Motley fool 3d printers
5 3D Printing Stocks to Consider in 2022
An in-depth look at the leading 3D printing stocks in the U.S stock market this year. Here’s what you need to know.
By Nicholas Rossolillo – Updated Jul 11, 2022 at 2:42PM
Back in the early 2010s, stocks were booming for 3D printing -- also known as additive manufacturing, a computer-controlled process in which three-dimensional objects are made. But the boom was followed by a bust as many pure-play 3D printing companies didn't immediately deliver on lofty expectations.
Rumors of the manufacturing technology's demise are clearly premature. These days, 3D printing is a high-growth niche that is steadily reshaping the manufacturing and industrial sectors. Some estimates point to a doubling in annual revenue from additive manufacturing between 2022 and 2026. Even growth investor Cathie Wood has launched a fund focused on manufacturing tech, The 3D Printing ETF (NYSEMKT:PRNT), via her company ARK Invest.
Here's what you need to know about 3D printing and additive manufacturing stocks for 2022:
Image source: Getty Images.
Investing in 3D printing stocks
The manufacturing of products in all corners of the economy is being revolutionized by 3D printing, from healthcare equipment to metal fabrication to housing construction. It's invading so many sectors that tech giants such as Microsoft (NASDAQ:MSFT), Autodesk (NASDAQ:ADSK), and HP (NYSE:HPQ) have launched products aimed at 3D printing and additive manufacturing. Other engineering and software outfits such as Dassault Systemes (OTC:DASTY), ANSYS (NASDAQ:ANSS), and Trimble (NASDAQ:TRMB) have also gotten involved in 3D printing technology.
Here are five key players to consider for 2022 that are a more focused bet on 3D printing:
Company | Market Cap | Description |
---|---|---|
Desktop Metal (NYSE:DM) | $1.3 billion | Recent IPO that focuses on metal fabrication technology. |
Stratasys (NASDAQ:SSYS) | $1.5 billion | One of the original 3D printing pioneers, with a wide array of printers and supporting design software. |
Xometry (NASDAQ:XMTR) | $1.9 billion | A manufacturing marketplace, including access to on-demand 3D printing services. |
3D Systems (NYSE:DDD) | $1.9 billion | Another original 3D printing pioneer and the largest pure-play stock on 3D printing technology. |
PTC (NASDAQ:PTC) | $11.7 billion | A manufacturing technology provider with a suite of software and related services for industrial businesses. |
1.
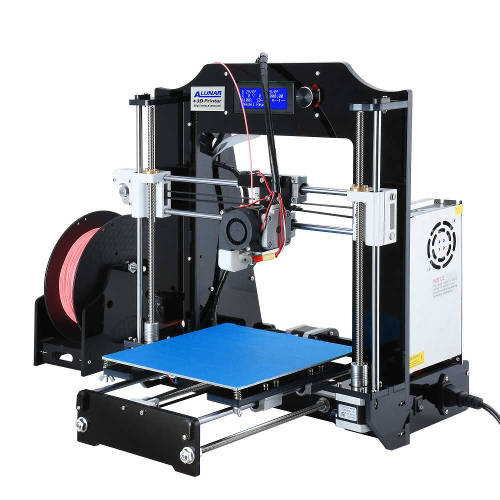
This company is a recent entry into the 3D printing space after going public via a SPAC at the end of 2020. The stock has been a terrible market underperformer since then, losing three-quarters of its value as of spring 2022. However, Desktop Metal could still be a promising investment for the long term.
As its name implies, Desktop Metal develops 3D printing hardware and accompanying design software for metal and carbon fiber parts. The company's smaller systems can handle prototyping and one-off parts, and larger printers are production grade-designed for manufacturing facilities. Desktop Metal serves companies operating in automotive, consumer goods, and heavy industrial equipment businesses.
Despite a tenuous start as a public company, Desktop Metal was actually increasing revenue at a torrid triple-digit pace in 2021. Gross profit margins are thin, and the company generated a steep net loss, but that should improve over time as the business scales its operation. Desktop Metal also has several hundred million dollars in cash and investments to fund its expansion. It used some of these funds to acquire additive manufacturing peer ExOne at the end of 2021.
2. Stratasys
Stratasys was part of the early 2010s 3D printing stock boom and bust, but its business has endured. Sales took a dip early in the COVID-19 pandemic but are rebounding as the Israel-based company picks up new manufacturing contracts.
Stratasys serves a diverse set of customers, including aerospace and automotive parts manufacturers, medical and dental companies, and makers of basic consumer products. In addition to a wide array of 3D printer models, Stratasys develops software to help users accelerate the time between design and final printing.
It isn't the highest-growth name on this list, but Stratasys is profitable (on a free cash flow basis) and has more than $500 million in cash and investments on its balance sheet, as well as no debt. Management thinks its payoff from years of research and development into additive manufacturing will accelerate in 2022.
3. Xometry
This is another newcomer to public markets. Xometry completed its initial public offering (IPO) over the summer of 2021, raising almost $350 million in cash in the process. As is often the case with new IPOs, the stock has underperformed since then. It has lost over half of its value from the time it started trading on public markets, but the business itself is rapidly growing.
Xometry is a marketplace for on-demand manufacturing of prototyping and mass production. It has a network of more than 5,000 suppliers that companies can call on to meet their fabrication needs. Among the suppliers on the Xometry platform are 3D printing companies, injection molding, and automated machining. The company reported having more than 28,000 active buyers utilizing its platform at the end of 2021.
Although it isn't profitable yet, Xometry's unique approach to the 3D printing and additive manufacturing industry is growing fast. Like other names on this list, it has a sizable war chest of cash and short-term investments that it can spend on research and marketing as it tries to attract more suppliers and buyers to its marketplace.
4. 3D Systems
3D Systems was another early player in the 3D printing industry, and while it suffered through the boom-and-bust period of the early 2010s, its business has held steady for much of the past decade. After a brief dip during the early days of the pandemic, 3D Systems is back in growth mode.
The company develops printers and design software for all sorts of materials and industries (medical device makers, dental labs, semiconductor designers, aerospace, and automotive manufacturers). It claims leadership among independent 3D printing companies (as measured by sales). As the 3D printing industry expands in the coming years, 3D Systems thinks it will be able to attract lots of new business with its extensive experience and global reach.
As an established tech outfit in the manufacturing sector, 3D Systems offers investors the prospect of more stable growth, along with profitability. It also has a large net cash position from which it can consolidate its lead in 3D printers and software technology.
5. PTC
By far the largest company on this list, PTC is a longtime technology partner of manufacturing and industrial enterprises. Fast approaching $2 billion in annualized sales and highly profitable, PTC has all the tools needed to digitally transform industrial businesses.
Besides 3D printing computer-aided design software (ANSYS is a peer and software partner that also operates in this space), PTC specializes in augmented reality, industrial IoT (Internet of Things), and product life-cycle management software. Most of its revenue is subscription-based (including its Creo software that enables 3D printing), making for a stable and steadily growing business model that generates ample cash flow. PTC puts spare cash to work developing new products for its partners and makes bolt-on acquisitions of other software companies that enhance its overall portfolio.
As a larger company, PTC won't be the fastest-growing stock in the additive manufacturing and 3D printing space. However, the company has established itself as a leader in industrial technology and should be a primary beneficiary as the production of manufactured goods gets more efficient.
The future of 3D printing
Manufacturing technology is making inroads throughout the global economy by reducing the cost of production and localizing and speeding up the time it takes to deliver customer orders. This is far from mere hype. Nevertheless, as is the case with all technology investments, progress won't go straight up. Expect twists and turns in these stocks as they develop new methods to design and make products.
