Hp metal 3d printer price
Metal 3D Printer – HP Metal Jet S100 3D Printing Solution
Contact an HP 3D Print expert
Choose the phone number for your country to speak to a local HP 3D Printing sales expert today.
België/Belgique
+32 78 48 44 69
Czech Republic
+420 239 050 531
Deutschland
+49 7031 986 90 13
+49 7031 986 90 17
España
+34 93 003 45 95
France
+33 6 28 78 35 59
Italia
+39 02 8295 2406
Nederland
+31 20 241 5685
Norway
+47 23 96 00 13
Österreich
+43 720 117035
+43 1424 0091
Romania
+40 376 300 174
Sweden
+46 8 446 891 49
Suisse/Switzerland
+41 44 511 2308
+41 44 511 2333
United Kingdom
+44 20 7365 8158
United States
+1 877 468 8369
Reinvent business opportunities with digitally driven industrial metal 3D printing for mass production
Watch video
Accelerate innovative
designs and products
Efficiently 3D print
metal parts at scale
Deliver top quality
3D printed metal parts
from a trusted global
industry leader
Scale growth with HP’s
flexible offering
Discover the complete HP Metal Jet S100 3D Printing Solution
Streamline your metal 3D printing workflow
Learn how this metal 3D printer solution gains efficiency from design to final part.
Software
Software
HP Metal Jet Software Solutions provide control to connected factory system solutions, focus on data flow across touchpoints, and prioritize operational uptime.
Materials
Materials
Two stainless steel powders available with process parameters that achieve MPIF 35 properties: HP Metal Jet SS 316L and HP Metal Jet SS 17-4PH.
Data courtesy3
Services
Services
HP Metal Jet Solution Services provide your business with a comprehensive suite of onboarding, maintenance, and professional services to help you achieve the most value with HP Metal Jet technology.
“The benefits I see with HP Metal Jet technology are process robustness, high machine productivity, and surface finish. Now we do consider HP’s Metal Jet technology a viable option for serial part manufacturing. We plan to leverage this technology across Schneider Electric’s lines of business to bring new added value to our products and customers.
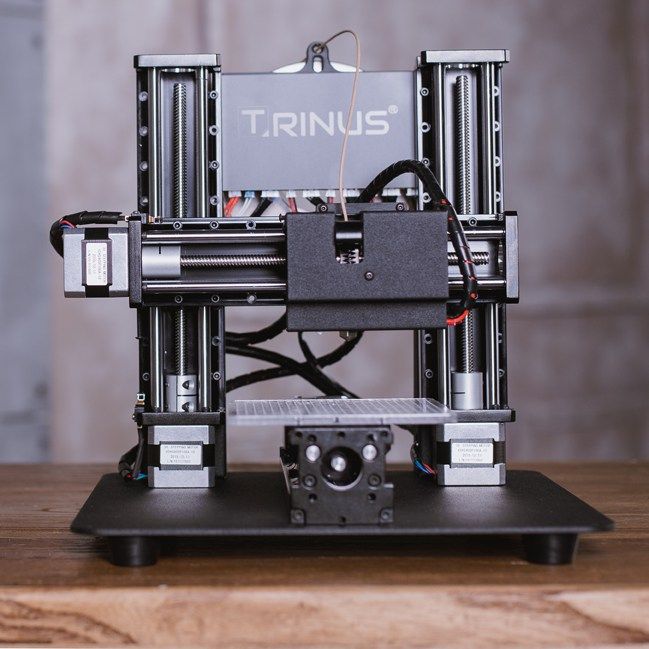
Guillaume Fribourg, Metallic materials & processes expert in Energy Management BU, Schneider Electric
Watch video
Data courtesy ⁴
"We see Metal Binder Jetting as the main growth driver for our Metal Additive Manufacturing division. Now, with the HP Metal Jet S100 Printing Solution, we can say AM has the possibility to enter into serial production markets."
Diego Laurent, CEO of GKN Powder Metallurgy
Watch video
Data courtesy ⁵
“By reducing the cycle time for the production of parts we can realize a higher volume of mass production very quickly. That’s why HP’s new Metal Jet platform is a huge leap forward for the industry and we look forward to raising the bar on what is possible to deliver more value and innovation for our customers.“
Dr. Martin Goede, Head of Technology Planning and Development, Volkswagen.
