Japan 3d printed house
Serendix Partners 3D prints spherical home in affordable, futuristic living first
0Shares
Japanese construction start-up Serendix Partners has managed to 3D print a futuristic spherical house from scratch in less than 24 hours, according to a Japan Today report.
Measuring just 107.6 square feet across, the tiny home is by no means roomy, but thanks to its 20,000-kilo frame, it’s sufficiently robust to serve as a permanent living space. In fact, the firm says its uniquely-styled abode is so tough and quick to build, that it meets Japanese earthquake and European insulation standards, thus it can safely be used for everything from vacationing to emergency housing.
“The sphere has a strong physical structure,” explain the Serendix Partners team on their website. “It can be used in various environments, [including as] a house that protects families from natural disasters. Using a 3D printer and advanced robotics, we are working on a design that only works with robots, and uses as little human hand [input] as possible. ”
Serendix’s spherical living plans
Working closely with architect Masayuki Sono, Serendix Partners specializes in using a combination of 3D printing and advanced robotics to build unique, low-cost architecture. The company may have been established in 2019, but Sono’s work in the field long predates its existence, and one of his earlier housing designs even won the 2015 installment of NASA’s esteemed Habitat Challenge.
Since then, however, Sono has sought to take his vision for futuristic housing away from the aerospace sector and into the mainstream, by designing tiny lodgings that can be bought for as little as $26,090. Known only as ‘Spheres,’ these homes are built to feature the lowest plausible outer surface area, so that they require the least possible material, keeping both their costs and lead times to a minimum.
While Serendix Partners has alluded to working with others in the development of its living pods before, it hasn’t revealed their identity. That being said, the firm has disclosed that as part of its R&D, it is “developing new functional materials,” with an emphasis on strength, durability, insulation, heat-resistance and aesthetics, and this now appears to have culminated in Sono’s design being put into practice.
Building a home in less than a day
Serendix Partners’ rapid build took place at one of residential construction firm Hyakunen Jutaku’s factories, in the Japanese city of Komaki. Working with (again) unspecified ‘overseas partners,’ the firm was reportedly able to 3D print a 20-metric ton reinforced concrete frame for the house in pieces, before assembling them into the finished article on the clock, taking just three hours to do so.
Overall, the full build took 23 hours and 12 minutes to complete, and while it’s not immediately clear whether the company was able to finish the Sphere’s interiors in that time, or if it just created an outer shell, this is still an impressive feat in itself.
When it comes to automation, Serendix Partners has made some bold claims in the past about the minimal need for ‘human hands’ within its housing construction process. Given the rapid pace at which the firm was able to wrap-up its build though, it appears this was vital to the project’s success, even if it did have to apply paint to the Sphere’s exterior manually, a step it intends to mechanize in future.
Moving forwards, it’s said that the company anticipates being able to reduce the lead times of its homes even more, via fine-tuning, technological advancements and further automation. In terms of its initial builds, Serendix Partners is now expected to sell them via its consortium of collaborators, after which it predicts they’ll be used for either camping, vacationing in or as shelters in disaster zones.
A render of MASK Architects’ 3D printed houses within the proposed Madre Natura development. Image via MASK Architects.Turning 3D printed buildings into art
While 3D printing hasn’t quite managed to crack the mainstream construction sector just yet, it has already been deployed to realize some pretty innovative design ideas. During September 2021, MASK Architects unveiled plans to erect a community of steel 3D printed modular houses in the city of Orani, featuring heart-shaped designs set to be made possible by its ‘EXOSTEEL’ construction system.
Earlier last year, in January, WASP also finished building its 3D printed ‘TECLA’ eco-habitat, a carbon-neutral structure created using locally-sourced, recyclable materials. Developed in response to the growing climate emergency, the house was erected over the course of around 18 months, with the aim of establishing a new sustainable home-building model.
Elsewhere, Simulaa has even experimented with 3D printing structures from organic matter, by building a fungi-based ‘Burlasite’ display that’s deliberately designed to decompose. The slow disintegration of the artistic piece, which won top prize at last year’s Tallinn Architecture Biennale, is meant to be thought-provoking and signify the slow passage of time.
