windings. As we start drawing current from 12V, the voltage on 12V will slightly drop because we start having resistive losses inside the supply, so it will start trying to compensate for those losses by slightly increasing the voltage it’s trying to achieve, so that the actual output voltage will more or less stay constant, no matter if you draw 1A or 20A.
But with that group regulation, not only will the power supply compensate for that voltage drop on 12V, at the same time it will also increase the output voltage on 5V and 3.3V even though we aren’t drawing any current here. The safety mechanisms in the supply are still monitoring those two voltages, though, and if they go above the safe limit, it’s going to shut itself off.
And that’s not uncommon to happen if you have a cheap supply and are drawing a good amount of load just from 12V, so one way to fix that, and that’s been done a lot, actually, is to just add a load to 5V and maybe 3.3V, all that needs to be is a resistor that wastes a few watts of power. I mean, I don’t think that’s very elegant, and I’ve not had to do it on any of my supplies yet, but then again, I don’t buy the very cheapest ATX supplies usually because I will probably use them in a PC at some point.
EfficiencyNext up, efficiency. If you’ve got cheap, subsidized, coal power, then you probably don’t care about a few extra watts that much, but when you’re paying 25 or 30ct per kWh, you probably do. Cheap industrial supplies will often claim “85-90% efficient”, which is hard to believe to say the least, typically they only manage about 70%. So if you have a printer that needs 100W to run, it will actually draw an extra 43W from the wall just for losses inside the power supply.
Brand-name industrial supplies are a lot better here, like the ones from Delta, Meanwell etc., but for ATX supplies, you have the “80+” certifications, which come in Standard, Bronze, Silver, Gold, Platinum and Titanium.
The higher you go up in level, the more efficient the supply will be across its entire load range, between 20% and 100% load. If a cheap supply only tells you one efficiency figure, that’s only for peak efficiency at one specific output load. Also, that achieve that better efficiency, 80+ supplies usually also use better components.
Switching on and offAnother upside of ATX supplies is the fact that you can switch them off. Not just with that switch on the back, which of course it super convenient, too, but by signaling through that green wire, you’ll no doubt have shoved a wire into the ATX connector before to turn it on or you’ll have seen these jumper plugs.
There are two incredibly cool things about this: First, we can control that signal with any 3D printer mainboard. Marlin has support for switching on and off an ATX supply, it’s right there in the config, so with one gcode command, you can enable all the high-power parts on your printer that are connected to the 12V line from an ATX supply, and with another, you can turn them off again, and you can even use that as an emergency stop for example through OctoPrint. You can also use those gcodes in the start and end gcode, so that before and after a print, the printer turns itself on and off automatically, that saves some standby power and reduces the risk of anything dramatic going wrong when the printer is just sitting idle.
But the cool thing with that is that an ATX supply always provides 5V power for your electronics, even when you’ve switched it off electronically through the green wire.
The 5V_SB line provides enough current for at least a printer control board, and in many cases also enough for a Raspberry Pi so that you don’t need a separate power supply for that.
5V_SB is intended for keeping some functions enabled in a computer when it’s off, like wake on LAN, and more recently also to allow charging through the USB ports. Check your power supply for the exact current rating.
So ATX supplies actually sound pretty cool so far, right? Well, there are two more things that are fairly strong arguments against using them. The first one is voltages. Now, printers have been moving to 24V because it’s easier to handle powerful heated beds with it as you’re reducing the current that’s needed to get the same output power, but it also gives stepper drivers more headroom to breath and actually improves the performance for higher movement speeds and fast accelerations in many cases. But of course, ATX supplies are only available with their main output voltage at 12V, while you can get these industrial ones in 5V, 12V, 24V, 36V, or 48V. Now, you or a printer manufacturers can work around that by for example carefully selecting the stepper motor and driver to work well at 12V, that’s totally doable, and move to a mains-powered heated bed. But then, of course once you do that, you don’t even need a power supply as capable as an ATX unit anymore, you can get away with one of these small brick-type supplies.
And the other factor, of course, is price. These industrial units have become incredibly cheap, spurred by an LED strip craze a few years ago and 3D printers coming up around the same time, so I just did a quick search for how much these are, shipped from Germany, taxes included;
A 12V 20A supply is 14€, a 30A unit is 16€, and a 24V, 10A unit, the same rating as in the MK3 is also 16€.
That is just incredibly hard to beat. Now of course, that’s the bargain bin quality units, so if you go for one of those, you should always buy one that’s rated for at least 30% more than you think you’ll need, and also, they will age over the years and lose some of their ampacity as the capacitors dry out, but the same exact thing also applies to super cheap ATX supplies. Now, with those you have to factor in that connectors are actually surprisingly expensive, even if you buy them in bulk, which is why modular supplies are so much more expensive than regular ones.
So you can get a “500W” unit, rated for 26A, so more like 300W, of which you should maybe use like 220W, for 16€, plus shipping this time, you can get a “600W” unit with two 20A rails, for around 22€, and then as we get into actually decent, brand-name, 80+ certified units, they start around 32€, 35€ for between 24 or 30A of output on 12V. Plus shipping.
