Evolution 3d printer
Careers – Evolve Additive Solutions
Evolve Additive Solutions is leading the way in the smart manufacturing revolution with a mission to produce innovative manufacturing solutions that enable our customers to manufacture in revolutionary new ways. Our commitment to innovation is what drives our employees to reach new heights in their careers. Your work matters here. That is why we are looking for the best new talent in our industry.
Director of Global Operations – Minnetonka, MN
At Evolve, the Director of Global Operations is a high-visibility role and is responsible for leading all aspects of the company’s manufacturing, operations, and customer service activities. The position will report directly to Chief Operating Officer and will be a key participant in all elements of our strategy and success. This individual will develop and implement strategic and tactical operational elements that align the company to enable new business growth while improving existing operational effectiveness. Focus areas include meeting business plan requirements and improving operational effectiveness, especially in planning for future growth, reducing the cost of goods sold, improving product quality and efficiency, finding, and securing strategic suppliers and partners, managing facilities on multiple sites, and meeting all established regulatory compliance & safety requirements.
Responsibilities
- Create and deploy an Operations Long-term vision to support necessary business objectives.
- Define and implement overall operations, manufacturing, and customer service strategy, structure, and processes.
- Manage the quarterly and annual budgeting process and P&L responsibilities for the Operations Department.
- Manage the ongoing S&OP process to ensure supply continuity in machines and materials.
- Monitor performance to proactively identify efficiency issues and propose solutions.
- Define architectures and roadmaps, manufacturing strategies, department schedules, budgets, business processes, and KPIs, and supervise corrective and preventive action.
- Maintain a working knowledge of all phases of operations.
- Supervises and leads the Operations Team.
- Interview, hire, train, and mentor the operations team. Acquire necessary resources to meet scheduled commitments.
- Motivate staff and provide technical direction and guidance and hands-on project management, recognizing the role as that of both manager and support resource/mentor – Act as a Player/Coach.
- Assure that the department achieves objectives and project completion within budget and time frame.
- Establishes and grows Operations best practices
- Be a student of current industry trends, ensuring the company maintains and expands its technology leadership position.
- Select, contract, and manage suppliers and own quality, cost, and lead-time of purchased material.
- Establish and maintain an effective Supply Chain management Strategy and Process.
- Establish and maintain an effective change order process.
- Leads day-to-day Operation’s functions
- Manage inventory, assembly, logistics, and facility operations.
- Manage health, safety, and environment.
- Select and implement ERP core operations solutions
- Select, contract, and manage service providers.
- Plan, justify, and execute capital projects.
- Perform assembly, testing, and facility improvement and maintenance tasks
- Provides Critical cross-functional Support
- Support Sales by providing lead time guidance and on-time delivery of hardware, materials, and ongoing service and support.
Support the order to cash system by contributing to the IT and ERP infrastructure.
- Support product and technology development activities by providing key insights, defining requirements, and providing resources.
Minimum Qualifications
- Possesses a BS or equivalent academic grounding.
- At least 10 – 15 years’ experience leading manufacturing of capital equipment.
- At least 5-years’ experience outsourcing and managing suppliers of electromechanical assemblies.
- At least 5-years’ experience supervising teams.
- Must possess experience justifying and implementing capital projects greater than $250K.
- Must possess advanced skills in contracts, lean manufacturing, and structured problem-solving frameworks such as Six Sigma or 8D.
- Demonstrated capability to excel in a pre-revenue, startup culture and is comfortable operating both at a strategic level as well as an individual contributor level.
Possesses familiarity with:
- Scaling and transitioning an operations organization from start-up to commercialization.
- Best practices Supply Chain Management in a Capital Equipment environment.
- Engineering change order process and control.
- International transport and logistics.
- Phase-gate Product Development and Introduction processes.
- UL, CSA, CE, and other product-safety certifications.
- Is authorized to work in the United States and without travel restrictions.
APPLICATION INSTRUCTIONS
Interested candidates should send their resume along with a cover to [email protected].
Electrostatic Process Scientist – Rochester, NY
The Electrostatic Scientist will be accountable for modeling the behavior of charged particles within the electrophotographic process to deliver micronized engineering plastics to the bonding process. The candidate will lead the understanding of the electrical behavior of the materials within the electrostatographic imaging and transfer process technology areas, helping to create a robust commercial design.
Responsibilities
- Lead the development and validation of models for the behavior of charged particles within the electrostatic process and with the transfer process.
- Identify electrostatic best practices and modeling software.
- Design software tools that provide guidance on electrostatic requirements and objectives for quality, speed, and economics.
