Multi material 3d printer metal
We made L-PBF dual-metal! - Aerosint
Share This Post
Share on facebook
Share on linkedin
Share on twitter
Share on email
This part was printed on the Aconity Midi + printer. This printer was designed by our partner Aconity 3D so our multi-material powder deposition technology could be integrated. The Aerosint recoater is today available as an extra option on the price list of the Aconity Midi+ printer.
We feel this is a major breakthrough for 3D printing and are happy to have accomplished this with Aconity 3D.. Multi-metal printing gives designers and engineers the ultimate degree of freedom to make better parts. We are very proud of this accomplishment. No other technology is today capable of producing such dual-metal parts. Multi-metal Laser Powder Bed Fusion creates a range of new use cases and applications that we feel excited to explore together with our partners in the future.
Some details about the part and process:
- Printed on Aconity3D GmbH Midi + L-PBF printer in which Aerosint’s dual-metal recoater was integrated
- Dimensions of the part: 6,9 mm height and diameter of 55 mm
- The part consists of 174 layers of 40 microns each
- Materials used: 316 L and CuCrZr
- CuCrZr channel diameter 1,7 mm
- Build time: approximately 5:40 hours
Subscribe To Our Mailing List
Get updates On Our Most recent news
PrevPrevious
NextNext
More To Explore
Media
Aerosint at Hannover Messe
After four days at the tradeshow, industry, politics and research are all sending a clear signal from Hannover : Pandemics and wars must not and will not slow down the process of industrial transformation !
June 15, 2022
Content
Direct pressure-assisted sintering of complex powder structures
At Aerosint we’ve developed the Selective Powder Deposition (SPD), a technology that allows the user to make 2D patterns with multiple powders in any shape or form they desire. Our goal is to empower you with this technology to make materials and parts like none you’ve seen before. One way to achieve this is via direct pressure assisted sintering on multi-material powder constructs.
May 13, 2022
Multi material 3d printing by Aerosint's selective powder deposition
You’ve probably read more than a few tech digest headlines claiming that “this new 3D printer is going to change the world!” It’s a sentiment often parroted by those who are adjacent or completely outside the industry. I think those of us in the industry know well the capabilities and limitations of our own technologies, and as much as we each want to claim we are going to change the world, we know change is slow and incremental.
Still, from our humble perspective at Aerosint it seems that many in the industry aren’t thinking fundamentally about how to make additive manufacturing truly revolutionary. What is world-changing about being able to make a complex plastic part that can’t be injection molded? Will it really have greater functionality than something simpler to manufacture? Is it really going to be useful for more than just prototyping or for art? For 3D printing to transform manufacturing in every industry sector, it needs to be able to process multiple materials efficiently and with high speed and high productivity. In this perspective, I’ll explain why multi-material 3D printing is valuable and why we at Aerosint think that the most practical way to get there is through selective deposition of powdered materials.
Isn’t single material 3D printing already useful?
The answer, for the moment, is “it depends.” There are some clearly interesting applications for 3D printed metal parts for strong, light, topology-optimized parts for aircraft that can be made on demand rather than stocked. The oil and gas industry is interested in being able to replace old and worn custom-made components from suppliers that no longer exist with new parts, fabricated on demand in decentralized locations. There is also clear interest in printing high performance polymer parts for high strength, temperature resistant parts for satellites, high-end and custom automotive applications, and for customized biomedical implants and medical devices.
Still, these applications are fairly niche and current AM processes are too slow and expensive to drive adoption of AM as a useful production tool in all industries. We believe the only way for additive manufacturing to become more productive, cheaper, and more capable is by using inexpensive, minimally processed materials and combining multiple materials in single parts. The AM techniques currently capable of processing multiple materials are excellent for prototyping but aren’t practical or cheap enough for scaled manufacturing. Multi-powder deposition in a powder bed fusion process could circumvent the costs and limitations of current multi-material AM methods and form the basis for scalable, economical production of multi-material parts.
Why is multi-material 3d printing important?
The ultimate goal of AM should be to make manufacturing overall much simpler, faster, and cheaper. It will become invaluable to industry only if the complex parts produced with AM methods can functionally replace whole assemblies of machined or molded parts. It’s possible that some assemblies could be replaced by a complex part of one material, but likely many more assemblies will need to contain multiple materials to function as intended. Looking around at the objects near you at your desk, you will notice that even the simplest of functional devices are rarely made from a single material.
