Degrees in 3d printing
TOP 10 3D Printing & Additive Manufacturing University Degrees
3D printing news News TOP 10 3D Printing & Additive Manufacturing University Degrees
Published on June 13, 2019 by Jamie D.
As 3D printing and additive manufacturing become mainstream, an influx of professionals who specialise in this area will be needed. Therefore, a number of universities have already started offering additive manufacturing and 3D printing university degrees. These university degrees will become hugely useful in the future as 3D printing becomes integral to sport, design, maritime, and more. We searched for eight of our favorites offered by US and UK universities to come up with our list. The degrees are not in order of best university or 3D printing degrees.
1 – Penn State University
Penn State World Campus offers an online Master of Engineering in Additive Manufacturing and Design (AMD) in partnership with Penn State’s College of Engineering and the School of Engineering Design, Technology, and Professional Programs. This course is worth 30 credits and focuses on how additive manufacturing is transforming a variety of sectors, such as manufacturing, aerospace, medical devices and more. The course also covers rapid prototyping, and the impact that being able to create one-off models from almost any material is having. It should provide students with the necessary knowledge to grow as a leader in 3D printing and prototyping technology to accelerate industry adoption.
– You can find more information HERE.
2 – Massachusetts Institute of Technology
One of, if not the most prestigious university in the world, MIT also offers two online courses on additive manufacturing. It includes a short 5-day course which provides insight into the technology – within 5 days, participants will learn the basics of 3D printing, materials involved, operate several types of 3D printers, and gain knowledge of the multiple technologies such as FDM, SLA, SLS, etc. Another course this time 12 weeks long, is called Additive Manufacturing for Innovative Design and Production and focuses on the fundamentals, applications, and implications of printing for design and manufacturing.
– You can find more information HERE for the 5-day course and HERE for the 12-week course.
3 – Carnegie Mellon University
Carnegie is a global research university known for its world-class, interdisciplinary programs and as such it offers a Master of Science in Additive Manufacturing (MSAM) two-semester full-time degree program. It is designed to educate students in the engineering science required to understand and advance additive manufacturing. Moreover, it provides hands-on experience with designing, adapting and building parts using current AM technology by including fundamental understanding with practical instruction in the technologies of AM.
– You can fine more information HERE.
4 – Ohio State University
The Master of Global Engineering Leadership (MGEL) at Ohio State University is a minimum 33-credit degree that aims to transform engineers into exceptional leaders in their field. The curriculum includes core courses that teach leadership and management, an understanding of the business-government environment relationship, while a strong engineering is provided through the choice of a specialized technical track. One of the specialized technical tracks is additive manufacturing and includes courses in computational modeling for additive manufacturing, AM for bio-medical devices and more.
– You can find more information HERE.
5 – Purdue University
The public research university in Indiana, Purdue University, has developed its Additive Manufacturing Certification Programs to give working professionals and students an opportunity to study industry case studies and receive proper training about the rapidly industrialising AM technologies and 3D printing market. The course aims to give students and professionals fundamental knowledge of AM skills that they will be able to directly apply to their projects. They offer four certificate courses, Additive Manufacturing Essentials, Additive Manufacturing Technology & Materials, Additive Manufacturing Design and Additive Manufacturing Business & Economics.
– You can find more information HERE.
6 – Nottingham University
A well-reputed university in the UK, offer a Masters (MSc) degree in Additive Manufacturing and 3D printing. This is a 1 year course, requiring an engineering or similar degree studied at undergraduate level. The course starts in September, involving modules in additive materials, metrology, and advanced additive manufacturing techniques. Nottingham University is a member of the Russell Group, due to the high level of research funding the university receives, as well as its high achievement.
-You can find more information HERE.
7 – Sheffield University
Sheffield University in the UK, offers a Masters in Additive Manufacturing and Advanced Manufacturing Technologies. Within the Department of Mechanical Engineering, this course includes modules such as dealing with aerospace materials, principles and applications of additive manufacturing, engineering composite materials, and more. This Masters appears to cover advanced forms of engineering in addition to just the 3D process, allowing for a good holistic qualification.
– You can find more information HERE.
8 – Derby University
Derby, another UK university, has started to offer a Masters (MSc) in Advanced Materials and Additive Manufacturing. This course includes modules such as additive manufacturing processes, design and materials selection, additive manufacturing applications, and data visualisation science.
– You can find more information HERE.
9 – University of Central Lancashire
The University of Central Lancashire offers a master program (MSc) in Additive Manufacturing for 1 year full-time or 2 years part-time. Graduates will have access to the Additive Manufacturing lab, housing some of the latest 3D printing equipment. This program intends to provide experience through projects, with hands-on use of equipment and software. It will also include relevant industry visits, guest speakers and industry-related projects.
– You can find more information HERE.
10 – Cranfield University
This university masters degree is more specific to metal additive manufacturing than additive manufacturing in general. You can study full-time for one year or part-time during two years. It will provide students with the latest knowledge and skills for metal Additive Manufacturing (AM), including AM processes and their capabilities, designing AM systems, qualification, modelling and materials. Practical experience will be gained through assignments and group and individual projects in close collaboration with leading industrial end-users.
– You can find more information HERE.
Did you find this useful for your studies? Let us know in a comment below or on our Facebook and Twitter pages! Don’t forget to sign up for our free weekly Newsletter, with all the latest news in 3D printing delivered straight to your inbox!
Additive Manufacturing and Design Master's Degree (M.Eng.) Online
How to ApplyRequest Info
In This Section
Program Summary
Position yourself to be a leader in the fast-growing 3D printing industry.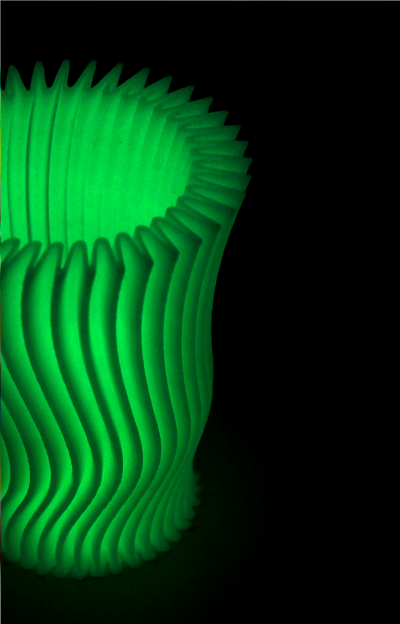
How To Apply
Apply by March 1 to start May 15
How To Apply
Costs and Financial Aid
30 Credits $1,121 per credit
Costs and Financial Aid
Nationally Recognized
Our graduate engineering programs are highly ranked by U.S. News & World Report.
