Materialise 3d print
Online 3D Printing Service | i.materialise
Oops...Seems your browser is blocking cookies. Please adjust your settings to accept cookies.
i.materialise is your online 3D printing service. Upload your 3D model, choose from 100+ different finishes and materials, select the size of your print, receive a price quote instantly and let us take care of printing and shipping your products.
How to Get Started
How to Order a 3D Print
Upload your 3D file
Select material, color & finish
Get an instant price & order
Let us take care of production
Receive your products
Why Order 3D Models on i.
Get Instant Prices
Upload your 3D file and get an instant price, no login required »
Online Marketplace
Did you print a great product? Open a shop and start selling today! »
Materials
20 Different materials including plastics, resins and metals »
Rush 3D Printing Service
Printing Polyamide in less than 48 hours »
Educational Discount
10% discount for students and teachers »
Expertise
Over 25 years of Additive Manufacturing experience »
Upload and Order Your 3D Model
Get instant prices for your 3D design seconds after uploading. With no registration or login required, several user-friendly interfaces for uploading, and over 40 accepted 3D files formats, we’ve got you covered.
Single Upload
Upload and edit one 3D file at a time.
Upload and edit one 3D file at a time
Upload 3D File
Multiple Upload
If you would like to order multiple files, you can upload up to 20 files in one go.
If you would like to order multiple files, you can upload up to 20 files in one go.
Upload Multiple Files
Container Upload
Put multiple small parts in a grid container and print them all together.
Put multiple small parts in a grid container and print them all together.
Learn more
Choose from a wide range of 3D Printing Materials
From titanium to multicolor+, polyamide, 18K gold and more, i.materialise has what you’re looking for. With 20 different materials and over 100 possible color and finish combinations, we offer only the highest quality to turn your ideas into 3D printed reality.
Resins
Perfect for smooth surfaces, high-quality, detailed prints and a huge variety of finishing and post-processing possibilities.
Polyamide (SLS)
A strong, flexible nylon material that is available at a reasonable price and offers a wide variety of colors and finishes.
Multicolor+
Perfect for strong, full-color models that are equally as good as injection molded parts.
925 Sterling Silver
A precious metal with a very high electrical and thermal conductivity. The material is very malleable and shines brightly after polishing.
Titanium
Light, strong, corrosion-resistant metal for functional parts, spare parts and jewelry.
Brass
An incredibly versatile precious metal that is available in a wide variety of colors and plating.
Discover More
Trusted Partner Of
Upload 3D Model | 3D Printing Service
Upload 3D Model | 3D Printing Service | i.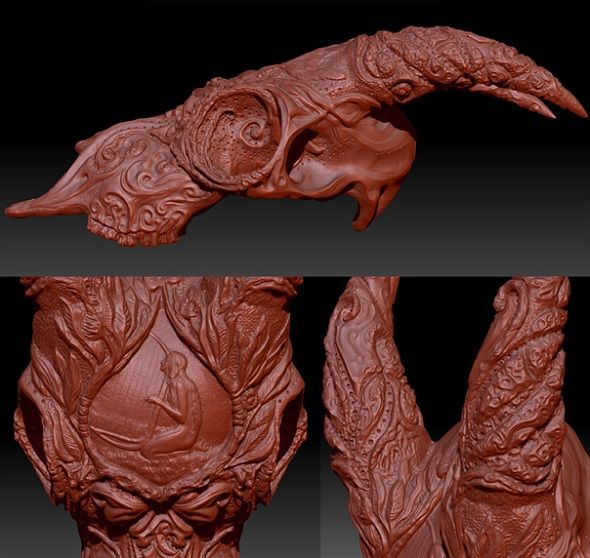
Oops...Seems your browser is blocking cookies. Please adjust your settings to accept cookies.
drag and drop it like it’s hot
Analyzing your design
Please wait for a few seconds while we update the 3D viewer with the repaired model.
Something went wrong while updating your model. Please try again.
No results found.
Sorry! Something went wrong. Please refresh the page and try again.