Now, honestly, that’s still not super expensive, but you can also get an industrial Meanwell power supply at 12V and 20A, or 24V and 10A for about 40 bucks. Honestly, if you’re building a printer, you’re ok with a 12V system, want a decent supply and maybe are thinking about using that 5V standby line, which I think is a really neat feature, then an ATX supply is still a really good choice.
But when it comes to manufacturers, not only are they probably getting even better deals on industrial supplies in bulk, but for them, a smaller packaging size is also worth a lot as it saves on logistics, and dealing with ATX connectors also adds cost and complexity because they’ll need to have some solution to plug all relevant cables in, which means making a custom PCB or another wire harness, spending money on connectors again and also spending more time during assembly. For them, I think it just makes a lot more sense to use the industrial supplies.
So if you’ve built a printer or customized one, let me know what you’ve used! Is the option for 24V the deciding factor? Maybe you’re also using an ATX supply with a boost converter just for the stepper drivers? Would totally make sense!
Get 24V 10A supplies
All my video gear
💙 Enjoying the videos? Support my work on Patreon!
Product links are affiliate links – I may earn a commission on qualifying purchases (at no extra cost to you)
Check out my second channel “More Layers” on YouTube for livestreams
Top 10 Best 3D Printer Power Supply | Buying Guide
Table of Contents
What is 3D Printer Power Supply?
Power supplies, or PSUs (power supply units), are generally burdensome metal boxes with a line of screw terminals or a heap of wires toward one side and a fan as an afterthought. At the point when you wire them up to your printer and plug them in, they appear to make things work mysteriously.
Be that as it may, what do they really do? PSUs will, in general, contain a transformer (or a progression of transformers), which gets the 110 to 240 volts from the divider and steps them down to a more sensible 12 to 24 volts. Likewise, inside a PSU is a rectifier circuit, which changes the divider’s AC current over to the DC current a 3D printer needs.
What to know before selecting the best 3d printer power supply?1. Kilowatts
The primary thing you need to do while picking a PSU figures the all-out power required for your assemble. We might want to thank the people at Outer Vision for making the extreme Power Supply Calculator – quite possibly the most-utilized PSU wattage number crunchers out there and an important apparatus for deciding the all-out wattage you should use in your construct.
After you ascertain complete wattage, we propose that manufacturers represent an all-out force in addition to a 20% cradle for security and future-sealing. Doing so will permit you to avoid the expense of another PSU on the off chance that you choose to introduce SLI or Crossfire GPUs later on.
2.
RankingSubsequent to sorting out your financial plan and force utilization needs, you may have to consider long-haul energy investment funds. The 80PLUS association has characterized the proficiency standard for power supplies and gives us an unmistakable illustration of what benefit efficiency is – something you ought to consistently endeavor to have on a PSU.
The 80PLUS affirmation standard certifications:Productivity: You can discover which PSUs are confirmed on the authority 80PLUS site that promises you the particular energy proficiency.
Exact Wattage:Some PSU suppliers sell items by a pinnacle power evaluated number. The 80PLUS endorsement guarantees the PSU produces 100% exact wattage when utilized. Genuine wattage is vital on the off chance that you purchase something dependent on pinnacle power since it won’t perform reliably without it.
Some commentators call this APFC, which is short for Active Power Factor Corrector. The motivation behind APFC is to make the clear force equivalent to genuine force.
APFC adjusts responsive stacking from the divider outlet to the PSU and keeps energy from being squandered from the force organization to customer – giving more noteworthy effectiveness for both the supplier and purchaser. Simultaneously, your PSU will have better voltage guidelines while running marginally cooler, allowing the PC to proceed as steady as could be expected.
3.
PriceConsider while picking a PSU is to decide your spending plan. When all is said in done, putting aside between 10-15% of the complete framework fabricate is a decent expense for every presentation proportion.
4.
Measured qualityAnother part of PSUs that regularly gets neglected is seclusion. Fortunately, it’s quite simple to sort out what kind of cabling you need on the grounds that there are just three alternatives:
Direct Cable:All PSU links come from the PSU lodging straightforwardly. This setting is less expensive underway or configuration, making PSUs less expensive to customers. Nonetheless, this isn’t useful for the aficionado who may have to change his work every now and then. Link the executives is likewise a lot harder with a wreck of spaghetti links to manage.
All fundamental links come from the PSU case straightforwardly, like ATX Power (20+4) connector, CPU (4+4) connector, and PCI-e (6+2) connector. Other unnecessary fittings like Molex (4-pin) and SATA (15-pin) connectors are secluded, permitting you to eliminate them freely. Semi-particular offers center ground estimating and is a good link to the board arrangement.
Full-Modular:All links are removable, making the establishment very simple and smooth. Link the executives is uncommonly simpler with a full-particular PSU, and it makes it simple in the event that you change constructs habitually or regardless of whether this is your first form.
5.
AppearanceThe last advance for aficionados is to take a gander at the visual plan of the PSU to discover one that coordinates the shading subject of the form. Everybody has their own style, and the main thing how the framework will look to you. Now and then, a PSU can be utilized as a highlight to your apparatuses rather than an inferior black box at the lower part of the case.