If you decide to invest, do so in a measured way. Maintain a diversified portfolio, be wary of stocks benefiting from investor over-optimism, and always leave spare cash to invest more when there are inevitable dips. Given enough time -- years and decades -- investing in 3D printing could eventually provide a big payoff.
Related communication stocks topics
Investing in 5G Stocks
As the 5G technology rollout continues, these companies look like winners.
Investing in Top Telecommunications Stocks
Our world is increasingly interconnected, and these companies make it happen.
Investing in Communication Stocks
Communications has a broad definition. These companies are the leaders in the space.
Investing in Top Consumer Discretionary Stocks
When people have a little extra cash, they indulge in offerings from these companies.
Nicholas Rossolillo has positions in Autodesk and PTC. The Motley Fool has positions in and recommends Autodesk, HP, and Microsoft. The Motley Fool recommends 3D Systems, ANSYS, Dassault Systemes, PTC, and Trimble Inc. The Motley Fool has a disclosure policy.
Motley Fool Investing Philosophy
- #1 Buy 25+ Companies
- #2 Hold Stocks for 5+ Years
- #3 Add New Savings Regularly
- #4 Hold Through Market Volatility
- #5 Let Winners Run
- #6 Target Long-Term Returns
Why do we invest this way? Learn More
Related Articles
3 Dividend-Paying Tech Stocks to Buy In October
Why Microsoft Fell Today
This Tech Giant Just Raised Its Dividend by 10%
How Many Blue Chip Stocks Are There?
10 Best Dividend Stocks to Buy Now in October
2 Dividend Raises That Can Boost Your Passive Income
Dow Jones Bear Market: 3 Stocks to Buy Now
Premium Investing Services
Invest better with The Motley Fool. Get stock recommendations, portfolio guidance, and more from The Motley Fool's premium services.
View Premium Services
3D Printing Is About to Explode; Here's 1 Way to Profit From It
Years ago, I bought shares of 3D Systems (DDD -7.36%). My investment did not pan out. I should have seen the warning signs. While it was easy to see the potential upside in a radical shift in manufacturing (an "important and emerging industry"), I was unable to find a top dog and first-mover company.
I felt the strongest pure-play was 3D, and their plant was nearby, so I made a small investment in the company. After several years, I took the loss and gave up on it.
Now I believe I have identified the top dog and first mover in additive manufacturing. I'm excited about Velo3D (VLD -10.42%). Here's why I think that additive manufacturing is about to soar far higher, and why Velo3D will lead the way.
Image source: Getty Images.
What is additive manufacturing?
3D manufacturing has been renamed additive manufacturing, or AM. The idea is that you are manufacturing something from nothing ("adding"), as opposed to subtractive manufacturing, where you create something by chipping away at a block of metal, plastic, or other material. Companies like Stratasys (SSYS -5.89%) with its MakerBot competed with 3D Systems in the public markets. And while noise was made, the stocks underperformed.
SSYS data by YCharts
These stocks focused on the little-guy manufacturers, the entrepreneurs with garage space who want to create things. And that might still pan out, of course. But I gave up on that idea.
What's exciting me now is the use of AM in the high end, with the creation of very expensive parts for large-cap companies. For instance, rocket engines. It would be amazing if an aerospace company could simply print out a rocket engine. Imagine the money that could be saved, and how much faster the manufacturing process would be. AM promises to be faster and cheaper than traditional manufacturing.
So now we have companies that are competing in that segment as well, like Desktop Metal (DM -8.51%), Markforged (MKFG -6.73%), and the soon-to-be-top-dog (I hope), Velo3D. All three of these stocks have had a very rocky 2022.
DM data by YCharts
But Velo3D is seeing amazing revenue growth and has a super-bright future. And there's a reason for that.
What was the problem with early AM?
There are two major problems with the 3D printing companies up to now. The first major problem that manufacturing companies saw was that after the part was designed, it would break down over time, also known as breakage. So if you wanted to 3D print a new part, you had to add supports to the part so that you could avoid part failure.
The other problem with the 3D printers is that you often had to redesign the part so the machine could create it. You have a part, you want to 3D print it because that's cheaper, and now you have to spend time redesigning the part for the machine. That's not cheap (or quick). So the manufacturing industry has been a little annoyed with these 3D printing companies that say they're going to change the world. It hasn't happened yet.
Velo3D came up with a solution to both of those problems: a 3D laser printer that does not have any breakage. And you can use your existing designs to print the part. That was the company's sales pitch to Elon Musk. And Musk, who is very open-minded, decided to try the machine out.
After testing, the head of additive manufacturing at SpaceX opined that the technology is five years ahead of everybody else. Musk was so excited that he tried to buy the company last year.
The founder/CEO, Benny Buller, did not want to sell. He founded this company, and it's his life dream. But Musk wanted to buy all the machines he had -- and the future machines, too. So SpaceX became a strategic investor. The company bought a bunch of the printers and preordered advance copies of the next generation of the printers (bigger ones). SpaceX wants to go to Mars, and they have to build rockets. They would love to laser-print as much as they can to save costs.
I am bullish on 3D printers, particularly if the machines work as advertised
I am not an engineer, so I cannot really judge the technology. But right now, demand is through the roof, even in this negative and ugly market. (While coming off a tiny base, sales are up 160% from a year ago). So Velo3D is one of my more bullish ideas.
My family started buying Velo3D stock in July and August, adding small positions over a couple of months. This is only a move for the risk-tolerant, as Velo3D isn't profitable and the company is still burning a lot of cash. The company finished Q2 with $142 million in cash, after burning through $44 million in three months.
If 3D manufacturing pans out, this is a massive opportunity over the next 20 to 30 years (and far longer than that, actually). And the CEO says his company will take market share from rivals and climb out into top dog status. I believe him, and I trust Musk's engineering judgment. So my money is here.
Taylor Carmichael has positions in Velo3D, Inc. The Motley Fool recommends 3D Systems and Velo3D, Inc. The Motley Fool has a disclosure policy.
3D printing processes
Metal casting with 3D printed ceramic shell
CAD model used for 3D printing. The process of manually modeling the preparation of geometric data for 3D computer graphics is similar to plastic arts such as sculpture. 3D scanning is the process of collecting digital data about the shape and appearance of a real object, creating a digital model based on it.
A variety of processes, equipment, and materials are used in the production of a three-dimensional object through the production of additives. 3D printing is also known as additive manufacturing, so the numerous 3D printing processes available tend to be additive in nature, with some key differences in the technologies and materials used in the process.
Some of the different types of physical transformations that are used in 3D printing include melt extrusion, light curing, continuous liquid interface, and sintering.
Content
- 1 Types of processes 3D print
- 2 Processes
- 2.1 Material extrusion
- 2.2 Powder Fusion
- 2.3 Spraying the binding
- 2.4 Stereolitography
- 2.5 COMPLY0016
- 2.6 Production of liquid additives
- 2.7 Laminating
- 2.8 Directed energy deposit (DED)
- 2.8.1 Powdered deposition of directed energy
- 2.8.2 Metal wire processing
- 3 Printers 9.1
- 3.2 Consumer use
- 3.3 Large 3D printers
- 3.4 Microscale and nanoscale 3D printing
Types of 3D printing processes
There are many different 3D printing processes that can be divided into seven categories: [1]
- Photopolymerization of VAT
- Inkjet Technology (Single and Multiple Jet Inkjet)
- Binder Spray
- Fusion Powder Bed
- Material Extrusion
- Directed Energy Release
- Sheet laminating
Each process and equipment has its pros and cons. These typically include aspects such as speed, cost, raw material versatility, geometric constraints and tolerances, as well as mechanical and external product properties such as strength, texture and color.
