3D printing printers
The Best Cheap 3D Printers for 2022
While we'd hesitate to call 3D printing a mature technology, you might say it has reached its teenage years. Through their first decade-and-change, 3D printers have come down in price, grown easier to set up and operate, and become more reliable. And you may pay less than you expect: Many once-high-end features have migrated down to inexpensive models.
PC Labs has been reviewing 3D printers since 2013. Today, the state of 3D printing is strong, but that wasn’t always the case. For the first several years, it was often an adventure getting one of these printers up and running, let alone successfully through our testing regimen. Issues with filament-based—aka fused filament fabrication (FFF) or fused deposition modeling (FDM)—printers were abundant.
Filament feeders had to be coaxed into delivering filament from the spool to the extruder. Print beds had to be manually aligned. The extruder or hot end had to be positioned just right to minimize the gap between the nozzle and the build plate (the flat surface on which the object is printed). Objects frequently stuck to the build plate, and required careful, sometimes unsuccessful, efforts to pry them off. These and other issues required painstaking effort to resolve, often combined with calls to tech support.
Not so much anymore. While they can still be rebellious at times, 3D printers have grown up a lot, and achieving the 3D printer basics has gotten a lot less likely to end in a shouting match over small things. And they've gotten a lot more affordable, too, for curious DIY-ers and hobbyists to try.
If you're in the market for a beginner or low-cost 3D printer, it's important to know how lower-end models differ. Read on for mini-reviews of the top budget 3D printers we've tested. After that, we go into more detail on understanding the 3D printer specs and tech relevant to beginning buyers. Ready to take the plunge? Read on.
Original Prusa Mini
Best Overall Budget 3D Printer
4.5 Outstanding
Bottom Line:
It requires assembly and calibration care (plus shipping from the Czech Republic), but the Original Prusa Mini is a compact, open-frame 3D printer that consistently produces superb-quality output for a great price.
PROS
- Top-notch object quality
- Supports a variety of filament types
- Useful, professionally printed user guide
- Great support resources
- Versatile, user-friendly software
CONS
- First-layer calibration can be tricky
- Only includes starter packets of filament
- Requires monitoring if young children or pets are around
Sold By | List Price | Price | |
---|---|---|---|
Prusa Research | $399.00 | $399.00 | See It (Opens in a new window) |
Read Our Original Prusa Mini Review
XYZprinting da Vinci Mini
Best Budget 3D Printer for Schools, Community Centers
4.0 Excellent
Bottom Line:
The XYZprinting da Vinci Mini is a consumer-oriented 3D printer that provides a winning combination of low price, ease of setup and use, solid print quality, and smooth, misprint-free operation.
PROS
- Very low price.
- Reasonably priced filament.
- Good print quality.
- No misprints in testing.
- Easy setup and operation.
- Quiet.
- Prints over a USB or Wi-Fi connection.
CONS
- Occasional problems in trying to launch prints.
- Removing printed objects from the print bed is sometimes tricky.
Sold By | List Price | Price | |
---|---|---|---|
Walmart | $199.95 | $199.95 | See It (Opens in a new window) |
Amazon | $199.95 | $199.95 | See It (Opens in a new window) |
Read Our XYZprinting da Vinci Mini Review
Toybox 3D Printer
Best Budget 3D Printer for Children
4.0 Excellent
Bottom Line:
The Toybox 3D Printer works well as a model designed for children, offering reliable printing from a browser or mobile device and a few thousand toys to print, plus creative options to output drawings or photos. Just bear in mind the tiny build area.
PROS
- Reliable, misprint-free printing
- Easy setup
- One-touch operation
- Well-composed help resources
- Access to more than 2,000 printable toys and projects
- Lets you create your own printable designs
CONS
- Tiny build area
- Not ideal for importing 3D files created elsewhere
Sold By | List Price | Price | |
---|---|---|---|
Amazon | $299.00 | $299.00 | See It (Opens in a new window) |
Toybox Labs | $379.00 | $299.00 | See It (Opens in a new window) |
Read Our Toybox 3D Printer Review
Monoprice Mini Delta V2 3D Printer
Best Budget 3D Printer for Beginners, Non-Techies
4.0 Excellent
Bottom Line:
3D printing gurus will be intrigued by the Monoprice Mini Delta V2's use of the delta rather than Cartesian coordinate system, but beginners will just enjoy its low price, ease of use, and speedy printing.
PROS
- Sub-$200 price
- Quick, nearly misprint-free printing
- Easy setup and operation
- Sturdy steel-and-aluminum frame
- Supports multiple filament types
CONS
- Tiny build area
- So-so print quality
- Mere one-year warranty
Sold By | List Price | Price | |
---|---|---|---|
Amazon | $323.98 | $323.98 | See It (Opens in a new window) |
Read Our Monoprice Mini Delta V2 3D Printer Review
Anycubic i3 Mega S
Best Budget 3D Printer With an Open Design, Big Build Area
3.5 Good
Bottom Line:
The Anycubic i3 Mega S, an inexpensive open-frame 3D printer, produced decent-quality prints in our testing. To get the most out of it, though, may require precise calibration.
PROS
- Modestly priced
- Large build area for an inexpensive printer
- Supports a variety of filament types
- Generally solid print quality
- Uses well-known Cura software
CONS
- Finicky print-platform alignment
- Supported coils of filament are small
- Poorly placed spool holder
Sold By | List Price | Price | |
---|---|---|---|
Amazon | $229.![]() | $229.98 | Check Stock (Opens in a new window) |
AnyCubic | $279.00 | $279.00 | Check Stock (Opens in a new window) |
Read Our Anycubic i3 Mega S Review
Anycubic Vyper
Best Budget 3D Printer for the Biggest Build Area Possible
3.5 Good
Bottom Line:
Anycubic's modestly priced Vyper whips up large 3D prints on its open-frame design, and provides automatic print-bed leveling. Just know that some minor assembly is required—and printed objects may require a bit of cleanup.
PROS
- Relatively large build area
- Automatic bed leveling
- Simple assembly
CONS
- Short (one-year) warranty
- Includes only a small starter filament coil
- Using Cura software with the Vyper requires tweaking a couple of settings
- Test prints showed some "hairy" filament residue
Sold By | List Price | Price | |
---|---|---|---|
Amazon | $429.![]() | $429.99 | See It (Opens in a new window) |
AnyCubic | $369.00 | $319.00 | See It (Opens in a new window) |
Read Our Anycubic Vyper Review
Creality Ender-3 V2
Best Budget 3D Printer for Tinkerers and DIY Types
3.5 Good
Bottom Line:
Hands-on tweaking defines Creality's budget-price Ender-3 V2, an open-frame 3D printer that you build from a kit. It produces generally above-par prints, but its print bed can be tricky to keep leveled.
PROS
- Inexpensive
- Slightly above-average print quality
- Good-size build area for its price
- Supports several filament types
CONS
- Manual print-bed leveling can be tricky
- Setup instructions could be deeper, more legible
- Questionable quality control on some parts
Sold By | List Price | Price | |
---|---|---|---|
Amazon | $299.![]() | $246.00 | See It (Opens in a new window) |
Read Our Creality Ender-3 V2 Review
Flashforge Finder 3D Printer
Best 3D Printer for the Very Tightest Budgets
3.5 Good
Bottom Line:
The Flashforge Finder 3D Printer is moderately priced and offers good print quality, but it proved tricky to get up and running in our tests.
PROS
- Quiet.
- Good print quality.
- Connects via USB 2.0 cable, USB thumb drive, or Wi-Fi.
- Reasonably priced.
CONS
- Some objects pulled off the platform during testing.
- Poor documentation.
- Modest build volume.
- Limited to printing with polylactic acid filament (PLA).