- Learn key relationships between product design characteristics and controls using fundamental mathematical models, state-of-the-art metrology and analytics, and fundamental physical models.
- Identify critical-to-function parameters, including target values and ranges.
- Develop specifications for the imaging module hardware and controls design.
- Collaborate and communicate cross-functionally with technical and non-technical colleagues to ensure the goals of the Evolve team are met.
Minimum Qualifications
- Ph.D. degree in Physics or in a related field of engineering or M.S. degree with 5 years of experience.
- Mastery of electrostatics, behavior of charged particles, electricity and magnetism, or similar focus areas.
- Exposure to robust design and design of experience.
- Creative problem solving.
- Experience with MATLAB, Python, or equivalent.
- Excellent written and verbal communication.
APPLICATION INSTRUCTIONS
Interested candidates should send their resume along with a cover to [email protected].
Principal Systems Engineer - Minnetonka, MN
As Principal Systems Engineer you have a central role in ensuring all Engineering activities contribute to our success. Deriving and establishing subsystem-level requirements so the product as a whole makes our customers satisfied and profitable is your main responsibility. Your ability and drive to comprehend and integrate an exceptionally wide set of mechanical, electrical, and information-processing functions enable you to lead in developing the most stunning innovation in plastics manufacturing in decades. You enjoy working with people with varying levels of experience, and both learn and teach in every interaction, so helping unite our diverse team in surmounting tough technical and business challenges are immensely rewarding for you.
Responsibilities
- Lead the development, adoption, and continuous improvement of Systems Engineering methods and tools, and coach stakeholders in their use.
- Define and own system hierarchy, system and subsystem specifications, and ensure systems meet business and customer requirements.
- Collaborate with Product Management to define product specifications and requirements.
- Identify and resolve system-level functional problems and improvement opportunities.
- Draw on sophisticated physics and materials knowledge and hands-on electrical, mechanical, and software skills to gain insights and contribute to hardware, software, materials, and process innovations.
- Provide engineering support and issue resolution to customers and suppliers.
- Contribute to the continuous improvement of Engineering standards and practices.
- As an Engineering Core Team member, define product architectures and roadmaps, supply-chain strategies, department schedules, budgets, business processes, and KPIs, and supervise corrective and preventive action.
Minimum Qualifications
- MS in a STEM field
- Authorized to work in the United States and without travel restrictions
- Ten years of Engineering experience
- Three years of experience in a leadership role developing complex machinery incorporating electronic controls and multiple types of sensors
- Formal training and practical experience in the application of Product Systems Engineering methods such as system block diagramming, requirements management including QFD or similar, system modeling for performance and reliability estimation, FMECA, and validation test planning
- Practical experience leading system testing, analyzing results and presenting conclusions and recommendations
- Broad familiarity with mechanical and electrical tools
- Strong assembly and troubleshooting skills
- Ability to produce reliable results without supervision in statistical data analysis using Minitab or similar tools
- Successful experience using Design of Experiments
- Experience with the development of equipment test standards, test processes and acceptance criteria for intra-tool and inter-tool testing, driving system correlation and results matching
- Strong report writing and presentation skills
- Broad familiarity with typical manufacturing processes and materials
- Some participation in:
- Research and selection of specialized fabrication processes
- Application of structured problem-solving frameworks such as Six Sigma or 8D
- Laboratory and chemical-handling safety
APPLICATION INSTRUCTIONS
Interested candidates should send their resume along with a cover to HR@evolveadditive. com.
Electrical Engineering Manager - Minnetonka, MN
The Electrical Engineering Manager will be responsible for the development and continuous improvement of all electrical aspects of Evolve’s world-leading industrial additive manufacturing systems and associated equipment. You will also participate in brainstorms, and collaborate with Mechanical, Software and Systems Engineering to define requirements and specifications for products and subsystems.
Responsibilities
- Recruit and supervise Electrical Engineering resources -- developing their professional competence and maximizing their business contribution.
- Establish and continuously improve Electrical Engineering standards and practices.
- Select, implement, and support Electrical Engineering tools and infrastructure.
- Select, contract, and manage engineering services providers and other technical suppliers.
- Design control system architectures, develop sensing and control subsystems, design power distribution, networking, noise mitigation, and safety solutions. Specify components, design PCBs and panels, and perform research and analysis.
- Perform assembly, testing, and facility improvement and maintenance tasks.
- As an Engineering and Operations Core Team member, define product architectures and roadmaps, supply-chain strategies, department schedules, budgets, business processes, and KPI's, and supervise corrective and preventive action.
