Inconel 3d printer cost
Inconel 718 3D Printing | Get Custom Metal 3D Prints Fast
Back
-
Materials
Materials by Service
Injection MoldingCNC Machining3D PrintingSheet Metal
Materials by Type
PlasticsMetalsElastomers
Related Links
Customer Supplied ResinsColors
Injection Molding Material Alternatives Guide
Struggling with thermoplastic material shortages? We created a detailed guide to resin substitutes for ABS, PC, PP, and other commonly molded thermoplastics.
Download
-
Resources
Design Tips Guides and Trend Reports Case Studies Design Aids Webinars and Trade Shows
Blog Videos FAQs Educators and Students Glossary
Industries Medical Aerospace Automotive Consumer Electronics Industrial Equipment
-
About Us
Who We Are Why Protolabs? Research and Development Cool Idea Award Partnerships Sustainability and Social Impact
Careers Investors Locations Press Procurement
Contact Us
Proto Labs, Inc.
5540 Pioneer Creek Dr.
Maple Plain, MN 55359
United StatesP: 877.479.3680
F: 763.479.2679
E: [email protected]Best-in-Class Online Quoting
After uploading your part design, you'll receive an online quote that includes manufacturing analysis to help improve part manufacturability. Within your quote, you can also adjust quantity and material and see price changes in real-time.
Learn More
Get a QuoteSign In
GET A QUOTE
Inconel is a high strength, corrosion resistant nickel chromium superalloy ideal for parts that will experience extreme temperatures and mechanical loading. Final parts built in Inconel 718 receive stress relief application. Solution and aging per AMS 5663 is also available to increase tensile strength and hardness.
Primary Benefits
- Oxidation and corrosion resistance
- High performance tensile, fatigue, creep, and rupture strength
- Available in large format with part sizes up to 31.
5” x 15.7” x 19.7” (800mm x 400mm x 500mm)
Inconel Material Properties
- US
- Metric
Applications for 3D-Printed Inconel
Inconel's corrosion resistance makes it frequently used for components like:
- Jet engine components
- Gas turbines
- Parts in cryogenic conditions
- Vessels
- Pumps
- Valves
- Piping
- Propeller blades
- Tubing, fittings
- Auxiliary propulsion motors
Related Resources
Inconel 718: A Workhorse Material for Additive Manufacturing
Inconel 718 is a go-to material for additive manufacturing of metal parts.
Read Blog
Combining Part Assemblies with Additive Manufacturing to Reduce Cost and Increase Performance
How to find the right opportunities to consolidate multi-part assemblies into single components with industrial 3D printing
Read White Paper
Post-Processing for Metal 3D Printing
Learn how to improve dimensional accuracy, surface roughness, and mechanical properties on metal parts with high-requirement applications.
Read Design Tip
Designing for Direct Metal Laser Sintering
Direct metal laser sintering (DMLS) produces complex, durable, lightweight metal parts. Depending on the design, DMLS can be a reliable way to manufacture metal parts.
Read Design Tip
Best metal 3D printers in 2022: comprehensive overview
What is the best metal 3D printer in 2022?
Over the past few years, there has been a surge in both supply and demand for metal 3D printers.
Manufacturers are launching metal additive manufacturing machines that are faster, easier to use, and more powerful with an increasing number of compatible metals.
Many businesses are adopting these 3D metal printing technologies to produce cost-effective metal parts and prototypes, benefiting as well from increased freedom of design linked to additive manufacturing. They are suitable for a variety of industries such as aerospace, automotive, health, engineering, and more.
Although metal 3D printer prices have been slowly and slightly decreasing, these machines are still relatively expensive acquisitions, mostly ranging from $80K to almost $1M.
With our metal 3D printer selection, we aim to provide a comprehensive overview of what’s available from well-established and distributed brands, at various price points, and with different metal 3D printing technologies.
The best metal 3D printers in 2022
Brand | Product | Build size | Country | Price Approximate starting prices based on supplier-provided information and public data. Prices may vary by region, over time and do not include additional products or services (taxes, shipping, accessories, training, installation, …). | |
---|---|---|---|---|---|
Markforged | Metal X (Gen 2) | 300 × 220 × 180 mm11.81 × 8.66 × 7.09 in | United States | $ 99,500125 000 €88,260 £14,831,072 ¥ | Quote |
Xact Metal | XM200C | 127 × 127 × 127 mm5 × 5 × 5 in | United States | $ 110,000100 000 €97,574 £16,396,160 ¥ | Quote |
Pollen AM | Pam Series MC | ⌀ 300 x 300 mm | – | $ 140,000135 000 €124,186 £20,867,840 ¥ | Quote |
TRUMPF | TruPrint 1000 | 100 × 100 × 100 mm3.![]() | – | $ 170,000170 000 €150,797 £25,339,520 ¥ | Quote |
3D Systems This brand is a certified partner from our network. | DMP Flex 100 | 100 × 100 × 80 mm3.94 × 3.94 × 3.15 in | – | $ 245,000245 000 €217,325 £36,518,720 ¥ | Quote |
EOS | EOS M 100 | 100 × 100 × 95 mm3.94 × 3.94 × 3.74 in | Germany | $ 350,000350 000 €310,464 £52,169,600 ¥ | Quote |
XJet | Carmel 700M | 501 × 140 × 200 mm19.72 × 5.51 × 7.87 in | – | $ 599,000599 000 €531,337 £89,284,544 ¥ | Quote |
Desktop Metal | Production System P-1 | 200 × 100 × 40 mm7.87 × 3.94 × 1.57 in | United States | upon request | Quote |
Desktop Metal | Studio 2 | 300 × 200 × 200 mm11.81 × 7.87 × 7.87 in | United States | upon request | Quote |
Digital Metal | DM P2500 | 203 × 180 × 69 mm7.![]() | – | upon request | Quote |
Formalloy | L-Series | 1000 × 1000 × 1000 mm39.37 × 39.37 × 39.37 in | United States | upon request | Quote |
GE Additive | Arcam EBM Spectra L | ⌀ 350 x 430 mm | United States | upon request | Quote |
GE Additive | M2 Series 5 | 250 × 250 × 350 mm9.84 × 9.84 × 13.78 in | – | upon request | Quote |
Renishaw | RenAM 500E | 245 × 245 × 335 mm9.65 × 9.65 × 13.19 in | – | upon request | Quote |
SLM Solutions | SLM 125 | 125 × 125 × 75 mm4.92 × 4.92 × 2.95 in | Germany | upon request | Quote |
SPEE3D | LIGHTSPEE3D | 300 × 300 × 300 mm11.81 × 11.81 × 11.81 in | – | upon request | Quote |
TRIDITIVE | AMCELL | ⌀ 300 x 350 mm | Spain | upon request | Quote |
Velo3D | Sapphire | ⌀ 315 x 1000 mm | – | upon request | Quote |
Expand to see more specs
Technology: The technologies listed above are main categories of metal 3D printing technologies. Most manufacturers have their own branded technologies, which fall into the main categories that are listed in the table.