The variety of processes and equipment allows it to be used by amateurs and professionals alike. Some of them are better suited for industrial use (in this case, the term “additive manufacturing” is preferable), while others make 3D printing accessible to the average consumer. Some printers are large enough to fabricate buildings, while others tend to create micro- and nano-sized objects, and in general many different technologies can be used to physically create the designed objects. [2]
Processes
Several 3D printing processes have been invented since the late 1970s. [3] Printers were originally large, expensive, and very limited in what they could produce. [4]
A large number of additive processes are now available. The main differences between the processes are in the way the layers are applied to create the parts and in the materials used. Some methods, for example, melt or soften the material to create layers. Selective Laser Melting (SLM) or Direct Metal Laser Sintering (DMLS), Selective Laser Sintering (SLS), Fused Deposition Simulation (FDM), [5] [6] or fused fiber fabrication (FFF), while others solidify liquid materials using various sophisticated techniques such as stereolithography (SLA). With the manufacture of laminate products (LOM), thin layers are cut into shapes and bonded together (eg paper, polymer, metal). Each method has its own advantages and disadvantages, so some companies offer a choice of powder and polymer as the material from which the object is built. [7] Others sometimes use standard ready-made business paper as the material to make a durable prototype. The main considerations when choosing a machine are usually speed, the cost of a 3D printer, a printed prototype, the choice and cost of materials, and color options.
[8]
Printers that work directly with metals are usually expensive. However, less expensive printers can be used to make the mold, which are then used to make metal parts.
Material extrusion
Schematic illustration of extrusion deposit; thread a) plastic is fed through a heated movable head b) which melts and extrudes it, depositing layer by layer in the desired form c) . Moving platform e) is lowered after each layer is applied. For such equipment, additional vertical support structures d) needed to support overhanging parts
Main article: Fused deposition simulation
Slow motion video of the robot model (Make Log logo) printed using FDM on a Fisher RepRapPro printer.
Fused fiber fabrication ( FFF ), also known by the trademark Fused deposition simulation gaskets. This principle was further developed by S. Scott Crump at the end of 1980s and commercialized in 1990 by Stratasys. [12] Since the patent for this technology has expired, a large community of open source developers has emerged. DIY variants using this type of 3D printer became known as the RepRap project (for a self-replicating rapid prototype). As a result, the price of this technology has fallen by two orders of magnitude since its inception, and it has become the most common form of 3D printing. [13]
In deposition modeling, a pattern or part is made by extruding small balls or streams of material that immediately solidify into layers. The thermoplastic filament or other material or mixture with a low melting point is fed into the extrusion nozzle head (3D printer extruder), where the filament is heated to the melting point and extruded onto the worktable. More recently, molten pellet deposition (or molten particle deposition) has been developed in which plastic particles or granules replace the need for filament. [14] [15] The nozzle head heats the material and turns the flow on and off. Typically, stepper motors or servo motors are used to move the die head and adjust the flow. The printer usually has 3 axes of movement. A automated manufacturing (CAM) software package is used to generate a G-code that is sent to a microcontroller that controls the motors.
Plastic is the most common material for this type of printing. Various polymers can be used, including acrylonitrile butadiene styrene (ABS), polycarbonate (PC), polylactic acid (PLA), high density polyethylene (HDPE), PC/ABS, polyphenylsulfone (PPS) and high impact polystyrene (HIPS). Typically, the polymer is in the form of a filament made from virgin resins. There are many projects in the open source community that aim to recycle household plastic waste into filaments. [16] [17] [18] [19] This includes machines used to shred and extrude plastic material into filaments, such as recyclebots. Additionally, fluoropolymers such as PTFE tubing are used in the process due to the material's ability to withstand high temperatures. This ability is especially useful in fiber transfer. [20]
Glass 3D printer, molten glass application
Metal and glass can also be used for 3D printing, although they are much more expensive and are usually used for art. However, the development of WAAM (Arc Wire Additive Manufacturing) has reduced the cost of metal 3D printing.
FDM is somewhat limited in the variety of shapes that can be made. For example, FDM usually cannot create structures like a stalactite as they will not be supported during build. Otherwise, a thin support must be built into the structure, which can be broken off during finishing. Typically, the software that converts the 3D model into a set of flat layers, called a slicer, will take care of adding these supports and some other resources to make these shapes possible.
Fusion Powder Bed
Schematic representation of grain bonding: moving head a) selectively bonds (by glue drops or laser sintering) the surface of the powder layer e) ; the moving platform e) gradually lowers the bed and the hardened object d) lies inside the loose powder. New powder is continuously added to the layer from the powder container. c) with alignment mechanism b)
Another approach to 3D printing is the selective fusing of materials in a granular layer. This technique connects the pieces of the layer and then moves up in the work area, adding another layer of granules and repeating the process until a piece is formed. This process uses unmelted material to support the projections and thin walls of the part being produced, reducing the need for temporary auxiliary supports for the part. For example, in selective thermal sintering, the thermal head heats layers of powder material. thermoplastic; when the layer is finished, the layer of powder is lowered and the automatic roller adds a new layer of material, which is sintered to form the next section of the model; Using a less intense thermal head instead of a laser makes this solution cheaper than using lasers and can be reduced to the size of a desktop. [21]
Laser sintering methods include selective laser sintering (SLS), with both metals and polymers (e.g. PA, PA-GF, Rigid GF, PEEK, PS, Alumide, Urea, elastomers) and direct metal laser sintering (DMLS). [22]
Selective laser sintering (SLS) was developed and patented by Dr. Carl Deckard and Dr. Joseph Beeman at the University of Texas at Austin in the mid 80s. [23] sponsored by DARPA. [24] A similar process was patented, but not commercialized, by R. F. Householder in 1979. [25]
Selective laser melting (SLM) does not use sintering to melt powder granules, but completely melts the powder with a high energy laser to create completely dense materials in a layer-by-layer process that has similar mechanical properties to conventional metals.
Electron Beam Melting (EBM) is a similar type of additive manufacturing technology for metal parts (such as titanium alloys). EBM manufactures parts by melting metal powder layer by layer with an electron beam in a high vacuum. Unlike metal sintering methods that operate at temperatures below the melting point, EBM parts do not contain voids. [26] [27]
Binder spraying
Binder inkjet 3D printing technique is the application of a bonding adhesive onto layers of a material, usually powdered. Materials can be ceramic or metal based. This method is also known as inkjet 3D printing system. To manufacture a part, the printer builds a model using a head that moves along the base of the platform and applies layer by layer, distributing a layer of powder (plaster, or resin) and applying a binder in the cross section of the part using inkjet printing. This is repeated until each layer has been printed. This technology allows full-color prototypes, protrusions and elastomer parts to be printed. The durability of powder prints can be improved by using wax or thermoset resin impregnation. [28]
Stereolithography
Schematic representation of photopolymerization; light-emitting device a) (laser or DLP) selectively illuminate the transparent bottom c) tank b) filled with liquid photopolymerizable resin; hardened resin d) is gradually lifted by a lifting platform e)
Main article: Stereolithography
The Stereolithography (SLA) process is based on the light curing (photopolymerization) of liquid materials into a solid form; it was patented at 1986 Chuck Hull. [29]
In this process, the vat of liquid polymer is exposed to controlled lighting (eg laser or digital light projector) under safe conditions. Most commonly, the exposed liquid polymer solidifies by crosslinking caused by the addition of carbon to the carbon double bonds in acrylates. [30] Polymerization occurs when photopolymers are exposed to light when photopolymers contain chromophores otherwise the addition of photosensitive molecules is used to react with the solution to start polymerization. The polymerization of monomers leads to the formation of cross-links, resulting in the formation of a polymer. Through these covalent bonds, the property of the solution is changed. [31] The build plate is then moved down in small increments and the liquid polymer is again exposed to light. The process is repeated until the model is built. The liquid polymer is then drained from the vat, leaving a solid model. In EnvisionTEC Perfactory [32] is an example of a DLP rapid prototyping system.
