Maker select 3d printer mods
Essential Mods to Upgrade Your 3D Printer (Maker Select v2)
When I first purchased my Maker Select, I already had a hefty list of mods planned before it even arrived. I spent weeks researching every ounce of information available, prepared to replace or upgrade any parts that would help improve my prints. While these machines have fantastic results right out of the box, a few changes can create even better prints that rival machines several times their cost.
In a nutshell, the Maker Select is essentially a low cost foundation that can be further improved over time. A quick trip to the hardware store is often all that it takes, where much of what you will need can be printed off that very machine! There is a wide range of part designs readily available, including everything from belt tensioners to cooling fan shrouds. We will look at the most important mods that every new owner should be made aware of, explain the reasoning for it and where to find more information.
MOSFET Board
The MOSFET Board is hands down the absolute most important upgrade for your 3D Printer. The electrical connectors which power the heated bed are not rated for the amount of electricity it consumes, where they will eventually melt and burn out. To remedy this issue, we use a MOSFET Board to bypass the underrated connectors and draw power directly from the power supply instead.
While you may be second guessing your purchase at this point, let me assure you that it is far from complicated and actually quite simple to do. My very first guide on this website covered the entire process, where I had absolutely no electrical wiring experience going into it. After having it completed, it was far from the intimidating ordeal I had pictured in my head. It costs less than $20 in parts from Amazon, can be completed in under 30 minutes and will ensure safe and happy printing in the future.
Guide: Installing a MOSFET Board (Maker Select V2)
Z-Brace Mods
The Maker Select and Wanhao Duplicator have an i3 frame design, resembling an upside down T shape. While this is widely used among many budget printers, the problem is that the vertical (Z) axis is not well supported and wobbles during print. As implied by the names, this results in backlash called “Z-wobble” and artifacts referred to as “Z-banding” which create visible lines in 3D printed objects.
The Z-Brace Mods are the answer to this problem, designed to stabilize the frame and make it more rigid. While several variations are available, the fundamental idea is to place brackets on both the vertical axis and the base of the 3D printer, affixing them together using metal rods. In doing so, the upper part of the printer cannot move freely and eliminates defects in prints.
Thingiverse: Original Z-Brace Mod
Thingiverse: Modified Z-Brace Mod
Amazon: Z-Brace Mod Kit
Rep Rap Champion’s Z-Brace Mod Kit
Maker Select V2.1 with Z-Brace Kit
Dii Cooler
Unless you are printing exclusively in ABS filament, you will see drastic improvements from better cooling. The 30mm fan included with the Maker Select is the bare minimum, only blowing enough air for relatively basic prints. When you have complex designs that require bridges or overhangs, the limitations of that little fan will quickly become apparent.
Using the Dii Cooler or a similar design, in combination with a large blower style fan, we can vastly improve the parts cooling. The differences are night and day, making this not only the cheapest but also the most effective upgrade to the overall print quality. Where the stock fan only blows air from a single side, the Dii Cooler has a 360 degree field of cooling that will ensure the plastic hardens almost immediately.
Thingiverse: Dii Cooler
Thingiverse: Thorped Cooler
Thingiverse: Cobra Cooler
Dii Cooler
Dii Cooler vs Stock Cooler
Glass Bed
The Maker Select includes two sheets of Build Tak for surface adhesion. In my initial rush of excitement and confusion, I actually stuck the spare sheet on top of the one which was already installed from the factory. While Build Tak does a relatively good job, it does start to experience wear and tear from repeat usage. Since my spare was no longer available due to beginner’s negligence, it was not long before it needed to be replaced.
There is no better option than glass when it comes to a build surface for 3D printers. It can be removed as needed, convenient when prints are stuck and difficult to break free. A wide variety of adhesives can be used on glass, eliminating problems with bed adhesion and warped prints. It also provides a solid, flat surface that can cover any potential defects in the heated bed.
