Fanuc 3d printer
FANUC TO DEMONSTRATE A WIDE RANGE OF CNC AND ROBOTIC SOLUTIONS AT FABTECH
FANUC will showcase our latest automation solutions to help drive the future of manufacturing at FABTECH 2021 in Chicago, Ill.
ROCHESTER HILLS, MI – (Sept. 2, 2021) – FANUC America, the leading supplier of CNCs, robotics, and ROBOMACHINEs will showcase our latest automation solutions to help drive the future of manufacturing at FABTECH 2021 in Chicago, Ill. See us in booth #B23022 in the North Hall, and booth #D45535 in the East Hall’s painting pavilion.
Factory Automation Demonstrations
FANUC’s Factory Automation division will demonstrate Visual Twin and Additive Manufacturing at FABTECH. The Visual Twin demonstration offers an exciting new way to see part production while highlighting FANUC’s end-to-end digitalization solutions for the machine shop. FANUC’s Visual Twin is an exact software replica of real CNC machine tools. The Visual Twin will display a virtualized 5-axis machine tool cutting a part, which mirrors the real-world machine’s behavior.
Additive Manufacturing, otherwise known as 3D printing, has been gaining popularity in industrial manufacturing to create prototypes, tooling and end-use production parts. Applications, including medical implants and aerospace parts, are growing as new hybrid machine tools combine additive manufacturing with CNC machining. The new demo highlights FANUC’s capabilities in this burgeoning market by incorporating a 3-axis machine equipped with a four-extruder head into a plastic 3D printer. FANUC 30i-B CNC equipped with the 21.5” Panel i H Pro will be featured on the machine to demonstrate its custom slicing and post-processing capabilities.
Robotic Demonstrations
Adaptive Arc Welding: A collaborative robot system will demonstrate how to help welding customers address gap conditions. First, an operator loads coupons and sets variable gaps of 0-1.5mm between the work pieces. Next, a CR-15iA collaborative robot uses FANUC’s Seam Tracking software with SERVO ROBOT’s FUJI-CAM 2. 0 sensor to communicate the gap conditions to the robot, which then performs adaptive welding. The adaptive process has the ability to change weaving amplitude, weave frequency, travel speed, wire feed speed, trim, as well as positional bias in X,Y,Z directions.
The demonstration also features the Lincoln Electric Power Wave® R450 robotic power source with the Advanced Module using the GMAW Pulse process.
CRX Collaborative Arc Welding Robot:
FANUC’s CRX collaborative arc welding robot offers the same high level of performance that FANUC ARC Mate robots are known for including the latest technologies and world-renowned reliability. Built-in sensors on each axis can allow the CRX welding cobot to work safely alongside people without the need for expensive guarding. In addition, the CRX can operate for eight years maintenance-free, which is a major advantage for companies looking to lower costs and increase productivity.
The CRX is extremely easy to use – even for those who have never used a robot. Interactive programming allows operators to teach weld joints using hand guidance or a new tablet interface with drag and drop icons. The CRX welding cobot supports several of FANUC’s advanced features including iRVision, Torch Angle Control, Touch Sensing and Thru Arc Seam Tracking (TAST). The CRX is shown with Lincoln Electric’s Power Wave® R450 robotic power source, and the new Lincoln Electric Smart Torch. FANUC’s CRX welding cobot demonstration will allow visitors to try its easy hand guidance and tablet programming features.
In addition, Lincoln Electric’s Fab-Pack® Cobot Guru™ featuring FANUC’s CRX will offer attendees a hands-on experience of this new collaborative robot welding solution.
The Fab-Pak Cobot Guru robotic welding system includes simplified programming with the new CRX tablet-based teach pendant, and the ability to teach at the torch by hand. Built for the industrial space, the Fab-Pak Cobot Guru system is compatible with all of Lincoln Electric’s weld programs to help customers maximize productivity.