Minimum Qualifications
- BS in Electrical Engineering or equivalent academic grounding
- Authorized to work in the United States and without travel restrictions
- Three years’ experience leading teams in the development of products incorporating high-speed data communication, and precision motion and process control, with substantial innovation accomplishments
- Five years’ experience in an Electrical Engineering role in an ISO-certified manufacturing organization, with substantial accomplishments in business process improvement
- Advanced skills in hardware selection and development for motion and process control, HMI, and device communication, including experience with FPGAs and embedded controllers, including cabinet and PCB layout and detail design
- Familiarity with source-control and ECAD tools, database applications, and ERP systems
- Familiarity with UL, CSA, CE, NEC, and NFPA certification requirements
- Broad familiarity with sensor technologies, and some participation in research and selection or development of specialized sensor technology
- Familiarity with typical electrical test and data acquisition equipment and software
- Some participation in the application of statistical methods and tools for manufacturing or testing
- Some participation in the application of structured problem-solving frameworks such as Six Sigma or 8D
APPLICATION INSTRUCTIONS
Interested candidates should send their resume along with a cover to HR@evolveadditive. com.
Office Manager – Minnetonka, MN
The Office Manager supports Evolve with administrative tasks and ensures smooth day-to-day operations of a fast-paced office. Based on a progressive approach to administrative support, this role requires a skill set that includes a high level of comfort with technology, excellent verbal and written communication skills, a passion for customer service, and the ability to problem-solve and excel in a self-directed environment.
Responsibilities
- Operate office machines, such as photocopiers and scanners, voice mail systems, and personal computers.
- Answer telephones, direct calls, take messages, greet visitors, and manage sign-in NDA or Tour forms.
- Communicate with employees and other stakeholders to answer questions, disseminate or explain information, and address complaints.
- Organize and coordinate various events, including employee appreciation, customer visits, and leadership meetings.
- Maintain and update filing, inventory, mailing, and database systems.
- Compile, copy, sort, and file records of office activities, business transactions, and other activities.
- Review files, records, and other documents to obtain information to respond to requests.
- Open, sort, and route incoming mail and prepare outgoing mail.
- Inventory and order materials, supplies, and services.
- Deliver messages and run errands.
- Process and prepare documents, such as business, government, and expense forms.
- Train other staff members to perform work activities use computer applications.
- Occasionally make travel arrangements for office personnel.
- Setup up computers, IT, keycard badge, phone list, email groups, text group, travel account, etc.
- Provide other administrative support as necessary, including scheduling staff meetings, board meetings, etc.
- Troubleshoot problems involving office equipment, such as computer hardware and software.
- Oversee and support all administrative duties in the office and ensure that office is operating smoothly.
- Assist with office layout and office moves.
- Maintain calendars for the CEO and other members of leadership as needed.
- Work with vendors such as IT, Cleaners, Vending machines, Coffee vendors, Shredding, OffiCenter, etc., to ensure items are completed promptly.
- Other duties as assigned by supervisor.
Minimum Qualification
- Associate degree or equivalent experience required.
- At least two years of experience in administrative roles.
- Self-motivated and able to appropriately manage multiple projects with discernment on how to prioritize.
- Accuracy and attention to detail.
- Organizational and time management skills with the ability to master complex tasks with minimal supervision.
- Must be familiar with Microsoft Office Suite: Excel, Word, PowerPoint.
- Able to work at a high level of attentiveness to detail and accuracy.
- Excellent interpersonal and communication skills, including the ability to work with a wide variety of individuals.
APPLICATION INSTRUCTIONS
Interested candidates should send their resume along with a cover letter to [email protected].
R&D Additive Manufacturing Engineer – Minnetonka, MN
The STEP R&D Additive Manufacturing Engineer will be accountable for optimizing the process for use within the Selective Thermoplastic Electrophotographic Process (STEP) system.
Responsibilities
- Operate and maintain complex additive printing equipment and execution of tests and experiments on this equipment.
- Develop robust troubleshooting procedures to ensure the operation of additive printing equipment in internal and external locations.
- Characterization of the electrophotographic performance of STEP materials.
- Analysis of the mechanical properties of test parts generated by the STEP process.
- Design and execution of test procedures to investigate and develop the imaging process necessary to meet the objectives for build accuracy and build rate.
- Determine the interplay between material parameters and the build process that are critical for accurate, strong, and attractive parts.
- Use analytical and statistical tools to identify of critical-to-quality parameters including target values and ranges.
- Understand technical risks and develop/execute mitigation plans.
- Lead, manage and facilitate communication and interaction with senior management, middle managers, and the development team.
Minimum Qualifications
- BS degree in physical sciences or engineering or equivalent experience in these fields.