Earn a Master of Engineering in Additive Manufacturing and Design
Additive manufacturing, also known as 3D printing, is a rapidly emerging trend in the manufacturing sector, redefining how everything from medical devices to aerospace structures are designed, engineered, manufactured, certified, and brought to market.
Fabricating three-dimensional parts layer by layer through additive manufacturing on a 3D printer provides engineers with unprecedented possibilities for designs and materials. In doing so, this innovative design process allows engineers to create light-weight structures, consolidate assemblies of multiple components into a single 3D printed part, and functionally grade structures using multi-material components to improve performance. This rapid prototyping ability is generating considerable interest in a wide range of industries, including aerospace, consumer goods, energy, medical, oil and gas, and space. The technology shows the potential to find new applications for virtually every material, as well as the opportunity to create new alloys and composites not previously thought possible.
Work With Faculty to Accelerate Additive Manufacturing and Design Technology
The 30-credit online Master of Engineering in Additive Manufacturing and Design (AMD) is offered through Penn State World Campus in partnership with Penn State's College of Engineering and the School of Engineering Design, Technology, and Professional Programs, along with the College of Earth and Mineral Sciences. It is the first multidisciplinary graduate-level program focused on additive manufacturing and design in the country.
The primary goal of the Additive Manufacturing and Design program is to prepare you to apply foundational knowledge, critical thinking, problem solving, and creativity, in your use of additive manufacturing and associated design tools and methods. You can grow as a leader in 3D printing and prototyping and help accelerate industry adoption of additive manufacturing, while striving for advancement of the technology and developing innovative solutions.
The Penn State Difference
This program combines a focused, groundbreaking curriculum with a flexible, convenient, online format, allowing you to maintain your professional commitments as you acquire a valued credential. You can learn from faculty who have experience teaching in online education environments, with a range of expertise in such fields as 3D printing, rapid prototyping, CAD/CAM, additive manufacturing, materials science, technology innovation, and leadership.
Your Engineering Course Work
The focus of the curriculum is to help engineers become well versed not only in technical engineering skills, but also in communication, ethics, entrepreneurial thinking, and professionalism. The courses can help you acquire the analytical and practical skills to digitally design, develop, analyze, numerically model, optimize, fabricate, and inspect new components and subassemblies, using additive manufacturing technologies.
Who Should Apply?
The program is designed for working professionals who have a bachelor's degree in engineering or a related technical field, relevant work experience, and some experience with proficiency 3D printing software and hardware, who are looking for career development opportunities to enhance their knowledge and skill sets in additive manufacturing and design.
3D Printing Technologies - FDM, FFF, SLA, DLP, PolyJet, CJP, SLS, SLM
FUSED DEPOSITION MODELING PRINT TECHNOLOGY – + FDM
One of the most popular, simple and cheap 3D printing technologies is Fused Depsition Modeling. The technology was invented more than 20 years ago and implemented by Stratasys, and still it remains the most popular. The principle of building a prototype using this method is simple and clear. The simulated 3D object in STL format is transferred to the 3D printer software. After placing the model in a virtual working chamber (automatically or manually), cutting the model into horizontal layers, the 3D printing process begins. The extruder print head melts the filament, laying down layer by layer according to the model data. If necessary, before starting printing, auxiliary structures (supports) are automatically or manually placed on a virtual 3D model, which, after printing, can be removed with a special solution or manually.
There are many types of equipment that print using this technology. They differ in terms of accuracy, the number of print heads, the size of the working platform, the presence or absence of a closed working chamber, consumable options, etc. There are models that support the ability to use different materials when printing. There are also industrial FDM 3D printers and personal ones.
The following materials can be used in FDM 3D printing:
- ABS
- PLA
- SBS plastic
- Nylon
- Polycarbonate
- HIPS support material
- PVA support material
- PETG plastic
- FLEX rubber-like plastic
- RUBBER plastic with rubber properties
The most popular materials are ABS and PLA. Products printed using FDM technology are characterized by elasticity, strength and stable physical characteristics, depending on the selected material. The construction accuracy varies from 0.027mm to 1mm. As a rule, the printed object has a layered (ribbed) surface, the severity of which depends on the thickness of one layer. This effect can be eliminated by post-processing with chemicals or grinding.
The advantages of FDM 3D printing technology include sufficient speed and ease of manufacture of products, safety, high accuracy, a wide choice of materials, as well as ease of use and maintenance of equipment. In addition, consumables for printing in this way are affordable. All this together makes this technology the most highly competitive and affordable in economic terms.
FDM 3D printing technology can be used for rapid prototyping and even small series production. Depending on the selected consumable material, this technology can be used to create parts of mechanisms, toys, interior items, jewelry, souvenirs and much more. The use of high-strength engineering thermoplastics makes it possible to apply this 3D printing method to products used in the aerospace industry.
Our company has several 3D printers working on this technology. You can order high-quality 3D printing using FDM technology from us with any of the available materials and in any available color option. We guarantee you the quality and efficiency of order execution of any degree of complexity.
To order 3D printing using FDM technology, you need to send us a file in STL format. Trust our professionalism and take advantage of the most affordable 3D printing.
STEREOLITHOGRAPHY PRINT TECHNOLOGY – + SLA
SLA 3D printing technology or laser stereolithography is based on the layer-by-layer curing of a liquid photopolymer under the action of a laser beam. The technology was invented in 1986 by Charles W. Hull, who founded 3D Systems, which manufactures 3D printers that print using this technique.
Photopolymer, which in this case acts as a consumable, is a resinous substance that changes its properties under the influence of ultraviolet radiation - it polymerizes and hardens. In this case, the wavelength and time of exposure to radiation will depend on the environmental conditions and the specific material.