Inkjet Printer Systems such as Objet PolyJet System Spray photopolymer materials onto the tray to build ultra-thin layers (16 to 30 µm) until the part is ready. Each photopolymer layer is cured with UV after blasting, resulting in fully cured models that can be processed and used immediately without post curing. The gel-like base material, designed to support complex geometries, is manually removed by water jetting. It is also suitable for elastomers. Another type of inkjet printing system is available on the market that can print layer by layer on photopolymer with intermediate UV curing to produce ophthalmic corrective lenses. In this case, no support structures are required, since ophthalmic lenses do not need protrusions. Luxexel, a Dutch language company, has commercialized this technology and printing platform. [33]
Ultra-small parts can be produced using 3D microfabrication technology used in multiphoton photopolymerization. This approach uses a focused laser to track a desired 3D object in a block of gel. Due to the non-linear nature of the photoexcitation, the gel only cures to a solid state where the laser has been focused, and the remaining gel is then washed off. Elements smaller than 100 nm, as well as complex structures with moving and interconnected parts, are easily fabricated. [34]
Another approach uses a synthetic resin that is cured using LEDs. [35]
In mask-image projection stereolithography, a three-dimensional digital model is cut into a set of horizontal planes. Each slice is converted into a 2D mask image. The image of the mask is then projected onto the surface of the photocurable liquid resin, and light is projected onto the resin to cure it in the form of a layer. [36] This technique has been used to create objects made up of multiple materials that solidify at different rates. [36] In research systems, light is projected from below, allowing the resin to spread quickly into uniform, thin layers, reducing production time from hours to minutes. [36] Commercially available devices such as the Objet Connex apply resin through small nozzles. [36]
Continuous liquid interface manufacturing (CLIP) is another form of additive manufacturing that uses a DLP-based photopolymerization process to create smooth, solid objects in a variety of shapes. The continuous CLIP process starts with a puddle of fluid. photopolymer resin. Part of the bottom of the pool is transparent to ultraviolet light (the "window"). As with previous DLP systems, a beam of ultraviolet light passes through the window, illuminating a precise section of the object. The light causes the resin to harden. The object rises slowly enough that the resin can drain and maintain contact with the bottom part of the object [37] CLIP differs from traditional DLP processes due to the oxygen-permeable membrane that sits underneath the resin, creating a "dead zone" (resistant liquid interface) preventing the resin from attaching to the window (photopolymerization between the window and the polymerizer is inhibited). [38]
Unlike stereolithography, the printing process is considered by its founders to be continuous and significantly faster than traditional DLP processes, allowing parts to be produced in minutes rather than hours. [37] [38] [39]
Recently, stereo 3D printing techniques have been further developed for the additive manufacturing of ceramic materials. Successful 3D printing of ceramics using stereolithography is achieved through photopolymerization of pre-ceramic polymers to give way to silicon-based ceramics in a class more commonly known as polymer ceramics, including silicon carbide and silicon oxycarbide. [30]
Computer Axial Lithography
Computed axial lithography is a 3D printing technique based on the inverse principle of computed tomography (CT) to create prints on a photocurable resin. It was developed in collaboration with the University of California at Berkeley with the Lawrence Livermore National Laboratory. [40] [41] [42] Unlike other 3D printing methods, it does not build models by applying layers of material, such as fused deposition modeling and stereolithography, instead it creates objects using a series of 2D images projected onto a resin cylinder. [40] [41] [42] It is notable for its ability to create objects much faster than other resin methods and for its ability to insert objects into prints. [40]
Liquid additive manufacturing
Liquid additive manufacturing (LAM) is an additive manufacturing method of applying a liquid or highly viscous material (such as liquid silicone rubber) to a building surface to create an object that is then vulcanized using heat to harden . [43] [44] [45] The process was originally created by Adrian Boyer and then built on the German RepRap. [43] [46] [47]
Lamination
Main article: Laminating
Some printers can use paper as a building material, which reduces printing costs. In the 1990s, some companies sold printers that cut out cross sections from a special adhesive. coated paper using a carbon dioxide laser and then laminated them together.
In 2005, Mcor Technologies Ltd developed a different process using regular sheets of office paper, a tungsten carbide blade to cut out the shape, and selective glue application and pressure to glue the prototype. [48]
There are also a number of printer companies that print laminated objects using thin plastic and metal sheets.
Main article: Ultrasonic densification
Ultrasonic densification (UC) or ultrasonic additive manufacturing (UAM) is a low temperature additive manufacturing or 3D metal printing technology.
Directed Energy Deposition (DED)
Directed Energy Powder Deposition
Directed Energy Powder Deposition uses a powerful laser to melt a metal powder that is fed into the focus of a laser beam. The laser beam usually passes through the center of the hardfacing head and is focused by one or more lenses into a small spot. The assembly takes place on an X-Y table which is controlled by a toolpath generated from a digital model to build the object layer by layer. The deposition head rises vertically as each layer is completed. The metal powder is delivered and distributed around the circumference of the head, or may be separated by an internal manifold and delivered through nozzles arranged in various configurations around the hardfacing head. A hermetically sealed chamber filled with an inert gas or a local inert shielding gas is often used to shield the molten bath from atmospheric oxygen for better control of material properties. The powder-fed directed energy process is similar to selective laser sintering, but the metal powder is applied only where material is being added to the part at that time. This process supports a wide range of materials, including titanium, stainless steel, aluminum and other specialty materials, as well as composites and materials with varying functionality. This process can not only completely create new metal parts, but can also add material to existing parts, such as for coatings, repairs, and hybrid manufacturing applications.
LENS (Laser Engineered Net Shaping), which was developed by Sandia National Labs, is one example of a powder-fed directed energy deposition process for 3D printing or restoring metal parts. [49] [50]
Metal wire processing
Laser-based wire feeding systems such as laser metal deposition wire (LMD-w) feed the wire through a nozzle that is laser melted using inert gas shielding either in an open environment (gas surrounding the laser) or in a sealed chamber. Freeform electron beam fabrication uses an electron beam heat source inside a vacuum chamber.
It is also possible to use conventional gas arc welding attached to the 3D scene to 3D print metals such as steel and aluminum. [51] Inexpensive open source RepRap-style 3-D printers were equipped with Arduino-based sensors and demonstrated acceptable metallurgical properties when using conventional welding wire as the starting material. [52]
Printers
Industrial ceramic and metal 3D printer
Industrial use
industries such as aerospace, architecture, automotive, defense and medical, and many others. As of 2018, the cost of 3-D printers has dropped to under $100, with lower-end, higher quality desktop printers costing roughly $2,500. These types of devices are widely used in industry for prototyping, jig making, fastening, fixing small custom components, and even additive manufacturing of real products. [53]
In addition, higher-end 3D printers have become relatively common for manufacturing and additive manufacturing. [53] For example, General Electric uses a high quality model to make turbine parts. [54] Many of these systems are used for rapid prototyping before mass production methods are applied. Volkswagen uses 3D printers on its assembly lines to print tools, fixtures and fixtures. They estimate that 3D printers save €250,000 a year. [55] According to one report, almost 75% of desktop 3D printers are used by industry and not by consumers. [56]
Military and defense companies also use 3D printers. The Royal Netherlands Air Force uses desktop 3D printers at its Vonsdrecht Air Force Base to make alignment fixtures and tools. [57] In the US, Hill Air Force Base uses 3D printed parts to repair fighter jets. [58]
Higher education has been a major buyer of desktop and professional 3D printers. [59] Significant purchases of desktop 3D printers by both public schools and universities helped support the desktop 3D printer market, which was struggling in 2015-2016. [60] Since higher education is the home of research, 3D printing is used to make equipment for further research and reduce costs. For example, chemists can 3D print flow reactor systems that would otherwise be too expensive to purchase. [61] The UCL School of Pharmacy in the UK has created a modular chemical synthesis flow reactor system that can be easily 3D printed in labs around the world at a low cost. [62] Libraries around the world have also become home to small 3D printers for educational institutions and the community. [63]
Consumer use
RepRap version 2.0 (Mendel)
All plastic parts for the machine on the right were produced by the machine on the left. Adrian Boyer (left) and Vic Olliver (right) are members of the RepRap project.
