How small can you 3d print
How Small Can a 3D Printer Print? – The 3D Bros
Printing small-scale 3D models with a 3D printer may be challenging because resolutions are not the same as the resolutions you use for two-dimensional pictures and for printing images on paper. Using your 3D printer in creating very small models or models with very fine features and details may involve a steep learning curve for new users. But as to how small your 3D printer can go, it depends mainly on its technology.
An FDM 3D printer can print 3D models as small as its nozzle diameter, which is at least 0.15 millimeters. Resin 3D printers like DLP and SLA can print much smaller details as it offers very fine Z resolutions. With resin printers, you can choose layer height options from 25 to 300 microns.
This article will discuss the differences in various types of 3D printers, especially in terms of their printing accuracy and their ability to print fine details. You will understand how their different 3D printing technologies and mechanisms affect the quality of their print output.
Most Common Types of 3D Printers
Different types of 3D printers use different printing technologies, processes, and materials, influencing their print accuracy and minimum feature size. The most common are:
- Fused deposition modeling (FDM) 3D printers, also known as fused filament fabrication (FFF) 3D printers
- Stereolithography (SLA) 3D printers
- Digital light processing (DLP) 3D printers
FDM/FFF 3D Printers
FDM or FFF 3D printers extrude thermoplastic filaments like polylactic acid (PLA) and acrylonitrile butadiene styrene (ABS) through a heated nozzle, which melts the plastic and applies layer upon layer of the molten material to create a form. The FDM printing process is widely used at the consumer level.
One advantage of using FDM is that three-dimensional printing models are easy. Once you calibrate your printer and upload your CAD file, the printing process begins with just a push of a button. FDM printing is also a speedy process, and the technology can cost-effectively print objects in low quantities.
However, FDM 3D printing is not known for turning in long-lasting and durable products because each one is created in multiple layers instead of a single piece. There are bound to be weak spots in applying the layering technique. Additionally, FDM’s thermoplastics cannot withstand extreme conditions, so they would melt or deform when exposed to hot environments and crack when exposed to cold.
FDM 3D printing is also not able to produce models at a fine resolution. Because of the layering method, the output tends to have rough edges and surfaces and may require sanding and other finishing to smoothen them out. The tolerances are larger, too, which could lead to multiple prints of similar parts having inconsistencies and significant differences.
SLA 3D Printers
Dental technician removing jaw model from a 3d printer at the laboratory, modeling frame for implant productionAn SLA 3D printer is a resin 3D printer that produces high-accuracy, watertight, and airtight prototypes and models in advanced plastic materials. It is known to print 3D models with smooth surface finish, fine features, and highly detailed designs.
With a highly precise laser, an SLA 3D printer delivers light to form and cure thin layers of liquid resin that stack up to form one solid object. The process of curing resin into hardened plastic is called photopolymerization. SLA resin formulations boast a broad range of thermal, optical, and mechanical properties that make them ideal for industrial and engineering thermoplastics applications.
Using light instead of heat to print prototypes make SLA reliable. By printing three-dimensional parts at close to room temperature, you don’t have to worry about thermal expansion and contraction, which can be prevalent when printing via FDM.
These parts and prototype printing using the SLA process are also isotropic, which means that they have high lateral strength levels that don’t alter with orientation.
DLP 3D Printers
Like an SLA printer, a DLP 3D printer also uses resin. It creates parts and models upside down, layer by layer, as its build platform goes down into a resin tank. And while an SLA 3D printer uses a laser as its light source, a DLP 3D printer uses a digital projector screen. An image of a layer’s pattern or shape is flashed across the build platform, and this light cures the liquid resin.
The light gets reflected onto microscopic-sized mirrors that are arranged on a semiconductor chip. This digital micromirror device (DMD), in turn, points the light to the bottom of the resin tank, defining the coordinates where the resin hardens in a particular layer.
DLP 3D printers are among the most precise and accurate 3D printers around, so they are great for highly detailed models. And like SLA printers, they create objects with a smooth surface finish.
How Small Can Your 3D Printer Print?
The different types of 3D printing technology have different minimum feature sizes.
How Small Can FDM 3D Printers Print?
FDM 3D printers can print features as small as the diameter of their printing nozzles. The most common nozzle size for these printers is 0.4 millimeters, so that means the smallest feature they can print is that same size, too. However, third-party nozzle upgrades are available. You can get a 0.15-millimeter nozzle and swap your printer’s old nozzle with it so you could print smaller features.
However, you have to keep in mind that how well a model or 3D figure turns out is also heavily influenced by its shape and the movements that the FDM printer needs to make to print it.
One major problem regarding printing small details with an FDM printer is that you have limited control over when the thermoplastic material starts to flow out from the nozzle and exactly when it stops. As such, an FDM printer will have an easier time creating fine details that are part of a larger object than creating a similar-sized detail on a much smaller object.
How Small Can SLA 3D Printers Print?
The minimum feature resolution for SLA 3D printers relies on the spot size of the laser beam. Because SLA technology does not involve thermal stresses like FDM, it is easier to print tall and thin shapes and very small features.