Sold By | List Price | Price | |
---|---|---|---|
Amazon | $729.00 | $729.00 | Check Stock (Opens in a new window) |
Read Our Flashforge Finder 3D Printer Review
Polaroid PlaySmart 3D Printer
Best Budget 3D Printer for Dabbling in Small Objects
3. 5 Good
Bottom Line:
The Polaroid PlaySmart 3D Printer is a compact, stylish 3D printer with above-par overall print quality, but, alas, a tiny build area for the money.
PROS
- Small, lightweight for a desktop 3D printer.
- Easy to set up and use.
- Supports PLA, PETG, and wood composite filaments.
- Multiple-color support.
- Wi-Fi camera monitors print jobs.
- Prints from USB drives, SD cards, or mobile devices.
CONS
- High price for its capabilities.
- Small build area.
- Too-brief warranty.
Sold By | List Price | Price | |
---|---|---|---|
Amazon | $699.00 | $699.00 | See It (Opens in a new window) |
Read Our Polaroid PlaySmart 3D Printer Review
XYZprinting da Vinci Jr. 1.0 A Pro
Best Budget 3D Printer With Closed Design, Roomy Build Area
3. 5 Good
Bottom Line:
The XYZprinting da Vinci Jr. 1.0 A Pro is a moderately priced closed-frame 3D printer with a large build volume and overall good performance, but a potentially balky filament-feeding system.
PROS
- Spacious build area
- Works with third-party filaments
- Self-leveling print bed
CONS
- Build plate is not heated
- Limited to PLA- and PETG-based filaments
- Guide tube is prone to detaching
Sold By | List Price | Price | |
---|---|---|---|
Amazon | $299.95 | $199.95 | See It (Opens in a new window) |
Best Buy | $449.95 | $449.95 | Check Stock (Opens in a new window) |
Read Our XYZprinting da Vinci Jr. 1.0 A Pro Review
Monoprice Voxel 3D Printer
Best Budget 3D Printer for Cheap Filament
3. 0 Average
Bottom Line:
The Monoprice Voxel is an under-$400 3D printer that's easy to set up and use. It exhibits generally good print quality, but it was unable to print two of our test objects.
PROS
- Easy to set up and use.
- Budget price for printer and filament spools.
- Supports PLA, ABS, and several composite filament types.
- Versatile software.
- Prints over Ethernet or Wi-Fi, or from a USB thumb drive.
CONS
- Frequent misprints on certain test objects.
- Slightly balky touch screen.
Sold By | List Price | Price | |
---|---|---|---|
Amazon | $449.99 | $369.26 | See It (Opens in a new window) |
Walmart | $429.99 | $369.26 | See It (Opens in a new window) |
Read Our Monoprice Voxel 3D Printer Review
Buying Guide: The Best Cheap 3D Printers for 2022
How to Buy a Cheap 3D Printer
The biggest changes to 3D printers over the last few years have come to the cheaper models. Nowadays, many of those classic, ornery 3D-printing issues have been resolved (most of the time, anyway), even for consumer and bargain-priced 3D printers. Automatic print-bed leveling is the norm, and you can usually remove 3D-printed objects from heated and/or flexible build plates with a minimum of coaxing. And most 3D printer manufacturers have either developed and refined their own software, or have adapted an open-source printing platform such as Cura(Opens in a new window).
(Credit: Zlata Ivleva)
What separates more expensive 3D printers from cheap ones ("cheap" defined as $500 or less, for the purposes of this article) is often a select group of features. These include the build volume, the type of frame, the varieties of supported filament, the software, and the connectivity mix. Let's run through those in turn.
What's the Right Build Volume for a 3D Printer?
A 3D printer’s build volume is the maximum dimensions (HWD) of a part that it can print. (We say “a part” because a 3D-printed object can consist of multiple parts that are printed, then glued or otherwise pieced together.) While the smallest build volume of any 3D printer we have tested is 3.9 by 3.9 by 4.9 inches, we consider any build volume smaller than 6 by 6 by 6 inches to be small, any between that and 10 by 10 by 10 inches as medium, and any printer with at least one build dimension of more than 10 inches as having a large build volume.
(Credit: Molly Flores)
As a general rule, inexpensive 3D printers have small build volumes, while more expensive ones have larger build volumes. This depends in part on the type of printer. Closed-frame 3D printers—and most semi-open models, which have a rigid top, base, and sides but are open in front and, often, back—tend to have small build volumes, while open-frame printers, lacking as rigid a physical structure, often have relatively large build volumes for the price. You'll want to weigh the build volume against the kinds of objects you will print.
Should I Get an Open-Frame or Closed-Frame 3D Printer?
Which brings us to the frame "form factor" question: open-frame versus closed-frame. Closed-frame 3D printers are boxlike devices, with a rigid base, walls (with a see-through door in front), and top. Among their advantages? They muffle the operating noise, as well as reduce the odor from melted filament (which is potentially an issue with ABS plastic), and they provide some protection for people or pets who might inadvertently touch the hot extruder. A downside: They tend to have smaller build volumes than open-frame 3D printers, which have fewer (often, no) walls to constrict them.
(Credit: Zlata Ivleva)
Low-cost 3D printers include both open-frame and closed-frame models, as well as a few stereolithography printers. If a relatively large build volume is a priority, you’re likely to get more bang for the buck with an open-frame model. Open-frames do have some clear downsides by definition: They tend to be noisy, emit odors when certain plastics are melted, and provide little protection for someone who might touch the hot extruder.
(Credit: Molly Flores)
Also, recognize some potential negatives of open frames, depending on the model. Some require assembly, being essentially kits, and most require more setup care than a closed-frame printer, plus more maintenance to keep them running smoothly. Still, these very traits should not deter—and may even appeal to—hobbyists and DIY folks.
What Should I Look for in 3D Printer Software and Connectivity?
Gone are the days when tinkerers had to cobble together several different programs to get a 3D printer to run. Manufacturers either include their own 3D printing program or modify an existing platform such as the open-source Cura.
3D printing software performs three main functions: processing an object file (resizing, moving, rotating, and in some cases duplicating it), slicing it (into virtual layers, based on your chosen resolution), and printing it. These are almost universally combined into a seamless process. Some high-end printers have software that supports a wider range of settings you can tweak, but even the basic suites work at least reasonably well.
More likely to vary among the cheaper set is the array of connection options from model to model. Nearly all have a USB Type-A port to fit a thumb drive for printing from document files. Most also have a USB Type-B port for connecting directly to a computer, and some offer Wi-Fi, too (or as an alternative), while a handful let you connect via Ethernet to share the printer across a local network.
Some printers support storing 3D files on an SD or microSD card (which may also contain the printer’s system files). Most 3D printer manufacturers (even the discount ones) have a mobile app to launch and monitor print jobs, and a few provide access to cloud services from which you can print.
While high-end 3D printers tend to have an abundance of connection choices, discount models vary widely in their choices. Some are generous and some are basic, so it pays to assess what a given model offers.
What Should I Look for in Filament Support?
Filament support tends to be a key area that separates the cheaper models from the higher-end ones. (See our guide to understanding 3D printing filaments for more particulars.) Inexpensive 3D printers tend to support a limited number of plastic filament types, some of them only PLA and/or ABS.
Recommended by Our Editors
3D Printing: What You Need to Know
3D Printer Filaments Explained
(Credit: Molly Flores)
PLA (polylactic acid) is a biodegradable, plant-based polymer, while ABS (acrylonitrile butadiene styrene) is the same tough plastic that Legos are made from. Objects printed from ABS are durable and nontoxic, though the material can be tricky to work with. ABS can emit an acrid, unpleasant odor during printing, and the bottom corners of objects being printed with it have a tendency to curl upward a bit, especially if you are using a non-heated print bed. This can lead to unsightly prints, and/or prints prematurely pulling off the build plate, ruining them.
