Ethylene vinyl acetate 3d printing
Braskem releases EVA based sustainable 3D printing filaments
3D Printing FilamentsBiomaterialsMaterialsSustainabilityThermoplastic Polymers
Based on bioplastic derived from raw sugarcane as well as from recycled polyethylene and polypropylene
3D Printing Media NetworkMay 10, 2022
2 minutes read
Stay up to date with everything that is happening in the wonderful world of AM via our LinkedIn community.
Braskem, the largest polyolefins producer in the Americas, as well as a market leader and pioneer producer of biopolymers on an industrial scale, released three new sustainable 3D printing filament product offerings for the additive manufacturing market. These first of their kind products include 3D printing filaments produced from bio-based ethylene vinyl acetate (EVA) filament derived from raw sugarcane as well from recycled polyethylene and polypropylene (PE/PP) blended filaments with, or without, carbon fiber.
These sustainable products will be displayed in conjunction with Braskem’s upcoming presence at Rapid + TCT , North America’s largest Additive Manufacturing conference, being held at Huntington Place, in Detroit, Michigan from May 17 to 19, 2022.
Jason Vagnozzi, Braskem Global Commercial Director of Additive Manufacturing, commented, “Braskem has a longstanding history of innovating and producing more sustainable bio-based polymers, and today’s launch announcement regarding green EVA and recycled polymer 3D printing filaments reaffirms our commitment to a more circular, carbon-neutral future. We couldn’t be more excited to present these newest additions to our 3D printing product portfolio at the RAPID + TCT 2022 conference as our clients seek more sustainability solutions for the future.”
Bio-based EVA Filament – FL600EVA-BIO
FL600EVA-BIO is a bio-based ethylene vinyl acetate (EVA) filament, derived from raw sugar care, providing a more sustainable alternative to traditional flexible materials available on the market. This low carbon footprint formulation delivers a unique combination of sustainability, flexibility, ductility, light-weighting, and moisture resistance for direct drive printing 3D printing systems. FL600EVA-BIO expands the availability of sustainable materials for use in 3D printing applications such as consumer, packaging, and industrial markets.
FL600EVA-BIO applications include packaging, shoes, fashion, consumer products and industrial applications, as well as rapid prototyping and mass customization. Parts are Flexible parts and lightweight. Filaments are compatible with direct drive system 3D printers.
Recycled Polyolefin Filament – FL600R
Braskem FL600R is a recycled filament designed for use in material extrusion-based Additive Manufacturing while maximizing sustainably sourced content. Primarily sourced from recycled bottle caps, FL600R is a recycled PE/PP blend containing over 90% sustainably sourced material, providing a more sustainable solution without sacrificing printability. This environmentally friendly filament provides the same low density as well as water, chemical, and impact resistance inherent to virgin polyethylene and polypropylene-based materials.
Recycled Polyolefin Filament with Carbon Fiber – FL605R-CF
Braskem FL605R-CF is an engineering-grade polymer for additive manufacturing, containing 90% recycled content. Primarily sourced from recycled bottle caps, FL605R-CF is a recycled PE/PP blend that incorporates the use of recycled carbon fiber for added strength and durability, providing a more sustainable solution without sacrificing printability and mechanical properties. This environmentally friendly filament provides the same low density as well as water, chemical, and impact resistance inherent to virgin polyethylene and polypropylene-based materials.
The Braskem 3D printing R&D Labs in PittsburghFor those attending the Rapid + TCT Conference, Jason Vagnozzi, Braskem Global Commercial Director of Additive Manufacturing, and Michelle Sing, Ph. D., Braskem Materials Development Research Engineer, will be keynote presenters. They will discuss the development and design of sustainable materials such as EVA for additive manufacturing. Please check the schedule for keynote presentation times during the show.
As one of the world’s largest producers of polyolefins, Braskem offers solutions across 3D printing technologies such as Fused Filament Fabrication (FFF), Selective Laser Sintering (SLS), and High-speed Pellet Extrusion. Through Braskem’s decades of expertise in materials science and product development, its state-of-the-art 3D printing labs, as well as its strategic partnerships with industry leaders, Braskem is committed to delivering new and innovative products to the market. If you are a start-up, university, equipment manufacturer, converter, compounder, or brand owner, Braskem’s product development professionals can collaborate with you on your next 3D printing solution.
