Northeastern 3d printing
Northeastern scientists bring space and medical applications to life with living 3D printable material
0Shares
Researchers from Northeastern University have devised a 3D printable living material capable of growing and healing itself.
The proof-of-concept study sought to harness the properties that are unique to the materials that make up living things for a wide range of purposes, ranging from therapeutic and medical, to industrial and even space applications.
Formed from genetically engineered E. coli, the scientists’ material is “truly living” as it is entirely biological and is not blended with anything else.
“Like a tree has cells embedded within it and it goes from a seed to a tree by assimilating resources from its surroundings in order to enact these structure-building programs, what we want to do is a similar thing but where we provide those programs in the form of DNA that we write and genetic engineering,” said Neel Joshi, Associate Professor of Chemistry and Chemical Biology at Northeastern.
Printing living cells
Genetically modified E. coli has been used in the creation of “living” 3D printable materials before, by researchers from the MIT Media Lab, Harvard University’s Wyss Institute, and the Dana-Farber Cancer Institute. The team’s Hybrid Living Material (HLM) fabrication platform used a combination of inkjet 3D printing, resins, and chemical signals to activate responses in biologically engineered microbes, with particular applications in the medical sector.
Elsewhere, scientists around the world have been experimenting with 3D printing living cells for bone-mimicking structures, to produce sensory neurons, and to study their mechanoresponsive behavior. However, while these materials contain living cells, they are not considered to be “alive”, as they are combined with various inert substances.
The Northeastern team’s new microbial material is, in contrast, entirely biological and is what they consider to be “truly living”.
Neel Joshi, associate professor of chemistry and chemical biology, works on programmable microbial ink for 3D printing of living materials, in the Mugar Life Sciences building. Photo via Matthew Modoono/Northeastern University.Programming E. coli for 3D printing
E. coli produces a particular protein that acts as a natural building block, called Curli fibers, which attach to a surface and one another to form a community. The same properties that make the Curli fibers a sort of glue for the bacteria also make it an attractive material for microbial engineers.
To create their living material, the researchers first worked out a way to engineer the bacterium E. coli to produce an entirely biological ink that could be used to 3D print solid structures. The scientists began by culturing genetically engineered E. coli in a flask, feeding the bacteria nutrients so that they multiplied and, as they divided, produced the Curli fiber polymers.
The researchers then filtered out the gelatinous polymers to form a microbial ink that could be fed into a 3D printer. While using microbes to make 3D printable inks is not new in itself, what sets this particular microbial ink apart is that it is 100 percent biological and not blended with any other substances.
The researchers 3D-printed small shapes using the microbial ink that they developed from the bacterium Escherichia coli, also known as E. coli. Image via Duraj-Thatte et al., Nature Communications.Testing the living material
The Northeastern team used the gelatinous material to print small objects in the shape of a circle, square, and cone. The aim of the project is to use the material’s living cells as “factories” to make materials with specific attributes, such as those that could be useful in medicine.
“Think about it as a platform for building many different things, not just bricks for buildings or construction,” said Joshi, who compares the team’s work to how polymer chemists devise plastic materials with various distinct purposes. “Biology is able to do similar things. Think about the difference between hair, which is flexible, and horns on a deer or a rhino or something. They’re made of similar materials, but they have very different functions.
“Biology has figured out how to tune those mechanical properties using a limited set of building blocks.”
Due to the material being “alive”, it can do what living things do, said Manjula-Basavanna, a postdoctoral fellow in Joshi’s laboratory. For example, the material is capable of healing itself, the way skin does, and in the right conditions, the cells within the microbial gel could simply make more of themselves. However, the material is not necessarily always growing.
“If you were to take [the] whole cone and dunk it into some glucose solution, the cells would eat that glucose and they would make more of that fiber and grow the cone into something bigger,” explained Joshi. “There is the option to leverage the fact that there are living cells there. But you can also just kill the cells and use it as an inert material.”
While the initial gel is made entirely from genetically engineered E. coli, the Northeastern team also experimented with mixing the ink with other genetically engineered microbes to create different 3D printing materials.
Through their experiments, the team fabricated a material capable of delivering an anti-cancer drug when it encounters a specific chemical stimulus, and a material that can trap the toxic chemical Bisphenol A from its surrounding environment.
While the study is so far a proof-of-concept, Joshi believes the microbial ink could pave the way for a whole range of possibilities for building things with biology. For instance, the material could have potential uses for constructing off-space habitats and their components, as well as numerous medical applications.
“If there is a way to manufacture in a more sustainable manner, it’s going to involve using living cells,” Joshi said. “This is advancing more towards that type of paradigm of building things with living cells.”
Further information on the study can be found in the paper titled: “Programmable microbial ink for 3D printing of living materials produced from genetically engineered protein nanofibers,” published in the Nature Communications journal. The study is co-authored by A. Duraj-Thatte, A. Manjula-Basavanna, J. Rutledge, J. Xia, S. Hassan, A. Sourlis, A. Rubio, A. Lesha, M. Zenkl, A. Kan, D. Weitz, Y. Zhang, N. Joshi.
