First consumer 3d printer
History of 3D Printing Timeline: Who Invented 3D Printing
3D Insider is ad supported and earns money from clicks, commissions from sales, and other ways.
The first 3D printer ever created was made in 1983 by Chuck Hull.The 3D printing buzz began a few years ago, catching the attention of the wider public in a big way. The media played a huge role in making “3D printing” the latest watchword in technological innovation. They began to showcase the true potential of this fascinating industry on a frequent basis. Since then, 3D printing has taken the nation by storm. People love the idea of being able to create all kinds of custom products as and when they need them. Yet despite this recent phenomenon, 3D printing has been with us for a while. It’s been around for a lot longer than most people realize, that’s for sure. The aim of this guide is to walk you through the detailed history of 3D printing. We’ll start from its early beginnings up to the present day and beyond.
3D printing In Layman’s Terms
Before moving on, it’s important to define 3D printing in laymen’s terms for the uninitiated readers. If you already understand the workings of 3D technology, feel free to skip this section. For everyone else, it’ll pay you to read through it. Don’t worry; we’re not going to get too technical here.
You’ll often hear others refer to 3D printing as additive manufacturing (AM). The latter involves the whole process of making 3D solid objects from computer-generated files, or digital files. The actual 3D printing process is only one part of the entire procedure. Despite this, the two terms are largely interchangeable these days, so for the sake of simplicity we’ll use 3D printing most of the time.
So what is 3D printing exactly and why should you care?
3D printing technology has begun to revolutionize the way we produce entire physical objects and parts in the last few years. The range of things produced by 3D printing today is vast, and continues to get more ambitious. At the time of writing, we can 3D print anything from simple toys to clothing to tools. We can also use the technology to produce musical instruments and even human body parts. Yes, you did read that right. The potential, it seems, is endless.
How does 3D printing work exactly?
The best way to describe 3D printing is to look at how a regular inkjet printer works. First we create the computerized file, whatever form that’s in. This could be a word processor file, a spreadsheet, or an image, etc. Once our file is ready we upload it to the printer via the computer, and then press the ‘PRINT’ button. The printer then extrudes (forces) ink from a nozzle onto the paper. After a single print cycle, the end result is a two-dimensional representation of the digital file. 3D printing operates in a similar way. The main differences are with the materials used and extra print-cycles.
With 3D printing, you also need to upload a digital file to the printer. You’ll see these files referred to as 3D models, 3D computer graphics, CAD files, and more. Whatever they are, the 3D printer needs a file before it can print your design. 3D printing uses special types of ink, known as filaments. These can range from thermoplastics to metals, glass, paper and even wood substances. We’ll look more into 3D printing materials later. And the other main difference is that 3D printing has to go through many print cycles, or layers, to produce a physical object. This is where it gets the name ‘additive manufacturing’. As you can see, the print theories between inkjet and 3D are very similar.
What else do I need to know about 3D printing and printer technology?
The most exciting thing about 3D printing today is that it’s no longer the stuff of scientists, engineers, and scientific experiments. It’s becoming popular because of the rising demand from interested consumers. The result is smaller, easier to operate machines at much lower costs. Hobbyists and enthusiasts can now buy budget end 3D printers for the price of a regular smartphone. Some even think we’ll soon be 3D printing our own unique products on demand. How cool is that!
3D Printing in the Late 1980s
Yes you read the title right. Stereolithography (SLA), commonly known as 3D printing, has been around since the 1980s. Those early pioneers called it Rapid Prototyping (RP) technologies. That’s a bit of a mouthful for most of us—hence the term 3D printing was born. Although printing is only one part of the process, most people prefer to use the term ‘3D printing’ when talking about the technology in general. Back in the 1980s, few could have realized the full potential of this amazing technology. They first used this early process as an affordable way to create prototypes for product development within certain industries.
Not a Lot of People Know This
Not a lot of people know this, but a Japanese lawyer called Dr. Hideo Kodama, was the first person to file a patent for Rapid Prototyping (RP) technology. Unfortunately for him, the authorities denied his application. Why? Because Kodama missed the one-year deadline and so failed to file the full patent requirements on time. This was back in May, 1980. As Dr. Kodama was a patent lawyer, his blunder was both embarrassing and disastrous.
Here’s something else that’s’ not common knowledge: Four years after Dr. Kodama, a French team of engineers decided to run with the technology. Although they had a keen interest in stereolithography, they soon had to abandon their mission. Despite their best intentions, there was a sad lack of interest in 3D printing from a business perspective. This wasn’t the end though. There was someone else who had a keen interest in the technology, and he picked up where the French left off.
Fast Forward to 1986
The actual origin of 3D printing, as we know it, has a different date. Today we can trace the very first patent for SLA back to 1986. To give you an idea of how long it’s been around, if you’re under 30 that’s before you were born. The patent belonged to an American inventor name Charles (Chuck) Hull. He was the first person to invent the SLA machine (3D printer). This was the first ever device of its kind to print a real physical part from a digital (computer generated) file. Hull later went on to co-found DTM Inc., which 3D Systems Corporation later acquired.
From its humble beginnings, 3D Systems Corporation went on to become a name synonymous with 3D printing. In fact, it’s one of the biggest and most productive organizations to operate within the wider 3D printing sector today. Even Hull himself admitted he underestimated the true impact and potential his creation would have on the modern world. Even today, new research and exciting innovation is moving ahead at an unprecedented rate.
Here’s a recap of events:
- 1980: Rapid Prototyping (RP) technology patent failed by Dr Kodama
- 1984: Stereolithography taken up by a French team but soon abandoned
- 1986: Stereolithography taken up by American inventor Charles (Chuck) Hull
- 1987: Very first SLA-1 machine
- 1988: First SLS machine by DTM Inc; later acquired by 3D Systems Corporation
There was plenty of other, lesser known activity going on in the background during this time:
- Ballistic Particle Manufacturing (BPM) patented by William Masters
- Laminated Object Manufacturing (LOM) patented by Michael Feygin
- Solid Ground Curing (SGC) patented by Itzchak Pomerantz et al
- Three-dimensional printing (3DP) patented by Emanuel Sachs et al
Only those involved in 3D printing technologies during the early 1990s would have known about the buzz going on at that time. But like all competition, it’s the best of the best that survive and go on to make their mark in the world. Today we have three originals remaining, which are:
- 3D Systems
- EOS
- Stratasys
The rest—as they say—is history.
When 3D Printing First Became Popular
3D printing first became popular back in the late 1980s, but not in the public sense. Its early popularity was among various industries. They liked it because it offered rapid prototyping of industrial products and designs. It proved to be quick and accurate, but it was also cost effective. For a lot of industries, rapid prototyping technology was checking a lot of boxes, and continues to do so.
Like with all great innovations, 3D printing had to go through a life cycle before it reached maturity. Most good ideas never take off, for all kinds of reasons, but a few do. The good news is that the additive manufacturing (AM) technology has made it. If we take 3D printing from its origin to the present day, it will look something like this:
- The Infancy Stage: 1981 to 1999
- The Adolescence Stage: 1999 to 2010
- The Adult Stage: 2011 to the present day
Some will say that 3D printers and 3D printing technology is now in its prime. Others will argue that there’s still a long and exciting road ahead of us. The latter group is most likely correct, as the future potential looks incredible. Think 3D food and human body parts—it’s all on the table.
Let’s take a look at each of these important stages one at a time:
Stage 1: The Infancy History of 3D Printing
This period is from 1981 through to 1999. It all began in Japan with Dr. Hideo Kodama of the Nagoya Municipal Industrial Research Institute (NMIRI). It was a public research institute in Nagoya city. It was here that Dr. Kodama published his findings of a fully-functional rapid prototyping (RP) system. The material used for the process was a photopolymer—a type of light-activated resin. This was a time when the first solid, 3D printed object came to be. Each print cycle added a new layer to the previous one. As it did this, each of these layers corresponded to a cross-sectional slice in the 3D model. This was the industry’s humble beginnings. And you know what happened after that to Dr. Hideo Kodama’s failed patent (see above).
Point of interest: Photopolymer is a kind of acrylic-based substance. It leaves the printer’s nozzle in liquid form from where an ultraviolet (UV) laser beam hits the exposed material. The exposed photopolymer instantly turns from a liquid to a solid plastic. After the printed layers eventually reach the model’s height, the 3D object is complete. When news of stereolithography first came out it excited inventors like nothing before it. For them, it meant they had the potential to print accurate prototypes and test new designs much faster. It also meant they’d be able to print prototypes with much less upfront investment time and costs.
Moving on three years to 1984, it was Chuck (Charles) Hull’s time. Hull went on to break new ground in 3D printing technology by inventing stereolithography (SLA or SL). SLA is special because it allows designers to create their 3D models using digital data files. They then upload these files to the printer to produce real physical, 3D objects, one layer at a time.
By the year 1992, Chuck Hall had realized his dream and created the world’s first ever SLA machine. Now anyone, who had the money, could fabricate complex 3D objects and object parts. SLA was a game changer. This new process took a fraction of the time compared to more traditional methods.
Also in 1992, DTM Inc. presented the first ever selective laser sintering (SLS) machine to the world. SLS works by shooting a laser at a powdered material rather than a liquid.