- Mechanical or troubleshooting process development experience preferred.
- Experienced in DOE, statistical design and analysis, and Six-sigma processes.
- Experience working on complex projects with multidisciplinary colleagues preferred.
- Demonstrated problem-solving skills
- 2 - 5 years’ experience with complex equipment.
APPLICATION INSTRUCTIONS
Interested candidates should send their resume along with a cover to [email protected].
Our culture is the foundation on which we base our success:
- Integrity: Honest – Reliable – Transparent
- Relentless: Commitment – Engaged – Inspired
- Pioneering: Disruptive – Innovative – Courageous
We offer a variety of benefits to contribute to your personal and professional success
Health Benefits |
---|
Medical |
7 different medical plans with different deductibles |
Dental |
Vision |
STD & LTD |
Life insurance |
Pre-Tax benefits: HSA – FSA |
EAP (Employee Assistance Plan) |
Other Benefits |
---|
10 Paid holidays |
PTO |
Bereavement pay |
401K |
Education assistance |
Training & development |
Career opportunities within the organization |
Employee discount program through Insperity |
Technology – Evolve Additive Solutions
Thinking that transforms.
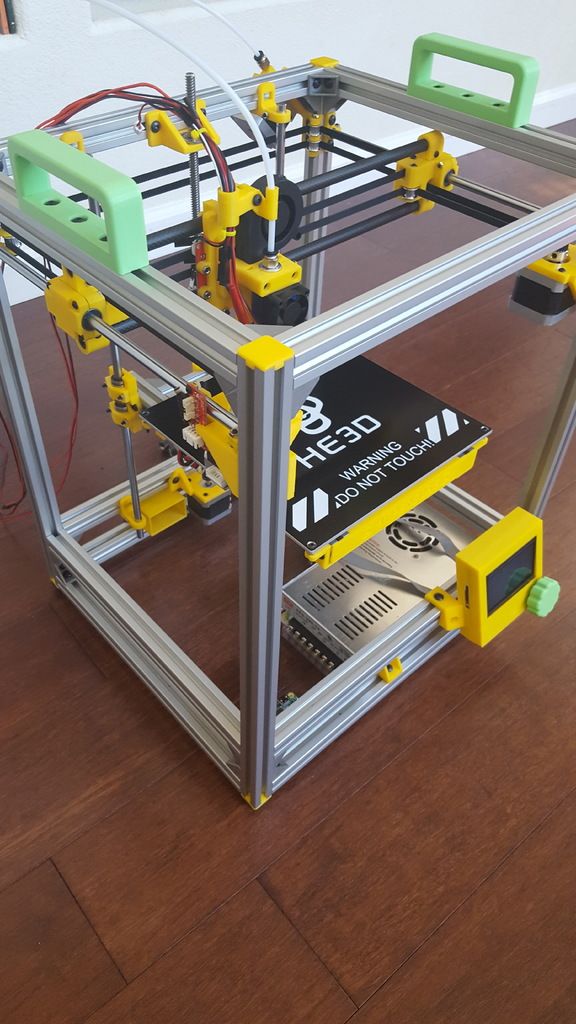
Technology that delivers.
Our Patented STEP Technology
STEP is Selective Thermoplastic Electrophotographic Process. The core of our technology is the Electrophotographic (EP) imaging and deposition. This uses the proven high volume 2D printing process. A 2D slice of a part with part material, support, and maybe multiple materials all in one image layer, then with heat, pressure, and cooling fuse it all onto the build. This creates a fully dense part with isotropic properties in all directions. (Image on right: ABS layer on the transfer belt with part and support material).
FIRST VIABLE ALTERNATIVE TO INJECTION MOLDING
We have developed a patented additive manufacturing technology strategy that frees you from your existing manufacturing constraints of making low volume production affordable – and we have the ability to allow you to reduce forecast estimates from 1 year to 90 days! From producing NEW products to part consolidation …. Evolve is transforming how the world manufactures.
See All Videos
Unlike other additive technologies that have been brought to the market in past 10 years, most if not all have been derivatives of an existing technology. STEP (Selective Thermoplastic Electrophotographic Process) is completely new and has been designed and developed specifically for production manufacturing.
STEP’s architecture utilizes the same three process phases that are the critical elements that enable STEP to deliver on the throughput and quality similar to injection molding.
One of the many benefits of the SVP (Scalable Volume Production) platform is our closed-loop process with sensor technology; each layer of the build is precisely aligned on top of the next incoming layer and the correct amount of material is deposited. If an error is detected a correction is made. This means a higher part quality with both repeatability and scalability.
For more details on how the technology works, read our White Paper in our Resource Library.