Several projects and companies are making efforts to develop affordable 3D printers for home use. Much of this work has been done and targeted at the DIY/Manufacturer/Enthusiast/First Companies Implementing Community, with additional links to the academic and hacker communities. [64]
The RepRap Project is one of the longest running projects in the desktop category. The RepRap project aims to produce a free and open source hardware (FOSH) 3D printer, whose full specifications are published in the GNU General Public License, that is capable of reproducing itself by printing many of its own (plastic) parts to create more machines. [65] [66] RepRaps have already shown the ability to print printed circuit boards [67] and metal parts. [68] [69] The world's most popular 3D printer is the Prusa i3, a RepRap printer. [70] [71]
Due to the goals of FOSH RepRap, many related projects have used their design for inspiration, creating an ecosystem of related or derivative 3D printers, most of which are also open source projects. The availability of these open source designs means that 3D printer options are easy to invent. However, the quality and complexity of printer designs, and the quality of kits or finished products, vary greatly from project to project. The rapid development of open source 3D printers is of interest in many areas, as it allows for hyper-customization and the use of public domain designs for manufacturing open source technology. This technology can also help sustainable development initiatives as the technology is easily and economically created from resources available to local communities. [72]
The cost of 3D printers has dropped dramatically since around 2010: machines that used to cost $20,000 now cost less than $1,000. [73] For example, as of 2013, several companies and individuals are selling parts to assemble various RepRap designs for as low as €400 / US$500. [74] Open Source Fab@Home project [75] has designed printers for general use with anything that can be sprayed through a nozzle, from chocolate to silicone sealant and chemicals. Printers designed to match the project's designs have been available from vendors in kits or pre-assembled form since 2012 at prices in the $2,000 range. [74] Several new 3D printers target the small, low-cost market, including mUVe3D and Lumifold. Rapide 3D has engineered a $1,499 professional grade crowdsourced 3D printer that won't vaporize or rattle during use. [76] At 3Doodler, "3D Printing Pen" raised $2.3 million on Kickstarter and pens sold for $99, [77] although 3D Doodler has been criticized for being more like a pen, than a 3D printer. [78]
As the cost of 3D printers has come down, they are becoming more financially attractive for self-production of personal goods. [79] In addition, home 3D printing products can reduce the environmental impact of manufacturing by reducing material use and distribution impacts. [80]
In addition, several RecycleBots, such as the commercially available Filastruder, have been designed and manufactured to convert plastic waste such as shampoo containers and milk jugs into inexpensive RepRap fibres. [81] There is some evidence that using this distributed disposal approach is better for the environment. [82]
RepRap development and hyper-customization 3D printers have created a new category of printers suitable for small businesses and consumers. Manufacturers such as Solidoodle, [54] Robo 3D, RepRapPro, and Pirks 3D have submitted models and kits priced under $1,000, thousands less than in September 2012. [54] Depending on the application, print resolution and production speed are somewhere between a personal printer and an industrial printer. A list of printers with prices and other information is maintained. [74] More recently, delta robots, like the TripodMaker, have been used for 3D printing to further increase fabrication speed. [83] For delta 3D printers, print accuracy depends on the position of the printer head due to its geometry and motion differences.
Some companies also offer 3D printing software to support equipment made by other companies. [84]
Large 3D printers
Large 3D printers have been designed for industrial, educational and demonstration use. A large delta style 3D printer was built in 2014 by SeeMeCNC. The printer is capable of creating objects up to 4 feet (1.2 m) in diameter and up to 10 feet (3.0 m) in height. It also uses plastic pellets as raw material instead of the usual plastic filaments used in other 3D printers. [85]
BigRep One.1 1 m³.
Another type of large printer is large scale additive manufacturing (BAAM). The goal is to develop printers capable of creating large objects at high speed. Cincinnati Incorporated's BAAM machine can produce an object at speeds 200 to 500 times faster than typical 3D printers available in 2014. Another BAAM machine is being developed by Lockheed Martin to print long objects up to 100 feet (30 m) for use in the aerospace industry. [86]
See also Construction 3D printing
Microscale and nanoscale 3D printing
Microelectronic device fabrication methods can be used for 3D printing of nanosized objects. Such printed objects are usually grown on a solid substrate, for example. the silicone plate they are attached to after printing as they are too small and fragile to be manipulated after assembly.
In one method, 3D nanostructures can be printed by physically moving a dynamic screen mask during the material deposition process, which is somewhat similar to the extrusion method of traditional 3D printers. Programmable height nanostructures with a resolution of only 10 nm have been obtained in this way by physical metal vapor deposition. A stencil mask controlled by a mechanical piezoactuator with a milled nanopore in a silicon nitride membrane. 9Kelly, Brett E.; Bhattacharya, Indrasen; Heidari, Hossein; Shusteff, Maxim; Spadaccini, Christopher M.; Taylor, Hayden K. (2019-01-31). "Volumetric additive manufacturing via tomographic reconstruction". Science . 363 (6431): 1075–1079. Bibcode:2019Sci...363.1075K. Doi:10.1126/science.aau7114. ISSN 0036-8075. PMID 30705152. 9 Grant-Jacob, James A.; Mills, Benjamin; Feinaeugle, Matthias; Sones, Collin L.; Oosterhuis, Gerrit; Hoppenbrouwers, Marc B.; Eason, Robert W. (2013-06-01). "Micron-scale copper wires printed using femtosecond laser-induced forward transfer with automated donor replenishment" (PDF). Optical Materials Express . 3 (6): 747. Bibcode:2013OMExp...3..747G. Doi:10.1364/ome.3.000747. ISSN 2159-3930.
Further reading
- Beaumont Newhall (May 1958) "Photosculpture," Image , 7 (5) : 100–105 Archived 2013-10-04 at the Wayback Machine
- François Willème, "Photo-sculpture," U.
S. Patent no. 43,822 (August 9, 1864). Available online at: U.S. Patent 43,822
- François Willème (May 15, 1861) "La sculpture photographique", Le Moniteur de la photographie , p. 34.
- "Rapid Prototyping in Europe and Japan" (PDF). JTEC/WTEC Panel Report. Archived from the original (PDF) on 2017-08-30. Retrieved December 28, 2016.
Fuel cells have been used in various types of vehicles, including forklifts, especially indoors where their net emissions are important for air quality and in space applications. The first commercially produced hydrogen fuel cell vehicle, the Toyota Mirai, was introduced in 2015, followed by Hyundai and Honda entering the market. Fuel cells are also being developed and tested in trucks, buses, boats, motorcycles and bicycles, among other types of vehicles.
As of 2017, there was a limited hydrogen infrastructure with 36 hydrogen fueling stations for vehicles publicly available in the US, however more hydrogen power stations are planned, especially in California.