Rough Around the Edges
As exciting as these new technologies were, they still had some way to go before they made mainstream news headlines. Complex 3D models, in particular, proved hard to perfect. All too often, objects would warp as the material hardened. The machines were also expensive. They were certainly too costly for solo investors and hobbyists. It’s for these reasons that the technology was unheard of for decades after those first inventions. Even today, a time when 3D printing has become a buzz word, the real potential continues to unfold.
Stage 2: The Adolescent History of 3D Printing
The adolescent history runs from 1999 through to 2010. The general public still wasn’t familiar with 3D printing technology, but there were plenty of others who were. This was the decade where we saw the first ever 3D printed organ. In this case it was a human bladder. We have the Scientists at Wake Forest Institute for Regenerative Medicine to thank for that. First they 3D printed the synthetic scaffolds of the organ. After that, they coated it with actual cells taken from real patients. It’s what happened next that was so exciting. Surgeons were able to implant the newly formed tissue into patients. What made this so groundbreaking is that the patient’s own immune system would not reject an implant made of their own body cells. Even today it sounds farfetched, but it happened, and bigger and better things continue to happen.
As far as medicine goes, this was the decade for 3D printing technologies. As research continued, more amazing medical uses for 3D printing emerged. Here are just three others that are hard to believe:
- The first fabricated, functional miniature kidney
- The first prosthetic leg which included complex components
- The first bio-printed blood vessels using human cells
3D Printing’s Open Source Movement
The medical profession was not the only beneficiary of 3D printing innovation during this decade. It was also a time where the open-source movement got involved with the technology. One historical movement led by Dr. Adrian Bowyer in 2005 has to get a mention here. His open-source initiative was an ambitious project. The challenge was to create a 3D printer that had the ability to build itself, or at least print the parts needed for the new machine. He aptly named this ‘The Replication Rapid-Prototyper Project‘ or RepRap for short.
By the year 2008, the Reprap Darwin 3D printer was born. This open-source project helped to launch 3D printing into the spotlight. For the first time people began to talk seriously about the potential of 3D technology. They could see that they had the power to create all kinds of things based on ideas. A website called ‘Kickstarter‘ launched in 2009. It’s now the largest funding platform in the world for creative projects. There have been countless 3D-printing-related projects crowd-funded from this one platform alone.
3D Printing Becomes a Buzz Word
It was somewhere around the mid-2000s when ‘3D printing’ became something of a buzz word. The very first selective laser sintering (SLS) machines were to become commercially viable. In 2006, on-demand manufacturing came into being for industrial parts. Soon after this, the ability to print with various other materials got industry even more excited. From an engineering standpoint, this was a huge deal, offering all sorts of options in parts production. At the end of this adolescent period in 3D printing history we began to see various collaborative co-creation services appear. The easily accessible 3D printing marketplace had arrived. Nowadays, people can exhibit their designs, share ideas, and freely swap information.
Also at the end of this era, MakerBot made an appearance. This was the first service of its kind to provide open-source DIY 3D printer kits. It was an affordable way for people to learn all about the technology as they built their own machines. At last, 3D printers were becoming accessible to the general public.
Stage 3: The Maturing History of 3D Printing
If you thought 3D printing had reached its peak, think again. It’s as though there’re no limits going forward. The speed in which the technology has picked up in recent times is nothing short of spectacular. It’s almost as if we’re living in the future. For home users, hobbyists, and small businesses, the news gets better all the time. Aside from the impressive technology, the other reasons why 3D printing is becoming so commonplace are as follows:
- The cost of 3D printers has plummeted
- The accuracy of 3D printing has improved and continues to get better
- The machines are user-friendly (anyone can use them)
- It’s easier to design 3D models thanks to free software programs
- Innovators continue to push the envelope, keeping things fresh and exciting
Charles Hull knew he was onto something big, but he could never have envisaged just how big it would all get. Today, anyone can print with materials other than plastics. There are options to print with metals, glass, paper and wood among others. What you can print is also keeping the industry alive and thrilling. You can print musical instruments, jewelry, household items, and clothing accessories. Future potential looks at 3D printed homes, drones, vehicles, foods, and other human body parts. There seems to be no limitations.
3D Printing in the Present Day – Where Are We Now?
Just when you thought things couldn’t get any better, things always do. At least this appears to be the case with 3D printing. The progress is so fast, and so groundbreaking, it won’t be long before the latter part of this guide is out of date. Seriously, it’s proving impossible to keep up sometimes. It’s only a matter of time when we’ll all be printing our own custom parts in 3D as and when we need them.
So what’s next? Nobody knows for sure, but what we can all agree on is that there will be more to write on 3D printing history in the future. At the time of writing this guide, the only limitations to date are human imagination, or so it seems. If we keep going like this, there will no longer be any ‘WOW’ factor. Perhaps that’s the only downside for those of us who love a great surprised.
The Road Ahead
Today, 3D printing is becoming more popular among the general public. Most people at least know what it is now, and some of the things it’s capable of. But unlike inkjet printing, few of us create 3D models and print them out on these amazing machines at home. At least not yet! The cost has come down by the thousands of dollars in recent years, and the technology has gotten better and continues to improve. But right now, the average person can’t justify owning their own machines, but this is set to change in the years ahead. It’s going to change because of the types of things we will be able to print in 3D in all kinds of different materials.
Anyone who wants to explore 3D printing and experience the technology can do. You don’t need to own a 3D printer to be able to print in 3D. It’s now possible to design your own 3D models using one of the free online 3D design programs like Tinkercad. Once you model is ready, you can find a local or online service to print your 3D model for you. It’s that easy.
There’s still plenty of future history around 3D printing so watch this space.
Written by Joseph Flynt.
Photo credit Adrian Bowyer
Warning; 3D printers should never be left unattended. They can pose a firesafety hazard.
The Complete History of 3D Printing: From 1980 to 2022
Some desktop 3D printers are inexpensive nowadays — and they can fit on your desktop or in a microwave-sized corner in your kitchen. However, this wasn’t always the case. For most of the history of 3D printing, these machines were the size of small tents, cost hundreds of thousands of dollars, and were suited only for niche projects.
You may be surprised to know that despite its appearance as a new, innovative technology, 3D printing has been around since the mid-1980s. What used to be just industrial 3D printers the size of small cranes transformed into potentially the solution to organ shortages, the housing crisis, and the democratization of manufacturing, in just 30 years.
The history of 3D printing is a long story, and we felt it was important to include everything relevant to the last 30 years of progress. We split the history of 3D printing into four main parts:
Table Of Contents
- History of 3D Printing Part 1: 1980 – 1995, Inception & early innovations in 3D printing
- History of 3D Printing Part 2: 1996 – 2009, the journey to democratization
- History of 3D Printing Part 3: 2009 – 2014: FDM & SLA patents expire, worldwide democratization of 3D printing
- History of 3D Printing Part 4: 2015 – Present – Metal 3D printing, cusp of major developments in 3D bioprinting and construction
- We also keep an up-to-date ranking of the 15 most valuable 3D printer companies.
History of 3D Printing Part 1: 1980 – 1995, Inception & early innovations in 3D printing
Who invented 3D Printing?
In May 1981, Dr Hideo Kodama at the Nagoya Municipal Industrial Research Institute published details concerning a ‘rapid prototyping‘ technique. This research was the first piece of literature to describe the layer-by-layer approach so intrinsic to 3D printing. His research involved printing photopolymers using a method which preceded stereolithography, and also spoke about cross-sectional slices of layers which lay on top of each other to form the 3D object.
However, Dr Kodama didn’t fulfil the patent application before his deadline and was never granted the patent.
Before this however, there were rumblings and references made to a stereolithography-like process in earlier research paper dating back to the 60s and 70s, and in a 1974 New Scientist column, David Jones, writing under the name Daedalus, actually published a satirical piece that jokingly described the SLA process.
Writing as Daedalus in the 3rd October 1974 edition of New Scientist. Source here.“He basically invented stereolithography with a laser, and invented it as a joke. A joke invention, but this one turned out to work!”
— Dr Adrian Bowyer, Founder of the RepRap movement, which will become important further on in 3D printing’s history.![]()
Instead, we had to wait several more years for the birth of 3D printing. But who invented 3D printing?
1984 – 87: Early History of 3D printing & invention of Stereolithography
Three years later in 1984, three French engineers named Alain Le Méhauté, Olivier de Witte, and Jean Claude André filed a patent for the Stereolithography process. They were to pioneer a new manufacturing process that was to revolutionize manufacturing!
But it wasn’t to be. The three men abandoned the patent soon after they filed it, citing ‘lack of business perspective.’ In hindsight, I’m sure they’re gutted.
Just three weeks after the French engineers, Charles ‘Chuck’ Hull filed his patent for Stereolithography, with new features such as the STL file format and digital slicing. His process used ultraviolet light to cure photopolymers. Since filing and obtaining the patents by 1986, Chuck Hull formed 3D Systems and released the first ever 3D printer, the SLA-1, in 1987. 3D printing was born.Chuck Hull with the first ever 3D printer, the SLA-1. Many agree Chuck is who invented 3D printing.
It is therefore arguable that either Chuck Hull or Dr Kodama invented 3D printing, though Chuck Hull is credited far more and rightfully so. Ideas are easy, executing them is the hard part.