The principle of building a model using laser stereolithography technology at the initial level is similar to any other - the modeled object in STL format is loaded into the 3D printer software, placed in a virtual working chamber and cut into layers. Photopolymer resin is poured into a special container. It contains a working platform on which the part will be built. Initially, the working platform is set so that it is covered with the thinnest layer of photopolymer (0.05-0.13 mm). This will be the size of the layer when printed. Then the laser is turned on, it irradiates the areas that will later become parts of the finished product. As a result of irradiation, the material hardens and the working platform sinks to the extent of the layer. The algorithm repeats again until all programmed layers are exhausted. Then the finished product is immersed in a special bath, into which a composition is poured to remove excess elements. And at the end, the product is again irradiated so that it gains maximum strength.
Stereolithography, like most other 3D printing technologies, requires support. After printing is completed, they are removed manually.
The main advantages of stereolithography technology are the highest precision and the ability to create the smallest and thin-walled objects. The technique is distinguished by easy post-processing of products and their almost perfect surface. The disadvantage of this technology is the impossibility of using several materials at once. Color printing is also not possible. The properties of the model and its color will determine the initial characteristics of one photopolymer. In addition, the cost of such printing and equipment is not cheap.
Due to the fact that stereolithography allows you to get a model of almost any degree of complexity, the main scope of this 3D printing is research. And due to the highest accuracy and detail, this technique is used in medicine, in particular in dentistry. Also, printed models are in demand in art, jewelry, museum work and restoration. There are photopolymers that can be used to print molded models. The model printed on a 3D printer, in this case, is poured with molding sand and placed in an oven for annealing at a temperature of 1000 degrees. As a result, the polymer burns out without leaving a trace, and the resulting form can be used for pouring metal under vacuum. As the metal cools, the mold breaks and the metal part is removed.
In our company you can order 3D printing using SLA technology. We have in our arsenal professional 3D printers using this technology and a wide range of photopolymer resins with various characteristics for 3D printing. We guarantee you high quality and prompt execution of the order. To order 3D printing using the laser stereolithography method, you need to provide us with a file in STL format.
Get the most out of high-precision and highly detailed stereolithographic 3D printing.
DIGITAL LIGHT PROCESSING PRINT TECHNOLOGY – + DLP
DLP 3D printing is one of the most accurate and fastest 3D printing methods. It is based on the technology that Larry Hornbeck invented for multimedia projectors. The peculiarity lies in the use of a special mirror matrix. Each individual pixel of this matrix is a microscopic mirror.
DLP stands for Digital Light Processing, which means "Digital Light Processing". Thus, this technology is one of the varieties of photopolymer 3D printing and photopolymer resin is used as a consumable. This resin is irradiated with projected light from the LEDs and hardens. The technology is very similar to stereolithography. However, with SLA 3D printing, each layer is, as it were, loomed with laser beams. And in DLP technology, the layer is completely projected onto a photopolymer using the same matrix with micromirrors, that is, this method is more like stamping. Thus, while maintaining the highest accuracy of 3D printing, it was possible to significantly increase its speed. At the moment, the speed of DLP printing is several times higher than FDM, SLM and SLA printing. For this reason, the DLP 3D printing technique is one of the most promising.
The thickness of one layer when printing using DLP technology is 10-15 microns, which is basically similar to the indicators for SLA 3D printing technology. For comparison, the FDM method implies a minimum thickness of at least 50 microns.
Since DLP printers are the main competitors of SLA printing, their application is about the same. They can print products for dentistry, jewelry, complex designs and even souvenirs. The technology is also in demand in the research area.
Photopolymers used in 3D printing with this method are diverse, and you can choose a material with the desired characteristics. For example, there are materials that mimic the properties of ABS plastic, hard engineering plastics, and even rubber. However, it is important to know that in some cases, under the influence of light, photopolymer products can crack and become brittle. This technology implies the impossibility of using several materials at once. Color printing is also not possible. The properties of the model and its color will determine the initial characteristics of one photopolymer.
However, there is also a drawback to DLP technology - as in the case of SLA 3D printers, the cost of equipment is very high, as in principle the price of photopolymers. Not every, even a large company, can afford such a 3D printer.
But this does not mean at all that you will not be able to take advantage of the speed and advantages of DLP printing, because you have the opportunity to order 3D printing on such a 3D printer in our company. To do this, you just need to provide us with an STL file with the desired model. We guarantee you prompt execution of the order and high quality.
Enjoy high-quality, fast, high-precision DLP printing.
PRINT TECHNOLOGY LED DISPLAY – + LED
One of the varieties of DLP 3D printing technology is LED 3D printing. That is, this method is based on the same digital light processing (as Digital Light Processing stands for). However, in devices for LED 3D printing, instead of a mirror chipped matrix, there is an LED display that immediately highlights a whole layer on the material, like a kind of light stamp. Using an LED display allows you to increase the speed of 3D printing. So it takes about 10-15 minutes to 3D print 2.5 cm along the Z-axis, and it's really fast. Although the print speed in any case will directly depend on the thickness of one layer.
As a consumable material, a photopolymer resin is used, which polymerizes under the action of ultraviolet light, that is, it changes its qualities, passing from a semi-liquid state to a solid one. There are many options for photopolymers, among which there are materials that, after the polymerization process, imitate the characteristics of solid, including engineering plastics. There are also those that are very similar to classic rubber after hardening, that is, they have the same strength and elasticity indicators. You can also choose biocompatible photopolymers. When choosing a material for printing, you should be guided by the technical characteristics and scope of a particular photopolymer.
Like any other photopolymer 3D printing, LED technology is characterized by the highest precision and detail. The thickness of one layer is only 10-15 microns. With its help, you can print thin-walled products, objects with complex geometry. Photopolymers practically do not shrink and do not change their geometry after hardening, and this is also an advantage, especially when it is necessary to print anatomically accurate models. The DLP LED 3D printing technology itself, although it provides for a layer-by-layer method for creating a model, still does not differ in pronounced layering of the finished model. The surface is almost perfectly smooth, requiring no additional processing.
If complex objects are printed, support must be used. They can be set in automatic or manual mode immediately before printing during the positioning of the model in the virtual working chamber. These supports are subsequently removed manually.
LED technology implies the impossibility of using several materials at once. Color 3D printing is also not possible. The properties of the finished prototype and its color will determine the initial characteristics of the photopolymer used.