There are some public hydrogen filling stations, and new stations are planned in Japan, Europe and other countries. Critics question whether hydrogen will be efficient or economical for cars compared to other zero-emission technologies.
Description and purpose of fuel cells in vehicles
All fuel cells consist of three parts: electrolyte, anode and cathode. In principle, a hydrogen fuel cell functions like a battery, generating electricity that can run on an electric motor. However, instead of needing to be recharged, the fuel cell can be fueled with hydrogen. Various types of fuel cells include polymer electrolyte membranes (PEM), direct methanol fuel cells, phosphoric acid fuel cells, molten carbonate fuel cells, solid oxide fuel cells, reformed methanol fuel cell, and regenerative fuel cells.history
The fuel cell concept was first demonstrated by Humphry Davy in 1801, but the invention of the first working fuel cell has been credited to William Grove, a chemist, lawyer and physicist.Grove's experiments with what he called a "gas battery" proved in 1842 that an electric current could be produced by an electrochemical reaction between hydrogen and oxygen over a platinum catalyst. The first modern fuel cell vehicle was a modified Allis-Chalmers farm tractor fitted with a 15 kilowatt fuel cell, about 1959 years old The space race of the Cold War contributed to the further development of fuel cell technology. The Gemini project has tested fuel cells to provide electrical power during manned space flights. Fuel cell development continued as part of the Apollo program. The electrical systems in the Apollo capsules and lunar modules used alkaline fuel cells. In 1966, General Motors developed the first fuel cell automobile, the Chevrolet Electrovan. It had a PEM fuel cell, a range of 120 miles and a top speed of 70 miles per hour. There were only two seats as a stack of fuel cells and large tanks of hydrogen and oxygen occupied the back of the van. Only one was built, as the project was considered a lien.
General Electric and others continued to operate on PEM fuel cells into the 1970s. Fuel cell containers continued to be limited mainly to space applications in the 1980s, including the space shuttle. However, the closure of the Apollo program sent many industry experts to private companies. By the 1990s, car manufacturers were interested in fuel cell applications and demonstrator cars were being prepared. In 2001, the first 700 bar (10,000 psi) hydrogen tanks were demonstrated, reducing the size of the fuel tanks that could be used in vehicles and expanding the range.
Applications
There are fuel cell vehicles for all modes of transport. The most common fuel cell vehicles are cars, buses, forklifts and material handling vehicles.Cars
The Honda FCX Clarity Concept was introduced in 2008 for leasing by customers in Japan and Southern California and discontinued by 2015. From 2008 to 2014, Honda leased a total of 45 FCX units in the US. Over 20 other FCEV prototypes and demonstrators were produced during this period, including the GM HydroGen4 and the Mercedes-Benz F-Cell.The Hyundai ix35 FCEV Fuel Cell has been available for rent since 2014 with 54 units.
Sales of the Toyota Mirai to government and corporate customers began in Japan in December 2014. Prices started at ¥6,700,000 (~US$57,400) before taxes and a 2,000,000 yen (~US$19,600) government incentive. Former President of the European Parliament Pat Cox has suggested that Toyota will initially lose about $100,000 for every Mirai sold. As of December 2017, worldwide sales were 5,300 worlds. Top selling markets were USA with 2.900 units, Japan from 2100 and Europe from 200.
Retail deliveries of the 2017 Honda Clarity Fuel Cell began in California in December 2016. The Clarity fuel cell, with a range of 366 miles (589 km), has the highest EPA range rating of any zero-emission vehicle in the US, including cell and battery electric vehicle fuel. The 2017 Brightness also has the highest combined and city fuel economy ratings of any EPA-rated hydrogen fuel cell vehicle, with a combined city/highway rating of 67 miles per gallon equivalent (MPGe) and 68 MPGe in city traffic.
In 2017, Daimler abandoned FCEV development, citing lower battery costs and increased EV range, and most automotive companies developing hydrogen vehicles have shifted their focus to battery electric vehicles.
Fuel Economy
The following table compares EPA fuel economy expressed in gasoline equivalent per kilogram per gallon (MPGe) for hydrogen fuel cell vehicles rated by the EPA as of December 2016 and available only in California.Fuel cell powered by ethanol reformer
In June 2016, Nissan announced plans to develop fuel cell vehicles that run on ethanol instead of hydrogen. Nissan claims that this technical approach would be cheaper and easier to deploy refueling infrastructure than hydrogen infrastructure. The vehicle will include a tank containing a mixture of water and ethanol, which is fed into an onboard reformer that separates it into hydrogen and carbon dioxide. The hydrogen is then fed into the solid oxide fuel cell. According to Nissan, the liquid fuel can be a 55:45 mixture of ethanol and water.Nissan plans to commercialize its technology by 2020.
Buses
Demonstration buses also exist, and in 2011 over 100 fuel cell buses were deployed worldwide. Most of these buses were made by UTC Power, Toyota, Ballard, Hydrogenics and Proton Motor. UTC buses have accumulated over 970,000 km (600,000 miles) of driving. Fuel cell buses have 30-141% fuel savings than diesel buses and natural gas buses. Fuel cell buses have been deployed in Whistler Canada, San Francisco, USA, Hamburg, Shanghai, London, England, Sao Paulo and other cities. The Whistler project was terminated in 2015. The Fuel Cell Bus Club is a global collaborative effort in fuel cell trial buses. Notable projects include:12 Fuel cell buses have been deployed in the Oakland and San Francisco area of California. Daimler AG's
completed a successful three-year trial in eleven cities in 2007 with thirty-six experimental buses based on Ballard Power Systems fuel cells.
A fleet of UTC Power fuel cell Thor buses deployed to California operated by the SunLine Transit Agency.
Brazil's first hydrogen fuel cell tire prototype has been deployed in Sao Paulo. The bus was made in Caxias do Sul, and the hydrogen fuel was to be produced in São Bernardo do Campo from water through electrolysis. The program, called "Ônibus Brasileiro a Hidrogênio" (Brazilian Hydrogen Bus), included three buses.Forklift
Fuel cell forklift (also called fuel cell forklift or fuel cell forklift) is an industrial fuel cell forklift used for lifting and transporting materials. Most fuel cells used in forklifts are powered by PEM fuel cells.In 2013, over 4,000 fuel elevators used in material handling were in operation in the US, of which only 500 received funding from DOE (2012). Fuel cell fleets are operated by a large number of companies including Sysco Foods, FedEx Freight, GENCO (from Wegmans, Coca-Cola, Kimberly Clark and Whole Foods) and HEB Grocers. Europe demonstrated 30 fuel cell forklifts with Hylift and expanded with HyLIFT-EUROPE to 200 units, with other projects in France and Austria.
Pike Research stated in 2011 that fuel cell forklifts will be the largest driver of hydrogen fuel demand by 2020.
PEM fuel cell forklift trucks offer significant advantages over petrol forklift trucks because they produce no local emissions. Fuel cell forklifts can run a full 8-hour shift on a single tank of hydrogen, can refuel in 3 minutes, and have a lifespan of 8-10 years. Fuel cell motorized forklifts are often used in refrigerated warehouses because their performance does not degrade at lower temperatures. In design, FC blocks are often made as replacements for replacements.