The products in the table are ranked by price (low to high).
Brand | Product | Technology | Build size | Country | Price Approximate starting prices based on supplier-provided information and public data. Prices may vary by region, over time and do not include additional products or services (taxes, shipping, accessories, training, installation, …). | |
---|---|---|---|---|---|---|
Markforged | Metal X (Gen 2) | Extrusion | 300 × 220 × 180 mm11.81 × 8.66 × 7.09 in | United States | $ 99,500125 000 €88,260 £14,831,072 ¥ | Get a quote |
Xact Metal | XM200C | SLM/DMLS | 127 × 127 × 127 mm5 × 5 × 5 in | United States | $ 110,000100 000 €97,574 £16,396,160 ¥ | Get a quote |
Pollen AM | Pam Series MC | Extrusion | ⌀ 300 x 300 mm | – | $ 140,000135 000 €124,186 £20,867,840 ¥ | Get a quote |
TRUMPF | TruPrint 1000 | SLM/DMLS | 100 × 100 × 100 mm3.![]() | – | $ 170,000170 000 €150,797 £25,339,520 ¥ | Get a quote |
3D Systems This brand is a certified partner from our network. | DMP Flex 100 | SLM/DMLS | 100 × 100 × 80 mm3.94 × 3.94 × 3.15 in | – | $ 245,000245 000 €217,325 £36,518,720 ¥ | Get a quote |
EOS | EOS M 100 | SLM/DMLS | 100 × 100 × 95 mm3.94 × 3.94 × 3.74 in | Germany | $ 350,000350 000 €310,464 £52,169,600 ¥ | Get a quote |
XJet | Carmel 700M | Material Jetting | 501 × 140 × 200 mm19.72 × 5.51 × 7.87 in | – | $ 599,000599 000 €531,337 £89,284,544 ¥ | Get a quote |
Desktop Metal | Production System P-1 | Binder Jetting | 200 × 100 × 40 mm7.87 × 3.94 × 1.57 in | United States | upon request | Get a quote |
Desktop Metal | Studio 2 | Extrusion | 300 × 200 × 200 mm11.![]() | United States | upon request | Get a quote |
Digital Metal | DM P2500 | Material Jetting | 203 × 180 × 69 mm7.99 × 7.09 × 2.72 in | – | upon request | Get a quote |
Formalloy | L-Series | Directed Energy Deposition | 1000 × 1000 × 1000 mm39.37 × 39.37 × 39.37 in | United States | upon request | Get a quote |
GE Additive | Arcam EBM Spectra L | EBM | ⌀ 350 x 430 mm | United States | upon request | Get a quote |
GE Additive | M2 Series 5 | SLM/DMLS | 250 × 250 × 350 mm9.84 × 9.84 × 13.78 in | – | upon request | Get a quote |
Renishaw | RenAM 500E | SLM/DMLS | 245 × 245 × 335 mm9.65 × 9.65 × 13.19 in | – | upon request | Get a quote |
SLM Solutions | SLM 125 | SLM/DMLS | 125 × 125 × 75 mm4.![]() | Germany | upon request | Get a quote |
SPEE3D | LIGHTSPEE3D | Material Jetting | 300 × 300 × 300 mm11.81 × 11.81 × 11.81 in | – | upon request | Get a quote |
TRIDITIVE | AMCELL | Extrusion | ⌀ 300 x 350 mm | Spain | upon request | Get a quote |
Velo3D | Sapphire | SLM/DMLS | ⌀ 315 x 1000 mm | – | upon request | Get a quote |
Main types of metal 3D printing technologies
The four main types of 3D metal printing technologies are:
- Metal Powder Bed Fusion 3D printing (SLS, SLM, DMP)
- Directed Energy Deposition (DED)
- Metal filament extrusion (FFF, FDM)
- Material Jetting and Binder Jetting
There are also some resin-based metal 3D printers, and metal sheet lamination 3D printers, but they are harder to come by.
It is not uncommon to see different acronyms and names for similar technologies. Each brand markets their own, proprietary methods. Some metal 3D printer companies even use a mix of different technologies.
A breakdown of the metal 3D printer market by technology types. Source: Aniwaa database (2019)Here we provide a deeper look into each 3D metal printer from our list. They are grouped together according to their main 3D printing technology type (powder bed fusion, material/binder jetting, extrusion, and DED).
Extrusion-based metal 3D printer selection (FFF, FDM)
Extrusion consists of heating the material (filament) and pushing it through a nozzle. In the metal 3D printing case, the filament is generally made up of metal particles mixed into a binding agent.
After the part is 3D printed, the result is a raw object or part; it must go through several post-processing steps– such as debinding and sintering– to attain its final form.