Top 10 3d printer power supplies to buy1.
Steady 12V30AUtilizing another gadget, the quality is steady. It very well may be utilized in LED, light bar, screen, hardware, etc. The info voltage has a wide scope of transformation, high effectiveness, and energy saving—yield wellbeing and soundness. The extent of utilization: screen TV extraordinary force supply, screen camera power supply, LED power supply, access control power supply, etc.
Special Functions:- Yield Frequency: 47-63Hz
- Yield Type: SingleOutput
- Force: 301 – 400WOutput
- Voltage: 12VOutput
- Current: 30A
Check customer reivews ON AMAZON
2.
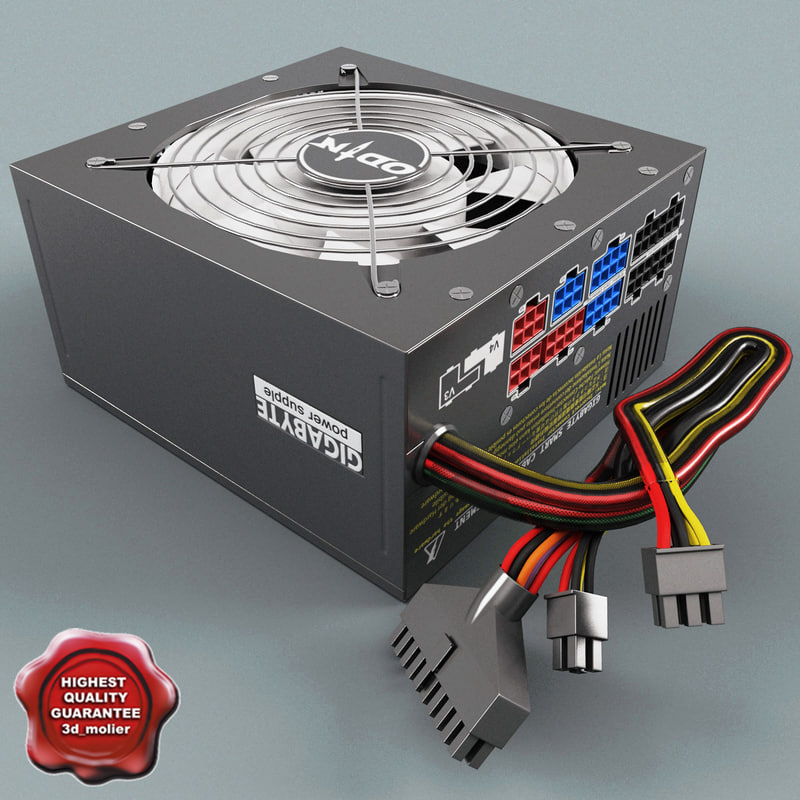
- High safety execution, with cut-off, over-voltage, assurance work.
- Low working temperature, long assistance life.
- Wide info voltage range, in accordance with worldwide principles.
- The force supply effectiveness is high, and the electromagnetic impedance is low.
- AC input voltage range: 85-264VAC 47-63Hz
- Info current: 115V/1.5A, 230V/0.75A
- Yield: 12V/0-15A
- AC inrush current: Cold-start current 20A/115A 40A/230V
- Spillage current: <1MA/240VAC
- Dc movable reach: +/_10% appraised yield voltage
- Over-burden assurance: 105%-135% hiccup mode, auto-recuperation
- More than voltage assurance: 115%-135% remove the yield, auto-recuperation
- The arrangement, rise, hold up time: 200ms, 50ms, 20ms.
- Burden guideline: +/_ 1%
- Working temperature: – 10oC~+60oC, 20%~90RH
CHECK CUSTOMER REVIEW ON AMAZON
3.
DC 12V 360W 30A – S-360-12General full reach AC input voltage. Against sticking execution, unwavering high quality. DC swell, high proficiency. Low temperature, long help life. Little size, high force thickness. Great protection properties, high dielectric strength. Full burden consumes in temperature, 100% consume in a test. Cut off/over-burden/over-voltage assurance/overcurrent/overheat insurance/work having a consistent current.
Special Functions:- Output Power: 360W
- Output Current: 30
- Output Frequency: 50/60HZ
- Model Number: S-360-12
- Output Type: Triple
- Output Power: 360W
- Material: Aluminum
CHECK CUSTOMER REVIEW ON AMAZON
4.