Painting:
FANUC America has designed and built its painting robots at the company’s Rochester Hills, Mich., headquarters for nearly 40 years. The FANUC P-40iA is the latest in the paint robot series. Ideal for a variety of painting and coating applications, the six-axis P-40iA offers the same reliability and proven technology as all FANUC products.
At Fabtech, a P-40iA paint robot equipped with the R-30iB Plus Mate controller will demonstrate painting metal parts using coordinated motion to reach all surfaces of the parts. Visitors will also have the opportunity to try out the new “Easy Teach” hand-guidance programming feature.
In addition to being easy to use, the P-40iA robot is extremely flexible to accommodate small lot sizes, new styles and other modifications, providing customers an affordable and versatile solution. Slim and lightweight, the P-40iA robot offers a variety of mounting positions, which helps companies challenged with small and narrow workspaces.
Spotwelding:
The R-2000iD/210FH spot welding robot is the latest model in a large family of industrial robots offering a variety of payloads and reaches. The robot offers a compact design with a hollow arm for better cable management, which minimizes interference with system equipment and allows the robot to operate in tight workspaces. Featuring a 210kg payload and 2605mm reach, the R-2000iD/210FH is ideal for spot welding and material handling applications.
At the show, the R-2000iD/210FH robot equipped with integrated FANUC Servo Gun Control and a hollow arm for spot welding dress out will perform simulated spot welding in and around a truck cab. The robot will use Dual Check Safety (DCS) Speed and Position Check software to limit the robot’s envelope within the compact workspace. Also featured will be FANUC’s latest R-30iB Plus controller with an intuitive iPendant for easy setup and operation.
FANUC will participate in two technology sessions including:
F34: Laser Ecosystems for Fiber Laser Cutting & Surface Cleaning on Tuesday, September 14, 8:00 -9:30 AM. Michael Sharpe, Laser Business Development Manager to present: Laser Ecosystem - Dynamics Through Full Digital Control.
F202: Automation for Metal & Finishing Processes on Wednesday, September 15, 3:30 - 5:00 PM. Barton Faylor, Senior Industry Marketing/Program Manager to present: CAD to Path Robot Programming. Is it Myth or Reality?
For more information on FANUC’s presence at FABTECH, visit www.fanucamerica.com/fabtech.
About FANUC America Corporation
FANUC America Corporation is a subsidiary of FANUC CORPORATION in Japan, and provides industry-leading CNC systems, robotics and factory automation. FANUC’s innovative technologies and proven expertise help manufacturers in the Americas maximize productivity, reliability and profitability.
FANUC embraces a culture of “Service First” which means that customer service is our highest priority. We are committed to supplying our customers with parts and support for the life of their FANUC products.
FANUC America is headquartered at 3900 W. Hamlin Road, Rochester Hills, MI 48309, and has facilities in: Auburn Hills, MI; Atlanta; Boston; Charlotte; Chicago; Cincinnati; Houston; Huntington Beach, CA; Los Angeles; Minneapolis; Montreal; Pine Brook, NJ; Pontiac, MI; Birmingham, AL; San Francisco; Seattle; Toronto; Buenos Aires, Argentina; Sao Paulo, and Manaus, Brazil; and Aguascalientes, Monterrey, and Queretaro, Mexico. For more information, please call: 888-FANUC-US (888-326-8287) or visit our website: www.fanucamerica.com . Also, connect with us on YouTube, Twitter, Facebook, LinkedIn and Instagram.
FANUC America Corporation PR contact:
Robotics: Cathy Powell
Public Relations and Communications Manager
FANUC America Corporation
T: 248-377-7570
E: [email protected]
Factory Automation: Debra Schug
CNC Strategic Communications Specialist
T: 847.898.5673
E: [email protected]
###
Fanuc
FANUC offers the widest range of industrial robots in the world. Covering a diverse range of applications and industries, FANUC robots are easy to operate and provide complete flexibility thanks to a range of application-specific options, straightforward integration, payloads up to 2.3 t and maximum reaches up to 4.7 m.