Most extrusion-based metal 3D printing processes include these steps.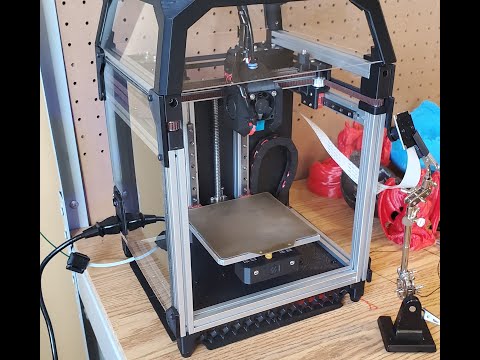
Desktop Metal’s Studio is an office-friendly, end-to-end metal 3D printing system. Aside from the printer, the Studio line also includes a debinding machine and a furnace for sintering. Indeed, parts 3D printed with this Desktop Metal 3D printer are “green”.
The Studio printer, with its proprietary Bound Metal Deposition technology, uses filament that is filled with small, metal rods. During debinding, the binding material (wax and polymer binders) is dissolved thanks to a proprietary liquid substance. The part is left porous, and must go in the furnace for its particles to fuse and densify the part.
Contact manufacturer Get a quote Add to comparison
MarkForged is specialized in continuous fiber 3D printing, but also offers metal 3D printing with their Metal X system, featuring Atomic Diffusion Additive Manufacturing (ADAM) technology.
This MarkForged 3D printer extrudes metal-filled plastic filament to form the part, which must then be washed with a special debinding fluid (Wash-1 Station) and then sintered in a furnace (Sinter-1 or Sinter-2 MarkForged machines).
Available metal 3D printer filament includes various Steels (h23, A2, D2 tool steels, 316L stainless steel) as well as Inconel, Copper, and Titanium.
Contact manufacturer Get a quote Add to comparison
Canada-based Rapidia offers an interesting and unique way to 3D print metal. They use a water-based metal paste, which eliminates the need for chemical debinding. The water evaporates during the 3D printing process, so the part only needs to go through the furnace in order to completely solidify and attain its final form.
Confirmed, available paste types include several Stainless Steels, Inconel, and a few ceramics. Copper, Tungsten Chrome Carbide, Titanium, and various other metals are in development.
The ExOne Metal Designlab, designed in collaboration with Rapidia, works on the same basis.
Contact manufacturer Get a quote Add to comparison
Pollen AM is a French manufacturer that has been producing pellet 3D printers since 2013. Their Pam Series MC is a delta-style 3D printer (cylindrical build volume) that can print metals, ceramics, and thermoplastics.
It extrudes injection-molding-grade pellets instead of metal 3D printer filament, driving material costs down significantly. Pollen AM names their technology “Pellet Additive Manufacturing”.
Contact manufacturer Get a quote Add to comparison
This machine was built with one goal: enable mass production 3D printing of metal parts 24/7. The AMCELL is fully automated, with auto feedstock control, environment control (temperatures, humidity, air filtering), and an ejection system fitted with a conveyor belt.
Rather than providing one, big build volume, the TRIDITIVE AMCELL boasts eight delta-style ø 220 x 330 mm build areas. Its eight “robots” deposit metal-infused filament to create 3D metal parts. TRIDITIVE states that resulting parts are similar to ones produced with traditional MIM (Metal Injection Molding) methods.
TRIDITIVE’s technology is called Automated Multimaterial Deposition®.
Contact manufacturer Get a quote Add to comparison
Metal powder bed fusion 3D printer selection (SLS, SLM, DMP, and more)
At the moment, the most commonly used metal additive manufacturing technology is powder bed fusion 3D printing. Simply put, the 3D printer creates objects out of a bed of powdered metal by using a powerful laser.
3D Systems, a historical actor on many 3D printing fronts, presents the DMP FLEX 100 as a fast, precise, and affordable metal 3D printer. It offers impressive part repeatability and surface finishes, of around 20 μm and 5 Ra μm respectively. DMP stands for Direct Metal Printing.
The printer comes with 3D Systems’ software 3DXpert All-in-One Software Solution for Metal Additive manufacturing. Their LaserForm metal 3D powders are certified.
Contact manufacturer Get a quote Add to comparison
This compact metal 3D printer is destined for the production of small parts in small quantities. Its material portfolio is especially interesting for medical use cases, namely dental crowns and bridges. EOS certified metal powders include Cobalt-Chrome, Stainless Steel, and Titanium.
The EOS M100’s laser spot is precise enough to provide a great level of detail, backed by 200 W of powder.
Contact manufacturer Get a quote Add to comparison
Originally a Swedish company, Arcam was acquired by GE Additive a few years ago. The Arcam EBM Spectra L is up to 20% faster than its predecessors and is able to reduce part costs by around 10%.
This metal 3D printer is dedicated to Titanium 3D printing, but Copper is in the pipeline as well. Its laser beam power is equal to 4.5 kW, partly explaining the printer’s high melting capacity and productivity. Common applications for this printer include orthopedic implants and parts for the aerospace industry.
Contact manufacturer Get a quote Add to comparison
Concept Laser is the company behind GE Additive’s M2 Series 5. It offers an easy, optimized workflow, with a separate processing chamber and handling area that is integrated into the system. This closed-loop material system ensures a safe environment that is free of powder for the operator.
The M2 metal additive manufacturing solution is compatible with a range of metals, from Stainless Steels to Aluminum, Nickel, Titanium, and Cobalt-Chrome.
Contact manufacturer Get a quote Add to comparison
The RenAM 500E is Renishaw’s entry-level metal additive manufacturing solution. It offers a relatively large build volume and powder can be handled via a dedicated glove box to avoid powder from getting free.
This system is also equipped with an oxygen sensor and a proprietary emission-filtering system branded SafeChange™.
Contact manufacturer Get a quote Add to comparison
Officially established in 2006, SLM Solutions has been a historical player in the powder bed fusion industry for many years. The SLM 125 boasts an open software architecture that allows users to tweak the system’s parameters according to specific use cases, materials, and general needs.
Options such as laser monitoring and melt pool monitoring are available for businesses that require full transparency and control over their production series.