Watch video
Data courtesy ⁶
“HP Metal Jet represents the first truly viable 3D technology for the industrial-scale production of metal parts.
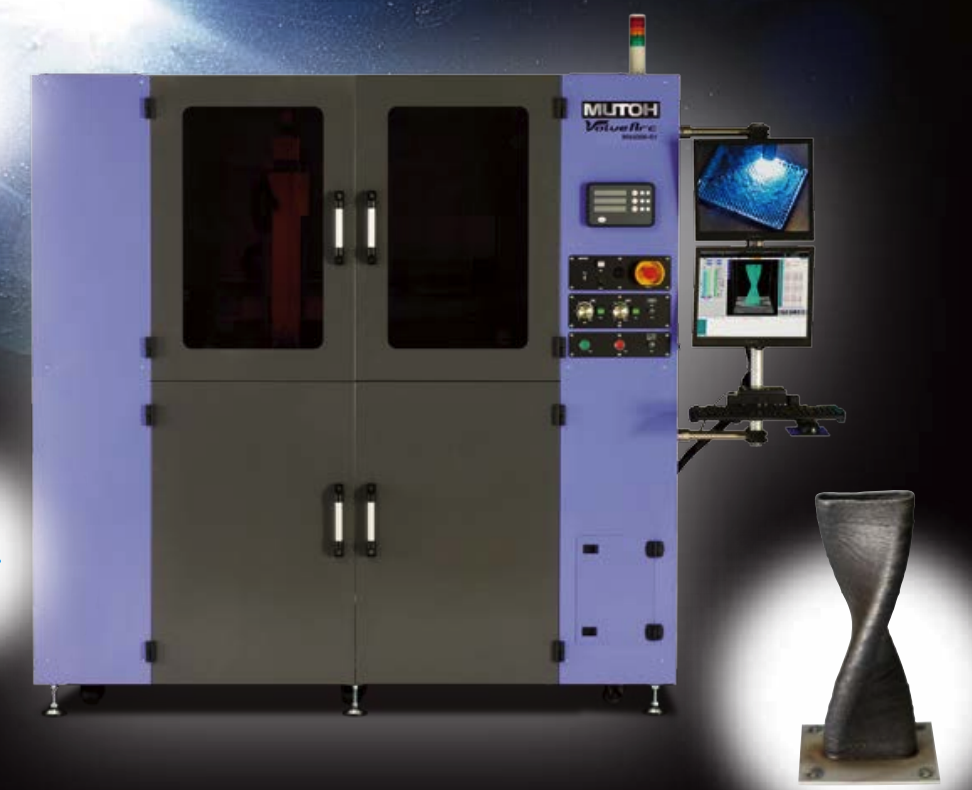
Rob Hall, President of Parmatech
Watch video
Data courtesy ⁷
Leverage Binder Jetting technology and HP's expertise in additive manufacturing
Why metal 3D printing?
- Innovative designs enabled for lightweight or consolidated parts, performance improvements and customization
- Improved efficiencies and economics
Why binder jetting?
- Higher productivity from layer by layer process; less post-processing and no support removal required
- Cost efficient by using metal powders from established global powder suppliers
Why HP Metal Jet 3D printing?
- HP Thermal Inkjet printhead delivers economics and part quality (surface finish and accuracy)
- Leverages IP from HP Latex and uses minimum binder agent allowing for thicker and larger mass parts
Explore new metal 3D printing applications
3D printing metal parts can help you eliminate the design constraints of analog technologies and produce innovative applications that you can mass customize and quickly deliver to market.
Industrial metal 3D printing applications
Data courtesy8
Air filter / 690V Circuit breakers
Company:
Schneider Electric
Benefits:
- Faster time to production
- Highly complex lattice geometry
- Cost effective serial production
- Weight reduction
- Assembly consolidation
- Ease of use
Material:
HP Metal Jet SS 316L
Data courtesy9
Digital engine component
Company:
Lumenium
Benefits:
- Highly dense near-net parts for complex applications
- Cost savings - less material waste and fewer machining steps
- Design freedom
Material:
HP Metal Jet SS 17-4PH
Fluidic manifold
Benefits:
- Design flexibility resulting in fluid/thermal transfer optimization and assembly consolidation
- Design freedom enables features impossible to manufacture using traditional techniques
Material:
HP Metal Jet SS 316L
Filter disk
Benefits:
- Porosity control for large-scale production of complex geometries
- Near-net shape porous geometries enables faster speed to market and supply chain simplification
Material:
HP Metal Jet SS 316L
Consumer goods metal 3D printing applications
Data courtesy10
KING Supersport-35 Putter
Company:
Cobra Golf
Benefits:
- Design freedom - optimal weight distribution
- Optimized performance with 3D printed body and lattice design
- Cost savings - eliminates the need for 3D printing supports and increases throughput
Material:
HP Metal Jet SS 316L
Post-processing:
Polishing, machining, PVD
Watch video
Data courtesy11
Rings and pendants
Company:
Legor
Benefits:
- Speed to market from design to production, saving additional time and costs from tooling
- New freedom to explore design spaces and create complex designs with varying sizes, shapes, thicknesses
Material:
HP Metal Jet SS 316L
Post-processing:
Polishing
Watch case
Benefits:
- Part quality – surface.
