Owning a 3d printer
11 Reasons Why You Should Buy A 3D Printer – 3D Printerly
3D printing used to be an expensive craft which would set you back several hundred dollars just to get started.
This, along with the high cost of printing materials and less beginner-friendly printers meant that it was quite challenging to get in to. Today it’s a much brighter scenario, where the average individual can get started with just $200 and get to printing great things.
In this article, I will go through a list of reasons why you should buy a 3D printer when you can. Even if you are already own, a 3D printer read on because I’m sure you will learn some things that may surprise you!
1. It’s a Great Hobby to MasterThere are many people out there who have spare time on their hands but just don’t have a hobby to spend that time on.
That’s where 3D printing can definitely help. There is a real community of 3D printing hobbyists who use some of their time to create great things and begin projects for things that are very useful, or just for the fun of it.
Regardless of your reason, you will learn a lot about your own creative and technical abilities after getting involved with a 3D printer.
If you want your 3D printing experience to be worth the investment in the long run, I’d advise that you learn the design and programming aspect of it.
This may seem daunting at first, but the programs out there today are beginner-friendly, and can be a very fun experience becoming well-versed in it.
You should be buying a 3D printer that has the correct balance between price, performance and durability. Many 3D printers that are $200-$300 work to a good enough standard to get you started.
On the other hand, if you want your 3D printer to be a premium one from the start and have excellent longevity, it could be worth forking out more for a higher priced 3D printer with great features, performance and warranty for your intended application.
After you gain a good level of experience, you’ll get to understand the key differences in what you can 3D print and at what quality. At this stage, this is when I would recommend you spend more to get something more premium for your 3D printing desires.
If you are thinking about getting into 3D printing, there can be a good amount of creativity involved if you want there to be. I would definitely recommend learning how to use free Computer Aided Design (CAD) programs to create your own designs.
Being able to convert ideas, into designs then into a 3D printed object makes the world of a difference in how much you can achieve with 3D printing.
Without creating your own designs, 3D printing can be quite limiting in some respects, in so far as you can only print what other people design.
In fairness, there are several designs all over the internet on websites like Thingiverse which will give you a lot more designs than you could ever ask for, but after some time it could get quite repetitive.
A cool thing about this is once you get to a good stage of CAD , you can share your designs with other people for them to print, and actually get feedback and praise from other users for your creativity.
There is somewhat of a learning curve to become comfortable in creating your designs through CAD programs, but the long-term impacts will be very beneficial to your 3D printing journey.
Not only this, but there are many other applications of CAD beyond the 3D printing scope so it’s a transferable skill of sorts.
3. DIY Fixes for Household ProblemsThis ties into the last point with creativity and being practical with your personal situations. An example from one 3D printer hobbyist comes from when his dishwasher broke and couldn’t be repaired.
He also couldn’t get a vital part from the manufacturer due to it being a discontinued model.
With his previous experience in design, he sought out to come up with the solution. This was a great opportunity he had to model the part in a free CAD program then print it out.
It isn’t as simple as it seems, however, as he needed to refine and improve the design a few times but it resulted in a new part for his dishwasher which was actually better than the original.
Not only did he prove his ability to get the job done with some persistence, but he got bragging rights from the wife too!
Another bright side is, if it that part does ever break again, he has the original design saved to be able to just print one again without the extra design work involved.
In this situation, rather than buying a new dishwasher, the cost of the 3D printer and the filament used would’ve been much more cost-efficient.
If he had started 3D printing when this problem arose, there would be an initial learning curve to get the experience required to do such a task. Since it was already a hobby of his, he could get right into the task.
4. Creates Things for Other HobbiesThe application of 3D printing really goes far and wide, being able to tap into other hobbies and industries with ease. Engineers, woodworkers and other technical individuals have applied 3D printing to their field to make a whole host of useful items.
This video by Marius Hornberger shows some of the real-world applications that 3D printing has done for him and his space. Note, this guy is an expert so don’t expect to be able to do what he does at an early stage, but it’s definitely something to work towards!
Once you get to an advanced stage of 3D printing, this is the type of benefit you can apply to the rest of your activities in the future.
You can really see how far 3D printing can expand horizons into other fields and industries. My article here on 3D printing applications in the medical field shows just a glimpse into it’s potential.
5. 3D Printing Gifts for People/ChildrenYou’ve probably seen a few 3D printed objects and many of them are figurines, action figures and small toys that look pretty cool. A lot of these objects are great gifts for comic and cosplay enthusiasts, general anime fans and basically every child out there.
Being able to print favorite superheroes and marvel characters in a wide range of colors really is sweet to see. A glow in the dark Batman model, or a slick golden snitch from Harry Potter, the possibilities are endless.
If not for yourself, this can be a few Birthday/Christmas presents off your list, as well as the knowledge that you created this wonderful object with your own hands…kinda.
Many gifts these days are quite general and predictable, but with a 3D printer and your imagination at your disposal, you can really get ahead of the gift-giving curve.