Contact manufacturer Get a quote Add to comparison
The TruPrint 1000 is TRUMPF’s most compact metal 3D printing system, with a 100mm-tall cylindrical build volume. It is suitable for the production of small parts and prototypes, and even small production series when equipped with the multilaser option that increases the printer’s speed.
This metal 3D printer can be operated remotely via a tablet application, which also gives access to its onboard camera stream.
Contact manufacturer Get a quote Add to comparison
The Velo3D Sapphire is a high-volume metal 3D printer from the US designed for production series. This metal 3D printer features Velo3D’s Intelligent Fusion technology to allow for complex geometries and 0° overhangs.
The system is also equipped with a range of metrology sensors that measure each and every layer that is 3D printed.
Contact manufacturer Get a quote Add to comparison
The XM200C is Xact Metal’s entry-level metal 3D printing solution. It is suitable for both research purposes and small production series. The XM200C benefits from a proprietary Xact Core gantry system for precise movements with a fusing speed of up to 500 mm/s.
Xact Metal offers their own materials, branded Xact Powder, including various Stainless Steels, Super Alloys, Tooling Steels, Aluminum, Titanium, Bronze, and Copper. Advanced users are able to use their own metal powders if needed.
Contact manufacturer Get a quote Add to comparison
Metal material jetting and binder jetting 3D printers
Material jetting 3D printers are equipped with various inkjet printheads (somewhat similar to 2D printing) that jet material onto a surface. The material then hardens, and another layer of “metal ink” is jetted on top.
Binder jetting is a similar process, but it is a binding agent that is jetted atop a layer of powder.
The Production System by Desktop Metal was designed for mass production. It is advertised by Desktop Metal as being a fast, cost-effective metal additive manufacturing solution, with a cost per part up to 20 times lower than with other metal 3D printing systems.
This Desktop Metal 3D printer is equipped with over 16,000 nozzles that are mounted onto a “print bar” that recoats the build plate with powder at the same time, hence explaining the technology’s name: Single Pass Jetting™.
Contact manufacturer Get a quote Add to comparison
Digital Metal, a Höganäs Group company, creates incredibly detailed metal parts with their DM P2500 system. It is able to print 3D metal parts with an accuracy as high as 0.001mm (1µ), and with a medical-grade surface quality of around 0.006mm (6µ).
Another interesting feat to point out is that almost 100% of leftover powder can be recycled for future prints. This metal AM machine is able to churn out serial production series efficiently and reliably; one of the company’s first DM P2500 printers has been running 24/7 since 2013, according to Digital Metal.
The Digital Metal DM P2500 is a certified metal 3D printer (CE and UL) that is compatible with certified metal materials (ISO 22068).
Contact manufacturer Get a quote Add to comparison
Australian manufacturer SPEE3D has developed an impressively fast metal 3D printing technology called Supersonic Deposition. The technology is based on metal cold spray, using compressed air to “jet” metal powder through a nozzle at high speeds.
This enables the LightSPEE3D to 3D print at up to 100 grams per minute and with a range of metals including copper.
Contact manufacturer Get a quote Add to comparison
XJet developed an impressive, proprietary jetting technology they call NanoParticle Jetting™. This inkjet method disperses millions of tiny droplets that contain nanoparticles of solid metal. The liquid material comes in cartridges that are easy to insert into the printer.
After being printed, the metal parts must go through support removal and sintering processes to attain their final form.
Contact manufacturer Get a quote Add to comparison
DED: Directed Energy Deposition metal additive manufacturing systems
Directed Energy Deposition (DED) is comparable to filament extrusion. The metal material is pushed through a special nozzle, like with FFF/FDM, but a powerful laser beam solidifies the material at its deposition point.
Formalloy produces a range of metal DED 3D printers with up to 5 axes of motion. They can be used to produce metal parts but also to repair or clad existing parts.
Different laser wavelengths are available, as well as different build volumes: 200 x 200 x 200 mm, 500 x 500 x 500 mm, and 1000 x 1000 x 1000 mm. Metal 3D printers from Formalloy can be customized depending on company requirements.
Contact manufacturer Get a quote Add to comparison
Alternative metal 3D printers and special mentions
Hybrid metal manufacturing systems
Some manufacturers are specialized in hybrid metal manufacturing systems. They combine both subtractive and additive manufacturing methods, often with robotic arms that are able to move on more than three axes.
Some of the biggest actors on the hybrid metal AM system market are:
- Gefertec (Germany)
- DMG Mori (Germany)
- Matsuura (Japan)
- Sodick (United States)
XXL-sized metal 3D printers for industrial production
For those that require very large metal parts, there are several huge, industrial machines that offer gigantic build volumes for industrial production. To name a few:
- Sciaky EBAM 300
- Titomic TKF1000
- ADC Aeroswift
- ADIRA AddCreator
- Fabrisonic SonicLayer 4000
- ExOne X1 160PRO
- InssTek MX-600
- BeAM Modulo 400
- Optomec Lens CS 600
- Additive Industries MetalFAB1
Metal 3D printers from China
There has recently been a lot of growth in the metal 3D printer market in Asia, and more specifically in China. Some Chinese brands have been upping their game in that respect, providing industrial-grade metal 3D printing options:
- Farsoon
- ZRapid Tech
- Shining 3D
- Wiiboox
However, we feel that they are not yet playing in the same league as the 3D printers from our main selection, mostly due to a lack of distribution networks, after-sales service and training, and other factors which tend to matter when considering them together as a whole.
R&D metal 3D printers for labs
In certain cases, metal 3D printers are used for research purposes to develop and test new materials. There are a few machines that are specifically designed for this:
- Open Additive PANDA-6”
- Freemelt ONE
- Sharebot metalONE
Pros and cons of metal 3D additive manufacturing
Benefits of 3D printing metal parts
- On-demand production: Metal additive manufacturing offers more flexibility and control over the production line.