1988 – 92: Stratasys, EOS, and FDM and SLS to rival SLA
Stereolithography had competition in the 3D printing space however, with rival processes in development. In 1988, Carl Deckard at the University of Texas filed a patent for Selective Laser Sintering (SLS) technology. Instead of using a UV light, SLS used a laser to trace and solidify layers of powder polymers. This innovative new technology was then leased to DTM Inc to use.
Then it became a three-horse race. Scott Crump co-founded Stratasys in 1989 and filed the patent for Fused Deposition Modeling, probably the most well-known 3D printing technology today. 3D Systems and Chuck Hull may have had a head start, but competitors were hot on his heels. The original FDM patent, granted over 25 years ago.
This competition was further exacerbated by the founding of EOS in 1989 in Germany by Dr Hans Langer. The German juggernaut would go on to dominate the SLS 3D printer market, as well as pioneer Direct Metal Laser Sintering in the mid-90s.
After the release of the SLA-1 a few years prior, Stratasys released their first FDM 3D printer in 1991. This was the first real competition for 3D Systems, as each had the patent rights to two very different 3D printing technologies. FDM parts were stronger and more chemically resistant, but SLA parts could be created quicker, and more accurately. Who would come out on top?
- For an up-to-date comparison of the two technologies as they are today, check out our comparison of FDM vs SLA.
The next year in 1992, DTM Inc brought out their first SLS 3D printer. It is however worth remembering that these machines were behemoths, not the compact and inexpensive desktop machines of today. They competed for industrial prototyping contracts, not to be your Christmas present. Nevertheless, the game was afoot. The three 3D printing technologies, which are still the three main plastic 3D printing technologies, were alive and kicking.
1993 – 95: ZCorp, Color Jet 3D printing, and maturation
Though less known in the modern day, ZCorp were another major 3D printing company back in the early 90s. In 1993, MIT developed a 3D printing technique based on inkjet printers – the ones we use to print in our offices on paper. Adapting this 2D technology for 3D, ZCorp released their first 3D printer, the Z Corp Z402. The technology was originally called Zprinting, though the range are now called Color Jet printers, but the technology is known as Binder Jetting. The first model used starch and plaster-based powder materials and a water-based binder to print objects.
The ZCorp Z402.In the same year, another novel 3D printing solution was brought closer to the market. In 1993, Royden Sanders founded Solidscape (originally called Sanders Prototype Inc. ), which created wax 3D printers. These didn’t create the conventional prototypes that other technologies sought to, but instead made wax molds. These molds were then used in investment casting to create objects out of other, more solid, materials. Solidscape released the Model Maker in 1994, their first wax 3D printer, establishing itself as a favorite among jewelers creating 3D printed jewelry.
In less than ten years, 3D printing had gone from being a fanciful idea on a piece of paper to an effective niche option in small-scale manufacturing. The machines might have been big and slow, but that was the norm in 1995. Even desktop computers were expensive then. Much more was to occur however, as we will find out.
The beginning of house 3D printing
Dr Behrokh Khoshnevis, an academic based in California, first envisioned 3D printing larger layers on huge, industrial-scale printers in the mid-1990s. His focus was on creating enormous parts for airplane propellors or sand molds.
However, in the face of a number of natural disasters, he realized the potential of the technology to create shelters in record time, and for far lower costs.
“In 1994 I started thinking about large-scale fabrication with 3D printing. I wasn’t happy with the speed of fabrication of the early 3D printers, and still they haven’t changed much as far as speed is concerned. I knew there was no other way to increase the speed of 3D printing than increase the layer height, but if you increase layer height then surface quality will suffer.
“So then I came up with the idea that I call Contour Crafting, in 1994. My first patent on it was issued in 1996, a couple years after.”
- You can read our full interview with Dr Khoshnevis here.
This was just the start of what is now one of 3D printing’s most promising applications.
History of 3D Printing Part 2: 1996 – 2009, the journey to democratization
The first ten years of the history of 3D printing led to the birth of future giants such as 3D Systems, Stratasys, and EOS. Still, in the mid-1990s, they were relative minnows compared to the billion-dollar valuations they now possess.
1996 – 98: Arcam, Objet, and the first 3D printing medical breakthrough
The late 1990s was another important time for newly established 3D printing companies. 1997 saw the creation of Arcam, who specialize in metal 3D printer machines and who are the only manufacturer of Electron Beam Melting (EBM) 3D printers. Additionally, the following year saw Objet Geometries established in 1998 in Israel, who would introduce their PolyJet 3D printing technology to the world.Arcam, a major metal 3D printer manufacturer who make Electron Beam Melting 3D printers, were established in 1997. This is one of their current EBM 3D printers.
Stepping away from the purely commercial side of 3D printing, 1999 saw the first extraordinary achievement by 3D printing in the medical industry. Scientists at the Wake Forest Institute for Regenerative Medicine managed to 3D bioprint synthetic scaffolds of a human bladder. They then coated these scaffolds with cells from the patient’s tissue before this newly generated tissue was implanted into the patient. Since this tissue was made from the patient’s own cells, there was a low-to-zero risk of the body rejecting it, marking an important win for 3D printing in medical.
- For more information on 3D printed organs, check out our feature story on 3D bioprinting
- We also have a feature story on 3D printing in medicine
1999 – 2002: 3D printing goes multi-colored, 3D Systems take over SLS
The turn of the millennium brought another set of milestones for 3D printing. ZCorp revealed the first multi color 3D printer, whilst Objet Geometries released their first inkjet 3D printer, both in 2000. Though Stratasys and 3D Systems were still two of the biggest names in the industry, churning out a variety of industrial machines, these hard-working understudies were growing in size and stature.
In a huge move at the time, 3D Systems took control of the Selective Laser Sintering market by acquiring DTM in April 2001. The move was worth $45M and saw 3D Systems become market leaders in two different 3D printing technologies: SLA and SLS.3D Systems’ buyout of DTM meant they controlled both the SLS and SLA market. This is one of DTM’s early SLS 3D printers under the 3D Systems umbrella.
2002: 3D printed bladders, and EnvisionTEC
The 3D printed bladder was merely the start for bioprinting and 3D printing’s ongoing usefulness in medical treatments. In 2002, a 3D printed miniature human kidney was created, again at the Wake Forest Institute for Regenerative Medicine. Though not full size, this represented a key advancement in bioprinting, exciting many that 3D printed organs could solve the shortage of organs available for transplant, and even 3D print hearts.
EnvisionTEC were also established in 2002, who have grown to become a major 3D printing company, selling over 40 printers which are widely used across the jewelry, bioprinting and dental industries.
2004 – 05: Beginnings of RepRap, and 3D Printing goes HD
During the years 2004 and 2005, the beginnings of what is arguably the single most important event in 3D printing history occurred. A senior lecturer at the University of Bath, Dr. Adrian Bowyer, had been inspired by 3D printing and had ideas for 3D printers that could self-replicate — building more versions of themselves.
“I’d been interested in self-reproducing machines since I was a child, I don’t really know where that originated — nearly 70 years ago. That was a constant background interest. Though it wasn’t a research activity, I had not done any research into self-replicating machines.
“They [3D printers] were fabulously expensive: the cheapest one when I started the RepRap project cost around £40,000, and in fact that was one of the ones we bought at the university. When I looked at how it worked, it seemed it would be possible to make such a machine at a considerably reduced price, but my primary aim was to produce a machine that could produce most of its parts. And so, that was the way the project went.” — Dr Bowyer, in an interview with 3DSourced.
The movement, named RepRap (short for ‘replicating rapid prototyper’), started off as an initiative within the University of Bath, but later gained popularity worldwide. The project was open source and focused on the spreading of low-cost 3D printing worldwide, leading to its democratization. Interest in these low cost 3D printers skyrocketed as people edited and tinkered with his designs.
- We’ve also ranked the best RepRap 3D printers.
ZCorp were intent on making 2005 their year too however, announcing their Spectrum Z510 3D printer. This wasn’t your average yearly upgrade with marginally improved specs, but a voyage into the unknown which shattered perceived limitations of 3D printing. The Z510 could not only print in color, but was the first 3D printer that could print in color in HD.
2005 – 08: Binder Jetting, RepRap becomes viable
Also in 2005, ExOne was established as a standalone company from the Extrude Hone Corporation. ExOne would go on to become a leader in Binder Jetting 3D printing, capable of 3D printing objects in metal as well as sandstone. Binder Jetting can create full-color sandstone objects, as well as metal parts with very complex geometries.
Whilst corporations were breaking records, Dr. Adrian Bowyer and his RepRap movement were also hard at work with more wholesome goals. The 2008 release of the ‘Darwin’ RepRap 3D printer was huge – the printer could self-replicate, and people could now easily and cheaply 3D print at home if they had moderate technological and technical knowledge.
Dr Bowyer talking about Vik Olliver using the first RepRap to ever print a part of itself:
“It wasn’t very reliable then! And I didn’t know beforehand because that was actually done by Vik Olliver on the other side of the world! In fact, I didn’t know he was going to try and do that before he did, he did and then put up a blog post and that’s how I learned about it. I thought wa-heyyyy! It worked!”
Darwin wasn’t pretty, but it was functional. What used to be an industry dominated by room-sized industrial machines could now be rivaled by machines that fit on top of a washing machine.
Anyone could easily obtain the parts to create their own Darwin, the only rule being that if you received the parts, you were under obligation to 3D print the parts for more Darwins for other enthusiasts. DIY 3D printer kits would go on to have an incredible impact.