The fact is, the design of functional devices requires that material properties be spatially varied to accomplish the intended function. Take for example the steel hinge and hardware in your aluminium desk lamp, or the rubber seal and plastic lid on your stainless steel insulated travel mug. To be clear, I’m not arguing that AM methods should be used to produce simple objects like lamps and travel mugs. 3D printing will likely always be reserved for creating products that require far more design effort and advanced functionality. Indeed, it is in these high value applications where multi-material processing is most needed.
Functionally-graded materials: the ultimate composites
Some of the most interesting and useful materials are actually made from two or more materials combined into one. These composite materials such as fiber-reinforced polymers have long been recognized as advantageous in making strong, light structures. The goal of composites is to combine the best mechanical properties of two or more materials into a single material with mechanical properties that surpass any of the constituent materials alone. In composites, the whole is greater than the sum of the parts.
The “holy grail” of composite materials are functionally graded materials (FGMs). Unlike traditional composites, in which a reinforcing material is distributed throughout a bulk matrix material, FGMs are composites in which two materials are joined with a graded interface to avoid a distinct boundary between the two bulk materials. The purpose of creating this gradation is to distribute over a larger volume the thermal and mechanical stresses that would otherwise be concentrated at a distinct material boundary and cause part cracking or breakage.
An FGM combines the best thermal, mechanical, and/or chemical properties (top) of two materials (in this case, steel and copper) into a single part with a graded interface that distributes stresses within a greater volume (below). The goal is to avoid part failure that would likely occur as a result of stress concentration at a material boundary (middle). Key: k = thermal conductivity, ???? = stress, ???? = strain, ???? = coefficient of thermal expansion, T = temperature, V = volume
Their resistance to failure makes FGMs most useful in extreme environments with extraordinarily high thermal, mechanical, and/or chemical stresses where a single-material part would inevitably fail. In an FGM the mechanical, thermal, or chemical advantages of each material effectively cancel out the disadvantages of the other. Note that not only the material composition can be graded; indeed, there are also very compelling reasons for grading the microstructure or porosity of a compositionally homogeneous part, and often the inspiration for these materials has come from examples of FGMs observed in nature. For the sake of brevity, however, I’ll limit my examples and discussion to FGMs with material composition gradients.
Examples of compositional FGMs
One “classical” example of an FGM is a graded metal-to-ceramic plate. Ceramic alone is hard, chemically resistant, and very thermally resistant but also rather brittle and with low impact toughness. Metal alone is strong and has high toughness, but its mechanical performance suffers when heated and it is easily corroded by strong acids and bases. A metal-to-ceramic FGM is capable of withstanding blazing temperatures and harsh chemical environments at the ceramic face while maintaining overall strength and resistance to brittle fracture thanks to the metal reinforcement.
Metal-ceramic FGMs were first described by researchers from Japan’s National Aeropace Laboratories of Science and Technology, in an effort to create effective, durable thermal barriers for reusable space “plane” vehicles. The researchers found that a plate composed of compositionally graded layers of nickel superalloy and a stabilized zirconium oxide on a nickel superalloy base could withstand heat gradients of over 1000 °C without cracking. Under the same conditions, a 100% nickel superalloy coated with 100% zirconium oxide and a chromium alloy as a relaxation layer in between experienced cracking due to thermal fatigue. These results served as early validation of the theorized benefits of FGMs and sparked massive interest in developing other FGMs.
Metal-ceramic FGMs can withstand high heat gradients without cracking or plastic deformation (graphic adapted from: A. Gupta, M. Talha, Progress in Aerospace Sciences. 79, 1–14 (2015).
Metal-metal FGMs have also been successfully created and shown to be useful. Steel-copper FGMs are of particular interest for combining the low cost and high strength of steel with the high thermal and electrical conductivity of copper. One recent example of a non-FGM multi-metal application highlights this interest convincingly. Researchers fabricated an injection molding tool with a steel molding surface and bulk copper body, joined with a proprietary buffer layer material. With the increased thermal conductivity of the tool due to the bulk copper, the mold cooling time was reduced by 10 seconds, thereby reducing the overall mold cycle time by 26%. The company estimated that increased productivity of the tool could save them $60,000 per mold per year. It’s possible that making a similar tool using a true FGM rather than a buffer layer could further reduce the molding cycle time of a tool.
