Forge finder 3d printer
Flashforge Finder 3D Printer for Children Use
Finder 2 (discontinued)
Finder is the perfect starter 3D printer for families, schools as well as novice users. Capable of printing right out of the box with few tweaks. All the heated elements are protected from touch, printing filament is non-toxic PLA.
The printer is now discontinued, you may check out its upgraded version Finder 3.
Buy Finder 3
Distinctive In Design
Patent Extruder
Removable Platform
140*140*140(mm)Build Volume
Build-in Filament Box
Touch Screen
Cloud Print
50dB Sound
Overview
It is fully assembled. And now with its assisted leveling system, you just need to do very few tweaks before starting to print. Featured with a 3.5-inch touchscreen, filament-run-out detection, USB stick and Wi-Fi connectivity and more, it becomes an even more friendly 3D printer for beginners.
Safe / Clean / Creative
provides stable printing of PLA
Finder is designed for kids and novices. We hope you can have a blast with this safe 3D printer making practical things to wildly imaginative creations. We conceal all the cables within the plastic alloy body. The frame is sleek, without any sharp edges. The hot nozzle is protected from touch, and the build plate is a piece of glass with no heat on it.
Removable build plate
Finder 2.0 adopts an extractable platform, thus it is easy to remove models, and it will not damage the platform or holder when removing the model.
Intelligent assisted leveling system
Finder features an intuitive calibration detection system to assist in leveling. You are directed to tighten or loosen the leveling screws until the beeps sound, then it detects the distance between nozzle and build plate to verify whether your leveling is completed. Leveling instruction will be shown on the touchscreen display.
Build-in filament box
Build-in filament box,
keeps desktop clean.
Buy Finder 3
Model Preview
It supports previewing the printing files. And the file name will appear with the model appearance. It does not need to worry about too many files in the printer because of 8 GB internal storage.
Low noise operation
And the noise level is as low as 50 dB, or even less. It makes Finder be a kind of printer great around kids of all ages or home 3D printing users alike.
Multi-communication
File transfer is very easy
FlashPrint
With a simple and intuitive interface and a list of preset parameters for printing, FlashPrint enables you to enter the wonderful world of 3D printing more easily. Featured with smart support, 2D into 3D, split model and more, it is a functional slicing software to achieve more possibilities.
Cloud print
The cloud platform can store user models. After binding devices, Online cloud slicing, remote printing status viewing, easy to control the printer.
USB Cable Connection
USB Stick
Ethernet
Wi-Fi
User Case
Specification
Printing
- Extruder Quantity 1
- Nozzle Diameter 0.
4 mm
- Maximum Extruder Temperature 240 ℃ (464 ℉)
- Print Speed 30-100 mm/s
- Filament Compatibility PLA, Wood, TPU 95A
- Filament Diameter 1.75mm (0.069 IN)
- Print Volume 140*140*140 mm(5.5*5.5*5.5IN)
- Layer Thickness 0.1-0.4 mm
- Print Precision ±0.2 mm
Mechanical & Dimension
- Printer Dimension 420*420*420 mm (16.5*16.5*16.5 IN)
- Screen 3.5-inch touch screen
- Net Weight 11 kg (24.3 LBS)
- Gross Weight 13.8kg (30.4 LBS)
- Internal Storage 8 G
- Running Noise 50 dB
- Working Environment 15-30 ℃ (59-86 ℉)
Electrical
- Power Input AC 100-240 V, 47-63 Hz
- Power 65 W
- Power Output 24 V, 2.71 A
- Connectivity USB cable, USB stick, Wi-Fi, Ethernet, FlashCloud, PolarCloud
Software
- Software FlashPrint
- File Input Format 3MF / STL / OBJ / FPP / BMP / PNG / JPG / JPEG files
- File Output Format GX/G
Buy Finder 3
Flashforge Finder 3, another super cost-effective 3d printer for beginners and advanced users, kids, teenagers and adults.