Is this the right solution for you? Speak with us today!
Are you interested in using robots with 3D scanning or machine vision?
R-2000iC/165F
R-2000
The R-2000 series is the most successful FANUC robot in the world. Featuring high performance capabilities and payload capacities ranging from 100 to 270 kg, it makes the perfect solution for multiple applications involving high payloads. Compact and high speed with a slim wrist and arm, the R-2000 is an all-rounder that is designed for all material handling applications and spot welding.
REACH
2655 mm / 104.5 in
PAYLOAD
165 kg / 363.7 lbs
FOOTPRINT
711x610 mm
WEIGHT
1090 kg
Recommended robotic platforms:LR Mate
Available with different reaches and wrist speeds, this human-arm sized robot is your best compact solution for fast handling and processing parts up to 7 kg across a whole range of industries including food or metal. Featuring optional integrated intelligent (vision & force) functionality for even higher levels of accuracy and productivity, LR Mate handling robots also come with special equipment for welding, painting, clean room.
REACH
717 mm / 28.2 ins
PAYLOAD
7 kg / 15.4 lbs
FOOTPRINT
Ø 190 mm
WEIGHT
25 kg / 55 lbs
LR Mate 200iD
Recommended robotic platforms:CR-14iA/L
CR Series
By integrating them into existing production environments, robots directly collaborate with humans, becoming a crucial part of the team. Alongside humans, they take over tedious, repetitive tasks, lifting up to 35 kg, thus maintaining the human’s health while automating entire assembly lines.
REACH
911 mm / 35.8 ins
PAYLOAD
14 kg / 30. 8 lbs
FOOTPRINT
296.5x235 mm
WEIGHT
55 kg / 121 lbs
Recommended robotic platforms:CRX Series
FANUC's latest collaborative robot designed to make installation and programming your cobots easier than ever before. By integrating them into existing production environments, robots directly collaborate with humans, becoming a crucial part of the team.
REACH
1249 mm / 49.1 ins
PAYLOAD
10 kg / 22 lbs
CRX-10iA
Recommended robotic platforms:Driven by Streamline
Metrology Automation Software
3D Infotech’s Streamline process control software is the soul of Universal Metrology Automation®. It allows you to easily set up new automated inspection jobs with a variety of robot and scanner brands.
A touchscreen user interface provides a friendly solution that is secure and permission-based.
Driven by Streamline
Metrology Automation Software
3D Infotech’s Streamline process control software is the soul of Universal Metrology Automation®. It allows you to easily set up new automated inspection jobs with a variety of robot and scanner brands.
A touchscreen user interface provides a friendly solution that is secure and permission-based.
Processes
Castings & Forgings
Injection Molding
CNC Machining
Metal Die & Stamping
Sheet Metal Forming
Additive 3D Printing
Composite Lay-up
Contact our metrology experts, they will be glad to help you find the best solution for your industry
which is better for prototyping?
3D printing and CNC machining are more popular and affordable than ever. When you want to make a prototype, you decide what is best to use.
In this article, I will show you the strengths and weaknesses of each technology to help you make a decision.
Difference between 3D printing and CNC machining
The difference between 3D printing and CNC machining is that 3D printing is additive manufacturing while CNC is subtractive manufacturing. 3D printers have a nozzle that feeds layers of material to make parts, while CNC machining consists of a cutting tool that removes material to make parts.
CNC machines allow you to change the cutting tool according to the complexity of the application. As a result, CNC machines can be used to produce relatively more detailed products with high precision.
On the other hand, 3D printers are capable of creating complex shapes, making them ideal for rapid prototyping applications.
But is a 3D printer a CNC machine? Short answer: yes, it is a type of CNC machine that consists of a computer-controlled nozzle to print material.
However, 3D printing involves heating the working element, followed by cooling and solidification. This increases the total processing time required to manufacture the object.
In addition, there are many other differences that distinguish a 3D printer from a CNC machine.