To stay up to date with the latest 3D printing news, don’t forget to subscribe to the 3D Printing Industry newsletter or follow us on Twitter or liking our page on Facebook.
For a deeper dive into additive manufacturing, you can now subscribe to our Youtube channel, featuring discussion, debriefs, and shots of 3D printing in-action.
Are you looking for a job in the additive manufacturing industry? Visit 3D Printing Jobs for a selection of roles in the industry.
Featured image shows Serendix Partners’ recently-3D printed ‘Sphere.’ Photo via Japan Today.
Tags Masayuki Sono MASK Architects Nasa Serendix Partners Simulaa Tallinn Architecture Biennale wasp
Paul Hanaphy
Paul is a history and journalism graduate with a passion for finding the latest scoop in technology news.
A Spherical Home Was 3D Printed in Less than 24 Hours
Published on March 15, 2022 by Madeleine P.
A house built in less than 24 hours and for less than $25,500: fiction or reality? That was the crazy challenge taken up by the company Serendix, which 3D printed this small spherical structure in precisely 23 hours and 12 minutes in Japan. Though the company revealed a first prototype in 2015 – which had moreover earned it first place in the 3D Printed Habitat Challenge organized by NASA – it has now achieved its goal with this concrete sphere of 20 tons, resistant to weather. Though it only has a modest surface area, only 10 square meters, the architect behind the concept imagined the structure to be used as transportable and meet emergency housing needs.
The promise of 3D printing in the construction industry has many dreaming: players are banking on complex shapes, dramatically reduced lead times, and less labor intensive work for workers. But it’s sometimes difficult to tell the difference. But can we really rely on 3D technologies to build our future homes? How sustainable is such a construction method? Is it a “wow effect” rather than a real innovation? In any case, some machine manufacturers are revealing a number of innovative projects or are showing strong growth, such as the American ICON, which raised $207 million last year. And on the Asian continent, the market is moving as shown by the project of the firm Serendix.
Layer by layer, the concrete was deposited to form the walls of this structure (photo credits: Serendix)
It was in 2020 that the firm filed patents for this 3D printed sphere concept. At the time, the idea was to propose a housing without frame, quick to build and accessible, all able to resist earthquakes and typhoons particularly numerous and severe in Japan. The objective was to provide emergency housing in times of crisis. Two years later, the project finally came to life; Serendix revealed a 3D printed construction, the first in the country.
Don’t get me wrong, this is not a conventional house – the interior structure here is 10 square meters and features a 20-ton concrete frame. This small area means that it is not subject to Japanese building regulations. The walls would be reinforced with ribs to insulate the sphere and meet the seismic performance of the country’s standards.
The assembly would have taken only 3 hours (photo credits: Serendix)
It is not known which concrete extrusion machine was used, only that the final assembly took only three hours. In total, with the creation of the openings and the waterproofing phase, it took only 23 hours and 12 minutes before the structure was functional. An incredible feat in the field!
What do you think of this 3D printed spherical home? Let us know in a comment below or on our LinkedIn, Facebook, and Twitter pages! Don’t forget to sign up for our free weekly Newsletter here, the latest 3D printing news straight to your inbox! You can also find all our videos on our YouTube channel.
The Japanese created a huge Delta 3D printer 4 meters high
Archive
from Asia. The Chinese have become one of the main developers of the most unique 3D printers. They tried to be one step ahead of the world by building their 3D printed houses, designing Chinese fighter jets with 3D printers, and building a 40 x 40 x 40 foot 3D printer capable of printing with graphene.