Related Articles
Back to top button
Ethylene vinyl acetate (EVA) as a new drug carrier for 3D printed medical drug delivery devices.
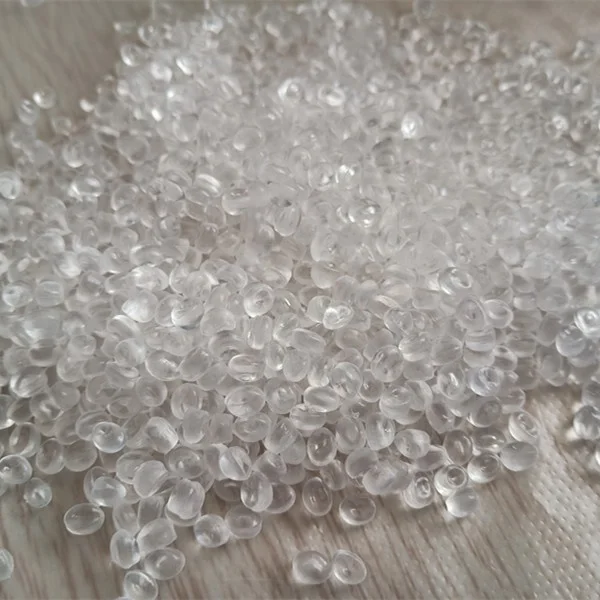
3D printing of high drug loaded dosage forms using thermoplastic polyurethanes.
Assessment of different polymers and drug loads for fused deposition modeling of drug loaded implants
- Wiebke Kempin, Christian Franz, Anne Seidlitz
Materials Science, Biology
European journal of pharmaceutics and biopharmaceutics : official journal of Arbeitsgemeinschaft fur Pharmazeutische Verfahrenstechnik e.V
- 2017
3D Printed Polymeric Drug-Eluting Implants.
Development of modified release 3D printed tablets (printlets) with pharmaceutical excipients using additive manufacturing.
- A. Goyanes, Fabrizio Fina, Annalisa Martorana, Daniel Sedough, S. Gaisford, A. Basit
Materials Science
International journal of pharmaceutics
- 2017
Optimize PLA/EVA Polymers Blend Compositional Coating for Next Generation Biodegradable Drug-Eluting Stents
- Naila Ishaque, Nauman Naseer, A.
Elaissari
Materials Science
Polymers
- 2022
In this research work, polymer blends of poly-lactic acid (PLA)/ethylene vinyl acetate (EVA) were prepared as the drug carrier materials for a bi-layer drug-loaded coating film for coronary stents.…
Formulation development and process analysis of drug-loaded filaments manufactured via hot-melt extrusion for 3D-printing of medicines
A development of 3D-printable filaments, which can continuously be produced via hot-melt extrusion, and it showed that powder feed rate and speed of the stretching device used after extrusion predominantly determine the diameter of the filament and thereby the mechanical resilience of a filament.
Strategies and mechanisms to improve the printability of pharmaceutical polymers Eudragit® EPO and Soluplus®.
Drug loading and printability of two different grades of prefabricated polyvinyl alcohol filaments for fused deposition modeling-based 3D printing
- A.
Hussain, Faisal Mahmood, Fahad Hussain
Chemistry, Materials Science
- 2020
Therapeutic doses of low-dose drug can be loaded efficiently in printed scaffolds of prefabricated polyvinyl alcohol filaments in terms of drug-loading capacity and printability.
Polymer Selection for Hot-Melt Extrusion Coupled to Fused Deposition Modelling in Pharmaceutics
- Gabriela G Pereira, S. Figueiredo, A. Fernandes, J. Pinto
Materials Science
Pharmaceutics
- 2020
The ability to integrate HME and FDM and predict and tailor the filaments’ properties will extend the range of printable polymers/formulations, and the properties of the most common pharmaceutical-grade polymers used are revised, providing suitable processing windows for different raw materials.
Development of filaments for fused deposition modeling 3D printing with medical grade poly(lactic-co-glycolic acid) copolymers
This work developed filaments for the manufacturing of custom implants and patient-tailored drug dosage forms with fused deposition modeling (FDM) three-dimensional (3D) printing from different medical grade poly(lactic-co-glycolic acid) copolymers.
