Dissolvable 3d printing filament
PVA & Support Material - Soluble filaments for support structures
Sort byRelevanceBestsellersCustomer ReviewsPrice, Low to HighPrice, High to LowNew arrivalsHighest Discount
-
- Soluble in cold water
- Ideal support material
- Wide temperature range
-
- Water-soluble
- Excellent layer formation
- Good solubility
-
- Water soluble
- Good adhesion to different materials
-
- Higher printing temperatures
- Better in combination with technical materials
- No nozzle clogging up to 255 ° C
-
- Support material
- Fast post-processing
- For dual extrusion
-
- Water-soluble material
- Compatible with many materials
- For complex structures
-
- Good binding with almost all materials
- Excellent solubility in water
-
- Easy to use and compatible with many filaments
- Wide temperature range
- For complex models
-
- Breakaway support material
- Easy to remove
- Easy to print
-
- Easily water soluble
- Ideal for dual extruder 3D printers
- No residue after dissolving
-
- Higher thermal stability
- Ideal for dual extruder
- Cold-water soluble
-
- Soluble material
- Especially for PC, ABS and ASA plastics
- For dual extruders
-
- Soluble by use of the DSS Station
- Residue-free
All prices incl. VAT.
Soluble filaments for support
One of the main limitations of FFF 3D printing compared to other additive manufacturing technologies is the need for the printed area of each layer to be supported by a previous printed layer. This means that any part of the part with an overhang greater than 45º or any bridge longer than 10mm requires support structures.
On single extruder FFF 3D printers, the only option for generating support structures is to use the same print material as the part. These supports must be removed mechanically after printing is complete, and various strategies are employed to facilitate this, such as making these supports with low-density structures and leaving a separation layer between the support and the part. This allows the supports to be removed manually without the use of tools, although the surface finishes of the surfaces in contact with the supports are often poorly finished.
Image 1: Supports on 3D printed parts.
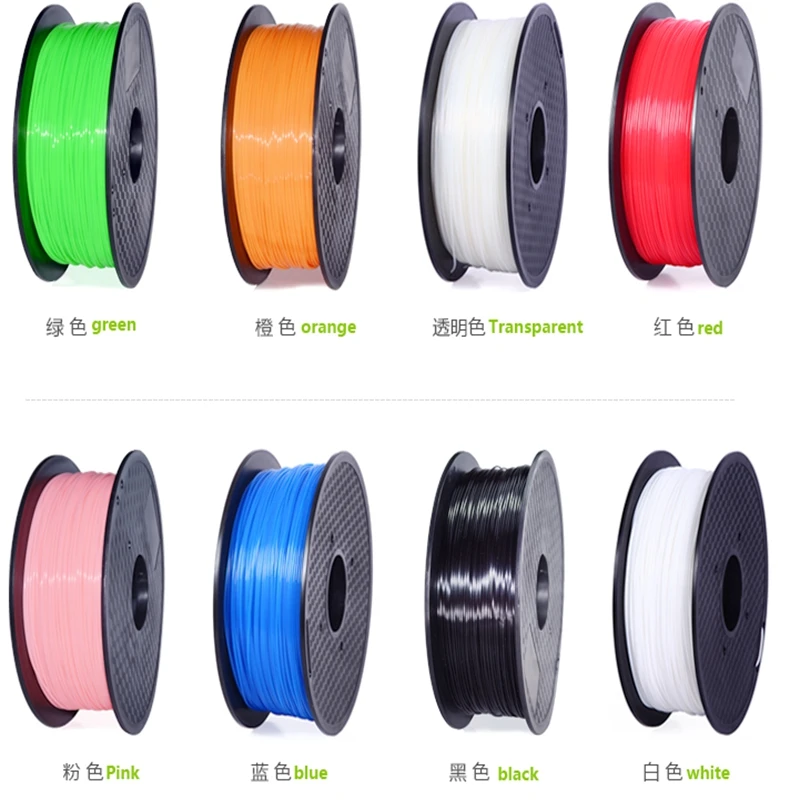
On FFF 3D printers with dual extruders, the range of options expands, as it is not necessary to use the same material for the part and for the supports. This opens the door to using materials that are soluble in solvents that do not dissolve the material of the part. This makes it possible to use dense supports in contact with the workpiece that guarantee an excellent finish on the contact surface.