Workflow
Looking at CNC machines and 3D printers from a technical point of view, both of these machines are controlled by a computer.
Interestingly, 3D printers belong to the CNC additive manufacturing industry.
3D printers are a type of CNC machines.The CNC motion control system is responsible for moving the cutting head over the material.
In 3D printers, the cutting head has been replaced by a print head that applies material and a controller controls its movement to print the desired shape or object.
Like any other CNC machine, 3D printers also have a similar workflow. Differences arise in the production process.
A typical workflow for CNC machines and 3D printers includes:
- Design part model in CAD software,
- Create toolpath for CAD design using CAM software
- Check program file for errors with simulation software
- Correct design or toolpath errors.
- Machining or printing a part.
CNC machines use CAD/CAM software to create designs and G-code files that are programmed into the machine for production.
Most 3D printing applications only require a 3D part design file to print. He then uses the CAM software to create a part program from the design.
The software used with 3D printers is similar to the CAM software used on CNC machines. They generate a G-code file used by CNC controllers.
Material Waste
CNC Metal MillingMaterial wastage in 3D printing is lower than in CNC machining. The main reason is that 3D printers only use the required material to create a part.
Because CNC machines use subtractive manufacturing techniques, they continuously cut out a block of material to give it the desired shape, resulting in a lot of material wastage.
Size and assembly
Compared to 3D printers, CNC machines are readily available in larger sizes. Making 3D printers more portable than CNC machines.
Most XXL rated CNCs have a footprint of a few square meters, while large 3D printers can have a maximum footprint of 1 square meter.
For example, some of the giant 3D printing machines have a build volume close to 1500×1200mm. While most industrial grade CNCs can have a working area of 3500 X 10,000 mm or more.
Since the CNC removes material from the workpiece by force, it must have a rigid construction strong enough to withstand high cutting forces.
The rigid frame is one of the most important parts of a CNC machine. This is the frame that holds all the other components together. It also acts as a guide for the cutting tool and provides a precise path for the tool.
On the other hand, 3D printers use the material in a molten or powder form, which eliminates the need for a rigid structure to apply high forces during the printing process.
Additions
CNC Coolant During machining, these machines use certain additives to provide a suitable processing environment for the tool and material.
For example, the CNC uses cutting fluids to lubricate and cool the material-to-tool contact point. Sometimes they also require dust collectors to keep their working environment clean.
In the case of 3D printers, they use a heated platform to help adhere the object to the print surface.
Tools
VMC threadingCNCs are versatile machines that allow you to change cutting tools to perform different types of cuts with different sizes and finishes.
3D printers lack this flexibility, and the printed object has the same resolution with a constant layer thickness throughout the print.
Accuracy and reproducibility
CNC machines can achieve higher precision than 3D printers because of the way they work.
The rigid frame of the CNC machine provides high repeatability with minimal vibration, making it suitable for high volume production where multiple items with the same dimensional accuracy are required.
On the other hand, 3D printers melt and print material layer by layer, resulting in printed parts subject to slight dimensional inaccuracies.
Surface quality
3D printed plastic part (left) and CNC plastic part (right)In terms of surface quality, CNC is better than 3D printed. This is due to the wide range of tools used by the CNC.
With various tools such as ball end mill, end mill, grinding belt, etc., the CNC can produce workpieces with high surface quality.
The layering process of 3D printers leaves behind a rough surface texture on the workpiece.
Today, 3D printed parts are treated with surface finishing methods such as painting, powder coating, electroplating, etc. to obtain a smooth surface.
Part strength and stability
Compared to 3D printing, CNC machining allows parts to be produced with tighter tolerances and greater strength.
CNC machines have a tolerance of ±0.025mm, while advanced 3D printing techniques such as direct metal laser sintering (DMLS) can only achieve a tolerance of around ±0.1mm.
In addition, because the CNC uses subtractive manufacturing techniques to make the part from a block of material, it does not lose the original strength of the material.