6. It’s Really Fun Once You Get the Hang of ItI’ve seen people create customized chess pieces, miniatures for Dungeons and Dragons, create their own games and build up sweet collections with 3D printing. This is a hobby which can be very fun and rewarding once you get over the initial learning curve.
Many times you don’t even have to go through a learning curve. When you have a well-built printer and have your settings down accurately, your prints should come out just as you picture, with a smooth, sturdy finish.
Your 3D prints don’t have to be just aesthetically pleasing, they can be functional objects that help you in your day-to-day activities.
I think one of the best things you can do with it is getting your family and friends involved in creating designs and seeing the final product. It’s a great way to bring people together in a fun and practical activity.
There’s a reason 3D printers are making their way into schools, universities and even libraries. There is just so much you can do with them.
People have printed survival whistles capable of going over 100 decibels, a happy birthday cake topper sign, tap sprinkler attachments, smartphone stands and much more!
7. Get a Head Start in a Rapidly Growing Industry3D printing is growing at a rapid pace and the technology behind it is only getting better and better. We’ve seen advances with printing prosthetics, prototypes, houses, and even 3D printers themselves (although not completely…yet).
It’s still somewhat in the early stages of development and once more people realize it’s potential, I can see a real snowball effect of 3D printing spreading around the world.
Lower income countries within Eastern Europe and Africa are seeing increases in 3D printing production as it gives people the ability to produce their own goods and equipment.
Being able to simply transport a 3D printer and the material to a location, then printing out objects saves massively on transport costs, especially to places with hard to access areas.
The numbers really speak for themselves. I’ve seen consistent annual growth figures for 3D printing sectors in the 15% range and even higher in the lower income areas. Just imagine in 10 years how far 3D printing will go, don’t be behind everyone else!
In just the last 3 years we’ve seen a massive influx of 3D printing manufacturers, to the point where printers are very affordable and beginner-friendly. It used to be a niche where only technically gifted people would be able to make real use of it, but times have changed.
There are many 3D printer enthusiasts out there who have made their craft a source of income. In today’s digital world, it’s increasingly easier to connect with people who demand specific objects and are willing to pay for that object.
Even though there are 3D printing services out there, this is a market people can still tap in to, or you could create your own!
If you have a niche which have a high demand for objects such as board games or children’s toys, you can target this to make money. You could build up a following on social media, forums and create your own website if you are really dedicated to this goal.
Some ideas that people have run with are Nerf guns and luxury vases, and they look to be pretty successful.
Even training people to 3D print can earn you some money. Many people are beginning to see the potential of 3D printing and want to learn how to become well-versed in the craft.
You could offer training to people or even create 3D printing courses to the growing number of people who are interested.
Being able to design and print objects to requested specifications is a well sought after skill, and people are willing to pay you for such a service. Get really good at it and it can be a side hustle for years to come.
9. Help Educate Your Children to be Technical & CreativeAlthough 3D printing is in its infancy stages, it has great benefits in the educational sector, especially for the younger people out there. Many educational organizations such as schools, universities and hospitals have introduced 3D printing in many creative ways.
There are many new learning possibilities with 3D printing, such as seeing actual designs from the computer come to something real and physical.
Being able to interact with the finished product and show people what you’ve created is a special kind of opportunity for children out there.
Everyone knows that children get excited when they can engage with practical activities. 3D printing is exactly that, and it takes bored students away from the usual reading and gives them interest in education.
3D printing isn’t the easiest thing to learn, but once you do learn it you can bet you’ll come out better at critical thinking and problem-solving.
It is an activity that really trains your logic and brain power as well as the creative mind. Being able to 3D print objects of complex shapes and sizes has the effect of creating innovation and the possibilities that students can create are never ending.
When people get the hands-on experience rather than just listening or reading, they can remember information at a better rate. Not only do students get the practical experience, but they retain the information at a relatively better rate than normal.
Universities in many places now have 3D printers for students to use at their own leisure. In the future, more and more universities and organizations will adopt this, so give your children the opportunity to start early and be the top of the class!
10. 3D Printing Can Be Environmentally FriendlyAccording to Science Direct, with a global adoption of the additive manufacturing process (3D printing), we could reduce global energy use by 27% in the year 2050.
The nature of 3D printing means that there is little to no waste because the material is being added to the final product compared to traditional methods of manufacturing, which takes away from a bigger object to make the final product.
Traditional manufacturing lends itself more to larger objects and high volume, while additive manufacturing is more suited to specialist smaller, intricate parts.
In many cases, additive manufacturing won’t be feasible for demands in production as supply won’t be able to keep up.
In cases where we can switch to additive manufacturing, it’s seen as a benefit to the environment.
Printing materials in this fashion reduces waste and mostly uses only what will be in the final product. The amount of electricity these printers use is relatively low compared to other traditional manufacturing methods.
I’ve written about how much electricity is used in 3D printing.
The usual process of manufacturing is quite a long process, from material extraction, to assembly, to the actual manufacturing and so on, it can leave a sizeable carbon footprint overall.
3D printing doesn’t have the several steps involved in making a final product, more so the minimal refining and assembly stage.
We also can greatly reduce factors such as transportation, storage facilities, logistics and much more.