Images of the first self-replicated Darwin RepRap 3D printers. Dr Adrian Bowyer is on the left.2008: Thingiverse, and the begininng of 3D printed prosthetics
Although now widely known, a small website called Thingiverse, owned by a fledgling company called Makerbot launched in 2008. Thingiverse allowed designers to upload their 3D printer models built on various 3D software for others to download for free and print at home. Since everybody loves free stuff, Thingiverse soon took off. It is now in the top 700 most popular websites in the USA, and just outside the top 1,000 websites in the world. Thingiverse now hosts over a million STL files that anyone can download and tinker with.
- We also have a list of 15 of the best sites to download 3D printer files.
Another major event in 2008 was the first 3D printed prosthetic. This extraordinary achievement was compounded by the fact that this prosthetic leg did not need to be assembled, it was 3D printed to function immediately. This opened many people’s eyes to how 3D printing could save time and labor, as fully-assembled objects could be printed from scratch.
The one-off nature of 3D printing also suggested that it would be the perfect method to create customized prosthetics and medical implants based on individual patients’ needs. Instead of the usual several-month lead times for prosthetics, 3D scanners could scan a patients’ arm or leg, and almost immediately begin to create a prosthetic that fit them perfectly.
Now in the present day, thousands of volunteers work to create 3D printed prosthetic hands and arms for children born without them. The project, called E-Nable, encourages people to print their own prosthetic hands to give away, and to develop and improve existing prosthetic models.
- We also have a full feature story on how millions of lives can be improved by 3D printed prosthetics.
Finally in 2008, Stratasys released a new material compatible with their FDM 3D printers. This wasn’t any material however, but a material that was bio-compatible. This opened the door for 3D bioprinting to become far more widely available in the near future.
The years up to the start of 2009 were an adolescence for 3D printing. New technologies became available such as Electron Beam Melting and Binder Jetting, medical advances were made, and the RepRap movement became viable.
In 2009 however, US patent law meant that within a few years 3D printers would become cheap enough for everybody to have one in their home if they wished.
House printing moves forward, and into space
Dr Khoshnevis refined and improved his house 3D printing technology — called Contour Crafting.
“We [managed to first accurately extrude concrete] around 2003.
And in 2004 my work became very famous, in the New York Times… and that’s when the world learned about [Contour Crafting], and it inspired a lot of others to go after it.”
However, facing economic disaster after the crash of 2008, the housing market bombed, along with Dr Khoshnevis’ investment from the industry.
“So I had to also chase the money. In 2008, 2009, real estate went down… and with it went construction, and the support I was getting from industry disappeared. So that’s when I started thinking about space.”
Without funding or support, yet fully confident Contour Crafting could change the world, Dr Khoshnevis embarked on his multi-planetary construction 3D printing vision.
The idea was deceptively simple: if we could print concrete on a 3D printer on Earth, an adapted version could be made that could print with locally-sourced lunar regolith to create Moon (or Mars) bases for permanent settlements in the near future.
History of 3D Printing Part 3: 2009 – 2014: FDM & SLA patents expire, worldwide democratization of 3D printing
A patent expired between end tail end of 2008 and the beginning of 2009. Big deal, patents expire all the time right? This patent was owned by a now-very-large company called Stratasys, for Fused Deposition Modeling technology.
FDM is the simplest 3D printing technology; it involves heating up a plastic filament until it melts, and then extrudes it out layer-by-layer. Since the technology could be replicated the most cheaply, business-minded hobbyists and small businesses watched on eagerly for the patent to fall into public domain so they could create their own versions.
The two biggest events in the history of 3D printing, for every day fans, was firstly the development of the RepRap 3D printer. This showed that low cost 3D printers could be done, and that most of the 3D printer parts could be 3D printed by another printer.
The second event was the expiration of the FDM patent. This meant that anyone could not build these cheap 3D printers with no legal issues, and set the tone for incredible advances in the industry.
2009: The first affordable FDM 3D printers
The first affordable FDM 3D printer kit was released in January 2009. It was called the BfB RapMan printer and although it was first, it wasn’t ugly or terrible. Future iterations were made, and perhaps it would have made a bigger impact if the fledgling company we mentioned earlier hadn’t appeared three months later.The BfB RapMan, the first affordable FDM 3D printer kit.
The first Makerbot DIY 3D printer kit released in April 2009. Makerbot were supporters of the open source community, and their first printer, called Cupcake CNC, could be built entirely from parts downloadable from Thingiverse. Demand exploded, and Makerbot had to ask their customers for help to create parts for their backlog of orders. Makerbot were becoming the early kings of affordable desktop 3D printers.
Makerbot’s first model, the Cupcake CNC.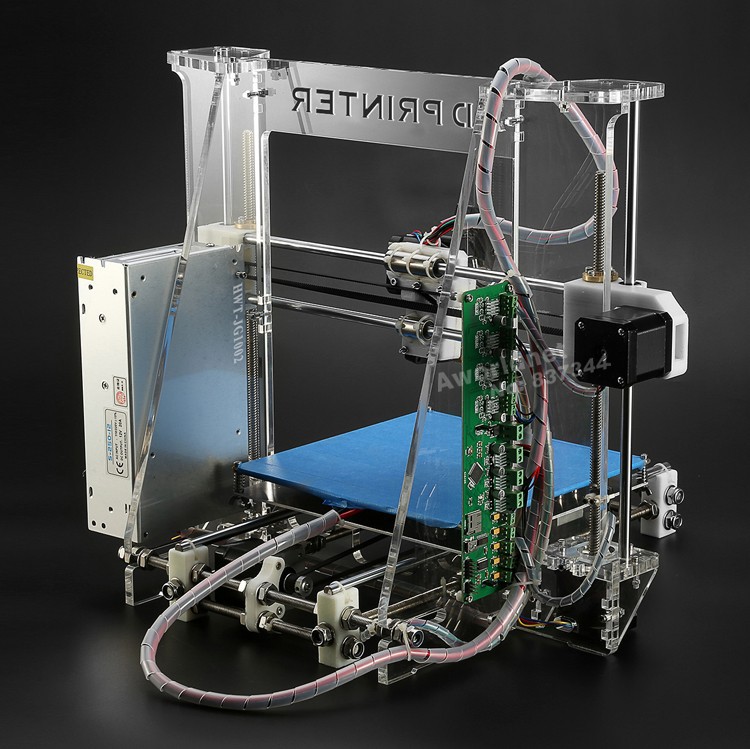
2009 wasn’t just a year for FDM printers however. Organovo, a 3D bioprinting firm, managed to create the first 3D printed blood vessel. This was managed on a new 3D bioprinter which showed significant promise for the future creation of whole organs such as kidneys and hearts.
- We also have a feature story on how close we are to functioning 3D printed hearts.
2009 – 11: Cars, gold jewelry, and the rise of Ultimaker
In recent years, online 3D printing service companies had sprung up to capitalize on the growing demand for 3D printed parts. These services work by allowing users to upload models they have either designed or downloaded, and pay for them to be 3D printed and mailed to their door. Some even allow users to sell their designs on an online marketplace and get paid for their designs.
Companies like Shapeways, Sculpteo, i.materialise, and later 3D Hubs, grew to print hundreds of thousands of parts on demand by the early 2010s. i.materialise then made headlines in 2011 when they were the first to offer 14k gold and sterling silver as 3D printable materials. Anyone who had designed something on their computers at home could (if they had deep enough pockets) have their model 3D printed in gold. The possibilities for custom and high fashion 3D printed jewelry expanded.
Also in 2011, Kor Ecologic produced the first 3D printed car. The car, called Urbee, uses electric motors and gets 200 miles to the gallon.
- Check out our ranking of the most exciting 3D printed car projects.
Though Makerbot had dominated the open source, desktop 3D printer market, competition was about to toughen up. Ultimaker was established in 2011 in Geldermalsen, Netherlands, and released the first Ultimaker 3D printer in March 2011. The Ultimaker Original was made from laser-cut plywood and proved an enormous success, launching them into the spotlight.The first Ultimaker 3D printer was a hit with 3D printing enthusiasts.
2012 – 14: The democratization of Stereolithography
Though the original patents for Stereolithography had expired over five years before, nobody had yet been able to create an affordable SLA 3D printer. This changed in June 2012 when the B9Creator released after raising over $500,000 on Kickstarter. The B9Creator utilized a similar technology to Stereolithography called Digital Light Processing (DLP), and could be pre-ordered for $2,375.
6 months later, the affordable resin 3D printer game was changed again, when a new and then unknown startup called Formlabs launched their Kickstarter campaign for a 3D printer called the Form 1. You could pre-order a Form 1 starting at $2,299, and unlike the B9Creator it utilized Stereolithography. The project was an instant hit, raising an almost unprecedented $2.95 million in 30 days. Formlabs have since gone on to release SLS 3D printers, an upgraded SLA 3D printer in the Form 3, and grow to a billoin-dollar valuation.
2012 – 13: Stratasys & Objet merge, Stratasys buys Makerbot
Objet Geometries had gone from strength to strength since the early 2000s, improving their PolyJet technology that could print in full-color. This eventually led to possibly the biggest acquisition in the history of the 3D printing industry. On April 16th 2012, Stratasys announced that it had merged with Objet in an all-stock transaction, with Stratasys being the surviving company. Stratasys would own 55% of this new company, with Objet owning 45%. This gargantuan deal meant the new Stratasys was worth $3 billion at the time.
