3D printing a human
3D Bioprinting of Living Tissues
Progress in drug testing and regenerative medicine could greatly benefit from laboratory-engineered human tissues built of a variety of cell types with precise 3D architecture. But production of greater than millimeter sized human tissues has been limited by a lack of methods for building tissues with embedded life-sustaining vascular networks.
Play
In this video, the Wyss Institute and Harvard SEAS team uses a customizable 3D bioprinting method to build a thick vascularized tissue structure comprising human stem cells, collective matrix, and blood vessel endothelial cells. Their work sets the stage for advancement of tissue replacement and tissue engineering techniques.Multidisciplinary research at the Wyss Institute has led to the development of a multi-material 3D bioprinting method that generates vascularized tissues composed of living human cells that are nearly ten-fold thicker than previously engineered tissues and that can sustain their architecture and function for upwards of six weeks. The method uses a customizable, printed silicone mold to house and plumb the printed tissue on a chip. Inside this mold, a grid of larger vascular channels containing living endothelial cells in silicone ink is printed, into which a self-supporting ink containing living mesenchymal stem cells (MSCs) is layered in a separate print job. After printing, a liquid composed of fibroblasts and extracellular matrix is used to fill open regions within the construct, adding a connective tissue component that cross-links and further stabilizes the entire structure.
Confocal microscopy image showing a cross-section of a 3D-printed, 1-centimeter-thick vascularized tissue construct showing stem cell differentiation towards development of bone cells, following one month of active perfusion of fluids, nutrients, and cell growth factors.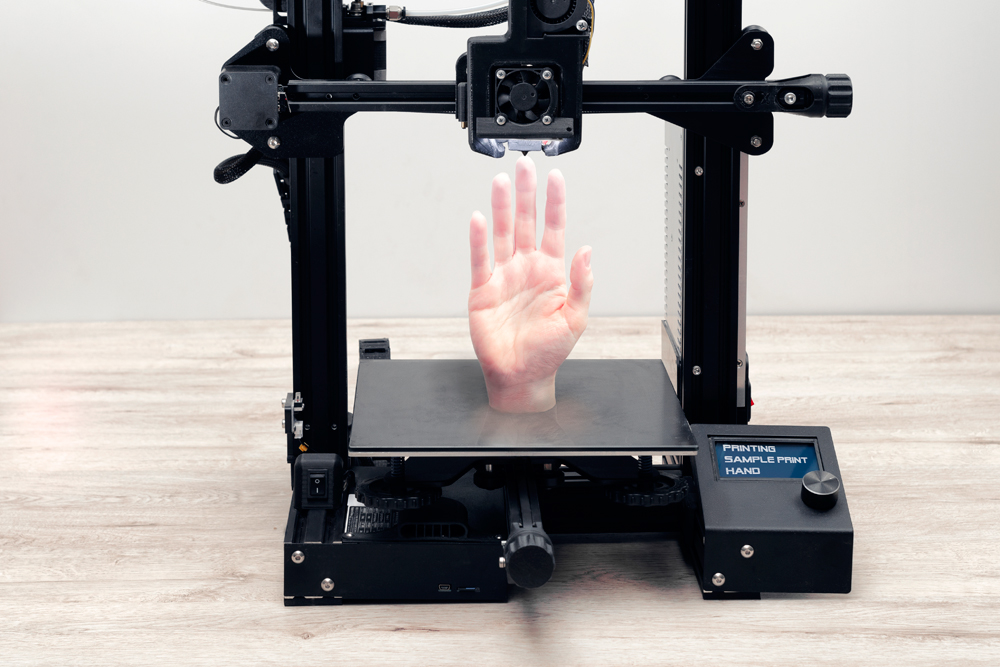
The resulting soft tissue structure can be immediately perfused with nutrients as well as growth and differentiation factors via a single inlet and outlet on opposite ends of the chip that connect to the vascular channel to ensure survival and maturation of the cells. In a proof-of-principle study, one centimeter thick bioprinted tissue constructs containing human bone marrow MSCs surrounded by connective tissue and supported by an artificial endothelium-lined vasculature, allowed the circulation of bone growth factors and, subsequently, the induction of bone development.