Guide: Installing a Glass Bed
Removed Build Tak
Glass Bed with Thermal Pads
Belt Tensioners
These 3D printers rely entirely on belts to move both the extruder assembly and the heated bed, constantly going back and fourth with immense precision. From the factory, these belts are kept tight using small metal springs, however they do start to wear out and stretch over time. As this happens, the belts can become loose and are no longer capable of the precise movements required.
Using 3D printed belt tensioners, we can replace these weakened springs and keep the belts tight to ensure accurate transitions. While a quick fix is to simply zip tie the belts, the adjustable belt tensioners will allow for variable tension using a set screw, becoming more taut as it is tightened.
Thingiverse: Simple Belt Tensioner
X-Axis Belt Tensioner
Y-Axis Belt Tensioner
Y-Carriage Plate
The Y-Carriage Plate is the square metal base which is below your heated bed. The original plate is stamped metal which actually weakens the structural integrity and results in warping over time. Many owners begin to notice trouble leveling their beds after continuous usage, only to find that the Y-Carriage Plate has deformed and is no longer flat. When replacing mine several months after purchasing the 3D printer, I noticed the original plate was starting to bow upwards in one of the corners.
Several companies have created superior replacements, machined from materials such as aluminum, carbon fiber and laminates. These are flat, thick sheets of rigid material, built to withstand the pressure created by the bed leveling screws. Designed to be a direct swap, they are simple to install and will make bed leveling much easier.
Guide: Replacing the Y-Carriage Plate (Maker Select V2)
Melamine Laminate Plate
Z-Extension Mods
The Maker Select and Wanhao Duplicator i3 are advertised as having a vertical build volume of 180mm. While they are capable of such, they are actually only able to print 143mm without modification. The wires on top of the extruder assembly will hit the printer frame, preventing it from reaching full volume and potentially causing damage in the process.
One option is to rotate the extruder motor, where the wires will be facing the rear of the printer as opposed to the top. This does however require extending the wires to increase the length, where the Z-Extensions are generally the better alternative. They can be 3D printed and installed with ease, raising the crossbeam by 37mm to accommodate the full build volume.
Thingiverse: Z-Extensions
Z-Extensions Front
Z-Extensions Side
Micro Swiss All-Metal Hotend
While the Micro Swiss All-Metal Hotend is not exactly one of our essential mods, it is a massive upgrade in terms of printing capabilities.
The stock nozzle is lined with plastic PTFE tubing which prevents heat from prematurely melting the filament and causing clogs. The downside is that this tubing begins to deteriorate and can even become toxic at higher temperatures (exceeding 250° Celsius). While this is not a problem for basic materials such as PLA and ABS, more exotic filaments such as PETG and Nylon often print at 250° Celsius or more.
The Micro Swiss All-Metal Hotend replaces the MK10 nozzle, thermal barrier tube and cooling block (optional) with steel and aluminum components. In doing so, the plastic PTFE tubing is no longer needed, allowing for higher temperatures and more abrasive materials to be used. With a variety of exciting filaments available, the Micro Swiss All-Metal Hotend is a fantastic upgrade which opens a lot of doors for your 3D printer!
Guide: Installing the Micro Swiss All-Metal Hotend (Maker Select V2)
Original MK10 Nozzle w/ PTFE Tube
Micro Swiss All-Metal Hotend
Moving Forward with Mods
While the aforementioned mods we covered are the most essential, they don’t even scratch the surface of what’s available.
These will however make the most difference in terms of print quality, fixing the most recognizable flaws on the stock machine. The Maker Select and Duplicator i3 have always been fantastic, but a few upgrades can have it printing just as well as the Prusa MK3 and other high end brands.
If you don’t want to stop there, there are still plenty of other mods that can further enhance these 3D Printers. Some of these might include upgrading the extruder gear, perhaps replacing the linear bearings, and flashing a bootloader to use your own choice of firmware and settings.
My Maker Select Plus Upgrades and Mods | by Jacob Swanson
These are the upgrades and mods that I’ve done to my Maker Select Plus with some useful information about them. I’ll continue to update this as I do more.
These are listed in no particular order.