Stratasys didn’t stop there however. Despite competition from Ultimaker, and open source fans Aleph Objects (who produce Lulzbot 3D printers), Makerbot were still doing very well. On June 23rd 2013, Stratasys announced that Makerbot was the newest item on its shopping list, acquiring the FDM 3D printer giant in a $604M deal, with $403M paid upfront in stock. The founders of Makerbot have all since departed, and their newest machines are no longer open source.
Cody Wilson and the 3D printed gun
Later in 2013, Cody Wilson became a viral sensation after his company Defense Distributed posted an STL file on its site for 3D printing a working 3D printed gun. The US Government ordered Defense Distributed to remove the designs three days later, but the gun had already been downloaded over 100,000 times.
Metal 3D printing has recently become big talk, but before 2015 when tens of startups appeared, the industry was dominated by a few large players like EOS, Arcam and SLM Solutions. 3D Systems’ intent in getting involved in the metal 3D printing sector led to them acquiring French company Phenix Systems in July 2013. 3D Systems paid $15.1M for 81% of the shares and integrated Phenix’s metal 3D printers into their product range.
2014: 3D Printing in space, and SLS and SLA patents expire
A few years after turning his attention to space, Dr Khoshnevis won NASA grand prizes, winning key prize money to further the research.
“We demonstrated at least two technologies that are viable. Technologies for building vertical structures such as hangars, shade walls, radiation protection walls, blast protection walls, and horizontal structures most particularly the landing pads, roads, we demonstrated the feasibility of those entirely to be made with in situ material.
![]()
“We actually built… and demonstrated it, that’s why we got Grand Prizes from NASA. My hope and expectation is that those technologies will eventually be used for planetary missions.”
The following year, a more wholesome achievement in 3D printing was realized. NASA announced they had used a 3D printer in space and created the first 3D printed object in space in 2014. This opened the door for future space manufacturing and the ability of future astronauts to create tools on-demand in space. If the team in space needed a particular item, they could be ‘beamed’ the design from Earth at light speed, and 3D print the tool out in space.
2014 was another big year for patents related to 3D printing expiring. First, the major SLS patent expired in 2014, meaning that cheaper alternatives could start being designed by individuals so inclined. Companies like Sintratec and Formlabs worked to create less expensive SLS 3D printers that were still viable. Up until then, most SLS machines were industrial, room-sized behemoths which started at $250,000. This new wave of SLS printers started at $5,000, helping to democratize Selective Laser Sintering.The patent for SLS which expired in 2014.
Moreover, on March 11th 2014 another major 3D printing patent expired. Though Chuck Hull’s original patent had expired a decade earlier, this new patent expiry meant a much more innovative SLA 3D printing process was now in the public domain. Companies such as Formlabs had launched SLA 3D printers a couple of years previously, which patent-holder 3D Systems did not take a shining to. In fact, 3D Systems sued Formlabs in 2012 after they raised their $2.9M from Kickstarter. The case was eventually settled, with Formlabs agreeing to pay an 8% royalty on all sales to 3D Systems.
Similarly, the original SLA patents expired in 2014.Though 3D printing had always previously been an industry dominated by a few large firms, this period was especially significant. The two original companies, 3D Systems and Stratasys, solidified their hold on the market by acquiring competitors like Phenix, Makerbot, DTM, Objet, and more.
The industry was far from a monopoly, however. Huge numbers of new competitors offered affordable machines that rivaled industrial 3D printers. Examples include Ultimaker, Lulzbot, and Prusa 3D printers in the desktop and DIY 3D printer kit markets, and Desktop Metal, Markforged, and Carbon 3D in the industrial sector. We will speak more on these newly-mentioned companies in the next part.
History of 3D Printing Part 4: 2015 – Present – Metal 3D printing, cusp of major developments in 3D bioprinting and construction
Carbon 3D and Desktop Metal: 0 to $1 billion in 3 years
Carbon 3D was formed on July 11th 2014 in California by Joseph and Philip DeSimone. The main tech behind the company was inspired by Terminator 2, and was named CLIP (Continuous Liquid Interface Production). By the end of 2017 the company had raised over $360 million and had a valuation of $1. 7 billion – more than Stratasys and 3D Systems (both companies fell sharply in value after the 2013-14 3D printing hysteria died down from valuations in excess of $3 billion previously).
But how did they manage this?
In March 2015, Joseph DeSimone gave the now-viral TED Talk about 3D printing 100x faster. This announced very clearly to the world that Carbon 3D were ones to watch if they could make their CLIP technology feasible. A major grievance of 3D printing was that it was too slow to ever be relied upon as a medium-volume manufacturing option. If Carbon 3D could really print so much faster, it would rival injection molding and other processes for large-volume plastic parts.
They were not the only new 3D printing startup to reach astronomical valuations and receive hundreds of millions of dollars in investment however. Another example is Desktop Metal, who at the same time released their Studio and Production System metal 3D printers.
Since being founded in October 2015, Desktop Metal have received over $200M in investment and the company is now valued at over $1bn. Interestingly, Desktop Metal’s technology, Bound Metal Deposition, is very similar to FDM, just that it works with metal instead. There’s a reason that Silicon Valley investors (as well as Ford, Google, BMW, GE, and more) clamored to invest – their metal 3D printers can print metal 10x cheaper than alternative printers!
Desktop Metal’s Production System metal 3D printer, their more expensive and premium printer, uses a new type of binder jetting technology called Single Pass Jetting. This technology allows for the building of metal parts in minutes, rather than hours as with Direct Metal Laser Sintering. It truly is revolutionary, promising to change metal manufacturing in the near future.
- For more info on recent 3D printing success stories, check out our 15 most valuable 3D printer companies ranking.
Though they may both be innovative, companies like Carbon 3D and Desktop Metal are valued very high compared to their current sales and profits. This is because investors are confident that they will grow to be far bigger and more profitable in the future. This trend occurs in most markets, not just 3D printing.
Take Tesla for example – their revenues are dwarfed by some of the larger carmakers, yet Tesla’s market cap is larger than Ford. This is based on belief that Tesla will become the largest carmaker in the world in the future. We will have to see whether companies such as Carbon and Desktop Metal, as well as others like Markforged, Formlabs and Xact Metal can fulfill their investors’ hopes in the same way.
3D Systems enter the Hall of Fame
30 years after 3D Systems had kickstarted the industry, their first ever 3D printer, the SLA-1, was declared a Historic Mechanical Engineering Landmark by the American Society of Mechanical Engineers. This formal recognition of the machine that started it all showed how far 3D printing had come since the 80s.
The SLA-1 was hailed a historic mechanical engineering landmark in 2016.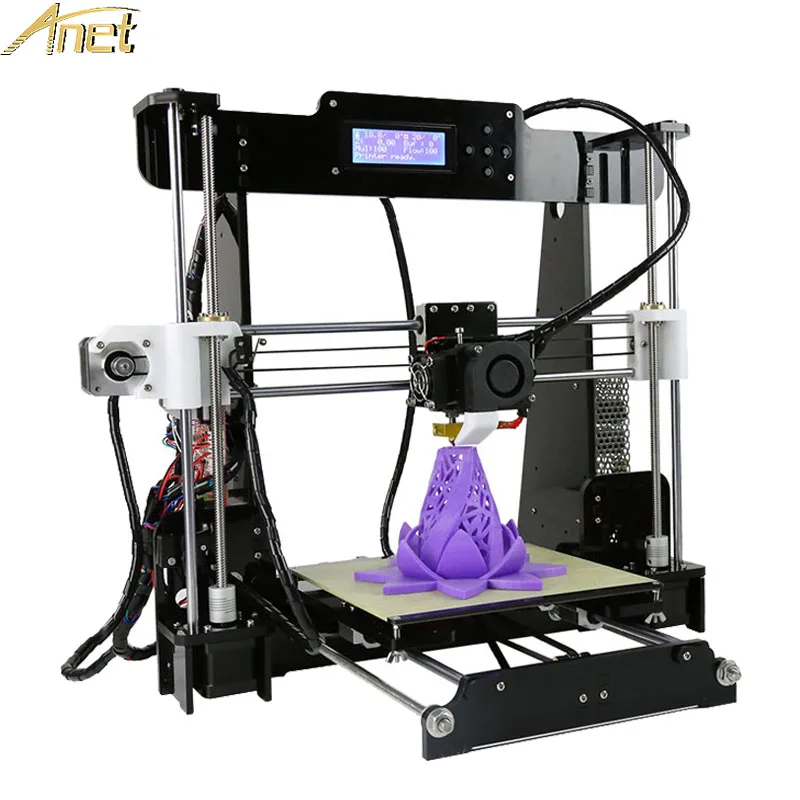
At around the same time, two very big technology companies entered the market. Household name big.
GE and HP enter
The first was HP, leaders in inkjet 2D printing, who in 2016 announced that they would sell printers featuring their patented Multi Jet Fusion (MJF) technology. HP have since gone on to refine this technology, and in 2018 announced full-color 3D printers, industrial 3D printers at a much lower price range of $50,000, and a move into the metal 3D printing market.