Motorcycles and bicycles
In 2005, the British firm Intelligent Energy launched the world's first working hydrogen motorcycle called ENV (Emission Neutral Vehicle). The motorcycle contains enough fuel to run for four hours and travel 160 km (100 miles) in urban areas with a top speed of 80 km/h (50 mph). In 2004, Honda developed a fuel cell motorcycle that used the Honda FC Stack. There are other examples of hydrogen fuel cell powered bicycles and bicycles.Suzuki Burgman has received "whole vehicle" approval in the EU. Taiwanese company APFCT is conducting a live street test using 80 motorized fuel cells for the Taiwan Energy Bureau using a fueling system from Italy's Acta SpA.
aircraft
Boeing researchers and industry partners across Europe conducted experimental flight tests in February 2008 of a manned aircraft powered only by fuel cells and light batteries. The fuel cell demonstrator aircraft, as it was called, used a hybrid proton-exchange fuel cell/lithium ion battery (PEM) system to power an electric motor that was connected to a conventional propeller. In 2003, the world's first propeller-driven aircraft was taken, which was completely powered by a fuel cell. The fuel cell was a unique FlatStack stack design that allowed the integration of the fuel cell with plane airfoils.There were several fuel cell unmanned aerial vehicles (UAVs). In 2007, Horizon fuel cell UAVs set a record flow rate for a small UAV. Military personnel are particularly interested in this application due to low noise levels, low thermal signature, and the ability to reach high altitudes.
In 2009, the Naval Research Laboratory (NRL) Ion-Tiger used a hydrogen fuel cell and flew for 23 hours and 17 minutes. Boeing is completing Phantom Eye, Altitude and Long Endurance (HALE) tests to be used for research and surveillance flying at 20,000 m (65,000 ft) for four days at a time. Fuel cells are also being used to provide additional power to aircraft, replacing fossil fuel generators previously used to start engines and power on board. Fuel cells can help aircraft reduce CO2 and other pollutant emissions and noise.
boats
The world's first HYDRA fuel cell used an AFC system with a net power of 6.5 kW. For every liter of fuel consumed, the average engine produces 140 times less hydrocarbons than the average modern car. Fuel cell engines have higher energy efficiency than internal combustion engines and therefore offer better range and significantly reduce emissions. Iceland has committed to converting its huge fishing fleet to use fuel cells to provide auxiliary power by 2015 and eventually provide main power to its boats.Amsterdam recently unveiled its first fuel cell powered boat that ferries people around the city's famous and beautiful canals.
Submarines
The first submersible application of fuel cells is the German Type 212 submarine. Each Type 212 contains nine PEM fuel cells distributed throughout the vessel, providing between 30 kW and 50 kW of electricity. This allows Type 212s to stay submerged longer and makes them harder to detect. Fuel cell submarines are also easier to design, manufacture and maintain than nuclear submarines.Trains
In March 2015, China South Rail Corporation (CSR) demonstrated the world's first hydrogen fuel cell tram at its assembly facility in Qingdao. Chief Engineer of CSR subsidiary Sifang Co Ltd. Liang Jianyin said the company is studying how to reduce the running costs of the tram. In total, 83 miles of track for the new vehicle were built in seven Chinese cities. China plans to spend 200 billion yuan ($32 billion) over the next five years to expand tram lines to more than 1,200 miles.In 2016, Alstom debuted the Coradia iLint, a regional hydrogen fuel cell train that will be the world's first algae plant. Coradia iLint will be able to reach 140 kilometers per hour (87 mph) and travel 600-800 kilometers (370-500 miles) on a full tank of hydrogen. The first Coradia iLint is expected to enter service in December 2017 on the Buxtehude-Bremervörde-Bremerhaven-Cuxhaven line in Lower Saxony, Germany.
Hydrogen infrastructure
Eberle and Rittmar von Helmolt stated in 2010 that challenges remain before fuel cell vehicles can become competitive with other technologies and result in a lack of a broad hydrogen infrastructure in the US: as of July 2017, there were 36 publicly available hydrogen filling stations in the US, 32 of which were located in California. In 2013, Governor Jerry Brown signed AB 8, a bill to fund $20 million a year for 10 years to build up to 100 stations. In 2014, the California Energy Commission allocated $46.6 million to build 28 plants.Japan received its first commercial hydrogen filling station in 2014. By March 2016, there were 80 hydrogen filling stations in Japan, and the Japanese government aims to double that number to 160 by 2020. In May 2017, there were 91 hydrogen filling stations in Japan. In July 2015, there were 18 public hydrogen filling stations in Germany. The German government hoped to increase this number to 50 by the end of 2016, but only 30 were opened in June 2017.
Codes and standards
Fuel cell vehicle is a classification in hydrogen hydrogen codes and standards and fuel cell codes and standards, other main standards are stationary fuel cell applications and portable fuel cell applications.US programs
In 2003, US President George W. Bush proposed the Hydrogen Fuel Initiative (HFI). HFI aims to further develop hydrogen fuel cells and infrastructure technologies to accelerate the commercial adoption of fuel cell vehicles. By 2008, the US contributed $1 billion to this project.In 2009Steven Chu, then US Secretary of Energy, argued that hydrogen vehicles "won't be practical for the next 10 to 20 years." In 2012, however, Chu stated that he saw fuel cell vehicles as more economically feasible, as natural gas prices fell and hydrogen conversion technologies improved. In June 2013, the California Energy Commission provided $18.7 million. USA for hydrogen filling stations. In 2013, Governor Brown signed AB 8, a bill to fund $20 million a year for 10 years for 100 stations. In 2013, the US Department of Energy announced that it had reached $4 million. United States planned for "further development of advanced hydrogen storage systems." On May 13, 2013, the Department of Energy launched h3USA, which is focused on advancing hydrogen infrastructure in the US.
Cost
By 2010, advances in fuel cell technology had reduced the size, weight and cost of fuel cell electric vehicles. In 2010, the US Department of Energy (DOE) estimated that the cost of automotive fuel cells had fallen from 80% to 80% since 2002 and that such fuel cells could be made at US$51/kW, assuming large manufacturing cost savings.Fuel cell electric vehicles have been manufactured with "a range of more than 250 miles between refuellings". They can be refueled in less than 5 minutes. Deployed fuel cell buses have 40% fuel savings compared to diesel buses. The EERE Fuel Cell Program states that since 2011, fuel cells have achieved fuel cell electric vehicle efficiency of 42 to 53% at full power and a durability of more than 75,000 miles with less than 10% voltage degradation, double that of 2006. In 2012 Lux Research, Inc. released a report concluding that by 2030 the cost of capital … will limit adoption to just 5.9GW, which would provide "an almost insurmountable barrier to adoption, except for niche applications." Lux analysis showed that by 2030, applications for stationary PEM fuel cells will reach $1 billion, while the automotive market, including fuel cell forklifts, will reach a total of $2 billion.
Environmental impact
The environmental impact of fuel cell vehicles depends on the primary energy from which hydrogen is produced.Fuel cell vehicles are only environmentally friendly when producing hydrogen using renewable energy. If so, fuel cell vehicles are cleaner and more efficient than fossil fuel vehicles. However, they are not as efficient as electric vehicle batteries, which use much less energy. Typically, a fuel cell vehicle consumes 2.4 times more energy than a battery electric vehicle because electrolysis and hydrogen storage are much less efficient than using electricity to directly load the battery.
As of 2009, cars used most of the oil consumed in the US and produced over 60% of carbon monoxide emissions and about 20% of greenhouse gas emissions in the United States, however hydrogen production for hydrocrest used in gasoline production is among its industrial applications accounted for about 10% of greenhouse gas emissions in the park area. In contrast, a vehicle using pure hydrogen emits several pollutants, producing mainly water and heat, although hydrogen production will create pollutants unless the hydrogen used in the fuel cell is produced using only renewable energy.
