Delft 3d printing
3Delft | High Quality 3D Printing
Scroll
Develop your ideas with us and receive perfect fitting 3D printed parts.
Anywhere from low to ultra high resolution and possible to ship anywhere.
Get Quote
PLA printed gear and impeller
Wood filament
PLA with movable parts
PLA used for mechanical purpose
Flexible SLA resin
SLA print with support
This is the 3Delft promise.
At 3Delft we strive for the best quality and fastest turnaround that we can deliver.
We pay close attention to our customers and their projects, and are always happy to go the extra mile for your comfort.
It’s entirely up to you how much input you get from us. We offer anything from quick, no-nonsense production to detailed consulting and design for the parts that you want.
We guarantee that all parts we print for you will live up to the highest 3D-printing standards, thanks to the technical expertise of our team, which they owe to their studies in engineering.
Are you getting as excited as we are?
Contact us right away and let’s transform your ideas into reality!
Services
Our modeling and 3D printing capabilities.
We do our best to provide every service with the highest efficiency, working quickly on our designs, and providing helpful counsel as soon as possible.
We strive to work as sustainably as we can, saving energy and recycling our waste from rejected prototypes and tests.
Modeling
Realize ideas with us.
Learn more
3D printing with FDM
Quick. Simple. Low-cost.
Learn more
3D printing with SLA
High-detail. Strong. Smooth.
Learn more
Ready to start rapid prototyping?
Get your ideas developed and receive perfect fitting 3D printed parts. Contact us to find out in which way we can help you with your project.
Get quote
Our team
We provide knowledge with passionate TU Delft students.
Jeroen van Pelt
Chief Business Development
Master Student High Tech Engineering
TU Delft
+31 6 40080182
Casper de Hoog
Chief Finance
Student Mechanical Engineering
TU Delft
+31 6 40199887
Constantijn Zevenbergen
Chief Operations
Master Student Electrical Power Engineering
TU Delft
+31 6 25534682
About 3Delft
3Delft is a startup founded by passionate TU Delft students who want to do more than just studying. Our main goal is to make a place for ambitious students in which technical and entrepreneurial skills can be developed. Many technical students have the intention to begin a startup, but don’t have enough resources or the perfect business plan to actually start. 3Delft provides building blocks for entrepreneurial improvement such as management, marketing, finance or customer service. The technical building blocks we provide cover subjects like integrated design, 3D printing and material sciences. By targeting technical companies in the region of Delft, we are stimulated to be truly innovative. The fact that our products will have a real use makes our work even more meaningful to us. That is how we make the best of our student years.
Trusted by
Stories — 3Delft | Rapid prototyping with expertise.
Scroll
Our proud partnerships and projects.
Improving the inspection of medical containers
Patient safety is one of the most important aspects in production of medicine. According to international standards, medical containers such as syringes, ampoules and vials should be 100% visually inspected. This action is mandatory to make sure containers do not contain defects or foreign particles.
Read More →
Printing a customizable boardgame
Qbuss is a 3-dimensional, artistic and customizable boardgame for 4-players designed by W.J.Jongeneel in collaboration with 3Delft. The game focuses on pathfinding to score points, which can be used to obscure the opponents gameplay and fortify your own.
Conventional mould-fabrication is expensive and unapproachable for hobby-conceptualization. With 3D printing on the rise, ideas that couldn’t be made before can now become your reality. 3D printing production is quick, easy and cost-effective.
Read More →
Providing tools for underwater robot innovation
One of the ways to minimise fuel consumption of freight ships is to keep a very clean hull, because a foul hull creates much more drag in the water, resulting in a much less efficient use of the engine power. In order to ensure the best circumstances for ships that pass through the port of Rotterdam, FleetCleaner offers an inspection and cleaning service with underwater robots.
Read More →
Making connections and learning from Dutch entrepreneurs
Last week, on the 16th of March 2021, We were very proud to be a part of the Entrepreneurship Day Delft! It was a great opportunity for us to learn from some very successful stories of other businesses; to present our company and what we want to do to a greater audience, and to get to know some interesting people!
Read More →
Eradicating insects with drones
Since the organic crop demand is rapidly growing, pesticides are less favorable to use against insects. A new automated solution has to take over from these pesticides. A Delft startup called PATS Drones solves this problem by using bat-like drones to automatically control insect populations.
Read More →
Innovating the pathology lab of Reinier de Graaf hospital
Over the past few months, 3Delft has been proudly working together with the pathology laboratory of Reinier de Graaf hospital in Delft. By making solutions for the transportation and storage of sampled tissues, the lab is now safer, user-friendlier and more efficient.