The field of application of LED 3D printing is basically the same as the field of use of DLP printing, since this technology is, in fact, its improvement. The technology is in demand in the production of hearing aids and earmolds, in dentistry and orthodontics, as well as in jewelry. Due to the high accuracy and detail of 3D objects printed using this technology, products will also be in demand in the field of research and engineering activities.
LED 3D printer is very expensive. However, this does not mean that its benefits are not available to you. You can order 3D printing using LED technology in our company. We offer you a large selection of photopolymer resins for printing and guarantee the high quality of models, in full compliance with the provided STL-file, and the prompt execution of the order.
Take full advantage of LED technology with our help.
POLYJET PRINT TECHNOLOGY – + PJ
PolyJet is a revolutionary 3D printing technology that is a powerful tool for high performance additive manufacturing. The technique was invented and patented by Stratasys. The operation of a PolyJet 3D printer is very similar to a conventional, well-known inkjet printer, but printing is carried out not on paper and not with simple ink, but on a special substrate in the chamber, and an acrylic-based liquid photopolymer acts as a material.
The PolyJet-enabled 3D printer is equipped with a special print head with nozzles. There can be several printheads, which allows you to print faster and even prototyping several objects at once. The printing process is carried out by dosed deposition of a photopolymer. One layer of 16 microns is sprayed at a time. Then this layer is exposed to an ultraviolet lamp and the photopolymer turns into a hard plastic. After that, the working platform with the substrate is lowered, and the algorithm is repeated again. When printing complex geometric shapes, a support material is used. For this technology, a special gel-like material has been created, which is easily removed with plain water or hands.
A key feature of PolyJet 3D printing technology is the ability to use multiple materials in one print run. At the same time, there are models of 3D printers that can mix photopolymers in various proportions, obtaining a variety of composite materials with certain characteristics. Also, this technology is characterized by the possibility of complex color reproduction. That is, it is possible to use color printing, the palette of which includes about 1000 colors and shades. In fact, it is the only additive manufacturing technology that supports these capabilities.
Other advantages of the method include: high printing speed, high accuracy and detail, perfect surface and generally excellent quality of printed objects. In addition, a wide range of materials allows you to create objects of almost any kind. More than 100 different photopolymer resins can be used as a base, mixing of which allows obtaining materials from transparent to completely opaque, from hard to elastic and rubbery. This is truly a new standard for realism in the most complex prints. PolyJet technology allows you to achieve perfect surface smoothness and imitate any even the most subtle texture. The camera of the PolyJet 3D printer is quite large, but if you need to print a large object, then it can be broken into parts, which are then simply glued together.
The only disadvantage of the technology is its high cost. The equipment is very expensive, and photopolymer resins are not cheap. But this does not mean that you cannot use this technology, because you have the opportunity to order 3D printing using PolyJet technology in our company. In a short time, we will implement your project on our own 3D printer. All you need is to provide us with the STL file.
PolyJet 3D printing technology is truly limitless.
COLOR JET PRINTING TECHNOLOGY – + CJP
Color inkjet 3D printing - CJP (ColorJet Printing) technology - a patented technique invented by 3D Systems. It consists in layer-by-layer gluing and coloring of the powder gypsum composite. 3D printing of this type is based on a technique called 3DP, which is its improvement.
3D printing by this method is based on the use of two materials: base and binder. To create the base layer, a consumable of the main type is used. It consists of gypsum mixed with a polymer. And the binder is used for gluing and staining the layers.
ColorJet Printing 3D printer has two cameras. A gypsum composite is poured into one of them, and the second chamber is used to remove excess material. The model is "grown" in layers. A special roller distributes a thin layer of material on the working platform. The print head applies the adhesive and colors the main consumable particles. All this is carried out in accordance with the loaded mathematical 3D model. The working surface is lowered by the amount of the layer (0.1016 mm), and the roller again applies a layer of gypsum composite powder, and so on until the model is printed to the end.
ColorJet Printing technology has a relatively low cost of printed models. Its advantage is the absence of the need for supports, since the non-glued material will act as supporting structures. In addition, the material that was not used during printing can be reused. It turns out that this method of additive manufacturing is waste-free.
The CJP technology is the only one that uses the CMYK printing color palette. This palette includes 390 thousand colors and shades. The material is dyed during the gluing of the layer, resulting in details with excellent color reproduction.
The accuracy of building a model by this method is very high, the minimum printed element has dimensions of 0.1-0.4 mm. The thickness of the walls of the prototype, which will not collapse under their own weight, is 0.102-0.089 mm.
Models printed using ColorJet Printing technology have a typical gypsum rough surface, characterized by a high degree of hygroscopicity. The strength of the models is average. However, finished models are easy to sand, paint and glue. To improve the characteristics of the model and protect them from moisture, you can cover the surface with varnishes, waxes, resins, as well as all kinds of fixatives.
The technology can be used for 3D printing of architectural models, product presentations, souvenirs, miniatures, etc. Despite the fact that the products are of low strength, they allow you to visually evaluate the prototypes.
CJP 3D printer has impressive dimensions and is quite expensive, despite the fact that the cost of printed prototypes is low, not everyone can afford such pleasure. In our company, you can order 3D printing using ColorJet Printing technology. We guarantee you prompt execution of the order and full compliance of the prototype with the modeled object. All you need is to provide us with an STL file with a 3D model.
Take advantage of CJP 3D printing technology with our help and appreciate all its advantages in practice.
SELECTIVE LASER SINTERING PRINT TECHNOLOGY – + SLS
Selective, that is, selective, laser sintering is a 3D printing technology that was created back in 1979. However, for a long time it was not available to the market until DTM was created in 1996. In 2001, 3D Systems bought this company, and in 2014 the patent expired, and now this technology is available to a wide range of consumers.
The SLS 3D printing technique consists in the fact that the material is heated by a laser beam until the particles are sintered, that is, not completely. As a result, the model turns out not to be solid, but as if “sintered” from individual tiny particles. If we consider the structure under magnification, then individual particles of the material will be visible, as if glued to each other.
The operation of a 3D printer that prints using SLS technology is as follows. Powder material is poured into the chamber. A 3D model in STL format is loaded into the software. The working platform is exposed and a thin layer of material (thickness about 120 microns) is applied to it, leveled with a roller. The laser sinters the powder particles according to the loaded model. After the layer is completed, the platform is lowered and a new layer of material is applied. The procedure will be repeated until the very last layer is completed.