The 3D printer adds layers of material on top of each other that are fused together to form the final product. This reduces the overall strength of the part, making it prone to breakage.
The minimum line thickness that a modern 3D printer can achieve is 0.4 mm.
Costs
CNC machines are comparatively more expensive than a 3D printer with the same working area.
In addition, the need for various accessories such as coolant supply system, special cutting tools, etc., further increases the maintenance cost of CNC machines.
For small prototyping businesses, a 3D printer is a cost-effective option because it allows prototyping without the need for expensive equipment.
CNC and 3D printing - basics
Additive and subtractive manufacturing
Additive Manufacturing Additive manufacturing is a technique that involves adding material layer by layer to produce a desired part or object. For example, 3D printers work on this principle.
This method is used for rapid prototyping of parts, production of complex parts and creation of customized products.
Subtractive ManufacturingThe subtractive manufacturing process removes material layer by layer from a blank block to create an object.
This is done with cutting tools and machines such as lathes, milling machines.
What is a CNC machine?
Various types of CNC machinesA CNC machine is a computer-controlled tool that can be used for various processing operations such as cutting, shaping and shaping various materials.
These machines usually have three axes of motion and can produce complex shapes from materials such as metal, wood, plastic, etc.
CNC technology has been used in manufacturing for decades. This allows machines to be programmed to perform complex operations automatically.
It is now an integral part of the production process in many industries and can be found in various types of machines.
Some of the common CNC machines include CNC milling machines, CNC lathes, laser cutters, plasma cutters, EDM machines, grinders, etc.
What is a 3D printer?
Vase 3D Printing with Snapmaker 2.03D printer is a type of automated machine that follows the principle of additive manufacturing and uses numerical control technology to produce the desired part from a CAD file.
These machines create 3D objects by laying down successive layers of material on a build plate until the object is complete.
The most common type of 3D printer is Fused Deposition Modeling (FDM) printers, which work by extruding thin filaments of heated plastic, metal, or other materials that cool and solidify after being deposited.
Practical application of 3D printing and CNC machining
Practical application of 3D printing and CNC machining depends on the material you plan to work with, the type of part you want to produce, the quantity and speed at which you want to make them.
The type of material you plan to use
The materials most commonly used for 3D printing are plastics, metals, and some biomaterials such as sugar or wood pulp.
3D printers can also use other materials such as ceramics and concrete, but these materials are less common because they take more time and effort to produce than plastics or metals.
By comparison, CNC machines can cut and mill almost any material. Some popular CNC machining materials are metals, wood, and plastics.
The materials that a CNC machine can cut depend on the design of the machine and the type of cutting tool installed in its cutting head.
Which is better for making metal parts?
CNC milling machine processes a metal workpiece. TheCNC machine is best for making metal parts because its rigid structure and transmission provide higher precision and accuracy than a 3D printer.
In addition, it allows the production of metal parts with higher tolerances compared to 3D printers.
What about plastic?
Both 3D printing and CNC machining are equally good for making plastic parts. The best option depends on the amount of detail you plan to make.
How many parts do you plan to make?
CNCs are better suited for machining large quantities of parts because they have higher repeatability.
If you are using a 3D printing technique to produce similar parts, it may be more expensive than CNC machining.
This is because 3D printers take more time and effort to complete a job, while CNC machines can produce many parts at once or in cycles with little effort.
3D printing is ideal for prototyping when fewer parts need to be produced (less than 10), whereas if you want to produce more parts, it is better to consider using a CNC machine.
For larger objects, consider CNC machining methods such as casting or injection molding as they are cost effective when producing parts in large quantities.
Which is better for prototyping?
While both 3D printers and CNC machines can produce custom parts or prototypes, 3D printers are much more efficient because they allow you to make multiple changes at a lower cost.
Therefore, various industries such as engineering, architecture, design and medicine use 3D printers for prototyping.
Will 3D printing replace CNC machines?