Many entry-level and low-price 3D printers stick exclusively to PLA. If you want to experiment with a larger variety of filaments—which include water-soluble filament, wood- and metal-laced composites, and both tough and flexible varieties—you may have to pay more, although a few discount models support a wide range of materials.
Should I Consider a 3D Printing Pen Instead?
Although they aren’t printers per se, inexpensive 3D pens are close kin to 3D printers—using the same filament types and a similar extrusion system—and we include them in the 3D printing category. Rather than tracing out a programmed pattern, you use the 3D pen much like a normal pen, except that you draw with molten plastic. You can trace a pattern or draw freehand, and even draw in three dimensions as the plastic quickly solidifies and hardens once extruded.
(Credit: 3Doodler)
Most 3D pens cost less than $100, and some cost $50 or less. At a glance, 3D pens may appear to be toys, but some artists and craftspeople have taken to them, as it is possible to make quite complicated and beautiful objects with them. If your aim in 3D printing is something closer to freehand design and free expression than computer-centric, structured, and repeatable output, you might give one a try.
So, What Is the Best Cheap 3D Printer to Buy?
Buying a budget 3D printer needn’t mean a world of sacrifice. Plenty of capable and reliable models sell at less than $500, and while they may not be as feature-rich as their more expensive cousins, there's no sense in paying for things you don’t need.
Many casual 3D-printing experimenters will be fine with printing over a USB cable or from a thumb drive, and sticking to PLA may be the best choice for a starter 3D printer. If you focus just on the features you want, you may be pleasantly surprised at what you find. Below, check out a spec breakdown of the best under-$500 3D printers we have reviewed, paralleling our picks above. Also, for a look at the broader market, see our guide to our favorite 3D printers overall.
Best 3D Printers Of 2022
Our list of the best 3D printers contains clear and concise information on all kinds of 3D printers.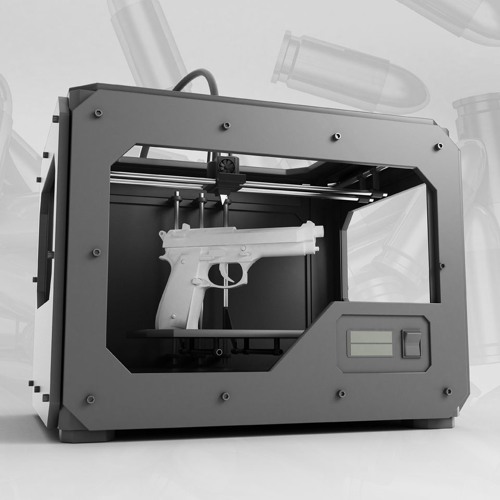
The best 3D printers have become more affordable, and the 3D printer market is growing at an explosive rate, with new brands and styles of printing making an appearance each year. Where many 3D printers used to be huge, expensive machines, developments in technology and production now mean that many of the best options you can buy are increasingly affordable and can sit on a desk in your home without needing workshop space.
Naturally, this means there's now a massive choice of 3D printers that cater to all sorts of user needs and budgets. While this choice is excellent, picking the best 3D printer for your specific needs can be difficult. However, this guide can help, as we pick some brilliant 3D printers for all uses and budgets, with clear buying advice to help you determine which one you should buy.
Printing hardware has taken off in recent years, so while a handful of filament printers (otherwise known as FDM printers) were all that was once available, there's now a wide variety of different styles to suit your needs across a range of budgets.
Unlike office-style printers that just print ink onto paper, 3D printers turn digital models into real-world objects made from plastic, metal, and wood. FDM printers now come in all shapes and sizes and are well-suited to prototyping and crafting larger objects. At the same time, resin-based (SLA, MSLA, and DLP) allow for much greater detail, typically at a smaller scale, making them a fantastic buy for anyone looking to design jewelry or create tabletop miniatures.
You can use 3D printers to build complete products, make spare parts, or simply create things you’ll find helpful for your home, office, and workshop. And, since 3D printing technology is within the grasp of just about anyone, you don’t have to utilize one to your advantage.
Whether you’re just getting your feet wet or are an expert, here are the best 3D printers ranges to consider. We've compared these printers across size, functionality, and use case, so there should be something for you, whatever it is you’re looking for. We also looked at their print resolution, build platform, filament type, and pricing.
Remember that the more expensive choices are better suited for professionals, while the best cheap 3D printers are ideal for those just starting.
The best 3D printers of 2022 in full:
Why you can trust TechRadar Our expert reviewers spend hours testing and comparing products and services so you can choose the best for you. Find out more about how we test.
The best 3D printers
Original Prusa MINI (Image credit: Prusa)1. Original Prusa MINI+
Small, affordable, and remarkable 3D printer
Specifications
Print technology: Fused Deposition Modeling
Build Area: 18 x 18 x 18cm
Minimum layer resolution: 50 microns
Maximum layer resolution: 200 microns
Dimensions: 33 x 33 x 38cm
Weight: 4.5kg
Today's Best Deals
Reasons to buy
+
Great value for an FDM printer
+
Easy to use
+
Supports a variety of filament types
Reasons to avoid
-
Reel sits separately
-
Imperfect print quality
-
Calibration can be tricky
This affordable open-frame 3D printer is small enough to sit on your desk and easy enough to assemble yourself without expertise. It comes in kit form and uses FDM (Fused Deposition Modeling) to turn popular modeling materials such as PLA, PETG, ASA, ABS, and Flex into accurate printed products.
There’s a Network LAN and USB port for simple connectivity and a user-friendly interface. The 2.8-inch 65k colour screen makes navigating the options and settings easy, and on first starting the machine, it takes you step by step through the set-up process. This entry-level printer should be the first choice for crafters, modelers, and engineering enthusiasts.
The Original Prusa MINI+ is a replacement for the Original Prusa MINI (minus the plus), the key advantage being that it now comes with a superPINDA sensor, which is not temperature dependent allowing the first layer calibration to be faster and more reliable.
Read the full review: Original Prusa MINI.
CEL-UK RoboxPro (Image credit: CEL-UK)2. CEL-UK RoboxPro
Best 3D printer for commercial printing
Specifications
Print technology: Fused Deposition Modeling
Build Area: 210 x 300 x 400mm
Minimum layer resolution: 50 microns
Maximum layer resolution: 500 microns
Dimensions: 513 x 508 x 605mm
Weight: 26kg
Today's Best Deals
Reasons to buy
+
Swappable print heads
+
Dual Extruder and auto bed leveling
+
Network ready, no wired needed
Reasons to avoid
-
Large scale printer, not ideal for home use
-
Can be difficult to load filament
CEL-UK is a leader in 3D Printer innovation, with the original Robox printers introducing many new features to the world of FDM 3D printers. The RoboxPro is Robox on a large scale with a feature set that reads like a 3D print wish list; auto filament loading, auto bed leveling, Wi-Fi, network printing, and swappable tool heads.
The main focus of the machine is quality and reliability, designed for anyone wanting a printer that can realize product ideas and get them to market. The enclosed design makes it an ideal choice for commercial and educational use.
There's a sizable touchscreen panel built into the front of the machine. It displays the current materials and can be used to navigate settings and print directly from USB or other external drives.
Read the full CEL-UK RoboxPro review.
(Image credit: Creality)3. Creality Ender-5 S1
An ideal 3D printer for any 3D print enthusiast or small business on a budget
Specifications
Print Technology: Fused Deposition Modeling
Build Area: 220 x 220 x 280mm
Minimum Layer Resolution: 0. 05mm
Maximum Layer Resolution: 0.35mm
Dimensions: 425 x 460 x 570mm
Weight: 12.1kg
Today's Best Deals
Reasons to buy
+
Incredible value
+
Robust design
+
High-quality tool head
Reasons to avoid
-
Not a true CORE XY printer
-
Large footprint
-
No enclosure for enhanced materials (Optional extra)
Having a predecessor with a decent reputation instantly puts pressure on the new model to perform. From the small amount of initial construction needed to build the printer to the outstanding bed leveling technology, the Ender-5 S1 proves to be a decent upgrade and on a completely different level of quality to the original Ender-5.