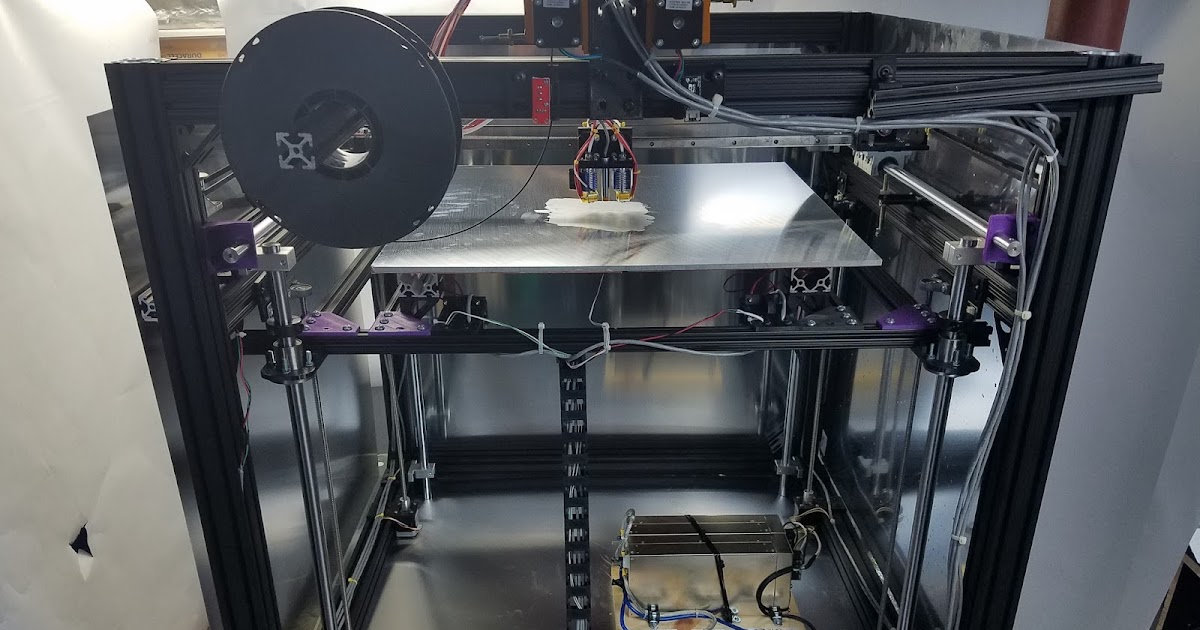
190×195×200mm Build Volume
Unlock your imagination!
The 200mm vertical Z-axis height meets the printing needs of most users. Let your imagination run wild!
Durable and more temperature-resistant extruder with the maximum printing temperature up to 260℃
Its direct drive extruder can print TPU 95A flexible filament.The heating temperature up to 260℃ achieves smoother filament feeding.
Support printing flexible filaments such as TPU 95A
It supports printing TPU 95A / PLA / ABS / HIPS / PETG / PETG PRO filaments, etc. It also supports printing third-party filaments, offering stronger compatibility and wider application range.
Intelligent sensor technology
01Power loss recovery:
Finder 3 can save the printing status in the event of an unexpected power failure and continue printing after the power is restored.
02Filament run-out reminder:
When the filament is used up or accidentally broken, Finder 3 will alarm and pause printing, and then continue printing after the filament is replenished or replaced.
Inherit classics and bring forth the new one
Finder 3 retains the classic red and black color scheme of Finder 2, and features integrated structure design. With no assembly required, it is easy to use in seconds after being unpacked; Smaller equipment size and larger build volume for higher volume utilization.
Dual platform options for individual needs
The removable glass platform and PEI magnetic steel plate platform are available for options. Easy platform removal and replacement to meet diversified printing needs.
Six functions in all aspects
Wi-Fi connection4.3-inch Touch screenBuilt-in extruder lampSilent operationCompatible with third party slicing softwareSupport for multi-data transmission
Specifications
Machine Type | Finder 3 |
Extruder Type | Direct drive extruder |
Nozzle Diameter | 0.4mm |
Maximum Extruder Temperature | 260℃ |
Platform Heating Temperature | ≤110℃ |
Printing Precision | ±0.![]() |
Printing Speed | ≤180mm/s |
Build Volume | 190×195×200mm |
Supported Filament | PLA/ABS/HIPS/PETG/ PETG PRO/TPU 95A |
Touch Screen | 4.3-inch |
Language | Chinese/English/Japanese/ French/German/Spanish |
Connectivity | USB/Internal storage/Wi-Fi |
Assisted Leveling | ✔ |
Resume Printing After Power Failure | ✔ |
Filament Run-out Reminder | ✔ |
Removable Platform | ✔ |
Silent Operation | ✔ |
Camera | ✖ |
BUY NOW
how additive technologies quietly change production, science and life
Today, 3D technologies have quietly penetrated into all spheres of our life. Rough plastic figures with ribbed edges are a thing of the past. With the help of additive technologies (layer-by-layer creation of something), tablets, metal parts and even meat are being created today. And scientific discoveries in this direction are made regularly. Technologies and areas of application are expanding almost daily. Cars, houses and even bridges are already being printed. nine0003
Outdated information
On the net you can find articles whose authors claim that 3D printers are not capable of working with metal ... But in Amsterdam, the world's first steel bridge has already been printed.
