How to strengthen 3d printed parts
5 Tips to Strengthen 3D Printed Parts
Structural integrity in 3D printing is important as 3D prints must not collapse while functioning. 3D printing is a popular manufacturing process with wide acceptance because of the quality it delivers. In terms of improving the strength of 3D printed parts, there are many things that come to play.
This article will provide details on how to make strong 3D prints and it is helpful for those either having a personal 3D printer or want to outsource to rapid prototyping services. If you have a personal 3D printer, you will learn how to tweak the settings to achieve the best results. If you want to outsource your projects, you will get information about different materials and recent post-processing technologies that will give you an idea of how to communicate to the prototyping service better. Go through a simplified version of how to make 3D printed parts strong.
Adjust Printer SettingsHaving a 3D printer for your personal works is more efficient and effective in personal product manufacture. However, unless you are deeply into 3D printing with knowledge surrounding its use, you might have a little trouble making a strong 3D print. There are many settings on your 3D printer that you can tweak for a high-quality and strong print. Below are how to make strong 3D prints using them.
One way of increasing the strength of a 3D print is by increasing the interior density. The interior density ranges from 0% to 100%, with zero means totally hollow while 100 means totally solid.
Theoretically, having a 100 infill density should make your 3D print very strong. However, practically most designers have noticed that anything beyond 70% has a lesser impact on strengthening the 3D print. Instead, there is a tremendous increase in filament use, printing time, cost, and burden on the 3D printer.
Note: Have at least a 20% infill density for strength and, if possible, tweak the wall thickness (explained below) before increasing the infill density.
The wall thickness of a 3D printed material is measured by “Wall Line Count” and “Outer Line Width.” It shows how thick the wall and increasing it is a critical way to make strong 3D prints. Increasing wall thickness will increase strength as 3D printed parts have more strain on the outside than the inside.
Not only does increasing the wall thickness strengthen the printed material, but it also improves overhangs (geometry shapes in 3D models that are difficult to print) and water tightness.
Note: For a regular product, at least have a wall thickness ≥ 1.2mm. You can then increase it for more strength.
Use Thinner LayersUsing a thin layer will lead to better adhesion and density between subsequent layers, which strengthens 3D printed parts. Designers have said that going as low as 0.1mm (100 microns) will maximize strength. However, there is also a complementary increase in printing time.
Another way of reinforcing 3D prints is by using the right infill pattern. Infill patterns work with infill density, and they serve as an internal support structure for 3D prints. They also add some stiffness to the part and prevent wall deformation. On how to make strong 3D prints using infill patterns, you should use a dense infill pattern ranging from 30-50%.
The type of infill pattern you use also determines how strong the 3D print will be. Three infills you can try are listed below:
· Triangular Infill PatternTriangular infill patterns are strong as they have a lesser chance of deforming, and they provide the best support structure. Most 3D enthusiasts attribute this to triangles being the strongest shape.
Using a triangular infill also improves print speed due to the straight-line movement of the printhead. Consequently, strength and speed make triangular infills the best choice among many 3D enthusiasts.
Rectangular infills can achieve 100% infill density due to their grid of parallel and perpendicular extrusions. Like the triangular infill, it also has a high print speed due to the print head’s straight-line movement.
· Hexagonal Infill PatternThey have tessellated hexagons and the highest strength to weight ratio. Unlike the previous two infill patterns, printing is slow due to the printhead constantly changing direction, but they are also effective in reinforcing 3D prints.
Adjust Flow RateAdjusting the flow rate can also be an ideal method to make 3D printed parts strong. However, using this method, you must be careful such that you do not cause under and over extrusion. Therefore, most designers make sure they only make small changes.
You can adjust the flow rate for the following:
- Wall Flow (Outer Wall Flow & Inner Wall Flow)
- Infill Flow
- Support Flow
You can adjust the flow rate to strengthen 3D prints. However, most people adjust the flow rate to fix other 3D printing issues such as the inability to achieve volumetric flow and to improve accuracy.
According to Cura, a popular slicer, you can strengthen your 3D prints by adjusting the line width to an even multiple of the layer height. However, you must be careful as this setting is directly related to extrusion, i.e., a massive change in line width can lead to over and under extrusion.
Reduce CoolingCooling is an important process in 3D printing which affects the adhesion of layers after setting. Quick cooling can reduce the adhesion due to a subsequent layer’s inability to bond with another. However, cooling also depends on the material you are using. For example, PLA works best under the action of a strong cooling fan. Therefore, you should reduce the cooling rate based on the material you are working with.