- Complex designs made possible: With 3D printing technology, it is possible to create highly detailed and intricate parts that would have to be broken down into several pieces with traditional methods.
- Waste reduction: Compared to CNC milling, for example, metal AM produces much less waste as it only consumes the material needed for a certain part. This is more true for extrusion-based methods than it is for powder-based methods, where it isn’t always possible to re-use 100% of unsintered or unbinded material.
- Lighter parts: Whereas metal parts are usually completely solid infill-wise with other methods, 3D printing allows parts to be more or less hollow without undermining their strength and resistance.
- Cost-effectiveness: All the above benefits of metal 3D printing can inherently reduce costs per part, although high metal 3D printer prices do represent a significant entry barrier. Reaching a positive return on investment can take a while depending on your throughput.
Limits of metal 3D printing
- Metal 3D printing prices: Metal AM systems are still quite expensive, as are metal powders and metal filaments. There are hidden costs, too (e.g. energy consumption, learning curve, etc.).
- Environmental constraints and safety precautions: Most metal 3D printers have a large footprint and require specific operating environments with controlled temperatures, hygrometry, and more.
- Post-processing: In many cases it is necessary for parts to be post-processed, whether it’s debinding and sintering or finishing touches for surface quality.
- Physical properties: It can be difficult to achieve the same physical properties that traditionally manufactured metal parts have. There are a number of factors (e.g. anisotropy) to take into account during the design process and file preparation before even trying to 3D print a certain part.
Metal 3D printing materials
Which metals can you 3D print?
A growing number of metals and metal alloys can be 3D printed. These are the main ones:
- Aluminum
- Titanium
- Nickel, Inconel
- Copper
- Bronze
- Cobalt, Cobalt-Chrome
- Steels (tooling, maraging, stainless)
- Precious metals (gold, silver, platinum)
Which metal 3D printing material formats are available?
Metal 3D printing material can be found in various formats, catering to different metal 3D printing methods. The most common are:
- Powder
- Wire
- Filament
It is also possible to find metal 3D printing resin as well as metal sheets for lamination-based 3D printers.
Metal 3D printer price: how much does a metal 3D printer cost?
Industrial metal 3D printer prices generally range from about $30,000 to over one million dollars for the most premium, industrial-grade metal additive manufacturing systems.
Additional costs to consider are the materials for metal 3D printing, which can cost a few hundred USD/kg, as well as costs linked to post-processing (tools, time, etc.).
Applications for metal AM systems
There are thousands of possibilities and use cases for metal 3D printing in a wide range of industries. A few industries have been incrementally using metal AM:
- Aerospace
- Automotive
- Medical
Whether it’s for tooling, replacement parts, or final products, many businesses can benefit from metal 3D printing.
However, metal additive manufacturing isn’t necessarily beneficial for every single metal part. Although some metal 3D printing systems have a relative capacity for serial production, it is generally cheaper to keep using traditional methods for simple parts.
For cases where complex geometries, rapid prototyping, and mass customization are required, metal AM is convenient and efficient.
Metal 3D printing services: order 3D metal parts online
For professionals with limited office space and human resources, low budgets, and/or few needs of custom parts and prototypes, metal 3D printing services can be an ideal solution.
These additive manufacturing service companies own a variety of high-quality 3D printers with different technologies, and their professionals are experts in 3D printing. It is possible to order metal 3D parts on-demand, without acquiring a 3D printer or having to buy a certain material for one-time use.
Here are some of the most trusted 3D printing service providers that offer metal printing services:
- Sculpteo
- Shapeways
- Hubs (ex 3D Hubs)
- Stratasys
- i.materialise
- Protolabs
Metal 3D printing technologies and acronyms
Many manufacturers develop proprietary variations of existing technologies and label them their own registered names:
- Powder Bed Fusion (PBF): DMLS (Direct Metal Laser Sintering), DMP (Direct Metal Printing), LaserCUSING, LBM (Laser Beam Melting), LMF (Laser Metal Fusion), SLS (Selective Laser Sintering), SLM (Selective Laser Melting)
- Directed Energy Deposition (DED): DMT (Direct Metal Tooling), EBAM (Electron Beam Additive Manufacturing), EBM (Electron Beam Melting), LENS (Laser Engineered Net Shaping), LMD (Laser Metal Deposition)
- Metal Material Jetting (MJ) or Binder Jetting (BJ): Magnet-o-Jet, Nanoparticle Jetting, SPJ (Single Pass Jetting), Metal Jet
- Metal filament extrusion/Fused Filament Fabrication (FFF): ADAM (Atomic Diffusion Additive Manufacturing), CEM (Composite Extrusion Modeling), FDM (Fused Deposition Modeling), FFD (Fused Feedstock Deposition), FMP (Filament Metal Printing), BMD (Bound Metal Deposition), MIM (Metal Injection Molding)
- Lamination: SL (Sheet Lamination), UAM (Ultrasonic Additive Manufacturing)
- Metal resin 3D printing: DLP (Digital Light Processing), FluidFM, SLA (Stereolithography)
Metal 3D printing FAQ
Is 3D printed metal strong?
Metal 3D printed parts can be as strong (or even stronger) as metal parts created with traditional manufacturing processes such as casting. The part’s strength will, however, depend on the metal AM method used and the conditions in which it is 3D printed.
When was 3D metal printing invented?
Metal 3D printing became possible in the 1990s with the development of Selective Laser Melting technology. However, 3D metal printing only started to gain traction and public interest from around 2010 onwards.
How does metal 3D printing work?
There are several ways to 3D print metal. Layers of metal filament can be deposited one after the other, producing a green part that must later go through debinding and sintering steps. It is also possible to fuse metal powder particles together with a laser, or with an inkjet printhead that deposits drops of binding material onto the powder.
How much does a 3D printer cost?
3D printing is a one-stop solution for a wide range of applications, from high-resolution model production to rapid prototyping, rapid tooling for traditional manufacturing processes, production of aids and end-use models.