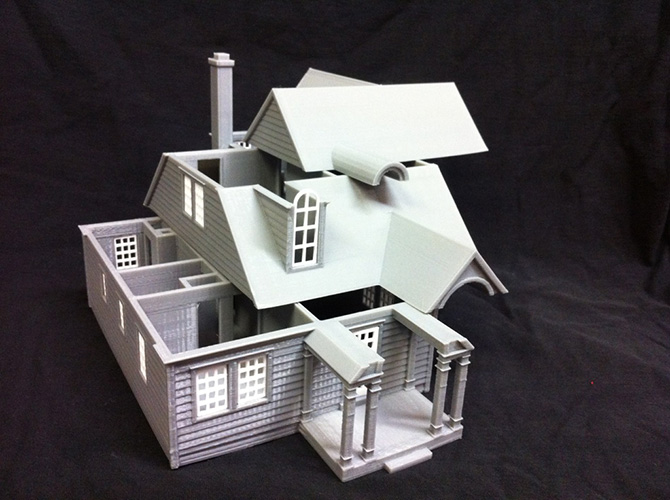
But that may change soon. A company called Genkei, which has been developing personal 3D printers in Japan for quite some time, has developed a huge 4m Delta 3D printer with students from the Tokyo University of Art and Design. This printer will be on display at the Tokyo National University of Fine Arts and the Museum of Music, as part of an exhibition running from Saturday, July 19th to Friday, August 8th. The exhibition is called "Materialization II" (マテリアライジング展Ⅱ). nine0003
The team is currently assembling this giant printer in the museum. They plan to install a working extruder within this week. “In 3-5 days we will run it on idle, and if everything goes well, we hope to have a test print in a week,” said Kato Hironao, one of the developers of the project.
As far as we know, this is the largest 3D printer ever built by Delta. At least that's what the company that created it says. Delta 3D printers are based on the design of Delta robots. Delta robots were developed in 1980 with the aim of automating some tasks in the production of various products. Recently, 3D printer manufacturers have taken this idea and applied it to today's 3D printing technology.
Although most FDM 3D printers today use spools of plastic filaments as "ink", Genkei decided to take a different path with this 3D printer.
“I would like to use a pelletized extruder in production if we have orders, but this printer will use a wider nozzle for normal PLA filament,” Kato explained. nine0026
If you watch the video below (courtesy of Genkei), you can see that the printer moves pretty well. There is no reason to believe that he will not print after mounting the extruder later this week. But you may also notice that the printer movements are somewhat slow. Most likely, printing an object of considerable size will take quite a long time.
What do you think about it? Share your thoughts on this in the comments to this article.
Watch the video and photos of the giant printer below:
The article was prepared for 3DToday.ru
Subscribe to the author
Subscribe
Don't want
Print on the printer ... home - News
What does it cost us to build a house? In modern realities, this is not at all difficult, it is enough to use a 3D printer. 3D printing is used in many areas of life, and construction is no exception. Thanks to the new technology, materials are saved, the configurations and shapes of the building become more diverse. In the next selection, information and educational resource ARCHITIME talked about the projects already implemented using 3D printing and the most interesting concepts that, it is possible, will become part of our everyday life tomorrow.
Pod Skyscraper. Tokyo, Japan
The author of the concept, Malaysian architect Hasif Rafiei, came up with an endless skyscraper: as soon as a new tenant wants to settle in the house, another residential module printed on a 3D printer will be built into the structure.
The building project is a frame with empty cells, where residential modules are integrated. The printing apparatus will be installed on the upper floors, and as the building grows, the printing system will rise higher and higher. Once the module is ready, the crane will place it in an empty cell. Residents will be able to choose the configuration of the modules and their design, and annoying or damaged blocks can be replaced or repaired. According to the architect, Pod Skyscraper will help improve the housing market in Japan. This concept with a modular system will allow you to complete the construction of housing as it is in demand. nine0003
3D printed houses for the farming community. Latin America
Fuseproject founder Yves Behar has teamed up with homebuilder ICON to help tackle the homeless problem in Latin America. The authors of the technology proposed using 3D printing to quickly create affordable and high-quality housing for families living below the poverty line.