Select Strong Material to Make Strong 3D PrintsIn 3D printing, there are some materials that are known to be weak. Therefore, making a strong 3D print can be about using strong 3D printing materials. There are three major materials with properties synonymous with strength.
ABS is a great 3D printing material for making strong 3D prints that are not suitable for heavy use. It is a thermoplastic with tough and light properties, which makes it a top plastic polymer in 3D printing.
PLAPLA is an expensive 3D printing material suitable for prints with heavy use and high resolution. It has a tensile strength of 7250 psi but will degrade on exposure to light.
PETGThis is a new filament recently gaining popularity due to its strength. It has a tensile strength of about 4100-8500 psi which makes it stronger than PLA and weaker than ABS. However, it is less flexible than PLA and more than ABS.
Choosing the Right MaterialTo choose the right material of the three, you have to consider the resistive force, bonding between later, bending forces, rigidity, and ability to resist impacts. Below is a comparison of the three in terms of each:
- Resistive force: PETG > PLA > ABS
- Bonding between layers: PETG > ABS and PLA
- Bending force: ABS > PETG > PLA
- Impact resistance: ABS = PETG > PLA
To learn more about the differences between PLA vs ABS, check out the article on RapidDirect.
Determine Part OrientationAnother way of reinforcing 3D prints is using part orientation. Part orientation is the positioning of a part on the 3D printer. 3D printers work by depositing thin layers of melted materials at a gradually increasing height. The gradual increase in height is what forms the 3-dimensional parts. On the deposition of a layer, it bonds with the previous layer. However, the interface between the two layers is a weak point, and 3D prints break at these interfaces.
A good way to understand this is by making a bracket used for a shelf. The thing you will notice is that the largest force will act downward where the bracket attaches to the shelf. Therefore, it is better to print on a side with an interface that is opposite the force.
If the part orientation is challenging, you should use materials that have a better bonding tendency, for example, PETG. Also, note that part orientation will affect the smoothest of the print surface and the print cost due to the requirement for many materials.
Applying Epoxy Coating to 3D PrintsThis is not a direct way of making strong 3D prints as it occurs after printing. It involves using epoxy/polyepoxide to strengthen 3D prints. Epoxy coating is an insoluble surface coating made from a hardener and epoxy coating. It is solvent resistance, durable and tough, making it a suitable way to coat materials such as PLA, ABS, and SLA.
Applying an epoxy coating to 3D prints is an easy task. Follow the steps below on how you could go about it:
- 3D prints the product according to the product design
- Let it cool and clean the surface.
- Pour a little part in a cup and warm it to achieve a viscous fluid
- Using a brush, apply the epoxy coating using a brush on the model without allowing the coating to drip down its side.
Also, use small brushes to get access to crevices and corners.
- Allow the 3D print to dry.
You do not need to use much as a little of the hardener can coat and strengthen the print. Applying epoxy coating on the 3D print makes it stronger and provides it with a clear and shiny surface.
Other Considerations to Make 3D Printed Parts StrongTweaking the 3D printer settings is not the only way to make a 3D print strong. Aside from the epoxy coating, which is a post-processing method, there are other methods you can use. Below are two important methods popular recent.
Annealing 3D PrintsAnnealing is a method that subjects 3D prints to an increase in temperature for strengthening purposes. According to the test, annealing is said to cause about a 40% increase in strength after use. It is compatible with materials such as PLA, ABS, PETG, and ASA.
Annealing is important in strengthening 3D prints as the structure of plastic makes it prone to failure. Before 3D printing, plastics have an amorphous/unorganized microstructure. However, when you heat the 3D prints, the amorphous structure reorganizes itself to a crystalline form which makes such 3D prints prone to failure.
Annealing is essential here as it changes 3D prints’ crystalline structures from large to small crystals. You can anneal the plastic polymer or the finished 3D printed product. To anneal the plastic polymer or 3D printed parts, heat it at a temperature above its glass transition point and below its melting point.
Electroplating Plastic 3D printsElectroplating is a popular method due to it being practical and affordable. It involves putting the 3D print in an electrolyte and a plating metal (popular industrial metals are zinc, chrome, and nickel. On passing an electric current through the electrolyte, the metallic ion forms a coating around the 3D print. This leads to the formation of durable and long-lasting 3D prints.
While suitable for the purpose, its disadvantage is that it would need many layers for making better 3D parts with high strength.