In 3D printing, you will need to get acquainted with the three dimensions: the X and Y dimensions, the two-dimensional planes, and the vertical Z dimension. The Z resolution is the thickness or height of a layer that the printer can produce.
The laser spot size of the SLA printer determines the XY resolution. The increments by which the laser beam is controlled also affects the XY resolution. As for the Z resolution, resin printers offer a layer height of between 25 to 300 microns.
How Small Can DLP 3D Printers Print?
Just like SLA printers, DLP printers offer a fine resolution. You can also pick a layer height option or Z resolution of anything between 25 and 300 microns. Meanwhile, the XY resolution is defined by pixel, which is the tiniest feature that the projector can print within a particular layer.
However, with DLP printers, there is a trade-off between build volume and resolution. The projector dictates the number of voxels or pixels available. The closer the projector is moved to the optical window, the smaller the pixels get, which increases the resolution of your print. As a result, the available build area also gets limited.
Calibration also plays a crucial role. Unlike SLA printers with the same light source throughout, with DLP projectors, you will need to factor in the non-uniform distribution of light on the build platform and lenses’ optical distortion. This means that the pixels right in the middle of the print object are not of the same shape and size as the pixels on its edges.
Final Thoughts
Generally, SLA and DLP printers can print much smaller features and details than FDM printers. More importantly, SLA and DLP are known for more accurate, precise, and more durable prints of industrial and engineering quality. But that is not to say that FDM technology doesn’t have its own strengths. That is why thorough research needs to be done on the pros and cons of each of these types of 3D printers to know which one suits your specific printing requirements.
Sources
- MH Manufacturing: Benefits and Disadvantages to 3D Printing in Manufacturing
- Pinshape Blog: 4 Things You Need to Know About 3D Printing Resolution
- Quora: How small of an object can a 3D printer print?
- All3DP: How Small Can You Go?
- All3DP: SLA vs. DLP: The Differences – Simply Explained
- Dummies: How to Print Tiny or Highly Detailed 3D Objects
- 3D Printing: How small can I expect FDM 3d printers to print?
- Formlabs: FDM vs. SLA: Compare the Two Most Popular Types of 3D Printers
- Formlabs: SLA vs. DLP: Guide to Resin 3D Printers
- Xometry: What is the smallest feature that you can print?
- Make Parts Fast: What is a DLP 3D Printer?
How Small Of An Item Can A 3D Printer Make? – 3dprintscape.com
One of the most amazing things about 3D printers is that they are capable of creating things out of what seems to be nothing. This means that what they do is that they create different objects using a bottom-up approach by putting together different small particles. But how small of an item can a 3D printer actually print?
In most cases, 3D printers can print as small as their nozzles allow them to do so. Some 3D printers can print at least 0.15 millimeters. However, it usually really all depends on the manufacturing specifications of the 3D printer and the type of 3D printer we are talking about here.
3D printers come in all shapes and sizes, and that means that there are also different types of 3D printers. In that case, the smallest thing that 3D printers can print will mostly depend on how small the 3D printer’s nozzles or manufacturing capabilities are. And there are also cases where it can depend on the type of 3D printer that you have.
What are the different types of 3D printers?
3D printers are amazing in the sense that they use a bottom-up approach when it comes to creating different designs. What they do is that they put together smaller particles that form one bigger structure. However, what you should know is that different 3D printers work differently. So, if we are to talk about how small of an item a 3D printer can print, it is equally important to talk about the different types of 3D printers.
FDM/FFF 3D Printers
Some of the most common types of 3D printers are FDM/FFF 3D printers. What these 3D printers do is that they extrude thermoplastic filaments through a heated nozzle so that the plastic material melts. In a sense, what happens is that these 3D printers put together small particles of heated plastic to create the form you want at the end of the 3D print job. This is the most common type of 3D printer in consumer markets.
The best part about FDM/FFF type of 3D printers is that they are very easy to use when creating three-dimensional printing models as you simply need to calibrate the machine and then upload your CAD file. From there, the printing process can be done with a simple push of a button. It’s that easy and speedy.
But the problem with these 3D printers is that they are not known for creating products that are quite durable because you need to know that what they do is that they put together several layers of plastic instead of printing one single piece. That means that there are going to be a few weak spots on the final product. Of course, you also need to consider that thermoplastics aren’t exactly the best when it comes to extreme conditions as they can easily melt or deform when exposed to heat or crack when exposed to cold.
And, in connection to our topic, FDM 3D printers are unable to produce models at the smallest scale possible. That is because, as mentioned, they rely on a method of layering plastics together. That means that it might be difficult to produce a really small product using an FDM printer.
SLA 3D Printers
SLA 3D printers are resin 3D printers that use a method that is quite different from what FDM printers do. What these 3D printers do is that they produce high-accuracy and water and airtight 3D models using plastic materials. In most cases, they are more accurate than FDM 3D printers as they are capable of producing models with fine features and accurate details.