In St. Petersburg, 3D printing technologies for metal products are being developed by a group of scientists from the Peter the Great Polytechnic University. In pursuit of increasing typing speed, they made a scientific discovery.
How are metal products printed?
Plastic 3D printing, which is already familiar to us, works like this: the printer melts the source material and, using a dispenser, applies a liquid substance to the product. It freezes. And so on, layer by layer. To pull off such a trick with metal, you need to figure out how to melt it and apply it. Do not destroy the printer. Any welder knows the solution.
Welding 2.0
Working in the Laboratory of Light Materials and Structures
Oleg Panchenko is in charge of the Laboratory of Light Materials and Structures at the St. Petersburg Polytech. Here, surfacing technologies are being developed. Since the 40s of the last century, they have been used for the manufacture of finished parts. If a hollow metal part was needed, then it was created in the only possible way - by hand. A highly skilled welder built up the walls of the product layer by layer. Long and very difficult. The larger the detail and the more complex the shape, the less chance of success. Even the best worker cannot move with the same speed and accuracy. nine0003
Accidental discovery
The team wanted to achieve the highest possible metal printing speed. Physicists were involved in the process. They proposed a solution that scientists had never thought of before. The object of attention was the electric arc that melts the steel wire in the welding machine. Scientists have studied how long burning lasts, the direction of prominences and plasma emissions, how current and voltage affect the rate of metal melting. And as a result, they found a way to redistribute energy for their tasks. Achieved concentration of maximum energy at the desired point. Due to this know-how, the modern welding machine has become twice as powerful. nine0003
Forges of Fortune of the New Age
To find out the second one, you will first have to travel back in time three thousand years ago. Then mankind mastered the hardening of metal. Ancient blacksmiths noticed that if an iron object is heated and then cooled sharply, for example, in water, it will become harder. The secret of the processing of swords and daggers was discovered in Asia in the temple record dating back to the 9th century BC.
“Heat until it glows like the rising sun in the desert, then cool it to the color of royal purple, immersing it in the body of a muscular slave. The strength of a slave, turning into a dagger, gives the metal hardness. nine0003
Over time, the methods became more humane, the blacksmiths realized that the properties of the product are affected by the speed of cooling, and not by the liquid, and certainly, to the relief of young strong slaves, not by their strength and health.
The experience of centuries and an industrial robot
Here, welders from the Polytech loaded metal with some physical properties into the printer, and as a result received slightly different ones.
“We have found superplasticity in an aluminum alloy. We got the same strength, but with the same strength, the elongation of the material before failure was three times greater. This happened because we got into such an interval of the cooling rate of the material, which no one had ever fallen into before.
A material that has greater plasticity is more resistant to destruction; like plasticine, it will stretch for a long time before breaking. And it is more reliable if it has minor defects. Simply put, if you make a bumper for a car out of such aluminum, then in an accident it will be able to absorb three times more energy than a regular one. This means that the likelihood that passengers will survive will greatly increase,” says Oleg Panchenko. nine0003
According to the scientist, they can now program a 3D printer so that it prints a product from one source material with areas that have different mechanical properties.
Life in 3D
3D for yourself printer
Today we have already learned how to print food. The scientific process is described as follows. Extrusion printing is used to create food. It sounds complicated, but in fact, any of us can become a 3D printer ourselves. nine0003
How to become a 3D printer? Instructions:
- Arming with pastry syringe
- Fill it with thick dough
- Squeeze a layer of dough onto a baking sheet
- Bake cookies
- Add another layer of dough
- Bake two-layer cookies READY! You are a 3D printer!