Upload 3d model
Share Your Model Recent models
3D model workspace
Materials
Loading. ..
Colors and Finishes
Loading...
{{$select.selected.name}} No results found.
Scale
Quantity
Price
{{vm.getProductProcessingStateKey() | translate}} Calculating
Discounted price
By clicking ‘Accept Repair’, I understand that the repair may have altered the geometry of my model.
(*) If the model is 3D printable in the requested material
Materials
Analyze
Optimize
3D Printing
- How It Works
- 3D Printing Materials
- 3D Printing Technologies
- Hire a 3D Designer
- Educational Discount
Business
- Manufacturing Partnership
- Referral Partnership
- White Label Integration
- Crowdfunding
- API
Support
- Contact Us
- Shipping Info
- Tutorials
- 3D Design Tools
Shop
- Shops
- Designers
- Open a Shop
Community
- About Us
- Blog
- Forum
Terms and Conditions Privacy Policy Cookie Statement Sitemap
© Copyright 2022 Materialise nv, all rights reserved. “i.materialise” is a registered trademark of Materialise nv.
Printer for the materialization of ideas
Alexander Osinev
Printing deep and wide!
About the general in boxes and globes
How it works
3D printer is a universal tool
Even for our parents, computer technology was inextricably linked with grinding numbers and solving mathematical problems formulated by specialists from various exact sciences. But obsession with mathematics is a thing of the past. The phrase "computer creativity" does not surprise anyone. If we talk about traditional creativity, it seems that writers were the first to move from typewriters to computer terminals, who appreciated the text editor as an alternative to marginal entries and manual reprinting of pages due to minor editing. Further more. The computer is now often almost the main tool for musicians, designers, architects and even filmmakers. It is especially important that the quality of films and books still depends not on the computer, but on the person. Computers, in fact, are still crunching numbers, saving us time (and most often money), leaving more opportunities for creativity itself.
Print deep and wide!
The development of computer peripherals - scanners, printers and other equipment - also did not stand still. New types of human activity, subdued by the general computer boom, often require special output and input devices. Computers have long been able to translate text, images and sounds into their native form and back, even the first developments in the field of analysis and reproduction of smells have appeared. In the 90s, a lot was done to make computer technology perceive and make digital models of real objects, which was solved by several 3D scanning technologies. Finally, the way back was paved: the computer was taught to create, on the basis of a digital three-dimensional model of an object, its completely material prototype. This was done thanks to 3D printing, which we will discuss in more detail in this article.
3D printing is not so new as to claim any cutting-edge scientific developments: the roots of this technology go back to the early 90s. However, many of us may consider 3D printing a curiosity. 3D printers have not become widespread up to entry into every home, it is too early to even say that these devices are in every company where the creation of a three-dimensional prototype is one of the mandatory steps. You can print literally anything - from a one-to-one scale model of a bolt to a miniature copy of a satellite or a future stadium, but the development of technology has long been held back (and partly still held back) by important factors. A 3D printer is an expensive piece of equipment, and although prices have steadily declined over the years, not every organization can afford it. In addition, a fairly high qualification is required when creating a computer three-dimensional model, and in this sense it is gratifying that in recent years designing on paper with a pencil and a ruler has become an anachronism.
General information in boxes and globes
There is a company in Noginsk near Moscow that has been mainly engaged in the production of packaging with full-color printing for many years. Here, quite a long time ago, they appreciated the convenience of working with computer three-dimensional models when creating a construct and design, and therefore they also mastered the corresponding software products. “When, over time, we learned how to operate with computer images well,” says Alexander Dobrolyubov, head of the Public Market company, “the idea arose to show customers not yet existing boxes in three-dimensional form. We found and mastered complex software products like Autodesk Maya, and then realized that you can not limit yourself to packaging alone.”