Using a precise laser, SLA printers are capable of creating accurate models as they deliver light to form and cure layers of resin. What happens is that these thin layers of resin stack up to one another to form one solid object.
So, the difference here is that these 3D printers use light instead of heat to print 3D models. This is why SLA 3D printers are widely used in a lot of industries that require their pinpoint accuracy and detailed printing. And you don’t even have to worry about the resin warping or cracking because of how heat isn’t in the equation here.
DLP 3D Printers
DLP 3D printers are like SLA printers in the sense that they also use resin. What they do is that they create parts and models layer by layer from top to bottom. But the difference here is that DLP 3D printers use a digital projector screen instead of using laser as their light source. The image of the model’s shape or pattern is flashed, and this is the light that cures the liquid resin to form the 3D model.
What happens is that the light gets reflected onto very small mirrors that are microscopic in size. These mirrors are arranged on a semiconductor chip and will point the light to the bottom of the resin tank while defining the coordinates where the resin should harden to form the layers of the 3D model.
Because of the way DLP 3D printers work, they are considered some of the most precise and accurate 3D printers. They are so accurate that they are capable of printing fine details and even smaller objects that other types of 3D printers cannot print.
How small of an item can a 3D printer make?
Now that you know the different types of 3D printers, let us now look at how small of an item these 3D printers can make. And it is important to know how these 3D printers work because you need to understand that different methods of 3D printing can make big differences in how small of an item they can print.
FLM 3D printers, for the most part, are highly dependent on their nozzles in the sense that they can print as small as what the nozzles allow them to do so. In most cases, these 3D printers have nozzle sizes that are 0.4 millimeters, but it isn’t rare for some nozzles to be as small as 0.15 millimeters. You can even get a 0.15-millimeter and then swap out your old one for the newer and smaller nozzle so that you can 3D print smaller and more accurate features.
But the problem here is that, because FDM 3D printers rely on thermoplastic, you don’t have any control as to how the plastic flows out from the nozzle. This means that it would be very difficult to 3D print something that is as small as 0.4 millimeters.
Meanwhile, for SLA 3D printers, the size of the item will depend on the spot size of the laser beam. So, when the spot size is quite small, it would be easier for you to 3D print a model that is quite small. It will also be easier to print tall and thin shapes with amazingly accurate features using SLA 3D printers.
When dealing with SLA 3D printers, you need to know the X, Y, and Z dimensions. The laser spot size of the SLA printer is what determines the XY resolution of the 3D printer. Then, for the Z resolution, these printers can offer heights between 25 to 300 microns, and that means that you can 3D print smaller and finer models.
Finally, DLP printers are similar to SLA printers in the sense that they are capable of producing materials with amazing resolution and detail. The size of the 3D print will once again rely on the XYZ resolutions, but the difference here is that the XY resolution is defined by pixels, which are tiny spots that you can see on the projector.
So, in a way, both SLA and DLP 3D printers rely mainly on how the machines are calibrated and on the manufacturing settings of these printers. And the consensus is that SLA and DLP 3D printers are much more capable than commercialized FDM printers when producing smaller materials.
Related Articles
- What Is the Size Limitation of 3D Printing?
- Best 3D Printing Infill Pattern – Complete Details Inside!
- Why Is 3d Printing Slow?
- Do 3D Printers Use a Lot of Power? (The Numbers Inside)
- Create a Temperature Tower Using Cura – The Easy Way
- 3D Printing Blobs and Zits: Tips to Avoid Them
Make sure you check out our YouTube channel, and if you would like any additional details or have any questions, please leave a comment below. If you liked this article and want to read others click here.
Is it possible to print 10 times faster on a 3D printer? Tips for increasing the speed of your 3D printer
3DPrintStory     3D printing process     Is it possible to print 10 times faster on a 3D printer? Tips for Increasing 3D Printer Speed
From time to time, all 3D printing enthusiasts think about increasing the speed of a 3D printer and creating figures and models in a matter of hours, not days. Wouldn't it be great if you could 3D print 10 times faster than you can now? This article provides tips on how to increase the speed of your 3D printer without losing quality.
Before we take a closer look at the secrets that will help you print faster and share ideas for fast 3D printing, it's worth a little imagination about the incredible future. Maybe one day you will buy an affordable and fast device that turns STL files into detailed figures and models from your favorite video games and movies in just a couple of hours or even faster... And this one will really happen. But! Now let's put aside the fantasies and return to the current reality. The reality is that the following tips will actually help you speed up your 3D printing, so let's get started.
There are great guys - John Hart and Jamison Goh from MIT - the real geniuses of modernizing technology. According to MIT news, these two professors, along with their colleagues, have been working to increase the speed of a 3D printer and have developed an innovative model called Fast FFF.
The name Fast FFF stands for "Production of Fast Fibers". This model is capable of stacking material 10 times faster than any existing desktop 3D printer. In addition, the print head with fantastic 3D printing speed can work with renewable materials.