News
Subscribe to
Subscribe
I do not want
2
Large Brazilian Neftekhimic Company Braskem offers three phylaments for FDM 3D printerers from biopolymers and crossed plastics . The new range includes ethylene vinyl acetate (EVA) derived from sugarcane, as well as two recycled filaments - a blend of polyethylene and polypropylene (PE/PP) in its pure form and with a carbon fiber filler.
FL600EVA-BIO
FL600EVA-BIO is a biopolymer filament based on plant derived ethylene vinyl acetate similar in properties to low density polyethylene. The material is highly elastic, with a hardness of 94 Shore A and an elongation at break of over 500%. The biopolymer is characterized by low density, hygroscopicity and heat shrinkage, good chemical resistance and is offered in natural shade filaments with a diameter of 1. 75 and 2.85 mm. Due to its softness and elasticity, it is recommended to use direct-fed extruders for working with this material.
FL600R
FL600R is a filament made from recycled polyethylene and polypropylene. The share of secondary raw materials reaches 90%. The material does not require pre-drying and the use of heat chambers, has characteristics similar to virgin polyethylene and polypropylene in terms of chemical resistance and impact strength, as well as low heat shrinkage and high dimensional stability. The filament is available in black filaments with a diameter of 1.75 and 2.85 mm.
FL605R-CF
FL605R-CF is a composite version of the FL600R with added carbon fiber for increased rigidity and strength. The share of secondary raw materials also reaches 90%, mainly recycled caps from plastic bottles are used. The composite has high strength characteristics and chemical resistance, low hygroscopicity, density and heat shrinkage, high dimensional stability. Thermal chambers and drying before 3D printing are not required. The material is offered in the form of black filaments with a diameter of 1.75 and 2.85 mm.
New content will be on display May 17-19 at Detroit's Rapid + TCT. More information about Braskem's offerings in the field of additive technologies can be found on the official website.
Do you have interesting news? Share your developments with us, and we will tell the whole world about them! We are waiting for your ideas at [email protected].
FFF fdm Braskem
Follow author
Follow
Don't want
2
Article comments
More interesting articles
6
Subscribe author
Subscribe
Don't want
REC offers a set of 1. 8 mm filaments, primarily for 3D printer operators...
Read more
5
Subscribe to the author
Subscribe
Don't want to
Cosmonaut Oleg Artemiev, who recently returned from the International Space Station, spoke about the experimental...
Read more
sarkazm
Loading
04/01/2016
39748
68
Follow author
Follow
Don't want
News from the world of printing in a short line
FDplast announced the release of a free...
Read more
Simple things are difficult. Letter from a chemist to a 3D printer. Solvents for plastics and protection against them / Sudo Null IT News Recently, there has been a real surge of interest in the chemistry of macromolecular compounds, associated with the emergence of affordable 3D printers and the need to navigate in their “inks” (i.
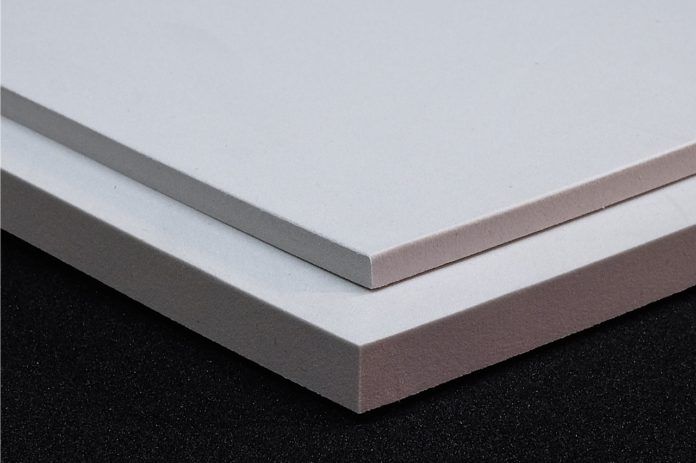
As I already wrote a couple of times in the comments to my articles, recently, from time to time, I have the idea to make myself an “exhibition” stand, which would present samples of plastics. Just because almost every second question of the chemical sense sounds like “what kind of plastic is it”. What this says, says that the possibilities of 3D printing have attracted so much public attention to plastics, polymers, etc. which even hundreds of online science popularizers could not do. Well, in general, looking at these trends, we can safely state that the future, the future is not so much for metals, but for composites and new types of polymers. So, those who today are thinking about choosing a chemical specialty - consider this option. Therefore, once again, your obedient servant decided to make his modest contribution and tell about what I constantly have to face. Today we read about solvents for plastics and the features of working with them. First, a little theoretical introduction.