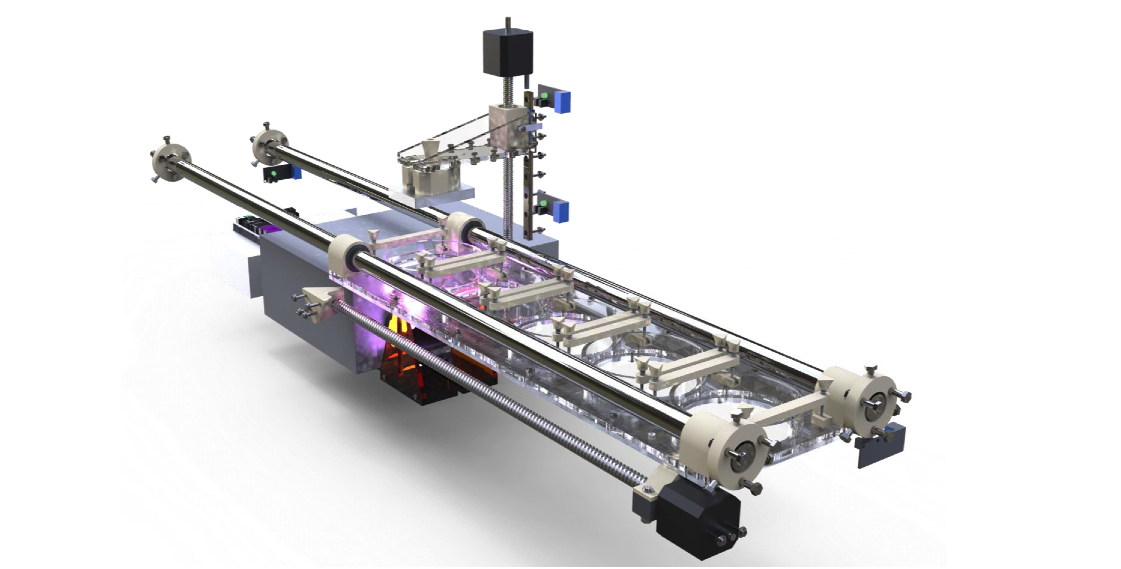
Polymer-polymer FGMs have interesting applications as well. Polymers have widely varying properties like elasticity, translucency, hardness, and toughness. With an FGM approach, rigid polymers could be joined to flexible polymers for ‘built-in’ bushings, rigid arms and soft joints for robotics, or other applications where a single part must replace an entire assembly with extraordinary differences in elasticity (as in the Michelin Vision concept tire shown above). Wear resistant polymers could be joined to tough polymers for non-metallic bearings or motion components, and strong, opaque crystalline polymers could be joined with transparent amorphous polymers to create jointless viewing holes or windows in parts. These are just a few applications we envision.
Polymer-polymer FGMs could simplify the construction of flexible joints connecting rigid elements for soft robotics (left), combine supple viscoelastic materials with stiff engineering polymers for applications like airless tires (top right), and bring furniture design to the next level (bottom right).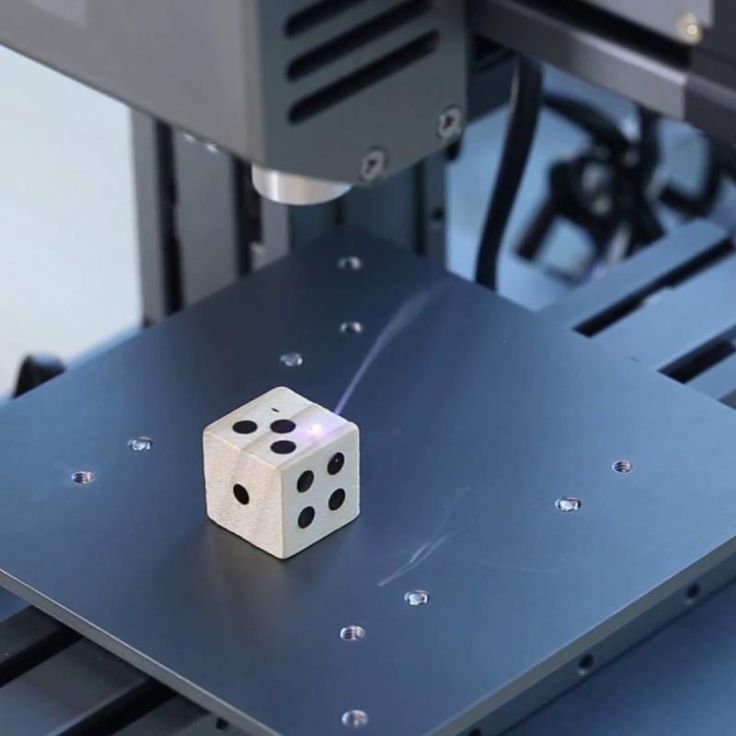
How multi-powder deposition will enable scalable, economical printing of FGMs
Most of the methods used to create FGMs that are described in the research literature are only capable of creating 1D gradients, which are useful only in a limited number of applications like thermal barrier tiles. To create multi-material parts and FGMs with complete 3D freedom, we need voxel-level spatial control over material placement. Several current AM techniques on the market are capable of this degree of compositional control, but they are primarily geared toward prototyping or one-off part fabrication.