An aluminium Y carriage plate wont warp as much as the stock stamped steel one and it’s lighter to boot! It’ll improve quality be reducing the weight of the build plate and help to keep the bed level.
Y Carriage Plate for Wanhao Duplicator i3 or Monoprice Maker Select 3D Printers
This is second revision of Wanhao i3 / Maker Select Y carriage plate. Y carriage plate compatible with popular Wanhao…
gulfcoast-robotics.com
Borosilicate glass is pretty much guaranteed to be smooth and flat. It will get rid of many bed leveling issues.
PLA sticks like glue to PEI, so it works really well applied to the top of the glass.
Gulfcoast Robotics GlassBorosilicate Glass for Wanhao Duplicator i3 Anet A8 MP Maker Select, 4mm Thick.
100% borosilicate glass, flat, heat resistant plate, does not warp during long term use. 4mm thick - will not break…
gulfcoast-robotics.com
PEI Sheet 8.66
This is real PEI (Polyethermide) - manufactured from Ultem 1000 and has an amber color, ideal for high temperature 3D…
gulfcoast-robotics.com
Installing the ADVi3++ firmware will allow you to tweak many more settings in the printer.
andrivet/ADVi3pp-Marlin
a custom firmware for Wanhao i3 Plus printers. fork of Marlin Firmware (https://github.com/MarlinFirmware/Marlin) …
github.com
A hardened nozzle will let you print with abrasive materials without having to worry. I have the Micro-Swiss kit, so I got their nozzle too.
Micro Swiss nozzle for MK10 All Metal Hotend Kit ONLY (Plated A2 Hardened Tool Steel)
This is Micro Swiss MK10 All Metal Hotend ONLY style nozzle, it will ONLY fit our MK10 All Metal Hotend Kit. This…
store.micro-swiss.com
A Z-Brace can improve quality by add more rigidity, which can also help to print faster. I went with the Gulfcoast Robotics kit. It’s nice, simple, and strong.
Gulfcoast Robotics Z-BraceRear Mounted Z-Brace Frame Support Kit for Wanhao Duplicator i3 and Maker Select PLUS 3D Printers
This kit is our newest design that replaces previously popular PLUS 3D Printer Z-brace kit. New kit is rear mounted and…
gulfcoast-robotics. com
Replacing the spring belt tensioner with one that is not flexible can improve print quality by reducing ghosting. The momentum of the bed could lead to the spring tensioner flexing.
Example ghostingSuper Simple Belt Tensioner by berky93
Super simple belt tensioner for the Wanhao Duplicator i3 (and clones). Using this you can have easy-install and…
www.thingiverse.com
The DiiiCooler is an upgraded print cooling solution. With it, you can increase quality/speed and bridge better. The downside is that it’s a bit harder to see the nozzle.
DiiiCooler for Wanhao Duplicator i3 / Maker Select by Pawpawpaw85
The DiiiCooler is a cooler that is to be mounted around the hotend of the Wanhao Duplicator i3. It provides a 360…
www.thingiverse.com
Here’s the blower fan that I used.
At first the fan didn’t work. Apparently the fan header on this fan is backwards. It is possible to pull the pins out and reverse it, but it’s a big pain. I destroyed the connector on one of the fans I got in the process.
Printing this in PLA is doable, but it’ll warp due to the heat, which leads into the next upgrade to print in PETG.
An all metal hotend will let you print at higher temperatures. I used the Microswiss All Metal Hotend Kit. You’ll want to use this for printing the DiiiCooler with PETG so it doesn’t melt.
There’s a PTFE tube in the default hotend that will breakdown at the temperatures required to print PETG.
Note that normal nozzles will no longer work with this upgrade. If you want/need another nozzle, make sure it’s from the kit’s manufacturer or listed as compatible.
You’ll want to do a PID tune to adjust how the printer maintains a consistent temperature.
I bought a Noctua 40mm Fan from Amazon to replace the stock cooling fan. My fan was making grinding noises and having issues running at full speed. Most 40mm fans will be 12 volts, but this fan includes a silencing kit. It ends up running around 16 volts while still being quieter than the stock fan.