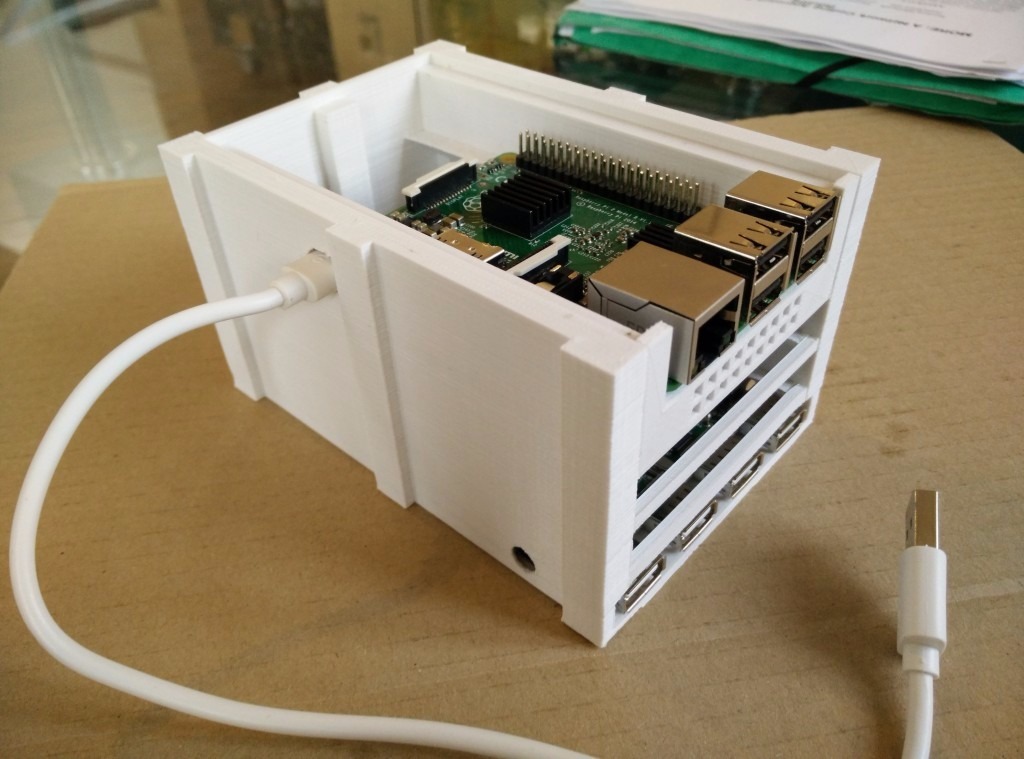
This expert 350W 24V 14.6A Switching CNC Power Supply can be broadly utilized in Industrial Automation and CNC Stepper/Servo System.
Special Functions:- 24V DC 14.6A yield
- AC input voltage range: 90~132V/180~264VAC
- 115V/230V AC chose by switch
- High effectiveness, minimal effort
- Constrained air cooling by worked in DC fan
- Low yield swell and whoop
- Over-current, over-voltage, cut off overheat securities
- 215*115*50mm (L*W*H)
CHECK CUSTOMER REVIEW ON AMAZON
5.
LED Full 24V 240WThe 240W 24 LED Outdoor Power Supply highlights general 100-277V AC voltage contribution with class 2. Its completely pruned aluminum lodging conveys an IP67 rating for outside area use. This flexible LED transformer will decrease 120V AC’s ability to be utilized with 24V DC lights.
Special Functions:- Output voltage: 24V DC
- Yield power: Max.
240W, 16A
- Voltage: 100-277V AC
- Frequency: 50/60Hz
- Working temperature: -40°C~+90°C
- Housing: Aluminum, completely pruned
- Wire length: 46cm (18″) wire leads for design introduce
- Dimensions: L225 x W74 X h51mm (L827/32 x W229/32 x h25/8″)
CHECK CUSTOMER REVIEW ON AMAZON
6.
DC24V 100W 4.5AThis expert 100W 24V 4.5A Switching CNC Power Supply can be generally utilized in Industrial Automation and CNC Stepper/Servo System. 115V and 230V can be chosen by the switch. Amazing functions (e.g., PWM control) and expert plans guarantee high productivity and unwavering high quality of the force supply. Ease likewise makes it more satisfactory for general utilization.
Special Functions:- 24V DC 4.5A yield
- AC input voltage range: 92~132V/175~264VAC
- 115V/230V AC chose by switch
- High productivity, minimal effort
- Free air cooling convection
- Low yield swell and whoop
- Over-current, over-voltage, cut off overheat securities
- 199*97*38mm (L*W*H)
CHECK CUSTOMER REVIEW ON AMAZON
7.
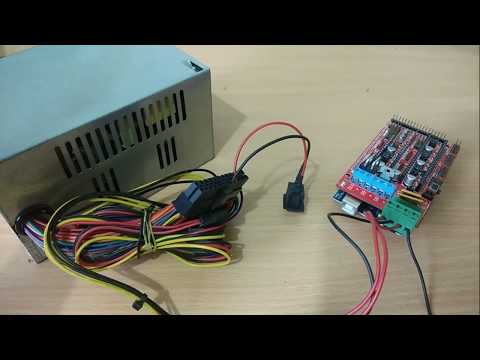
Automatic over-burden cut-off, over Voltage cut-off, programmed warm cut-off, impede. Voltage consistency: There are no voltage variances at all at power on, during communication, get, or at power off. It accompanies worked in cooling fan and numerous openings on the metal case, which makes heat scattering more productive: smaller little size, high proficiency, unwavering high quality, and stable execution. Indoor utilize as it were.
Special Functions:- Yield Current: 0-15A
- Yield Frequency: 50HZ-60HZ
- Model Number: C360W
- Yield Type: Dual
- Yield Power: 301 – 400W
CHECK CUSTOMER REVIEW ON AMAZON
8.