This gives 3D printing and additive manufacturing the comparative advantage in environmental impact.
The negative I can point out with 3D printing is it’s widespread use of plastic, which does unfortunately generate its own carbon footprint in the material extraction.
The good thing here is the ability of 3D printers to use a wide range of materials so you are not inclined to use these materials if you choose not to.
11. 3D Printing Gives a Competitive EdgeAn example being how its introduction into the hearing aid industry created a massive takeover in how they are manufactured. Over a very short period of time, the whole industry changed its technique to incorporate 3D printing into its creation.
A real majority of companies which adopt the additive manufacturing process of 3D printing report their ability to gain a competitive advantage over other companies.
According to Forbes, it is 93% of companies using this technology in 2018 that gained this, and it’s due to reduced time to the market, adaptability in manufacturing and a shorter production process.
Not only do companies gain this advantage, but they also increase their product quality and service through the 3D printing technology. The speed of innovation allows lead times for model building to go from weeks or days to a matter of hours in many cases.
The cost of production is greatly lowered wherever 3D printing is adopted. There is real freedom of choice in design and customization for complex, yet durable manufactured products.
The costs of 3D printing is greatly reduced for many reasons, one of the main ones being the reduction in labor costs due to the 3D printer doing most of the work.
Once the design is created, and the settings are input, 3D printers do most of the work after that, so labor costs can be reduced to almost zero in the manufacturing process.
It so happens that 70% of companies that use 3D printing in their field increased their investments in 2018, compared to 49% in 2017.
This just comes to show how much of a change 3D printing is making in the world of business and innovation, and I can only see it growing in the long term.
8 Reasons Why You Should Not Buy A Home 3D Printer « Fabbaloo
A typical home 3D printer [Source: Fabbaloo]Many Fabbaloo readers own their own 3D printer, while others contemplate buying one. But should you?
There are plenty of good reasons for having a 3D printer at your disposal, not the least of which is the ability to rapidly build almost any type of plastic part you might require. But there are some cases where it might not be advisable to buy your own 3D printer and operate it at home.
You Can’t Afford It
Sure, there are some pretty inexpensive 3D printers available today, even around the US$200 mark. That’s a low price, but for that price you often receive not only a very basic machine, but one that will potentially require considerable tuning and even some modifications to work reliably. To avoid this effort, you’d have to buy a more expensive device, but that might be out of your budget.
Don’t buy a 3D printer unless you can afford the type of machine you really need.
You Have Only One Project To Do
While it’s exciting to 3D print objects, many people stall after a few weeks of usage simply because they run out of things to print. It’s possible to browse online 3D model repositories like Thingiverse or PrusaPrinters to find more printable content, but you could be just trying to justify the purchase unless you actually need or want the items printed.
Don’t buy a 3D printer unless you’re confident you have a notion of what you intend on doing with it for the long term.
You Don’t Know CAD
It’s easy to 3D print pre-made 3D models, but soon after that you’ll want to print your own designs. But do you know how to produce them? Learning proper 3D CAD tools is a nontrivial task, and depending on the tool you choose it could also be expensive.
Don’t buy a 3D printer unless you already know a CAD tool or have the intention of eventually learning how to use one, and have the time and money to do so.
You Have No Ventilation
The truth is that most 3D printers do emit some noxious materials, and it’s more than just nasty odors. They also emit undetectable nanoparticles that could be breathed in and who knows what kind of long-term health issues that may cause.
Don’t buy a 3D printer unless you have a properly ventilated area in which to place the device, or intend on setting that up.
Someone Won’t Like The Noise
Many 3D printers, aside from the most recent devices, are pretty noisy. The stepper motors driving the motion system can buzz repeatedly as they move axes back and forth. Depending on the location of your device, there could be an annoying noise echoing through the home and that could be quite annoying to anyone not as excited about 3D printing as you are.
Don’t buy a 3D printer unless you are certain you can keep it quiet or there’s no one else to hear it.
Or The Smell
Even with ventilation, desktop 3D printers do emit odors. Some of them are pleasant, but most are awful plastic smells that could put off almost anyone. The smells vary by material, and that means you might suddenly find your home smelling awful if using a new filament. And don’t get me started about resin 3D printer materials.
Don’t buy a 3D printer unless you’re willing to smell nasty odors during print operations.
You Have Pets Or Very Small Children
Most desktop 3D printers are “open style” in which the moving parts and hot end are exposed to the air. This results in a lower price for the machine, but also introduces the possibility of an accident, should someone or something stick an appendage into the wrong part of the device.
This could happen if you happen to have very small inquisitive children on the loose or even pets that might stick their nose into the wrong area and suddenly find themselves trapped or even burned. Not safe!
Don’t buy a 3D printer if you have small children or pets that cannot be properly secured from the 3D printer.
You’re Not A Fix-it Type
Desktop 3D printers are not exactly like other household appliances: they break and you have to fix them. Your toaster likely will last decades without incident, but your 3D printer will last mere hours until something goes awry.
Even worse, while you could call someone to drop by and fix your broken dishwasher, you can’t easily do that for a broken 3D printer. There just aren’t a lot of service companies yet.