"The materiel is the part with the materiel..."
To tell in a nutshell about the dissolution of polymers will not work with all the desire, because the topic is voluminous and ambiguous (you can even say “will pull on a university course”, hello to you, Leonid Petrovich Krul, I repay the debt for the 8-ku in the Navy). A good (read educational) review for people with a fairly high level of technical (chemists and engineers) literacy can be read here. The dissolution process will be discussed below, for now, a few words about the choice of solvent (or why something dissolves plastic, but something does not).
In general, the selection of a suitable solvent is made by two methods:
1. Using the Hildebrand solubility parameters. This calculation applies if polymer (p) and solvent (s) have the same polar and hydrogen bond parameter, then the following simple rule works:
|δ s - δ p | ≤ 3.6 MPa 1/2
As an example, I will give the Hildebrand parameters for some polymers:
Whoever wants to test himself can calculate the solubility at his leisure :). You can and should look for constants in this book. It is important to note that the Hildebrand parameters are only useful for non-polar and weakly polar mixtures in the absence of hydrogen bonds (dipole moment <2 D (Debye). For other cases, method 2 is used.
Note: for those who traditionally “knew it but forgot”, I remind you that according to IUPAC standards (what kind they are - see the article about the periodic table) solvents are qualitatively grouped into non-polar, polar aprotic and polar protic solvents, for division into groups of which, their dielectric constant is often used. Most commonly, a protic solvent is a solvent that has a hydrogen atom bonded to an oxygen (as in a hydroxyl group), nitrogen (as in an amino group), or fluorine (as in hydrogen fluoride). In general, any solvent that contains mobile H + is called a protic solvent. Molecules of such solvents easily donate protons (H + ) to other reagents. Conversely, aprotic solvents cannot donate protons, since they do not contain H + . They usually have high dielectric constant and high polarity. The picture below shows examples of common solvents, divided into classes.
We return to the selection of the solvent. As I already wrote, if Hilderbrand does not fit, we use Hansen.
2. Using the Hansen solubility parameters, for each solute, one can compose an approximate spherical "volume" of solubility with radius R. Only solvents that have Hansen solubility parameters in this volume can dissolve this polymer:
[4(δ d2 - Δ D1 ) 2 + (δ P2 - δ P1 ) 2 + (δ H3 - δ H2 ) 2 ] ] ] ] ] ] ] ] ] ] ] ]0002 The interaction radius R depends on the type of polymer. R values are usually in the range of 4 to 15 MPa 1/2 . The Hansen parameters needed to calculate the solubility of your system can be found in this book. For clarity, the picture below shows the Hansen parameters (similar to Hilderbrant) for some commonly used polymers.
If someone really needs to do targeted solvent screening for their polymer using the Hansen method, I recommend looking at the HSPiP program, which does an excellent job of this task. Click here for an overview and description of the work.
In general, we can say the following. First, the "golden rule of dissolution" - like will dissolve in like - works for polymers as well. Those. Compounds with similar chemical structures are more likely to dissolve than compounds with different structures. Second, the higher the molecular weight of the polymer, the closer the solubility parameter of the solvent and polymer must be in order for the polymer to dissolve in the solvent. For linear and branched polymers, the plot of solubility versus solubility parameter for a number of solvents will reach a maximum when the solubility parameters (Hansen/Hilderbrandt) of the solute and solvent are the same. In the case of a crosslinked polymer, the amount of swelling, i.e. the absorption of the solvent, will reach a maximum when the solubility parameters of the solvent match those of the polymer. Thirdly, the solubility parameters of polymers do not change much with temperature, while the parameters of low molecular weight compounds often decrease markedly with increasing temperature, so the higher the molecular weight of the polymer, the closer the solubility parameter of the solvent must be for dissolving the polymer in the solvent.
Okay, I hope I didn't tire the reader too much. I hasten to move from theory to practice.