Near-net shape parts that can achieve class A1 finish after post-processing
- Cost savings – less machining and assembly steps to produce complex watch case geometries
Material:
HP Metal Jet SS 316L
Automotive metal 3D printing applications
Data courtesy12
Gearshift knob
Company:
Volkswagen group
Benefits:
- Speed to market from design to production, saving additional time and costs from tooling
- Weight reduction
- Design freedom for new features and capabilities previously not economically viable to mass produce
Material:
HP Metal Jet SS 316L
Post-processing:
Shot peening
Data courtesy12
Personalized keyfobs
Company:
Volkswagen group
Benefits:
- Speed to market from design to production, saving dditional time and costs from tooling
- Mass customization to offer more value to customers looking for unique products
Material:
HP Metal Jet SS 316L
Post-processing:
Polishing
Valve spool
Benefits:
- Complex shape and size - parts without support structures, allowing larger, more complex geometries
- Cost savings – less material waste and fewer machining steps when producing parts for large-scale production
Material:
HP Metal Jet SS 17-4PH
Post-processing:
Polishing
Metal Jet production service
14Experience HP Metal Jet quality. To order metal 3D parts, upload your design file,15 get a design compatibility check from HP, and receive your order from manufacturing partners.14
Order metal 3D parts
Metal 3D printing service production partners
Collaborate with metal part production leaders to help you scale your metal additive manufacturing
GKN Powder Metallurgy
The world’s leading producer of materials and products using powder metallurgy technologies.
Parmatech
World leader in metal injection molding, specializing in producing low-cost, high-volume metal parts for the medical and industrial sectors.
Any questions?
Reach out to a metal 3D printing expert!
Disclaimers
To achieve 4 times nozzle redundancy, nozzles are aligned so that four nozzles print the same 1/1200-inch dot row in the powder bed. This means up to four different nozzles can print HP Metal Jet binding agent in the same 1200 dpi grid point, helping to suppress defects.
For more information, see https://www.hp.com/metaljet-whitepaper.
Powder removal involves a mix of automated and manual processes, where trace amounts of loose powder may be lost.
Data courtesy of Lumenium.
Data courtesy of Schneider Electric.
Data courtesy of GKN Powder Metallurgy.
Data courtesy of Volkswagen.
Data courtesy of Parmatech.
Data courtesy of Schneider Electric.
Data courtesy of Lumenium.
Data courtesy of Cobra Golf.
Data courtesy of Legor.
Data courtesy of Volkswagen.
Subscription offering only available in US and selected countries in Europe. Please contact us for more information.
HP does not provide manufacturing services. Customers work directly with and pay for manufacturing services provided by a trusted third-party manufacturing partner responsible for fulfilling the order.
HP provides design compatibility check for HP Metal Jet printing. Metal Jet Production Service is available in the US and Western Europe.
We currently accept OBJ, STL, 3MF, X_T (Parasolid), STEP, and IGES files.
Pendant
Data courtesy11
HP Metal Jet SS 316L - extreme resistance to corrosion and high temperatures
A non-magnetic austenite stainless steel used in applications requiring extremely high corrosion resistance, excellent elongation, ductility, and strength at elevated temperatures. The high alloy and low carbon content makes it a great fit for automotive, aerospace, medical, jewelry, and oil/chemical industries.
Digital engine component
Data courtesy3
HP Metal Jet SS 17-4PH - high strength and wear resistance
A martensite precipitation hardening stainless steel used in applications that require a combination of high strength and mechanical properties with good corrosion and wear resistance. Properties can be tailored through heat treatment, making this versatile material valuable for a wide use of applications in the medical, aerospace, marine, food processing, and automotive industries.