A strong 3D print is one that does not collapse on use, which makes knowing how to make strong 3D prints. Very important. There are three ways of strengthening 3D prints. One is during the process itself (by tweaking the 3D printer’s Settings), using the right materials, and after-process treatments. Using any of the methods, you have a chance of making strong 3D prints or talking to or communicating with the prototyping service on how to strengthen 3D printed parts.
RapidDirect – Provide Custom 3D Printing Services3D printing is a popular method used for its quality, efficiency, and effectiveness, and its ability to make complex parts. However, improving strengthening a 3D print comes with advanced knowledge on how a 3D printer works, the right material to use, and post-processing techniques.
If you desire a 3D print with the right attributes in the form of strength, durability, aesthetics, and quality, partnering with RapidDirect, one of the best rapid prototyping services in China, is a great choice. We provide custom 3D printing services, and you can get an instant quote for custom machined parts and full-dimensional reports inspection reports. For anything related to 3D printing, contact us today.
Get an Instant Quote For 3D Printed Parts
FAQsHow do you reinforce PLA 3D prints?
PLA is one of the most frequently used materials in 3D printing. It has a huge tensile strength making it suitable for making structural parts. While strong, you can also reinforce PLA 3D prints using the methods highlighted above. Common methods of strengthening the 3D prints include applying epoxy, annealing, or electroplating.
What is the strongest 3D printable material?
Among all the printable materials used in 3D printing, polycarbonate is the strongest. It was dubbed the true king of desktop printing due to its strength (tensile strength of 9800 psi) and heat resistance. The heat resistance makes it require extraordinarily high temperature (bed should be at about 1450 while the head should be at about 2900. You will also need to enclose the material due to it warping in an open environment. Polycarbonate is suitable for making high-strength functional components.
How do I make prints stronger?
There are many ways you can use to make prints stronger. You can tweak your 3D printer’s setting, you can change the materials to stronger materials, and you can use after-processing methods such as coating with epoxy materials, annealing, and electroplating.
11 Ways How To Make 3D Printed Parts Stronger – A Simple Guide – 3D Printerly
3D prints have many functional uses which can require a good amount of strength to perform properly. Even if you have some aesthetic 3D prints, you’ll still want a certain level of strength so it can hold up well.
I decided to write an article detailing how you can make your 3D printed parts stronger, allowing you to have more confidence in the durability of objects you are making.
Keep on reading through to get some good tips on how to improve and strengthen your 3D prints.
Why Are Your 3D Prints Coming Out Soft, Weak & Brittle?The main cause of brittle or weak 3D prints is the accumulation of moisture in the filament. Some 3D filaments naturally tend to absorb moisture from the air due to overexposure. Trying to heat filament to a high temperature that has absorbed moisture can cause bubbles and popping, leading to weak extrusion.
What you want to do in this situation is dry your filament. There are a few ways to dry filament effective, the first method being to put your filament spool in an oven at low heat.
You first have to make sure your oven temperature is correctly calibrated with a thermometer because oven temperatures can be quite inaccurate, especially at lower temperatures.
Another more popular method is to use a specialized filament dryer like the SUNLU Filament Dryer from Amazon. Most people who use this are very happy with their results, being able to save filament they thought were no longer effective.
There have been a few mixed reviews though with people saying it doesn’t heat up enough, though these may be faulty units.
One user who 3D prints Nylon, which is notorious for absorbing moisture used the SUNLU Filament Dryer and said his prints are now coming out clean and beautiful.
I’d recommend that you use an extra layer of insulation like a large plastic bag or a cardboard box to retain the heat in.
Other factors that may contribute to a soft, weak, and brittle print is the infill density and wall thickness. I’ll take you through the idea methods to improve strength in your 3D prints below.
How Do You Reinforce & Make 3D Prints Stronger? PLA, ABS, PETG & More1. Use Stronger Materials
Instead of using materials that are known to be weak in some cases, you can choose to use materials that can hold up well with strong forces or impact.
I’d recommend going with something like Polycarbonate with Carbon Fiber Reinforcement from Amazon.
This filament is gaining plenty of traction in the 3D printing community for providing real strength in 3D prints. It has over 600 ratings and is currently at 4.4/5.0 at the time of writing.
The best thing about this is just how easy it is to print compared to ABS, which is another stronger material that people use.
Another widely used filament that people use for functional 3D prints or for strength in general is OVERTURE PETG 1.75mm Filament, known to be a little stronger than PLA, and still pretty easy to 3D print with.