Since there is unused material in the working chamber, the need for supports simply disappears, because complex and overhanging parts will be supported by unused material. This allows you to get models of any, even very complex geometry.
Powder polymers, metals and their alloys, ceramics, glass, composite materials can be used as consumables. But in any case, the material must be in powder form. Due to the fact that the power of laser radiation can be adjusted, the degree of melting of the material can change, and, accordingly, the strength and uniformity of the structure of the resulting model. Currently, the most popular material for 3D printing using SLS technology is polyamide. This is a versatile powder material that can be used in almost any field. If powdered metal is used for printing, it is preheated to make printing faster and easier.
As a result of 3D printing, models are obtained with a surface that requires processing, in particular grinding. Models made of polyamide are sensitive to moisture, so they must be coated with a protective compound, such as moisture-resistant paint, if outdoor use is planned.
Selective laser sintering shows excellent results when used in small-scale production, as well as for the manufacture of master models. This 3D printing technology is in demand in the aerospace industry, in manufacturing, etc.
The disadvantages of SLS 3D printing technology are the high cost of equipment. In addition, the powder material is potentially harmful to the human body, so a separate room with air conditioning and an air filter is equipped for such 3D printers. All this imposes difficulties for additive manufacturing using this technique. But this does not mean that you cannot take advantage of the possibilities of selective laser sintering technology, because our company provides professional 3D printing services on such equipment. You can order 3D printing using SLS technology from us. All you need is to provide us with a file with a 3D model in STL format. We guarantee you high quality printing in full accordance with the provided 3D model.
SELECTIVE LASER MELTING PRINT TECHNOLOGY – + SLM
Selective (selective) laser melting - SLM is a 3D printing method from a mathematical CAD model, which is used to create 3D objects by melting metal powders. For this, high-power lasers are used.
Using this technology, it is possible to create precise metal parts that will later be used in various units and assemblies, including non-separable structures that change their geometry during use. This type of printing is becoming more and more widespread, because the parts created by this method are in many ways superior in their mechanical and physical characteristics to products produced by traditional methods.
The advantages of 3D printing using SLM technology are: the ability to solve the most complex production problems, including in the aerospace industry, where parts and assemblies have a hard load and serious requirements are imposed. Also, SLM printing is used in experimental and scientific and technical activities, where it is possible to significantly reduce the R&D cycle, because the most complex mechanisms and products can be created without serious equipment.
The technology also allows you to print objects with internal cavities, which can significantly reduce the weight of products.
The essence of the method lies in the layer-by-layer application of metal powder on a special heated platform and its subsequent processing with a high-power laser, in accordance with the CAD model. The working chamber of the 3D printer, where the melting process itself takes place, is filled with argon or nitrogen. The choice of gas will depend on which consumable is selected for printing. Inert gas will be mainly consumed in preparation for printing, when the chamber is purged, because it is necessary to achieve conditions so that the percentage of oxygen in the chamber is no more than 0.15%. This is a necessary condition in order to avoid the oxidation of metals. Consumables can be: powdered metals and alloys. It can be tool or stainless steel, titanium and its alloys, aluminum, platinum, gold, as well as cobalt-chromium alloys.
The model is fused layer by layer. After the printing of the prototype is completed, it is removed from the chamber with the working platform and separated from it mechanically. In the future, it may require processing, because the surface of the product may not be ideal. However, the product will be very strong and uniform in structure, similar to cast.
One of the advantages of the technology is its economy and non-waste. After all, unsintered material can be reused. The thickness of one layer is 20-100 microns. Thus, SLM 3D printing is a very precise and highly detailed additive manufacturing technique.
The cost of 3D printers using this method is very high. And in general, their operation is by no means a simple matter, requiring special conditions. But you have a great opportunity to use 3D printing using selective laser fusion technology with the help of our company. All you need is just to order 3D printing using this technique in our company. To do this, you need to provide us with an STL file with a CAD model for printing.
Take advantage of the innovative method of creating high-precision metal products - SLM printing.
ELECTRON BEAM MELTING PRINT TECHNOLOGY – + EBM
One of the most reliable metal 3D printing methods is EBM printing or electron beam melting. This is an additive manufacturing technology that is used to create high-strength, comparable to cast, metal products. Pure (without impurities) metal powder acts as a consumable. Printing is carried out in a vacuum chamber, which minimizes the oxidation of the material, such as pure titanium.
Electron beam melting is very similar to SLS 3D printing technology, that is, selective laser melting. However, it does not use powerful lasers, but electron emitters, which serve as sources of powerful energy used to melt metal. So-called electron guns fire high power electron beams that fuse metal powder. The method is similar to other 3D printing methods - the layering of consumables. A layer of metal powder is applied, and electron beams, following the contour of the model, fuse the material. Then the algorithm is repeated again until all layers are created and a finished three-dimensional object is obtained in accordance with the mathematical 3D model.
As a result of such 3D printing, a high-density metal model is obtained, and the porosity of the structure is absent. This means that additional processing by the method of firing for a strong fusion of the material in the model is not required. And the model itself will have high strength characteristics initially, that is, it will not differ in any way from cast products.
Electron beam melting is printed at high background temperatures of 700-1000 degrees Celsius. This avoids a strong temperature difference between the already cooled printed layer and the fresh hot layer. Therefore, printed parts will not suffer from residual mechanical stress. This is how the highest possible strength of EBM-printed products is achieved.
This 3D printing technology is used to create high-precision titanium prostheses and implants, such as hip and knee implants, skull parts, etc. Titanium combines strength and biocompatibility.
EBM printing is also used in the aerospace industry. With the help of this technology, load-bearing structural elements of various devices (aircraft, rockets), as well as parts of their engines, are printed. For this purpose, strong and light powder metals are used.
EBM printing equipment is very expensive. However, you can order 3D printing using the technology of electron beam melting of powder metal. We are ready to fulfill your order in the shortest possible time, and we guarantee the high quality of printed products, in full accordance with the provided STL file.
Take advantage of high-precision and high-strength metal 3D printing - electron beam melting (EBM).
3D printing for "dummies" or "what is a 3D printer?"