Read More →
Revolutionizing greenhouses with data and robotics
As greenhouses keep on getting larger and larger, growers are facing more difficult challenges. Monitoring hectares of plants combined with controlling diseases and pests is highly labour intensive. Applied Drone Innovations (ADI) develops powerful solutions for this. They make greenhouse monitoring systems, collect valuable data which they also process to increase crop yields and quality while reducing operational costs.
Read More →
Free tablets for student houses!
A group of students from Delft University of Technology have developed the first digital-in-home advertisement platform called Turff. It is a tablet with smart features such as a financial accounting system, a list of who will be eating at home and more. In exchange, the tablet will show screensavers with advertisements when it is not used.
Read More →
Giving the world a helping hand
Alex Lamp is a volunteer of the e-NABLE network. She gives 3D-printed hands to those who need them. Here at 3Delft, we like to support such communities. That is why we spread awareness to help Alex grow her network. Here is her story:
Read More →
Vattenfall Solar Team
The Vattenfall Solar Team is aiming to build world’s fastest solar car to win the Bridgestone World Solar Challenge 2019. We like to see how they show the possibilities of high-end technology and sustainable energy. Their next creation will be NunaX. We are proud to contribute to NunaX by providing lightweight 3D printed parts, which are optimized by combining our knowledge of production and material sciences.
Read More →
The schiphol project
Master Graduate Sian Wong designed this building for his graduation thesis. The woody auditorium and the gray mechanical system are 3D printed by 3Delft. We congratulate him on achieving a 9.0 / 10.0 for this project.
Read More →
Stieltjesweg
The Stieltjesweg building is a student housing on the campus of the TU Delft. Our modeling experts recreated the building with a CAD software. Then the model was 3D printed. Now students living at the Stieltjesweg can physically show their friends and families where they have lived in their college days.
Read More →
Projectgroup WB08
The WB08 project group at TU Delft has created a desktop CNC machine that consists of customized 3D printed components. We are proud of their result and we wish them success with the project and the rest of their studies.
Read More →
Why focus on sustainability?
At 3Delft we want to contribute to the future. We look for interesting and innovative projects that improve the world around us, so that we might enjoy the fruits of those innovations further down the line. We believe that building a future full of opportunity and progress if grounded on a sustainable foundation, where we use our resources responsibly and sparingly, save energy where possible and take care of our own waste. The world is growing towards that sustainable future, and that’s why we want to start with that philosophy early on. Not only so that we can make our company future-proof, but also to show that we are always looking forward.
What can we do?
There are many ways to improve the sustainability of our company, and we ultimately strive for an ideal situation in which we waste nothing. So far these are the steps that we have taken:
We always strive to minimize the use of plastic we need need to achieve great quality prints.
3D printing is a technology that is becoming ever more sophisticated, which means that the right printers can very effectively use little filament for good result. We never let our saving mind-set get in the way of quality, but we do take the time to ensure that no unnecessary plastic is used.
We collect and upcycle all the failed prints and remaining filament we have from the FDM printers.
PLA is a widely used bioplastic for FDM printing, but it’s difficult to recycle (although it can be composted in the right conditions). We have looked around us and found a colleague at MTB3D who shares our ambitions for reusing the waste product. Together we collect all our waste PLA and melt it into large discs that can be used for decoration or production of new useful products.
We return our empty filament spools to our supplier.
For FDM printing, we use big spools of filament that are made of black plastic that is very hard to recycle. By returning the spools to our supplier we ensure that we don’t have to throw them away with the regular plastic, and they are used again.
We hardly ever use heating in our office and always turn off all appliances that are not operational.
With several printers running, our office is never more than chilly, but that’s nothing that a sweater can’t fix. We save energy by turning off the radiator and turning off all lights and appliances whenever we’re not in the office, which means saving a lot of energy when working from home.
Students at Delft University of Technology have developed a way to 3D print flexible materials
This technology would have significant potential for 3D printing clothes, shoes and many other products. Ben Kromhout and Lucas Lambrichts, students of the Conceptual Design Technologies course at the Delft University of Technology in the Netherlands, have developed an innovative way to 3D print flexible materials. They do not deny that hard-soft 3D printing is possible with expensive industrial equipment – however, the students decided to achieve the same effect on an affordable consumer 3D printer, in this case, the Ultimaker 2.
Initially, students were inspired to produce flexible yet rigid objects using a conventional 3D printer by a project on Instructables that detailed how to make a double-curved tree. The project used special schemes to optimize the material, and the students decided to apply the same method to create a flexible material using 3D printing. To turn the schematic into a 3D model, the team used Illustrator and SolidWorks to create multiple prototypes of varying sizes.