2. Increase Wall Thickness
One of the best methods to strengthen and reinforce your 3D prints is to increase your wall thickness. The wall thickness is simply how thick the exterior wall of your 3D print is, measured by “Wall Line Count” and “Outer Line Width”.
You don’t want a wall thickness less than 1.2mm. I’d recommend having a minimum wall thickness of 1. 6mm, but for more strength, you can definitely go higher.
Increasing wall thickness also has the benefits of improving overhangs as well as making 3D prints more watertight.
3. Increase Infill Density
The infill pattern is the internal structure of the object being printed. The amount of infill you need depends mainly on the object you are creating, but generally speaking, you want an infill of at least 20% for good strength.
If you want to go the extra mile, you can raise it up to 40%+, but there are diminishing returns to increasing infill density.
The more you increase it, the less improvement in strength you’ll get in your 3D printed part. I’d recommend first increasing your wall thickness before increasing infill density so high.
Generally, 3D printer users don’t exceed 40% unless they need some real functionality and the print will be load-bearing.
In many cases, even 10% infill with a Cubic infill pattern works pretty well for strength.
4. Use a Strong Infill Pattern
Using an infill pattern built for strength is a good idea to reinforce your 3D prints and strengthen them. When it comes to strength, people tend to use Grid or the Cubic (Honeycomb) pattern.
The Triangle pattern is really good for strength too, but you will need to have a good top layer thickness to get an even top surface.
Infill patterns work closely with infill density, where some infill patterns at 10% infill density will be much stronger than others. Gyroid is known to perform well at low infill densities, but it isn’t a very strong infill pattern overall.
Gyroid is better for flexible filament and for when you might use dissolvable filament like HIPS.
While you slice your 3D print, you can check out how dense the infill actually is by checking the “Preview” tab.
5. Changing the Orientation (Extrusion Direction)
Simply placing the prints horizontally, diagonally, or vertically on your print bed can change the strength of the prints due to the direction that the 3D prints are created.
Some people have run tests on rectangular 3D prints that are oriented in different directions, and found significant changes in part strength.
It’s mainly to do with the build direction and how 3D prints are built through separate layers that bond together. When a 3D print breaks, it’s usually going to be from a separation of the layer lines.
What you can do is figure out which direction your 3D printed part is going to have the most weight and force behind it, then orient the part to not have layer lines in that same direction, but opposite.
A simple example would be for a shelf bracket, where the force is going to be pointing downwards. 3D-Pros showed how they 3D printed a shelf bracket in two orientations. One failed miserably, while the other stood up strong.
Instead of having the orientation flat on the build plate, you should 3D print the shelf bracket on it’s side, so its layers are built across rather than along the part which has force on it and is more likely to break.
This can be confusing to understand at first, but you can get a better understanding by seeing it visually.
Check the video below for guidance on orienting your 3D prints.
6. Adjust Flow Rate
Adjusting your flow rate slightly is another way to reinforce and strengthen your 3D prints. If you choose to adjust this though, you want to make fairly small changes because you can end up causing under extrusion and over extrusion.
You can adjust the flow for specific parts of your 3D print such as the “Wall Flow” which includes the “Outer Wall Flow” & “Inner Wall Flow”, “Infill Flow”, “Support Flow”, and more.
Though, in most cases, adjusting the flow is a temporary fix for another issue so you would be better to directly increase line width rather than adjust flow rates.
7. Line Width
Cura, which is a popular slicer mentions that adjusting your line width to an even multiple of the layer height of your print can actually make your 3D printed objects stronger.
Try not to adjust Line Width too much, similar to the Flow Rate because it can lead to over and under extrusion again. It’s a good idea to adjust print speed to indirectly adjust the flow and line width to a certain extent.
8. Decrease Print Speed
Using a lower print speed, as mentioned above can increase the strength of 3D prints because it can leave more material behind to fill in any gaps that would occur if the speed was too high.
If you increase your Line Width, you want to also increase Print Speed to keep a more constant Flow Rate. This can also improve print quality when balanced correctly.
If you do decrease your print speed, you may have to decrease your printing temperature to account for the increased period of time your filament will be under heat.
9. Reduce Cooling
Cooling parts too quickly can lead to bad layer adhesion since the heated filament doesn’t have enough time to properly bond with the previous layer.
Depending on what material you are 3D printing, you can try to reduce your cooling fan rate, so your parts can bond together strongly during the printing process.