OctoPrint is a web application that you can use to control and print remotely.
OctoPrintPlugin can be used to print to OctoPrint using Cura. I use this Docker image for running OctoPrint.
You can use the The Universal Spool Holder and a Filament Guide to take some weight off of the gantry. It can also help if you have a spool with snagging issues.
Production of 3D printers in Europe. What blond birch trees are silent about ... / Sudo Null IT News market, with whom it is only possible (whom I did not meet - my beloved partner met), after which
decided “That's it, let's go! We are going to 3D”Being, on the one hand, a dreamy and enthusiastic person, but on the other hand, a cynical and prudent businessman, before diving headlong into the industry, it was decided to shake the pool of 3D printer manufacturers vigorously before choosing an accent for future distribution.
I won’t dwell on this stage too much, I’ll just say one thing: they were “shaking” with uncomfortable questions, meetings, real tests, weighted price comparisons - companies from the top 10 brands that occupied the media space, the low-level segment was not considered in principle due to strictly defined competence distribution groups.
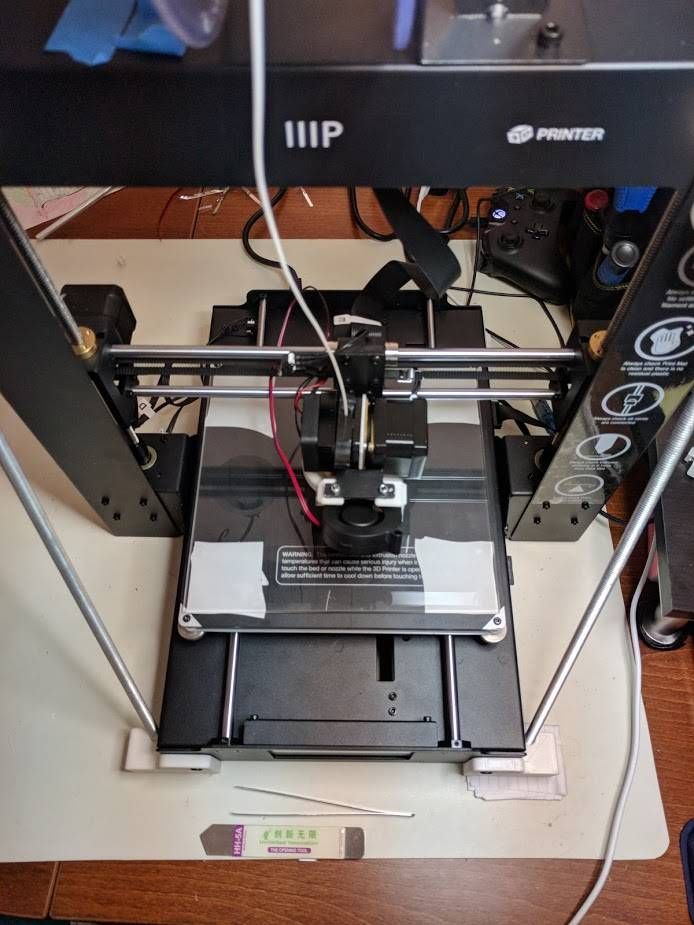
And so, in April of this year, we were thrown by a wave in the Spanish town of Navarre, where I personally saw the European level of assembly of 3D printers at factory bq , which I wanted to share with you, not forgetting the “cherry” at the end of the story.
The town where the factory of the company bq is located, producing Witbox printers, as usual for Europe (and I have been to many factories in Europe and China), is very small and expectedly romantic:
In the morning after arrival to the city - we went to the factory ourselves, the meeting was somewhat chaotic, because on the same day, more distributors from Italy and Colombia arrived at bq.
It was all the more interesting for me to see the production through the eyes of a person for whose arrival there was no time to prepare (by building the Potemkin villages according to a custom known in Rus').
What can I say, after the Chinese cold, poorly lit workshops with girls wrapping themselves in warm clothes with belongings on the desktops, the European assembly is always like oil for the soul.