This innovative bioprinting approach can be modified to create various vascularized 3D tissues for regenerative medicine and drug testing endeavors. The Wyss team is also investigating the use of 3D bioprinting to fabricate new versions of the Institute’s organs on chips devices, which makes their manufacturing process more automated and enables development of increasingly complex microphysiological devices. This effort has resulted in the first entirely 3D-printed organ on a chip – a heart on a chip – with integrated soft strain sensors.
- 1/7 Cross section of long-term perfusion of HUVEC-lined (red) vascular network supporting HNDFladen (green) matrix.
- 2/7 Top-down view of long-term perfusion of HUVEC-lined (red) vascular network supporting HNDFladen (green) matrix.
- 3/7 Photograph cross section of printed tissue construct housed within a perfusion chamber.
- 4/7 Photograph cross section of printed tissue construct housed within a perfusion chamber.
- 5/7 Photograph of a printed tissue construct housed within a perfusion chamber.
- 6/7 Photograph of vasculature network and cell inks.
- 7/7 Photograph of 3D printed vasculature network (red) within Red is the
- Next
- Prev
On the Road to 3-D Printed Organs
For years, scientists have predicted that 3-D printing—which has been used it to make toys, homes, scientific tools and even a plastic bunny that contained a DNA code for its own replication—could one day be harnessed to print live, human body parts to mitigate a shortage of donor organs. So far, researchers also used 3-D printing in medicine and dentistry to create dental implants, prosthetics, and models for surgeons to practice on before they make cuts on a patient. But many researchers have moved beyond printing with plastics and metals—printing with cells that then form living human tissues.
No one has printed fully functional, transplantable human organs just yet, but scientists are getting closer, making pieces of tissue that can be used to test drugs and designing methods to overcome the challenges of recreating the body’s complex biology.
First steps
A confocal microscopy image showing 3-D–printed stem cells differentiating into bone cells
LEWIS LAB, WYSS INSTITUTE AT HARVARD UNIVERSITY
The first 3-D printer was developed in the late 1980s. It could print small objects designed using computer-aided design (CAD) software. A design would be virtually sliced into layers only three-thousandths of a millimeter thick. Then, the printer would piece that design into the complete product.
There were two main strategies a printer might use to lay down the pattern: it could extrude a paste through a very fine tip, printing the design starting with the bottom layer and working upward with each layer being supported by the previous layers. Alternatively, it could start with a container filled with resin and use a pointed laser to solidify portions of that resin to create a solid object from the top down, which would be lifted and removed from the surrounding resin.
When it comes to printing cells and biomaterials to make replicas of body parts and organs, these same two strategies apply, but the ability to work with biological materials in this way has required input from cell biologists, engineers, developmental biologists, materials scientists, and others.
So far, scientists have printed mini organoids and microfluidics models of tissues, also known as organs on chips. Both have yielded practical and theoretical insights into the function of the human body. Some of these models are used by pharmaceutical companies to test drugs before moving on to animal studies and eventually clinical trials. One group, for example, printed cardiac cells on a chip and connected it to a bioreactor before using it to test the cardiac toxicity of a well-known cancer drug, doxorubicin. The team showed that the cells beating rate decreased dramatically after exposure to the drug.
However, scientists have yet to construct organs that truly replicate the myriad structural characteristics and functions of human tissues. “There are a number of companies who are attempting to do things like 3-D print ears,” and researchers have already reported transplanting 3-D printed ears onto children who had birth defects that left their ears underdeveloped, notes Robby Bowles, a bioengineer at the University of Utah. The ear transplants are, he says, “kind of the first proof of concept of 3-D printing for medicine.”
Researchers have been using 3D-printing techniques in hopes of developing tissues that can be transplanted into humans. Some printed tissues, such as skin and bone, are already being tested in humans, while many others are early in development.
See full caption
THE SCIENTIST STAFF
Bowles adds that researchers are still “a ways away” from printing more-complex tissues and organs that can be transplanted into living organisms. But, for many scientists, that’s precisely the goal. As of February 2020, more than 112,000 people in the US are waiting for an organ transplant, according to the United Network for Organ Sharing. About 20 of them die each day.
For many years, biological engineers have tried to build 3-D scaffolds that they could seed with stem cells that would eventually differentiate and grow into the shapes of organs, but “to a large extent those techniques don’t allow you to introduce kind of the organization of gradients and the patterning that is in the tissue,” says Bowles. “There is no control over where the cells go in that tissue.” By contrast, 3-D printing enables researchers with to very precisely direct the placement of cells—a feat that could lead to better control over organ development.