The cubed design might not be a true CORE XY printer, but the robust frame and tool head design's and precision enables a print quality that pits this printer against models that are at least twice the price.
The design is refined, the tool head completely overhauled, and with upgrade options such as an enclosure and laser head, there is plenty of scopes to expand your creativity. This is a printer designed for both enthusiasts and small business users.
Read our full Creality-5 S1 review.
(Image credit: TRILAB)4. TRILAB DeltiQ 2
Distinctive delta design for professional 3D printing
Specifications
Print technology: Fused Deposition Modeling (FMD)
Build area: 25 x 25 x 30cm
Minimum layer resolution: 50 microns
Maximum layer resolution: Variable
Dimensions: 41 x 50 x 81cm
Weight: 10kg
Today's Best Deals
Reasons to buy
+
Elegant design
+
Easy expansion
Reasons to avoid
-
Not suitable for all materials
-
Fully open design
This elegant delta design should get your attention if you’re looking for a professional 3D printer for fairly large and complex projects. It uses FDM technology to build 3D models from rolls of filament. Still, instead of the more common cartesian printers, the TRILAB DeltiQ 2 has a fixed round build plate with the extruder suspended between three arms that move the print head along three axes. It gives this model a fairly small footprint, while its high tower design ensures it can print some quite large pieces.
And unlike most 3D printers, it has two extruder options, one for standard PLA and PETG and the other for flexibles. It just requires a little retooling to swap between them. The TRILAB DeltiQ 2 uses some of the best components available in its construction, and the interface is a smartphone running a dedicated app. This handsome, high-end workshop printer would sit well in any laboratory, studio or classroom.
Read our full TRILAB DeltiQ 2 review.
Original PRUSA SL1 (Image credit: PRUSA)5. Original PRUSA SL1S SPEED
The best MSLA printer just got better
Specifications
Print technology: Stereolithography
Build area: 320 x 450 x 500mm
Minimum layer resolution: 25 microns
Maximum layer resolution: 100 microns
Dimensions: 400 x 237 x 225 mm
Weight: 4. 5kg
Today's Best Deals
Reasons to buy
+
Rapid printing
+
Great build quality
Reasons to avoid
-
High maintenance
-
Limited build volume
Prusa Research revolutionized the FDM 3D printer market, and this model looks set to do the same for SLA printers. While this printer uses stereolithography technology, it's a slight variant known as MSLA.
This uses a monochrome LCD and UV LED to expose the resin, which is cheaper than precision lasers but just as accurate. The SL1S SPEED replaces the outgoing SL1, and as you might have guessed from that model name, it’s faster – around ten times faster and with a vastly improved print quality.
The SL1S's design hasn't physically changed a great deal over the SL1. It features the same touchscreen LCD on the front, which is again good and responsive.
The speedy new model looks set to lead the SLA market with support from the excellent PrusaSlicer software and a huge open-source community.
Read our full Original Prusa SL1S 3D printer review.
Anycubic Vyper (Image credit: Anycubic)6. AnyCubic Vyper
The best beginner friendly FDM 3D printer
Specifications
Print technology: Fused Deposition Modeling
Build area: 245 x 245 x 260mm
Dimensions: 508 × 457 × 516mm
Weight: 10kg
Colour
Black
Condition
New
Today's Best Deals
Reasons to buy
+
Built-in accessories drawer
+
Reliable automatic bed-leveling
+
Great value for the features you get
Reasons to avoid
-
Excessive initial stringing
-
Questionable build quality in places
-
Cura profile needs fine-tuning
If the world of 3D printing ever seemed too intimidating for you, look no further than the AnyCubic Vyper. While perfect for beginners with its auto-leveling feature and minimal assembly, seasoned printing hobbyists will also appreciate what it can offer, albeit with a few adjustments.
As the 'automatic leveling' might imply, the AnyCubic Vyper removes the need to align your build plate manually should you want to move the machine to a different location. It's fast and accurate, saving time when setting up your first print, which makes setting up and getting started a breeze.
The touchscreen control panel is satisfyingly fast and easy to use, but we found that the estimated print completion time was consistently incorrect. Once the printer is properly optimized, you'll enjoy impressive print quality.
Read our full AnyCubic Vyper review.
Raise3D E2 (Image credit: Raise3D)7. Raise3D E2
The best workhorse 3D printer
Specifications
Print technology: Fused Deposition Modeling
Build area: 330 x 240 x 240mm
Minimum layer resolution: 20 microns
Maximum layer resolution: 250 microns
Dimensions: 607 x 596 x 465mm
Weight: 35kg
Colour
Black
Condition
New
Today's Best Deals
Reasons to buy
+
High-resolution print capability
+
Innovative ouch screen interface
+
Dual Extruder system can work independently
Reasons to avoid
-
Huge and heavy, not ideal for home use
-
Careful placement of bed required
-
Needs manual assistance for filament loading
3D printing has come of age, and machines like the Raise3D E2 bring high-end FFF printing to the home, education, and business. This dual extrusion printer goes head-to-head with the RoboxPro and will fulfill most companies' design and development needs with slick business and network integration.
The printer display is vast and detailed, and you can swiftly access all the printer settings through the fast and responsive touchscreen interface. You can print directly from a USB key, wired connection, network, or Wi-Fi, making it ideal if several people are utilizing the printer. You will also find many step-by-step videos for many of the printer's features.
Home and educational users will benefit from a simple interface and near-faultless reliability. The only drawback of this machine is its size and weight.
Read the full Raise3D E review.
(Image credit: Anycubic)8. Anycubic Photon M3
Detailed 3D modelling for beginners
Specifications
Print technology: Stereolithography (SLA)
Build area: 18 x 18 x 18cm
Minimum layer resolution: 50 microns
Maximum layer resolution: 200 microns
Dimensions: 18 x 16. 4 x 10cm
Weight: 7kg
Colour
Yellow
Condition
New
Today's Best Deals
Reasons to buy
+
Good value
+
Detailed models
Reasons to avoid
-
Print size is small
-
Poorly placed USB port
The Anycubic Photon M3 is the ideal entry-level resin printer to introduce you to 3D printing. It’s relatively easy to set up and operate, and the box includes everything you need to get started except for the UV resin. This compact model will fit easily on your desk in a well-ventilated room, though the build volume is somewhat limited at 180 x 163.9 x 102.4mm or 7 x 6.5 x 4-inches.
This modest machine can turn out surprisingly detailed models for printing small plastic parts or artistic pieces. The interface is a 7.6-inch panel, and the software will help you print your project and slice it. If you want to make larger models, you should consider one of Anycubic’s larger 3D printers, but this is a great place to start for $299 (about £275 / AU$480).
Read our full Anycubic Photon M3 review.
Snapmaker 2.0 A350 (Image credit: Snapmaker)9. Snapmaker 2.0 A350
Best 3-in-1 3D printer
Specifications
Print technology: Fused Filament Fabrication, CNC, Laser
Build area: 350 x 350 x 350mm
Minimum layer resolution: 50 microns
Maximum layer resolution: 300 microns
Dimensions: 645 x 480 x 580mm
Weight: 29kg
Today's Best Deals
Reasons to buy
+
3D printer, CNC, and Laser cutter in one
+
Solid design and build quality
+
Easy to understand software
Reasons to avoid
-
Switching between uses takes time
-
Enclosure purchased separately
-
Very noisy when printing
A true 3-in-1 machine makes sense because 3D printers, CNC, and Laser cutters all use the same basic mechanics and technology. The original Snapmaker has a dedicated following, so it is no surprise that Snapmaker 2.0 builds on its predecessor's reputation and features.