Immediately striking: Space and Cleanliness
We were taken step by step through the entire production, allowing us to take general photographs without zooming in.
Below are the most interesting of them, in my humble opinion, with a few comments:
At the first stage in production, tables with guides are assembled, fixed inside the platform, and then the control electronics are fixed.
Under each printer, there is CHECK list , in which the assemblers mark the operations performed, and the intermediate testers check the operability or lack of it at a certain stage (these are white sheets inside each Witbox printer in the photo):
External electronics - installed by blue collar guys on this line. they also test this electronics:
In the next room we found FANUC Robodrill - in fact a large 3D printer, but in a non-additive manufacturing format.
Seeing it, the engineer of our company, who came to study, trembled and began to excitedly whisper in my ear that “this thing is worth more than anything that is here,” which made me worry for no apparent reason.
Our question: "What is it used for?" was shown to us on a stack of these spare parts stacked side by side.
This is a snap-box for the electronic filling of the printer, the Spaniards in bq grind it on their own:
Then followed the phrase that made me think:
“We used to print these boards on our own Witbox 3D printers, but with an increase in production it became absolutely unjustified in terms of time costs”
Guys from Russia, manufacturers of 3D printers, often boasted to me that many of the spare parts for their "gadgets" are produced on their own printers.
It can be concluded that the number of units produced is hardly large in these specific cases and can indirectly indicate a small amount of accumulated production experience.
Next to FANUC is the Laser Cutting Plotter , which makes the outer bright panels for the future printer.
Maybe I called it wrong, but for me, an office rat, such large machines, before my eyes turning huge sheets into beautifully shaped, ready-to-install external panels with a logo on board, always make a fascinating impression.
Even before the panels are installed, each printer is started to print a calibration pattern (below you will see a number of these printing Witboxes).
If the test is successful, the printer goes to packaging. At the same time, the model printed on this particular printer MUST be put into the box.
Doesn't pass the test - they make an additional adjustment to the victorious one.
Here I trembled again and for a long time fascinated looked at the bluish backlight of the print area, appreciating with peripheral vision an elegant solution for laying PLA plastic without the flip over the top, which is standard for most devices of this kind:
Printers that have passed the print test are equipped with external panels (yellow, black or white):
to play around" to our engineer, who became very close to like-minded Spanish engineers during the short time of our visit):
I liked EVERYTHING on the final packaging.
1. Double box - beautiful inner and outer shipping:
The guys from bq said that the printer in this package can withstand a fall from a height of 1 meter:
- Reel PLA - plastic (two for Witbox printer with two extruders)
— 4GB SD - card
— Additional HOT END — extruder nozzle (I almost burst into tears when I saw it, and girlishly framed the photo as a token of sincere gratitude for such attention to customers):
- Instructions and warranty card for 2 years operation
shipments to Madrid, main warehouse bq
after the mandatory palletization procedure:
In the morning - this (printed on a Witbox 3D printer, as evidenced by the inscription on the board) forklift
… will load them onto a truck bound for sunny Madrid, so that the “swallows” will then fly around the world…
Koda. Curtain.
Cherry
(which was promised above):
Why is the actual post placed in the hub Open Source ?
At the end of our trip we asked the Europeans:
Why are you, an absolutely successful IT company, second in the market in Spain in sales of smartphones and tablets, investing in the production of 3D printers?
Why are you so actively sharing information with us, investing your time, effort and money, including in the Russian market?
Are you not afraid that the #Chinese will come and eat you? Aren't you afraid that manufacturers in Russia will be able to knock out all Europeans and Americans from the 3D printer market?
Are you confident in the long term of your strategy?
The answer of Mario and Antonio from bq threw me into complete confusion:
We are NOT afraid of the Chinese.![]()
The exact scheme of the WitBox 3D printer with all the spare parts is posted on our website:
Download, do it yourself.
We are deeply convinced that this data should be available so that the entire engineering community can hot-start the printer to the ideal, and the culture of production, its level, believe us, is extremely difficult to repeat.