As the engineers noted, in order to increase the speed of 3D printing, three main factors had to be taken into account:
- The force applied by the print head when pushing the 3D printing material through the nozzle;
- The time required to heat up the material so that it melts and can flow through the nozzle;
- Print head movement speed.
All these things have been improved in the Fast FFF prototype. As a result, it was possible to 3D print two simple eyeglass frames in less than 4 minutes and a complex bevel gear in about 10 minutes. These models were printed with a 0.2mm layer and proved to be strong and durable.
Fast FFF prototype 3D printer cost about $15,000. This is a good price compared to expensive commercial 3D printers that cost over $100,000 and are about three times slower. But if you compare the price to an affordable home 3D printer under $300 or $500, the Fast FFF is clearly too expensive, even though it can 3D print 10 times faster than a regular FDM 3D printer. And it's currently unclear if an affordable ultra-fast 3D printer for home use will hit the market...
While you can't get your home 3D printer to 3D print 10 times faster than it is now, or beat the innovative Fast FFF machine, there are secrets :).
Most of the tips that can help improve your 3D printing speed can also affect the quality of your figurine or model. However, sometimes it's worth it.
Adjust 3D print speed
Settings is the first thing you can try if you want to increase your 3D print speed. Every hobbyist likes to work with certain slicing software. It is worth exploring all the possibilities and changing the settings to suit your needs.
The ability to control the speed of the print head is amazing. Sometimes this does not negatively affect the quality of a complex 3D printed model. And when you do something simple, you can significantly increase the speed without losing quality.
Replace nozzle
Sometimes you don't care about 3D printing accuracy. In this case, a larger nozzle may suffice. For example, you can change the nozzle on your 3D printer from 0.4mm to 0.8mm. Or you can choose even 1.0mm print head.
Much depends on your current nozzle size. Standard printheads are 0.2mm and 0.4mm. But choosing a larger size can save time and speed up 3D printing.
Increase layer height
If you increase the speed of the 3D printer by changing the nozzle to a larger diameter, you will also have to increase the layer height of the 3D print. The maximum height you can select is approximately 75% of the current nozzle diameter.
So if you change the nozzle from 0.4 mm to 0.8 mm, you can increase the layer height to 0.6 mm. These settings will affect the quality of your 3D model and cause you to lose a lot of impressive detail because the layers will be thinner and the speed will be much faster. Keep this in mind when experimenting with nozzle size and layer height.
Reduce wall thickness of 3D models
100% infill models and figurines take longer to print, but are durable when finished. You've probably guessed how to make 3D print faster by playing with wall thickness and reducing infill. But in this case, you need to be careful, because the thin walls of the 3D model and less infill can lead to poor quality 3D printing.
If you have a resin based 3D printer, you can save resin and increase 3D printing speed by working with the appropriate DLP/SLA Eco version of STL files offered by Gambody - Premium 3D Printing. The Eco version ensures that your walls are thick enough to make your 3D model strong, detailed and of the highest quality.
Print two 3D models at the same time
Another way to speed up your 3D printer without sacrificing product quality is to work on two projects at the same time. This is only possible if both models or figurines are small and can fit on the same 3D printer table without interfering with each other.
This option can be set in the slicing software. Select centering and place both models for 3D printing on the work surface. The main disadvantage of this method is that both models will be printed from the same material, but the final print speed will be significantly increased.
Do not use supports
When a large amount of support material is needed to 3D print a complex model, printing time will increase. This way, whether you choose to do projects with fewer supports or learn how to 3D print without supports, you can speed up and print the prototypes and figures you need faster.
Change the infill pattern of a 3D model
If you don't want to adjust the infill density, but still want to improve 3D printing speed, try adjusting the infill pattern in the slicer settings. People work with different patterns, but the most popular version for speed optimization is "lines" or "straight lines".
Filling in a line pattern is very simple. Your 3D printer will make fewer moves when creating a straight infill figurine and can reduce print time by up to 20%-25%. But the models will not be as durable as those with a triangular or mesh pattern.
Adjust the jerk and acceleration settings
After making changes to the slicing software in the hope of increasing the speed of 3D printing, you can also try changing the jerk settings. They are responsible for how fast the print head can move. Of course, the print head must move smoothly, because increasing the speed can negatively affect the quality of the 3D print and even lead to problems with the mechanical part of the 3D printer.
There are also acceleration settings that need to be adjusted. They control the speed at which the print head reaches its maximum speed. It's worth playing around with these settings to find a balance between the jerk and acceleration settings to slightly increase print speed without affecting the quality of the 3D model or 3D printer.
For example, if you work with the jerk setting at 10 (low) and select a speed of 60mm/sec, you won't save much time in 3D printing, but the print quality will be ok. Increasing speed to 120mm/s and jerk to 40 will cut 3D printing time by 25%! However, the quality of the printed 3D model will also be greatly reduced.
Replace 3D Printer
If you are not satisfied with your current 3D print speed capabilities, you can always look for another 3D printer with higher speed. However, such a device can be expensive. Most printers designed for home use are not as fast as industrial 3D printers.