The company began to look for the right technology and discovered 3D printing. In 2007, a ZPrinter 510 3D machine was purchased. “Through trial and error,” says Alexander Dobrolyubov, “we came to the conclusion that some products at the prototyping stage can be done quickly and well by 3D printing. We began to take orders for the creation of prototypes of all kinds of products from outside. In order to be less dependent on external orders for 3D printing, the Public Market made sure that the company also had its own project for a 3D printer. This project was the creation of a large relief globe. By itself, the globe may not be 100% used for its intended purpose, but as an original piece of furniture it will decorate the office of any leader and will be a great gift. The choice was based not so much on opportunistic considerations as on the personal sympathies of employees for such a project. Nevertheless, the project needed to be brought to the stage where a globe of one size or another could be placed on the floor or on a table, and not stop only at the contemplation of the model on the computer screen. And the ZPrinter 510 helped with that.
How it works
The technology used by Z Corporation printers (namely, this company produces devices under the ZPrinter brand) basically involves layer-by-layer growth of a model from plaster powder in a special chamber. In various models of Z-printers, the build chambers have different volumes, which determine the maximum size of the object being grown.
The model to be printed must be as realistic as possible, without infinitely thin walls and open surfaces. If it’s quite simple, it should fully correspond to the future subject, and not be its simplified likeness. For example, it is not enough if the computer models of the fragments of the globe are only some parts of the surface of the sphere. These fragments must have a certain thickness, calculated on the basis of the expected loads on the final product. The printer software is able to point out a number of errors in the simulation, but the operator, based on his own experience, must also see the weaknesses himself.
If everything is in order with the computer model, the printer driver programmatically breaks it into layers of 0.1 mm, which are then applied one after another. In the course of printing, the gypsum particles are held together with a special binder, and the surface of the future model is simultaneously painted in accordance with the developed design.
Printing is from top to bottom, while the movable bottom of the chamber drops slightly after applying the next layer. The chamber is gradually filled with gypsum over the entire area to the current level of the height of the model, but the binder unites only those particles that should become part of the final prototype. It turns out that at every moment the model being built is surrounded on all sides by powder - it performs the function of supporting the model and its individual parts. This is necessary because the printer allows you to print objects with fairly small details, and before special processing after printing, gypsum remains a very fragile material that breaks even with a slight impact. An additional plus of this approach is that Z Corporation printers allow you to grow several models at once, which can be located throughout the volume of the chamber. So, for example, it happens when growing fragments for three-dimensional globes in the Public Market.
After printing is completed, the grown models are dried. Then the chamber is freed from excess powder, which will be reused. Almost finished and still very fragile models are carefully moved into a special blowing chamber, where powder residues are removed from them and treated with an impregnating composition that makes the model durable. Which one depends on the specified strength criteria. Finally, in order for the model to dry after impregnation and be ready for use, you need to wait a few more minutes. Depending on the model, ZCorp printers allow you to perform certain auxiliary actions automatically.
3D printer - universal tool
The above technology, of course, limits the designer's imagination to some rules, but for the most part they are tied to the elementary laws of physics. Otherwise, you can print the most complex models, which makes the scope of the printer very wide. According to Alexander Dobrolyubov, the possibilities of 3D printing technology awaken creativity, which he sees in the example of Public Market employees. “Our ZPrinter 510 is especially interesting and often indispensable for creating prototypes of products that have a great artistic component. These are shoes, architectural objects, and clothes,” says Alexander. “Healthcare institutions are asking us questions about preparing ideal training models.” In this regard, he spoke about a recent call from doctors who needed help preparing for a complex operation - a full-size model of a human head that accurately takes into account the internal structure of a particular patient and was created on the basis of tomography results. “And I don’t know how it would be possible to solve such a problem without a 3D printer,” Alexander concludes.
At the same time, it must be admitted that 3D printing is still expensive due to the low prevalence of the technology and the lack of awareness among end users. The price of components, consumables and, as a result, the cost of printing is very high. Buying a printer for occasional use may not justify itself. Alexander has no doubt that without his own project, his company would certainly not have profited from the printer. “It so happened,” he explains, “that the embossed globe is a unique product, and we can really make money on it. The uniqueness of the project is that we can make the globe the way the customer wants to see it: we vary the sizes, textures, colors. In addition to being unique, it is also convenient for both us and our clients.” Public Market has already produced a considerable number of various products, including globes, and on the day when Alexander answered questions for this article, another globe was in the works, the diameter of which, at the request of the customer, will be 1 m 20 cm.