- 1 3D printing term
- 2 3D printing methods
- 2.1 Extrusion printing
- 2.2 Melting, sintering or gluing
- 2.3 Stereolithography
- 2.4 Lamination
- 3 Fused Deposition Printing (FDM)
- 3.1 Consumables
- 3.2 Extruder
- 3.3 Working platform
- 3.4 Positioners
- 3.5 Control
- 3.6 Varieties of FDM printers
- 4 Laser stereolithography (SLA)
- 4.1 Lasers and projectors
- 4.2 Cuvette and resin
- 4.3 Varieties of Stereolithography Printers
The term 3D printing
The term 3D printing has several synonyms, one of which quite briefly and accurately characterizes the essence of the process - "additive manufacturing", that is, production by adding material. The term was not coined by chance, because this is the main difference between multiple 3D printing technologies and the usual methods of industrial production, which in turn received the name "subtractive technologies", that is, "subtractive". If during milling, grinding, cutting and other similar procedures, excess material is removed from the workpiece, then in the case of additive manufacturing, material is gradually added until a solid model is obtained.
Soon 3D printing will even be tested on the International Space Station
Strictly speaking, many traditional methods could be classified as "additive" in the broad sense of the word - for example, casting or riveting. However, it should be borne in mind that in these cases, either the consumption of materials is required for the manufacture of specific tools used in the production of specific parts (as in the case of casting), or the whole process is reduced to joining ready-made parts (welding, riveting, etc. ). In order for the technology to be classified as “3D printing”, the final product must be built from raw materials, not blanks, and the formation of objects must be arbitrary - that is, without the use of forms. The latter means that additive manufacturing requires a software component. Roughly speaking, additive manufacturing requires computer control so that the shape of final products can be determined by building digital models. It was this factor that delayed the widespread adoption of 3D printing until the moment when numerical control and 3D design became widely available and highly productive.
3D printing techniques
3D printing technologies are numerous, and there are even more names for them due to patent restrictions. However, you can try to divide technologies into main areas:
Extrusion printing
This includes methods such as deposition fusion (FDM) and multi-jet printing (MJM). This method is based on the extrusion (extrusion) of consumables with the sequential formation of the finished product. As a rule, consumables consist of thermoplastics or composite materials based on them.
Melting, sintering or bonding
This approach is based on bonding powdered material together. Formation is done in different ways. The simplest is gluing, as is the case with 3D inkjet printing (3DP). Such printers deposit thin layers of powder onto the build platform, which are then selectively bonded with a binder. Powders can be made up of virtually any material that can be ground to a powder—plastic, wood, metal.
This model of James Bond's Aston Martin was successfully printed on Voxeljet's SLS printer and just as successfully blown up during the filming of Skyfall instead of the expensive original
sintering (SLS and DMLS) and smelting (SLM), which allow you to create all-metal parts. As with 3D inkjet printing, these devices apply thin layers of powder, but the material is not glued together, but sintered or melted using a laser. Laser sintering (SLS) is used to work with both plastic and metal powders, although metal pellets usually have a more fusible shell, and after printing they are additionally sintered in special ovens. DMLS is a variant of SLS installations with more powerful lasers that allow sintering metal powders directly without additives. SLM printers provide not just sintering of particles, but their complete melting, which allows you to create monolithic models that do not suffer from the relative fragility caused by the porosity of the structure. As a rule, printers for working with metal powders are equipped with vacuum working chambers, or they replace air with inert gases. Such a complication of the design is caused by the need to work with metals and alloys subject to oxidation - for example, with titanium.
Stereolithography
How an SLA printer works
Stereolithography printers use special liquid materials called "photopolymer resins". The term "photopolymerization" refers to the ability of a material to harden when exposed to light. As a rule, such materials react to ultraviolet irradiation.
Resin is poured into a special container with a movable platform, which is installed in a position near the surface of the liquid. The layer of resin covering the platform corresponds to one layer of the digital model. Then a thin layer of resin is processed by a laser beam, hardening at the points of contact. At the end of illumination, the platform together with the finished layer is immersed to the thickness of the next layer, and illumination is performed again.
Lamination
Laminating (LOM) 3D printers workflow
Some 3D printers build models using sheet materials - paper, foil, plastic film.
Layers of material are glued on top of each other and cut along the contours of the digital model using a laser or a blade.
These machines are well suited for prototyping and can use very cheap consumables, including regular office paper. However, the complexity and noise of these printers, coupled with the limitations of the models they produce, limit their popularity.
Fused deposition modeling (FDM) and laser stereolithography (SLA) have become the most popular 3D printing methods used in the home and office.
Let's take a closer look at these technologies.
Fused Deposition Printing (FDM)
FDM is perhaps the simplest and most affordable 3D construction method, which makes it very popular.
High demand for FDM printers is driving device and consumable prices down rapidly, along with technology advances towards ease of use and improved reliability.
Consumables
ABS filament spool and finished model
FDM printers are designed to print with thermoplastics, which are usually supplied as thin filaments wound on spools. The range of "clean" plastics is very wide. One of the most popular materials is polylactide or "PLA plastic". This material is made from corn or sugar cane, which makes it non-toxic and environmentally friendly, but makes it relatively short-lived. ABS plastic, on the other hand, is very durable and wear-resistant, although it is susceptible to direct sunlight and can release small amounts of harmful fumes when heated. Many plastic items that we use on a daily basis are made from this material: housings for household appliances, plumbing fixtures, plastic cards, toys, etc.
In addition to PLA and ABS, printing is possible with nylon, polycarbonate, polyethylene and many other thermoplastics that are widely used in modern industry. More exotic materials are also possible, such as polyvinyl alcohol, known as "PVA plastic". This material dissolves in water, which makes it very useful for printing complex geometric patterns. But more on that below.
Model made from Laywoo-D3. Changing the extrusion temperature allows you to achieve different shades and simulate annual rings
It is not necessary to print with homogeneous plastics. It is also possible to use composite materials imitating wood, metals, stone. Such materials use all the same thermoplastics, but with impurities of non-plastic materials.
So, Laywoo-D3 consists partly of natural wood dust, which allows you to print "wooden" products, including furniture.
The material called BronzeFill is filled with real bronze, and models made from it can be ground and polished, achieving a high similarity to products made from pure bronze.