Differentiation
Ideally, 3-D printed organs would be built from cells that a patient’s immune system could recognize as its own, to avoid immune rejection and the need for patients to take immunosuppressive drugs. Such organs could potentially be built from patient-specific induced pluripotent stem cells, but one challenge is getting the cells to differentiate into the subtype of mature cell that’s needed to build a particular organ. “The difficulty is kind of coming together and producing complex patternings of cells and biomaterials together to produce different functions of the different tissues and organs,” says Bowles.
To imitate the patterns seen in vivo, scientists print cells into hydrogels or other environments with molecular signals and gradients designed to coax the cells into organizing themselves into lifelike organs. Scientists can use 3-D printing to build these hydrogels as well. With other techniques, “the patterns achieved have typically been two-dimensional,” Eben Alsberg, a bioengineer at the University of Illinois, tells The Scientist in an email. “Three-dimensional bioprinting permits much more control over signal presentation in 3D.”
So far, researchers have created patches of tissue that mimic portions of certain organs but haven’t managed to replicate the complexity or cell density of a full organ. But it’s possible that in some patients, even a patch would be an effective treatment. At the end of 2016, a company called Organovo announced the start of a program to develop 3-D printed liver tissue for human transplants after a study showed that transplanted patches of 3-D printed liver cells successfully engrafted in a mouse model of a genetic liver disease and boosted several biomarkers that suggested an improvement in liver function.
Vasculature
Only in the past few years have researchers started to make headway with one of the biggest challenges in printing 3-D organs: creating vasculature. After the patches were engrafted into the mouse’s liver in the Organovo study, blood was delivered to it by the surrounding liver tissue, but an entire organ would need to come prepared for blood flow.
“For any cells to stay alive, [the organ] needs that blood supply, so it can’t just be this huge chunk of tissue,” says Courtney Gegg, a senior director of tissue engineering at Prellis Biologics, which makes and sells scaffolds to support 3-D printed tissue. “That’s been recognized as one of the key issues.”
Mark Skylar-Scott, a bioengineer at the Wyss Institute, says that the problem has “held back tissue engineering for decades.” But in 2018, Sébastian Uzel, Skylar-Scott, and a team at the Wyss Institute managed to 3-D print a tiny, beating heart ventricle complete with blood vessels. A few days after printing the tissue, Uzel says he came into the lab to find a piece of twitching tissue, which was both “very terrifying and exciting.”
For any cells to stay alive, [the organ] needs that blood supply, so it can’t just be this huge chunk of tissue.
—Courtney Gegg, Prellis Biologics
Instead of printing the veins in layers, the team used embedded printing—a technique in which, instead of building from the bottom of a slide upwards, material is extruded directly into a bath, or matrix. This strategy, which allows the researchers to print “free form in 3-D,” says Skylar-Scott, rather having to print each layer one on top of the other to support the structure, is a more efficient way to print a vascular tree. The matrix in this case was the cellular material that made up the heart ventricle. A gelatin-like ink pushed these cells gently out of the way to create a network of channels. Once printing was finished, the combination was warmed up. This heat caused the cellular matrix to solidify, but the gelatin to liquify so it could then be rinsed out, leaving space for blood to flow through.
But that doesn’t mean the problem is completely solved. The Wyss Institute team’s ventricle had blood vessels, but not nearly as many as a full-sized heart. Gegg points out that to truly imitate human biology, “an individual cell will have to be within 200 microns of your nearest blood supply. . . . Everything has to be very, very close.” That’s far more intricate than what researchers have printed so far.
Due to hurdles with adding vasculature and many other challenges that still face 3-D–printed tissues, laboratory-built organs won’t be available for transplant anytime soon. In the meantime, 3-D printing portions of tissue is helping accelerate both basic and clinical research about the human body.
Emma Yasinski is a Florida-based freelance reporter. Follow her on Twitter @EmmaYas24.
3d printing of a person - 3d printing of figures of people on a 3d printer in Moscow
Masterpieces of fine art always amaze with filigree and liveliness of human images. It would seem that copying the human image will forever remain beyond the capabilities of ordinary people. But, nevertheless, time moves inexorably forward, sweeping away restrictions and providing opportunities.