Subscribe to the 3D Printing Industry newsletter for the latest news in additive manufacturing. You can also stay connected by following us on Twitter and liking us on Facebook.
Looking for a career in additive manufacturing? Visit 3D Printing Jobs for a selection of roles in the industry.
Subscribe to our YouTube channel for the latest 3D printing video shorts, reviews and webinar replays.
Featured image shows Neel Joshi, associate professor of chemistry and chemical biology, and Avinash Manjula-Basavanna, a postdoctoral researcher, work on programmable microbial ink for 3D printing of living materials, in the Mugar Life Sciences building. Photo by Matthew Modoono/Northeastern University.
Tags A. Duraj-Thatte A. Kan A. Lesha A. Manjula-Basavanna A. Rubio A. Sourlis D. Weitz Dana-Farber Cancer Institute Harvard University J. Rutledge J. Xia M. Zenkl Manjula-Basavanna MIT Media Lab N. Joshi Neel Joshi Northeastern university S. Hassan Wyss Institute Y. Zhang
Hayley Everett
Hayley is a Technology Journalist for 3DPI and has a background in B2B publications spanning manufacturing, tools and cycling. Writing news and features, she holds a keen interest in emerging technologies which are impacting the world we live in.
With live 3D printable material, Northeastern researchers bring space and medical applications to life.
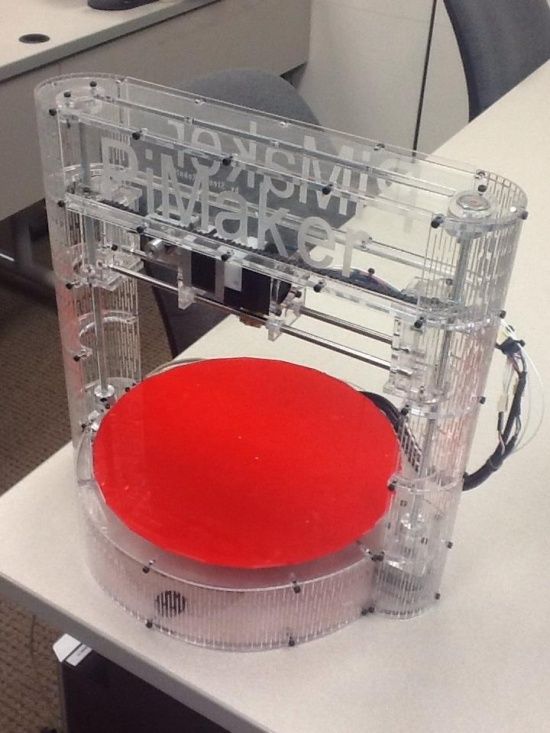
Northeastern University researchers have created a 3D printable living substance that can self-grow and cure.
The proof-of-concept study aimed to leverage the unique qualities of the materials that make up living organisms for a variety of uses, including therapeutic and medicinal, industrial, and even space applications.
The scientists’ material is “really living” because it is wholly biological and not combined with anything else. It was created from genetically altered E. coli.
“Like a tree has cells embedded within it and grows from a seed to a tree by assimilating materials from its surrounds to perform these structure-building programs,” said Neel Joshi, Associate Professor of Chemistry and Chemical Biology at Northeastern University.
Living cells can be printed.
Researchers from the MIT Media Lab, Harvard University’s Wyss Institute, and the Dana-Farber Cancer Institute have previously employed genetically modified E. coli to create “alive” 3D printing materials.
The team’s Hybrid Living Material (HLM) manufacturing platform uses inkjet 3D printing, resins,
and chemical signals to activate reactions in biologically designed bacteria, with applications in the medical field.
Scientists have been experimenting with 3D printing living cells for bone-mimicking structures,
producing sensory neurons, and studying their mechanoresponsive behaviour in other parts of the world. These materials, however, contain living cells but are not termed “life” because they are mixed with numerous inert chemicals.
E. coli programming for 3D printing
Curli fibres,
which E. coli creates as
a natural building component,
adhere to a surface and to one another
to form a community,
which are produced by E. coli.
Curli fibres are intriguing to microbial engineers because they have the same qualities that make them a kind of glue for bacteria.
To make their living material, the researchers first devised a method of engineering the bacterium E. coli to produce a fully biological ink capable of 3D printing solid objects.
The researchers started by growing genetically modified E. coli in a flask and fed the bacteria nutrition
so that they could multiply and generate Curli fibre polymers
as they divided.
The gelatinous polymers were then filtered out, resulting in a
microbial ink that could be fed into a 3D printer.
While the use of microorganisms to create 3D printed inks is not new,
The fact that this microbial ink is 100 per cent biological and not combined with any other ingredients distinguishes it from others.
Examining the live matter
The Northeastern team printed miniature items in the shapes of a circle, square, and cone using the gelatinous material. The project’s goal is to employ the material’s live cells as “factories” to create materials
with certain properties,
such as those beneficial in medicine.