The second household name was GE. Following the incorporation of a new company called GE Additive, the multinational giant acquired metal 3D printing companies Arcam and Concept Laser in late 2016 as part of a $1.4bn move into the additive manufacturing industry. GE Additive also tried to acquire SLM Solutions, but were ultimately unable to.
The incumbents now had HP and GE to worry about too. These deep-pocketed giants could invest billions in gaining a crucial technological advantage, and were now forced to innovate harder than ever. Competition is usually only a good thing for consumers however, as each company worked harder and harder to optimize their technologies to be as effective as possible.
The Ultimaker 3
Regarding the desktop 3D printer market, Ultimaker’s October 2016 release of the Ultimaker 3 was another landmark. It was an instant hit, earning boatloads of Best 3D Printer awards and cementing Ultimaker as a key player in the industry, while remaining committed to the open source philosophy. Ultimaker have since released the S3 and S5, which have received positive reviews.The Ultimaker 3 is one of the best 3D printers on the market.
3D printing in construction: a very exciting prospect
But while all these companies were concentrating on 3D printing for manufacturing, others saw it as the solution to the growing housing crisis. 3D printing in construction was a $70M industry in 2017, but reports project it to be worth $40bn by 2027.
Companies such as Apis Cor and WinSun were started, creating huge concrete 3D printers that could build skeletons of houses far quicker and cheaper than any human. This advance was immortalized by Apis Cor 3D printing a whole house in just 24 hours. Other construction and architectural projects involving 3D printing were completed throughout the 2016-2018 period include 3D printed bridges, houses, and even plans for skyscrapers in Dubai.
Ultimaker S5 vs Makerbot Method: The Prosumer 3D Printer Battle 2018/19
Both Ultimaker and Makerbot grew extraordinarily throughout the mid-2010s, and were flying high off their Ultimaker 3 and Makerbot Replicator ranges respectively. By mid-2018 this battle was to move into the prosumer 3D printer range with the release of the Ultimaker S5 in May 2018, and the Makerbot Method in December. Both represented a step up in price, from around $3,000 up to over $5,000.
This was a change from both companies’ roots. They started building small FDM printers — remember the original kits made of wood? — and were previously more aligned with the RepRap philosophy. This move upmarket is an interesting one, though it is worth noting that Makerbot offer a Replicator+ model catered especially to 3D printing in education, retailing at around $2,000.
The Low Cost LCD 3D Printing Revolution
Resin 3D printers used to cost thousands, and that would only afford you a basic SLA printer. Then Digital Light Processing came along a number of years ago, offering a more scalable and modern alternative.
Then it was the turn of LCD 3D printing — more similar in process to DLP than SLA — to usher in the new era of low cost resin printing. Suddenly low cost resin printers like the ELEGOO Mars and AnyCubic Photon offered reasonably accurate resin prints at a printer cost of less than $500. When the first Formlabs printers came out, people found it astonishing that you could print accurate resin objects for $3,500 — oh how things have changed.
- We have a ranking of 5 of the best cheap LCD 3D printers.
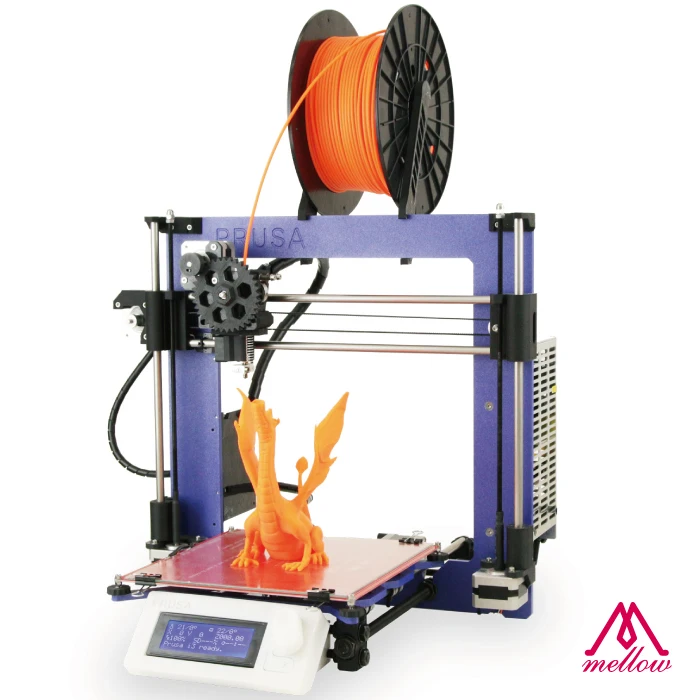
World’s Biggest 3D Printed Building: Apis Cor One-Ups Itself
Apis Cor already made headlines when they built a house in 24 hours. Then in October 2019 they went further, building a huge 3D printed building in Dubai. Dubai has been known for its openness to innovative new technologies, especially 3D printing, with this huge structure earmarked for administrative staffing.
Carl Deckard, inventor of SLS, dies at 58
One of the four original 3D printing company founders, Carl Deckard passed away on December 23rd 2019, at the age of just 59. The genius inventor of Selective Laser Sintering had since founded a number of other companies and held 27 patents, and was the most major figure in the history of 3D printing to pass away.
The founders of SLA and FDM, Chuck Hull and S. Scott Crump respectively, are still part of their companies, that are now both public and boast valuations of just under $1 billion dollars. It is unknown how much equity they hold.
EOS’ founder Dr Hans Langer, is 3D printing’s first and currently only billionaire, with an estimated net worth of $3. 1bn as of August 2020 according to Forbes. The German company never went public, and is still successful 30 years on in the SLS and DMLS 3D printer markets.
History of 3D printing
In this section, we wanted to trace the history of 3D printing from its inception to the present day, as well as give a forecast regarding the future development of technology.
The first 3d printer was invented by the American Charles Hull, he worked on the technology of stereolithography (SLA), a patent for the technology was issued in 1986. The printer was a fairly large industrial installation. The installation "grew" a three-dimensional model by applying a photopolymerizable material to a moving platform. The basis was a digital model pre-modeled on a computer (3D model). This 3d printer created three-dimensional objects, rising by 0.1-0.2 mm - the height of the layer. Despite the fact that the first device had many disadvantages, the technology has received its application. Charles Hull is also the co-founder of 3dsystems, one of the world's leading manufacturers of industrial 3D printers.
Charles Hull was not the only one to experiment with 3D printing technology, as in 1986 Carl Deckard invented Selective Laser Sintering (SLS). You can learn more about the method in another article, briefly: a laser beam sinters a powder (plastic, metal, etc.), while the mass of the powder is heated in the working chamber to a temperature close to the melting point. The basis is also a digital model pre-modeled on a computer (3D model). After the laser passes through the horizontal layer, the chamber is lowered to the layer height (usually 0.1-0.2 mm), the powder mass is leveled with a special device and a new layer is applied.
However, the most famous and widespread 3D printing method today is layer-by-layer direction (FDM). The idea of technology belongs to Scott Crump (Scott Crump), the patent dates back to 1988. You can learn more about the method in another article, in short: material (usually plastic) is fed from the heated nozzle of the print head using a stepper motor, the print head moves on linear guides along 1 or two axes, and the platform moves along 1 or 2 axes . The basis of the movement is also a 3D model. The molten plastic is laid on the platform along the established contour, after which the head or platform is moved and a new layer is applied on top of the old one. Scott Crump is one of the founders of Stratasys, which is also one of the leaders in the production of industrial 3D printers.
All the devices described above belonged to the class of industrial devices and were quite expensive, so one of the first 3d Dimension printers from Stratasys in 1991 cost from 50 to 220 thousand US dollars (depending on the model and configuration). Printers based on the technologies described above cost even more and until very recently, only a narrow circle of interested specialists knew about these devices.
Everything began to change since 2006, when the RepRap project (from the English Replicating Rapid Prototyper - a self-replicating mechanism for rapid prototyping) was founded, with the goal of creating a self-copying device, which was a 3D printer working on technology FDM (layer by layer deposition). Only, unlike expensive industrial devices, it looked like a clumsy invention made from improvised means. Metal shafts serve as a frame, they also serve as guides for the print head. driven by simple stepper motors. The software is open source. Almost all connecting parts are printed from plastic on the 3D printer itself. This idea originated among English scientists and aimed at spreading available additive technologies so that users can download 3D models on the Internet and create the necessary products, thus minimizing the production chain.
Leaving aside the ideological component, the community (which exists and develops to this day) managed to create a 3d printer accessible to the "ordinary person". So a set of unprinted parts can cost around a couple of hundred US dollars and a finished device from $500. And even though these devices looked unsightly and were significantly inferior in quality to their industrial counterparts, all this was an incredible impetus for the development of 3D printing technology.
As the RepRap project developed, 3D printers began to appear, taking as a basis the base laid down by the movement in technical and, sometimes, ideological terms (for example, commitment to the concept of open source - OpenSource). The companies that made printers tried to make them better both in terms of performance, design and user experience. The first RepRap printers cannot be called a commercial product, since it is not so easy to manage (and even more so to assemble) and it is not always possible to achieve stable work results. Nevertheless, companies tried to close the more than significant gap in quality, leaving a significant gap in cost whenever possible.
First of all, it is worth mentioning the MakerBot company, which started as a startup, took RepRap ideas as a basis and gradually turned them into a product of a new quality.