All components on the face. The syringe is an extruder, the hands are a manipulator, the brain is a computer that programs movements. The printer does the same, but more accurately and faster. Today, no matter how loud the phrase “printing food” sounds, the possibilities of the method are very limited. This is more of a semi-finished product than a watermelon rolling out of a printer. But, for example, bakeries are already using 3D technology. They allow you to significantly speed up the process of creating products with a complex design and reduce the number of defects. Robots don't make mistakes. nine0003
Printing people
It's still far away, but parts of our bodies have been printing for a long time and very successfully. In medicine, additive technologies are now used to create prostheses. In Russia, they were the first to be mastered at the Research Institute of Traumatology and Orthopedics named after R.R. Harmful.
“The main advantage of using 3D printing for the production of endoprostheses is that it can be used to produce unique products that exactly match the shape of the patient’s bone tissue defect, as well as having a special coating of implant-to-bone contact surfaces specified by doctors, which ensures osseointegration , that is, the connection of a bone and a metal structure.
Precisely made implant and high-quality osseointegration mean a multiple reduction in the risks of complications and repeated prosthetics,” says Mikhail Zhmailo, Head of the Applied Research and Development Department at Peter the Great St. Petersburg Polytechnic University. nine0003
And the plastic heart will beat
Doctors turned to biomechanics with a seemingly strange request. And can they print the exact layout of a child's heart with all the physiological details. Scientists have created a program that can analyze computed tomography images and design a layout of an organ in a few minutes.
Printed polymer heart
Of course, such a heart will not beat. But doctors before a complex operation can practice on it. Cut, sew, reprint and try again
Where is the limit?
Are we far from being able to print a living human organ that would replace a donor one. The last major breakthrough in bioprinting was, by the standards of the fast-growing 3D industry, a very long time ago - seven years ago. Scientists were able to reproduce on the printer the thyroid gland ... of a mouse.
“Of course, there is a perspective, but we must understand that this is a very difficult task. A solution will be found, there are prerequisites and groundwork for this, but printing a human organ is still not the same as printing a bracket, a vase or a hamburger patty,” Mikhail Zhmailo believes. nine0003
The printed world won
3D printing in any form is still a complex and expensive process. And today, additive technologies cannot yet replace the usual means of production. But those studies that are taking place right now allow us to speed up, simplify and reduce the cost of the process.
At Peter the Great St. Petersburg Polytechnic Institute, scientists proudly display a fan blade. These drive air through the mines of a concrete plant. nine0003
Oleg Panchenko demonstrates a printed part. This is not a demonstration model, but a real order. The company needed parts of complex shape. The steel mill took an order of 100 pieces. The complex production process dragged on for months. The printer turned out to be cheaper and faster. In the future, customers will be able to immediately request metal products with the qualities they need. And soon, says Oleg Panchenko, printers will become an integral part of our lives. They brought the device to the river bank, pressed the print button, and an hour later they crossed the bridge to the other side. nine0003
Industrial 3D printers for resin-coated sand for injection molds and polystyrene
SLS technology (Selective Laser Sintering - Selective Laser Sintering)
SLS 3D Printer Scheme for Polymer Coated Sand and Polystyrene
Technical parameters of industrial 3D printers SLS-PS
Model nine0155 | SLS-500PS | SLS-1000PS | SLS-1200PS | SLS-1400PS |
CO2 laser, Power W | 55 | one hundred | one hundred | 100*2 100*4 |
Scanning system Dynamic focus nine0155 | 8 m/s | 8 m/s | 8 m/s | 8 m/s*2 8 m/s*4 |
Print Layer Thickness | 0.![]() | |||
Print Accuracy | ±0.2mm (L≤200mm), ±0.1% (L>200mm) | |||
Print chamber size mm nine0155 | X500 Y500 Z400 | X1000 Y1000 X600 | X1200 Y1200 Z600 | X1400 Y1400 Z500 |
Powder supply | Two pistons on both sides | |||
Print material | Color coated sand, polystyrene | |||
Operating system | Windows XP | |||
Software | HUST 3DP (independent research and development) | |||
File Format | stl, online cuts in the process of formation, changing the layer thickness, scanning. 3D visualization | |||
3D printer dimensions mm nine0155 | X2070 Y1280 Z2080 | X2150 Y2170 Z3100 | X2350 Y2390 Z3400 | X2520 Y1790 Z2780 |
Power supply | 3 phases, 4 lines with earth, 380V±10%, 50Hz | |||
Working temperature | 18-25°C | |||
Operating Humidity | Not more than 60% | |||
Power input kW | 3 | four | five | 9/16 |
Catalog
Download >>> View >>>