“Think of it as a platform for
building a variety of things,
not just bricks for structures or construction,”
Joshi said, comparing the team’s work to how polymer scientists create plastic materials for a variety of uses. “Biology is capable of similar feats. Consider the difference between flexible hair and horns on a deer, rhino, or other animals. They’re made of comparable materials, but their purposes are vastly different.
Because the material is “alive,” it may perform the same functions as living creatures, according to Manjula-Basavanna, a postdoctoral fellow in Joshi’s group. For example, the material can mend itself in the same way as the skin can, and under the appropriate conditions, the cells within the microbial gel might simply reproduce themselves. The substance, on the other hand, does not always increase.
“If you submerge [the] complete cone in a glucose solution, the cells will eat the glucose and produce more fibre, causing the cone to grow larger,” Joshi stated. “It’s possible to make use of the fact that there are living cells there.” However, you can simply destroy the cells and use the substance as an inert material.”
A World of Possibilities
While the initial gel is formed
completely of genetically modified E. coli,
the Northeastern researchers also tried mixing the ink with other genetically modified organisms
to develop various 3D printing materials.
The scientists used their trials to create a material that can deliver an anti-cancer medicine when it comes into contact with a specific chemical stimulus
, as well as a material that can trap the dangerous toxin Bisphenol A in its environment.
While the research is only a proof-of-concept,
Joshi believes the microbial ink might open up a world of possibilities for biologically-based construction.
For example,
the material could be used to build off-plane
t dwellings and their components,
as well as a variety of medical applications.
“It will involve employing living cells if there is a way to manufacture in a more sustainable manner,” Joshi added. “We’re getting closer to that type of paradigm of making things out of living cells.”
3D Printing in the North-Eastern Administrative District
Authorization
Place a company
You are in the category:
Advertising and printing
3D printing
Premium seat is free,
Be the first to review
1. 3D Printing Lab
3D Printing Lab
+7 (495) 587-41-40
lab3dprint.ru
m. Preobrazhenskaya Square – 0.7 km, 11 min. on foot
Open until 19:00
Closes after 2:17
Be the first to review
2. Mister Print Pro
Printing on clothes to order in Moscow - photos, inscriptions, logos
+7 (499) 213-03-75
mrprint.pro
Krasnoselskaya metro station – 0. 6 km, 10 min. on foot
Open until 22:00
Closes after 5:17
Be the first to review
3. Center for 3D printing "3DVision"
3D Printing Center
+7 (495) 662-98-58
3dvision.su
m. Oktyabrskoye Pole - 0.9 km, 14 min. on foot
Open until 18:00
Closes after 1:17
Be the first to review
4 VolPrint
3D printing in Moscow.
+7 (495) 880-02-50
tomsk. volprint.ru
m. Shchelkovskaya - 1 km, 16 min. on foot
Closed until 9:00
Be the first to review
5. "Photo to the house"
Production of photo wallpapers, banners, self-leveling floors
+7 (495) 175-64-32
fotovdom.ru
m. Highway Enthusiasts – 0.4 km, 6 min. on foot
Open until 21:00
Closes after 4:17
Show all subcategories of
3D printers will change the world in three years // Watch
Study: 3D printers will change the world in three years // Watch-
Profile
3D printers and 3D printing April 2, 2013, 10:41 am
3D printing technology never ceases to excite the minds of its followers. However, at the moment, 3D printers are quite expensive and generally inaccessible to the mass consumer. Analysts from Gartner claim that printers will cost less than $2,000 by 2016.
3D printing technology never ceases to excite the minds of its followers. They describe a world where clothes will not be bought in stores, but will be downloaded from the Internet and printed. A world where everyone can create things on their own. However, at the moment, serious 3D printers are quite expensive and generally inaccessible to the mass consumer. Analysts at Gartner say that by 2016, industrial-quality printers will cost less than $2,000.
Of course, there is already a $75 3D printer out there, but it's designed more for creating handmade crafts than for printing serious models and objects. Despite the high cost, the market is already mastering the new technology. For example, in Japan, people are digitized and their figures are printed on a 3D printer with amazing accuracy. One inventor even started printing full-fledged cars. It is hard to even imagine what applications 3D printing will find after the technology becomes mainstream.
The Gartner report says that the proliferation of 3D printers will lead to a rapid drop in the price of 3D printers. The gradual development and reduction in the cost of technology will make it more and more mass. Exploiting the full potential of 3D printing will save you money, time and productivity.
"Businesses must continually monitor technology development to determine where improvements can be made," said Pete Basiler, director of research at Gartner. 3D printing is a tool for empowerment. Already, it allows you to create parts and products that are changing the lives of countries in distress and areas affected by the crisis.
Already, some small businesses, if they can afford a 3D printer, see little need for it. In this regard, 3D printing needs something more than low cost. She needs a retail market where designers can sell professional quality work.