60V 10A S 600WAll-inclusive full reach AC input voltage against sticking execution, unwavering high quality. DC swell, high proficiency, low temperature, long life. Little size, high force thickness, great protection properties, high dielectric strength full burden high temperature consume in and 100% maturing test there is short out/over-burden/over-voltage assurance/over-current/overheat insurance/steady current capacity there are wellbeing guidelines, low force supply the best arrangement.
- Yield Current: 0-10A
- Yield Frequency: 50-60HZ
- Model Number: S-600W-60V
- Yield Type: Single
- Yield Power: 600W
CHECK CUSTOMER REVIEW ON AMAZON
9.
HLG-600h 600WHLG-600H arrangement is a 600W AC/DC LED driver highlighting the double mode steady voltage and consistent flow yield. HLG-600H works from 90 ~ 305VAC and offers models with various evaluated voltage going somewhere in the range of 12V and 54V. Because of the high effectiveness of up to 96%, with the fanless plan, the whole arrangement is able to work for – 40°C ~ +90°C case temperature under free air convection. The plan of metal lodging and IP67/IP65 entrance security level permits this arrangement to fit both indoor and open-air applications. HLG-600H is outfitted with different capacity alternatives, such as darkening procedures, to give the ideal plan flexibility to the LED lighting framework.
- Yield Current: 0-50A
- Yield Frequency: 47 – 63HZ.
- Model Number: HLG-600H
- Yield Type: Single
- Yield Power: >500W
CHECK PRICE ON AMAZON
10.
S-500-12Underlying over voltage, over current, and short out insurance. Ensure the soundness and high proficiency of force supply. Against sticking, breezed through EMC assessment, wave under 20MV. Consistent voltage yield, accept stable force supply for LED lightings to arrive at a long lifetime.
Special Functions:- Yield Current: 0-50A
- Yield Frequency: 50/60HZ
- Model Number: S
- Yield Type: Triple
- Yield Power: 401 – 500w
check price on amazon
Watch How to Wire the Power Supply to the 3D Printer RAMPS Board [Video]
Top 5 FAQ and Answers Related to best 3d printer power supplyHow would I get a 24v force supply from my PC?
Utilize a DC converter to get than 24VDC. But what you can do, and effectively, is to utilize a DC/DC converter. This little module is helpful for this reason and can get you up to 50 watts.
Do you need an incredible PC for 3D printing?
From firmware moves up to running the printer progressively, nearly anything should be possible from a PC or PC. I would suggest ensuring you have at any rate 4GB of RAM and a genuinely amazing processor.
What causes power supply disappointment?
Electric Interference: Lightning, power spikes, and so forth Voltage variance. Soil/Foreign Substance: Cigarette smoke, house dust, and so on. Overheating and additionally Ventilation Failures: The most widely recognized reason for an SMPS disappointment is overheating.
For what reason is my force supply not working?
Watch that it has not inadvertently been turned off. Attachment the PSU power link into a divider attachment or flood defender, and turn on the PC. … On the off chance that it doesn’t light, attempt an alternate force link and an alternate attachment to wipe out those things as the wellspring of the issue.
Will a motherboard kill a force supply?
A motherboard can’t execute a PSU. Regardless of whether you short the voltage yields, the PSU should just closure.
SummaryThe best spot to begin when searching for a 3D printer power supply is to pick a yield voltage. The two most regular decisions are 12 and 24 volts. The main factor while picking voltages is your hot end. These are, for the most part, sold in 12V and 24V designs. Just locate your hot end’s particulars to discover which you own.
Your force supply ought to give the voltage needed by your hot end. The following most significant rating for your 3D printer power supply is yield current. As recently expressed, this will be the restricting element for your warm bed and the complete number of hot finishes you are working on. The simplest method to look into your 3D printer power supply online is via looking for the wattage and afterward finding the alternative that has the right voltage evaluations. When buying another 3D printer power supply, it’s in every case best to watch that it works before you plug it into crucial hardware like your 3D printer.
By reading this guide, I hope you got the full idea of Top 10 Best 3D Printer Power Supply | Buying Guide
Please share this Top 10 Best 3D Printer Power Supply | Buying Guide with your friends and do a comment below about your feedback.
We will meet you on next article.
Until you can read, Can You Dissolve Polylactic Acid(PLA)? Process of Dissolve PLA
How to fix a broken 3D printer | F1-IT
Repair of 3D printers is very important to us. Considering the number of broken 3D printers that we and our students had, we fixed many of them. Here's how.
Let's take a look at troubleshooting a 3D printer that won't turn on.
Please note that some of these steps may seem redundant and are basic. However, it is important to rule out any possibility. Here are the steps to take. The idea is to narrow down to what is the cause. For example, maybe it's a power cable. You can buy accessories for a 3D printer here https://3d-diy.ru/catalog/spare-parts-3d-printer/
Step 1: Make sure it's really on
Step 2: Check the outlet
You want to make sure the outlet is working. For example, the circuit breaker may have turned off. So plug the lamp into this socket and make sure the lamp can turn on. If the lamp lights up, you know that the problem is not with the outlet.