Image 2: Raise3D Pro2 dual extruder. Source: Raise3D
There are many different soluble support filaments available, but they are not all the same, nor do they all have the same compatibility. When selecting a soluble carrier material, it is important to consider a number of characteristics to ensure compatibility with the printing material used. These characteristics are:
There are currently three main types of soluble support materials:
- Organic solvent soluble filaments
- Water soluble filaments using an activator
- Water soluble filaments
SOLUBLE FILAMENTS IN ORGANIC SOLVENTS.

These are materials with similar properties to the material used in the part but which can be dissolved in a solvent that does not attack or dissolve the material that they complement.
There are currently not many options for this type of filament, mainly due to two problems: on the one hand, materials with similar physicochemical properties that make them compatible with each other also generally behave in a similar way with most solvents, making it difficult to find a suitable solvent. On the other hand, many of these organic solvents are highly toxic or not accessible to most users and require specialised waste treatment.
Image 3: D-Limoneno. Source: Filament2print
The most commonly used filament of this type is HIPS, whose properties make it compatible with most ABS and ASA-based materials. In addition to having similar thermal properties, it has good adhesion to ABS and ASA. It is currently one of the most widely used support materials, not only because of its compatibility with ABS, but also because of its low cost and because it is soluble in D-Limonene, an accessible, inexpensive and low-toxicity organic solvent.
WATER-SOLUBLE FILAMENTS THROUGH THE USE OF AN ACTIVATOR.
These are ATP-based polymers (acrylate terpolymers). These materials have the characteristic of being soluble in alkaline solutions. They have excellent compatibility with ABS and ASA based materials, and can also be used with polycarbonate (although their compatibility is somewhat lower).
They are not directly soluble in water, as they require water to have an alkaline pH, so the use of a buffer activator, such as 3DWash, is necessary.
Image 4: 3DWash. Source: Traxer
They are a perfect alternative to HIPS, not only because they do not require the use of organic solvents, but also because they are filaments developed and additivated specifically for use as support material, so they generally dissolve more quickly and leave less residue on the part.
Video 1: Video presentation of PolyDissolve S2. Source:Polymaker
Some representative filaments are PolyDissolve S2 and Z-SUPPORT ATP.
WATER-SOLUBLE FILAMENTS
One of the main objectives of manufacturers has been to obtain support filaments soluble directly in water. This is because it does not require organic solvents or alkaline solutions, making it the safest and most accessible alternative for most users.
This is why it is the category with the widest variety of different materials, and with options compatible with a wide range of filaments.
Within the water-soluble filaments, two types can be distinguished:
Water soluble filaments compatible with low temperature materials: These are filaments based on PVA (polyvinyl alcohol) or BVOH (butenediol vinyl alcohol). Both materials have excellent compatibility with PLA and can be used with PA (although their compatibility is not as good). BVOH can be considered as an evolution of PVA and has a number of advantages over PVA, such as better compatibility with PETG or even with some flexible filaments and a higher dissolution rate in cold water. Some PVA filaments are LAY-PVA or PVA Raise, while Mowiflex or Z-SUPPORT Premium are based on BVOH.
Video 2: Comparison between PVA and BVOH. Source: BCN3D
Water-soluble filaments compatible with high-temperature materials: These are the most advanced support filaments currently available. They are made up of a material composed of a blend of a water-soluble polymer (similar to the previous ones) and a sugar, generally trehalose, a polysaccharide that is rapidly soluble in water and with high thermal stability. The proportion between polymer and sugar, together with the use of certain additives specific to each manufacturer, makes it possible to obtain different formulations of water-soluble materials that are compatible with materials in a wide range of temperatures, from ABS to PEEK or ULTEM.
Image 5: PA-CF part with supports made of Aquatek X1. Source: 3DXTech
Some filaments such as Aquasys 120 or Aquatek X1 are compatible with PLA as well as ABS, ASA, PA, PETG or certain flexible filaments. Aquasys 120 can also be used with PC or PP. In addition, both materials can withstand chamber temperatures of up to 120°C and are therefore also suitable for use in industrial printers.