Each prototype uses two variables, each of which can be modified to test the flexibility of the resulting material. The ratio of circuit cells and voids between lines is configured differently in each prototype, while the thickness of the printed material remains unchanged for the purity of the experiment. In total, the developers tested four combinations of variables: the first model used small cells and small voids, the second used small cells and large voids, the third used large cells and small voids, and the fourth used large cells and large voids. The total size of the model was 95x95 mm, void size before scaling - 0.7 mm and 0.35 mm. The scales of the tested models are 1:1 and 1:1.36 (19 and 14 cells, respectively). The thickness of the material is 1 mm.
When making the first and third models, which use smaller voids, the students encountered some difficulties. Due to the insufficiently high resolution, the 3D printer was unable to print small elements of the model without touching each other. From the test results, Kromhout and Lambrichts concluded that the most flexible model is the fourth, with the largest cells and voids. According to the students, the material printed according to this scheme almost feels like textile.
The 3D printing experiment yielded interesting results, but the developers' conclusions were limited due to the small number of models tested. The students managed to show that a flexible material can be printed from hard PLA plastic on a regular personal 3D printer. On the other hand, the lack of flexibility of the remaining models means that it is not possible to draw precise conclusions about the relationship between the scope of the scheme and the flexibility of the resulting material. Students expect other researchers to continue to work in this direction in order to expand the possibilities of materials available for 3D printing.
Dutch students create a metal 3D printer based on the Prusa i3
3D printing
Metal 3D printing remains the cream of the crop in additive manufacturing. Metal parts can achieve high levels of detail, strength and durability.
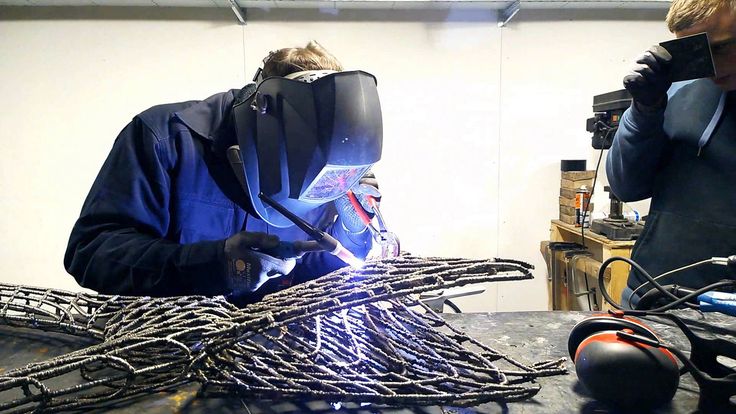
So students from the Delft University of Technology in the Netherlands are considering the use of gas shielded arc welding ("MIG welding" in English terminology) in combination with CNC machines for 3D metal printing. The very idea of using arc welding for 3D printing is not new, because there are a considerable number of industrial five-axis repair machines and experimental budget 3D printers on the market that use the same principle, but a couple of points in the new project are quite interesting.
The project is based on the work of the notorious Professor Joshua Pearce of Michigan Technological University, who pioneered the use of arc welding in combination with Rostock's widely available Delta RepRap printer. But unlike the original project, the current one uses the no less famous and much more popular RepRap with a rectangular coordinate system - the third generation Prusa (i3).
According to the developers, “This system allows the work platform to move only along the Y axis, while the electrode moves along the X and Z axes. Thus, increased build control is achieved due to reduced inertia. Another advantage of using a rectangular coordinate system is the ease of use. Delta robots require much more effort and precision in calibration.”
Another interesting point is the supply of inert gases to the construction area, which allows working with metals subject to oxidation. This solution has long been used in industrial 3D printing machines that work with titanium powders, although such devices usually use a sealed working chamber filled with gas. In this case, the older method of supplying an inert gas to the welding area with a hose is used - this method has long been used in manual and semi-automatic arc welding. The main thing is that there are no drafts.
As a result, the team hopes that the technologically simplified version, which allows achieving higher build quality, will attract the attention of enthusiasts. Of course, at the end of the work, the details of the project will be made publicly available in the hope that the community will make their own efforts to improve the method.
The team tested the prototype by printing the first models: straight lines and a vertical wall. The welding machine was set to feed the wire at a speed of four meters per minute. True, the electrode movement speed so far reaches only 300 mm/min, which is several times slower than the average desktop FDM printer.
We bring to your attention a demonstration video of the new printer:
Of course, these are only the first steps in the development of the project. In the near future, device specifications should become available, allowing the printing community to join in the further development of the technology.
Follow author
Follow
Don't want
1
More interesting articles
brtv
Loading
10/16/2022
2299
9
Subscribe to the author
Subscribe
Don't want
Hello my friend! Today I decided to assemble a simple pneumohydraulic generator or Generator...
Read more
0
Subscribe to the author
Subscribe
Don't want
Ones Technology is a research and development center under the Ministry of Industry of Turkey.