The SnapMaker boasts excellent build quality and comes with clear assembly instructions. The assembly takes around 20 minutes. There's a 5-inch (720x1280px) touchscreen on the machine that can be used to select options, preview models, calibrate and open stored files. The touch screen is a powerful addition to the usability of the machine — it runs on Android OS and features a Quad-Core A7 CPU @1.1GHz.
The A350 is the largest of three models and proves proficient in all disciplines. Swapping between the three heads and beds does take time to reconfigure and calibrate, but for the price and features, it's worth it.
Read the full Snapmaker 2.0 A350 review.
- We've also featured the best printers and the best laptops for graphic design.
What is a 3D printer?
A 3D printer is a machine that creates three-dimensional objects using computer-created designs (like a digital 3D or CAD model).
These machines rely on an additive manufacturing process to build objects layer by layer.
How to choose the best 3D printers for you?
To select the best 3D printer, you'll need to consider what you're going to do with it. If you're going to be printing small objects, then a small-size printer is apt, but a large printer is naturally the best option for bigger creations.
For printing high-quality objects with fine details, you'll need a high resolution printer, but these prints will cost more and take more time to get ready.
Look out for the printer's interface and the overall ease of use, along with other aspects like the kind of software it uses, the type of filament, build platform, and pricing.
The best 3D printers: How we test
3D printers are tested using a collection of bespoke benchmarks that help show the strengths and weaknesses of each model that, after time, can be compared against other products. These will differ depending on printer type, but a filament printer will be tested for stringing, bridging, and speed, as well as additional commentary on detail, achieved, and noise levels.
This will be done fairly, with dues given to different materials and printer types, with resin printers being subject to smaller, more detailed models to replace the stringing test. Design, price, and performance will also be explored as sections within the reviews.
All our tests are conducted from the perspective of the printers target market where possible, so expect to see a lot of tabletop miniatures and figurines alongside the usual 'benches' (test models that are also dubbed as 'torture tests' to see where a printer needs to be better optimized for future prints).
Round up of today's best deals
Creality Ender-5 S1
$89.99
View
See all prices
Anycubic Vyper
$429. 99
View
See all prices
Raise3D E2
$3,499
View
See all prices
Anycubic Photon M3
$319.99
View
See all prices
powered by
Sign up to theTechRadar Pro newsletter to get all the top news, opinion, features and guidance your business needs to succeed!
Contact me with news and offers from other Future brandsReceive email from us on behalf of our trusted partners or sponsorsCollin is the B2B Hardware Editor for TechRadar Pro. He has been in journalism for years with experience in both small and large markets including Gearadical, DailyBeast, FutureNet and more.
3D printing for "dummies" or "what is a 3D printer?"
- 1 3D printing term
- 2 3D printing methods
- 2.1 Extrusion printing
- 2.2 Melting, sintering or gluing
- 2.3 Stereolithography
- 2.4 Lamination
- 3 Fused Deposition Printing (FDM)
- 3.1 Consumables
- 3.2 Extruder
- 3.3 Working platform
- 3.4 Positioners
- 3.5 Control
- 3.6 Varieties of FDM printers
- 4 Laser stereolithography (SLA)
- 4.1 Lasers and projectors
- 4.2 Cuvette and resin
- 4.3 Types of stereolithographic printers
3D printing term
The term 3D printing has several synonyms, one of which quite briefly and accurately characterizes the essence of the process - "additive manufacturing", that is, production by adding material. The term was not coined by chance, because this is the main difference between multiple 3D printing technologies and the usual methods of industrial production, which in turn received the name "subtractive technologies", that is, "subtractive". If during milling, grinding, cutting and other similar procedures, excess material is removed from the workpiece, then in the case of additive manufacturing, material is gradually added until a solid model is obtained.
Soon 3D printing will even be tested on the International Space Station
Strictly speaking, many traditional methods could be classified as "additive" in the broad sense of the word - for example, casting or riveting. However, it should be borne in mind that in these cases, either the consumption of materials is required for the manufacture of specific tools used in the production of specific parts (as in the case of casting), or the whole process is reduced to joining ready-made parts (welding, riveting, etc. ). In order for the technology to be classified as “3D printing”, the final product must be built from raw materials, not blanks, and the formation of objects must be arbitrary - that is, without the use of forms. The latter means that additive manufacturing requires a software component. Roughly speaking, additive manufacturing requires computer control so that the shape of final products can be determined by building digital models. It was this factor that delayed the widespread adoption of 3D printing until the moment when numerical control and 3D design became widely available and highly productive.
3D printing techniques
3D printing technologies are numerous, and there are even more names for them due to patent restrictions. However, you can try to divide technologies into main areas:
Extrusion printing
This includes methods such as deposition deposition (FDM) and multi-jet printing (MJM). This method is based on the extrusion (extrusion) of consumables with the sequential formation of the finished product. As a rule, consumables consist of thermoplastics or composite materials based on them.
Melting, sintering or bonding
This approach is based on bonding powdered material together. Formation is done in different ways. The simplest is gluing, as is the case with 3D inkjet printing (3DP). Such printers deposit thin layers of powder onto the build platform, which are then selectively bonded with a binder. Powders can be made up of virtually any material that can be ground to a powder—plastic, wood, metal.
This model of James Bond's Aston Martin was successfully printed on Voxeljet's SLS printer and blown up just as successfully during the filming of Skyfall instead of the expensive original
sintering (SLS and DMLS) and smelting (SLM), which allow you to create all-metal parts. As with 3D inkjet printing, these devices apply thin layers of powder, but the material is not glued together, but sintered or melted using a laser. Laser sintering (SLS) is used to work with both plastic and metal powders, although metal pellets usually have a more fusible shell, and after printing they are additionally sintered in special ovens. DMLS is a variant of SLS installations with more powerful lasers that allow sintering metal powders directly without additives. SLM printers provide not just sintering of particles, but their complete melting, which allows you to create monolithic models that do not suffer from the relative fragility caused by the porosity of the structure. As a rule, printers for working with metal powders are equipped with vacuum working chambers, or they replace air with inert gases. Such a complication of the design is caused by the need to work with metals and alloys subject to oxidation - for example, with titanium.
Stereolithography
How an SLA printer works
Stereolithography printers use special liquid materials called "photopolymer resins". The term "photopolymerization" refers to the ability of a material to harden when exposed to light. As a rule, such materials react to ultraviolet irradiation.
Resin is poured into a special container with a movable platform, which is installed in a position near the surface of the liquid. The layer of resin covering the platform corresponds to one layer of the digital model. Then a thin layer of resin is processed by a laser beam, hardening at the points of contact. At the end of illumination, the platform together with the finished layer is immersed to the thickness of the next layer, and illumination is performed again.
Lamination
Laminating (LOM) 3D printers workflow
Some 3D printers build models using sheet materials - paper, foil, plastic film.
Layers of material are glued on top of each other and cut to the contours of the digital model using a laser or a blade.
These machines are well suited for prototyping and can use very cheap consumables, including regular office paper. However, the complexity and noise of these printers, coupled with the limitations of the models they produce, limit their popularity.
Fused Deposition Modeling (FDM) and Laser Stereolithography (SLA) are the most popular 3D printing methods used in the home and office.
Let's take a closer look at these technologies.
Fused Deposition Printing (FDM)
FDM is perhaps the simplest and most affordable 3D construction method, which makes it very popular.
High demand for FDM printers is driving device and consumable prices down rapidly, along with technology advances towards ease of use and improved reliability.