Chemical welding of plastics
Traditionally, if you suddenly need to splice several pieces of plastic, various methods are used. Some of them are shown in the picture:
In industry, either welding based on physical methods (such as ultrasonic or laser) or mechanical joining is often used. Much less often, adhesive methods of joining (adhesives, melts or polymer solutions) are used. Such methods are used when assembling plastic showcases in stores, gluing various aquariums, wardrobe trunks and covers. But probably the most popular user of this method is a DIY-er, or in our opinion, a do-it-yourselfer. Since the days of the USSR, inventors and simply handy citizens of all stripes have glued the cases of their crafts from plexiglass and dichloroethane. With the advent of affordable 3D printers, polymer solutions have received a second life in the form of props that are created during printing and which need to be somehow removed in the finished product. It is not always possible (and advisable) to do this mechanically, so His Majesty "Plastic Solvent" often comes into play.
Note : speaking for myself, despite being able to 3D print the model, I still glue plexiglass the old fashioned way when I need to make a box or something like that (without bezier curves). At KDPV, by the way, just an example of such a “momentary! things”, which was hastily glued with a red plexiglass solution (PMMA) from a cone.
So, chemical welding of plastic is the process of combining plastic surfaces softened with a solvent. The solvent temporarily transfers the polymer to a "rarefied" state at room temperature. When this happens, the polymer chains are free to move in the liquid and can mix with other such dissolved chains. After some time, the solvent, due to diffusion and evaporation, will penetrate through the polymer and migrate into the environment, while the polymer chains will become denser (~packed) and lose their mobility. A frozen ball of tangled polymer chains is the weld in this type of welding. Graphically, the mechanism of the plastic dissolution process is shown in the picture below:
Typically, normal dissolution includes a solvent penetration step, a polymer swelling step, and a polymer diffusion step into the solvent. The initially vitrified polymer contains many microchannels and holes of molecular size (according to the so-called infiltration layer).
Upon contact with the solvent, the latter fills these channels and holes and starts the diffusion process (no new channels are formed). Schematically, such a surface layer of a dissolving polymer looks like this (roughly speaking, “glue” = a gel-like mass, what is located in the middle between a solid polymer and a liquid solvent):
With the mechanism, I hope everything is more or less clear, it is time to move on to the specifics of “what and what”. In the theoretical part, I briefly tried to explain how the solvent screening process works for a particular type of polymer. Those. there is as yet no universal and comprehensive table for the dissolution of polymers.
And this topic is relevant. Confirmation is the fact that quite often on the pages of various thematic resources (DIY, 3D, amateur radio, etc.) questions like “how to process” / “how to glue” / “how to dissolve” one or another type of plastic appear with noticeable frequency . Interestingly, in most cases, answers are given by people with polymer chemistry (Navy) acquaintances, apparently rather weakly. As a result, there is even more confusion and "room for creativity" of all kinds of amateurs, sellers and other obscurantists. Traditionally, innocent users lose money and time. So, look at the table below and wind it on a mustache.
The dark square in the table at the intersection of the "polymer" - "solvent" lines indicates that it is possible to carry out chemical welding using these components.
: a square at the intersection of "ABS" - "acetone" - with the letter H , because it was the habra community that convinced me that ABS glues mainly with acetone (my acetone dissolved ABS, but then glue nothing worked with this solution, because it crumbled).
If there is usually no problem with the presence of plastic, then quite often there is a problem with the presence of the desired solvent. Everyone gets out to the best of their ability - someone simply orders the necessary solvents, someone is looking for them at a flea market, and someone is trying to pick up empirically from what is sold in stores. Under the spoiler, if anything, the composition of commercially available solvents for varnishes and paints (taken from chemister).
Where can I get welding electrodes for plastics?
Solvents:
Solvent 645: toluene 50%, butyl acetate 18%, ethyl acetate 12%, butanol 10%, ethanol 10%.
Solvent 646: toluene 50%, ethanol 15%, butyl acetate (or amyl acetate) 10%, butanol 10%, ethyl cellosolve 8%, acetone 7%.
Solvent 647: toluene (or pyrobenzene) 41.3%, butyl acetate (or amyl acetate) 29.8%, ethyl acetate 21.2%, butanol 7.7%.
Solvent 648: butyl acetate 50%, toluene 20%, butanol 20%, ethanol 10%.