In a short period of existence, 3D printers have been able to partially replace the CNC used in the fields of medicine, architecture, product design, etc.
With its controlled deposition printing technology and the ability to create complex shapes, 3D printers are now increasingly being used to create architectural models and real structures.
Medical prostheses such as dental implants, orthopedics, etc. are now using 3D printers to produce various parts like never before.
These manufacturing shifts seen in these industries are a prime example of how 3D printers could replace CNC in the near future.
While 3D printers can replace CNC in many areas, they still cannot replace CNC when it comes to producing parts with high precision and tight tolerances.
In addition, the wide range of materials that the CNC can work with is a huge advantage of the CNC over 3D printers.
In short, CNC is here to stay. Although they have lost their importance in some industries, they are the most commonly used machines in the manufacturing industry.
It is difficult to say whether one will completely replace the other. But in the future, they will be used together to create complex molds and prototypes.
In fact, CNC hybrid 3D printers are currently used in some industries.
Traditionally, printing and cutting were done on separate machines, but these hybrid printers or CNCs can do both tasks on the same machine.
Final thoughts - which is better?
Since the introduction of 3D printing into the manufacturing industry, it has taken over some of the work of CNC, but they could not take over all.
Much of the work is still done on CNC machines such as milling, turning, milling and grinding machines.
CNC and 3D printers are part of the puzzle. They both have their places, and both are needed to complete it.
They have different capabilities and can be used on different parts and objects for different applications.
Is CNC the same as 3D printing?
Technically yes, but functionally no. Like CNC, 3D printers are also computer controlled and work in a similar way, but CNC uses subtractive manufacturing methods while 3D printers use additive manufacturing.
Which is cheaper? CNC or 3D printing?
3D printing is cheaper than CNC because relatively less raw materials are used to create an object. 3D printers also cost less and don't require special tools or setups before production starts.
Is CNC faster than 3D printing?
In general, CNC is faster than 3D printing. This is because a CNC cutter can remove materials faster than a 3D printer can extrude and place material.
Manufacture of 3D printers in Europe. What blond birches are silent about ... / Sudo Null IT News market, with whom it is only possible (whom I did not meet - my beloved partner met), after which I decided
“That's it, let's go! We are going to 3D”Being, on the one hand, a dreamy and enthusiastic person, but on the other hand, a cynical and prudent businessman, before diving headlong into the industry, it was decided to shake the pool of 3D printer manufacturers vigorously before choosing an accent for future distribution.
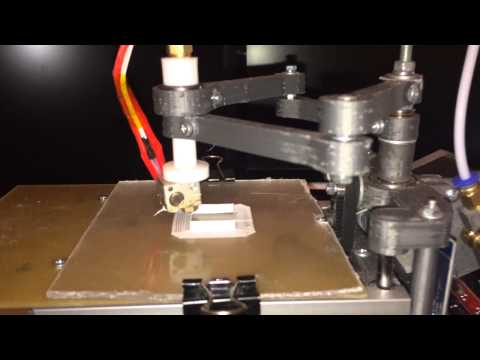
I won’t stop at this stage too much, I’ll just say one thing: they were “shaking” with uncomfortable questions, meetings, real tests, weighted price comparisons - companies from the top 10 brands that occupied the media space, the low-level segment was not considered in principle due to strictly defined competence distribution groups.
And so, in April of this year, we were thrown by a wave in the Spanish town of Navarre, where I personally saw the European level of assembly of 3D printers at factory bq , which I wanted to share with you, not forgetting the "cherry" at the end of the story.
The town where the factory of the company bq is located, producing printers Witbox , as usual for Europe (and I have been to many factories in Europe and China), is very small and expectedly romantic:
to the city - we went to the factory ourselves, the meeting was somewhat chaotic, because on the same day, more distributors from Italy and Colombia arrived at bq.
It was all the more interesting for me to see the production through the eyes of a person for whose arrival there was no time to prepare (by building the Potemkin villages according to a custom known in Russia).