Consumables
ABS filament spool and finished model
FDM printers are designed to print with thermoplastics, which are usually supplied as thin filaments wound on spools. The range of "clean" plastics is very wide. One of the most popular materials is polylactide or "PLA plastic". This material is made from corn or sugar cane, which makes it non-toxic and environmentally friendly, but makes it relatively short-lived. ABS plastic, on the other hand, is very durable and wear-resistant, although it is susceptible to direct sunlight and can release small amounts of harmful fumes when heated. Many plastic items that we use on a daily basis are made from this material: housings for household appliances, plumbing fixtures, plastic cards, toys, etc.
In addition to PLA and ABS, printing is possible with nylon, polycarbonate, polyethylene and many other thermoplastics that are widely used in modern industry. More exotic materials are also possible, such as polyvinyl alcohol, known as "PVA plastic". This material dissolves in water, which makes it very useful for printing complex geometric patterns. But more on that below.
Model made from Laywoo-D3. Changing the extrusion temperature allows you to achieve different shades and simulate annual rings
It is not necessary to print with homogeneous plastics. It is also possible to use composite materials imitating wood, metals, stone. Such materials use all the same thermoplastics, but with impurities of non-plastic materials.
So, Laywoo-D3 consists partly of natural wood dust, which allows you to print "wooden" products, including furniture.
The material called BronzeFill is filled with real bronze, and models made from it can be ground and polished, achieving a high similarity to products made from pure bronze.
One has only to remember that thermoplastics serve as a binding element in composite materials - they determine the thresholds of strength, thermal stability and other physical and chemical properties of finished models.
Extruder
Extruder - FDM print head. Strictly speaking, this is not entirely true, because the head consists of several parts, of which only the feed mechanism is directly "extruder". However, by tradition, the term "extruder" is commonly used as a synonym for the entire print assembly.
FDM extruder general design
The extruder is designed for melting and applying thermoplastic thread. The first component is the thread feed mechanism, which consists of rollers and gears driven by an electric motor. The mechanism feeds the thread into a special heated metal tube with a small diameter nozzle, called a "hot end" or simply a "nozzle". The same mechanism is used to remove the thread if a change of material is needed.
The hot end is used to heat and melt the thread fed by the puller. As a rule, nozzles are made from brass or aluminum, although more heat-resistant, but also more expensive materials can be used. For printing with the most popular plastics, a brass nozzle is quite enough. The “nozzle” itself is attached to the end of the tube with a threaded connection and can be replaced with a new one in case of wear or if a change in diameter is necessary. The nozzle diameter determines the thickness of the molten filament and, as a result, affects the print resolution. The heating of the hot end is controlled by a thermistor. Temperature control is very important, because when the material is overheated, pyrolysis can occur, that is, the decomposition of plastic, which contributes both to the loss of the properties of the material itself and to clogging of the nozzle.
PrintBox3D One FDM Printer Extruder
To prevent the filament from melting too early, the top of the hot end is cooled by heatsinks and fans. This point is of great importance, since thermoplastics that pass the glass transition temperature significantly expand in volume and increase the friction of the material with the walls of the hot end. If the length of such a section is too long, the pulling mechanism may not have enough strength to push the thread.
The number of extruders may vary depending on the purpose of the 3D printer. The simplest options use a single printhead. The dual extruder greatly expands the capabilities of the device, allowing you to print one model in two different colors, as well as using different materials. The last point is important when building complex models with overhanging structural elements: FDM printers cannot print “over the air”, since the applied layers require support. In the case of hinged elements, temporary support structures have to be printed, which are removed after printing is completed. The removal process is fraught with damage to the model itself and requires accuracy. In addition, if the model has a complex structure with internal cavities that are difficult to access, building conventional supports may not be practical due to the difficulty in removing excess material.
Finished model with PVA supports (white) before and after washing
In such cases, the same water-soluble polyvinyl alcohol (PVA) comes in handy. Using a dual extruder, you can build a model from waterproof thermoplastic using PVA to create supports.
After printing, PVA can be simply dissolved in water and a complex product of perfect quality can be obtained.
Some FDM printers can use three or even four extruders.
Working platform
Heated platform covered with removable glass work table
Models are built on a special platform, often equipped with heating elements. Preheating is required for a wide range of plastics, including the popular ABS, which are subject to a high degree of shrinkage when cooled. The rapid loss of volume by cold coats compared to freshly applied material can lead to model distortion or delamination. The heating of the platform makes it possible to significantly equalize the temperature gradient between the upper and lower layers.
Heating is not recommended for some materials. A typical example is PLA plastic, which requires a fairly long time to harden. Heating PLA can lead to deformation of the lower layers under the weight of the upper ones. When working with PLA, measures are usually taken not to heat up, but to cool the model. Such printers have characteristic open cases and additional fans blowing fresh layers of the model.
Calibration screw for work platform covered with blue masking tape
The platform needs to be calibrated before printing to ensure that the nozzle does not hit the applied layers and move too far causing air-to-air printing resulting in plastic vermicelli. The calibration process can be either manual or automatic. In manual mode, calibration is performed by positioning the nozzle at different points on the platform and adjusting the platform inclination using the support screws to achieve the optimal distance between the surface and the nozzle.
As a rule, platforms are equipped with an additional element - a removable table. This design simplifies the cleaning of the working surface and facilitates the removal of the finished model. Stages are made from various materials, including aluminum, acrylic, glass, etc. The choice of material for the manufacture of the stage depends on the presence of heating and consumables for which the printer is optimized.
For a better adhesion of the first layer of the model to the surface of the table, additional tools are often used, including polyimide film, glue and even hairspray! But the most popular tool is inexpensive, but effective masking tape. Some manufacturers make perforated tables that hold the model well but are difficult to clean. In general, the expediency of applying additional funds to the table depends on the consumable material and the material of the table itself.
Positioning mechanisms
Scheme of operation of positioning mechanisms
Of course, the print head must move relative to the working platform, and unlike conventional office printers, positioning must be carried out not in two, but in three planes, including height adjustment.
Positioning pattern may vary. The simplest and most common option involves mounting the print head on perpendicular guides driven by stepper motors and providing positioning along the X and Y axes.
Vertical positioning is carried out by moving the working platform.
On the other hand, it is possible to move the extruder in one plane and the platforms in two.
SeemeCNC ORION Delta Printer
One option that is gaining popularity is the delta coordinate system.
Such devices are called "delta robots" in the industry.
In delta printers, the print head is suspended on three manipulators, each of which moves along a vertical rail.
The synchronous symmetrical movement of the manipulators allows you to change the height of the extruder above the platform, and the asymmetric movement causes the head to move in the horizontal plane.
A variant of this system is the reverse delta design, where the extruder is fixed to the ceiling of the working chamber, and the platform moves on three support arms.
Delta printers have a cylindrical build area, and their design makes it easy to increase the height of the working area with minimal design changes by extending the rails.
In the end, everything depends on the decision of the designers, but the fundamental principle does not change.
Control
Typical Arduino-based controller with add-on modules
The operation of the FDM printer, including nozzle and platform temperature, filament feed rate, and stepper motors for positioning the extruder, is controlled by fairly simple electronic controllers. Most controllers are based on the Arduino platform, which has an open architecture.
The programming language used by the printers is called G-code (G-Code) and consists of a list of commands executed in turn by the 3D printer systems. G-code is compiled by programs called "slicers" - standard 3D printer software that combines some of the features of graphics editors with the ability to set print options through a graphical interface. The choice of slicer depends on the printer model. RepRap printers use open source slicers such as Skeinforge, Replicator G and Repetier-Host. Some companies make printers that require proprietary software.
Program code for printing is generated using slicers
As an example, we can mention Cube printers from 3D Systems. There are companies that offer proprietary software but allow third-party software, as is the case with the latest generation of MakerBot 3D printers.