For example, the cheapest FDM printers can cost as little as $300 or even $200, and they typically print at 60mm/sec. They will never reach the speed of industrial equipment such as the Massivit 1800 which can reach speeds of 1000mm/s.
Select objects for 3D printing quickly
Another way to increase the speed of 3D printing is to search for new ideas for 3D printing as quickly as possible. It is ideal for beginners who want to learn on the go and improve their skills as they progress from simple models to more complex figures.
13 notes about 3D printing, after 3 years of owning a 3D printer / Habr
This article will be, first of all, of interest both to those who have directly dealt with 3D printing, that is, who owns a 3D printer, but also to those who are just about to join the ranks of 3D printers and are thinking about buying their own printer.
In the framework of this article, I would like to present my observations as a direct owner of a 3D printer for more than 3 years.
Despite the fact that 3D printers have been known for a long time and, in my memory, have become widely used, judging by the information on various resources, starting around 2010 (I may be wrong, these are my subjective observations), for a long time I ignored this area, it’s hard to say why…
Probably, he considered it some kind of “childish pampering”, another hype topic for which there is simply not enough time…
The break happened when one of the wheels on my travel suitcase wore out. You know, a big plastic suitcase, with four spinning wheels on the bottom. Unfortunately, it is a “rather disposable item”, due to the lack of bearings on the wheels, which is why the wear of the friction point of the axle and wheel allows the suitcase to last no more than one or two seasons.
And it’s like “lightning flashed in the middle of the day: 3D printer!” It is with his help that I can fix this problem! Looking ahead, I’ll say that I didn’t succeed in fixing the suitcase in this way, so I had to use a different approach ...
As a result, I "upped" him - by installing wheels from unnecessary roller skates. Thanks to this “up”, the suitcase has become a real all-terrain vehicle and, even being very loaded, it rides easily - pushed forward even with “one finger”. And even in the snow, 5-6 cm thick. A tank, not a suitcase turned out! By the way - I took spinning wheeled "units" in Leroy. Then he took off and threw out his native plastic wheels from there, inserting from roller skates:
But this thought itself became a kind of trigger that allowed me to finally join the world of printers and buy my first 3D printer.
Like many, before buying it, I studied various forums and sites for a long time, delving into all the subtleties. And for some reason, I immediately liked the type of printer called the delta printer. Probably because during operation it looks like some kind of "alien device".
If at your leisure you like to sit “looking into the carpet”, then with the advent of such a printer you will have a much more interesting activity, even, one might say, hypnotizing :-))
And this, in fact, is my delta (if anyone interesting), which went, let's say, "ultimate up": all the electronics were placed upstairs, on a self-made welded frame, covered with polyethylene and a magnetic door was made. The coil with a bar is installed at the top, on the frame. The axis on which the coil is put on is machined on a lathe from aluminum and a bearing from the VAZ timing is inserted into it. As a result, the coil - "rotates even from the passage of a fly nearby":
Well, yes, I won’t argue for a long time, let’s start reviewing the main facts that I have accumulated as a result of owning this car . .. The facts are purely subjective and may differ from your vision. In any case, I will be glad to comments, clarifications, etc.
▍ NOTE 1. Delta is good, but...
Here I should give a number of my observations regarding the delta printer:
- It contains a completely finished frame of the future box, which makes it easy to form a thermal chamber. I understand that many printers are made in the form factor of a “certain box” (but this point cannot be ignored), which greatly facilitates the process of wrapping this box with heat-insulating material. In my case, as such a material, I used a plastic film.
- Already thanks to its design, delta allows you to work at much higher speeds than XY printers. By the way, it is on the delta principle that many modern high-speed industrial robots are built to sort various parts directly on the conveyor belt:
However, this plus does not allow to fully realize the occurrence of parasitic vibrations, even despite their suppressors:
Thus, accurate printing is possible, only at speeds (at least that was the case for me), no more than 60 mm per second. A complex procedure for aligning the movement of the head parallel to the table, which is why, for many, the so-called "lens" appears. People struggle with it with varying degrees of success, but I have not encountered this on my printer and for me, therefore, the “lens” has never been a problem. At the same point, it is worth noting the calibration of the table, which was initially absent on the first deltas, and I had to use an external third-party solution from one American do-it-yourselfer called EZBED. This solution was a hardware-software complex that allows you to quickly and easily calibrate the printing table, that is, to let the printer understand its geometry. Modern printers do not have this issue as they come with a built-in calibration solution. It is worth noting that I solved this problem by attaching a limit switch to the print head, and using the Marlin-1.1.9 firmware.
▍ NOTE 2. "Size doesn't matter..." :-)
When I got the printer, I was impressed by the possibility of huge printouts, a la the handguards of some futuristic rifles, huge body parts, etc.
However, if you try to analyze the results of your many years of practice, it turns out that in most cases, rather small objects were printed that easily fit in the palm of your hand, a maximum of two palms. Despite such a seemingly small size, the printing of these details took a significant amount of time. Of course, this very much depends on which nozzle you print with. But, despite this, it is difficult to disagree with the fact that most of the printed parts will be quite utilitarian and small in size.