In a 2005 wheel well analysis, the DOE estimated that fuel cell electric vehicles using hydrogen produced from natural gas would result in about 55% CO2 emissions per mile of internal combustion engines and have about 25% fewer emissions than hybrid vehicles. . In 2006, Ulf Bossel stated that the large amount of energy required to extract hydrogen from natural compounds (water, natural gas, biomass), packs the light gas by compression or liquefaction, transfers the energy carrier to the user, and also loses energy when Richard Gilbert, co-inventor "Transport Revolutions: Moving People and Freight Without Oil" (2010), also recalls that extracting hydrogen gas ends up using some of the energy it creates. The energy is then absorbed by converting the hydrogen back into electricity in the fuel cells.” “This means that only a quarter of the initially available energy reaches the electric motor”… Such conversion losses prevent, for example, recharging an electric vehicle (EV) such as a Nissan Leaf or a Chevy Volt.
from a wall socket. In 2010, a 2010 analysis of hydrogen fuel cell vehicles from Argonne National Laboratories states that h3 renewable feeds offer a much greater green home effect. This result has recently been confirmed. In 2010, the US DOE Well-to-Wheels publication suggested that the efficiency of a single step of compressing hydrogen to 4,250 psi (43.1 MPa) at a gas station is 9four%. A 2016 study in the November issue of the journal Energy by scientists from Stanford University and the Technical University of Munich found that even with local hydrogen production, “investing in all-electric battery vehicles is the more economical choice for reducing carbon dioxide emissions, primarily due to their lower cost and significantly higher energy efficiency.”
criticism
In 2008, Professor Jeremy P. Myers in The Electrochemical Journal wrote: “Although fuel cells are efficient compared to internal combustion engines, they are not as efficient as batteries, primarily due to the inefficiency of the oxygen reduction reaction …hey is best for off-grid operation or where fuel can be provided continuously.For applications requiring frequent and relatively fast starts... where zero emissions are required, as in enclosed spaces such as warehouses and where hydrogen is considered an acceptable reactant, [the PEM fuel cell] is becoming an increasingly attractive choice [when exchanging batteries is inconvenient]." The practical cost of fuel cells for vehicles will remain high, however, until production volumes are factored into scale and a well-developed supply chain. Until then, costs are about an order of magnitude higher than DOE targets.
Also in 2008, Wired News reported that "Experts say it will be 40 years or more before hydrogen has any meaningful impact on gasoline consumption or global warming, and we cannot afford to wait that long. At the same time, fuel cells are diverting resources away from more immediate solutions.” The Economist, in 2008, quotes Robert Zubrin, author of Energy Victory, as saying, "Hydrogen is just the worst vehicle." The magazine noted that most of the hydrogen is generated by steam reformation, which creates at least as much carbon dioxide emissions per mile as some of today's gasoline cars.
On the other hand, if hydrogen could be produced using renewable energy, "it would be easier to just use this energy to charge the batteries of all electric or plug-in hybrid vehicles." Los Angeles Times wrote in 2009year: "No matter how you look at it, hydrogen is a disgusting way to drive cars." The Washington Post asked in November 2009: "If you wanted to store energy in the form of hydrogen and then use that hydrogen to produce electricity for an engine, when the electrical energy is already waiting to be sucked out of outlets across America and stored in automatic batteries...? »
The Motley Fool stated in 2013 that "there are still price-limiting barriers [for hydrogen vehicles] regarding transportation, storage and, most importantly, production." Volkswagen Rudolf Krebs stated in 2013 that "no matter how great you make cars yourself, the laws of physics get in the way of their overall efficiency. The most efficient way to convert energy into mobility is with electricity.
” He elaborated: “Hydrogen mobility only makes sense if you use green energy,” but… you need to first convert it to “low efficiency” hydrogen, where “you lose about 40 percent of the initial energy.” You then have to compress the hydrogen and store it at high pressure in tanks that use more energy. "And then you have to convert the hydrogen back to electricity in a fuel cell, with another efficiency loss." Krebs continued: "After all, out of your initial 100 percent electrical power, you get 30-40 percent."
In 2014, electric vehicle and energy futurist Julian Cox published an analysis using US government NREL and EPA data that debunks widely held political assumptions about the claimed emissions benefits from using hydrogen in transportation. Cox computed the emissions generated per paired EPA combined-cycle orbit, as well as per wheel, on real-time hydrogen fuel cell vehicles and figures combined with test subjects included in the US Department of Energy's long-term NREL FCV study.
The report presents official data that categorically refutes the marketer's claims of any inherent advantages of hydrogen fuel cells over drive trains of equivalent conventional gasoline hybrids and even conventional small-engined cars with equivalent performance of drive trains due to the intensity of hydrogen emissions from natural gas. The report further demonstrated the economic inevitability of continued use of methane in hydrogen production due to the cut-off effect of hydrogen fuel cell renewable mileage costs due to losses in converting electricity to and from hydrogen compared to the direct use of electricity in a conventional electric vehicle. The analysis runs counter to the marketing claims of vehicle manufacturers involved in promoting hydrogen fuel cells, and whose claims are often reflected in public policy statements. The analysis found that government policy on hydrogen fuel cells has been misled by a false equivalence to very large, very old, or very powerful gasoline vehicles, which do not accurately reflect the choice of emission reduction technologies that are readily available among lower cost and pre-existing new choices.
cars for consumers, and also to the taxpayer who funded the excess hydrogen infrastructure on the assumption that, on scientific grounds, is factually false. Instead, marketing, and therefore government policy claims for hydrogen, can be backed up by official US DOE figures that they are highly misleading. Cox wrote in 2014 that extracting hydrogen from methane is "significantly richer in carbon per unit of energy than coal". Mistaken fossil hydrogen from hydraulic fracturing for an environmentally sustainable energy path threatens to encourage energy policies that will dilute and potentially destroy global efforts to prevent climate change at the risk of diverting investment and focusing on vehicle technologies that are economically compatible with renewable energy." . Business Insider commented in 2013:
Pure hydrogen can be produced industrially, but it consumes energy. If that energy isn't coming from renewable sources, then fuel cell cars aren't as clean as they seem. … Another problem is the lack of infrastructure.
Gas stations need to invest in the ability to fill hydrogen tanks before FCEVs are practical, and it's unlikely many will do so while there are so few customers on the road. … Worsening the lack of infrastructure is the high cost of the technology. Fuel cells are "still very, very expensive."
In 2014, climate blogger and former Department of Energy official Joseph Romm devoted three articles to criticism of hydrogen vehicles. He stated that FCVs still have not overcome the following challenges: the high cost of vehicles, the high cost of refueling, and the lack of fuel delivery infrastructure. “It will take several miracles to overcome all these problems simultaneously in the coming decades.” What's more, he said, "FCVs are not green" due to the release of methane during natural gas production, and when hydrogen is produced, like 95% of it using the steam reforming process. He concluded that renewables could not be used economically to produce hydrogen for the FCV fleet "now or in the future".
A GreenTech Media analyst made similar findings in 2014. In 2015, Clean Technica listed some of the disadvantages of hydrogen fuel cell vehicles, as did Car Throttle. Another Clean Technica writer concluded, "While hydrogen may have a role to play in the world of energy storage (especially in seasonal storage), it seems like a dead end when it comes to public vehicles."
A 2017 analysis published in Green Car Reports found that the best hydrogen fuel cells consume “more than three times as much electricity per mile as an electric vehicle … generate more greenhouse gas emissions than other powertrain technologies … [and have] very high fuel costs… Given all the hurdles and demands for new infrastructure (estimated at $400 billion), fuel cell vehicles appear to be a niche technology at best, with little impact on US oil consumption. In 2017, Michael Barnard, writing in Forbes, pointed out the continuing disadvantages of hydrogen fuel cell vehicles and concluded that "By 2008, it was quite clear that hydrogen was and would be inferior to battery technology as energy storage for vehicles.
Learn more