Their flagship product (and in our opinion the best to this day) remains the MakerBot Replicator 2 3D printer. The model was released in 2012 and later discontinued, but remains one of the most popular 3D printer models to this day " personal" segment (according to 3dhubs). The word "personal" is in brackets because this printer, which cost $2,200 at the time of release, was (and is) primarily used for business purposes, but falls into the personal segment due to its cost. This model differs from its progenitors (RepRap), being, in fact, a finished commercial product. Manufacturers abandoned the concept of OpenSource, closing all sources and software codes.
In parallel with the release of equipment, the company actively developed the Thingiverse resource, which contains many models for 3d printing, available for download for free. During the development of the first printer and beyond, the community has helped the company a lot, testing the product and offering various upgrades. After the release of the Replicator 2 (and the closure of development), the situation has changed. You can learn more about the history of MakerBot and other companies and people associated with 3d printing by watching the film Print the legend.
This film also highlights the history of Formlabs, one of the first companies to launch an affordable 3D printer based on SLA (Strereolithography) technology. The company raised funds for the first FORM 1 model through crowdfunding, encountered production difficulties, but eventually released an affordable and productive 3D printer, closing the quality gap described above.
And although the 3D printers described above were far from perfect, they laid the foundation for the development of affordable 3D printing technology, which continues to this day. At the moment, the quality of FDM and SLA printers is increasing, but there is no significant price reduction, rather, on the contrary, it is growing slightly. Along with FDM and SLA, many companies are developing in the field of powder sintering (SLS), as well as metal printing. Despite the fact that such printers cannot be called affordable, their price is much lower in comparison with analogues from the professional segment. It is also worth noting the development of the line of materials, in addition to the standard ABS and PLA plastics, today many different materials are used, including nylon, carbon fiber and other durable and refractory materials.
Personal 3d printers of today are very close to professional devices, the development of which also does not stop. In addition to the "founders" of the technology (Stratasys, 3dsystems), many small companies specializing in industrial 3D printing technologies (metal in particular) have emerged. 3D printing is also attracting the attention of large corporations, which, with varying degrees of success, are striving to take their place in a growing market. Here it is worth highlighting HP, which recently released the HP Jet Fusion 3D 4200 model, which has gained popularity among 3d printing professionals (as of 2018, it is at the top of the ranking of professional 3D printers in the quarterly reports of the 3dhubs portal).
However, 3D printing technologies are developing not only in breadth, but also in depth. One of the main disadvantages of 3D printing, compared to other production methods, is the low speed of creating models. A significant advance in terms of accelerating 3D printing was the invention of CLIP technology by CARBON, printers operating on this technology can produce models 100 times faster than classic SLA technology.
There is also a constant expansion of the range, properties and quality of materials and post-processing of products. All this accelerates the transition to the use of 3d printers in production, and not just as prototyping devices. Today, many large and not only companies and organizations are closely using a 3D printer in their production chain: from consumer goods manufacturers NIKE and PUMA to BOEING and SPACE X (the latter prints engine parts for its rockets that could not be made in any other way) .
In addition to the "classic" scope of 3D printing, today more and more often you can see news about how a house or some organ (or rather, a small part of it) was printed on a 3D printer from bio-material. And this is true, several companies around the world are testing or already partially using 3D printing in the construction of buildings and structures. This mainly concerns the contour pouring of walls (similar to the FDM method) with a special composite concrete mixture. And in Amsterdam there is a 3D printed bridge project and this list will only expand over time, since the use of 3D printing in construction can significantly reduce costs and increase the speed of work at certain stages.
With regards to medicine, here 3D printing also finds application, but at the moment it is not printing organs, but rather the use of technology in prosthetics (of various kinds) and bone replacement. Also, 3D printing technology is widely used in dentistry (SLA technology). Regarding the printing of organs, this is still far in the future, at the moment bio-3D printers are experimental facilities in the early stages, the success of which is limited to printing a few limited-viable cells.
Looking to the future, it is safe to say that 3D printing technology will expand both in breadth and depth, improving technology, speeding up processes, improving quality and improving material properties. 3D printers will increasingly replace old methods in production chains of various scales, and world production, due to this, will move towards the “on demand” scheme of work, increasing the degree of product customization. Perhaps someday, 3D printers will be widely used at the household level for the production of necessary things (the dream and goal of the RepRap movement), but this requires not only the development of technology, but also a paradigm shift in social thinking, as well as the development of a powerful design ecosystem ( 3d modeling) products (which is often forgotten).
3d printing of houses (and other structures) will no doubt also develop, reducing costs and production time, which, together with the development of new approaches in architecture and urban planning (such as modular construction and the prefabricated method), will give a tangible impetus to development the industry as a whole.
Biological 3D printers will be an important tool in scientific research. However, before they appear in hospitals and clinics, where they will print new organs, it is still very, very far away (in fact, this is science fiction).
The History of Modern 3D Printers — — IS Consulting
Even before the advent of writing, people learned to share information through drawings on cave walls. But this method had a significant drawback: these records could not be taken with you. Over time, mankind came up with printing technology, and in subsequent centuries it changed significantly and reached a three-dimensional, three-dimensional version.
The first mention of printing dates back to the second century. At that time, a kind of paper and paint had already appeared in China, people had learned to engrave texts on various surfaces. At first, they printed on marble columns, stones, but gradually switched to more convenient wooden bars.
After the invention of paper, printing began to develop more strongly. In the fifteenth century, Johannes Gutenberg came up with the idea of casting stencils with letters from lead and using them for subsequent printing on paper. Approximately two centuries later, mankind moved from stencils to printing presses. The first production typewriter was designed by Terry Pelegrino in 1808. And in 1868 a patent was issued for a typewriter, which already looked more like devices used at the end of the last century.
The first black and white printers appeared in 1985, and in 1988 the production of color models began. Today, large and small printers can be found in the office, at school, and even in almost every home, because these devices are needed for study or work.
In the mid-1990s, a situation developed in the world economy in which the volume of sales of manufacturing plants decreased several times, which meant a transition to small-scale production. Ultimately, companies found that developing molds, patterns, and prototypes for more and more new models was very expensive. Approximately then, devices that can quickly and cost-effectively produce models become popular - machine tools with numerical control. Many of them remained in the manufacturing sector, but the intensive development of a separate branch of “evolution” led to the emergence of office 3D printers - this is how the history of 3D printing began.
3D printing dates back to 1948, when the American Charles Hull developed a technology that allows growing three-dimensional objects from photopolymers in a liquid state under the action of a laser. And only in 1986 he received a patent for his invention. In the same year, he founded 3D System and began developing the first industrial 3D printing machine, which was released to the public a year later in 1987. Of course, this was not yet the first 3D printer in the modern sense, but it was she who determined that objects were built up in layers.
An interesting fact is that Hull was a chemist and his invention came to him in a dream. And now, thanks to his offspring, you can make a revolution in medicine. With its help, teeth, bones and even entire organs are already being printed.
With his first printer and the founding of 3D Systems, now in the hundreds of millions of dollars, Hull launched an entire industry. And although 3D printing is a familiar name for it, another term is gaining popularity - "additive technologies". This definition is more capacious and better reveals the essence of the invention. After all, this revolution lies in the fact that, unlike traditional production methods, when a finished product is obtained from a finished piece of material by processing, cutting off the unnecessary, the opposite happens with an additive approach: the product is created by gradually adding fresh material. The process itself is as follows: a laser beam initiates a photopolymerization reaction, the plastic hardens, and after a certain number of steps you get a finished object. Similar reactions have been known for a long time, but it took time to combine them with the use of printing.
Around the same time, the development was carried out by the Japanese Hideo Kadama and several French scientists who even managed to get a patent. But Charles Hull went further and created the company 3D Systems for the commercial use of patented developments. Therefore, he gained great fame.
Initially, 3D Systems created several installations that were called "stereolithography apparatus". After receiving feedback from its customers, the company improved the device and released the SLA 250 model. Stereolithography continues to improve: the layer thickness of this technology is 0.05-0.15 mm, and object sizes are about 50-60 cm, although there are exceptions, reaching up to 2 meters.
The first consumer printers from 3D Systems appeared in early 2012. They were several dozen times smaller and lighter than their "ancestors".
Charles Hull was not the only inventor who experimented with 3D printing technologies. Along with stereolithography, other 3D printing technologies also developed.
The technology of forming three-dimensional models from layered sheet material (LOM) appeared in 1985, a year before Charles Hull received a patent for stereolithography. Its author is Mikhailo Feigen, who proposed layer-by-layer formation of three-dimensional models from sheet material: films, polyester, composite, plastic, paper, etc., fastening the layers together using a heated roller.
Making a model by hand would require several days or even weeks of work, and with the help of a LOM printer, such a model can be recreated in a few hours.
Models made using the M. Feigen technology turn out to be rough, it is difficult to remove excess material from their surface due to the risk of delamination.
In 1986, Carl Descartes invented the method of selective laser sintering. The essence of the method lies in the layer-by-layer sintering of the powder material by a laser beam.
In the working chamber, the powder is heated to a temperature bordering on the melting point. After that, the material is leveled and the laser beam draws the necessary contour on its surface. When the beam touches the powder, it is heated to the melting point and sintered. After that, a new layer of powder is poured into the chamber, and the sintering process is repeated. The cycles of adding material, its leveling and sintering are repeated according to a predetermined scheme until a finished model with a rough porous structure is formed on the working table of the chamber. The finished product is removed from the printer and excess powder is removed.