One step above is Aquasys 180, probably the most advanced and most compatible support material available today. As well as being compatible with the same materials as Aquasys 120, it can be used with PEKK, PEEK, ULTEM and PPSU as it can withstand chamber temperatures of up to 180°C.
Image 6: Part with supports manufactured in Aqusys 180. Source: Infinite Material Solutions
However, the main advantage of this type of filaments (their high solubility in water) is also their main disadvantage, as they are highly sensitive to environmental humidity. This makes it necessary to keep these filaments in special containers, both during storage and use. Moreover, as these filaments absorb moisture, their adhesion worsens and the risk of clogging increases.
HOW TO CHOOSE THE MOST SUITABLE SOLUBLE FILAMENT.
When selecting the most suitable soluble filament, it is necessary to analyse the material to be complemented.
-
ABS/ASA: In general it is advisable to avoid the use of HIPS as it involves the handling of organic solvents and generates waste that cannot be disposed of directly.
In this case, water-soluble ATP filaments with the use of an activator are the most recommended option. They have excellent compatibility with these materials and have a low sensitivity to moisture, making them easier to store and use, as well as minimising the risk of printing failure.
-
PLA: The materials with the best compatibility with PLA are those based on PVA and BVOH. Within these, BVOH-based materials are less sensitive to moisture, although in general PVA-based materials are slightly cheaper.
-
PETG/PA: Although it is possible to use PVA and BVOH as support material with PETG and PA, their compatibility is not particularly good. In this case, the best option is water-soluble filaments compatible with high temperature materials such as Aquasys 120.
-
Flexibles: Compatibility between support and flexible materials has never been particularly good.
It is possible to use BVOH or materials such as Aquasys 120 with some flexible filaments, however it will be necessary to test each flexible filament to verify compatibility.
-
If you usually use soluble supports with different materials, the ideal option is to use a single material that is compatible with all materials, such as Aquasys 120 or Aquatek X1, rather than having a different one for each material.
Although soluble filaments are often referred to as a single group, they actually consist of different materials, with their own very specific characteristics. Nowadays it is possible to find high quality soluble filaments compatible with almost any material on the market, from PLA to PEEK.
Subscribe to our monthly newsletter and you will receive every month in your email the latest news and tips on 3D printing.
* By registering you accept our privacy policy.
Using Dissolvable Filament to Create Supports
Using Dissolvable 3D Printing Filament is an easy and effective way to create support structures for your 3D printed part. In this article, we'll take a look at the different types of dissolvable filaments on offer, the benefits of using them over insoluble filaments, and tips and tricks for the smoothest possible printing process.
FDM 3D printing is a manufacturing technology that allows you to create parts with complex geometries that are usually impossible to obtain using traditional methods. However, when using this technology, each layer of the part requires supports, either on the structure of the part itself or on an additional support structure.
With a single extruder 3D printer, you are limited to using the base material of the printed part to create the support structure. Things are different with dual-extruder printers, since dissolvable filaments can be used to create support structures.
Soluble 3D Printing Filament Types
Water Soluble 3D Printing Filaments
Such materials are known for their solubility in ordinary water without any aggregates. This makes them an excellent option, as their dissolution does not pose any danger, and also does not cause any reaction to the base material of the product.
One of these materials is PVA, which is the most commonly used support material in 3D printing. BVOH is another widely used material with better material compatibility than PVA as well as faster dissolution time.
Water Soluble Chemical 3D Printer Filaments
Some industrial grade materials are not compatible with filaments such as PVA or BVO due to their chemical properties and/or heat resistance. For this reason, materials like BVOH or PVA have been designed with additional properties to make them compatible with high temperature materials such as PEEK, PEKK, PPSU, PP and others.
In order to dissolve these supports, the pH of the water must be acidic in order to break down the sugar that this type of material normally contains, as this is less dangerous than the use of solvents.
Soluble 3D Printer Filaments with Organic Solvents
These are the least used materials due to the difficulty of using organic solvents with polymers most used in 3D printing as the solvent can react with the print material and damage it.
The advantage of using these materials is their high compatibility with the construction material. The most common example is HIPS as a support material for ABS.