There is nothing to fear here.
In connection with this - to the inquisitive inhabitants of Habr POLL :
Corporate 3D printing: why haven't new devices appeared in houses and apartments?
- Technology
- Roman Arkhangelsky Author
Today, 3D printing services are focused on the B2B market. How long will this trend last?
The first 3D printing technology and printer appeared back in 1984 in the USA, at that time this method was called "stereolithography". Then, in the next decade, new technologies and installations for 3D printing began to be developed and patented in different countries. For some time, the technology was tested, fine-tuned, production costs were optimized, and in the early 2000s, 3D printers began to appear at relatively low prices. In 2009In 1999, the patent for the popular FDM printing technology was lifted, which led to the emergence of many desktop 3D printers of this type and a sharp decrease in prices, China became the main damper. By 2010, 3D printing technologies gained popularity, became accessible and understandable to ordinary users, and not to highly specialized organizations. At that time, there were big news about 3D technologies in the field of fashion, mechanical engineering and aircraft building, medicine in the media, there was a lot of noise around 3D food printers. But over time, the news about "entertaining" 3D printing has become much less, probably, manufacturers of 3D equipment and world leaders in the field of 3D printing services have realized that it is not so profitable to arrange various PR campaigns in the fields of fashion, art, food industry, aimed mainly at individuals who are not actually the main buyers. Firstly, due to the lack of proper skills for working with 3D printing. Secondly, due to not the most budgetary cost of printers and consumables, which can provide a fairly high quality. Of course, 3D printing is still used for marketing purposes, for the development and implementation of innovative products, including in light industry, for example, Adidas recently launched the production of sneakers with a sole printed on a 3D printer.
However, in general, 3D printing achievements and news have moved into a professional direction, turning to the traditional target audience: engineering, industrial and machine-building organizations, medical and pharmaceutical companies.
In Russia, the hype about 3D printing came in 2013-2014, when the technology was not fully explored and seemed quite simple. When we opened the CubicPrints.ru online 3D printing service in 2013, we faced the fact that people had little understanding of the 3D printing process. They often called us, and the dialogue went something like this: I broke a part from a coffee grinder, now I’ll come to you, will you print it in an hour? I had to patiently explain that this does not work. Getting the printer up and running first requires the development of a digital 3D model adapted for 3D printing, a process that can already take hours to days depending on complexity. Printing itself takes not 10-15 minutes, but depending on the size of the model and the selected technology, it can take up to two days.
Still, 3D printing is for organizations
As a result, it became clear that at the moment there are many barriers to expanding the B2C market, primarily in the competence of people. 3D modeling is not a trivial task, and few people have the necessary skills. The next obstacle is the ratio of technological possibilities and the cost of 3D printing. It is logical that the cheaper the material, the more restrictions on its use. Individuals usually want to order souvenir items, original gifts, complex broken household parts, etc. Such tasks usually require printing on professional 3D printers, but in this case the cost of production is higher than using budget desktop machines , since more expensive raw materials and expensive equipment maintenance are used. When buying a 3D printer for personal home use, all the same nuances arise: the presence of 3D modeling skills, the ability to maintain the printer, while the quality obtained during home printing does not always meet expectations. Our turn from B2C to B2B market happened naturally, we were contacted by the design departments of various engineering and manufacturing companies. I must say that we not only reoriented 3D printing to the B2B sphere, but also expanded our own production by adding plastic injection. As practice has shown, 3D printers are mainly used to create prototypes and foundry master models. After debugging prototypes, production of final products is usually required. In this case, it is more convenient to work with full-cycle companies, since even at the modeling stage, it is possible to think over the adaptation of products for further casting to the requirements of a particular production method. Therefore, our services have also expanded to casting, based on the needs of customers who contacted us for design development, prototype printing and were interested in the possibility of further mass production.