The device is capable of working with powder polymers, foundry wax, nylon, ceramics, metal powders, while switching from one material to another, the chamber should be thoroughly cleaned of the remnants of the previous material. Several models can be grown in one chamber at once.
Layered compaction technology was developed by the Israeli company Cubital in 1987. At its core, it resembles photocopying. On a selectively charged plate made of glass, a pattern of the base of the model is formed. This template is placed over a thin layer of photopolymer evenly distributed over the work surface, after which it is exposed to ultraviolet light. The photopolymer layer corresponding to this template layer becomes solid, liquid residues are removed, and the voids are filled with liquid wax, which quickly hardens. The described sequence of actions is repeated many times until the finished model is formed. The operation of the machine can be paused to remove defective layers, and later resumed.
The device, based on SGC printing technology, uses expensive, toxic and quite rare polymers. It works quite noisily and requires constant monitoring by the operator. The estimated cost of the 3D printer is $470,000.
In 1988, Scott Crump patented his invention, the idea of which is layer-by-layer casting with an extrudable melt. The essence of the technology lies in the fact that in the print head the material (melt from plastic, metal, casting wax) is preheated to the melting temperature and enters the working chamber. The head releases the molten material in the form of a thread, which is laid on the work table. After that, the platform is lowered down by the thickness of one layer so that the next layer can be formed.
After receiving a patent for the invention, Scott Crump founded the Stratasys company for the production of 3D printing devices. The first 3D Dimension printer with an extruding print head appeared in 1991, its estimated cost was from 50 to 220 thousand US dollars.
Selective laser sintering (SLS) was invented by Deckard and Beeman at the University of Texas at Austin. The two scientists also formed a company to promote their technology, but in 2001 it was bought out by 3D Systems.
The modern historical stage in the development of 3D printing started in 1993 with the creation of Solidscape. It produced inkjet printers that preceded 3D printers. In 1993, 2 students at MIT came up with "3D printing technology" or 3DP. This development resembled the printing process of an inkjet printer. He created images not on paper, but in a special container, and they were voluminous. Then, in 1996, the concept of "3D printing" and the first 3D printer appeared. The sale and creation of devices according to this principle was carried out by Z corporation, which lasted until 2012, since it was bought out by 3D Systems.
The first 3D printers had low power, worked slowly, and as the speed increased, the products were obtained with large errors. Only in 2005 did 3D printers with high print quality appear.
The next milestones in this field were in 2005 (color printing appeared) and 2006, when Adrian Bower founded the RepRap project.
It is on the Bower principle that most modern 3D printers with FDM technology work. The goal of the RepRap project was to create 3D printers that could replicate their parts. Two years after the start of the project, the English designers of the University of Bath released a printer that is capable of printing about half of its parts.
Until 2008, any 3D printer could only work with the use of one type of consumable - ABS plastic. This is one of the best consumables for 3D printing. But Objet Geometries Ltd. developed the Connex500 printer, which could work with different types of materials at the same time.
The history of the creation of a 3D printer continued with the emergence of a technology called PolyJet, based on the use of photopolymer liquid plastic. With this method of printing, the head "draws" a layer of photopolymer, which is instantly illuminated by a lamp. The method turned out to be advantageous in many respects: its price is much lower, and high accuracy makes it possible to manufacture not just models, but ready-to-use parts.
In 2010, a group of scientists from the Fluid Interfaces Group from the Massachusetts Institute of Technology presented to the public the first 3D printer "Cornucopia" for recreating food. Instead of plain paper, food is loaded into the food printer, which the machine cools, mixes and uses to create the finished product.
The main inventors of the printing device "Cornucopia" are scientists Amit Zoran and Marcello Coelho. Their innovative device is able to take cooking to a new stage of development. The concept will be able to "print" previously unknown dishes with a predetermined nutritional value, quality and taste.
The following year, a biological printer appeared, printing with human and animal stem cells.
At the end of the first decade of the 21st century, a group of scientists from the Institute of Regenerative Medicine at Wick Forest University came to the conclusion that human tissues can be printed using inkjet printers, filling them with living cells. From that moment, painstaking work began on the creation of a bioprinter for growing human organs. Such a device was demonstrated in September 2011 at a conference on new technologies and design. It functions just like a normal inkjet printer, but instead of ink, it uses human and animal stem cells.
A 3D printer is capable of printing pieces of tissue, skin, spinal discs, knee cartilage, and complete organs. Before printing, the patient's organ is scanned from different angles and the information obtained is loaded into a three-dimensional printer, along with a tissue sample of the organ. For several hours of operation, the device recreates an exact copy of the organ, including blood vessels.
The scientists also recreated the heart of a rat, which worked successfully after being implanted in an experimental animal.
This unique device can heal wounds directly on the patient, as well as eliminate mechanical damage to organs resulting from gunshot and stab wounds, accidents, etc. To do this, he scans the wound (organ) and fills it with the appropriate type of freshly grown tissue.
In 2011, scientists from the UK were the first to show a 3D printer that could print any chocolate figurine or a simple chocolate bar. The printer stacks layers on top of each other. Due to the ability of chocolate to quickly solidify and harden when cooled, the printing process is quite fast.
2011 is the year of the creation of the first 3D printed aircraft. This idea belonged to engineers from the University of Southampton (UK). They said that it was not difficult in the printing process, but in the design stage. The 3D aircraft model flew perfectly at a relatively high speed.
Previously, 3D printers were bulky and very expensive, but in 2011, researchers from the Vienna University of Technology introduced the smallest, lightest, and cheapest 3D printer in terms of printing costs. The new model uses additive photopolymerization technology for photosensitive resin, weighs 1.5 kilograms and costs about 1,200 euros.
In 2012, printers for home use appeared, such a 3D printer prints using FDM technology. In 2014, a printer for simultaneous printing of several colors and materials appeared. In the same year, many corporations showed interest in 3D printing.
3D printers can safely be called the most necessary and useful devices of our present and future. Technologies for creating 3D models are widely used in various fields. For example, small 3D printers can create all sorts of little things needed in everyday life: toys, dishes, furniture and decorations.
Scientists from the University of Oxford proposed a printer capable of producing synthetic materials, as well as materials with some properties of living tissues. Italian roboticist Enrico Dini has created a D-Shape printer that can print the layout of a two-story building, including rooms, stairs, pipes and partitions. It uses only sand and an inorganic compound. Scientists compare the strength of the resulting material with reinforced concrete.
Now the number of materials that are used for 3D printing has exceeded one hundred. Materials that can be used today include acrylic, concrete, hydrogel, paper, gypsum, wood fiber, ice, metal powder, nylon, polycaprolactone, polylactide, polypropylene, low-density polyethylene, and chocolate.
Now they print cakes, and entire houses, and even models of supernovae, created as a result of mathematical modeling. Today, the global market for such products is more than $3 billion, and according to forecasts for 2020, this figure will reach $12 billion.
It is too early to talk about the maturity of the market, but the fact that the largest aircraft engine manufacturer Rolls-Royce is already printing turbine blades, trusting people's lives with new technology, speaks for itself. Such giants do not take up 3D printing out of mere curiosity. It's a matter of costs. If you need to create a prototype, show it to someone, make something that, according to the results of tests, will have to be finalized, there is no better way than to print a model on a 3D printer. Much less time and money is wasted. Moreover, both directly and indirectly: the material costs in the traditional approach, expressed in the amount of waste, in some industries reach enormous values. In the aircraft industry, for example, there is even such an indicator as the percentage of raw materials that eventually find their embodiment in an aircraft.
The advantages that have spawned hundreds of start-ups creating real things in various industries are the speed of prototyping, low overhead, the availability of a variety of 3D printers, coupled with a decrease in cost and an expansion of the range of microelectronic base.
But it's not just about simplicity and cheapness. Returning to aircraft engines, today these are the most complex products from an engineering point of view, which experience colossal and repeated loads. Previously, the process of creating some parts had to be divided into several stages, since the traditional method of production simply did not allow creating objects of such complex shapes in one go. Now, with the use of 3D printing, this has become possible. And, importantly, the creation of such products is an excellent illustration of the modern approach to production, when most of the operations, from the creation of a drawing to the operation of the product, are controlled by a computer. After all, before starting printing, the object is designed and processed on a computer, converted into a special format understandable for the printer, and after that it is sent, again in digital form, for printing.
The reverse process, also associated with computer processing, is also possible: when a real object is digitized using a 3D scanner, converted into a drawing format and reproduced on a three-dimensional printer in an unchanged or corrected form. Another property of additive technologies is connected with this: the ability to quickly adjust the finished product or create a new one from scratch, depending on the specific needs of the client. The same printing of internal organs or parts of the skeleton without taking into account the characteristics of a particular patient is impossible.
Additive technologies also have their drawbacks. The main criticism focuses around the low speed of creating products and their quality. For 20 years, the speed of 3D printing has increased significantly. And it will continue to grow: manufacturers are increasingly using multiple printheads, which not only speeds up the process, but also allows you to use different colors and even materials in one pass.
The quality is also not as bad as many claim. Models obtained using inexpensive printers intended for home use come out rough, the details are lame, but, on the one hand, the resolution of devices is growing, and on the other, submicron resolution is not always needed even in industrial production.