Lunar regolith 3d printing
3D Printed Lunar Regolith Bricks Can Withstand the Extreme Environments in Space
3D printing news News 3D Printed Lunar Regolith Bricks Can Withstand the Extreme Environments in Space
Published on October 29, 2022 by Madeleine P.
Since the first space flight in the 1960s, humankind has dreamed of not just visiting the stars but of residing among them. Though living on the Moon or Mars might seem like science-fiction, it is actually something that is being actively worked towards by a number of organizations and 3D printing may be one of the keys to its success. And now it may be one step closer to feasibility. Researchers at the University of Central Florida have successfully created 3D printed bricks that could be used to construct bases on the Artemis Base Camp made out of lunar regolith and saltwater.
This is certainly not the first time that efforts have been made to use 3D printing for housing in space. In fact, there are a number of projects that are currently ongoing testing. This includes Redwire’s testing on the international space station to determine whether lunar regolith, or the soil and rock deposits on the surface of the Moon could be used to create habitations, NASA’s current work with AI Space Factory on a 3D printed lunar habitat and Washington State University’s research into 3D printing on Mars. However, up to this point it has been relatively hypothetical. This is one of the first projects to show that regolith bricks are able to withstand the extreme environments that are found in outer space.
Lunar regolith consists of loose rocks, dust and materials found on the surface of the Moon (photo credits: NASA)
3D Printed Lunar Regolith Bricks Able to Withstand Extremes
The study Effect of sintering temperature on microstructure and mechanical properties of molded Martian and Lunar regolith was published in a recent issue of Ceramics International and was undergone by researchers from a team led by Associate Professor Ranajay Ghosh from UCF’s Department of Mechniacal and Aersopace Engineering. The lead author is Peter Warren, a research assistant, but co-authors include Nandhini Raju, Hossein Ebrahimi, Milos Krsmanovic and aerospace engineering professor Seetha Raghavan and Jayanta Kapa. They sought to discover whether a fixed Artemis base camp on the Moon could be constructed from these 3D printed lunar regolith bricks.
To create the bricks, the team turned to binder jetting with a binding agent made out of saltwater and powder made from regolith from UCF’s Exolith Lab. Binder jetting was the perfect technology as it is uniquely suitable for ceramic-like materials that are difficult to melt with lasers. Ghosh further notes that this gives it enormous potential for regolith-based extraterrestrial manufacturing. Though the initial green parts were relatively weak, after being baked at heat of up to 1200 degrees Celsius the bricks were sufficiently strong for their purpose.
UCF Mechanical and Aerospace Engineering Associate Professor Ranajay Ghosh and graduate research assistant Peter Warren displaying the cyrlindrical bricks created using simulated lunar and Martian regolith and saltwater (photo credits: UCF)
And the results are certainly promising. The researchers found that the resulting cylindrical bricks were able to withstand pressure that was up to 250 million times the Earth’s atmosphere. This suggests that binder jetting could be used in the future for the construction of materials and structures in space. Most importantly, it demonstrates that off-world structures would be able to be built using resources found in space. By opening up this path, future missions could reduce the need to take up valuable space and weight limits by transporting building materials, making habitation much more likely.
Ghosh concludes, “This research contributes to the ongoing debate in space exploration community on finding the balance between in-situ extraterrestrial resource utilization versus material transported from Earth. The further we develop techniques that utilize the abundance of regolith, the more capability we will have in establishing and expanding base camps on the moon, Mars, and other planets in the future.” If you would like to learn more you can purchase the full study HERE
What do you think of these 3D printed lunar regolith bricks? Let us know in a comment below or on our LinkedIn, Facebook, and Twitter pages! Don’t forget to sign up for our free weekly Newsletter here, the latest 3D printing news straight to your inbox! You can also find all our videos on our YouTube channel.
*Cover Photo Credits: NASA
NASA to explore 3D printed lunar structure possibilities with Redwire Regolith Print launch
0Shares
NASA is launching a new set of scientific experiments to the International Space Station (ISS), including a study from mission-critical space systems specialist Redwire that will determine the feasibility of 3D printing regolith for the on-demand construction of lunar structures.