However, when you consider investing in a 3D printer, the viability of a solution usually boils down to a simple question: Is it cost-effective for your business? How much does a 3D printer cost and how much time and money can it save your business? nine0003
3D printer prices range from $200 to $500,000 depending on the printing process, materials, and complexity of the solution.
In this guide, we'll break down 3D printing costs by technology, compare outsourcing versus in-house manufacturing, list factors to consider when calculating the cost of each model, and look at what else to look for when comparing different solutions. for 3D printing and other production methods. nine0003
Interactive
This interactive ROI tool will help you find out how much time and money you can save by 3D printing with a Formlabs 3D printer.
Calculate Your Costs
The three most well-known plastic 3D printing technologies today are Fused Deposition Modeling (FDM), Stereolithography (SLA), and Selective Laser Sintering (SLS).
Each technology has its advantages and disadvantages - take a look at the infographic:
Download this high resolution infographic here. Interested in learning more about FDM, SLA and SLS 3D printing technologies? Check out our detailed guide.
Prices for 3D printers have dropped significantly in recent years, and today all three technologies are available in compact, low cost systems.
FDM generally produces models at a lower cost if you only print relatively simple prototypes in limited numbers. SLA technology offers higher resolution and quality, as well as a wide choice of 3D printing materials at a slightly higher price. But this difference is quickly offset when you print complex designs or larger batches due to the less labor-intensive post-processing process. Finally, SLS technology is the most cost effective for medium to high volume production of high quality functional models. nine0003
Comparing the total cost of different 3D printers by price tags alone will not give you a complete picture of how the cost of a 3D printer and a printed model will compare. The cost of 3D printing materials and labor significantly affects the cost of a model, depending on the application and your production needs.
Let's look at the different factors and costs for each process.
FDM, also known as Fused Filament Manufacturing (FFF), is a printing method where the parts of a model are made by melting and extruding a thermoplastic filament, which the printer's nozzle applies layer by layer onto the model being made. nine0003
FDM is the most popular form of consumer grade 3D printing, fueled by the proliferation of hobbyist 3D printers. However, professional and industrial FDM printers are also popular among professionals.
The cheapest 3D printers are FDM printers. DIY kits for FDM 3D printers start at $200. However, most of these models are more like toys or DIY projects that require a significant amount of time to build, set up and calibrate. The quality of the print largely depends on the success of these operations. In addition, machines require repairs and regular maintenance to keep them working, so they are more suitable for people with a higher engineering education who have a lot of time and patience. nine0003
Hobbyist FDM 3D printers cost between $500 and $1,500, come pre-assembled or unassembled, require less setup, but have the same disadvantages as the cheapest 3D printers. More expensive models are capable of large print volumes and work with a wide variety of materials besides low temperature ones such as PLA.
Professional 3D FDM printers start at $2,500 and large format professional FDM printers are available from $4,000. The cost of the most modern industrial FDM printers can exceed 10,000 US dollars. Most of these printers come pre-assembled and calibrated in the box, or they can be automatically calibrated. Printers in this category offer better print quality, a wider range of media, higher print volumes, improved reliability, and ease of use and maintenance. In addition, professional 3D printer manufacturers offer customer support services for troubleshooting. nine0003
Material costs for FDM 3D printing range from $50 to $150/kg for most standard and engineering filaments, and $100 to $200/kg for auxiliary materials. There are also cheaper alternatives, but they are of lower quality.
In addition, FDM printing can be very labor intensive. Successful printing of complex models requires support structures that must be removed manually or dissolved in water. To obtain a high quality surface and remove layer lines, lengthy manual post-processing of models, such as sanding, is necessary. nine0003
SLA 3D printers use the process of photopolymerization, that is, the conversion of liquid polymers into hardened plastic using a laser. SLA is one of the most popular processes among professionals due to its high resolution, accuracy and material versatility.
Models printed on SLA printers have the highest precision, sharpest detail and smoothest surface possible of any plastic 3D printing technology. But the main advantage of the SLA method is its versatility. SLA polymers have a wide range of optical, mechanical and thermal properties that match those of standard, engineering and industrial thermoplastics. nine0003
SLA 3D printers can handle a wide range of resin materials for a wide variety of applications.
SLA used to be used only in large and complex industrial 3D printers costing over $200,000, but the process is now much more affordable. With the Formlabs Form 3+ Printer, businesses can now use industrial quality SLA printing for as little as $3,750. With Form 3L, large format SLA printing starts at just $11,000. nine0003
Stereolithographic 3D printers will be shipped in a box assembled and calibrated. These are professional tools that are highly reliable and require virtually no maintenance. Technical support is also always available. It provides troubleshooting in a critical situation (but its probability is extremely small).
Most standard and engineered polymers for SLA technology cost between $149 and $200 per liter. nine0003
SLA printers are easy to use and many workflow steps such as rinsing and final curing can be automated to reduce labor costs. Printed models have a high quality surface immediately after printing and require only simple post-processing to remove supporting structures.
Selective Laser Sintering (SLS) 3D printers use a high power laser to sinter fine polymer powder particles. The unsprayed powder supports the model during printing and eliminates the need for special support structures. This makes SLS ideal for complex geometries, including internal features, grooves, thin walls, and negative taper. nine0003
Models produced using SLS printing have excellent mechanical characteristics - their strength can be compared with the strength of injection molded parts. As a result, SLS technology is the most popular plastic 3D printing process for industrial applications.
SLS printed nylon models are ideal for a range of functional applications, from consumer product design to healthcare applications.
Like SLA, SLS was previously only available in large format, complex 3D printing systems costing $200,000 or more. With the Formlabs Fuse 1 stereolithography printer, businesses can now solve industrial-scale tasks with SLS technology starting at $18,500. The complete kit, which includes the post-processing and powder recovery system, costs $31,845.
As with SLA printers, stereolithographic printers are shipped assembled and calibrated in the box. They are reliable and can operate 24/7. The package includes in-depth training and fast technical support. nine0003
SLS nylon print materials cost about US$100/kg. SLS does not require supporting structures and unused powder can be reused, reducing material costs.