Our process to convert pellets to power is unique. Once the process is complete, we have created very small particles which allows greater detail and accuracy. Our particles are in the range of 20 to 25 microns.
The process to convert pellets to STEP compatible powder is sustainable with near zero waste or scrap. Undersized and oversized particles created during the process are fed back to the melt state along with virgin material such that in the end 100% of what goes into the process is used without waste. This is an important part of our vision for sustainability. The process to recover and re-use support material will be part of the offering as material volume scales. This is not only good for the environment; it is also part of the path to the lowest possible material cost and a reduced carbon footprint.
It is imperative that manufactures maintain their uptime, mitigate production risk, and supply chain disruptions. With a manufacturing network comprised of connected factories the ability to repeatably manufacture the exact same part anywhere in the world, wherever you have an Evolve SVP platform system located is possible.
So whether you’re a skeptic or a believer in the digitization of manufacturing or Industry 4.0, the reality is your world is changing. Competitors are moving faster, supply chain models are transforming, and consumers are rewarding brands that give them fast, affordable access to mass customized offerings. The Evolve SVP™ (Scalable Volume Production) platform is purpose-built for this new digitized world — and it’s ready to accelerate your digital transformation.
The SVP platform was designed for the connected factory environment and the onset of the Industrial Internet of Things (IIoT). One of the greatest advantages of the technology is when multiple machines are deployed because your production ability is increased, and supply chain risks are minimal.
Our partnerships with software suppliers allows us to optimize build preparation, including part slicing and nesting, as well as global production planning, scheduling, and execution. Through our global partnerships, companies pursuing industrialized additive manufacturing will have access to a joint software/hardware solution that delivers greater speed, flexibility, and repeatability for high-volume AM.
And the Evolve SVP platform is built with AI and machine learning. NO other additive technology can alter their process on a layer-by-layer basis. This accelerates problem solving and produces a superior end product.
WHAT DIFFERENTIATES OUR PLATFORM?
The Evolve SVP platform is the first true plastics manufacturing technology to achieve mass customization, just-in-time production and dependable quality. Here are five key differentiators that allow us to deliver on that promise:
SPEEDDelivering high standards for cycle times, yields and repeatability, the Evolve platform meets the needs for low to mid-volume production runs. The Evolve platform is the fastest additive manufacturing technology available at production scale. Traditionally, technology limitations meant additive manufacturing could not deliver high-quality, cost-effective parts without compromising throughput.
As manufacturing best practices inevitably change, the Evolve platform has the ability to integrate new materials. It’s capable of a range of real engineering thermoplastics, including amorphous and semi-crystalline, to produce color and multi-material parts that meet your precise production requirements.
SCALABILITYNo matter the length of the production run, the Evolve platform delivers a seamless solution architecture with platform extensibility and part customization capabilities to get you up and running quickly. Achieve accelerated scalability on your factory floor with the platform’s Industry 4.0 capabilities.
QUALITYEach part is produced through our full fusion layer-to-layer method that maximizes high-quality surface finish, fine details and functionality. The platform is uniquely designed for repeatability without compromising throughput or flexibility.
The Evolve platform has a low total cost of production. Its unique nesting system and machine speed deliver more parts at a rapid rate. This allows us to deliver a cost-competitive alternative to injection molding.
History of 3D printing
In this section, we wanted to trace the history of 3D printing from its inception to the present day, as well as give a forecast regarding the future development of technology.
The first 3d printer was invented by the American Charles Hull, he worked on the technology of stereolithography (SLA), a patent for the technology was issued in 1986. The printer was a fairly large industrial installation. The installation "grew" a three-dimensional model by applying a photopolymerizable material to a moving platform. The basis was a digital model pre-modeled on a computer (3D model). This 3d printer created three-dimensional objects, rising by 0. 1-0.2 mm - the height of the layer. Despite the fact that the first device had many disadvantages, the technology has received its application. Charles Hull is also the co-founder of 3dsystems, one of the world's leading manufacturers of industrial 3D printers.
Charles Hull was not the only one to experiment with 3D printing technology, as in 1986 Carl Deckard invented Selective Laser Sintering (SLS). You can learn more about the method in another article, briefly: a laser beam sinters a powder (plastic, metal, etc.), while the mass of the powder is heated in the working chamber to a temperature close to the melting point. The basis is also a digital model pre-modeled on a computer (3D model). After the laser passes through the horizontal layer, the chamber is lowered to the layer height (usually 0.1-0.2 mm), the powder mass is leveled with a special device and a new layer is applied.