The modules will be interlocked with a common kitchen, dining room and housekeeping space. All interior elements will also be 3D printed. The project, according to the team of architects, can become a model for the production of high-quality housing, which will help eliminate the problem of homelessness for people around the world. nine0003
Gaia 3D printed house. Mass Lombardo, Italy
Italian 3D printing technology developer WASP has built a house demonstrating the ability of the modular 3D printer Crane Wasp to create houses from biodegradable materials in various formats and sizes. Gaia is the result of a limited and optimized use of agricultural resources, which, thanks to technology, has been transformed into a biodegradable residential building with minimal environmental impact. The 30 sq.m Gaia house is printed using a mixture of soil taken from the surrounding area and waste from rice production - chopped straw and husks. If the building is not maintained, it can turn into soil.
nine0003
Project Milestone. Eindhoven, The Netherlands
The Eindhoven University of Technology, together with local architecture studio Houben & Van Mierlo Architecten, are planning to create the world's first commercial 3D printed housing project available for rent. The houses will have curved walls with balconies and deep-set windows and doors. Each house will be printed using a specially formulated low-cement concrete mix. Architects believe that 3D printing allows for a wider variety of shapes than traditional building methods. 3D printing may evolve to the point where computerized software will help people design and build their own homes, literally at the touch of a button. nine0003
SOM-designed pavilion. US
Architecture firm SOM and the US Department of Energy's Oak Ridge National Laboratory have created the largest 3D printed polymer structure, the curved pavilion. A closed battery system links it to an Oak Ridge-designed vehicle that was made using the same technology.
The project is designed as a prototype for the Additive Manufacturing Integrated Energy (AMIE) initiative, which aims to promote new ways of generating, storing and using electricity. The building envelope consists of 80% opaque panels and 20% glazing. Solar panels are integrated into the roof, feeding a battery under the building that powers the structure in the evening. The 3D printed car generates its own energy using a hybrid electric system. Both the pavilion and the vehicle share energy with each other through a wireless system in which the energy is transmitted through electromagnetic fields and then captured and distributed by a receiving device. The authors of the original idea noted that the project pioneered two-way, wireless power exchange between a 3D printed vehicle, a power grid, and photovoltaics embedded in a structure. nine0003
Curve Appeal. Chicago, USA
A team of architects proposed a design for a house made of 3D plastic, carbon fiber and glass.
The Curve Appeal project includes a curved, arcuate structure consisting of outer panels and an inner core. The area of the houses will reach from 56 to 74 square meters: this space will include a kitchen, a bathroom, a living room and one bedroom.
Mobile Europe. Amsterdam, The Netherlands nine0003
Dus Architects combined 3D-printed bioplastics and resilient dense fabric to create a sculptural façade for the building that hosted the European Union meetings for half a year in 2016. The architects have developed a special bio-based plastic made from linseed oil. The advantage of this material is not only that it is created from plants, but also that it can be recycled - crushed and reused in printing.
Dubai Future Foundation office. Dubai, UAE
The UAE has completed the world's first 3D printed office building project. The new facility is located on the territory of the Emirates Towers complex. The futuristic building was printed on a huge 3D printer by extruding a cement mixture layer by layer.
Small mobile 3D printers were also involved. The total area of the "office of the future", consisting of several small buildings located side by side, is 250 sq.m. It took just over two weeks to build and finish. nine0003
Salt printed house
The project is based on the fusion of traditional methods and 3D printing technology using salt and special cement. On the outside, the 3D printed house is made from a reinforced cementitious polymer, a stronger and harder material that, unlike conventional concrete, is more resistant to various impacts. Buildings built from such material have a small mass. Walls can be processed with a grinder, machine tool, sandblasting equipment, they can be made matte or glossy. The rooms will be placed in transparent 3D structures called "SALTYGLOO" in the form of vessels made from salt polymers - strong, light, cheap and translucent. nine0003
And in conclusion - an unusual project for the restoration of Notre Dame de Paris.
Paris, France
Immediately after the fire at Notre Dame Cathedral in Paris, numerous restoration projects began to appear. The authors of one of the ideas - employees of the Dutch company Concr3De - proposed a way to combine old materials with new technologies. Concr3De has already made a 3D model of the Strix, one of the most famous Notre Dame gargoyles, which appeared on the roof of the cathedral during the 19th century restoration. The statue was made from a mixture of materials taken from the ashes of the temple, and the process of its creation took less than a day. Concr3De proposes to use the original material of the damaged building during its reconstruction and to make all the lost stone elements of the cathedral on a 3D printer. The company is confident that the copies will not differ from the originals and will withstand any climatic vagaries. Even limestone damaged by the high temperatures of the flames could be used in the restoration process, the authors of the project believe.
![]()
Learn more