Don’t buy a 3D printer unless you are prepared to do some fixing on your own.
And there you have eight reasons why you might consider NOT buying a 3D printer for your home. They are now in the price range of many people, but there are more factors to consider.
13 notes about 3D printing, after 3 years of owning a 3D printer / Habr
This article will be, first of all, of interest both to those who have directly dealt with 3D printing, that is, who owns a 3D printer, but also to those who are just about to join the ranks of 3D printers and are thinking about buying their own printer.
In the framework of this article, I want to present my observations, as a direct owner of a 3D printer, for more than 3 years.
Despite the fact that 3D printers have been known for a long time and, in my memory, have become widely used, judging by the information on various resources, starting around 2010 (I may be wrong, these are my subjective observations), for a long time I ignored this area, it’s hard to say why…
Probably thought it was some kind of "childish pampering", another hype topic for which there is simply not enough time. ..
The turning point happened when one of the wheels on my travel suitcase wore out. You know, a big plastic suitcase, with four spinning wheels on the bottom. Unfortunately, it is a “rather disposable thing”, due to the lack of bearings on the wheels, which is why the wear of the friction point of the axle and wheel allows the suitcase to last no more than one or two seasons.
And it’s like “lightning flashed in the middle of the day: 3D printer!” It is with his help that I can fix this problem! Looking ahead, I’ll say that I didn’t succeed in fixing the suitcase in this way, so I had to use a different approach ...
As a result, I “upped” it - installing wheels from unnecessary roller skates. Thanks to this “up”, the suitcase has become a real all-terrain vehicle and, even being very loaded, it rides easily - pushed forward even with “one finger”. And even in the snow, 5-6 cm thick. A tank, not a suitcase turned out! By the way - I took spinning wheeled "units" in Leroy. Then he took off and threw out his native plastic wheels from there, inserting from roller skates:
But this thought itself became a kind of trigger that allowed me to finally join the world of printers and buy my first 3D printer.
Like many, before buying it, I studied various forums and sites for a long time, delving into all the subtleties. And for some reason, I immediately liked the type of printer called the delta printer. Probably because during operation it looks like some kind of "alien device".
If at your leisure you like to sit “looking into the carpet”, then with the advent of such a printer you will have a much more interesting activity, even hypnotizing, one might say :-))
And this, in fact, is my delta (if anyone is interested), which went through, let's say, the "ultimate up": all the electronics are placed upstairs, on a self-made welded frame, covered with polyethylene and a magnetic door is made. The coil with a bar is installed at the top, on the frame. The axis on which the coil is put on is machined on a lathe from aluminum and a bearing from the VAZ timing is inserted into it. As a result, the coil - "rotates even from the passage of a fly nearby":
Well, yes, I won’t argue for a long time, let’s start reviewing the main facts that I have accumulated as a result of owning this car ... The facts are purely subjective and may differ from your vision. In any case, I will be glad to comments, clarifications, etc.
▍ NOTE 1. Delta is good, but...
Here I should give a number of my observations regarding the delta printer:
- It contains a completely finished frame of the future box, which makes it easy to form a heat chamber. I understand that many printers are made in the form factor of a “certain box” (but this point cannot be ignored), which greatly facilitates the process of wrapping this box with heat-insulating material.
In my case, as such a material, I used a plastic film.
- Already thanks to its design, delta allows you to work at much higher speeds than XY printers. By the way, it is on the delta principle that many modern high-speed industrial robots are built to sort various parts directly on the conveyor belt:
However, this plus does not allow to fully realize the occurrence of parasitic vibrations, even despite their suppressors:
Thus, accurate printing is possible, only at speeds (at least that was the case for me), no more than 60 mm per second. A complex procedure for aligning the movement of the head parallel to the table, which is why, for many, the so-called "lens" appears. People struggle with it with varying degrees of success, but I have not encountered this on my printer and for me, therefore, the “lens” has never been a problem. At the same point, it is worth noting the calibration of the table, which was initially absent on the first deltas, and I had to use an external third-party solution from one American do-it-yourselfer called EZBED. This solution was a hardware-software complex that allows you to quickly and easily calibrate the printing table, that is, to let the printer understand its geometry. Modern printers do not have this issue as they come with a built-in calibration solution. It is worth noting that I solved this problem by attaching a limit switch to the print head, and using the Marlin-1.1.9 firmware.
▍ NOTE 2. "Size doesn't matter..." :-)
When I got the printer, I was impressed by the possibility of huge printouts, a la the handguards of some futuristic rifles, huge body parts, etc.
However, if you try to analyze the results of your many years of practice, it turns out that in most cases, rather small objects were printed that easily fit in the palm of your hand, a maximum of two palms. Despite such a seemingly small size, the printing of these details took a significant amount of time. Of course, this very much depends on which nozzle you print with. But, despite this, it is difficult to disagree with the fact that most of the printed parts will be quite utilitarian and small in size.
Therefore, to be honest, the need for a printer that allows you to print "Venus de Milo in life size" is not obvious.