Step 3. Check the power cable.
If your 3D printer's power cable fits something else, try testing it on another device. If the other device turns on, the problem is not with the power cable.
In case you don't have anything else suitable for this power cable, you will need to test it thoroughly. You can do this with a multimeter. If you're going to do it, do it safely.
Step 4 Check if the fuse in your 3D printer is blown.
Your 3D printer may have blown a fuse. I hope you're lucky that this is a problem as it can be as simple as replacing a fuse.
Be aware that if you replace a fuse and it stops working again, you most likely have a short circuit somewhere.
You can try turning off all heating elements. Then replace the fuse and turn on the printer. Don't try to actually print anything. Just see if you can turn something on.
Step 5. Check the switch
If you have a multimeter and know how to use it, you can test the switch to see if it is the problem.
Step 6 - Checking the output of the power supply
Once again, if you know how to use a multimeter, you should have an idea of how to do it. Perhaps, for some reason, the power supply does not pass enough voltage.
Quite often it happens that the power supply fails. Especially in cheaper 3D printers. Keep in mind that sometimes there was a good reason besides the cheap PSU. Imagine if you replace the PSU only to screw it up again because there was a short circuit somewhere.
3D printer screen not working
If you now know you have power but the screen still won't turn on, here's what you should try.
Step 1 - Check Wiring
Remember that you must first make sure the printer is actually getting power and turning on.
Check shield wiring. Make sure the connectors are securely fastened. After you have checked the wiring, be sure to turn on the power and check the screen again.
Step 2 - Check the signal
This is another situation where experience with multimeters and oscilloscopes comes in handy. I can't tell you how to do this, but maybe we'll write an article about it in the future.
If you are not getting a stable signal, you may need to replace the control board.
Step 3 - Replacing the 3D Printer Screen
If none of these other things worked, you probably need to replace the screen.
The 3D printer nozzle does not heat up
First, try manually heating the nozzle using your 3D printer's menu. Because there are so many different printers out there, it's hard to say exactly how you'll do it. This menu option is often referred to as Preheat. Keep in mind that your printer may require you to set the temperature. There is also usually a "Start" or "OK" button.
If the nozzle still does not heat up, check that the heating element is actually connected to the printer control board. Although not very common, you may find that you may need to replace the heating element.
3D printer stops in the middle of printing
This may be due to a G-code or a power problem. Also, make sure you don't run out of filament in the middle of printing. We will write more about this in the future.
If the 3D printer needs any repair, it will most likely be related to the power system. Otherwise, it may be a G-code problem. One thing I've seen is that people get the thread diameter wrong. Make sure you have the correct filament diameter for your 3D printer.
The most common thread diameter is 1.75 mm and the next most common is 3 mm.
It is also possible that there is old plastic in the nozzle that has melted and cooled so that it is stuck. This is due to insufficient plastic yield. You must make sure that the nozzle is heated to the correct temperature. Also make sure your extruder's stepper motor is running.
Not enough plastic coming out of 3D printer nozzle
Sometimes caused by nozzle not getting hot enough, nozzle sticking, dirty teeth on extruder pinion gear and friction in hot end/Bowden tube.
This may be a calibration or extrusion multiplier setting problem.
Have you changed your stepper motor recently?
It is possible that the pinion gear has a different diameter than your old one.
Another problem may be that the new stepper motor has a different number of steps per revolution than your old one.
Filament stuck - cannot be removed
Generally you want to make sure you preheat the nozzle before removing the filament.
What I do is pre-heat the nozzle, then release the tensioner on the extruder and push some filament through until I can see the part coming out of the nozzle well.
As soon as I see this, I continue to hold the tensioner so that it does not compress the thread and pull the thread.
Why you should build your first 3D printer yourself / Habr
- It's faster than waiting from China Anet A8 for 109$ (hereinafter referred to as ordinary
washing powder3D printer) - This is more qualitative (with non-crooked hands)
And finally, sooner or later you will face the need to repair / modify the printer and you will still have to master the practical skills for these devices.
And at the most inopportune moment.
And given that there were New Year holidays and long quarantine winter evenings ahead,
in two days I bought all the necessary components in three local stores, which cost the same 109dollars.
And only thanks to the "Martian rule" the total amount increased by only three evergreens.
But contrary to the well-known tape from the film, I used blue (and how could I do without it) electrical tape and plastic ties.
In general, if you are only thinking of assembling a 3D printer - welcome under cat,
where will be my thoughts on the design and assembly of some nodes.
For there are so many detailed assembly instructions on the Internet.
So, let's start with the Martian rule - after purchasing all the necessary components, consider that you are on the red planet, and the next rocket from Earth will be in half a year.
Thanks to this, I avoided an increase in the cost of the device by at least one and a half times and still improved the quality of the mechanical part.
The only thing you can afford is to go to neighboring manufactured goods or unscrew a spare part from your favorite moon rover is great.
Next, we will talk about assembling a Prusa-compatible Graber I3 printer, but it also applies to any device based on the RAMPS 1.4 + Arduino Mega 2560 control board.
Let's go from the ~stove~case - here it's worth discarding the aesthetics completely and imagine that you grabbed it with your hand and started to stagger.