One has only to remember that thermoplastics serve as a binding element in composite materials - they determine the thresholds of strength, thermal stability and other physical and chemical properties of finished models.
Extruder
Extruder - FDM print head. Strictly speaking, this is not entirely true, because the head consists of several parts, of which only the feed mechanism is directly "extruder". However, by tradition, the term "extruder" is commonly used as a synonym for the entire print assembly.
FDM extruder general design
The extruder is designed for melting and applying thermoplastic thread. The first component is the thread feed mechanism, which consists of rollers and gears driven by an electric motor. The mechanism feeds the thread into a special heated metal tube with a small diameter nozzle, called a "hot end" or simply a "nozzle". The same mechanism is used to remove the thread if a change of material is needed.
The hot end is used to heat and melt the thread fed by the puller. As a rule, nozzles are made from brass or aluminum, although more heat-resistant, but also more expensive materials can be used. For printing with the most popular plastics, a brass nozzle is quite enough. The “nozzle” itself is attached to the end of the tube with a threaded connection and can be replaced with a new one in case of wear or if a change in diameter is necessary. The nozzle diameter determines the thickness of the molten filament and, as a result, affects the print resolution. The heating of the hot end is controlled by a thermistor. Temperature control is very important, because when the material is overheated, pyrolysis can occur, that is, the decomposition of plastic, which contributes both to the loss of the properties of the material itself and to clogging of the nozzle.
PrintBox3D One FDM Printer Extruder
In order to prevent the filament from melting too early, the top of the hot end is cooled by heatsinks and fans. This point is of great importance, since thermoplastics that pass the glass transition temperature significantly expand in volume and increase the friction of the material with the walls of the hot end. If the length of such a section is too long, the pulling mechanism may not have enough strength to push the thread.
The number of extruders may vary depending on the purpose of the 3D printer. The simplest options use a single print head. The dual extruder greatly expands the capabilities of the device, allowing you to print one model in two different colors, as well as using different materials. The last point is important when building complex models with overhanging structural elements: FDM printers cannot print “over the air”, since the applied layers require support. In the case of hinged elements, temporary support structures have to be printed, which are removed after printing is completed. The removal process is fraught with damage to the model itself and requires accuracy. In addition, if the model has a complex structure with internal cavities that are difficult to access, building conventional supports may not be practical due to the difficulty in removing excess material.
Finished model with PVA supports (white) before and after washing
In such cases, the same water-soluble polyvinyl alcohol (PVA) comes in handy. Using a dual extruder, you can build a model from waterproof thermoplastic using PVA to create supports.
After printing, PVA can simply be dissolved in water and a complex product of perfect quality can be obtained.
Some FDM printers can use three or even four extruders.
Work platform
Heated platform covered with removable glass work table
Models are built on a special platform, often equipped with heating elements. Preheating is required for a wide range of plastics, including the popular ABS, which are subject to a high degree of shrinkage when cooled. The rapid loss of volume by cold coats compared to freshly applied material can lead to model distortion or delamination. The heating of the platform makes it possible to significantly equalize the temperature gradient between the upper and lower layers.
Heating is not recommended for some materials. A typical example is PLA plastic, which requires a fairly long time to harden. Heating PLA can lead to deformation of the lower layers under the weight of the upper ones. When working with PLA, measures are usually taken not to heat up, but to cool the model. Such printers have characteristic open cases and additional fans blowing fresh layers of the model.
Calibration screw for work platform covered with blue masking tape
The platform needs to be calibrated before printing to ensure that the nozzle doesn't hit the applied layers and move too far causing air-to-air printing resulting in plastic vermicelli. The calibration process can be either manual or automatic. In manual mode, calibration is performed by positioning the nozzle at different points on the platform and adjusting the platform inclination using the support screws to achieve the optimal distance between the surface and the nozzle.
As a rule, platforms are equipped with an additional element - a removable table. This design simplifies the cleaning of the working surface and facilitates the removal of the finished model. Stages are made from various materials, including aluminum, acrylic, glass, etc. The choice of material for the manufacture of the stage depends on the presence of heating and consumables for which the printer is optimized.
For a better adhesion of the first layer of the model to the surface of the table, additional tools are often used, including polyimide film, glue and even hairspray! But the most popular tool is inexpensive, but effective masking tape. Some manufacturers make perforated tables that hold the model well but are difficult to clean. In general, the expediency of applying additional funds to the table depends on the consumable material and the material of the table itself.
Positioning mechanisms
Scheme of operation of positioning mechanisms
Of course, the print head must move relative to the working platform, and unlike conventional office printers, positioning must be carried out not in two, but in three planes, including height adjustment.
Positioning pattern may vary. The simplest and most common option involves mounting the print head on perpendicular guides driven by stepper motors and providing positioning along the X and Y axes.
Vertical positioning is carried out by moving the working platform.
On the other hand, it is possible to move the extruder in one plane and the platforms in two.
SeemeCNC ORION Delta Printer
One option that is gaining popularity is the delta coordinate system.
Such devices are called "delta robots" in the industry.
In delta printers, the print head is suspended on three manipulators, each of which moves along a vertical rail.
The synchronous symmetrical movement of the manipulators allows you to change the height of the extruder above the platform, and the asymmetric movement causes the head to move in the horizontal plane.
A variant of this system is the reverse delta design, where the extruder is fixed to the ceiling of the working chamber, and the platform moves on three support arms.
Delta printers have a cylindrical build area, and their design makes it easy to increase the height of the working area with minimal design changes by extending the rails.
In the end, everything depends on the decision of the designers, but the fundamental principle does not change.
Control
Typical Arduino-based controller with add-on modules
FDM printer operation, including nozzle and platform temperature, filament feed rate, and stepper motors for positioning the extruder, is controlled by fairly simple electronic controllers. Most controllers are based on the Arduino platform, which has an open architecture.
The programming language used by printers is called G-code (G-Code) and consists of a list of commands executed in turn by the 3D printer systems. G-code is compiled by programs called "slicers" - standard 3D printer software that combines some of the features of graphics editors with the ability to set print options through a graphical interface. The choice of slicer depends on the printer model. RepRap printers use open source slicers such as Skeinforge, Replicator G and Repetier-Host. Some companies make printers that require proprietary software.