PLA works best with a fairly strong cooling fan, but can try to balance this with printing temperature, print speed, and flow rate.
10.
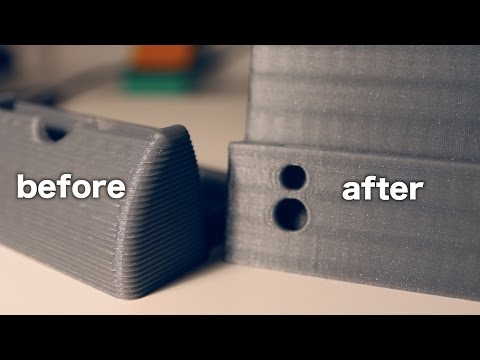
The use of thicker layers leads to better adhesion between layers. Thicker layers will present more gaps between the adjacent parts of the layers. Tests have show that larger layer heights have been observed to produce 3D prints that are stronger.
A layer height of 0.3mm has been shown to out-perform a layer height of 0.1mm in the strength category. Try using a larger layer height if print quality is not essential for the specific 3D print. It is also beneficial because it speeds up printing times.
Check the video below for more details about strength testing for different layer heights.
11. Increase Nozzle Size
Not only can you decrease the printing time of your 3D prints, but you can also increase the strength of your parts by using a larger nozzle diameter like 0. 6mm or 0.8mm.
The video below by ModBot goes through the process of just how much faster he could print, as well as the increased strength he got from the increase in layer height.
It’s related to the increased flow rate and increased layer width, leading to a more rigid part. It also improves how smoothly filament can extrude and create better layer adhesion.
Other Things to Try to Strengthen 3D PrintsAnnealing 3D Prints
Annealing 3D prints is a heat treatment process of putting 3D printed objects under an increased temperature to strengthen its integrity. With some testing, people have shown increases in strength of 40% according to Fargo 3D Printing’s testing.
You can check out Josef Prusa’s video on annealing, where he tests 4 different materials – PLA, ABS, PETG, ASA to see just what kind of differences occur by annealing.
Electroplating 3D Prints
This practice is becoming more popular because it is practical and affordable. This involves immersing the printing part in a water and metal salt solution. Electric current is then passed through it, thus causing metal cat-ions, like a thin coating, to form around it.
The result is durable and long-lasting 3D prints. The only downside is that many layers may be required if you want a stronger print. Some plating materials include Zinc, Chrome, and Nickel. These three have the most industrial applications.
What this does is simple, to orient the model such that the weakest point, which is the layer boundary is not so exposed. The result is stronger 3D prints.
For more on electroplating 3D prints, check out the video below.
Check out another great video on electroplating, with simple instructions on how to get great finishes on your models.
How To Strengthen Finished 3D Prints: Use of Epoxy Coating
When you are done printing the model, an Epoxy can be applied correctly to strengthen the model after printing. Epoxy, also known as polyepoxide is a functional hardener, used to make your read-made model stronger.
With the aid of a brush, gently apply the epoxy coating to the 3D prints in a way that the epoxy will not drip down. Use smaller brushes for crevices and hard to reach corners so that every part of the exterior is well covered.
A very popular 3D printing epoxy coating that tons of people have had success with is the XTC-3D High Performance Print Coating from Amazon.
It works with all sorts of 3D printed materials like PLA, ABS, SLA prints, as well as even wood, paper and other materials.
A kit of this epoxy is very long-lasting because you don’t need to use much at all to get good results.
Many people say “a little goes a long way”. After the epoxy cures, you get some extra strength and a lovely clear and shiny surface that looks great.
It is a simple thing to do, but if you would like to know more about applying an epoxy coating to 3D prints, check out the video by Matter Hackers.
How to Strengthen Resin 3D Prints
To strengthen resin 3D prints, increase the wall thickness of the model if it’s hollowed out to around 3mm. You can increase durability by adding around 25% flexible resin to the resin vat so it has some flexible strength. Make sure not to over cure the model which can make resin brittle.
How to make a 3D printed part more durable
As we are all well aware, parts printed on a regular home 3D printer are not as strong and last as long as the original ones. We thought it would be great to learn how to somehow strengthen the printed parts, and worked on this idea a bit.
Such stronger parts will allow us to use them in real work, under high load. Then, instead of looking for original replacement parts for broken ones in gadgets, robots, cars, mechanical toys, or for any project in development, we can simply print them.