The secret of Public Market's success is that they have not forgotten the main thing here: a printer, even if it performs three-dimensional printing, is just a tool. To make money with such a device, you need ideas and the ability to bring them to mind. “The production of globes is not only printing,” says the head of the Public Market. - Print - twenty percent of the whole case. Bringing the product to such a form that it can be used for a long time is not easy. Fragments must match in color and size, and meet strict strength criteria. To solve some problems, it was necessary to develop their own techniques. But it is the 3D printer that suits us more than any other technology.”
Our interlocutor admits that the ZPrinter 510 is not only expensive, but also difficult to use. At the same time, he is convinced that any thinking person understands that complex, unique equipment requires additional efforts from the user, including intellectual ones. “Developers from Z Corporation do not stand still, they offer new options for both software and equipment,” notes Alexander. “I think that with proper service support, reasonable prices for spare parts and consumables, 3D printing technology will definitely have a worthy future.”
Public Market decided not to reduce its own three-dimensional projects to globes alone. The site www.mentalauto.ru has recently started working, where users are invited to implement their tuning ideas based on computer 3D prototypes of popular car models by editing some elements of the car design directly on the site. After installing a small free 3D player, you can operate a full-fledged 3D model, use your own graphics and save the results of your work. Thus, a car enthusiast can not only enjoy a virtual three-dimensional model of his tuned iron horse, but also, using 3D printing, reproduce each tuning element to adjust and refine the three-dimensional model. After all, it is better to first experiment on plaster, and only then embody ideas in metal and plastic. Perhaps this is one of those steps towards the consumer 3D printing, which in the future will make the technology available to everyone.
CAD and graphics 6`2010
- csd
- consistent software distribution
- zprinter 510
3DNews Technologies and IT market. News printers, print servers, scanners, copiers... A new 3D printing method makes models... The most interesting in the reviews 02/04/2019 [10:48], Konstantin Khodakovsky 3D printers are becoming more and more affordable and widespread. There is a whole range of technologies for recreating a three-dimensional model in a material: this is the extrusion method by applying strips of molten plastic, and the photopolymer method using pixel-by-pixel or layer-by-layer solidification of the material, and laser powder baking, and lamination. But one way or another, all these methods are related to additive manufacturing, that is, they are associated with the sequential, layer by layer, creation of a figure. A separate group are milling machines, laser engravers and cutters. A new technology created by Californian technologists takes a completely different approach and immediately produces a solid structure by projecting light onto a container of translucent polymer resin, which hardens under the influence of radiation. "This is an exciting achievement for rapidly prototyping fairly small and transparent parts," , said chemist Joseph DeSimone of the University of North Carolina at Chapel Hill. Electrical engineer Hayden Taylor of the University of California at Berkeley explained that the printer described in Science magazine resembles a CT scan in reverse. In tomographs, an x-ray tube rotates around the patient, taking images of sections of the internal organs of the body. These projections are then used by a computer to create a three-dimensional image. The development team, on the other hand, used a 3D computer model of the object to create projections from different angles. This chemical is an ester of acrylic acid and has a tendency to polymerize: once the number of absorbed photons reaches a certain threshold, the resin molecules join in chains to form a hard, translucent plastic. The remaining liquid is then removed. Speaking about the speed of the experimental prototype, the copy of Auguste Rodin's sculpture "The Thinker" shown in the attached video, a few centimeters high, took about two minutes to print. According to Mr. Taylor, this method outperforms existing ones not only in terms of printing speed and smoother surfaces (although it doesn't seem to be doing very well in terms of rendering details), but also in the ability to print over existing objects to create a new part or kind of shell. |