Of course, you can object to me that “I’m going to buy a printer, I’ll get used to it a little and I’ll get started!!!”
One simple point must be taken into account here: there are no universal things. And in order to understand how much 3D printing in general and your printer, in particular, you will need to solve your problems, and how much it will be able to solve such problems, you just need to first try the 3D printing method personally and then a lot will become clear to you .
Therefore, for a beginner, I recommend taking a small printer that allows you to print extremely small items that fit in the palm of two. With such a device, you will definitely never lose, as it will always be needed. In addition, with its help you will be able to get used to the printing process and, if necessary, purchase a larger device, already clearly understanding its capabilities and ability to solve your set of tasks.
▍ NOTE 3. "What type of printer to get."
Based on the foregoing, I do not recommend taking a delta printer and this can be said right away.
Not because it is bad, in fact, it prints quite accurately, its main problem (in my opinion) is the inability to print rectangular flat, fairly large case components, as well as the inability to fully realize high-speed work, since the quality drops critically. Here it turns out to be a rather offensive situation - the printer can work quickly, but this cannot be done, since the quality will be “nothing”.
And then what kind to take? Depending on the budget and capabilities, I recommend taking any cube printer, for example, the same Core XY (the head moves, and the table goes down as the model “grows”, from top to bottom):
Image source: thingiverse.com
Such a printer allows you to easily print fairly large flat parts of cases, has good speed and accuracy. In addition, the presence of a rigid box-shaped frame allows it to be easily covered with polyethylene to create a sealed heat chamber. In addition, the very fact that the table does not move while working reduces the number of problems with model peeling.
However, the advantages of this printer will not be fully revealed if it has a direct extruder. On the one hand, it will allow printing with rubber-like materials, on the other -
large inertia and head weight. And these are parasitic vibrations, wear of the fur. parts, etc. (like everything in life, “we treat one thing and cripple another” :-))
At the initial stages, this may not be necessary, but in the future it may be necessary to print, for example, tires for your homemade car. And with this, the Bowden extruder has obvious problems. Although, in fairness, printing with such a rubber-like material is far from a daily need. However, whoever seeks will always find: over time, I found a way to “upgrade” my printer with a Bowden extruder to print with flexible materials. "Crutches" of course. But even so.
By the way, there are printers of a cheaper type, the so-called "drygostol", printing by moving the table and head:
They are inexpensive, moderately accurate, but they require a sufficiently high-quality gluing of the printed model to the table, because the table moves, and the model can come off when the table is jerked sharply. When printing large models, this can be a problem.
▍ NOTE 4. What to print with?
It's only a matter of taste and purpose. That is, if your printout will only stand on a shelf and should differ in some kind of aesthetic appearance, these are some requirements, if the printout is an engineering part that will be operated under conditions of increased mechanical load, these are different requirements. That is, in the first case, you can use any PLA, SBS plastics, and others with similar properties.
For engineering parts, for example, I only use ABS. It combines high hardness, strength and low price. Although I understand that now this last statement will cause a storm of comments in the style of “no! - there is even stronger, even better, the same PETG, etc. ":-)
Just here I wanted to say that thanks to the low price and the practical experiments that I conducted with ABS plastic, I realized that it is completely meets all my requirements.
However, the fact that ABS plastic releases carcinogenic substances when heated is quite annoying and forces you to take measures to prevent poisoning. For this, my printer prints completely closed and on an open balcony. After printing, the printer chamber opens, and it remains open in this form until it is completely ventilated and cools down.
▍ NOTE 5. "ABS is difficult to type on, it flakes, peels off the table, etc..."
With a properly configured printer (in my case, at a print temperature of 205 degrees, a thermal chamber and a desktop temperature of 100 degrees), the use of auxiliary techniques, for example, among which, one can name the so-called ABS juice (which is ABS- plastic dissolved in acetone), you can create wear-resistant and durable things, without any hypothetical problems.
For example, my printer has been printing for many hours at temperatures well below freezing. And this happened more than once, not twice, not three! And the print quality was excellent:
12-hour ABS printing at -4 C
▍ NOTE 6. Acetone for post-processing and ABS juicing
At one time, I wrote a fairly detailed article on this topic and I will try to give the main excerpts from it. The essence of the issue here is as follows: due to the fact that different GOSTs are used for the production of acetone, acetone differs in quality. Despite the fact that it would seem that “acetone is also acetone in Africa,” nevertheless, one type of acetone can differ significantly from each other. For example, ordinary acetone, which can be bought at any hardware store, such as "1000 little things", "store near the house" and the like, is very low quality acetone, smells disgusting (although someone like it, maybe someone likes its pleasant building aroma and "aftertaste" :-))).
In contrast to it, there is a much higher quality acetone, which, however, is not found at all in any household stores, even large chain stores, such as Auchan or Leroy Merlin.
This type of acetone is found exclusively in shops that sell varnishes and paints for automotive work, i.e. these are highly specialized shops for car workshops:
Acetone, which can be purchased there, is of excellent quality, smells almost like alcohol, quickly disappears,
:-) - this is a joke, of course, don't even try it.