The need for this guide came to the author when he bought bike bags on eBay. One for a friend, one for myself. The attachment of the bags meant that the handlebars were one inch (2.54 cm) thick and barely fitted a women's bike. The handlebar of the men's bicycle had a diameter of 3.15 mm, and the mount did not fit on it.
Therefore, the idea came up to make a part according to the size of the corresponding fastener by printing it on a 3D printer.
Step 1 Required part
Here is the node to be reproduced on the 3D printer.
To print something, you first need 3D model files. They, respectively, need to be found and downloaded on the Internet or developed independently. The second option seemed to be the only one possible, since it was impossible to find ready-made 3D models for such a specific part, and it was necessary to modify the one that was available so that it fit on the steering wheel.
However, everyone knows that 3D printed parts are not durable. Normally printed, this knot would not be strong enough to securely hold a heavy bag on a bumpy road. Then the idea arose to somehow strengthen this part, giving it enough strength.
The author has been involved in ship modeling for several years and had the opportunity to see how layers of fiberglass and epoxy make even thin plywood parts stronger, as a result of which they can withstand high loads without problems.
Therefore, in this work, it was decided to use fiberglass and epoxy adhesive-resin.
The original plan was to take a drawing of the part, make the necessary dimensional changes, and cover everything with fiberglass cloth and epoxy. So, let's start modeling.
Step 2. First draft
The part should look like this. All sizes are adjusted, everything as a whole is enlarged and thickened. The surfaces have also been enlarged so that fiberglass can be glued on them.
In addition, grooves are provided on each side to fill them with epoxy for extra strength. Through holes are also modeled to make it easier for the assembly parts to connect to each other and to allow fiberglass and resin to connect them from the inside.
Part printed on the Up printer and checked to see if it fits.
The type of filling was chosen as lattice, which made it possible to leave enough empty space inside the part. In a normal situation, this reduces strength, but this was done deliberately. A few more holes were drilled into the piece to allow the epoxy to penetrate and reinforce it.
Step 3 Apply fiberglass and epoxy to the first project
This is the messiest part of the job. Epoxy and fiberglass are difficult to work with. Everything sticks everywhere so that you can hardly wash it off later.
First, strips of fiberglass fabric were glued to both halves of the part to make them stick together better.
Then everything was laid out on a piece of nylon, since epoxy, fortunately, does not stick to nylon so fatally. After that, the epoxy was applied to the surface of the part, a piece of fiberglass cloth was cut to the appropriate shape and size, on top of which the epoxy glue was again applied. There was so much glue that the fiberglass became transparent.
This whole procedure was repeated for the other side of the part, after which the resin cured for a day. Even a little more, so that everything is held together tightly.
Step 4.
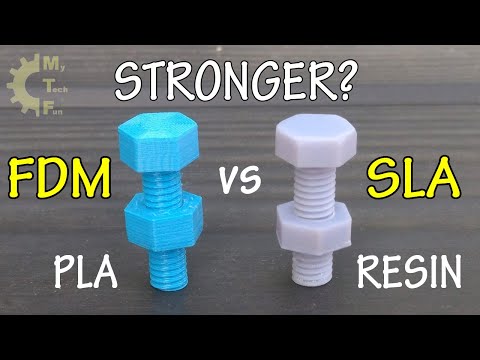
It was also decided to add more epoxy to the end grooves specially provided for this.
Step 5. Project Two
During the development of the first project, it was understood that the part would be partially filled with epoxy through additional holes drilled in it, and fiberglass impregnated with epoxy would hold it on the outside. In the process of printing the first part, the idea was born to model only its shell, and inside everything in general to make only epoxy glue and fiberglass.
And so, while the first project was freezing, it was decided to start modeling the second one. I wanted to compare both options in terms of strength and ease of manufacture. In the second project, a different approach was used to fill in two fragments of a part (two parts are needed for fastening).
The photo shows that the second project is an empty shell with walls 1 mm thick. The rounded fragment is separated from the larger one to simplify the filling process. It must then, when the epoxy hardens, be fixed with screws.
Step 6. Filling the second project with epoxy and fiber
To begin with, fiberglass was cut into small pieces, and the resulting shreds filled both parts of the part a little more than half. Then you need to add epoxy glue drop by drop and press the trim a little so that they are well saturated.
Step 7. Filling in further project 2. Fragment 1
Continue to drip and trample until all the fiberglass is saturated, after which we add more pieces of fiberglass, repeating this step until the final filling of the part. Now we fix the second fragment of the part with screws. In the end, the level of the mixture of epoxy and fiberglass should be up to the brim.