Solvent 649: xylene 50%, ethyl cellosolve 30%, isobutanol 20%.
Thinner 650: xylene 50%, butanol 30%, ethyl cellosolve 20%.
Thinner 651: white spirit 90%, butanol 10%.
Solvent KR-36: butanol 80%, butyl acetate 20%.
Solvent R-4: toluene 62%, acetone 26%, butyl acetate 12%.
Thinner P-10: xylene 85%, acetone 15%.
Solvent P-12: toluene 60%, butyl acetate 30%, xylene 10%.
Solvent P-14: cyclohexanone 50%, toluene 50%.
Solvent P-24: solvent 50%, xylene 35%, acetone 15%.
Solvent R-40: toluene 50%, ethyl cellosolve 30%, acetone 20%.
Solvent P-219: toluene 34%, cyclohexanone 33%, acetone 33%.
Solvent R-3160: butanol 60%, ethanol 40%.
RKCH solvent: xylene 90%, butyl acetate 10%.
RML solvent: ethanol 64%, ethyl cellosolve 16%, toluene 10%, butanol 10%.
Solvent RML-315: toluene 25%, xylene 25%, butyl acetate 18%, ethyl cellosolve 17%, butanol 15%.
Solvent RS-1: toluene 60%, butyl acetate 30%, xylene 10%.
Solvent RS-2: white spirit 70%, xylene 30%.
RFG solvent: ethanol 75%, butanol 25%.
RE-1 solvent: xylene 50%, acetone 20%, butanol 15%, ethanol 15%.
Solvent RE-2: solvent 70%, ethanol 20%, acetone 10%.
Solvent RE-3: solvent 50%, ethanol 20%, acetone 20%, ethyl cellosolve 10%.
Solvent RE-4: solvent 50%, acetone 30%, ethanol 20%.
Solvent FK-1 (?): absolute alcohol (99.8%) 95%, ethyl acetate 5%
Thinners:
Thinner for water-based varnishes and paints: butanol 62%, butyl cellosolve 38%.
Thinner M: ethanol 65%, butyl acetate 30%, ethyl acetate 5%.
Diluent P-7: cyclohexanone 50%, ethanol 50%.
Thinner P-197: xylene 60%, butyl acetate 20%, ethyl cellosolve 20%.
Thinner WFD: toluene 50%, butyl acetate (or amyl acetate) 18%, butanol 10%, ethanol 10%, ethyl acetate 9%, acetone 3%.
Thinner RKB-1: xylene 50%, butanol 50%.
Thinner RKB-2: butanol 95%, xylene 5%.
Diluent RKB-3: xylene 90%, butanol 10%.
Thinners for electric paint:
Thinner RE-1V: solvent 70%, butanol 20%, diacetone alcohol 10%.
Thinner RE-2V: solvent 60%, butyl acetate 20%, ethyl cellosolve 20%.
Thinner RE-3V: solvent 50%, butanol 30%, ethyl cellosolve 20%.
Thinner RE-4V: ethyl cellosolve 50%, solvent 50%.
Thinner RE-5V: xylene 40%, cyclohexanone 25%, ethyl cellosolve 25%, butanol 10%.
Thinner RE-6V: solvent 50%, xylene 35%, diacetone alcohol 15%.
Thinner RE-7V: xylene 60%, butyl acetate 25%, diacetone alcohol 10%, cyclohexanone 5%.
Thinner RE-8V: butanol 75%, xylene 25%.
Thinner RE-9V: solvent 50%, butyl acetate 30%, ethyl cellosolve 20%.
Thinner RE-10V: solvent 40%, butanol 40%, ethyl cellosolve 20%.
Thinner RE-11V: xylene 40%, ethyl cellosolve 30%, butyl acetate 20%, cyclohexanone 10%.
Thinners:
Thinner DMZ-R: butyl acetate (or amyl acetate) 39%, toluene 30%, ethyl acetate 16%, acetone 15%.
Thinner R-5: xylene 40%, butyl acetate 30%, acetone 30%.
Thinner R-6: pyrobenzene 40%, ethanol 30%, butanol 15%, butyl acetate 15%.
Thinner R-60: ethanol 70%, ethyl cellosolve 30%.
Thinner RVL: chlorobenzene 50%, ethyl cellosolve 50%.