Therefore, to be honest, the need for a printer that allows you to print "Venus de Milo in life size" is not obvious.
Of course, you can object to me that “I’m going to buy a printer, I’ll get used to it a bit and I’ll get started!!!”
Here you need to take into account one simple point: there are no universal things. And in order to understand how much 3D printing in general and your printer, in particular, you will need to solve your problems, and how much it will be able to solve such problems, you just need to first try the 3D printing method personally and then a lot will become clear to you .
Therefore, for a beginner, I recommend taking a small printer that allows you to print extremely small items that fit in the palm of two. With such a device, you will definitely never lose, as it will always be needed. In addition, with its help you will be able to get comfortable with the printing process and, if necessary, purchase a larger device, already clearly understanding its capabilities and ability to solve your set of tasks.
▍ NOTE 3. "What type of printer to get."
Based on the foregoing, I do not recommend taking a delta printer and this can be said right away.
Not because it is bad, in fact, it prints quite accurately, its main problem (in my opinion) is the inability to print rectangular flat, fairly large case components, as well as the inability to fully realize high-speed work, since the quality drops critically. Here it turns out to be a rather offensive situation - the printer can work quickly, but this cannot be done, since the quality will be “nothing”.
And then what kind to take? Depending on the budget and capabilities, I recommend taking any cube printer, for example, the same Core XY (the head moves, and the table goes down as the model “grows”, from top to bottom):
Image source: thingiverse.com
Such a printer allows you to easily print fairly large flat parts of cases, has good speed and accuracy. In addition, the presence of a rigid box-shaped frame allows it to be easily covered with polyethylene to create a sealed heat chamber. In addition, the very fact that the table does not move while working reduces the number of problems with model peeling.
However, the advantages of this printer will not be fully revealed if it has a direct extruder. On the one hand, it will allow printing with rubber-like materials, on the other -
large inertia and head weight. And these are parasitic vibrations, wear of the fur. parts, etc. (like everything in life, “we treat one thing and cripple another” :-))
At the initial stages, this may not be necessary, but in the future it may be necessary to print, for example, tires for your homemade car. And with this, the Bowden extruder has obvious problems. Although, in fairness, printing with such a rubber-like material is far from a daily need. However, whoever seeks will always find: over time, I found a way to “upgrade” my printer with a Bowden extruder to print with flexible materials. "Crutches" of course. But even so.
By the way, there are printers of a cheaper type, the so-called "drygostol", printing by moving the table and head:
They are inexpensive, moderately accurate, but they require a sufficiently high-quality gluing of the printed model to the table, because the table moves, and the model can come off when the table is jerked sharply. When printing large models, this can be a problem.
▍ NOTE 4. What to print with?
It's only a matter of taste and purpose. That is, if your printout will only stand on a shelf and should differ in some kind of aesthetic appearance, these are some requirements, if the printout is an engineering part that will be operated under conditions of increased mechanical load, these are different requirements. That is, in the first case, you can use any PLA, SBS plastics, and others with similar properties.
For engineering parts, for example, I only use ABS. It combines high hardness, strength and low price. Although I understand that now this last statement will cause a storm of comments in the style of “no! - there is even stronger, even better, the same PETG, etc. ":-)
I just wanted to say here that thanks to the low price and the practical experiments that I conducted with ABS plastic, I realized that it is completely meets all my requirements.
However, the fact that ABS plastic releases carcinogenic substances when heated is quite annoying and forces you to take measures to prevent poisoning. For this, my printer prints completely closed and on an open balcony. After printing, the printer chamber opens, and it remains open in this form until it is completely ventilated and cools down.
▍ NOTE 5. "ABS is difficult to type on, it separates, peels off the table, and in general.
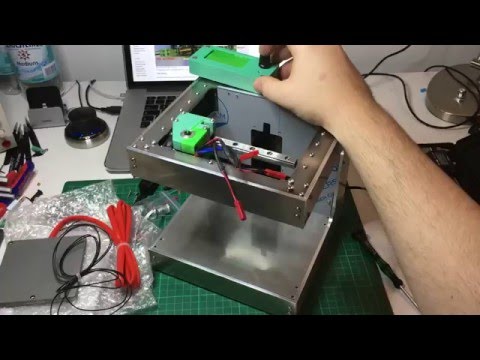
With a properly configured printer (in my case, at a print temperature of 205 degrees, a thermal chamber and a desktop temperature of 100 degrees), the use of auxiliary techniques, for example, among which, one can name the so-called ABS juice (which is an ABS- plastic dissolved in acetone), you can create wear-resistant and durable things, without any hypothetical problems.
For example, my printer has been printing for many hours at temperatures well below freezing. And this happened more than once, not twice, not three! And the print quality was excellent:
12 hour ABS printing at -4 C
At one time, I wrote a fairly detailed article on this topic and I will try to give the main excerpts from it. The essence of the issue here is as follows: due to the fact that different GOSTs are used for the production of acetone, acetone differs in quality. Despite the fact that it would seem that “acetone is also acetone in Africa,” nevertheless, one type of acetone can differ significantly from each other.