However, the most famous and widespread 3D printing method today is layer-by-layer direction (FDM). The idea of technology belongs to Scott Crump (Scott Crump), the patent dates back to 1988. You can learn more about the method in another article, in short: material (usually plastic) is fed from the heated nozzle of the print head using a stepper motor, the print head moves on linear guides along 1 or two axes, and the platform moves along 1 or 2 axes . The basis of the movement is also a 3D model. The molten plastic is laid on the platform along the established contour, after which the head or platform is moved and a new layer is applied on top of the old one. Scott Crump is one of the founders of Stratasys, which is also one of the leaders in the production of industrial 3D printers.
All the devices described above belonged to the class of industrial devices and were quite expensive, so one of the first 3d Dimension printers from Stratasys in 1991 cost from 50 to 220 thousand US dollars (depending on the model and configuration). Printers based on the technologies described above cost even more and until very recently, only a narrow circle of interested specialists knew about these devices.
Everything began to change since 2006, when the RepRap project (from the English Replicating Rapid Prototyper - a self-replicating mechanism for rapid prototyping) was founded, with the goal of creating a self-copying device, which was a 3D printer working on technology FDM (layer by layer deposition). Only, unlike expensive industrial devices, it looked like a clumsy invention made from improvised means. Metal shafts serve as a frame, they also serve as guides for the print head. driven by simple stepper motors. The software is open source. Almost all connecting parts are printed from plastic on the 3D printer itself. This idea originated among English scientists and aimed at spreading available additive technologies so that users can download 3D models on the Internet and create the necessary products, thus minimizing the production chain.
Leaving aside the ideological component, the community (which exists and develops to this day) managed to create a 3d printer accessible to the "ordinary person". So a set of unprinted parts can cost around a couple of hundred US dollars and a finished device from $500. And even though these devices looked unsightly and were significantly inferior in quality to their industrial counterparts, all this was an incredible impetus for the development of 3D printing technology.
As the RepRap project developed, 3D printers began to appear, taking as a basis the base laid down by the movement in technical and, sometimes, ideological terms (for example, commitment to the concept of open source - OpenSource). The companies that made printers tried to make them better both in terms of performance, design and user experience. The first RepRap printers cannot be called a commercial product, since it is not so easy to manage (and even more so to assemble) and it is not always possible to achieve stable work results. Nevertheless, companies tried to close the more than significant gap in quality, leaving a significant gap in cost whenever possible.
First of all, it is worth mentioning the MakerBot company, which started as a startup, took RepRap ideas as a basis and gradually turned them into a product of a new quality.
Their flagship product (and in our opinion the best to this day) remains the MakerBot Replicator 2 3D printer. The model was released in 2012 and later discontinued, but remains one of the most popular 3D printer models to this day " personal" segment (according to 3dhubs). The word "personal" is in brackets because this printer, which cost $2,200 at the time of release, was (and is) primarily used for business purposes, but falls into the personal segment due to its cost. This model differs from its progenitors (RepRap), being, in fact, a finished commercial product. Manufacturers abandoned the concept of OpenSource, closing all sources and software codes.
In parallel with the release of equipment, the company actively developed the Thingiverse resource, which contains many models for 3d printing, available for download for free. During the development of the first printer and beyond, the community has helped the company a lot, testing the product and offering various upgrades. After the release of the Replicator 2 (and the closure of development), the situation has changed. You can learn more about the history of MakerBot and other companies and people associated with 3d printing by watching the film Print the legend.
This film also highlights the history of Formlabs, one of the first companies to launch an affordable 3D printer based on SLA (Strereolithography) technology. The company raised funds for the first FORM 1 model through crowdfunding, encountered production difficulties, but eventually released an affordable and productive 3D printer, closing the quality gap described above.
And although the 3D printers described above were far from perfect, they laid the foundation for the development of affordable 3D printing technology, which continues to this day. At the moment, the quality of FDM and SLA printers is increasing, but there is no significant price reduction, rather, on the contrary, it is growing slightly. Along with FDM and SLA, many companies are developing in the field of powder sintering (SLS), as well as metal printing. Despite the fact that such printers cannot be called affordable, their price is much lower in comparison with analogues from the professional segment. It is also worth noting the development of the line of materials, in addition to the standard ABS and PLA plastics, today many different materials are used, including nylon, carbon fiber and other durable and refractory materials.
Personal 3d printers of today are very close to professional devices, the development of which also does not stop. In addition to the "founders" of the technology (Stratasys, 3dsystems), many small companies specializing in industrial 3D printing technologies (metal in particular) have emerged. 3D printing is also attracting the attention of large corporations, which, with varying degrees of success, are striving to take their place in a growing market. Here it is worth highlighting HP, which recently released the HP Jet Fusion 3D 4200 model, which has gained popularity among 3d printing professionals (as of 2018, it is at the top of the ranking of professional 3D printers in the quarterly reports of the 3dhubs portal).