Fused deposition modeling (FDM) systems with mixing extruders (e.g. ZMorph) and material jetting systems (e.g. Stratasys Connex) are capable of producing polymer-polymer FGMs. Still, neither type of of system is able to produce series of parts at a manufacturing scale or speed, and both are quite limited in terms of materials range since they can only directly process polymers. In particular for the material jetting systems, the UV curable resins used are so prohibitively expensive they are impractical for anything but prototyping or creating one-of-a-kind custom pieces.
Direct metal deposition (DMD) is an AM technique in which fine metal powders are sprayed in a jet of air into a melt pool created by a high power laser. With this technique it is possible to make certain metal-metal and metal-ceramic FGMs in 3D with nearly continuous gradients. Unfortunately, the process is relatively slow, being point-by-point and part-at-once. The cost of the machine itself is very high and costs due to large amounts of material waste (upwards of 70%) are very high.
Several current AM techniques such as FDM (top left), material jetting (top right), and DMD (bottom) can produce FGMs, but all suffer from material, cost, and productivity limitations.
We believe multi-powder deposition is the key to scalable and economical fabrication of advanced multi-material parts. Powder bed fusion processes, like selective laser sintering (SLS) or selective laser melting (SLM), are some of the fastest AM methods and are capable of printing small batches of the same or different parts, but they currently are only capable of processing a single material. A multi-powder deposition system integrated into an SLS or SLM system would enable true voxel-level control over part material composition, thus enabling FGM-based part production and more in general, multi material 3D printing.
As we’ve written in the past, we were not the first to recognize the value of multi-powder deposition as a basis for multi material 3D printing. Several researchers have previously developed systems to produce detailed powder images based on acoustically-induced powder flow through a pipette. With a two-powder system and mixing hopper, this pipette system can even produce gradients in powder composition. Even so, the method is inherently point-by-point and must be successfully parallelized to be a practical multi-material powder recoater system in an SLS/SLM process to achieve multi-material 3D printing.
Aerosint’s technology is a line-by-line powder deposition process in which powder voxels are selectively transferred from a rotating drum to the build surface. Theoretically, as many materials as the number of drums can be patterned. So far we have demonstrated two-powder deposition. Unlike other AM technologies, the patterning process does not rely on specific chemical properties of the material; the powder can be polymer, metal, or ceramic, as long as the powder flowability and particle size distribution are compatible with the process. While we haven’t yet achieved the same minimum feature size as the pipette based systems, our process may easily be 10–100x faster than a single-pipette system. We hope to exceed the powder recoater speeds currently used in SLS to surpass the current speed and productivity of SLS.
Aerosint’s technology selectively deposits multiple powder materials on a machine build surface in a line-by-line manner. We have successfully co-patterned alumina and titanium (top right), 316L stainless steel and copper (bottom left), and TPU and PA12 (white and black, respectively, bottom right).
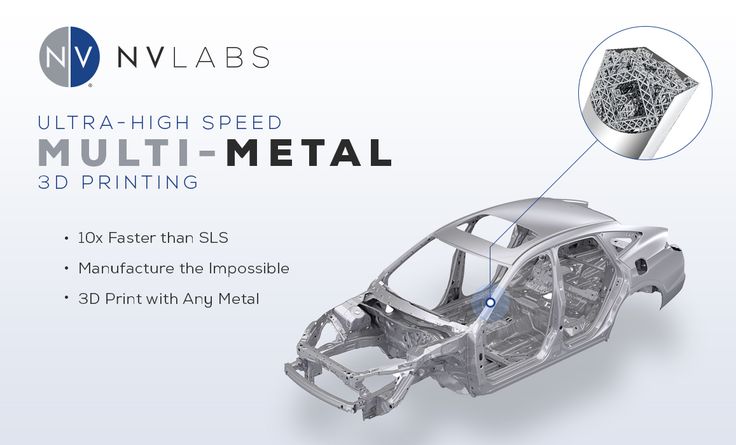
The most fundamental challenge in our process is bi-material consolidation or sintering. There are clear physical limitations in co-sintering two materials with vastly different melting or sintering temperatures. Even so, many researchers have demonstrated successful metal-metal and metal-ceramic co-sintering through prudent selection of materials with compatible properties. The combinations aren’t limitless, but we think they are plentiful enough to create a range of useful FGMs. We are in the process of launching partnerships with research institutions and academics with extensive experience in the domain of material co-sintering and metal and ceramic 3D printing.