HP Metal Jet Onboarding Services
Launch and scale your HP Metal Jet S100 3D Printing Solution with installation and training onboarding services designed to quickly and efficiently get your team, equipment, and site up and running.
HP Metal Jet Maintenance Services
Maximize your overall equipment effectiveness (OEE) with proactive, preventive, and responsive HP Metal Jet Maintenance Services tailored to your operational needs.
HP Metal Jet Professional Services
Optimize and accelerate your application designs as well as process and new material development efforts with HP Metal Jet Professional Services customized to help you achieve your desired part quality and production outcomes.
HP Metal Jet Command Center
Client/server application for system setup, registration, device monitoring, and connectivity management.
HP Metal Jet API
Application Programming Interface (API) for streamlined access to device data and device orchestration for process development and production workflow management.
HP Metal Jet Process Development Suite
Integrated build management, process parameter editing, sintering simulation, and process monitoring reduce time and effort in process development.
HP launches new Metal Jet S100 3D printer at IMTS: technical specifications and pricing
0Shares
The HP Metal Jet 3D printer has been launched by HP at the 2022 International Manufacturing Technology Show (IMTS). 3D Printing Industry is in Chicago this week for the show.
HP’s efforts to expand into metal 3D printing began to take shape in 2017 when plans for a high-volume jetting system were unveiled at its Security Analyst Meeting. As identified by 3D Printing Industry in 2017, HP’s metal 3D printer was expected to use Metal Injection Molding powder. HP would confirm this a year later.
Announced in 2018, HP’s much-anticipated Metal Jet technology is designed to work with Metal Injection Molding (MIM) materials rather than the spherical powders used in laser sintering metal additive manufacturing systems. According to the Global Head of the firm’s 3D Printing Metals business, Ramon Pastor, this is “a big deal,” as it enables users “to drive down cost-per-part” by 20% to 33%.
The Metal Jet S100 will launch with stainless steel 316L and 17-4PH compatibility. Pastor says that its efficiency improves its ergonomics in a way that allows it “to drive scale,” and HP “sees huge opportunities” for the system to address clients in the industrial, medical, consumer, and automotive industries.
A facility fitted with Metal Jet S100 3D printers. Photo via HP.HP’s Metal Jet 3D printing journey
Since unveiling its MJF concept back in 2014, HP has built a 3D printing offering in polymer-based machines and materials. In that time, HP systems have 3D printed over 130 million parts, and MJF continues to address the needs of firms across sectors, with the likes of Toyota now 3D printing automotive spares via the technology and Ocado 3D printing fulfillment bots.
Desktop Metal, Markforged, and Digital Metal have all launched their MIM powder-based machines. With a longer history and broader customer base, metal injection molding powders are currently cheaper than the metal powders required for additive manufacturing processes such as Direct Metal Laser Sintering (DMLS) or Electron Beam Melting (EBM). However, it has often been pointed out that material cost is not the only challenge when it comes to scaling metal 3D printing; repeatability/reliability, cycle time, post-processing, and capital investment are just some of the other considerations. Potential customers will no doubt be happy to pay less for materials.
Speaking ahead of the Metal Jet S100’s launch, Pastor described the platform as the “first introduced that is prepared to economically bring parts at scale. ” HP’s metal 3D printing boss added that the system has been built with a “focus on total cost of ownership,” in a way that ensures “the variable cost of a part is the point at which users can scale production.”
Launching the Metal Jet S100
So, how does HP’s first Metal Jet 3D printer work? As the company has now revealed, the Metal Jet S100 comes fitted with a 430 x 309 x 200 mm powder bed onto which droplets of material are jetted by six HP Thermal Inkjet printheads attached to two print bars, equipped with a total of 63,360 nozzles.
Using these printheads, the system is capable of precisely placing up to 630 million nanogram-sized drops of liquid binder per second layer-by-layer to form parts with a resolution of 1,200 dots per inch (dpi).
In practice, the Metal Jet S100 is designed to be modular, so more than one can be installed to create a continuous production line as part of a four-step process. After print preparation and manufacturing via HP’s powder management station, users can then debind parts using its curing station before removing any excess powder with any third-party system of their choosing.