SLS is the least labor-intensive plastic 3D printing process in the production environment, because the printed models are of high quality right away, and to remove excess powder, they simply need to be cleaned.
There are several processes for 3D printing not only plastics but also metals. nine0003
Metal FDM printers are similar in design to traditional FDM printers, but use extruded metal rods held together by a resin binder. The finished parts of the model are sintered in an oven to remove the binder.
SLM and DMLS printers are similar to SLS printers, but instead of polymer powders, they fuse metal powder particles layer by layer using a laser. 3D printers based on SLM and DMLS technologies can create strong, precise and complex metal products, making this process ideal for the aerospace, automotive and medical industries. nine0003
Prices for metal 3D printers have also begun to decline, ranging from $100,000 to $1 million today. However, these systems are still out of reach for most businesses.
SLA 3D printing is available as an alternative for casting workflows that allow metal models to be produced cheaper and faster than traditional methods and provide greater design freedom.
Technical report
Get design guides for 3D printing samples, see the step-by-step direct investment casting process, and study guides for indirect investment casting and sand casting.
Download white paper
Different plastic and metal 3D printing processes have unique qualities that make them suitable for different applications. Below is a comparison of different printing technologies.
Fused Deposition Modeling (FDM) | Stereolithography (SLA) | Selective Laser Sintering (SLS) | Metal FDM Printing | Selective Laser Melting (SLM) and Direct Metal Sintering (19008) 9008 | |
---|---|---|---|---|---|
Permission | ★☆ | ★ opa ★ ution | ★ opa | ★cle | ★cle ★ MyQUTION | SUMPLE | 1112 HICE | ★ opa ☆ | 1111111 ☆☆☆ | 1 ☆ | ★ opa |
Ease of use | x 300 x 600 mm (Desktop and Workshop 3D printers) | Up to ~300 x 335 x 200 mm (Desktop and Workshop 3D printers) | Up to 165 x 165 x 300 mm (3D - workshop printers) | Up to 300 x 200 x 200 mm | Up to 400 x 400 x 400 mm |
Price range | DIY kits for 3D printers start at $200, while hobby printers cost $500-1500.![]() | Professional desktop printers start at $3,750, while high-volume large format desktop printers are available from $11,000. nine0112 | Workshop industrial printers start at $18,500 and traditional industrial printers start at $100,000. | Metal FDM printers start at $100,000, but complete solutions including an oven are much more expensive. | DMLS/SLM solutions start at around $200,000. These printers require special infrastructure conditions, which can further increase costs. |
Cost of materials | US$50-150/kg for most standard and engineering yarns and US$100-200/kg for auxiliary materials. | US$50-150/L for most standard and engineering polymers. | US$100/kg for nylon. SLS does not require supporting structures and unused powder can be reused, reducing material costs. | Depends on material and technology.![]() | Depends on material and technology. Significantly higher than plastic. nine0112 |
Labor | Manual removal of support structures (soluble support structures may be used in some cases). Long post-processing is required to obtain a high quality surface. | Washing and final polymerization (both can be automated). Simple post-processing to remove supporting structures. | Easy cleaning to remove excess powder. | Washing and sintering (both can be automated). It is possible to use mechanical processing and other types of surface treatment. nine0112 | Stress relief, support structure removal, heat treatment, and mechanical and other surface treatments. |
Materials | Standard thermoplastics such as ABS, PLA and their various blends. | Various polymers (thermosetting plastics). Standard, engineering (similar to ABS and PP, similar to silicone, flexible, heat resistant, rigid), injection molding, dental and medical (biocompatible).![]() | Engineering thermoplastics - typically nylon and its composites (nylon 12 biocompatible + sterilizable). | Stainless steel, tool steel, inconel, copper, titanium. | Stainless steel, tool steel, titanium, cobalt-chromium, copper, aluminium, nickel alloys. |
Applications | Basic experimental models, low cost rapid prototyping of simple parts. | Prototypes with a high level of detail requiring close tolerances and smooth surfaces: molds, tooling, templates, medical models and functional parts. nine0112 | Complex geometries, functional prototypes, low volume production or limited trial production. | Strong and durable models, tools and production aids. | Strong and durable models with complex geometries; ideal for the aerospace, automotive and medical industries. |
When calculating the cost of one model, the cost of ownership of equipment, material costs and labor costs are usually taken into account. It is important to understand the factors that affect each of these cost components, as well as the questions to ask in order to evaluate alternative production methods and uncover hidden costs. nine0003
Hardware ownership costs are fixed costs: 3D printer price, service contracts, installation and maintenance. These amounts must be paid whether your printer is idle or produces dozens of models per week.
Add up all projected fixed costs over the lifetime of the equipment, then divide by the number of models you plan to make. As a rule, the higher the performance and efficiency of your 3D printer, the lower the cost of ownership of equipment per model. nine0003
In recent years, desktop 3D printers have shown excellent results in reducing the cost of ownership of equipment. With a price 10 to 100 times lower than traditional industrial 3D printers and the ability to produce thousands of models over a lifetime, the cost of ownership can be negligible.
Questions:
-
Are there installation, training or additional initial costs other than the cost of the machine itself? nine0003
-
Do I need to sign a (mandatory) service contract? What does it include?
-
What accessories and tools are needed to make the final models?
-
What kind of maintenance is required for the machine to function properly? What is the expected annual maintenance cost? Will it change with an increase in production volumes?
The 3D printing raw materials and consumables you need to create models at an affordable price. These costs largely depend on the number of models you produce. nine0003
When calculating the cost of materials, determine how much material is required to create one model, and multiply this figure by the cost of the material. Count the amount of waste and any other consumables. As production grows, the cost of ownership of equipment decreases, and the cost of 3D printing materials tends to become more balanced.