What can I say, after the Chinese cold, poorly lit workshops with girls wrapping themselves in warm clothes with belongings on the desktops, the European assembly is always like oil for the soul.
It immediately catches the eye: Spaciousness and Cleanliness
We were taken step by step through the entire production, allowing us to take photos of a general plan without zooming in.
Below are the most interesting of them, in my humble opinion, with a few comments:
At the first stage in production, tables with guides are assembled, fixed inside the platform, and then the control electronics are fixed.
Under each printer there is CHECK list , in which the assemblers mark the operations performed, and the intermediate testers check the health or absence of it at a certain stage (these are white sheets inside each Witbox printer in the photo):
External electronics - installed by blue collar guys on this line. they also test this electronics:
In the next room we found FANUC Robodrill - in fact a large 3D printer, but in a non-additive manufacturing format.
Seeing it, the engineer of our company, who came to study, trembled and began to excitedly whisper in my ear that “this thing is worth more than anything that is here,” which made me worry for no apparent reason.
Our question: "What is it used for?" was shown to us on a stack of these spare parts stacked side by side.
This is a snap-box for the electronic filling of the printer, the Spaniards in bq grind it on their own:
Then followed the phrase that made me think:
“We used to print these boards on our own Witbox 3D printers, but with an increase in production it became absolutely unjustified in terms of time costs”
Guys from Russia, manufacturers of 3D printers, often boasted to me that many of the spare parts for their "gadgets" are produced on their own printers.
It can be concluded that the number of units produced is hardly large in these specific cases and can indirectly indicate a small amount of accumulated production experience.
Next to FANUC is the Laser Cutting Plotter , which makes the outer bright panels for the future printer.
Maybe I called it wrong, but for me, an office rat, such large machines, before my eyes turning huge sheets into beautifully shaped, ready-to-install external panels with a logo on board, always make a fascinating impression.
Even before the panels are installed, each printer starts to print a calibration pattern (below you will see a number of these print Witboxes).
If the test is successful, the printer goes to packaging. At the same time, the model printed on this particular printer MUST be put into the box.
Doesn't pass the test - they make an additional adjustment to the victorious one.
Here I trembled again and for a long time fascinated looked at the bluish backlight of the print area, appreciating with peripheral vision an elegant solution for laying PLA plastic without the flip over the top, which is standard for most devices of this kind:
Printers that have passed the print test are equipped with external panels (yellow, black or white):
to play around” to our engineer, who became very close to like-minded Spanish engineers during the short time of our visit):
I liked EVERYTHING on the final packaging.
1. Double box - beautiful inner and outer shipping:
The guys from bq said that the printer in this package can withstand a fall from a height of 1 meter:
- Reel PLA - plastic (two for Witbox printer with two extruders)
— 4GB SD - card
— Additional HOT END — extruder nozzle (I almost burst into tears when I saw it, and girlishly framed the photo as a sign of sincere gratitude for such attention to customers):
- Instructions and warranty card for 2 years operation
despatch to Madrid, main warehouse bq
after the mandatory palletization procedure:
In the morning - this (printed on a Witbox 3D printer, as evidenced by the inscription on the board) forklift
… will load them onto a truck bound for sunny Madrid, so that the “swallows” will then fly around the world…
Coda. Curtain.
Cherry
(which was promised above):
Why is the post itself placed in the hub Open Source ?
At the end of our trip we asked the Europeans:
Why are you, an absolutely successful IT company, second in the market in Spain in sales of smartphones and tablets, investing money in the production of 3D printers?
Why are you so actively sharing information with us, investing your time, effort and money, including in the Russian market?
Are you not afraid that the #Chinese will come and eat you? Aren't you afraid that manufacturers in Russia will be able to knock out all Europeans and Americans from the 3D printer market?
Are you confident in the long term of your strategy?
The answer of Mario and Antonio from bq threw me into complete confusion:
We are NOT afraid of the Chinese.![]()
Learn more