To help realize the potential of this automated process, HP has begun working with partners GKN, Parmatech, Cobra Golf, the Legor Group, and Volkswagen. User-wise, the technology has also been adopted by initial clients like Domin Digital Motion, Lumenium, and Schneider Electric, the latter of which has already harnessed it to optimize the production of industrial metal air filters.
“This metal air filter is used in circuit breakers for when you have an inspected electric arc, and you need this not to affect the rest of the installation,” explained Pastor. “Usually, these filters are made through traditional measures, and it’s very, very expensive. We’ve been able to cut the time to produce it, and make weight reduction improvements, as they’re now 20% more compact. ”
Speculators have argued that the massive gap between announcement in 2017, and launch in 2022 of the HP Metal Jet was a deliberate tactic. The announcement giving pause to potential customers who might defer their capital investments knowing an HP metal 3D printer was on the horizon. Will the success of HP’s efforts with Multi Jet Fusion translate into similar results in the metal 3D printing space?
Furthermore, it is noteworthy that the number of additive manufacturing companies producing MIM-based 3D printing systems is relatively small – with an element of cross-pollination.
Schneider Electric’s Metal Jet-3D printed 690V power filters. Photo via Schneider Electric, HP.Technical specifications and pricing
Below are the technical specifications for the HP Metal Jet S100 3D printer. Debuted at IMTS 2022, the system is available to order now in the US, Western Europe and China, and is expected to be made widely available by h2 2023. Pricing information has been requested from HP and the article will be updated.
Technology | HP Metal Jet |
Build Volume | 430 x 309 x 200 mm |
Build Speed | 1,990 cc/hr8 |
Layer Thickness | 35 – 140 μm |
Print resolution (X,Y) | 1,200 dpi |
Printhead system | 6 Thermal Inkjet Printheads (63,360 nozzles) |
Dimensions | 2,975 x 1,350 x 2,410 mm |
Weight | 851kg |
To stay up to date with the latest 3D printing news, don’t forget to subscribe to the 3D Printing Industry newsletter or follow us on Twitter or liking our page on Facebook.
While you’re here, why not subscribe to our Youtube channel? featuring discussion, debriefs, video shorts and webinar replays.
Are you looking for a job in the additive manufacturing industry? Visit 3D Printing Jobs for a selection of roles in the industry.
Featured image shows a facility fitted with Metal Jet S100 3D printers. Photo via HP.
Tags Desktop Metal digital metal Domin Digital Motion GKN HP IMTS 2022 Legor Group Lumenium markforged Ocado Parmatech Ramon Pastor Schneider Electric Tim Weber Toyota Volkswagen
Paul Hanaphy
Paul is a history and journalism graduate with a passion for finding the latest scoop in technology news.
Overview of HP 3D printers at IMTS 2018 / Sudo Null IT News
Video
HP Metal Jet
Characteristics
- Print area — 430x320x200 mm0018
- Layer thickness - from 50 microns
- Material - AISI 316 steel
- Price - on request
According to the company's representatives, HP Metal Jet provides an increase in productivity up to 50 times and has a lower cost of the resulting products, compared with counterparts working on other technologies.
The HP Metal Jet features twice the number of print lines and four times the number of nozzles compared to competing solutions.
Volkswagen will be an early adopter of the HP Metal Jet as the automaker plans to make parts from stainless steel.
The high precision and low cost of prints make the HP Metal Jet a top competitor for a range of technologies from SLM to injection molding.
Metal Jet sales start in 2019. The cost will not exceed 400 thousand dollars. The price tag for competing solutions starts at $1 million.
HP Jet Fusion 4200
Features
- Print area up to 380x284x380 mm.
- Layer thickness - from 80 microns.
- Material - polyamide 11 and 12
- Price - on request
In addition to the Metal Jet, Hewlett-Packard's pavilion featured machines from the Jet Fusion line - the Jet Fusion 4200 industrial SHS machine and the 500/300 series color SLS printer.
SHS (selective heat sintering) technology is similar to SLS. The main difference is that a thermal print head is used instead of a laser. According to Hewlett-Packard, the Jet Fusion 4200 print speed is 10 times faster than competitors' SLS solutions.
The speed, ease of use, and relatively low cost of $200,000 or more make the Jet Fusion 4200 a replacement for plastic injection machines. Material for printing - polyamides "nylon 11" and "nylon 12".