Insoluble and dissolvable filaments for 3D printers
Soluble filaments for support structures have advantages and disadvantages compared to using insoluble filaments:
- Easy to remove supports
- Since the supports are soluble, simply dip the model in the appropriate solvent and wait until the supports are gone. This is very useful for parts with a very complex structure.
- Improved contact surface quality
- This advantage is related to the first point; since the material is easily removed, a strong base can be created in the area where supports are required, resulting in a smooth surface without filament residue.
- Less need for post-processing of the model
- The ability to print complex 3D models with high surface quality using dissolvable filaments also reduces the need for post-processing tasks such as polishing, sanding, gluing, etc.
- Longer print times in increasing the time of 3D printing, since materials need to be changed in the process. However, there are techniques for optimizing the support structure to reduce this problem.
Tips for creating support structures with dissolvable filaments
By changing some settings in your slicer, you can get solid supports to improve the quality of your 3D model.
Strengthening the Supports
It is quite common to create thin supports for very thin parts of a model, however they are not strong and tend to break during the printing process. To increase their durability, you can adjust the following support configuration options:
Horizontal Support Extension: Increases the overall thickness of the support, allowing the tower to be thicker and stronger.
Avoid breakage of supports during printing
The thickness of supports is equal to the diameter of the hot end, so they are usually quite fragile and can break during printing. By changing the pattern and other parameters, the strength can be increased:
- Support pattern: Patterns such as grid and triangle are quite resistant to tearing during printing. It is recommended to print such patterns only on soluble material, as they are quite difficult to remove.
- Supports printing speed: If the supports are printed too fast, there is a risk of breaking the structure. Reducing the speed avoids vibration or damage to the structure as the head passes.
Improving the quality of the surface of the model
The quality of the contact surface depends on the distance Z from the support pattern, the direction of the upper and lower perimeter lines and the amount of material holding the base of the model. Changing these parameters can improve the quality of the surface, but will complicate the process of extracting supports.
- Density of supports: The higher the density, the better the model will hold and therefore the surface finish will improve.
- Top/Bottom Line Direction: Changing the direction of the perimeter pattern helps hold the bottom layer of the model, as it allows the support and the perimeter pattern to intersect better.
- Support Pattern and Top/Bottom Pattern: The support and perimeter patterns affect how the support model attaches, ideally the patterns should overlap as often as possible to better secure the first layer.
Always remember that it is important to keep filaments in a dry environment, as soluble materials readily absorb moisture and can cause printing problems. Materials such as PVA and BVOH can be dissolved in normal water. This water can also be heated to shorten the removal time of supports.
We hope you follow our advice and recommendations to improve the surface quality of your 3D printed parts and make the process faster and more efficient.
We will keep you updated with the latest news!
Your team IGO3D Russia
Our groups on social networks:
Vkontakte
Telegram
Youtube
Soluble thread for support from Verbatim / 3D Seal / 3DMAG.org
29 Verbatim, which actively entered the 3D printing market back in 2014, never ceases to please with its new products. More recently, butene vinyl alcohol copolymer (BVOH) filament has been released as an effective water-soluble solution for printing complex parts requiring support structures.
These filaments have rightfully become one of the most important filaments in the world of 3D printing, as they allow manufacturers to produce parts with complex projections and geometries with much greater efficiency. The novelty is made for 3D printers with dual extrusion, it features a high feed rate and a short dissolution time. Dry figures: the filament extrusion speed is 30mm/sec. Recommended printing temperature: 200-230 degrees Celsius, the temperature of the heated "platform" - 70-80 degrees. Easily dissolves when placed in water at a ratio of 1 to 20.
Naturally, the thread showed its best properties with the products of the manufacturing company. Suitable for all dual extrusion 3D printers, such as the popular Ultimaker 3. The developers are confident that their BVOH filament will be useful to companies around the world due to its efficiency (dissolves faster than PVA analogues). One diameter version is currently available - 1.75 mm. At the end of September, it is planned to release a 2.85 mm thread.
Related posts:
-
just4fun
3d printing → Facilan C8 is a new print material that could outshine PLA and ABS 0 - Learn more