However, 3D printing technologies are developing not only in breadth, but also in depth. One of the main disadvantages of 3D printing, compared to other production methods, is the low speed of creating models. A significant advance in terms of accelerating 3D printing was the invention of CLIP technology by CARBON, printers operating on this technology can produce models 100 times faster than classic SLA technology.
There is also a constant expansion of the range, properties and quality of materials and post-processing of products. All this accelerates the transition to the use of 3d printers in production, and not just as prototyping devices. Today, many large and not only companies and organizations are closely using a 3D printer in their production chain: from consumer goods manufacturers NIKE and PUMA to BOEING and SPACE X (the latter prints engine parts for its rockets that could not be made in any other way) .
In addition to the "classic" scope of 3D printing, today more and more often you can see news about how a house or some organ (or rather, a small part of it) was printed on a 3D printer from bio-material. And this is true, several companies around the world are testing or already partially using 3D printing in the construction of buildings and structures. This mainly concerns the contour pouring of walls (similar to the FDM method) with a special composite concrete mixture. And in Amsterdam there is a 3D printed bridge project and this list will only expand over time, since the use of 3D printing in construction can significantly reduce costs and increase the speed of work at certain stages.
With regards to medicine, here 3D printing also finds application, but at the moment it is not printing organs, but rather the use of technology in prosthetics (of various kinds) and bone replacement. Also, 3D printing technology is widely used in dentistry (SLA technology). Regarding the printing of organs, this is still far in the future, at the moment bio-3D printers are experimental facilities in the early stages, the success of which is limited to printing a few limited-viable cells.
Looking to the future, it is safe to say that 3D printing technology will expand both in breadth and depth, improving technology, speeding up processes, improving quality and improving material properties. 3D printers will increasingly replace old methods in production chains of various scales, and world production, due to this, will move towards the “on demand” scheme of work, increasing the degree of product customization. Perhaps someday, 3D printers will be widely used at the household level for the production of necessary things (the dream and goal of the RepRap movement), but this requires not only the development of technology, but also a paradigm shift in social thinking, as well as the development of a powerful design ecosystem ( 3d modeling) products (which is often forgotten).
3d printing of houses (and other structures) will no doubt also develop, reducing costs and production time, which, together with the development of new approaches in architecture and urban planning (such as modular construction and the prefabricated method), will give a tangible impetus to development the industry as a whole.
Biological 3D printers will be an important tool in scientific research. However, before they appear in hospitals and clinics, where they will print new organs, it is still very, very far away (in fact, this is science fiction).
history of creation and development, who invented and invented when
3D printers appeared in industrial enterprises, educational organizations, became available for home use, ceasing to be exclusive equipment. When and by whom was the 3D printer invented, what 3D printing technologies exist and where are they applied, what is the future of 3D equipment?
The first 3D printer: history of creation
Engineers-inventors from different countries took part in the development of 3D technologies. Chuck Hull, an American developer, is considered a pioneer in the world of 3D printing. He began to create a “installation for stereolithography” in 1984, and a couple of years later he received a patent for it. This made it possible to transfer the project to a commercial footing: in 1988, mass production of 3D printers began.
Interesting! Hull became the first, because he managed to patent his invention. But even before him, the Japanese Hideo Kodama came up with the technology of photopolymer curing of models and tried in May 1980 years to get a patent, later - in 1984 - the French Olivier de Witte, Alain le Meho and Jean-Claude André filed an application for their invention of a stereolithography apparatus. But for one reason or another, neither the first nor the second could patent their own developments.
The printing technology is as follows: a liquid light-sensitive substance - a photopolymer - is laid out in a thin layer and immediately cured under the influence of UV rays, turning into plastic and acquiring a given shape.
In the same year 1988 that Hull's 3D printers hit the market, another American, Steven Scott Crump, proposed a new way of 3D printing - deposition modeling. And the third technique, which was laser sintering of a photopolymer, but not a solution, but a powder, was introduced by Carl Deckard, an engineer from the University of Texas.
All three machines for printing 3D objects became the prototypes of modern printers designed to create three-dimensional models. The first units were not distinguished by high quality and accuracy of printed products, but this was only the first step in breakthrough 3D printing technology.
Help. The term "3D printing" appeared only in 1995, and the name "3D printer" was given to the invented units in 1996.