HP Jet Fusion 500/300
Features
- Printable area - up to 332 x 190 x 248 mm
- Layer thickness - from 80 microns
- Material - polyamide 11 and 12
- Price - on request
The HP Jet Fusion 500/300 Series SLS printers are designed for plain and full color polyamide printing. The price of devices - from 50 thousand dollars - this makes them affordable for small and medium-sized businesses.
The Jet Fusion 500 and Jet Fusion 300 models feature "the world's first integrated and automated material feed system," as the manufacturer calls it, which simplifies the 3D printing process, reduces user intervention, and improves overall efficiency. The devices support major file formats such as OBJ, VRML, and 3MF.
All post-processing and preparation of the powder for reuse does not require additional modules - these processes take place inside the plant.
Sales of HP Jet Fusion 500/300 series 3D printers in Russia will begin in 2019. By pre-ordering from the Top 3D Shop, you can get the actual prices and purchase offer for these models at the time of sale.
Total
HP continues to develop the market for professional 3D printing equipment, applying its own new developments in its products. The presented models - HP Metal Jet, Jet Fusion 500/300 and Jet Fusion 4200 - promise the user not only the traditional quality for this manufacturer, but also the lower cost of prints, which is no less important.
Looking for a business printer? Write to us at [email protected] and we will select the best device for your requirements and capabilities.
Want more exciting news from the world of 3D technology?
Follow us on social. networks:
The most expensive 3D printers in the world
- home
- News AT
- World
- The most expensive 3D printers in the world
Various technologies do not stand still, they are constantly developing. This article proposes to consider the evolution of industrial 3D printers today, which are the most expensive in the world and why.
3D printers are unique in terms of the variety of different 3D printing methods, materials used and their applications. You can spend as little as $100 to get a reliable 3D printer to make a huge variety of parts from affordable plastic material. On the other hand, you can spend over a million dollars to buy a 3D printer to 3D print parts with large and complex construction geometries. They can be used in the aerospace industry, the production of space satellites or miniature biocompatible devices for medical purposes. The most expensive 3D printers on the market today use 1 to 12 powerful lasers to fuse metal powder, sinter polymer materials, or polymerize resin, and 3D printing from a given 3D model occurs by applying the powder layer by layer, which is a process additive manufacturing.
It can be noted that the size of the 3D printer does not determine how expensive the 3D printer will be. Today, the price often depends on advanced patented technologies and features that allow a 3D printer to produce fast and high-quality 3D-printed parts without requiring special technical knowledge from the operator.
Some of the most expensive printers are not even for sale. Carbon 3D's 3D printers are available for rent only, which allows them to be used by many users. Others use their 3D printers on a project-by-project basis, such as the Vulcan construction printer from homebuilder Icon 3.
Stargate, the world's largest metal 3D printer built by Relativity Space to 3D print rockets, it's not for sale, but if it was, it would definitely make our list. Many of the most exciting technologies in 3D printing can only be used for custom 3D printing, not for purchase. (Source: Relativity Space)
Let's look at the criteria that affect the cost of a modern industrial 3D printer.
Features 3 D -Printers affecting their price:
- The uniqueness of the technology when creating
- How automated the processes in the 3D printer
- Dimensions of the working chamber
- allowing the quality control
- software
- Numerous controls and adjustments
- Controlled environment inside the working chamber (use of inert gas, the possibility of heating/cooling the working platform)
Let's break down these features:
Features that drive price increases for 3D printers include printer technology-specific software, real-time 3D printing control systems, and anything that automates processes that sometimes are performed manually in cheaper systems (layer leveling, subsequent post-processing or powder sieving) or processes that require knowledge of metallurgy or polymers.
Production technology requiring a vacuum chamber in a 3D printer, filling the working chamber with an inert gas, or printers that are certified for use in clean rooms and having these characteristics are significantly reflected in the final price of this equipment.
The materials used in the 3D printing process also have a significant impact on the final cost of a 3D printer. Many 3D printers only work with proprietary materials that have been developed by the manufacturer for that 3D printer. They can be metal powder, special resins filled with carbon fiber particles, and unique polymer powders. At this point in time, it is possible to 3D print anything from pure gold to advanced engineering plastics on 3D printers, even in the harsh environment of space.
There are 3D printers that can 3D print multiple materials in one job, and there are multicolor 3D printers that are also in the higher price segment.