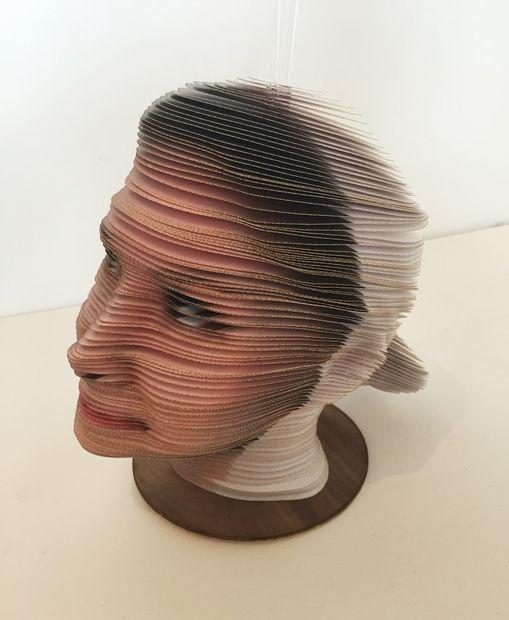
In contrast, there is a much higher quality acetone, which, however, is not found at all in any household stores, even large chain stores, such as Auchan or Leroy Merlin.
This type of acetone is found exclusively in shops that sell varnishes and paints for automotive work - that is, these are highly specialized shops for auto repair shops:
Acetone, which can be purchased there, is of excellent quality, smells almost like alcohol, quickly disappears,
:-) - this is a joke, of course, don't even try it.
However, its main advantage, compared to household type acetone, is that it perfectly dissolves ABS plastic and does not allow it to precipitate. For me personally, it was a very surprising observation when the same ABS plastic was perfectly dissolved with acetone from an auto shop, and completely precipitated when I tried to use household acetone (I just ran out of good acetone, and I had to use "what is ").
Therefore, if you want your result to be always excellent, then here is the right acetone. It should be labeled "for professional use":
▍ NOTE 7. What about ABS juice?
"ABS juice" is what printers call a mixture of acetone and pieces of ABS plastic dissolved in it. This mixture is smeared on the surface of the desktop before printing and allowed to dry. Thanks to this spread, the model easily sticks to the desktop and does not peel off during the printing process. After printing is completed and the platen has cooled down, the model can be easily separated.
All that needs to be said here is that, after trying different approaches over time, I settled on using flexible metal spatulas, also called “Japanese-style spatulas”:
According to the results of many tests, this method of spreading turned out to be one of the most convenient options, such spatulas can be cleaned very quickly and easily after work. In other words, highly recommended!
▍ NOTE 8. "Yes, it's impossible to do anything sensible on it, I indulged a little and decided to sell it - you can't use it for anything good anyway"
I absolutely disagree with the statement above, which is periodically heard from newcomers to 3D printing. You can even say more: at the moment I can’t even imagine how I used to live without a 3D printer! Since it is he who makes it possible for any do-it-yourselfer to significantly expand their capabilities and make piece products, almost of factory quality! Of course, for this, appropriate hands must be applied to the 3D printer, but that’s another question… and take on things that I would never have thought to take on before!
For example, among my homemade products, the following can be listed:
- Heated sole for boots, which is a hose integrated into the insole (and filled with household silicone from a household store), through which water flows, heated with a catalytic type hand warmer.
Water is pumped using a small peristaltic pump. The engine with a metal gearbox, which is used in the creation of this pump, allows you to develop a force of 3 kg, which is even redundant for this homemade product. The engine is powered by Peltier elements mounted next to the catalytic heater. The project is currently in progress.
- Centrifugal water pump, mounted on the shaft of an internal combustion engine, which drives a portable high-pressure air compressor with a pressure of 500 bar. The pump pumps coolant through the casing of the high pressure pump, or rather its second stage. Despite the fact that the pump is 3D printed and runs at over 6,000 rpm, nothing “fell apart, crumbled, or broke.” As you can see in the photo, the pump is installed instead of the “starter”, that is, the armstarter. The compressor scheme as a whole is as follows: 2 engines. Connected by clutch. One is heavy duty. The second is modified and turned into a high pressure compressor:
Yes, before assembling this, I also did not believe that this was possible. Moreover, even when I collected it, I did not believe my eyes :-))). However, it is a fact…
- I printed a number of Ranque-Hilsch test tubes, the essence of which I described in detail in this article.
- Printed mass of parts, more than 100 pieces, to create 10 web-controlled robots. There was also a detailed article about this here.
Well, and a bunch of all sorts of useful and not very crafts. As you can see from my crafts above, I have a special passion for creating some useful things, a utilitarian direction. That is, so that the printout is useful, and does not belong to the type of “yyy breathe, Mikola, what am I doing here” :-), and then put it on the shelf and that's it. Although, engineers are also not alien to beauties, and this will be my next fact below.