However, its main advantage, compared to household type acetone, is that it perfectly dissolves ABS plastic and does not allow it to precipitate. For me personally, it was a very surprising observation when the same ABS plastic was perfectly dissolved with acetone from an auto shop, and completely precipitated when I tried to use household acetone (I just ran out of good acetone, and I had to use "what is ").
Therefore, if you want your results to always be excellent, then here is the right acetone. It should be labeled "for professional use":
▍ NOTE 7. What about ABS juice?
"ABS juice" is what printers call a mixture of acetone and pieces of ABS plastic dissolved in it. This mixture is smeared on the surface of the desktop before printing and allowed to dry. Thanks to this spread, the model easily sticks to the desktop and does not peel off during the printing process. After printing is completed and the platen has cooled down, the model can be easily separated.
All that needs to be said here is that, after trying different approaches over time, I settled on using flexible metal spatulas, also called "Japanese type spatulas":
According to the results of many tests, this method of spreading turned out to be one of the most convenient options, such spatulas can be cleaned very quickly and easily after work. In other words, highly recommended!
▍ NOTE 8. "Yes, nothing sensible can be done on it, I indulged a little and decided to sell it - you can't use it for anything good anyway"
I absolutely disagree with the statement above, which is periodically heard from newcomers to 3D printing. You can even say more: at the moment I can’t even imagine how I used to live without a 3D printer! Since it is he who makes it possible for any do-it-yourselfer to significantly expand their capabilities and make piece products, almost of factory quality! Of course, for this, appropriate hands must be applied to the 3D printer, but that’s another question… and take on things that I would never have thought to take on before!
For example, among my homemade products, the following can be listed:
- Heated sole for boots, which is a hose integrated into the insole (and filled with household silicone from a household store), through which water flows, heated with a catalytic type hand warmer.
Water is pumped using a small peristaltic pump. The engine with a metal gearbox, which is used in the creation of this pump, allows you to develop a force of 3 kg, which is even redundant for this homemade product. The engine is powered by Peltier elements mounted next to the catalytic heater. The project is currently in progress.
- Centrifugal water pump mounted on the shaft of an internal combustion engine that drives a high pressure wearable air compressor with a pressure of 500 bar. The pump pumps coolant through the casing of the high pressure pump, or rather its second stage. Despite the fact that the pump is 3D printed and runs at over 6000 rpm, nothing “fell apart, fell apart, didn’t break.” As you can see in the photo, the pump is installed instead of the “starter”, that is, the armstarter. The compressor scheme as a whole is as follows: 2 engines. Connected by clutch. One is heavy duty. The second is modified and turned into a high pressure compressor:
Yes, before assembling this, I also did not believe that this was possible. Moreover, even when I collected it, I did not believe my eyes :-))). However, it is a fact…
- I printed a number of Rank-Hilsch test tubes, the essence of which I have described in detail in this article.
- Printed mass of parts, more than 100 pieces, to create 10 web-controlled robots. There was also a detailed article about this here.
Well, and a bunch of all sorts of useful and not very crafts. As you can see from my crafts above, I have a special passion for creating some useful things, a utilitarian direction. That is, so that the printout is useful, and does not belong to the type “yyy breathe, Mikola, what am I doing here” :-), and then put it on the shelf and that's it. Although, engineers are also not alien to beauties, and this will be my next fact below.
▍ NOTE 9 Proper placement of the model when printing is half the battle
It would seem an obvious fact, but many underestimate it. Here I mean the following: by experience, I accidentally discovered that when printing various statues (in which I, completely unexpectedly for myself, discovered another passion of mine), it is advisable to place the statues at an angle to the printing table.
This allows the layers in the printout to run at an angle of approximately 45-50 degrees to the model. The result of this is that the printed model is almost completely invisible layers and the model looks like it has been post-processed, but at the same time retains a deep matte color, which, to my personal taste, is more like a marble than a glossy result of processing in an acetone bath :
An additional advantage of this method is that the layers going at an angle of 45-50 ° to the model give it additional strength. This is especially true for printing statues, which contain many thin elements that are easily chipped when the statue is accidentally dropped from a table or shelf (learned from bitter experience, this happened to me many times, and ruined some fairly decent prints).
That is, the layers going across the model, if the model has a large length in height, does not allow it to maintain sufficient strength. For better understanding, I tried to illustrate this point in the figures below:
▍ NOTE 10. Bleeding must be taken into account when printing, especially if the model is composed of separate parts and must be assembled by joining these parts to each other, entering into each other, etc.
I tried to illustrate this point in the figures below. The implication here is that if you're printing a composite model, you need to correct for the amount of bleed on the plastic (I'm not sure what it's called, but at least I tried to convey what I mean). If this is not taken into account, then the model will not fit.
For example, in my case this correction is 0.2 mm per diameter - if I want the model to fit more tightly; if I need a free joint, without excessive density, then 0.3 mm per diameter:
That is, suppose that the blue part has a size of 10x10mm. So it must be modeled in a CAD program as 9.8x9.8 mm (if we want it to sit tight) or 9.7x9.7 mm (to sit freely). Well, or expand the hole in the green part, and leave the blue one as it is.