THE MOST EXPENSIVE 3 D -PRINTERS
The 3D printer manufacturers discussed below are reluctant to publish exact prices for their products. This is due not only to competition, but also to the fact that 3D printers have a basic package, as well as a package with additional options according to customer requirements. That said, with that in mind, below is a look at some of the most expensive 3D printers available today - all costing over half a million US dollars - and what they provide.
E-PLUS3D EP-M450H
3D printer EP-M450H LPBF (Source: E-Plus 3D)
Chinese company E-Plus3D produces industrial metal 3D printers with a large construction of construction for additive manufacturing for various industries in the country. These 3D printers are used in the aerospace, automotive, electronics, and engineering industries to produce not only large-sized parts such as heavy-duty molds, but also mass-produced parts.
The EP-M450H Metal 3D Printer is the company's largest 3D printer with a build chamber of 456 x 456 x 1080 mm, producing 99.9% density metal parts from a wide range of materials at a speed of 55 cm³ per hour.
XJet Carmel 1400C
Israeli company XJet has developed a unique ceramic 3D printing technology. NanoParticle Jetting (NPJ) technology allows the production of metal and ceramic parts with a high level of detail, smooth surface roughness and geometric accuracy. The high cost of this 3D printer is not only due to the technology itself, patented materials that make this printer a serious investment, but also to the advanced automation of the 3D printer itself, which makes it easy to use.
Carmel 1400C, equipped with one of the largest 1400 cm² work platform in the industry, which allows you to simultaneously produce several ceramic parts.
SLM Solutions NXG Xll 600
NXG XII 600 Large Metal 3D Printer (Source: SLM Solutions) range of printers, but its NXG Xll 600 is what the company says is a revolution in industrial additive manufacturing. The NXG XII 600 was designed for high-volume additive manufacturing and features the industry's first 12 1,000W lasers with a 600x600x600 build chamber. Lasers provide high build speed up to 1000 cm 3 /h and capacity not available for other machines.
In addition to lasers, the NXG Xll 600 has all the benefits that SLM Solutions customers have been asking for over the years, including automatic start-up, laser focusing, closed powder feed and material screening, and other latest developments.
UpNano NanoOne Bio
The Austrian company UpNano has developed a two-photon 3D printer using hydrogel-based bio-ink that allows direct printing of 3D structures containing living cells, both at the meso- and microscale. The NanoOne Bio printer is based on the NanoOne line of laser printers capable of creating structures of 12 orders. The new hydrogel is the only commercially available resin that allows live cells to be embedded directly from culture plates into 3D printed structures for biological applications.
UpNano claims that the combination of X Hydrobio INX U200 and NanoOne Bio opens up new possibilities in biomedical research and development, both in industry and academia, allowing pharmaceutical companies and research institutes to create cell models that mimic natural growth conditions in the body person.
Black Buffalo 3D
Black Buffalo's new 1G construction printer (Source: Black Buffalo)
Black Buffalo 3D, an American company based in South Korea, officially unveiled its Nexcon 1G earlier this year, which is a 3D printer for building houses and other large concrete objects. The printer can create a 92.9 square meter structure in less than 20 hours. It uses Black Buffalo's patented cementitious material, the company calls it ink, that can be dyed to a chosen color and is also customizable to 3D print locally according to the temperature, humidity and altitude conditions of the area.
The Nexcon 1G is a modular 3D construction printer that can be extended along the X, Y and Z axes to scale up (or down) a project up to three stories high. The 1G printer is unique in that users can reposition the base rails and move the printer to a new printable area without having to remove the X or Z axis.
Optomec LENS 860
Energy Deposition (DED), which allows the recovery of large titanium components, such as those used in aircraft engines. Optomec offers several models of 3D printers that have large build chambers like 860x600x610 and laser power of 3 kW.
The LENS 860 machining systems are ideal for the fabrication, repair or coating of medium to large metal parts.
ExOne S-Max Pro
While many ExOne printers (now owned by Desktop Metal) are still very affordable given that high volume 3D printers can cost quite a few zeros.
3D printers are used to 3D print complex and detailed sand molds and cores for foundries producing large metal parts for industrial use. The S-Max Pro features a 1,260 liter build chamber for fast 3D printing of sand molds and cores. A new automated print head enables fast 3D printing, while improved sand compaction ensures the density and strength of complex sand mold designs. As the most advanced system in the ExOne family of sand 3D printers, the S-Max Pro is focused on continuous 24/7 production and offers Industry 4.0 integration with cloud connectivity and real-time machine monitoring.