▍ NOTE 9 Proper placement of the model when printing is half the battle
It would seem an obvious fact, but many underestimate it. Here I mean the following: by experience, I accidentally discovered that when printing various statues (in which I, completely unexpectedly for myself, discovered another passion of mine), it is advisable to place the statues at an angle to the printing table.
This allows the layers in the printout to run at an angle of approximately 45-50 degrees to the model. The result of this is that the printed model is almost completely invisible layers and the model looks like it has been post-processed, but at the same time retains a deep matte color, which, to my personal taste, is more like a marble than a glossy result of processing in an acetone bath :
An additional advantage of this method is that the layers going at an angle of 45-50 ° to the model give it additional strength. This is especially true for printing statues, which contain many thin elements that easily break off when the statue is accidentally dropped from a table or shelf (learned from bitter experience, this happened to me many times, and ruined some fairly decent prints).
That is, layers running across the model, if the model has a large extension in height, does not allow it to maintain sufficient strength. For better understanding, I tried to illustrate this point in the figures below:
▍ NOTE 10. Bleeding must be taken into account when printing, especially if the model is composed of separate parts and must be assembled by joining these parts to each other, entering into each other, etc.
I tried to illustrate this point in the figures below. The implication here is that if you're printing a composite model, you'll need to correct for the amount of bleed on the plastic (I'm not sure what it's called, but I at least tried to convey what I mean). If this is not taken into account, then the model will not fit.
For example, in my case this correction is 0.2 mm per diameter - if I want the model to fit more tightly; if I need a free joint, without excessive density, then 0.3 mm per diameter:
That is, suppose that the blue part has a size of 10x10mm. So it must be modeled in the CAD program as 9.8x9.8 mm (if we want it to sit tight) or 9.7x9.7 mm (to sit freely). Well, or expand the hole in the green part, and leave the blue one as it is.
This is often a problem when you download a prefabricated model from the Internet - but it is not going to, even if you crack! And because no amendments have been made…
For your specific case, the amendments may be different.
▍ NOTE 11. What if...
In fact, this note complements note number 8. Using a 3D printer allows you to create metal parts using a printed 3D model. For this, the casting method is used according to the lost wax or burnt model. In our case, we will deal mainly with casting metal on a burnt model.
Briefly, it looks like this: printing a 3D model (using PLA plastic) → pouring it with plaster → burning the PLA plastic, simultaneously with burning the mold, in a conventional stove oven → pouring the resulting shape with molten metal (melted in a conventional microwave) .
Image source: 3dtopo.com
I told about a simple method of melting metals in a home microwave oven here.
There was even a good article about casting on Habré.
▍ NOTE 12. Durability?
Despite the fact that ABS plastic is called exposed to ultraviolet radiation and, accordingly, burns out, losing its strength in the sun, in my practice, even printouts that are constantly exposed to the sun have not lost their strength and color at all, continuing to be successfully used and Currently.
It should also be added here that printouts are constantly exposed not only to the rays of the sun, but also work continuously in damp conditions!
As such printouts, I can give an example of winglets for technical cranes, which I printed out, but, unfortunately, did not photograph this process; as well as fasteners on shoes that I use “both in the snow, and in the heat and in the pouring rain, and in general are always with me”:
▍ NOTE 13.
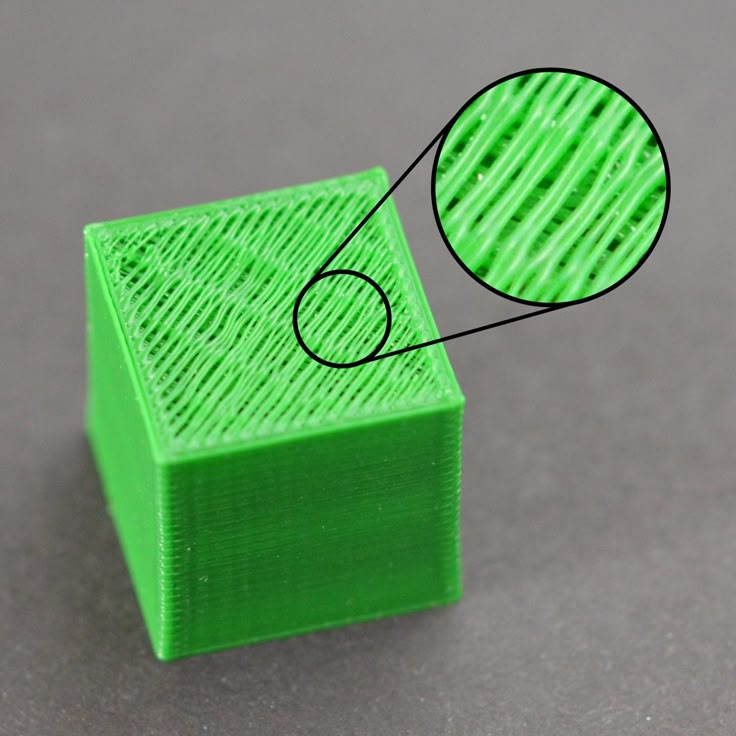