Correct! Without proper mechanical strength, you will either have to set the level of the printer table every time, or screw it with screws to the kitchen worktop.
From this point of view, the presence of a high box at the base adds rigidity compared to the original grabber or Annushka.
But for the second time since the start, I would have collected RepRap Mendel
Yes, the body is made of plywood, as I will have to paint, peel and drill during assembly, the main thing is not to loosen the seats, giving room for backlash.
It is better to paint with acrylic varnishes - they do not stink, unless their version is sprayed.
And of course, plywood is preferable to metal in terms of acoustic comfort.
The only disadvantage of the selected ATX version of the case is the inconvenient vertical position of the screen compared to the original Graber version:
Pros - better durability, you don't have to worry about laying wires and fixing the control board, using cheap ATX power supplies.
So we come to the second cornerstone issue - NUTRITION.
Our 12 volt unit should provide 20A.
Remember how you chose a PSU for your gaming/school/work PC?
By weight!
I will say right away that if you buy a new power supply from a store, it is no lighter than 1 kilo and the declared power is from 400W.
If used - look at the current and before use you should remove the cover and blow out all the dust with a compressor - at a tire fitting you will blow it out for three rubles along with cockroaches.
Go ahead, computer geeks / 3D people are cool guys, but sometimes they forget Ohm's law by connecting power to the RAMPS with one, Carl wire AWG-20 (section ~ 0.5mm sq.)
I did the right thing, and made a mistake! !!
On a hot table with a power of 120W, a current of 10A simply melted the power plug
I had to dismantle it and solder the wires.
Yes, about soldering irons - the power of 60W is decidedly small: neither the old-fashioned one with a copper (thick) tip, nor the modern one with a thermostat could melt the solder in the process of soldering an acoustic wire with a cross section of 1.5 squares to a hot table.
I had to unearth an ax of war from the pantry:
But it won’t be a crime to use 1 square wire and solder not 3, but 2 twisted AWG-20 wires from the power supply, then 60W is enough.
Continuing Ohm's Law - You have already purchased "cheap" NEMA-17 stepper motors, now it's time to look at the current consumption of the windings.
Standard model 1.66 (1.7) A, reinforced - 2 (2.1) A, "quiet / cheap" - 1.33 A, I have the last one.
The current output by a conventional 4988 driver is up to 2Amps (even the dock does not speak to the winding or in general.
Everything seems to be OK, but there are two motors and RAMPS on the Z axis, and other control boards obviously contain two connectors for their parallel connection .
No, it's not scary if the R100 resistors are charred at the maximum current (there are boards with R50 for half the current).
And not even that the engines do not receive enough power (I have 0.75A everywhere except for the Z axis)
It's just that with this inclusion, the characteristics of the engines must match ABSOLUTELY, otherwise a wedge / skipping steps is possible in certain modes.
The REPETIER firmware did not cope with this at all, MARLIN got lost once at the stage of moving the extruder from the parking position at the beginning of printing.
Neither shuffling the motors nor the drivers helped.
The Z axis with two motors is saved only by their serial connection:
And oh, miracle, everything worked not on 2 amperes, but on the same 0.75 as the rest of the axis!
Someone may reproach me for the insufficient accuracy of the assembly of the axles, and as a result, the large required force on the Z-shafts.
I will answer - with the printer turned off, turn the right / left shaft by hand - what will happen to the free one?
That's right, for most it will remain motionless, but for me, when connected in parallel due to self-induction, the second shaft also turned.
Yes, about the shafts - usually, the Graber is designed for Hozmag threaded studs m5 with a pitch of 0.8mm.
They should be lubricated with any paste-like grease for bearings - CV joint, "blue" for needle bearings, graphite and hot grease!
In general, you are on your way to your grandfather's garage / car market, or even better, take lubricant from Lunokhod bike chains.
Of course, you can also buy the glamorous white Molycote-DX, but this is a matter of taste.