The Redwire Regolith Print (RRP) study will head to the ISS on Northrop Grumman’s Cygnus spacecraft, targeted for launch on August 10th just before 6pm EDT. At a media teleconference hosted by NASA in the lead-up to the launch, Redwire’s Chief Technology Officer Michael Snyder explained what the firm hopes to achieve with the project, and what it could mean for future space exploration missions.
“The Redwire Regolith Print project is a tech demo of on-orbit additive manufacturing using regolith simulating feedstock material,” he said. “This represents a critical step in developing sustainable manufacturing capabilities for lunar surfaces that will ultimately establish a permanent human presence off-earth by utilizing available resources with adaptive systems. So this is really exciting for the future and hopefully, something like this gets eventually deployed to the moon.”
The Redwire Regolith Print study
National space agencies like NASA are continuing to seek a permanent presence on the moon and Mars, and using raw resources available on-site to build structures and habitats could reduce how much material future missions need to bring from Earth. As a result, this could significantly reduce the launch mass and cost of future missions and provide a more sustainable method of constructing housing and other structures on planetary bodies.
Once installed on the ISS, the RRP project will seek to demonstrate the potential for 3D printing with regolith feedstock material in microgravity using the Made In Space additive manufacturing device currently housed aboard the station. Regolith is the loose rock and soil found on the surfaces of planetary bodies such as the Moon, and the study hopes to demonstrate the feasibility of 3D printing the material to construct on-demand habitats on future space exploration missions.
During the project, Redwire will use a feedstock made up of metal oxides and a binder that simulates regolith to 3D print multiple plates that, once brought back to earth, will be formed to the exact specifications of the required test specimens. Printing the samples as plates will also enable Redwire to produce as many samples as possible for the destructive testing phase. The regolith-simulating samples will be printed using an extrusion-based 3D printing technique similar to fused deposition.
“For this demonstration, an initial set of three specimens will be produced on the ISS,” explained Snyder. “That will be done by installing newly developed manufacturing components into Redwire’s existing additive manufacturing facility. Once those components or specimens are returned, NASA will test the material properties of the prints by performing destructive tests.”
The Redwire Regolith Print facility suite, consisting of Redwire’s Additive Manufacturing Facility, and the print heads, plates and lunar regolith simulant feedstock that will be launching to the International Space Station.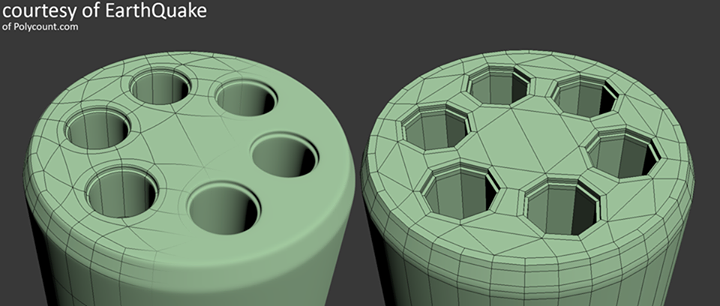
The hardware for the Made In Space additive manufacturing device was developed in partnership with NASA’s Marshall Space Flight Center and was created to identify and test the methodology for regular manufacturing in the US on a lunar surface to support NASA’s Artemis program. A key phase of NASA’s Artemis plan is to create lunar infrastructures for future exploration missions to the surface, that will be critical to humanity’s sustainable presence on the moon and beyond, Snyder said.
“The payload is practically a manufacturing head that is inserted into our existing additive manufacturing facility on the ISS,” he added. “Since 2016, we have produced over 200 tools for it so this is basically a new deposition head and a new deposition plate that we will be printing on. We’re really excited about this because it’s the first time testing a new manufacturing technique in microgravity.”