Note:
I will add a few words about polymers that are not included in the table. Of course, this is the favorite "folk" filament - PLA , which dissolves best in polar aprotic solvents: pyridine, N-methylpyrrolidone, ethyl acetate, propylene carbonate, dioxalane, dioxane, dichloromethane, chloroform, acetone (?? - depends on the manufacturer of the PLA filament and the "additives" contained inside, this the same is true for other polymers), nitrobenzene, acetonitrile, dimethylacetamide, etc. A promising 3D polymer PEEK (aka polyetherketone) is remarkably soluble in 4-chlorophenol (a harder version is a mixture of 80% chloroform and 20% dichloroacetic acid). Chlorophenols (not only 4-, but also 2-chlorophenol) can also dissolve the widely used and beloved PET . At the request of readers, I will also mention a fairly new polymer of the PET series, the so-called PETG (polyethylene terephthalate glycol). Like its older brother, this polymer is resistant to a number of commonly used components available, soluble only in HFIP (hexafluoropropanol). Soft and pliable TPU (thermoplastic polyurethane), like other polyurethanes, can be dissolved in N,N-dimethylformamide (DMF), tetrahydrofuran, ethyl acetate, cyclohexanone, dimethylacetamide. By the way, mounting foam is also polyurethane. I didn’t look at what is in the composition of special liquids for washing foam guns, but I suspect that some of the components mentioned are definitely there. Polymer PCL (polycaprolactone) dissolves in anisole, 2,2,2-trifluoroethanol, N,N-dimethylformamide, methylpyrrolidone, tetrahydrofuran, dichloromethane, acetone, chloroform and DMSO (dimethyl sulfoxide, also sold in the Dimexide pharmacy).
PDMS (polydimethylsiloxane) widely used for prototyping (especially in scientific institutions related to micro- and nanofluidics) is dissolved with glacial acetic acid. By the way, many other silicones have similar properties, ranging from two-component construction silicones to those on which stickers with prices are glued (therefore, washing off the glue residue from the price tag with ABS plastic, for example, will be most productive using some kind of vinegar essence). And finally, a little exotic. EVA (ethylene vinyl acetate), PP (polypropylene), PE (polyethylene, LD/HD) are soluble in 1,2,4-trichlorobenzene, and PVP (polyvinylpyrrolidone) in dimethylacetamide.
Solvent Safety
Since solvents, to put it mildly, are not the aroma of cherry blossoms for you, then the issue of safety when working with them is on the agenda. It is sad to see how young guys without any means of protection sometimes work with acetone, some with chloroform, and some even with benzene. And the rules of safety, they are known to be "written in blood"...
The main ways of getting solvents into the human body (and their vapors) are through the respiratory organs and through the skin. I don’t consider any deviations (like ingestion), because a person in their right mind will never drink benzene. The mentioned reagents have a predominantly narcotic effect, have a pronounced irritant effect on the mucous membranes of the upper respiratory tract and the conjunctiva of the eye, and a moderate irritant effect on the skin. The best protection against them is to work in conditions of supply and exhaust ventilation, in special boxes. If it happens in specialized workshops or laboratories, then most often there is already a fume hood.
If it is impossible to arrange the necessary ventilation, those working with organic solvents are provided with personal protective equipment: respirators, gas masks, oxygen-insulating devices, etc. (depending on vapor concentration). In general, solvent vapors are remarkably adsorbed by activated carbon (and many other sorbents). It is not for nothing that some solvents were actively used to assess the sorption capacity of a material (the so-called “desiccator method”). I personally "had the honor" to check the sorption capacity of coals by their absorption of carbon tetrachloride CCl 4 . Most of the vapors will be able to hold a gas mask with a class A box or a respirator mask with a similar filter cartridge. Like this:
It is important to look in the description for something like " protects against vapors of organic compounds (gasoline, kerosene, acetone, benzene and its homologues, xylene, carbon disulfide, etc.), phosphorus and organochlorine pesticides, dust, smoke, fog ". But for such a mask, it is also desirable to have sealed glasses, the glasses of which are rubbed against fogging with a solution containing gelatin, sugar and water in a ratio of 2:20:50
. It is better, of course, if you have money, to immediately take some kind of industrial filtering gas mask or a protective panoramic mask and kill two birds with one stone (=save on glasses).