Based on our experience, we can say that the main customers of 3D printing are organizations that test innovative developments, manufacture various devices, as well as manufacturers of plastic products, companies from the medical sector and the military-industrial complex. According to the report of Ernst & Young, for April, 2016 the main world consumers of 3D printing are the companies producing plastic products (30.4% of the market), pharmaceutical and medical organizations (29.4%), the share of electronics manufacturers and engineering companies in total accounts for 37% of the market. At the same time, consumer goods, wholesale and retail trade occupy only 7% of the market. The Ernst & Young study included 214 companies from 12 countries that have experience with 3D printing.
Materials and machines
The most popular materials for 3D printing are plastics and metals. According to an analytical report by Ernst & Young, polymers are most often used for printing (53% of the market), in the world market, metal occupies 44%. This statistic is also confirmed in a recent report by consultants Wohlers Associates, Inc. (world leaders in 3D printing analytics), according to the Wohlers Report 2017, collected from 100 service providers, 61 industrial printer manufacturers and 19manufacturers of materials and desktop 3D printers worldwide, polymer materials account for 51% of the total turnover. Experts from the world's largest community 3dhubs found that the most popular polymer printing technology is PolyJet - this is an assessment received from both organizations and private users. According to Wohlers Report 2017, metal 3D printing accounts for 19.8%. At the same time, according to Ernst & Young, the global demand for metal printing is higher than for polymer printing, 52% versus 31%, which indicates a trend towards the development of metal printing technologies and an increase in turnover in this area. According to experts, the Russian 3D printing market accounts for only 1.5% of the global consumption of metal powders. Our own experience does not confirm the growth in demand for metal printing, the share of metal orders is less than 5% of the total. We attribute this to the limitations of this technology, including the high roughness of the resulting surface, as well as the rather high cost of consumables, which are mainly produced and shipped from abroad, which is not very profitable at the current exchange rate.
Polymers make up over 80% of our 3D printing orders.
At the same time, based on our experience, sometimes it is much more profitable for companies to resort to specialized services than to buy 3D equipment for their own use. Professional and industrial machines, which are usually used for production tasks, are quite expensive. For example, an industrial 3D printer for printing with photopolymer costs from $100,000. Typically, companies don't have enough 3D printing jobs to amortize this cost profitably. In addition, qualified specialists are needed to work with the equipment, the purchase of expensive consumables, which are simply not worked out with small print volumes. For example, CubicPrints.ru is sometimes approached by organizations that have their own household 3D printers, but either have difficulty setting it up, which is also a non-trivial task, or do not get the proper quality and go to industrial 3D printing. Our practical findings are supported by data from the Ernst & Young report: according to a survey 900 global companies, 9. 3% prefer to own 3D printers, 8.3% choose contractors. However, companies that purchased their own equipment faced the problems described above. According to Ernst & Young forecast, in 5 years the situation in the use of 3D printing will change in favor of service providers. Thus, 41.3% of the surveyed companies confirmed that they consider transferring tasks for additive manufacturing to specialized services as the most profitable, and 25.6% would prefer to keep their own fleet of 3D printers. We observe a similar trend among individuals. In our practice, there are many cases when people who are optimally suited for printing on a household printer are going to buy a personal desktop version, but having thoroughly studied all the issues, they refuse this idea. For example, there is a customer who has been printing car components for us for several years. Since usually a batch includes several different models of 10-20 pieces each, durable wear-resistant material and production in a short time are required, we quickly print such orders from ABS plastic on household 3D printers.
At first, the customer thought that it would be more profitable to have their own printer and reprint models as needed. However, after watching how our engineer chooses the optimal angle for placing the model on the desktop, and then cleans the printed parts from plastic supports, he decided that it was easier to pay for the work than to study all the details and spend time finishing the details to the final state.
Forecasts
As for the development of 3D printing in the B2C segment, I think that this is an inevitable process, however, it seems that global changes in favor of individuals should not be expected in the next few years. First, the cost of printers and materials should decrease. Second, 3D printers must overcome their current technological limitations. Thirdly, it is necessary to develop 3D modeling skills among schoolchildren and students. Now many technical universities and some schools have a 3D modeling course, and there are also various online libraries (for example, thingiverse.