Almost the same for the smaller, rounded fragment.
Step 8. Filling in the project 2. Fragment 2
For this fragment, a slightly different approach was used: the part was not filled halfway from the very beginning. Only one layer of fiberglass was laid on the bottom, then another one - with an overlap on the edges. These layers were impregnated with epoxy until they became completely transparent, after which the following layers were laid one by one and pressed down to absorb the glue. A little epoxy was added every 2-3 coats.
The first method gave us a part with more epoxy and a little less fiberglass inside. With the second method, there is more fiberglass in the part and less epoxy between layers.
Step 9. Everything should now be cured
The parts were periodically checked, more resin was added to the voids formed when the resin was absorbed. Where necessary, fiberglass was added. It took about a day to fully dry. There are epoxy adhesives on the market that cure faster, you can also add more hardener to speed up the process. However, we do not recommend this, because it will only complicate the work and prevent the glue from penetrating into all corners.
Step 10. Assembling the finished assembly
The parts turned out pretty good, especially on the second project. Attaching them to the bag went without problems. They fit great. Now you need to attach the bag to the bike.
Step 11 Remove the plastic parts
This step was not really intended. It was supposed to simply use 3D printed and reinforced parts. But when it came to sanding, the printed "skin" simply began to break off at the corners, the rest was also removed without problems. This “skin” did not give any additional strength, therefore it was almost completely removed, and the part became a composite epoxy-fiberglass.
Step 12. Summary
The part held up without problems during a 20-day trip to Sweden, Poland, Germany and Denmark. The front bag was always filled to overflowing with food, a lot of bumpy roads were passed. The parts have served perfectly and are still stronger than stone.
Here are some more useful notes.
- Interestingly, epoxy does not adhere very well to ABS. That is why additional holes through which it will penetrate inside and fasten the structure are simply required.
- Reinforcing a part from the outside is much more difficult than filling it. The first option takes a lot of time, but the completed part is easier. Undoubtedly, a reinforced part is much stronger than a simply printed and unreinforced part. This is easy to check if you test the reinforced and non-reinforced parts for twisting. Fortified like a stone, the usual easily changes shape.
- The second hardening method is much simpler and produces a much neater result. After the resin has cured, almost nothing needs to be cleaned. And what happened has the strength of granite!
- Both fillings with different amounts of fiberglass give the same feeling of solidity and solidity. However, the one with more fibers, theoretically and almost without a doubt, should withstand more weight.
- In the second project, the assembly is heavier, since the inside is completely made of fiberglass and epoxy resin. The weight is slightly reduced after removing the surrounding plastic.
In this case, however, the dimensions of the part will also change. Therefore, the dimensions need to be thought about in advance and take into account the removal of plastic when modeling.
- In the second project, it is also possible to provide grooves, grooves and voids, then the weight can be reduced.
Strengthening a 3D Printed Part from Instructables.com
Processing 3D printed models
One of the problems that all fans of FDM 3D printing, without exception, encounter is the ribbing of external surfaces. Since the technology itself is based on the sequential application of layers of plastic, this effect cannot be avoided. You can, of course, make it less noticeable by increasing the vertical resolution of the printer (i.e. applying thinner layers), but you won’t be able to completely get rid of the ribbing.
PLA 3D model before and after torch treatment. The internal structure is visible under the sagging outer layer
Almost from the very first days of the RepRap project, the search began for methods of processing finished models in order to smooth surfaces. Emphasis was placed on two features of thermoplastics: the ability to melt when exposed to high temperatures and soften on contact with the appropriate chemicals.
As a rule, heat treatment does not give good results - it is quite difficult to control the heating of the surface, and this leads to plastic boiling, sagging or simply emitting toxic fumes. However, this method can be tried on solid PLA models.
Chemical treatment is more promising, but it also comes with its own set of challenges. In addition to technological problems, the problem of reagents is relevant - different plastics react with different solvents. If acetone perfectly dissolves ABS plastic, then it has almost no effect on PLA plastic. With limonene, everything is exactly the opposite.
The main chemical smoothing techniques still revolve around ABS plastic due to its high popularity and low cost of suitable solvents.
A typical ABS solvent is acetone. Its good dissolving power allows it to be used as an adhesive for component parts of ABS models, although a homemade mixture is usually used for this, produced by dissolving ABS chips in acetone. The same glue (only a thicker consistency) is often used to repair delaminations or cracks.