My favorite protective equipment (after thrust)
The already mentioned panoramic mask (excellent visibility after a gas mask from the USSR)
She, but on the other side
And my pride, a filter box with protection against mercury vapor.
After the respiratory organs, the weak point when working with solvents is exposed skin. If the face is hidden under a gas mask, hands remain. Many solvents are perfectly absorbed through the skin (toluene, tetrahydrofuran) and can cause severe dermatitis and eczema (benzene, methylene chloride, chloroform, etc.). Therefore, the best option would be a) the use of protective gloves (gloves made of polyvinyl alcohol - for organochlorine, all others, like latex or nitrile - are suitable only for alcohols, ketones), b) the use of special protective ointments and pastes.
Addition: hidden under the spoiler are tables of resistance of the material of protective gloves to various solvents, found by Kriminalist, for which many thanks to him. Highly recommended for viewing before buying "protective equipment"
Resistance of gloves to solvents
Table No. 1 - simpler (clickable)
Table No. 2 - more serious (everything is clickable)
When working with aromatic solvents (toluene, benzene, solvents, xylenes), pastes are used: IER-1, HIOT-6, PM-1, YALOT. When working with naphthenic, paraffinic and mixed solvents - YALOT, HIOT-6, IER-1. The compositions of these time-tested ointments (often referred to as "biological gloves") are shown in the picture below.
Well, just a few words about clothes. Under normal conditions, it makes no sense to use something extraordinary like a military chemical protection suit. Overalls (dressing gown) made of cotton fabric are quite enough to protect the body. In the case of particularly aggressive organochlorines or aromatics, an apron / cape with PVC / PVA or rubber / neoprene coating is added to this.
Note: in Europe there is even a special organization ECSA - E uropean C chlorinated S olvents A ssociation (European Chlorinated Solvents Association), which issues an annual bulletin detailing the necessary protective equipment when working with such solvents, materials, tools, etc.
Summing up, we can say that if the described rules are followed, working with solvents will be not only interesting, but also safe. On this I take my leave, with solutions of polymers it is finished.
P.S. Under the spoiler is a table with MPC / description of the physiological effects of common solvents. Taken from reference book Drinberg S.A. Solvents for paints and varnishes for 1986. So read on, but check for the fact of compliance with modern realities (in terms of the accuracy of the MPC, it is unlikely that it could increase, but it will decrease completely).
Important! if you did not find your solvent in the table, I strongly recommend using the TOXNET database (Hazardous Substances Data Bank - Database of hazardous substances under the auspices of the US National Library of Medicine) and look there.
Solvents. MPC & body exposure
P.P.S. An appeal to those who ask to check the solubility of a particular plastic in solvents - after the article there is a wonderful button "Support the author". If a sufficient amount is accumulated, it will be possible to check the solubility;) Also, these issues can be resolved through the consultation system mentioned at the beginning of the article.
Important! All updates and intermediate notes from which habra-articles are then smoothly formed can now be seen in my telegram channel lab66 . Subscribe not to wait for the next article, but to be immediately aware of all research :)
Solvents for paints and varnishes: a reference guide. L.: Chemistry, 1986.
Zhilov Yu.D. Handbook of occupational health and industrial sanitation. M., Higher School, 1989.
IM Neiman Personal protective equipment at work. Profizdat, M., 1954.
Yue C.Y. The structure and strength of solvent welds between dissimilar amorphous thermoplastics. International Journal of Adhesion and Adhesives, 8(1), p. 47, 1988.
Tres P: Assembly techniques for plastics. Designing Plastic Parts for Assembly, Reference book (ISBN 1-569-
-6), Hanser Gardner Publications, Inc., 1995.
Rosato's Plastics Encyclopedia and Dictionary, Reference book (ISBN 3-446-16490-1), Carl Hanser Verlag, 1993.
Desai J, Barry CMF, Mead JL, Staceer RG: Solvent welding of ABS and HIPS: a case study in methylene chloride substitution. ANTEC 2001, Conference proceedings, Society of Plastics Engineers, Dallas, May 2001.
Warwick CM Solvent welding. Handbook of Adhesion, 2nd Edition, Reference book (ISBN 0-471-80874-1), John Wiley & Sons, 2005.
Learn more