This is often a problem when you download a prefabricated model from the Internet - but it is not going to, even if you crack! And because no amendments have been made…
For your particular case, the amendments may be different.
▍ NOTE 11. What if...
In fact, this note complements note number 8. Using a 3D printer allows you to create metal parts using a printed 3D model. For this, the casting method is used according to the lost wax or burnt model. In our case, we will deal mainly with metal casting on a burnt model.
Briefly, it looks like this: printing a 3D model (using PLA plastic) → pouring it with plaster → burning PLA plastic, simultaneously with burning the mold, in a conventional stove oven → pouring the resulting mold with molten metal (melted in a conventional microwave) .
Image source: 3dtopo.com
I told about a simple method of melting metals in a home microwave oven here.
There was even a good article about casting on Habré.
▍ NOTE 12. Durability?
Despite the fact that ABS plastic is called exposed to ultraviolet radiation and, accordingly, burns out, losing its strength in the sun, in my practice, even printouts that are constantly exposed to the sun have not lost their strength and color at all, continuing to be successfully used and Currently.
It should also be added here that printouts are constantly exposed not only to the rays of the sun, but also work continuously in damp conditions!
As such printouts, I can give an example of winglets for technical cranes, which I printed out, but, unfortunately, did not photograph this process; as well as fasteners on shoes that I use “both in the snow, and in the heat and in the pouring rain, and in general are always with me”:
▍ NOTE 13.
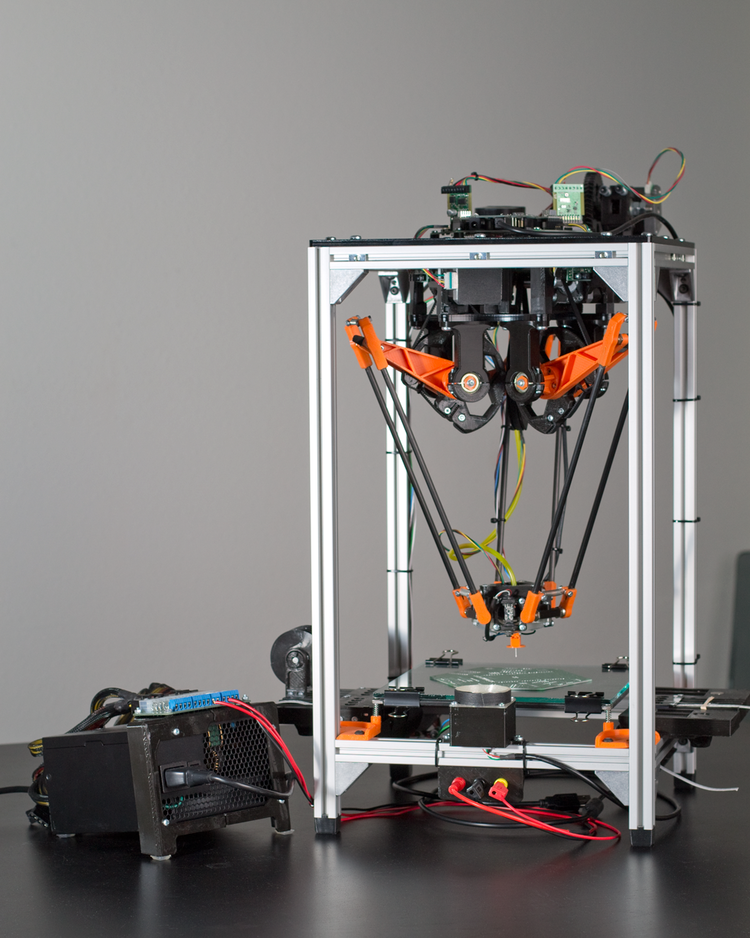
Periodically, there is a need to print parts containing a particular thread. Modeling such products requires a good understanding of what a thread is in general, as well as what corrections need to be made in your particular case, which I have already described above.
But since I've owned a metal lathe for a long time, I'm not at all happy with the 3D printed carving that looks like "something very carving-like".
I am satisfied with an exceptionally perfect carving. Therefore, I keep in stock a large set of various taps and dies, with which I cut all my threads in plastic printouts:
I posted a photo of dies and taps not to brag, but to make the reader understand that serious carving requires a serious approach (unfortunately). And considerable costs for all this thread-cutting iron ...
To create your own threads (both threaded channels and threaded pins), I recommend the following reference materials: for holes, for pins.
Well, that's where I want to end my story and note that he does not claim to be exceptionally accurate and exhaustive. Nevertheless, I tried to state a number of my observations. It will be interesting to read yours, in the comments!
95% cheaper: how 3D printing works for today's business
Unfortunately, even industry experts do not fully understand the potential of using additive technologies in their work. Because of the high-profile headlines that a car or even a house was printed on a 3D printer, the whole essence of the technology and its advantages over traditional working methods are lost. After all, for the most part, it is needed to replace routine processes and make the final product cheaper than when working with traditional means.
From stone carving to additive manufacturing – why do businesses need 3D printing?