Redwire has been working with NASA’s Marshall Space Flight Center for some time on the project, having taken part in the first round of the 3D Printed Habitat Centennial Challenge. The multi-phase challenge was aimed to advance the construction technology needed to create sustainable housing solutions for Earth and beyond, and was the origin of Redwire’s regolith-simulating material.
Once the 3D printed regolith samples are returned to Earth, they will be analyzed and compared with samples produced in a ground facility prior to launch. Comparing the samples will help Redwire to validate that the printing process works at levels of gravity lower than that on Earth.
“The capability has already been proven on Earth, but requires further validation in the space environment,” said Snyder. “Operating both on the ground and in microgravity will increase the competence in the process for use on planetary bodies with gravity fields, including the Moon and Mars. The regolith print demonstration will be the first-ever test of manufacturing regolith simulate feedstock in space.”
The RRP study will launch on Northrop Grumman’s 16th commercial resupply services mission on August 10th from NASA’s Wallops Flight Facility in Virginia. Other experiments and supplies also being launched to the ISS include engineered tissue to study muscle loss, slime mold, a flow boiling and condensation experiment, and thermal protection systems, among other things.
3D printing for off-world structures
Additive manufacturing is garnering increasing interest from multiple national space agencies as they seek to establish a permanent presence on the moon.
For instance, Texas-based construction firm ICON has gained a NASA contract for the development of a full-scale prototype off-world 3D printer. As part of the project, the team is working on fabricating space-faring structures using only lunar regolith.
3D printing with lunar regolith in zero gravity has also been explored by scientists from the Technical University of Braunschweig and Laser Zentrum Hannover, in a project titled ‘MOONRISE’. The scientists devised a customized laser that, with further R&D, could form the basis of a flight-ready lunar rover enabling astronauts to create economical long-term structures on the moon.
Elsewhere, Russian space agency Roscosmos has confirmed its support for long-term missions by 3D printing structures made from on-site material, and China’s National Space Administration has revealed its own plans to 3D print a base on the Moon.
Redwire’s Howie Schulman, project lead, packs the Redwire Regolith Print printing plate ahead of delivery to NASA for launch. Photo via Redwire.Nominations for the 2021 3D Printing Industry Awards are now open, have your say who is leading the industry now.
Subscribe to the 3D Printing Industry newsletter for the latest news in additive manufacturing. You can also stay connected by following us on Twitter and liking us on Facebook.
Looking for a career in additive manufacturing? Visit 3D Printing Jobs for a selection of roles in the industry.
Subscribe to our YouTube channel for the latest 3D printing video shorts, reviews and webinar replays.
Featured image shows the Redwire Regolith Print facility suite, consisting of Redwire’s Additive Manufacturing Facility, and the print heads, plates and lunar regolith simulant feedstock that will be launching to the International Space Station. Photo via Redwire.
Tags China National Space Administration Cygnus spacecraft icon International Space Station Laser Zentrum Hannover Made in Space Michael Snyder MOONRISE Nasa Nasa Artemis NASA centennial challenge NASA Marshall Space Flight Center Northrop Grumman Redwire Redwire Regolith Print Roscosmos Technical University of Braunschweig
Hayley Everett
Hayley is a Technology Journalist for 3DPI and has a background in B2B publications spanning manufacturing, tools and cycling. Writing news and features, she holds a keen interest in emerging technologies which are impacting the world we live in.
3D printing as a basis for the colonization of the Moon
News
Chugunov and professors Iskander Akhatov and Igor Shishkovsky spoke about the possibility of using additive technologies to support future missions to explore the moon in their review published in the journal Acta Astronautica.
The scientists' article contains a comprehensive description of the properties of the lunar soil (regolith) and its imitators - mineralogy, morphology and chemical composition in light of the use of this natural material as a raw material for 3D printing on the lunar surface. The authors analyzed the applicability of various 3D printing methods presented in the literature, including selective sintering of lunar soil with laser, microwave and concentrated solar radiation for the construction of infrastructure for future habitable lunar stations. Among the main factors for analysis, the authors chose the possibility of adapting additive manufacturing methods to lunar gravity, energy consumption, technology scalability and autonomy of application.