Along with increased aesthetics, an important factor in the development of smoothing methods is increased strength. The monolithic outer shell reinforces the models, preventing delamination and ensuring their tightness.
Hand sanding
Makeraser is a combination tool designed to also work on the outer surface of models models. However, processing with a brush is a laborious task, and even requiring a certain skill. After all, already softened plastic is easy to deform with the brush itself, that is, the hairs will leave a mark on the plastic, which may not even out before the acetone evaporates. It is possible to equalize pronounced irregularities with this method, but it is quite difficult to achieve a smooth surface.
The advantage of this treatment is the selective application of acetone, which avoids smoothing sharp corners. After all, a pyramid was built for Cheops, not a cone, right?
An attempt to create a special tool for manual processing was a device called Makeraser. Basically, it's a simple felt-tip pen with a reservoir filled with acetone or acetone glue and a built-in scraper to remove models from the platform. From a practical point of view, this tool is best suited for gluing parts of a model or applying ABS/Acetone glue to the build bed just before printing to combat underlayer curl.
Acetone dip
Failed surface leveling by dip
A more promising and simpler method is acetone dip. Exposure of the ABS model in undiluted acetone for about 10 seconds is sufficient to dissolve the outer layer of the model. The specific exposure time may vary depending on the quality of the original model and the concentration of acetone. Since the sale of pure acetone is regulated, a technical solvent can be used.
After exposure, the model must be exposed to air until the acetone has evaporated. The process may take about half an hour.
Although this method is quite fast, it is difficult to control the process. With excessive exposure, the model will simply begin to dissolve, quickly losing small features. In addition, contamination of acetone with plastic of the same color can lead to streaks on subsequent models dipped in the same solution. A more controlled process is acetone vapor treatment.
Probably the most efficient way to get glossy ABS models. This method requires placing the model in a container with a small amount of acetone at the bottom. The model itself should not come into contact with acetone, so the model should be placed on a platform or hung above the surface of the solvent. When installing on a platform, the material properties of the stand should be taken into account. Wood is not suitable for this task due to its porosity: the bottom surface of the model will stick to the wood, and it will be quite difficult to separate it. The best option is to use a metal stand.
It is advisable not to use wood as a platform
After placing the model, the container must be heated to increase the temperature of the acetone. Acetone also evaporates at room temperature, but too slowly. Please note that boiling acetone is not recommended, as this will cause condensation to accumulate on the model, which in turn can cause streaks. Thus, for best results, do not exceed the temperature threshold of 56°C.
A safe, homemade steamer that uses boiling water in an outer pot to heat the acetone in an inner pot.
Holding time varies greatly with the temperature of the acetone. So, when boiling, only a few seconds can suffice, while experiments at room temperature required up to 40 minutes of exposure. Fortunately, using a transparent container, you can determine the readiness of the model "by eye".
As with dipping, the completed model must be aired out before the outer surface hardens, avoiding unnecessary physical contact.
Both when immersing models in acetone and when working with steam, the wall thickness of the models must be taken into account. The shell must be thick enough to withstand the inevitable loss of the outer layer. In addition, especially subtle features may simply dissolve, and sharp corners will be smoothed out.
Safety Instructions
Successful Acetone Vaporization of an ABS Model
Acetone is not considered highly toxic, but care must be taken nonetheless. Inhalation of vapors can lead to pulmonary edema and pneumonia. A sign of poisoning is a feeling of intoxication, accompanied by dizziness. In addition, acetone causes irritation of the mucous membranes. When working with acetone, do not neglect personal protective equipment - goggles and gloves.
Particular attention should be paid to the flammability of acetone. Air mixtures with an acetone concentration of up to 13% by volume are explosive - when processing with acetone vapors, it is strongly recommended to work in a well-ventilated room and, if possible, use an exhaust hood. Do not use an open fire to heat acetone: since solvent vapors are heavier than air, they will displace air from the vessel, and once outside, they will cool and come into direct contact with the fire with all the ensuing consequences. It is also not recommended to tightly close the vessel, especially with strong heating, in order to avoid destruction under pressure.
Commercial options
Stratasys Finishing Touch Smoothing Station
In addition to the Makeraser described above, there are also commercially produced units for steaming both acetone and other solvents - dichloromethane, butanone, etc.
Stratasys manufactures a little-known but successful Finishing Touch that can process any variation of ABS to a quality virtually indistinguishable from injection molded models. The process is facilitated by the presence of a recirculation system, which saves on solvent and prevents air pollution by potentially dangerous fumes.