For any business that produces a physical product, a prototype is essential. Previously, the processes were labor-intensive - prototypes had to be sculpted from clay or carved from stone, which took a lot of time, and if you made a mistake somewhere or something needs to be changed, you had to redo the whole form again.
Today, thanks to additive technologies, businesses have the opportunity to automate these processes and reduce not only the time spent on a project from several days to hours, but also the funds invested in the product.
Thus, different departments in companies benefit from the introduction of technology:
- R&D employees begin to do their work faster, as the production of a prototype is automated and takes less time;
- Designers can quickly prepare new iterations, since all work is completely digital;
- Everyone who demonstrates their products - from sales to top management - can convince customers and business partners with the help of visual prototypes;
- Marketing departments can demonstrate prototypes to focus groups to prepare a final product that meets the needs of the client, and additionally make small souvenirs for promotional purposes.
In-house and outsourcing - 3D printing methods
There are three main methods of prototyping in terms of additive technologies: outsourcing work to a 3D printing company, printing with your own industrial printers, or working with your own desktop printers. The choice of method depends more on the scope of work in the company and its financial capabilities.
Consider the advantages and disadvantages of each method.
3D Printing Bureau are best suited for small complex jobs. It is worth contacting the bureau when you have less than five orders per month, but they require non-standard materials. Bureaus are also useful when different materials are needed to make each item. In other cases, this is the slowest and most expensive option.
Advantages:
- Bureaus work with several 3D printing technologies at once, such as SLA, FDM and SLS;
- The bureau has more materials in stock, including rare or very expensive ones;
- The Bureau will advise on materials and their limitations;
- If contractors do not work well, then you can quickly terminate the contract and find new ones.
Drawbacks:
- The cost of a prototype will be ten times higher than when working with our own desktop and industrial 3D printers;
- Much slower than native 3D printing (may take weeks instead of one day).
In-house industrial 3D printers is a reliable option for large production (200 pieces per week or more). Products are made of one material, and their size is more than 30 cm³. This option may suit the R&D centers of the largest companies. However, businesses often do not use industrial printers in affordable volumes, which is why the cost of equipment will take a long time to “fight back”.
Advantages:
- Allows deep immersion in technology;
- Work faster than in cooperation with the bureau;
- The production of a product at high throughput will be cheaper compared to a bureau.
Drawbacks:
- Installation costs about $30,000 for an entry-level system, $300,000 for a full-fledged production system;
- Complete production systems require separate specialists to work with them, as well as more than 30 m² of production areas, industrial HVAC systems, finishing stations, cleaning stations, etc.;
- At low throughput, this will cost more than service bureaus and desktop 3D printers;
- Higher cost per part and total cost of ownership compared to desktop 3D printers, even in large scale production
- Limited range of materials compared to service bureaus;
- The cost of materials per kilogram is higher than for desktop printers.
Desktop 3D printers are great for businesses when they have a lot of projects and speed is important. For small companies, you can get one desktop printer to get a newly developed prototype within a few hours.
A larger business that manufactures more than 200 items a week assembles a farm of several printers - for them it is cheaper than installing industrial ones. Such farms will also give more flexibility and provide access to several materials at the same time. Sometimes companies can use the services of a 3D printing bureau when larger parts or rare materials are needed for work.
Benefits:
- The cost of a printer to get started is 10 times less than a commercial one;
- Cost per part and total cost of ownership is the most affordable of the in-house manufacturing options;
- Allows deep immersion in technology;
- Compact, resulting in less space requirements.
Drawbacks:
- Low reproducibility compared to industrial machines;
- There will not be many manufactured products in one batch;
- Not all desktop 3D printer manufacturers provide long-term warranties and support.
How Lush saves on 3D printing
Lush is one example of how the company is using 3D printing with its own desktop printers. The company has located its farm in an R&D center in the south of England, where employees come up with ideas for new forms of cosmetics.
The R&D center itself also offers support to Lush's global manufacturing sites in the UK, Japan, Australia, Croatia and Germany. They can order the right molds and special tools to give cosmetics their whimsical look.
3D printing on its own printers has opened the way for Lush employees to creatively solve problems and quickly respond to customer requests.
The team now designs a product and launches production in less than a day, with 4.5 hours spent printing a new mold. This was also the case with Lush, a charity project to help wildlife in Australia during last year's wildfires, which brought the new product to market within a week.
With access to the full range of digital manufacturing tools, the R&D center completed 580 designs in the first half of 2020. This saved a significant amount of time and labor. In doing so, they were able to respond more quickly to the pandemic and prioritize projects that clients needed in a volatile year.
The 3D printing process itself turned out to be several times cheaper than traditional methods of work when delegating them to outsourcing - an average of 95%.
Comparison of in-house and outsourced 3D printing costs Source - Lush and Formlabs calculations
Product | The cost of outsourced work | Cost of printing on a 3D printer (including labor) | Saving |
Thank You Coin Mold | £114 | £6 | 95% |
Architectural model of the R&D center | £15,000 | £900 | 94% |
Special tooling for production | £99 | £4.![]() |