Possibilities and advantages of the masterpiece technology
Every person on the planet is unique, therefore, any copy of a person, whether it be a statuette, a model or a portrait on paper, will also have a uniqueness. 3D printing of people is a technology that allows you to reduce the centuries-old most complex mystery of sculpture, painting, modeling of human images to a few simple manipulations with modern digital equipment.
And, let it sound a little cynical, but 3D printing of a person opens up incredible opportunities in various areas of our lives. Just imagine, the creation of sculptural copies of a person takes months, and sometimes years. The cost of such a sculpture is often simply beyond the reach of an ordinary person. And the chances of becoming a model of a talented sculptor are negligible.
On the other hand, getting your own exact copy a few centimeters in size is now not at all difficult and not expensive. Moreover, a real boom in the popularity of 3D printing is brewing in the world, which will soon create a significant alternative to photo printing and video chronicles. And it's not just about private ambitions and fun!
Spheres of demand for 3D printing technology of people
3D printing of figurines is already widespread today in:
● advertising;
● decoration of wedding celebrations;
● souvenir industry;
● prototyping of industrial and commercial facilities;
● design;
● medicine.
The noble mission of innovative technology
Moreover, the circle of people professionally interested in the service in order to develop their business is constantly growing. In addition to the persistent interest in technology, its profitability and spectacularity, 3D printing of people also serves noble purposes, for example:
● allows blind people to tactilely get acquainted with the external images of their relatives and friends, communication with which is limited to virtual space;
● allows future parents to admire their baby in the womb, not only with the help of ultrasound pictures. 3D printing of a baby figurine built thanks to innovations will allow you to get to know him visually even before he is born;
● Printing figurines on a 3D printer helps people with mental trauma and disorders to adapt to a certain social environment;
● in psychology and educational disciplines, three-dimensional models of people are involved in methods of working with children.
Steps for creating 3D copies of a person
High-quality and high-quality 3D printing of people actually requires several preparatory steps.
● In the first, a full-length 3D scan of a person is performed
● In the second, a copy of the 3D model is carefully processed
● In the third, the figure is scaled down and printed.
The technology also includes a number of post-press processing steps. Figures may require surface grinding, painting or tinting, freeing them from auxiliary elements - clamps, additional details, coating with protective varnishes, finishing agents.
Consumables and features of technological processes
Various materials are used for 3D printing of human figures and
even different equipment, technically and technologically different from each other. So, the result can be presented in plastic, gypsum, polymer mixtures. It can be single color or multicolor. Realistic or only in general terms reminiscent of the original.
Human 3D printing technologies are also different. The most popular and frequently used are two:
● layer-by-layer reconstruction of the model on an inkjet 3D printer;
● laser baking, stereolithography on a laser printer.
For the best and most accurate reproduction of the image of a person, it is advisable to use the method of layer-by-layer gluing of a cellulose-starch mixture.
The use of 3D printed human figures in the advertising industry
Of course, the advertising industry has traditionally been at the forefront of bringing innovation to its service. 3D printing of human figures has become the basis of several high-profile advertising campaigns in Spain, Germany, and the UK, during which passers-by on the streets and visitors to shopping centers were asked to quickly create their own miniature on a 3D printer.
But the scope of advertising use of this technology is much wider:
● Figures of real company employees in company uniforms can make up a static installation.
● May be part of a believable animated advertisement.
● Given as a souvenir, they will be a powerful motivation for a common cause and common success.
● 3D printing of human figures in addition to the presentation of 3D models of industrial, construction, social facilities can bring liveliness and dynamics to the presentation of projects.
● Using a 3D printer, you can create not only mini copies of real people, but also transform familiar replicated images of famous sculptures. For example, dress the Venus de Milo in the costume of a stewardess of the advertised airline, and use a mini copy of Rodin's sculpture in an advertisement for ladies' accessories.
The position of 3D copies of a person in souvenir production
A treasure trove of invaluable prospects 3D printer and human printing will bring to souvenir production. With the help of technology, you can make:
● popular interior figurines;
● intricate paperweights;
● gift personalized figurines;
● wedding souvenirs of the bride and groom;
● commemorative figurines of anniversaries and heroes of the occasion.
Variants of representation of the image in a three-dimensional miniature
When creating souvenir miniatures of people, you can most often find three directions for recreating the image:
● realistic or ordinary, the one that can be found in an amateur photo or in life;
● staged, when models are presented in fantasy, stylized images, for example, superheroes or characters from famous fairy tales, movies, literary works, comics;
● wedding, couple real or fictional image.