Successful processing of multiple materials in AM will drive manufacturing toward greater efficiency only if the AM method itself is efficient. A process combining multi-powder deposition with bi-material co-sintering represents one of the best methods for enabling material-efficient, fast, and productive multi-material 3D printing. The mastery of this process will open up a world of advanced devices made more robust and efficient than ever.
3D metal printing! - new technology developed
Feb292016
Metal 3D printing!
Plastic is a very flexible and convenient composite for 3D printing, but it is not enough for the full use of technology in production. Most functional parts and components require a stronger material, and metal 3D printers have long been used in various industries. This technology, like 3D printing in general, continues to improve, and many companies are developing and improving available printing methods.
Metal 3D printing!
One such company is NVBOTS, a company specializing in the invention and sale of 3D printers. Last month, the organization announced the launch of the NVLABS project, focused on developing new metal 3D printing technology. It will allow the use of several materials simultaneously at much higher speeds than laser sintering (SLS) technology can offer. And some time ago, the company announced the successful invention of multi-metal 3D printing technology, developed by the enterprise for commercial use. There are no analogues of this technique yet, and it will be the first technology in the world that allows printing with several metals at the same time.
Metal 3D printing!
According to the development team, their new printing technology will work with virtually any metal in the future and will allow the use of multiple materials throughout the manufacturing process. The speed of producing finished parts will be up to 10 times faster than in SLS technology. This system will completely eliminate the need for traditional production methods. This will reduce manufacturing costs due to faster creation of parts and requires a minimum number of maintenance personnel. To date, the list of metals available for printing consists of 21 items and continues to expand rapidly to include the most common materials.
Metal 3D printing!
New NVBOTS technology could have an incredible impact on industry change. Since the system allows the use of multiple materials, large parts can be made in one piece, rather than as two separate elements that require subsequent connection. Taking car manufacturing as an example, the entire body of a vehicle can be assembled from different metals at the same time, depending on the design needs. That is, a process that usually takes several days or even weeks can be completed much faster with less production costs.
Metal 3D printing!
The new technology is expected to become a high-speed alternative to SLS printing and have a major impact on the medical, automotive and aerospace industries. It will also allow engineers to speed up the prototype testing phase and give them greater freedom in the design and 3D modeling of products. Thanks to it, a lot of new opportunities will open up, which traditional methods of production significantly limit.
Back to main page
The CeraFab Multi 2M30 3D printer is interesting in that it has the ability to 3D print with two photopolymer materials simultaneously. This is achieved through the use of two containers on a movable platform. When changing the material, automatic cleaning of residues is provided to avoid mixing. As a result, stereolithographic printing of products with areas of different density or transparency, the combination of electrically conductive and insulating materials, ceramics and metals, as well as the integration of materials with magnetic properties becomes possible. Combination is possible both from layer to layer and within one layer.
The resolution of the mask with LED illumination is 1920x1080 with a pixel size of 40 microns, the thickness of the layers varies within 10-100 microns. The size of the construction area reaches 76x43x170 mm.
One example of the application of the new system is the 3D printing of a mandibular implant demonstrator with a zirconia ceramic shell filled with a bioresorbable material ( in the illustration above ). Such a design should contribute to the restoration of bone tissues with the gradual replacement of the implant filling and the final complete osseointegration of the hard shell.
Additional information is available on the manufacturer's website at this link.
stereolithography Lithoz CeraFab Multi 2M30
Follow author
Follow
Don't want
5
Article comments
More interesting articles
5
Subscribe to the author
Subscribe
Don't want
Institute of Laser and Welding Technologies (ILIST) of St. Petersburg State Marine Tech...
Read more
5
Subscribe to the author
Subscribe
Don't want
Scientists from the Perm National Research Polytechnic University have designed an exp.