Be sure to check what materials you need to create specific models, as the cost of 3D printing consumables can vary greatly. Please note that some 3D printers only work with their proprietary materials and thus limit your ability to use third party materials. nine0003
Questions:
-
What is the cost of each type of 3D printing material?
-
How much material is required to create one particular model, including waste?
-
What is the shelf life of the materials?
-
Do I need other consumables to create models?
-
Can the machine work with third-party materials?
While 3D printing can replace complex traditional manufacturing methods and provide significant time savings, depending on the 3D printing technology, it can still be quite labor intensive. nine0003
Professional desktop 3D printers are generally optimized for ease of use. DIY kits for 3D printers and hobby printers often require additional effort to adjust settings, while regular maintenance or material changes on traditional industrial machines can involve time-consuming tasks that require the assistance of a skilled operator.
Post-processing workflows vary depending on the 3D printing process, but in most cases include cleaning up models and removing support structures or excess material. However, there are solutions to automate some specific tasks. For example, Formlabs Form Wash and Form Cure simplify the wash and finish process for Formlabs SLA 3D printers, while Fuse Sift offers a turnkey post-processing and powder recovery system for the Fuse 1 SLS printer. nine0003
More complex processes such as SLA and SLS do not take long to achieve high quality models, while FDM models require lengthy manual post-processing to improve quality and remove layer lines.
Questions:
-
What is the whole model production workflow? What specific steps are required to set up printing, change materials, and post-process models?
nine0298 -
How long does it take to post-process one specific model?
-
Are there any tools or devices available to automate some of these tasks?
Outsource production orders to 3rd party service bureaus or labs when you use 3D printing only occasionally or to produce large models in non-standard materials. Typically, the bureau has several in-house 3D printing processes such as SLA, SLS, FDM, as well as metal 3D printers. They can also provide advice on a variety of materials and offer additional services such as design or improved finishes. nine0003
The main disadvantages of outsourcing are the high cost and duration of production. One of the main advantages of 3D printing is its speed compared to traditional production methods. But it is noticeably reduced if the delivery of the model produced by the involved organization takes several days or even weeks. And as demand and capacity grow, the costs of outsourcing are rising rapidly.
Desktop 3D printers are the perfect solution for fast model production. Depending on the number of parts needed and the volume of prints, the investment in a professional 3D printer can pay for itself in just a few months. nine0003
With desktop and workshop printers, you can pay for the capacity that matches your business needs and scale your production by adding more devices as demand grows, without the heavy investment of a large format 3D printer. Using multiple 3D printers also allows you to print models from different materials at the same time. But if there is a need for the production of large parts or the use of non-standard materials, service bureaus can come to the rescue. nine0003
Investment, material and labor costs are relatively easy to calculate. But what about indirect costs and hard-to-calculate factors that affect your business? Let's look at some of the main considerations when comparing a desktop 3D printer to outsourcing or other manufacturing methods.
Save time: What if you could get products to market a few months faster? Or reduce the delivery time of your products by a few days or weeks? 3D printing simplifies traditional prototyping and manufacturing workflows, helping you save time and stay ahead of the competition. nine0003
Top results: 3D printing allows you to create more iterations, overcome failures faster, and produce better end products. Troubleshooting a design early on also helps avoid costly redesign and the use of additional tools.
Interaction: Having high-quality prototypes and models allows you to communicate more effectively with customers, clients, suppliers and other stakeholders. Avoid misunderstandings and costly mistakes. nine0003
Intellectual Property Protection: Do you work with confidential information? Making your own models means you don't have to transfer intellectual property (IP) to third parties, reducing the risk of IP leakage or theft.
Usually, calculating cost per part, lead time, and comparing alternatives to see if a solution is right for your business is a tedious task of creating a complex spreadsheet in an attempt to collect all of the often hidden information from a manufacturer. nine0003
Use our simple online tool to calculate cost per model and order lead time when printing with a Formlabs stereolithographic 3D printer and compare time and cost savings with other manufacturing methods.
Calculate Cost and Time
Desktop Metal 3D Printer Pricing and Specifications Announced
Desktop Metal revealed that their long-awaited metal 3D printing system uses multiple technologies and that two 3D printing systems are currently in development. nine0003
The Desktop Metal Studio system is based on FDM and the production system is based on inkjet and powder. Both Studio and Production systems are now backed up. A series of photographs accompanying an article in today's MIT Technology Review show a series of 3D prints from printers.
Desktop Metal Studio 3D Printer
The Desktop Metal Studio Printer extrudes bonded metal rods and resembles FDM 3D printers that use plastic. nine0003
Specifications: print speed 16cm3/hour, layer height 50µm and build area 300x200x200mm (HWD).
Received 3D prints require post-processing for trimming and sintering. For this purpose, Desktop Metal has developed an "Office Sintering Furnace".
The SiC Industrial Microwave Oven is "fully automated, temperature controlled and its compact size fits perfectly into office doors."
3D steel propeller printed with a thin layer of ceramic between the supports for easy removal. nine0003
3D printing process scaling
Desktop Metal also gave basic information about the production system. The company describes it as “the first 3D 3D printing system for mass production. The manufacturing system, coming in 2018, delivers the speed, quality and cost per part needed to compete with traditional manufacturing processes. ”
Bold announcement that the system is 100 times faster at 20 times the cost. The company describes this process as Single Pass Jetting,
Breakthrough single pass (SPJ) process delivers speeds up to 8200 cc/h, 100 times faster than laser systems. The right tool is the fastest way to make complex metal parts.
"Single Pass Jetting assembles metal parts in minutes instead of hours," says Desktop Metal. The build area is reported to be 330x330x330mm (HWD), the resolution is listed below 50 voxels, and the print speed is 8200cm 3 per hour.
3D printed screw and wing nut from Desktop Metal showing tolerances.
Demonstration of the internal structures of the lattice.
The benefits of the Desktop Metal system are described as bi-directional, single-pass inkjet printing with two printed strips containing "over 32,000 jets" working in conjunction with powder spreaders. The 3D printing system allows "creating millions of droplets per second".