“3D printing technologies will form the basis for creating the necessary infrastructure for lunar exploration, providing future astronauts with the protection of habitation modules, landing sites, necessary tools and spare parts, using local resources.” He believes that “there is no one universal 3D printing method suitable for solving all these problems. It would be advisable to develop a strategy for using a whole range of different 3D printing methods, choosing the most suitable approaches for specific purposes,” says Maxim Isachenkov.
The team of authors hope that the published review will help researchers working in this field to find the most promising directions for further research and development, as well as attract the attention of scientists and engineers working in related fields.
Now a team of scientists led by Professor Shishkovsky has moved from the analysis of foreign developments in this area and is conducting their own research. The laboratory of additive technologies at the CDMM Center at Skoltech launched work on the applicability of various additive technologies for 3D printing of lunar regolith. The scientists focused on stereolithographic printing methods, which make it possible to obtain high-strength precision ceramic products. First samples (pictured) obtained at the Skoltech Additive Manufacturing Laboratory from a lunar soil simulator developed by NASA's Center for the Study of the Lunar Surface and Asteroids (CLASS) showed the fundamental possibility of such an approach.
From left to right: lunar regolith simulator, paste obtained from it and samples printed by stereolithography
The Skoltech team plans to produce more complex functional products, up to the construction of residential blocks, conduct mechanical tests and adapt such technologies for autonomous operation in lunar gravity.
Press release
Do you have interesting news? Share your developments with us, and we will tell the whole world about them! We are waiting for your ideas at news@3Dtoday. ru
Space Moon Skoltech regolith
Subscribe to the author
Subscribe
Don't want
5
New 3D-printed lunar regolith bricks can withstand 250 million atmospheres of pressure
Scientists are constantly coming up with new methods to build habitats on the moon and beyond
03 As part of its Artemis lunar program, NASA has asked scientists to develop new methods for building lunar bases that can withstand the harsh conditions of our moon.
Thanks to experiments carried out by specialists from the University of Central Florida, future lunar astronauts will be able to use bricks from lunar regolith and salt water to build bases. This was reported in a statement by the press service of the university.
Moon outpost colony. 300ad/iStock
Ranajay Ghosh, faculty member of the Department of Mechanical and Aerospace Engineering, UCF, and colleagues have found that 3D printed bricks from lunar regolith - dust and loose rock from the moon's surface - can withstand the moon's extreme conditions. The results of the study were detailed in a recent issue of Ceramics International.
In their design, the team combined 3D printing and Binder Jetting, an additive manufacturing process in which a liquid binder is placed on top of a layer of solid particles. "The Binder Jetting technique is ideal for refractory materials that are difficult to laser melt," says Ghose. "Therefore, this technology has a high potential for the sustainable production of regolith-based parts, components and building structures."
In their Binder Jetting experiment, the researchers used salt water as a binder, with powder acting as lunar regolith.
Ranajay Ghose and Peter Warren demonstrate space bricks
Regolith and human blood could form the basis for future space habitats
First, scientists printed raw blanks, which were then fired in a kiln at temperatures up to 1200 °C. This made it possible to manufacture products that can withstand pressures 250 million times higher than Earth's atmospheric pressure.
The team's work paves the way for future BJT crewed flights in space, Ghosh said. In addition, the results of the study show that bricks can be made in space from readily available materials. This is an extremely important discovery, given the fact that transporting a huge amount of building materials to the moon would be prohibitively expensive.
"The results of this experiment are an important argument in the ongoing debate about finding a balance between using extraterrestrial resources in situ and transporting materials from Earth," says Ghose. "The longer we improve technologies that use regolith, the more opportunities we will have to build and deploy outports on the Moon, Mars and other planets in the solar system."
Last year, scientists at the University of Manchester proposed using the blood and urine of astronauts as a binder for future habitation on Mars.