Yes, here the "Martian Rule" saved me for the first time - I screwed up the sockets of the nuts of the left carriage of the Z axis I almost ran to buy 3D plastic X/Z carriages and "regular" trapezoid studs/nuts 0003 By the way, there were no stainless steel studs in the local hardware store - I took ordinary, galvanized ones. Filed off the threads a bit so they fit into 5mm sockets and bingo! The advantages of such tuning are a normally considered thread pitch of 1mm and the fact that not a threaded part, but a cylindrical part is clamped into the stepper sleeve! Yes, before assembling I recommend reaming the mounting holes of the Z-axis motors with a drill 5 - the distance between the guide and the threaded stud varies slightly in the mount and carriages! As a result, this leads to the fact that when moving along the Z axis, the upper ends of the pins move in a circular orbit, and the extruder walks. In general, you need to select the position of the motors so that the pins remain on the same axis when the axes rotate (via the printer menu). In addition, many mounting holes were reamed, because the sockets in the plywood of my version of the printer are cut out for the M5 nut. Don't forget to press down on the plank when drilling from the back side, otherwise chipping of the plywood can be catastrophic. In a word, the base of the body is assembled on five-millimeter bolts!!! Yeah, and the notorious left carriage is generally assembled on screeds: The fact is that with 6mm studs and 4 fastening screws, a touch was found on their threaded parts. I didn't use 3mm screws and hope for half a millimeter, but used zip ties. This is a truly unique fastener that has replaced the wire used in the past. The only thing that screeds cannot withstand is water hammer in the country water supply. So if you're going to Mars, bring more zip ties! Now let's move on to the control board itself, or rather to the stepper motor drivers and their settings. Let's talk more specifically about the fight against noise. Someone puts expensive TMC2100 drivers in "silent" mode (by the way, you only need two of them - on the X and Y axes) But really it's all about psychoacoustics: carriage speed of 60 mm / s and a 20-toothed gear with a 2-mm belt pitch, we get a frequency of 4800 Hz !!! OMG! This is the same peak frequency of perception! Is it possible to double the microstepping (and at the same time the current in order to avoid skipping steps) by installing a DRV8825? thereby shifting the frequency range upwards. And you can show the noise of the middle finger Of course, you can completely remove the microsteps, and stop at the positioning accuracy of the X, Y axes of 0. For most tasks, this is enough, the printer will start to "bass" at 300Hz. But it's all about individual preference and sound perception - experiment with a smaller microstep divider and find your comfortable frequency! Where the DRV8825 really comes in handy at 1/32 micro pitch is the standard MK8 extruder! If we calculate that with a 1.75mm filament and an 11mm toothed roller, on a standard 0.4mm nozzle and a 16 divider, we get a 0.2mm column of plastic per step!!! This replacement is justified only after adjusting the pressing force, extruder temperature, plastic type and stepper motor current! If you cannot ensure that the feed system operates normally without clicking and with less than half the nominal current on the stepper, this path is not suitable. Then you should either print a geared feed system, or buy a "Titan", which contradicts the "Martian Rule". Has the quality improved from such tuning? At least the supports began to separate without excessive effort, which is already an indicator. To print gears and other parts of the RepRap system (partially self-reproducing printer), a certain print quality is required. But having reached it, the need for the above paragraph disappears. OK, the second most important part after assembling/setting up the X/Z axis is the print table!!! Here I am not against plywood, but not for it either! Maybe the proximity of the heating element, even if it was covered with thermal insulation, was influenced by the fact that I did not paint the plywood base with silver, or maybe three bearings instead of four. In general, the level of the table walked constantly, unpredictably and by 0.2 mm! And if it wasn't for the "Martian Rule", an auto level would have been bought. In a word, armed with a grinder, I built a table for 4 bearings from an aluminum-polyethylene-aluminum sandwich: Now the table walks no more than 0.05 mm (checked with probes to adjust the valves) and I don’t even correct it for the layer 0. Yes, the springs are mega-rigid, I took brass adjusting screws from the same table as the upper support / spring guides. And the glass of the table, it is 4 mm, because this is its main rigid element (the 1.5 mm textolite of the heater "walks" and bends as it wants). Clamps should preferably be placed as close to the corners as possible, but this interferes with the control/adjustment of the gap! And yes, my axles turned out to be longer, I didn’t cut them, but fixed them with ties - it’s more reliable! Print area is 190x180x180 (XYZ). Of course, you can radically redo everything (make the table lower, change the fastening of the belt on it, otherwise position the extruder), but for now it suits me. And a few words about firmware - I counted 8 different names, but I tried only three: At first I grabbed the second version of Marlin, hoping to switch from Arduino Mega to Due, which has been gathering dust in the box for a long time, but the firmware is heavy both during compilation and for the 8-bit Atmega2560. Then stuck with engines in Repetir. Teacup considered between glasses of tea - not ours how to quickly launch the 2004 screen - gave up this idea. Well, I returned to Marlin version 1.1.9, downloading separately examples of firmware from github. I came up with a fresh version from Aliexpress's Prusa_i3_MKS_Gen_2Z_V1.2, set only my table sizes, steps and inverted the Y direction. That's basically all my notes/remarks. Yes, the choice of filament should also be taken responsibly. Don't print out of shit Liberator! Of course, you've probably already bought a roll of ABS along with the rest of the accessories, but it's better to save it for later, and start with PETj, coPET or PLA. I bought coPET right away. The fact is that these plastics are not as demanding in terms of parameters and printing conditions as ABS. Someone even prints with them on printers without heated bed! ABS is good only for the price, but if you print in a living room not under an exhaust hood, the aroma will still be the same. Yes, and they talk about the dangers to health from its fumes, and heating the table to the desired 100-110 degrees Celsius requires titanic patience. By the way, I got the "Zaporozhets" right, up to a hundred So, having printed a skein of filament, I almost ordered a second one, but I found ABS + half the price! On it, the part behaves differently (compared to conventional ABS), the temperature of the table is 90-100 degrees Celsius, and even the first model was still printed, albeit with a tear off of the edges. After that, a hood with a carbon filter was built, a new coil holder and blowing the RAMPS power transistors.
jumper by moving to a 1/4 microstep. 2 mm.
20/0.30 mm.
accelerates heats for 10 minutes, up to 120 - nothing.