Slicers are not intended for 3D design per se. This task is done with CAD editors and requires some 3D design skills. Although beginners should not despair: digital models of a wide variety of designs are offered on many sites, often even for free. Finally, some companies and individuals offer 3D design services for custom printing.
Finally, 3D printers can be used in conjunction with 3D scanners to automate the process of digitizing objects. Many of these devices are designed specifically to work with 3D printers. Notable examples include the 3D Systems Sense handheld scanner and the MakerBot Digitizer handheld desktop scanner.
MakerBot Replicator 5th Generation FDM Printer with built-in control module on the top of the frame
The user interface of a 3D printer can consist of a simple USB port for connecting to a personal computer. In such cases, the device is actually controlled by the slicer.
The disadvantage of this simplification is a rather high probability of printing failure when the computer freezes or slows down.
A more advanced option includes an internal memory or memory card interface to make the process standalone.
These models are equipped with control modules that allow you to adjust many print parameters (such as print speed or extrusion temperature). The module may include a small LCD display or even a mini-tablet.
Varieties of FDM printers
Professional Stratasys Fortus 360mc FDM printer that allows printing with nylon
FDM printers are very, very diverse, ranging from the simplest homemade RepRap printers to industrial installations capable of printing large-sized objects.
Stratasys, founded by Scott Crump, the inventor of FDM technology, is a leader in the production of industrial installations.
You can build the simplest FDM printers yourself. Such devices are called RepRap, where "Rep" indicates the possibility of "replication", that is, self-reproduction.
RepRap printers can be used to print custom built plastic parts.
Controller, rails, belts, motors and other components can be easily purchased separately.
Of course, assembling such a device on your own requires serious technical and even engineering skills.
Some manufacturers make it easy by selling DIY kits, but these kits still require a good understanding of the technology. RepRap Printers
And, despite their "homemade nature", RepRap printers are quite capable of producing models with quality at the level of expensive branded counterparts.
Ordinary users who do not want to delve into the intricacies of the process, but require only a convenient device for household use, can purchase a ready-made FDM printer.
Many companies are focusing on the development of the consumer market segment, offering 3D printers for sale that are ready to print “right out of the box” and do not require serious computer skills.
3D Systems Cube consumer 3D printer
The most famous example of a consumer 3D printer is the 3D Systems Cube.
While it doesn't boast a huge build area, ultra-fast print speeds, or superb build quality, it's easy to use, affordable, and safe: This printer has received the necessary certification to be used even by children.
Mankati FDM printer demonstration: http://youtu.be/51rypJIK4y0
Laser Stereolithography (SLA)
Stereolithographic 3D printers are widely used in dental prosthetics
Stereolithographic printers are the second most popular and widespread after FDM printers.
These units deliver exceptional print quality.
The resolution of some SLA printers is measured in a matter of microns - it is not surprising that these devices quickly won the love of jewelers and dentists.
The software side of laser stereolithography is almost identical to FDM printing, so we will not repeat ourselves and will only touch on the distinctive features of the technology.
Lasers and projectors
Projector illumination of a photopolymer model using Kudo3D Titan DLP printer as an example
The cost of stereolithography printers is rapidly declining due to growing competition due to high demand and the use of new technologies that reduce the cost of construction.
Although the technology is generically referred to as "laser" stereolithography, most recent developments use UV LED projectors for the most part.
Projectors are cheaper and more reliable than lasers, do not require the use of delicate mirrors to deflect the laser beam, and have higher performance. The latter is explained by the fact that the contour of the whole layer is illuminated as a whole, and not sequentially, point by point, as is the case with laser options. This variant of the technology is called projection stereolithography, "DLP-SLA" or simply "DLP". However, both options are currently common - both laser and projector versions.
Cuvette and resin
Photopolymer resin is poured into a cuvette
A photopolymer resin that looks like epoxy is used as consumables for stereolithography printers. Resins can have a variety of characteristics, but they all share one key feature for 3D printing applications: these materials harden when exposed to ultraviolet light. Hence, in fact, the name "photopolymer".
When polymerized, resins can have a wide variety of physical characteristics. Some resins are like rubber, others are hard plastics like ABS. You can choose different colors and degrees of transparency. The main disadvantage of resins and SLA printing in general is the cost of consumables, which significantly exceeds the cost of thermoplastics.
On the other hand, stereolithography printers are mainly used by jewelers and dentists who do not need to build large parts but appreciate the savings from fast and accurate prototyping. Thus, SLA printers and consumables pay for themselves very quickly.
Example of a model printed on a laser stereolithographic 3D printer
Resin is poured into a cuvette, which can be equipped with a lowering platform. In this case, the printer uses a leveling device to flatten the thin layer of resin covering the platform just prior to irradiation. As the model is being made, the platform, together with the finished layers, is “embedded” in the resin. Upon completion of printing, the model is removed from the cuvette, treated with a special solution to remove liquid resin residues and placed in an ultraviolet oven, where the final illumination of the model is performed.
Some SLA and DLP printers work in an "inverted" scheme: the model is not immersed in the consumable, but "pulled" out of it, while the laser or projector is placed under the cuvette, and not above it. This approach eliminates the need to level the surface after each exposure, but requires the use of a cuvette made of a material transparent to ultraviolet light, such as quartz glass.
The accuracy of stereolithographic printers is extremely high. For comparison, the standard for vertical resolution for FDM printers is considered to be 100 microns, and some variants of SLA printers allow you to apply layers as thin as 15 microns. But this is not the limit. The problem, rather, is not so much in the accuracy of lasers, but in the speed of the process: the higher the resolution, the lower the print speed. The use of digital projectors allows you to significantly speed up the process, because each layer is illuminated entirely. As a result, some DLP printer manufacturers claim to be able to print with a vertical resolution of one micron!
Video from CES 2013 showing Formlabs Form1 stereolithography 3D printer in action: http://youtu.be/IjaUasw64VE
Stereolithography Printer Options
Formlabs Form1 Desktop Stereolithography Printer
As with FDM printers, SLA printers come in a wide range in terms of size, features and cost. Professional installations can cost tens if not hundreds of thousands of dollars and weigh a couple of tons, but the rapid development of desktop SLA and DLP printers is gradually reducing the cost of equipment without compromising print quality.
Models such as the Titan 1 promise to make stereolithographic 3D printing affordable for small businesses and even home use at around $1,000. Formlabs' Form 1 is available now for a factory selling price of $3,299.
The developer of the DLP printer Peachy generally intends to overcome the lower price barrier of $100.
At the same time, the cost of photopolymer resins remains quite high, although the average price has fallen from $150 to $50 per liter over the past couple of years.
Of course, the growing demand for stereolithographic printers will stimulate the growth in the production of consumables, which will lead to further price reductions.
Go to the main page of the Encyclopedia of 3D printing
EBM Industrial Metal 3D Printers
Technology of additive 3D printing with metal powder by electron beam melting (EBM – Electron Beam Melting)
Industrial 3D printers for printing metals using electron beam melting (sintering) are designed for the production of ready-to-use metal products (parts). At the same time, the printed parts can have an arbitrary shape, internal cavities, various filling factors (porosity), arched design, parts in parts made in a bionic design to reduce weight and increase the strength of products.
In world practice, industrial EBM 3D printers are often used for the production of osteoimplants (artificial bone implants) according to the individual dimensions and geometry of the patient's bones, taken using computed tomography. And there are a number of good reasons for this. Titanium and stainless steel alloys are used to construct osteoimplants. Unlike SLM 3D printers, where the sintering energy is generated using a laser, electron beam printers can use metal powders of a coarser (larger) fraction, for example, 75-120 microns.
For use inside the human body, the surface roughness of the osteoimplant is not critical and can even provide better fusion with the rest of the body tissues and germination with mesh and arch structures of artificial bones. Larger fractions of metal powders have a lower cost, which reduces the cost of the production process.