Program code for printing is generated using slicers
As an example, we can mention Cube printers from 3D Systems. There are companies that offer proprietary software but allow third-party software, as is the case with the latest generation of MakerBot 3D printers.
Slicers are not intended for 3D design per se. This task is done with CAD editors and requires some 3D design skills. Although beginners should not despair: digital models of a wide variety of designs are offered on many sites, often even for free. Finally, some companies and individuals offer 3D design services for custom printing.
Finally, 3D printers can be used in conjunction with 3D scanners to automate the process of digitizing objects. Many of these devices are designed specifically to work with 3D printers. Notable examples include the 3D Systems Sense handheld scanner and the MakerBot Digitizer handheld desktop scanner.
MakerBot Replicator 5th Generation FDM Printer with built-in control module on the top of the frame
The user interface of a 3D printer can consist of a simple USB port for connecting to a personal computer. In such cases, the device is actually controlled by the slicer.
The disadvantage of this simplification is a rather high probability of printing failure when the computer freezes or slows down.
A more advanced option includes an internal memory or memory card interface to make the process standalone.
These models are equipped with control modules that allow you to adjust many print parameters (such as print speed or extrusion temperature). The module may include a small LCD display or even a mini-tablet.
Varieties of FDM printers
Stratasys Fortus 360mc professional FDM printer that allows printing with nylon
FDM printers are very, very diverse, ranging from the simplest home-made RepRap printers to industrial installations capable of printing large-sized objects.
Stratasys, founded by Scott Crump, the inventor of FDM technology, is a leader in the production of industrial installations.
You can build the simplest FDM printers yourself. Such devices are called RepRap, where "Rep" indicates the possibility of "replication", that is, self-reproduction.
RepRap printers can be used to print custom built plastic parts.
Controller, rails, belts, motors and other components can be easily purchased separately.
Of course, assembling such a device on your own requires serious technical and even engineering skills.
Some manufacturers make it easy by selling DIY kits, but these kits still require a good understanding of the technology. RepRap Printers
And, despite their "homemade nature", RepRap printers are quite capable of producing models with quality at the level of expensive branded counterparts.
Ordinary users who do not want to delve into the intricacies of the process, but require only a convenient device for household use, can purchase a ready-made FDM printer.
Many companies focus on the development of the consumer segment of the market, offering 3D printers for sale that are ready to print "straight out of the box" and do not require serious computer skills.
3D Systems Cube consumer 3D printer
The most famous example of a consumer 3D printer is the 3D Systems Cube.
While it doesn't boast a huge build area, ultra-fast print speed, or unsurpassed model build quality, it's easy to use, affordable, and safe: This printer has received the necessary certification to be used even by children.
Mankati FDM printer demonstration: http://youtu.be/51rypJIK4y0
Laser Stereolithography (SLA)
Stereolithographic 3D printers are widely used in dental prosthetics
Stereolithographic printers are the second most popular and widespread after FDM printers.
These units deliver exceptional print quality.
The resolution of some SLA printers is measured in a matter of microns - it is not surprising that these devices quickly won the love of jewelers and dentists.
The software side of laser stereolithography is almost identical to FDM printing, so we will not repeat ourselves and will only touch on the distinctive features of the technology.
Lasers and projectors
Projector illumination of a photopolymer model using Kudo3D Titan DLP printer as an example
The cost of stereolithographic printers is rapidly declining, due to growing competition due to high demand and the use of new technologies that reduce the cost of construction.
Although the technology is generically referred to as "laser" stereolithography, most recent developments use UV LED projectors for the most part.
Projectors are cheaper and more reliable than lasers, do not require the use of delicate mirrors to deflect the laser beam, and have higher performance. The latter is explained by the fact that the contour of the whole layer is illuminated as a whole, and not sequentially, point by point, as is the case with laser options. This variant of the technology is called projection stereolithography, "DLP-SLA" or simply "DLP". However, both options are currently common - both laser and projector versions.
Cuvette and resin
Photopolymer resin is poured into a cuvette
A photopolymer resin that looks like epoxy is used as consumables for stereolithographic printers. Resins can have a variety of characteristics, but they all share one key feature for 3D printing applications: these materials harden when exposed to ultraviolet light. Hence, in fact, the name "photopolymer".
When polymerized, resins can have a wide variety of physical characteristics. Some resins are like rubber, others are hard plastics like ABS. You can choose different colors and degrees of transparency. The main disadvantage of resins and SLA printing in general is the cost of consumables, which significantly exceeds the cost of thermoplastics.
On the other hand, stereolithographic printers are mainly used by jewelers and dentists who do not need to build large parts but appreciate the savings from fast and accurate prototyping. Thus, SLA printers and consumables pay for themselves very quickly.
An example of a model printed on a laser stereolithographic 3D printer
Resin is poured into a cuvette, which can be equipped with a lowering platform. In this case, the printer uses a leveling device to flatten the thin layer of resin covering the platform just prior to irradiation. As the model is being made, the platform, together with the finished layers, is “embedded” in the resin. Upon completion of printing, the model is removed from the cuvette, treated with a special solution to remove liquid resin residues and placed in an ultraviolet oven, where the final illumination of the model is performed.
Some SLA and DLP printers work in an “inverted” way: the model is not immersed in the consumable, but “pulled” out of it, while the laser or projector is placed under the cuvette, and not above it. This approach eliminates the need to level the surface after each exposure, but requires the use of a cuvette made of a material transparent to ultraviolet light, such as quartz glass.
The accuracy of stereolithographic printers is extremely high. For comparison, the standard for vertical resolution for FDM printers is considered to be 100 microns, and some variants of SLA printers allow you to apply layers as thin as 15 microns. But this is not the limit. The problem, rather, is not so much in the accuracy of lasers, but in the speed of the process: the higher the resolution, the lower the print speed. The use of digital projectors allows you to significantly speed up the process, because each layer is illuminated entirely. As a result, some DLP printer manufacturers claim to be able to print with a vertical resolution of one micron!
Video from CES 2013 showing Formlabs Form1 stereolithography 3D printer in action: http://youtu.be/IjaUasw64VE
Stereolithography Printer Options
Formlabs Form1 Desktop Stereolithography Printer
As with FDM printers, SLA printers come in a wide range in terms of size, features and cost.