Evolution in 3D printing
Algorithms for creating a three-dimensional object have been gradually improved. New materials and methods of their processing appeared, printing accuracy increased and the quality of finished products improved. Each of the methods for making 3D models has its own advantages and disadvantages. Different areas of production are suitable for their own technology, and even the earliest of all remains relevant decades after its first announcement.
LOM
LOM (laminated object manufacturing) was invented in 1985 by Mikhailo Feigen. A three-dimensional figure is formed from thin layers of plastic, paper, fabric, and composite materials. The films are cut along the contour with a laser, then the material is heated and joined in layers under pressure.
Important! The cost of materials for LOM printing is low, this makes it possible to minimize the cost of products. But the price of printers is an order of magnitude higher than, for example, FDM devices, so this technique is not in demand for personal use.
SLS
The abbreviation SLS stands for selective laser sintering. The process is as follows:
- powder or granules are scattered in a thin uniform layer;
- the laser beam sinters the filament in the areas defined by the digital model;
- the next layer is poured and leveled, and the cycle is repeated until a complete object is obtained.
Important ! It is allowed to print several models at the same time in one chamber of the printer.
![]()
The filament is polymer powder, ceramic granules, nylon and metal powder.
SGC
SGC (solid ground curing) is a layer-by-layer compaction technique implemented by Cubital engineers (Israel). The printing procedure consists in projecting a template onto a photopolymer layer. The area illuminated by ultraviolet rays hardens, the cavities are filled with wax, and the formation of the next layer begins. Actions are repeated many times, and a three-dimensional detail appears. At the end of the process, the wax melts.
Important! The cost of the equipment is very high, and expensive toxic polymers are applicable as a filament.
The technology received a second name - mask stereolithography.
FDM
Fused deposition modeling can literally be translated as “layer-by-layer fusion”. Most modern 3D printers use this particular technology of printing with thermoplastic materials. The filament is fed into the extruder, melted and extruded with a thin thread onto the platform, where a three-dimensional model grows layer by layer.
Reference:
- FDM technology prints parts of any complexity;
- The range of thermoplastics allows you to choose the right color and properties for printing;
- formed objects can be processed - sanded, painted, finished on CNC machines and manually.
Affordable cost of printers and filament led to their use for home use.
RepRap
The Replicating Rapid Prototyper - RepRap for short - launched in 2006. His goal is to create a printer capable of reproducing itself. The first copy of the self-replicating apparatus was presented in 2008. He printed about half of his own structural components and mechanisms.
Diagrams, drawings and explanatory documentation are available for download on the Internet. Thanks to RepRap printers and free access to instructions, anyone can set up small-scale production to create 3D models with minimal investment in the purchase of equipment. All costs are in the purchase of plastic.
The first food printer
The idea to print food was brought to life by scientists at the Massachusetts Institute of Technology. Amit Zoran and Marcello Coelho of Fluid Interfaces Group released a 3D printer that recreates food in 2010. The device was called Cornucopia (from the English. "Cornucopia"). The printing device independently creates mixtures, cools to a predetermined temperature and creates a finished product, which is a dish with the necessary taste, smell and texture and has the required nutritional value.
3D printer in medicine
The seemingly utopian idea to fill the printing device with living cells instead of ink has come true - a bioprinter has been invented. The equipment that came out of the walls of the American University of Wake Forest is designed to recreate human organs from stem cells.
What a bioprinter can print:
- blood vessels;
- leather;
- tissue pieces;
- cartilage;
- whole organs - kidneys, bladder, heart.
Interesting . The bioprinter is used to speed up wound healing. The device, after scanning the damage, prints the tissues filling the wound directly on the patient's body.
The future of 3D printing
3D printing is the technology of the future. Being a real multifunctional and at the same time compact factory, the 3D printer will be used in many areas: construction, medicine, automotive, electronics, food industry, pharmaceuticals.
- Construction . The printed house is no longer considered a miracle. In China, Dubai and European countries, there are already architectural objects printed by huge 3D construction printers using mortar as a filament.
- Medicine .
The main direction of introduction of printing devices is obtaining organs for transplantation. The formation of blood vessels, skin integuments is successfully practiced in the environment of scientific medical institutions.
- Automotive . 3D printing technology is already being used to produce parts. There are prototypes completely created on the printer.
- Food industry . In addition to creating culinary masterpieces, printing devices will be used to produce dishes with desired properties - dietary, with precisely calculated nutritional value. Food for space travelers is also proposed to be printed.
These are just a few of the applications for 3D printing technology. Thanks to the ability to reduce the cost of products by reducing production costs, more and more enterprises will be equipped with printing devices, and in everyday life they will firmly take their place next to traditional inkjet and laser devices.