Bride and groom figurines - this is just the beginning!
The industry of wedding paraphernalia, in addition to commemorative figurines of the newlyweds, can use 3D printing of figurines to create original decorations for invitations, decorating a wedding cake, a festive table, use mini-copies as props for an original wedding photo shoot and video shooting of a romantic love-story.
Online services and their features
It is worth saying a few words about online 3D scanning services. This first step of 3D printing a figurine takes the least time and is the least labor intensive. The presence of many specialized applications on the network that help you scan the image yourself makes the task even easier.
Actually, the results of scanning and allow you to remotely provide services of three-dimensional modeling of a person. The more diligently the scan is made, the more similarity will be between the model and the figurine. By the way, the service of 3D printing of people can be provided not only on the basis of a scan of a real person, but also on the basis of photographs taken from different angles.
How to obtain the necessary sources for 3D printing
To recreate the image in a 3D model, try to get pictures from eight angles in a circle, where the angle step will be 45 degrees. This information will be useful to those who plan to organize a surprise related to the secret production of a mini-copy of a person on a 3D printer. And even if a spontaneous photo session provides less information about the image than a scan, the result will still be recognizable.
Our company is ready to offer all interested people 3D human printing services, as well as business cooperation in this area. Our technical equipment allows us to implement not only our own, but also third-party projects, providing a successful launching pad for your business to take off. We will be glad to assist you in creating a three-dimensional human copy and mutually beneficial cooperation.
3D human figurines • Custom made from photo
3D human figurine • Custom made from photo.
Studio of design and 3D print 3DSOL Creates exclusive
3D figures of people according to the photos sent photos for an unexpected
gift to a person to a person
to order a 3D figure on photo
9000 2 TIN 15040704444080 2 MIRS and 3D printing
3D figures of people from photo
We ran out of ideas and you don't know what to give
to a loved one? Send us a photo, according to them we will make a mini-copy of it, a 3d figurine with a portrait resemblance, which will be an unexpected surprise for a relative, friend.
icon-Phot icon-Mail
Ask a question
Portfolio
PAIRSTICS
9000 3DSOLIn several photographs, we will produce paired statuels of two loving each other, and they are presented close to their close ones. .
More
Celebrity figurines
3DSOL
Order 3d celebrity figurines for your collection. Choose a photo where you like the emotion and pose of your idol.
More details
Athletes figurines
3DSOL
a gift to someone close to you.
More details
Character figurines
3DSOL
Order a 3D figurine of your favorite character for your collection. Give your loved one a mini-copy of their favorite character.
More
Sculptural compositions
3DSOL
Order exclusive figurines, full-length 3D figures for landscaping parks, recreation areas, decoration of festive events.
More details
Hobby figurines
3DSOL
Give your loved one a 3d figurine — his mini-copy, which will remind him of his favorite pastime.
Read more
Caricature figurines
3DSOL
Caricature 3d figurine is an excellent gift solution for a loved one. This is a gift that will definitely never be forgotten and will delight every time
More details
Single figurines Pair figurines Famous people figurines Athletes figurines Character figurines Sculptural compositions Hobby figurines Caricature figurines
Photopolymer figurines
Large selection of photopolymer 3D technologies print 3D growth figures made of foam and plastic have found their application in a variety of areas: outdoor advertising, decorating cafes and restaurants, decorating shopping centers and offices, photo studios and children's entertainment centers, conducting promotions and advertising campaigns, landscape gardening and decor. »
© Sprint3d
Order a 3D growth figure
Materials for 3D printing
Reviews
The best gift is an unexpected surprise. But often the problem arises that the holiday is near, and you have run out of all the ideas and you don’t know what to give.
Design and 3d printing studio 3dSol offers an excellent option: to make exact mini copies - 3d figures of people you love based on the photos you sent.
The figurine will remain with a person for life, it will give a good mood, remind you of you and a memorable day.
We will help in its manufacture, surprise you with an acceptable price and good quality. You can order both a figure of one person and a composition of a group of people.
3d figurine from the photo is a good gift for parents on their wedding anniversary, friend, team leader.
It is better to give a single figurine to a loved one for any holiday. It will be done in an original way every year, and fix changes in a person's appearance.