Also, 3D printers that print metals using electron beam melting have a higher speed of building a product. The printing itself takes place at a high temperature in the chamber, including metal powder. This makes it possible to obtain finished products with a high degree of sintering (fusion) without the need for additional heat treatment in vacuum furnaces, as in printing using SLM technology.
In the products themselves, there are no residual thermal stresses that contribute to the formation of cracks and subsequent destruction during the loaded operation of the products.
What is the additive 3D technology of electron beam melting EBM?
A removable build platform is firmly attached to the piston of the elevator system of the 3D printer. A vacuum is created in the sealed chamber of the 3D printer, which is necessary for the free movement of electrons. By the way, the principle of operation of a cathode-beam printer strongly resembles the operation of the kinescopes of the first televisions.
The scattered electron beam heats up the removable platform and chamber. The moving carriage applies and levels the first layer of metal powder onto the platform. The scattered beam of electrons, if necessary, produces additional heating of the powder layer. Then the beam is focused to a point and at a high scanning speed, in accordance with the program, begins to fuse the metal powder. Electrons are emitted by a tungsten cathode heated to the glow temperature. They are accelerated by a high voltage of 60 kV applied to the anode, which is the build platform and the powder chamber.
The primary anode serves to improve the focusing of the electron beam. The focusing coil compresses the beam, while the scanning coil deviates it along the X and Y axes. Focused to a point with a diameter of 0.2 mm, an electron beam with a power of up to 3 kW easily fuses even an increased layer of metal powder. Scanning by a magnetic field of a beam of electrons flying at the speed of light is absolutely inertialess, in contrast to a scanning system with mirrors and lasers. It allows you to move the electron beam at a tremendous speed up to 10 km / s and fuse metal powder in a multi-beam way at 100 points simultaneously!
Which accordingly affects the increase in printer productivity, which is at least two to four times higher than the productivity of similar metal laser printers. It should be understood that the energy saturation of electron beam 3D printers of EBM technology is many times higher than the energy of existing models of laser 3D printers using SLM technology. Although inferior to them in the accuracy of the additive construction of products.
After the first layer of metal powder has been melted, the piston moves down by a construction step (about 0.2 mm), the carriage applies and levels the next layer of powder, and the next cycle of zone electron beam melting takes place.
To level the inaccuracy of the platform on which the product is printed, and to level the horizontal surface, at the beginning of the additive printing process, legs - stands are printed. The requirements for their strength and quality are low, so they are printed with a low degree of volume filling. It should be noted that when printing, a large amount of heat is released in the product, so heating with a scanning beam is done only when necessary. In general, the preheating temperature of the powder surface can vary in the range of 500 - 1000°C depending on the material of the powder.
At the end of the production of the finished product, the piston moves up, with the help of a special industrial vacuum cleaner and brush, unused metal powder is collected.
Attention! It is possible to open the vacuum chamber and let oxygenated air into it only after the chamber has cooled down. Metal powders are extremely flammable and ignite instantly in air, especially when heated to high temperatures.
Attention! Work on cleaning unused powder is carried out in a respirator to prevent damage to the respiratory organs by fine metal powder.
After the chamber has cooled down and the unused powder is completely removed, the build platform with the finished product welded to it is unscrewed from the piston. Then, using a tungsten string on an electroerosive machine, the part is cut off from the platform. It is further machined to remove the remnants of the legs. If necessary, sandblasting is performed to reduce the surface roughness of the product.
Additional heat treatment of parts in most cases is not required. The product is ready for use immediately after printing. And this also affects the cost reduction of additive metal printing on electron beam 3D printers. It should be noted that in the cost of additive 3D printing with metal powder using SLM laser technology, the depreciation of a 3D printer is up to 70% of the cost of the finished product. And the contribution to the cost of a rather expensive, at first glance, metal powder is in second or third place.
Electron beam 3D printers, having higher productivity, make a much smaller contribution from printer depreciation to the cost of the finished product and, accordingly, reduce its cost.
EBM200 industrial cathode beam 3D metal printer technical parameters
3D printer settings | Meaning |
Maximum build size | 200x200x240mm |
Product construction accuracy | (Standard - Ti6Al4V) ± 0.2 mm |
Maximum electron beam power | 3 kW |
Accelerating anode voltage (on powder) | 60 kV |
Accelerating anode current | 0-50mA |
Hot cathode type | Tungsten filament |
Minimum Beam Spot Diameter | 0. |
Maximum Beam Scanning Speed | > 10 km/s |
Multipath melting | Up to 100 points |
Ultimate vacuum | <10 -2 Pa |
Helium partial pressure | 0.05-1.0Pa |
Powder heating | Scattered Beam Scanning |
Powder surface temperature | 500-1000℃ |
3D printer cooling system | Chiller using distilled water |
Monitoring the build process | Through the glass of the vacuum chamber |
CAD Interface | STL file format |
Software | Meta Build v1. |
Printer size | 2100x1000x2300 mm |
Printer weight | 2000 kg |
Source of power | 3 phase, 380 V, 36 A, 8 kW |
Catalog
Download >>> View >>>
3D printer kit
- Industrial 3D printer of EBM technology.
- Chiller, for the 3D printer cooling system with distilled water.
- Vacuum drying chamber for metal powder.
- Industrial vacuum cleaner.
Optional:
- Pneumohydraulic machine (sandblaster).
- Machine for electroerosive cutting.
- Air conditioner and dehumidifier.
Room requirements for metal additive 3D printing by electron beam method:
- Maintaining a stable temperature and humidity regime.
- Maintaining a stable temperature and humidity regime.
- Temperature 20-26 degrees.
- Humidity less than 40% non-condensing.
- To do this, the room for 3D metal printing should be equipped with an air conditioner and a dehumidifier.
Types of metal powders for additive 3D printing by electron beam method
- Titanium and titanium-based alloys.
- Aluminum alloys.
- Heat resistant steel alloys.
- Cobalt and chromium alloys.
- Stainless steel 316L.
- Copper alloys and many others.
3D Metal 3D Printer Applications:
- Aerospace,
- medical,
- military,
- industrial area.
Benefits of Electron Beam Additive 3D Printing (EBM):
- High performance EBM 3D printers compared to SLM technology.
- Low cost of products.
- Uses less expensive coarser grade metal powder.
- Possibility of recycling of metal powder after its screening and vacuum drying.
- The electron beam is controlled by magnetic fields.
- Expensive optical mirrors and germanium or diamond lenses are missing.
- Inertialess electron beam control gives the highest scanning speed.
- Beam scattering allows heating metal powder without the use of additional heaters and obtaining a high density of products.
- It is successfully used for the production of orthopedic bone implants (osteoimplants) made of titanium, made porous and arched, promoting osseointegration - fusion of bone tissues with an implant (implant).
- Allows you to print products from two different materials with a gradual gradient of composition change along the Z axis.
- Allows you to create heat-resistant nozzles and blades for gas turbines, including jet engines. In addition, it is used to create load-bearing titanium elements of an aircraft wing.
- It is used to create elements of rocket engines: combustion chambers and nozzles with resistance to temperatures above 3000°C. Where high pressure and temperature require the use of refractory and durable materials such as titanium.
- Unlimited by the geometric complexity of the manufactured parts without the need for subsequent assembly or welding.
- Ability to print internal cavities and parts in parts.
Drawbacks of electron beam additive 3D technology (EBM):
- Relatively small build chamber.
- Increased roughness, printed products.
- During the operation of a 3D printer, X-ray bremsstrahlung occurs, from which it is necessary to protect both equipment and maintenance personnel.
- Respiratory protection of service personnel from fine metal powder is required.
- Tendency to ignite metal powders of titanium and steel.
China is the world's first economy and the world's largest manufacturer of 3D printers.
